この紹介記事は、[特种铸造及有色合金/Special Casting & Nonferrous Alloys]によって発行された論文「["Influence of Casting Distance on Microstructure of Simultaneously Mixed Controlled Diffusion Solidified Al-Si Alloys"]」の研究内容を紹介するものです。
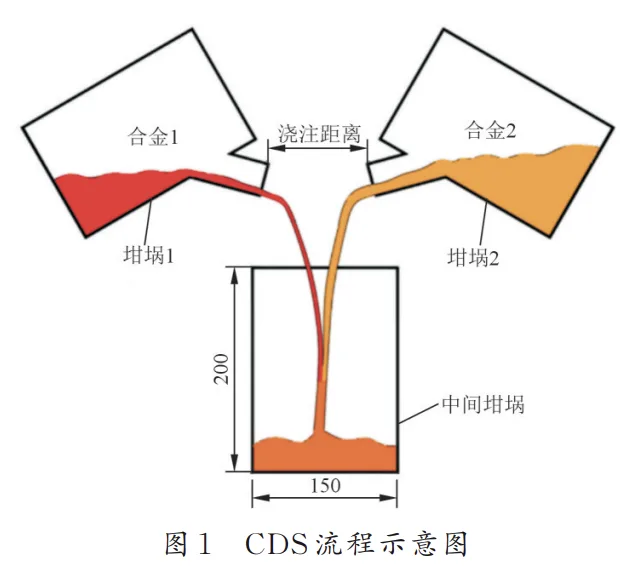
1. 概要:
- タイトル: Influence of Casting Distance on Microstructure of Simultaneously Mixed Controlled Diffusion Solidified Al-Si Alloys / 浇注距离对同时混合受控扩散凝固Al-Si合金组织影响 / 鋳造距離が同時混合制御拡散凝固Al-Si合金の微細組織に及ぼす影響
- 著者: LI Shaosi, CHEN Tijun / 李绍斯, 陈体军 / 李紹斯、陳体軍
- 発行年: 2025年2月
- 発行ジャーナル/学会: Special Casting & Nonferrous Alloys / 特种铸造及有色合金 / 特殊鋳造及び非鉄合金
- キーワード: Controlled Diffusion Solidification (CDS), Al-Si Alloy, Casting Distance, Nucleation Rate, Primary α-Al / 受控扩散凝固(CDS); Al-Si合金;浇注距离;形核率;初生a-Al / 制御拡散凝固(CDS)、Al-Si合金、鋳造距離、核生成速度、初晶α-Al
2. 概要 / はじめに
ターゲット合金Al-8Siを、前駆合金1として純Al、前駆合金2としてAl-12Siを特定の質量比と温度で用いて、制御拡散凝固(CDS)法により作製し、数値シミュレーションと実験的検証の組み合わせにより、混合溶融金属の流動場、温度場、溶質場、核生成速度、および実験的に得られた鋳造品の初晶α-Al相の粒径と形状を分析した。その結果、鋳造距離が両母合金の混合効果に影響を与えることが明らかになった。鋳造距離が過小または過大の場合、混合溶融金属の溶質場と温度場は不均一となり、核生成速度は低下し、実験的に得られた鋳造品の初晶α-Al結晶粒は粗大で不規則となる。鋳造距離が80mmの場合、混合効果が最も良好で、温度場、溶質場が最も均一で核生成速度が最も高く、初晶α-Al相の平均粒径と形状因子はそれぞれ57.6 µmと1.55であった。
以纯A1为母合金1, Al-12Si为母合金2, 在一定的质量比和温度下, 采用受控扩散凝固(CDS)的方法得到目标合金Al-8Si。采用数值模拟和试验验证相结合的方法对混合熔体的流场、温度场、溶质场和形核率以及试验所得铸件的初生α-Al相尺寸、形状进行分析。结果表明, 浇注距离对两种母合金混合效果产生影响, 在浇注距离过小或过大时, 混合熔体的溶质场和温度场都不均匀, 形核率较低, 试验所得铸件的初生α-Al晶粒粗大且不规则。浇注距离为80 mm时, 混合效果最好, 温度场、溶质场最均匀且形核率最高, 初生α-Al相的晶粒尺寸和形状因子分别为57.6 µm和1.55。
3. 研究背景:
研究テーマの背景:
