この論文の要約は、['Paper Title:General manufacturing route for medical devices']と題された論文を、['Publisher:Metallic Biomaterials Processing and Medical Device Manufacturing, Elsevier Ltd.']にて発表された論文に基づいて作成されています。
1. 概要:
- タイトル: General manufacturing route for medical devices
- 著者: Yu Sun, Sen Yu and Gui Wang
- 出版年: 2021年
- 出版ジャーナル/学会: Metallic Biomaterials Processing and Medical Device Manufacturing, Elsevier Ltd.
- キーワード: Manufacturing process, medical devices, metal industry, casting, forming, heat treatment, joining, titanium alloys
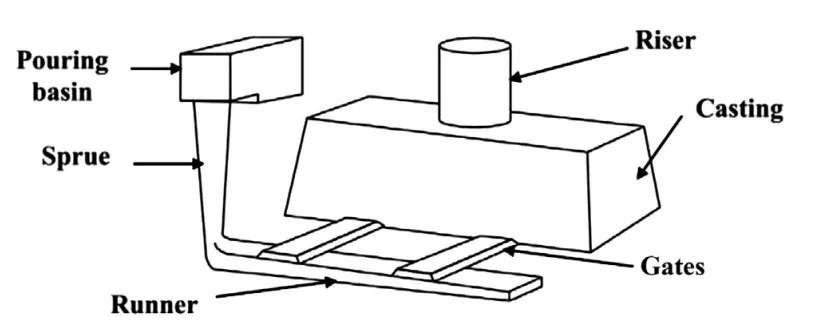
2. 研究背景:
研究トピックの背景:
製造業は第二次産業の本質であり、原材料を最終製品に変換します。医療機器産業は、単純な外科用器具から複雑な医療システムまで、幅広い製品を製造するために多岐にわたる製造プロセスを利用しています。これらのプロセスは、生体材料から部品を製造するために金属産業から応用されています。現代の製造業には、製品設計から部品統合までのすべての中間プロセスが含まれています。
既存研究の現状:
金属産業では、製造ルートは通常、溶融金属を凝固させ、次に機械的に成形することを含みます。熱と塑性変形は、金属の機械的特性に大きな影響を与えます。製造プロセスの背後にある科学を理解することは、高品質で経済的な部品を製造し、特に金型設計と鋳造の実践において効果的な技術を確立するために不可欠です。
研究の必要性:
この章では、医療機器の主要な製造プロセス、特に原材料から一次形状までのルートに焦点を当てています。鋳造、成形、熱処理、接合を強調し、医療機器分野における品質と費用対効果の高い生産に不可欠な基礎科学原理を解説します。チタン合金の主要な製造加工の詳細な例も含まれています。
3. 研究目的と研究課題:
研究目的:
この章の目的は、医療機器の一般的な製造ルート、特に金属加工に焦点を当てて解明することです。医療機器の製造に関連する鋳造、成形、熱処理、接合などの主要な製造プロセスについて、ハンドブックレベルの理解を提供することを目指しています。
主な研究内容:
この章で取り上げる主な研究分野は以下のとおりです。
- 金属鋳造の基礎とプロセス、金属の流れ、凝固、欠陥形成など。
- 金属成形プロセス、圧延、鍛造、押出し、引抜き、および温度の影響を含む。
- 熱処理方法とその微細構造と特性への影響。
- 医療機器製造における材料接合のための溶接技術。
- チタン合金チューブおよびワイヤの特定の製造プロセス。
研究仮説:
ハンドブックの章であるため、研究仮説は明示的に述べられていません。しかし、根底にある前提は、これらの製造プロセスを十分に理解することが、金属生体材料から高品質の医療機器を製造するために不可欠であるということです。
4. 研究方法
研究デザイン:
この章では、記述的かつ解説的なアプローチを採用し、金属材料から医療機器を製造する際に伴う基本的な原理とプロセスを概説しています。さまざまな製造技術の構造化された概要を提供し、金属鋳造と成形に焦点を当てています。
データ収集方法:
この章では、材料科学および製造工学における既存の知識と原理を統合しています。この分野で確立された理論と実践に基づいて、製造ルートを記述および説明しています。
