この技術概要は、Dirk Lehmhus、Christoph Pille、Dustin BorheckらがGiesserei(2018年)に発表した学術論文「Leakage-free cooling channels for Die-cast housing components」に基づいています。これは、CASTMANの専門家がGemini、ChatGPT、GrokなどのLLM AIの支援を受け、HPDC専門家のために分析・要約したものです。
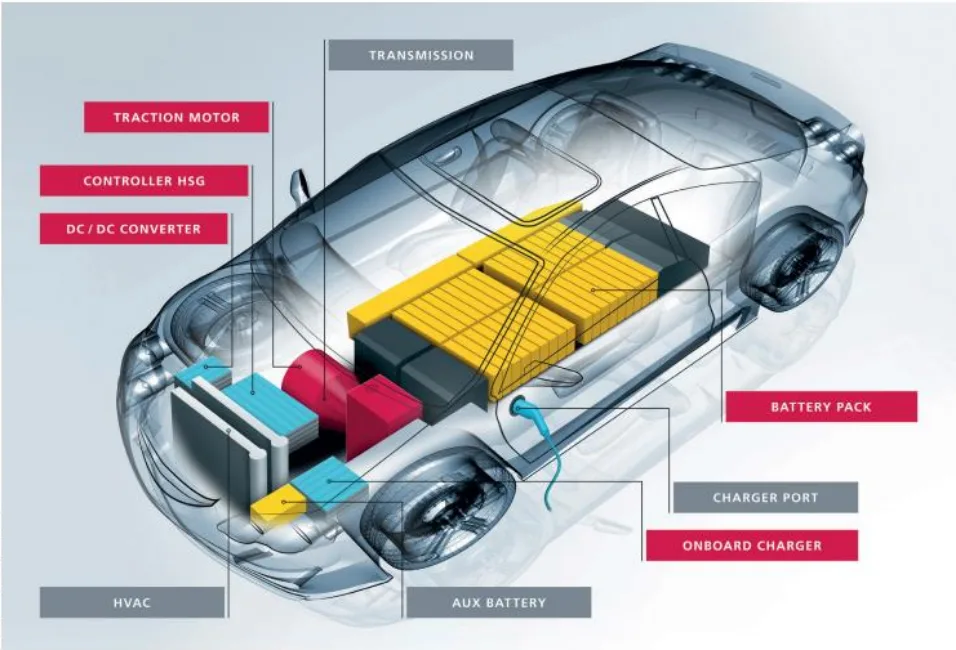
キーワード
- 主要キーワード: ダイカスト冷却チャネル
- 副次キーワード: Eモビリティ向けHPDC、ZLeakチューブ技術、ダイカスト熱管理、鋳造シミュレーション(WinCast)、アルミニウムチューブインサート、電気モーターハウジング鋳造、ダイカスト熱伝達係数
エグゼクティブサマリー
- 課題: Eモビリティの台頭は、バッテリーやモーターなどのコンポーネントに対する高度な熱管理を要求しています。チューブの潰れや高価な複数部品の組み立てに頼ることなく、複雑で漏れのない冷却チャネルを一体型高圧ダイカスト(HPDC)ハウジングに統合することは、主要な製造上の障壁でした。
- 手法: 「CoolCast」プロジェクトの研究者たちは、安定化および除去が可能な二層式充填材を備えた特殊なアルミニウムチューブインサートである「ZLeakチューブ」技術について広範な試験を実施しました。彼らは様々な合金、肉厚、HPDCプロセスパラメータをテストし、物理的な実験と高度なWinCast expert鋳造シミュレーションの両方を用いて結果を分析しました。
- 画期的な成果: この研究は、ZLeakチューブ技術がHPDC用途において実現可能であるだけでなく、非常に高い予測可能性を持つことを成功裏に証明しました。決定的に重要なのは、鋳造シミュレーションがパイプの圧縮と変位を正確にモデル化できることであり、これにより設計者は金型を製作する前に、堅牢で複雑な冷却経路を設計し、金型とプロセスを最適化することが可能になります。
- 結論: この研究は、複雑な統合冷却システムを持つ一体型ダイカストコンポーネントを製造するための強力で新しい方法を検証するものです。これは、次世代の電気自動車に不可欠な、高性能で熱的に最適化された部品を製造するための、明確でデータに基づいた道筋を提供します。
課題:この研究がHPDC専門家にとって重要な理由
自動車産業がEモビリティへとシフトするにつれて、効果的な熱管理が最重要課題となっています。バッテリーパック、パワーエレクトロニクス、トラクションモーターなどの主要コンポーネントはかなりの熱を発生させ、最適な性能と寿命を維持するために高度な冷却が必要です(初期画像参照)。高圧ダイカスト(HPDC)は、これらのコンポーネントが必要とする軽量で複雑なハウジングを製造するのに理想的なプロセスですが、内部冷却チャネルの統合は常に大きな課題でした。
何十年もの間、エンジニアはもどかしい限界に直面してきました。補強されていない標準的なアルミニウムチューブを鋳込もうとすると、溶融金属の莫大な圧力と熱で潰れてしまうことがよくあります(Image 1参照)。代替の解決策には、それぞれ独自の欠点があります。
- 2ピースハウジング: 追加の金型、複雑な接合およびシールプロセスが必要で、接合部での熱応力に弱く、コストと潜在的な故障箇所を増加させます。
- 鋼管インサート: 鋳造プロセスには耐えられますが、アルミニウム鋳物との熱膨張の不一致を引き起こし、隙間の形成、熱伝達の低下、潜在的な腐食問題につながります。