アルミニウム合金は、高い強度重量比、低コスト、豊富な資源、良好な熱伝導性、耐食性、および加工の容易さから広く使用されている。従来の鋳造法では、アルミニウム合金の凝固温度範囲が広いため、粗大な樹枝状組織が生成される。樹枝状凝固は、マクロ偏析、ポーラス、および微小亀裂を引き起こし、機械的特性に深刻な影響を与える可能性がある。制御拡散凝固(CDS)は、非樹枝状(球状)組織を達成することにより、優れた鋳造特性を得るための効果的な方法である。
アルミニウム合金は、高い強度重量比を有し、軽金属に分類され、さらに低コスト、豊富な資源、良好な熱伝導性、耐食性、加工の容易さなどの特徴を有し、広い応用が期待されている。従来の鋳造法では、アルミニウム合金の凝固過程における結晶温度範囲が大きいため、微細組織は粗大な樹枝状晶となる。[4] 研究により、鋳造品中の樹枝状組織の凝固様式は、大きな引け巣、空孔を発生させるだけでなく、成分の不均一性、内部に大量の気孔や微小亀裂を形成し、鋳造品の力学性能に深刻な影響を与えることが明らかになっている。
既存研究の現状:
非樹枝状組織を得るための既存の方法には、鋳造中の結晶粒微細化剤の添加、電磁振動、機械的攪拌などがある。しかし、これらの方法には、不純物の導入、高コスト、複雑なプロセスなどの制限がある。従来のCDS技術は利点を提供するものの、依然として異常な結晶粒や不均一な結晶粒径を生成する可能性がある。
研究者らは、鋳込み中に結晶粒微細化剤[5]、電磁振動[6-8]、機械攪拌などの方法を用いて非樹枝状スラリーを得る研究を行ってきた。しかし、結晶粒微細化剤の添加は不純物を導入する可能性があり、結晶粒微細化剤のコストも高い。電磁振動と機械攪拌は、追加の外部設備を必要とし、コストが高く、工程が複雑であり、工業的応用には一定の制約がある。従来の制御拡散凝固技術には多くの制約があり、完全に要求を満たす合金であっても、依然として異常な結晶粒、不均一な結晶粒径が発生する。
研究の必要性:
CDSプロセスにおける鋳造距離の影響に関する研究は限られている。CDSパラメータを最適化し、Al-Si合金の機械的特性と成形性を向上させるために、本研究では、制御拡散混合効果に対する鋳造距離の影響を調査し、結晶粒の核生成、成長、形態、および形成メカニズムに焦点を当てる。これは、非鉄合金における制御拡散凝固技術の応用に関する参考資料を提供することを目的とする。
現在、国内ではCDS鋳造距離に関する研究報告は少ない。同時混合CDSプロセスのパラメータをさらに改善し、Al-Si合金の力学性能と成形性を向上させるために、本研究では、母合金の異なる鋳造距離が制御拡散混合効果に及ぼす影響を分析し、結晶粒の核生成、成長様式、形態などの形成メカニズムを研究し、制御拡散凝固技術の非鉄合金への応用に関する参考資料を提供することを目的とする。
4. 研究目的と研究課題:
研究目的:
本研究の目的は、Al-Si合金の同時混合CDSの混合効果に対する鋳造距離の影響を調査することである。これには、凝固中の温度場、溶質場、流動場、および核生成速度の分析、およびこれらと初晶α-Alの微細組織、結晶粒径、および形状との相関関係の解明が含まれる。
本研究では、母合金の異なる鋳造距離が制御拡散混合効果に及ぼす影響を分析し、結晶粒の核生成、成長様式、形態などの形成メカニズムを研究する。
主要な研究課題:
主要な研究課題は以下のとおりである。
- 鋳造距離は、同時混合CDSにおける混合溶融金属の温度場、溶質場、および流動場にどのように影響するか?
- 鋳造距離は、CDSにおける核生成速度と凝固プロセスにどのように影響するか?
- CDS Al-Si合金において均一な微細組織と微細な結晶粒径を達成するための最適な鋳造距離は?
- 鋳造距離は、CDS Al-Si合金における初晶α-Al相の結晶粒径と形状にどのように影響するか?