分析方法:
この章では、記述的分析手法を用いて、複雑な製造プロセスを基本的なステップと原理に分解しています。鋳造における凝固(Fig. 3.2)、鋳造中の収縮(Fig. 3.5)、熱間圧延中の微細構造の進化(Fig. 3.11)など、主要な概念とメカニズムを説明するために図と例を使用しています。
研究対象と範囲:
この章の範囲は、医療機器の一般的な製造ルートに焦点を当てており、特に金属鋳造、金属成形、熱処理、溶接を取り上げています。主な対象は、金属生体材料と、それらを医療部品に成形するために使用される製造プロセスです。この章には、例示材料としてチタン合金に焦点を当てた具体的な内容も含まれています。
5. 主な研究成果:
主な研究成果:
- 金属鋳造: 製造プロセスとしての金属鋳造の詳細な説明。流体流動(流動性、注湯温度、ゲートシステム)、凝固(核生成、結晶成長、結晶粒組織)、熱伝達、鋳造欠陥の形成(収縮、偏析)などの基礎を網羅しています。インベストメント鋳造やインゴット鋳造などのさまざまな鋳造プロセスについて説明しています (Fig. 3.7, Fig. 3.8, Fig. 3.9)。
- 金属成形: 圧延(平圧延、異形圧延、リング圧延、ねじ圧延)、鍛造(型鍛造、自由鍛造)、押出し(正押出し、逆押出し、横押出し)、引抜きなど、金属成形プロセスの包括的な概要。温度(冷間、温間、熱間加工)が金属成形に及ぼす影響について説明しています (Fig. 3.10, Fig. 3.11, Fig. 3.12, Fig. 3.13, Fig. 3.14, Fig. 3.15, Fig. 3.16, Fig. 3.17, Fig. 3.18, Fig. 3.19, Fig. 3.20, Fig. 3.21)。
- 熱処理: 熱処理プロセス(焼ならし、焼なまし、焼入れ、焼戻し)と、金属材料の微細構造と特性に及ぼす影響について説明しています (Fig. 3.22, Fig. 3.23)。
- 溶接: 接合プロセスとしての溶接の説明。溶融溶接、溶接ゾーン(母材、溶接金属、HAZ)、溶接品質に影響を与える要因など (Fig. 3.24, Fig. 3.25)。チタンチューブの溶接に関する具体的な考慮事項を提供しています。
- チタン合金加工: チタン合金チューブおよびワイヤの特定の製造ルートについて説明しています。チューブの押出し(穿孔押出し、後方絞り)と圧延、ワイヤの引抜きなど (Fig. 3.26, Fig. 3.27, Fig. 3.28, Fig. 3.29)。
データ解釈:
- 鋳造における流動性: 流動性は、粘度、表面張力、凝固パターンによって決まります。より高い過熱度と金型表面特性は、金属の流動能力に影響を与えます。
- 凝固と結晶粒組織: 凝固は核生成と結晶成長を介して発生し、鋳造特性に影響を与える結晶粒組織につながります。冷却速度はデンドライト構造に影響を与えます (Fig. 3.4)。
- 収縮と気孔率: 凝固中の収縮は気孔率につながる可能性があり、鋳造設計と指向性凝固によって軽減できます。Table 3.1 は、金属の凝固収縮を示しています。
- 成形における温度: 温度は金属成形に大きな影響を与えます。冷間加工は強度を高めますが延性を低下させ、熱間加工は動的再結晶により大きな形状変化を可能にします (Fig. 3.11)。
- 熱処理効果: 焼なまし、焼ならし、焼入れ、焼戻しなどの熱処理プロセスは、微細構造や硬度、強度などの機械的特性を修正するために使用されます (Fig. 3.23)。
- 溶接ゾーン: 溶融溶接は、微細構造と特性が異なる明確なゾーン(母材、溶接金属、HAZ)を作成します。溶接パラメータと材料特性は、HAZ の特性に影響を与えます (Fig. 3.24)。
図の名前リスト:
- Figure 3.1 Schematic illustration of a typical riser-gated casting.