この研究は、一体型ダイカスト部品内に幾何学的に複雑で漏れのない冷却チャネルを直接作成し、性能と経済効率を両立させる新しいアプローチを検証することで、この重要な産業ニーズに対応します。
アプローチ:方法論の解明
この課題に取り組むため、「CoolCast」プロジェクトでは、チューブ技術の開発者であるMH Technologies、ダイカスト専門企業のae group ag、金型メーカーのSchaufler Tooling GmbH、シミュレーション専門企業のRWP GmbH、そしてFraunhofer IFAMが協力し、業界のリーダーたちが集結しました。
研究の中心となったのは、特許取得済みのZLeakチューブ技術です。この革新的なアプローチは、水溶性の外層と、粗粒で媒体が浸透可能な内層コアからなる、独自の二層式コアで満たされたアルミニウムチューブインサートを使用します(Image 2参照)。この充填材は、HPDCプロセスに耐えるために必要な構造的安定性を提供し、後で簡単に洗い流すことができます。
研究チームは、Bühler-SC/N-66ダイカストマシンを使用して厳密な実験プログラムを実施しました。彼らは特殊な金型(Image 3参照)で様々なチューブインサートをテストし、主要なパラメータを変化させました。
- パイプ材質: アルミニウム合金EN AW-6063およびEN AW-3003
- パイプ形状: 外径12mm、肉厚1mm、1.5mm、2mm
- プロセスパラメータ: 600~1200 barの鋳造圧力、2.5~4.5 m/sの鋳造ピストン速度、室温~200°Cのパイプ予熱温度
物理的な試験と並行して、チームはWinCast expertシミュレーションソフトウェアを使用して、金型充填、凝固、熱応力をモデル化しました。シミュレーション結果は、溶湯流れの進行を検証するための断続ショット(interrupted shot)テストを含む実験データと比較して検証されました(Image 4参照)。
画期的な成果:主要な研究結果とデータ
この研究により、この技術の産業応用における実現可能性と予測可能性を示す、いくつかの重要な発見が得られました。
- 発見1:パイプの圧縮は予測可能で圧力に依存する。 実験により、最大鋳造圧力とチューブの圧縮(内径の減少)との間に、ほぼ線形の関係があることが明らかになりました。Image 5に示すように、肉厚1mmのパイプは、1.5mmまたは2mmのパイプよりも大幅に圧縮されました。さらに、EN AW-3003合金チューブは、EN AW-6063製の同様のチューブよりも圧縮率が低く、材料選択の重要性を浮き彫りにしました。
- 発見2:変位は熱的影響と機械的制約によって引き起こされる。 予想に反して、再圧縮圧力が金型内のパイプの変位(移動)に与える影響は軽微でした。支配的な要因は、溶湯流れによる熱的影響と機械的なセットアップでした。Image 6に示すように、パイプを予熱することで変位が大幅に減少しました。パイプの一端に可動ベアリングを使用することも、位置ずれを緩和するのに効果的であることが証明されました。
- 発見3:シミュレーションは現実の挙動を正確にモデル化する。 このプロジェクトの重要な成果の1つは、鋳造シミュレーションの検証です。ソフトウェアは、パイプ内の任意の時点での温度-時間曲線を予測でき、最高温度が530°Cに達し、それに伴い材料強度が大幅に低下することを示しました(Image 7参照)。最も重要なのは、シミュレーションによって予測されたパイプの変位と、鋳造部品で実際に測定された変位との間に強い相関関係があったことです(Image 8参照)。これは、設計およびプロセスエンジニアリングのためのツールとしての信頼性を証明しています。