本研究では、母合金の異なる鋳造距離が制御拡散混合効果に及ぼす影響を分析し、結晶粒の核生成、成長様式、形態などの形成メカニズムを研究し、制御拡散凝固技術の非鉄合金への応用に関する参考資料を提供することを目的とする。
5. 研究方法
研究デザイン:
本研究では、数値シミュレーションと実験的検証の組み合わせを採用した。Fluentソフトウェアを用いて、純Al(合金1)とAl-12Si(合金2)のCDSプロセスをシミュレーションし、Al-8Si合金を得た。シミュレーションでは、温度場、溶質場、および流動場を分析するために、鋳造距離(60mm、80mm、100mm)を変化させた。実験は、シミュレーション結果を検証し、微細組織を分析するために、60、70、80、90、および100mmの鋳造距離で実施した。
Fluentソフトウェアを用いて、純Al(合金1)とAl-12Si(合金2)を混合して目標合金Al-8Siを得るプロセスをシミュレーションした。CDSプロセスの概略図を図1に示す。シミュレーションでは、連続の式(質量保存則)、Navier-Stokes方程式(運動量保存則)、エネルギー保存則、およびその他の関連する方程式と熱物性値は、先行研究と同様とした。[12] 試験の鋳造距離は5つのグループに分け、それぞれ60、70、80、90、100mmとし、順次検証を行った。試験における坩堝の寸法パラメータとCDSのプロセスパラメータは、シミュレーションのパラメータと完全に一致させた。
データ収集方法:
数値シミュレーションデータには、温度場、溶質場、流動場、および核生成速度が含まれる。実験データには、光学顕微鏡(OM)で得られた微細組織写真、およびImage-Pro-Plus 6.0ソフトウェアを用いて測定した結晶粒径と形状因子が含まれる。
Fluent数値シミュレーションを用いて、中間坩堝内の混合溶融金属の流動場、温度場、溶質場の分布、およびその後の凝固時の核生成速度を観察した。実験的検証と組み合わせて、最適な混合パラメータを得た。Axio Scope Al光学顕微鏡(OM)を用いて、鋳造品の断面中心付近の微細組織を観察した。Image-Pro-Plus 6.0ソフトウェアを用いて、初晶α-Alの平均結晶粒径と形状因子を計算した。
分析方法:
シミュレーション結果を分析して、鋳造距離が溶融金属の混合特性と核生成速度に及ぼす影響を評価した。実験的な微細組織を分析して、結晶粒の形態とサイズを評価した。結晶粒径(D)と形状因子(F)は、式:D=2√(A₁/π)、F = P² / (4πA₁) を用いて計算した。
Fluent数値シミュレーションを用いて、中間坩堝内の混合溶融金属の流動場、温度場、溶質場の分布、およびその後の凝固時の核生成速度を観察した。Image-Pro-Plus 6.0ソフトウェアを用いて、初晶α-Alの平均結晶粒径と形状因子を計算し、以下の判定基準に従って評価した:D=2√A₁/π、F = P² / (4πA₁)。ここで、Dは結晶粒の平均直径、Aは結晶粒の断面積、Pは結晶粒の境界周囲長、Fは結晶粒の形状因子である。