- Figure 3.2 (A) Illustration of solidification and temperature distribution in the solidifying metal and (B) a well-developed dendritic structures casting.
- Figure 3.3 grain structure of as cast meta ls (A) a pure zinc showing typical combination of columnar grains from the mold wall and equiaxed grains in the center, (B) as cast grain for magnesium can be refined by adding an inoculant (C) during the casting process.
- Figure 3.4 (A) Temperature distribution during the casting solidification and (B) coarse dendritic structures with large spacing between dendrite arms result from a slow cooling rate.
- Figure 3.5 illustration of three-stage shrinkage during casting.
- Figure 3.6 Schematic of (A) microsegregation, (B) typical macrosegregation pattern in a steel ingot.
- Figure 3.7 Classification of casting processes.
- Figure 3.8 The investment-casting process.
- Figure 3.9 Schematics of an ingot casting process and development of typical grain structures.
- Figure 3.10 The schematic diagram for stress-strain curve of a low-carbon steel.
- Figure 3.11 Schematic illustration of microstructure evolution during the hot rolling process.
- Figure 3.12 Grain structure comparison between a machined and rolled bolt.
- Figure 3.13 Schematic illustration of rolling process.
- Figure 3.14 Closed-die forging with flash. (A) Schematic diagram with flash terminology. (B) Forging sequence in closed-die forging of connecting rods.
- Figure 3.15 Open-die forging.
- Figure 3.16 The basic principles of metal extrusion.
- Figure 3.17 The relationship between force and displacement for positive and reverse extrusion.
- Figure 3.18 Process of drawing.
- Figure 3.19 Schematic showing the mechanism of straight-knife shearing.
- Figure 3.20 Bending in the V-die.
- Figure 3.21 Progression of metal flow in drawing a cup from a flat blank.
- Figure 3.22 1 Local magnification of iron-carbon phase diagram.
- Figure 3.23 Schematic diagram of the main annealing processes: (A) deformed state, (B) recovered, (C) partially recrystallized, (D) fully recrystallized, (E) grain growth, and (F) abnormal grain growth.
- Figure 3.24 Features of a typical fusion-weld zone in arc welding.
- Figure 3.25 Grain structure in (A) a deep weld and (B) a shallow weld; note that the grains in the solidified weld metal are perpendicular to their interface with the base metal. (C) Weld bead on a cold-rolled nickel strip produced by a laser beam. (D) Microhardness (HV) profile across a weld bead.
- Figure 3.26 Schematic diagram of solid ingot perforation and extrusion process.
- Figure 3.27 Schematic diagram of pipe reverse extrusion.
- Figure 3.28 Schematic diagram of the working principle of skew rolling perforating machine.
- Figure 3.29 Principle of high-pressure hot gas forming.