- 発見4:熱伝達は定量化および最適化が可能である。 カスタムのテスト装置(Image 9参照)を使用して、研究者たちはチューブと鋳物との間の熱伝達係数(HTC)を測定しました。Image 10の結果は、EN AW-6063の場合、HTCが再圧縮圧力とともに増加する傾向があり、EN AW-3003の値は一般的に高いことを示しています。この研究はまた、界面に微細な隙間が形成される可能性があることを認めており(Image 11, Image 13参照)、これが熱性能に影響を与え、さらなる最適化の余地がある領域であることを示しています。
HPDC製品への実用的な示唆
この研究は、先進的なダイカストコンポーネントに取り組むエンジニアや設計者にとって、直ちに適用可能な洞察を提供します。
- プロセスエンジニアへ: 研究結果は、プロセス制御のための明確な指針を提供します。パイプの圧縮は、予測可能な範囲内で再圧縮圧力を調整することで管理できます(Image 5参照)。パイプの移動を最小限に抑え、位置精度を確保するためには、圧力調整だけに頼るのではなく、インサートの予熱や溶湯流れの最適化といった熱管理戦略に焦点を当てるべきです(Image 6参照)。
- 品質管理チームへ: 検証済みのシミュレーションモデル(Image 8参照)は、強力な予測品質ツールです。仮想センサー(Image 7参照)を使用することで、エンジニアは最初の部品を鋳造する前に、パイプの測定困難な領域での熱条件を監視し、応力を予測することができ、時間とスクラップを削減できます。
- 金型設計者へ: この技術は設計者に新たな自由を与えます。直径の1.5倍という狭い曲げ半径のパイプを作成できる能力は、電気モーターハウジングの試作品で示されたように(Image 12参照)、非常に複雑で効率的な冷却チャネルレイアウトを可能にします。設計者は、予測可能なレベルのパイプ圧縮と変位をCADモデルに組み込むことで、最終部品がすべての幾何公差を満たすことを保証できます。
論文詳細
Leakage-free cooling channels for Die-cast housing components
1. 概要:
- タイトル (Title): Leakage-free cooling channels for Die-cast housing components
- 著者 (Author): DIRK LEHMHUS, CHRISTOPH PILLE, DUSTIN BORHECK, BREMEN, FELICIA BUMBU, THOMAS SCHWEGLER, LAI CHINGEN, JUSTIN LEE, JINHO YOO, IN CHEON, KOREA, PETER LUTZE, GERS TUNGEN AND REINHARD VOMHOF, KONRAD WEISS, ROETGEN
- 発行年 (Year of publication): 2018
- 掲載誌/学会 (Journal/academic society of publication): Giesserei
- キーワード (Keywords): Electro mobility, Die-cast, Cooling channels, Housing components, ZLeak Tube, Casting simulation
2. 要旨 (Abstract):