研究対象と範囲:
本研究では、Al-Si合金、特に純AlとAl-12SiのCDSによって製造されたAl-8Si合金に焦点を当てた。鋳造距離は主要な変数であり、60mm、70mm、80mm、90mm、および100mmの距離を調査した。
純Al(合金1)とAl-12Si(合金2)を混合して目標合金Al-8Siを得るプロセスをシミュレーションした。試験の鋳造距離は5つのグループに分け、それぞれ60、70、80、90、100mmとし、順次検証を行った。
6. 主な研究成果:
主要な研究成果:
- 最適な混合を提供する80mmの鋳造距離: シミュレーション結果は、80mmの鋳造距離が最も均一な温度場と溶質場、および最も高い核生成速度をもたらすことを示した。
- 80mmでの微細組織の微細化: 実験的に、80mmの鋳造距離での微細組織は、最も微細で等軸な初晶α-Al結晶粒を示した。
- 結晶粒径と形状因子: 80mmの鋳造距離では、平均結晶粒径は57.6 µm、形状因子は1.55であり、他の距離と比較して微細化され、より球状の結晶粒を示した。
- 鋳造距離の場への影響: 鋳造距離が短すぎるまたは長すぎる場合、不均一な温度場と溶質場、より低い核生成速度、およびより粗大で不規則な結晶粒につながった。
結果は、鋳造距離が2種類の母合金の混合効果に影響を与えることを示している。鋳造距離が小さすぎるか大きすぎる場合、混合溶融金属の溶質場と温度場は均一ではなく、核生成速度は低く、実験で得られた鋳造品の初晶α-Al結晶粒は粗大で不規則であった。鋳造距離が80mmの場合、混合効果が最も良く、温度場と溶質場が最も均一で、核生成速度が最も高く、初晶α-Al相の結晶粒径と形状因子はそれぞれ57.6 µmと1.55であった。鋳造距離が80mmの場合、核生成領域が最も広く、濃い色の領域は核生成領域、灰色の領域は液相領域である(図5b参照)。鋳造距離が80mmの場合、結晶粒径が最も小さく、均一であり、平均結晶粒径は57.6 µm、形状因子は1.55であった。
提示されたデータの分析:
- 温度場と溶質場(図2&3): 80mmでは、温度場と溶質場が最も均一である。60mmと100mmでは、不均一性が観察され、混合が不十分であることを示している。
- 流動場(図4): 80mmでは、溶融金属の流れが均等に分布しており、混合を促進している。60mmと100mmでは、流れが偏っており、偏析につながっている。
- 核生成速度(図5): 核生成領域は80mmで最大化されており、均一な場と流れと相関している。
- 微細組織(図6): 結晶粒径は最小化され、形状因子は80mmで1(より球状)に最も近く、最適な微細組織を確認している。80mmでの結晶粒径と形状因子は、60mmと100mmよりも大幅に優れている。