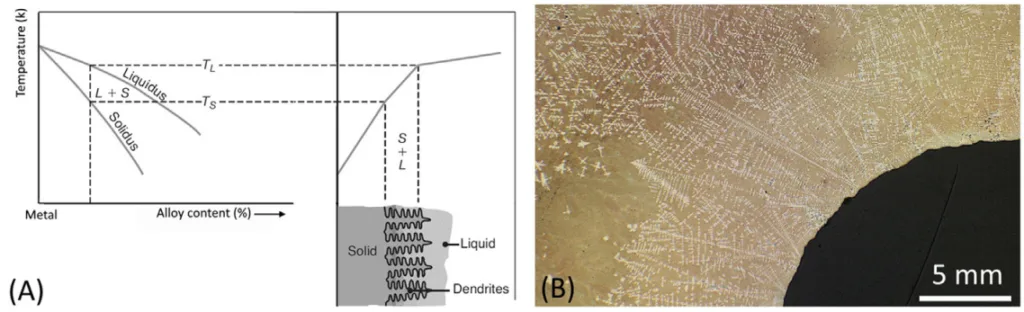
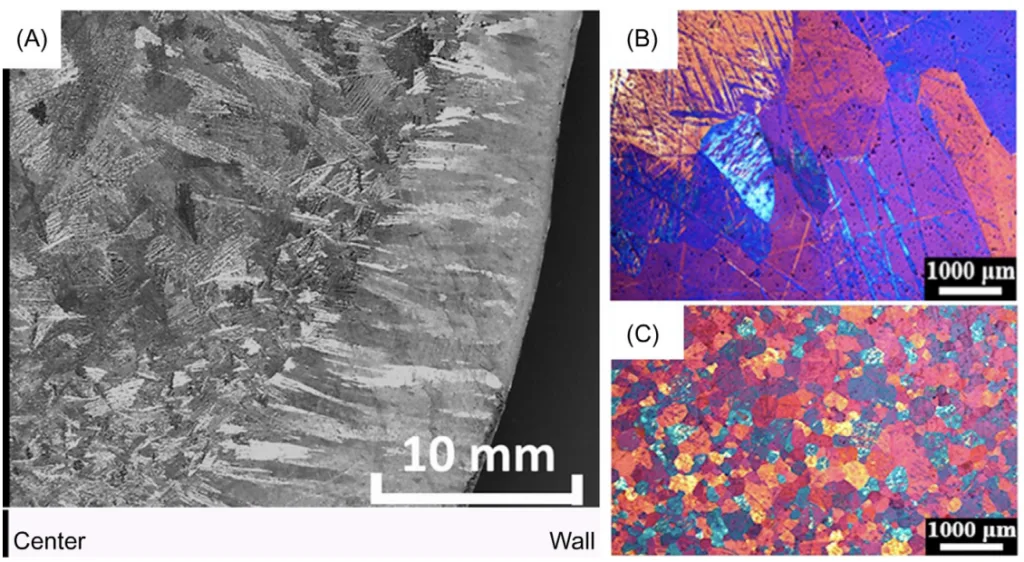
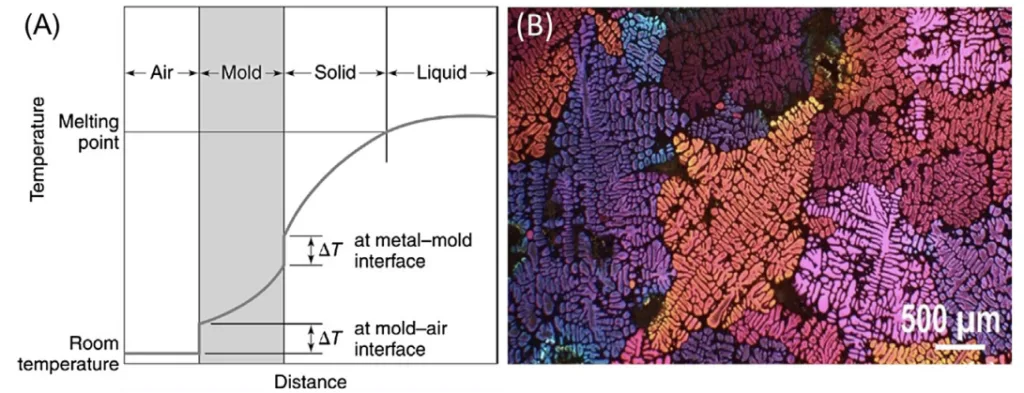

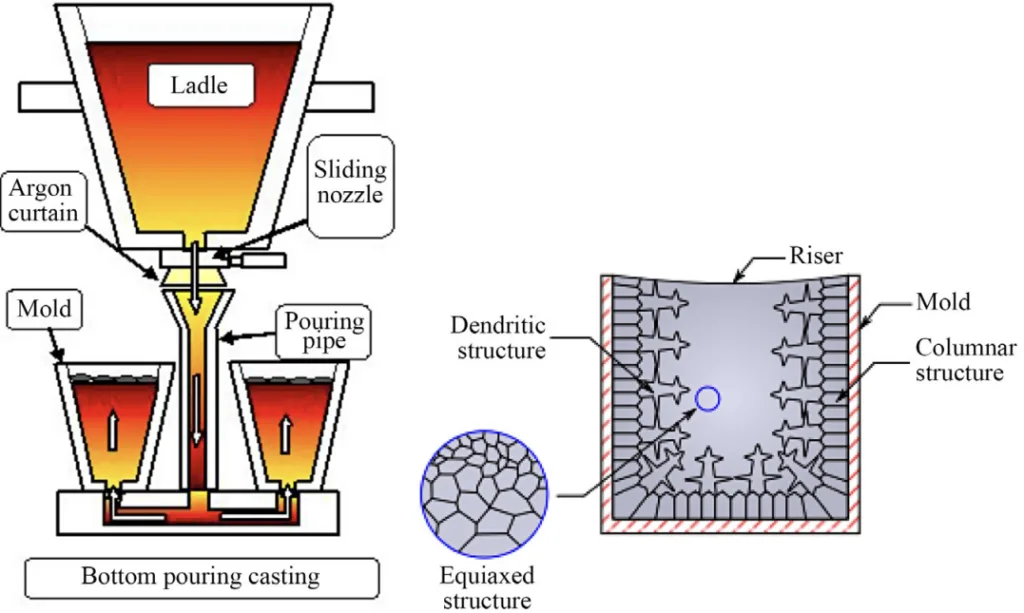
6. 結論:
主な研究成果の要約:
この章では、医療機器の一般的な製造ルートの包括的な概要を提供し、金属鋳造、成形、熱処理、溶接に焦点を当てています。各製造技術の基本原理、プロセス、および影響要因について詳しく説明しています。チタン合金加工などの具体的な例は、医療機器製造におけるこれらの方法の実用的な応用を示しています。この章では、目的とする製品の品質と性能を達成するために、材料の挙動とプロセスパラメータを理解することの重要性を強調しています。
研究の学術的意義:
この章は、医療機器製造および材料科学の分野の専門家や研究者にとって貴重なリソースとして役立ちます。さまざまな製造プロセスに関する重要な知識を統合し、この分野における理解とさらなる研究のための構造化されたフレームワークを提供します。各プロセスの根底にある科学的原理を強調し、製造冶金学のより深い理解を促進します。
実際的な意義:
医療機器業界の実務家にとって、この章は、金属部品の製造プロセスを選択および最適化するための実用的なガイダンスを提供します。プロセスのパラメータ、欠陥制御、材料の選択に関する洞察を提供し、高品質で信頼性の高い医療機器の製造を支援します。鋳造、成形、熱処理、溶接技術の詳細な説明は、プロセス設計と改善のための基礎を提供します。