電気自動車コンポーネントの出力密度の増加は、高度な熱管理ソリューションを必要とします。本稿は、犠牲充填材を用いたアルミニウムチューブインサートである「ZLeakチューブ」技術を使用して、高圧ダイカスト(HPDC)コンポーネントに複雑な媒体輸送冷却チャネルを直接統合することの実現可能性を調査します。物理的な鋳造試験と数値シミュレーションの組み合わせを通じて、この研究は、鋳造圧力、ピストン速度、予熱などのプロセスパラメータが、チューブインサートの安定性、圧縮、および変位に与える影響を分析します。この研究は、この技術がHPDC条件下で安定しており、その挙動がシミュレーションツールを使用して予測可能であることを検証し、電気モーターやパワーエレクトロニクスハウジングなどの用途向けに、統合された漏れのない冷却機能を備えた一体型の軽量ハウジングの設計と製造への道を開きます。
3. 緒言 (Introduction):
Eモビリティの進歩は、新たな設計課題を提示しており、主な焦点は純粋な出力密度から熱条件の最適化へと移行しています。幾何学的に複雑な冷却チャネルは、バッテリー、パワーエレクトロニクス、モーター用のハウジングに製造プロセス中に統合されなければなりません。これには、性能と経済性を両立させる新しいコンセプトが必要です。支持されていないアルミニウムチューブを鋳込んだり、複数部品のハウジングを使用したりする従来の方法には、大きな欠点があります。本研究は、現代の電気駆動系の熱的要求を満たすために、一体型HPDCコンポーネントに統合冷却チャネルを作成する新しいアプローチを探求します。
4. 研究の概要 (Summary of the study):
研究テーマの背景:
熱管理は、電気自動車の数多くの組み立て品における重要な設計ポイントです。特にバッテリー素子、パワーエレクトロニクス、トラクションモーターでは、最適な温度を確保し、電力および容量の損失を防ぐために、熱放散を制御する必要があります。HPDCはこれらのハウジングを製造するための好ましい方法ですが、必要とされる中空チャネル構造を統合することは、大きな製造上の課題です。
従来の研究状況:
ハウジングに冷却チャネルを作成する従来のアプローチには、低圧または重力鋳造と砂中子(生産性の低下)、2ピースHPDCハウジング(高価、追加の加工および接合工程が必要)、鋼管の鋳込み(熱膨張の不一致)などがありました。油圧ラインにはチューブの鋳込みが使用されますが、冷却用に補強されていないアルミニウムチューブを使用することは、HPDCプロセスで安定していないため問題があります(Image 1参照)。Combicoreアプローチのような充填材ベースのコンセプトが存在し、本研究は代替の特許取得済み充填材技術に基づいています。
研究の目的:
「CoolCast」プロジェクトは、HPDC部品に冷却チャネルを作成するためのZLeakチューブ技術の使用を調査および検証することを目的としていました。主な目的は、プロセス限界を決定し、プロセスパラメータがパイプの圧縮および変形に与える影響を理解し、これらの効果を表現する鋳造シミュレーションの能力を検証し、結果として得られる冷却チャネルの応用関連特性を評価することでした。
中核的研究:
研究には、異なるアルミニウム合金(EN AW-6063, EN AW-3003)と肉厚で作られた直線および曲線状のZLeakチューブインサートを使用した鋳造実験が含まれていました。これらの実験は、鋳造圧力、ピストン速度、インサート予熱温度を変化させながらHPDCマシンで実施されました。得られた鋳造品は、パイプの圧縮と変位について分析されました。物理的な結果は、WinCast expertシミュレーションソフトウェアからの予測と比較されました。さらに、パイプと鋳物との間の熱伝達係数が実験的に決定されました。最後に、この知識は電気モーターハウジングに似たデモンストレーターコンポーネントに適用されました。