図2は、異なる鋳造距離における混合溶融金属の半分の高さの断面における温度場を示し、図3は、異なる鋳造距離における混合溶融金属の半分の高さの断面における溶質場を示し、図4は、異なる鋳造距離における混合溶融金属の半分の高さの断面における流動場を示し、図5は、異なる鋳造距離に対応する凝固領域を示し、図6は、異なる鋳造距離におけるCDS初晶α-Alの微細組織写真と、対応する結晶粒径と形状因子を示す。鋳造距離が80mmの場合、温度場、溶質場が最も均一で、核生成速度が最も高く、初晶α-Al相の結晶粒径が最も小さく、均一である。
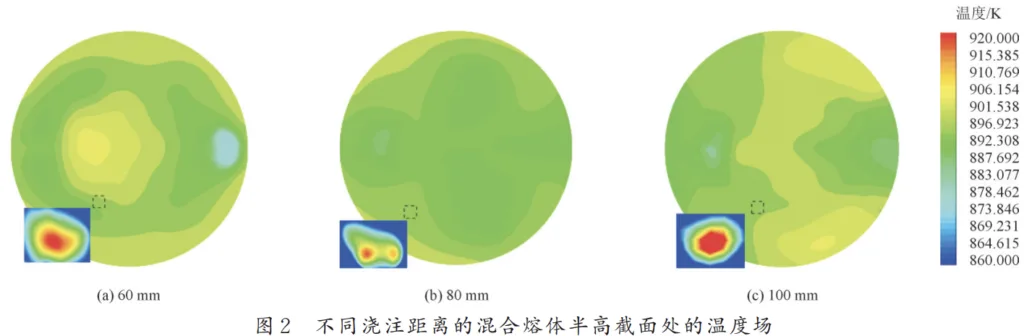
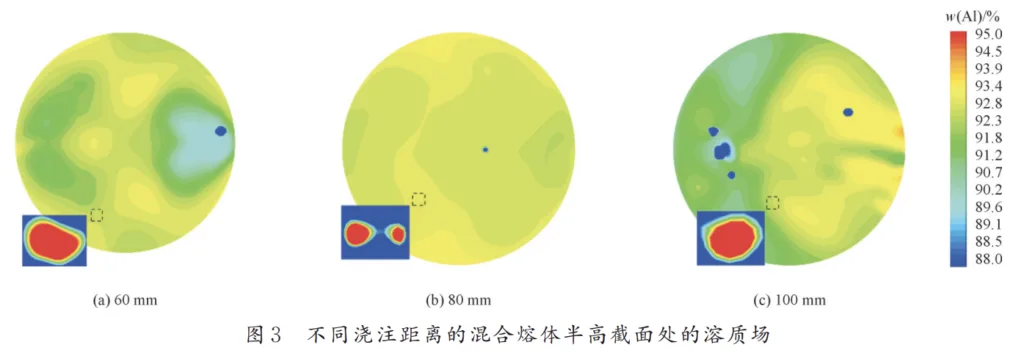
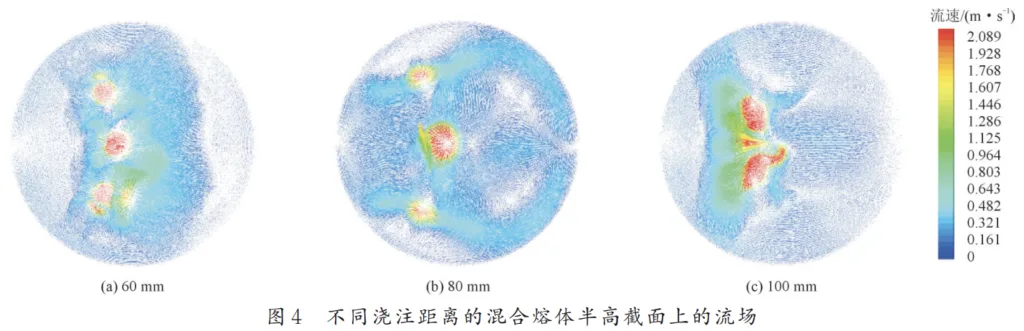
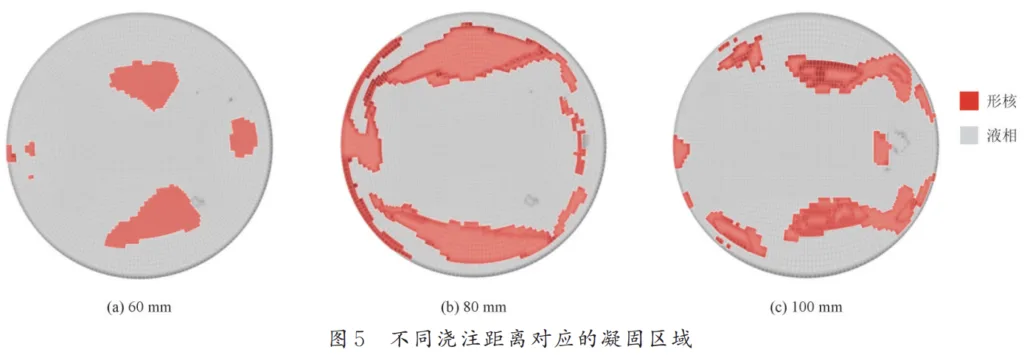
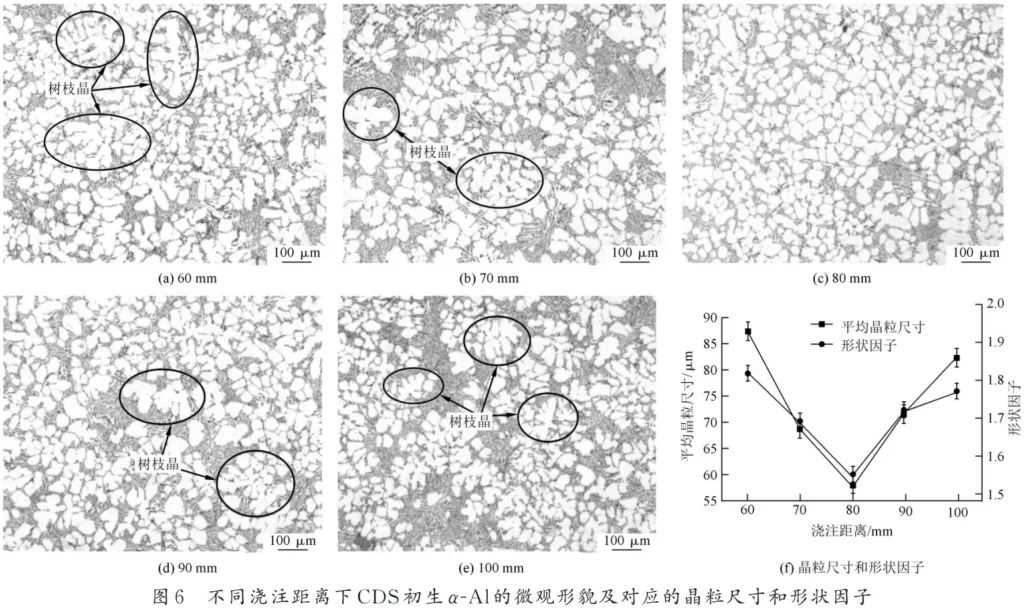
図のリスト:
- Fig.1 Schematic diagram of CDS process / 図1 CDSプロセス模式図
- Fig.2 Temperature fields in the cross section at half height of mixtures with different casting distances / 図2 異なる鋳造距離における混合溶融金属の半分の高さの断面における温度場
- Fig.3 Concentration fields in the cross section at half height of mixtures with different casting distances / 図3 異なる鋳造距離における混合溶融金属の半分の高さの断面における溶質場
- Fig.4 Flow fields in the cross section at half height of mixtures with different casting distances / 図4 異なる鋳造距離における混合溶融金属の半分の高さの断面における流動場
- Fig.5 Solidified regions corresponding to different casting distances / 図5 異なる鋳造距離に対応する凝固領域
- Fig.6 Micromorphologies of CDS primary α-Al with different casting distances as well as the corresponding grain size and shape factor / 図6 異なる鋳造距離におけるCDS初晶α-Alの微細組織写真と、対応する結晶粒径と形状因子
7. 結論:
主要な知見の要約:
本研究は、鋳造距離が同時混合CDS Al-Si合金の微細組織に大きな影響を与えることを実証した。80mmの鋳造距離が最適であることが特定され、均一な温度場と溶質場、高い核生成速度、および微細で球状の初晶α-Al結晶粒をもたらした。この距離からの逸脱は、短くても長くても、不均一な場、より低い核生成速度、およびより粗大で不規則な結晶粒につながった。