研究の限界
ハンドブックの章として、広範な概要を提供し、非常に具体的または最先端の研究トピックには深く立ち入っていません。各プロセスの網羅性は、1つの章の範囲によって制限されています。各製造方法の網羅的な研究というよりも、入門書および参考点として役立ちます。
7. 今後のフォローアップ研究:
- 今後のフォローアップ研究の方向性
今後の研究では、鋳造または成形とアディティブマニュファクチャリングの統合、特定の生体材料に対する新規な熱処理戦略、医療機器における異種金属接合のための高度な溶接技術など、議論された各製造プロセス内の高度なバリエーションと最適化を探求することができます。 - さらなる探求が必要な分野
さらなる探求が必要な分野には、医療機器製造におけるインダストリー4.0技術の応用、これらのルートを使用して加工された材料の生体適合性と長期性能に関する詳細な研究、および医療機器産業向けの持続可能で費用対効果の高い製造ソリューションの開発が含まれます。
8. 参考文献:
- J. Campbell, Casting, second ed., Elsevier, Butterworth-Heinemann, 2003.
- B. Cantor, K. O'Reilly, Solidification and Casting, CRC Press, 2002.
- K. Serope, S.R. Schmid, Manufacturing Engineering and Technology, seventh ed., P&C ECS, 2013.
- K.R. Ravi, R.M. Pillai, K.R. Amaranathan, B.C. Pai, M. Chakraborty, Fluidity of aluminum alloys and composites: a review, J. Alloy. Compd. 456 (2008) 201–210.
- P.R. Beeley, R.F. Smart, Investment Casting, Maney Publishing for IOM3, the Institute of Materials, Minerals and Mining, 1995.
- J. Campbell, Complete Casting Handbook Metal Casting Processes, Metallurgy, Techniques and Design, second ed., Elsevier, 2015.
- F. Herlach, Solidification and Crystallization, John Wiley & Sons, 2004.
- C. Beckermann, Macrosegregation, ASM Handbook, Volume 15: Casting, ASM Handbook Committee, 2008, pp. 348-352. https://doi.org/10.1361/asmhba0005216.
- R. Mehrabian, M. Keane, M.C. Flemings, Interdendritic fluid flow and macrosegregation; influence of gravity, Metall. Trans. 1 (1979) 1209–1220.
- H. Fredriksson, U. Åkerlind, Materials Processing During Casting, John Wiley & Sons Ltd, 2012.
- T. Altan, G. Ngaile, G. Shen, Cold and Hot Forging: Fundamentals and Applications, ASM International, 2004.
- T.A. Perkins, T.J. Kronenberger, J.T. Roth, Metallic forging using electrical flow as an alternative to warm/hot working, J. Manuf. Sci. Eng 129 (2007) 84–94.
- M. Spittel, T. Spittel, Metal Forming Data of Ferrous Alloys - Deformation Behaviour, Springer, Berlin Heidelberg, 2009.
- J.L. Duncan, Geometric and Mechanics Models of Sheet Forming Processes, Elsevier Inc, 2002.
- K. Styles, A. Bichard, Working Drawings Handbook, Taylor and Francis, 2012.
- C.N.A. Kumar, R. Deivanathan, Effect of aluminium alloy and mild steel on the productivity in sheet metal forming processes, Appl. Mech. Mater 234 (2012) 64–68.
- S.C. Babu, V.S.S. Kumar. 2012. Experimental studies on incremental forming of stainless steel AISI 304 sheets. Proc. IMechE Part B J. Eng. Manufacture 226 (7) 1224-1229.
- W.H. Sillekens, G. Kurz, R.J. Werkhoven, Magnesium forging technology: state-of-the-art and development perspectives, in: L. Katgerman, F. Soetens (Eds.), 11th International Aluminium Conference - INALCO 2010 New Frontiers in Light Metals, IOS Press © 2010 The authors and IOS Press, 2010.
- Z. Feng, L. Chai, Z. Chen, T. Jin, G. Shi, Y. Jin, et al., Forging technology and microstructure and mechanical properties of a novel high temperature titanium alloy resistant to 650°C, in: Y. Han (Ed.), High Performance Structural Materials. CMC 2017, Springer, 2018.
- T.P. Wang, K.M. Qi, Metal Plastic Processing-Rolling Theory and Process, Metallurgical Industry Press, 2001.
- M.P. Dixit, U.S. Dixit, Modeling of Metal Forming and Machining Processes, Springer, London, 2008.
- B.R. Song, Rolling Technology, Metallurgical Industry Press, 2014.
- H. Tschaetsch, Extrusion, Metal Forming Practise, Springer, Berlin, Heidelberg, 2006.
- L. Katgerman, F. Soetens, A.R. Eivani, A.J. den Bakker, J. Zhou, J. Duszczyk, An Investigation of Dynamic Recrystallization During Hot Extrusion of Al-4.5Zn-1Mg Alloy, IOS Press, 2010.
- Dorel Banabic, Advanced Methods in Material Forming, Springer,, Berlin, Heidelberg, 2007.
- George E. Totten, Steel Heat Treatment, Taylor and Francis, 2006.
- M.I. Khan, Welding Science and Technology, New Age International, 2007.