同時混合制御拡散凝固シミュレーションの結果から、鋳造距離が80mmの場合、温度場と溶質場が最も均一であり、このとき微小溶融プールの数が最も多く、サイズが最も小さく、このとき混合効果が最も優れていることがわかった。2種類の母合金溶融金属が混合する前に適切な初期流速を有しているため、混合溶融金属が中間坩堝の底部に到達した後、周囲に均一に流れ拡散し、迅速かつ均一な混合が実現できると考えられる。核生成速度からわかるように、鋳造距離が80mmの場合、核生成領域が最大、つまり核生成速度が最も高い。異なるパラメータにおける鋳造品の微細組織形態を観察すると、鋳造距離が80mmの場合、結晶粒径が最も小さく、均一である。
研究の学術的意義:
本研究は、Al-Si合金のCDSパラメータ、特に鋳造距離の最適化に関する貴重な洞察を提供する。同時混合CDSにおける鋳造距離、溶融金属混合、凝固挙動、および微細組織発達の関係を明らかにした。この知見は、CDSプロセスのより深い理解と、高性能アルミニウム合金鋳造品の製造におけるその可能性に貢献する。
本研究では、最適な鋳造距離において、初晶α-Alがさらに微細で球状化し、理想的な半凝固非樹枝状スラリーと鋳塊が得られ、鋳造品の性能向上の目的を達成できることも明らかになった。したがって、本研究で提案された同時混合CDSは、従来のCDSの欠点を克服できると考えられる。
実用的な意義:
この知見は、Al-Si合金で望ましい微細組織と特性を達成するためには、同時混合CDSにおいて鋳造距離を制御することが重要であることを示唆している。80mmの鋳造距離は、このCDS法を用いて微細組織化されたAl-8Si合金を製造するための参考として使用できる。これにより、Al-Si合金鋳造品の機械的特性と成形性が向上し、これらの材料を利用する産業に恩恵をもたらす可能性がある。
鋳造距離が80mmの場合、混合効果が最も良く、温度場、溶質場が最も均一で、核生成速度が最も高く、初晶α-Al相の結晶粒径と形状因子はそれぞれ57.6 µmと1.55であった。これは、提案された同時混合CDSが、良好な混合効果により、従来のCDSの欠点を回避できることを意味する。
研究の限界と今後の研究分野:
本研究は、特定のAl-Si合金組成(Al-8Si)と限られた範囲の鋳造距離に焦点を当てた。今後の研究では、他のAl-Si合金組成や、注湯温度や混合速度を含む、より広範囲の鋳造パラメータに対する鋳造距離の影響を調査することができる。異なる鋳造距離における凝固メカニズムと微細組織発達に関するさらなる調査も有益であろう。
研究対象はAl-Si合金である。今後の研究では、他のアルミニウムシリコン合金組成や、より広範囲の鋳造パラメータ、例えば鋳造温度や混合速度に対する鋳造距離の影響を調査することができる。異なる鋳造距離における凝固メカニズムと微細組織の進化をさらに調査することも有益であろう。
8. 参考文献:
- [1] 徐通,张宇飞,李咏凯. 高性能亚共晶铝硅合金的研究[J]. 材料研究与应用, 2017, 11(4): 236-239.