- B.K. Choudhary, J. Christopher, D.P. Rao Palaparti, E. Isaac Samuel, M.D. Mathew, Influence of temperature and post weld heat treatment on tensile stress-strain and work hardening behaviour of modified 9Cr-1Mo steel, Mater. Des 52 (2013) 58-66.
- K.E. Thelning, Steel and Its Heat Treatment, Butterworth-Heinemann, 2013.
- R.M. Mahamood, E.T. Akinlabi, Non-contact welding technologies: fusion welding, Advanced Noncontact Cutting and Joining Technologies. Mechanical Engineering Series, Springer, Cham, 2018.
- R. Timings, Fabrication and Welding Engineering, Taylor and Francis, 2008.
- P.T. Houldcroft, R. John, Welding and Cutting: A Guide to Fusion Welding and Associated Cutting Processes, Elsevier, Woodhead Publishing, 2001.
- R.W. Messler, Welding as a Joining Process, Elsevier Inc, 2004.
- G.F. Deyev, Surface Phenomena in Fusion Welding Processes, Taylor and Francis, 2010.
- V.Y. Osadchy, A.S. Vavilin, V.G. Zimovec, A.P. Kolikov, The technology and equipment of the pipe production, internet engineering, Moscow, 2002 (in Russian).
- S.B. Bodlani, S.C.K. Yuen, G.N. Nurick, The energy absorption characteristics of square mild steel tubes with multiple induced circular hole discontinuities-part 1: experiments, J. Appl. Mech 76 (2009) 041012.
- S.D. Hu, B. Ye, L.X. Li, Materials properties of thick-wall cold-rolled welded tube with a rectangular or square hollow section, Constr. Build Mater 25 (2011) 2683-2689.
- R.S. Saluja, V. Singh. 2019. Subjective factors consideration in the selection of welding technique for welded tube manufacturing. In: R. Narayanan, S. Joshi, U. Dixit (Eds.). Advances in Computational Methods in Manufacturing. Lecture Notes on Multidisciplinary Industrial Engineering, Springer, Singapore.
- A. Kumar, M. Sapp, J. Vincelli, M.C. Gupta, A study on laser cleaning and pulsed gas tungsten arc welding of Ti-3Al-2.5V alloy tubes, J. Mater. Process Tech. 210 (2009) 64-71.
- A. Kumar, Mool C. Gupta, Surface preparation of Ti-3Al-2.5V alloy tubes for welding using a fiber laser, Opt. Lasers Eng 47 (2009) 1259–1265.
- B. Ren, G. Tao, P. Wen, C. Du, Study on weldability window and interface morphology of steel tube and tungsten alloy rod welded by explosive welding, Int. J. Refractory Met. Hard Mater 84 (2019) 105005.
- H. Pan, Z. Wang, Y. Hui, C. Yang, X. Deng, C. Bao, Product Design and Production Practice of 700MPa High Strength Hot Rolled Strip for Auto Axle Tube, Springer International Publishing, 2016.
- S. Yuan, Development and trends in internal high pressure forming, Metal Form. Technol. 21 (4) (2003) 32-34.
- R. Neugebauer, A. Sterzing, F. Schieck. Opportunities for progressive applications by means of integrating and combining various technologies with hydroforming, Tube Hydroforming Technology-Proceedings Tubehydro, Harbin, 2007, pp. 65-69.
- X. Long, L. Shuyu, A new type of rod and tubular high-power ultrasonic-focused radiator, J Nanjing Univ. (Nat. Sci.) 05 (2012) 544-552.
- H. Hosseinabadi, S.S.A. Goodarzi, A coupled stream function-finite element analysis for wire drawing processes, Int. J. Adv. Manuf. Technol 57 (2011) 917–926.
9. 著作権:
- この資料は "Yu Sun, Sen Yu and Gui Wang" の論文: "General manufacturing route for medical devices" に基づいています。
- 論文ソース: https://doi.org/10.1016/B978-0-08-102965-7.00003-5
この資料は上記の論文に基づいて要約されたものであり、商業目的での無断使用は禁止されています。
Copyright © 2025 CASTMAN. All rights reserved.