- [2] WU Y. Application of aluminum alloy in aircraft [J]. Journal of Physics, 2022, 2228(1): 12-24.
- [3] XU YJ, ZHAO DD, LI YJ. A thermodynamic study on the effect of solute on the nucleation driving force, solid-liquid interfacial energy, and grain refinement of Al alloys [J]. Metallurgical and Materials Transactions, 2018, A49: 1770-1781.
- [4] LIU B, KANG J, YANG X, et al. Effects of hollow sand mold on the microstructure and mechanical properties of a low pressure aluminum alloy casting [J]. Journal of Materials Research and Technology, 2024, 28: 4488-4497.
- [5] 丁俭,靳子惠,杜喜望,等. 添加A1-5Ti-B和A1-2Zr-Er对铸态铝锌镁合金力学性能的影响[J]. 材料科学与工艺, 2017, 25(2): 39-44.
- [6] 李安庆,张立华,蒋日鹏,等. 冷却速度及超声振动协同作用对7085铝合金凝固组织及力学性能的影响[J]. 材料工程, 2021, 49 (8): 63-71.
- [7] 余柯培,沈利,麻永林,等. 电磁能对ZL102铝合金凝固组织的影响[J]. 内蒙古科技大学学报, 2019, 38(1): 18-21.
- [8] 彭洪美,李晓谦,蒋日鹏. 熔体超声处理对7050铝合金铸锭微观偏析的影响[J]. 北京理工大学学报, 2016, 36(11): 1105-1110.
- [9] 李夏,李元东,马颖,等. 混合方式对受控扩散凝固过共晶 Al-Si 合金初生硅相的影响[J]. 中国有色金属学报, 2011, 21(12): 3033-3041.
- [10] LI YD, HU SH, LI X. Study on hypereutectic Al-Si alloy fabricated by liquid-liquid mixing [J]. Advanced Materials Research, 2013, 815:13-18.
- [11] POURGHARIBSHAHI M, DIVANDARJ M, LARIJANI H S, et al. Controlled diffusion solidification processing: A review [J]. Journal of Materials Processing Technology, 2017, 250 (1): 203-219.
- [12] CHEN TJ, YANG XK, XUE H, et al. Mixing process and nucleation of an Al-Si alloy during controlled diffusion solidification with modified and effect of melt mass [J]. Journal of Materials Science, 2022, 57: 3018-3040.
- [13] XUE H, CHEN TJ. Effect of mixing temperature on microstructure of an Al-Si alloy prepared by controlled diffusion solidification [J]. China Foundry, 2023, 20(3): 241-252.
- [14] LIU YH, CHEN TJ. Effect of standing time after mixing on the mixture microstructure of an Al-Si alloy during controlled diffusion solidification with modified [J]. Metals, 2023, 13(4): 733-740.
- [15] KHALAF A A. Studying of non-dendritic microstructure forming in controlled diffusion solidification [J]. International Journal of Metal Casting, 2022, 16(1): 223-233.
9. 著作権:
- この資料は、"[LI Shaosi, CHEN Tijun]"の論文:「[Influence of Casting Distance on Microstructure of Simultaneously Mixed Controlled Diffusion Solidified Al-Si Alloys]」に基づいています。
- 論文ソース: DOI: 10.15980/j.tzzz.T20240050
この資料は上記論文を紹介するために作成されたものであり、商業目的での無断使用は禁止されています。
Copyright © 2025 CASTMAN. All rights reserved.