5. 研究方法論 (Research Methodology)
研究設計:
研究は、物理的な実験と数値シミュレーションを組み合わせました。単純なテスト形状(直線パイプ、Image 3a)から始め、より複雑な形状(曲線パイプ、Image 3b)、そして最終的に完全なデモンストレーターコンポーネント(Image 12)へと進む、多段階のプロジェクト構造が使用されました。これにより、プロセスパラメータと鋳造結果との間の相関関係を体系的に決定することができました。
データ収集および分析方法:
データは、鋳造部品のX線分析を通じてパイプの圧縮と変位を決定することにより、物理的な測定を通じて収集されました。プロセスデータ(圧力、速度)はダイカストマシンから記録されました。カスタムのテストリグ(Image 9)が、パイプと鋳物との間の熱伝達係数を測定するために構築されました。シミュレーションソフトウェアWinCast expertは、溶湯流れ、温度プロファイル、応力、変形に関する予測データを生成するために使用されました。実験データとシミュレーションデータは、定量的に比較されました(Image 8)。
研究テーマと範囲:
範囲には以下が含まれます:
- パイプ材質: EN AW-6063, EN AW-3003
- パイプ形状: 外径12mm、肉厚2mm, 1.5mm, 1mm
- 変化させたプロセスパラメータ: 鋳造圧力(600-1200 bar), ピストン速度(2.5-4.5 m/s), パイプ予熱(室温, 100°C, 200°C)
- パイプの圧縮、変位、熱伝達係数の分析
- 実験結果に対する鋳造シミュレーション予測の検証
- 螺旋状の冷却チャネルを持つデモンストレーターコンポーネントへの適用
6. 主な結果 (Key Results):
主な結果:
- パイプの圧縮は、最大鋳造圧力にほぼ線形的に依存し、EN AW-3003合金はEN AW-6063よりも少ない圧縮を示します(Image 5)。
- パイプの変位は、主に熱的要因(溶湯流れ、予熱温度)と機械的制約(ベアリングタイプ)に影響され、再圧縮圧力は軽微な影響しか与えません(Image 6)。
- WinCast expertによる鋳造シミュレーションは、充填中のパイプ温度(最大530°C)とパイプの最終的な変位を正確に予測し、予測エンジニアリングのためのその使用を検証します(Image 7, Image 8)。
- パイプと鋳物との間の熱伝達係数は測定可能であり、EN AW-6063の場合、再圧縮圧力とともに増加する傾向があります。界面での微細な隙間の存在が、熱伝達に影響を与える重要な要因です(Image 10, Image 11)。
- この技術は、螺旋状の冷却チャネルを持つデモンストレーター電気モーターハウジングに成功裏に適用され、複雑なコンポーネントの製造の実現可能性を証明しました(Image 12, Image 13)。
図のリスト (Figure Name List):
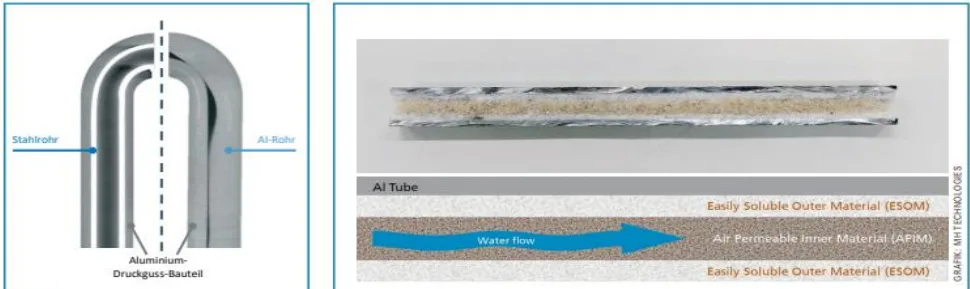
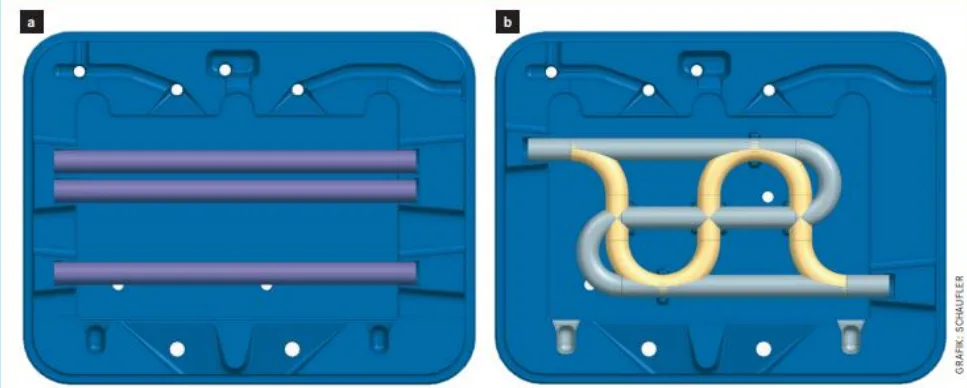
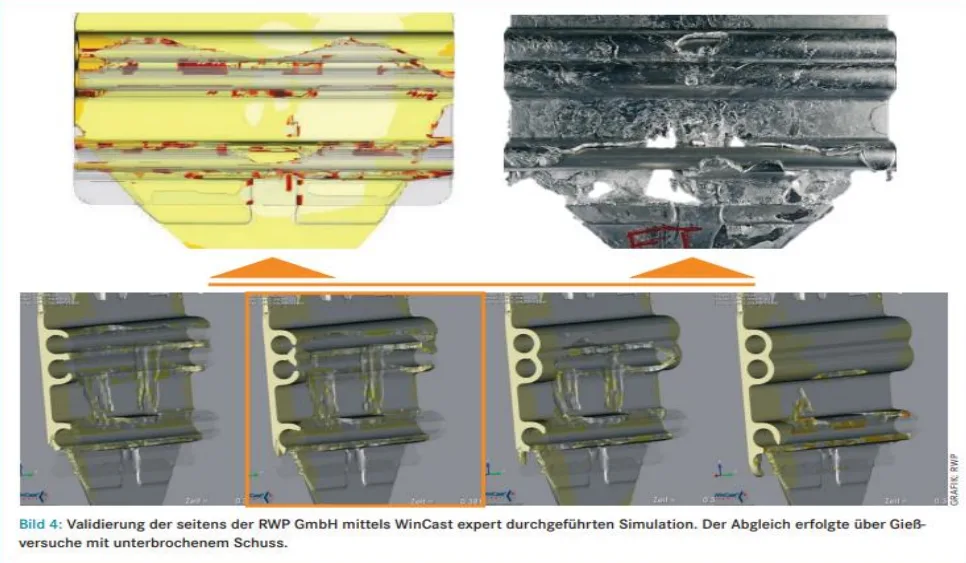
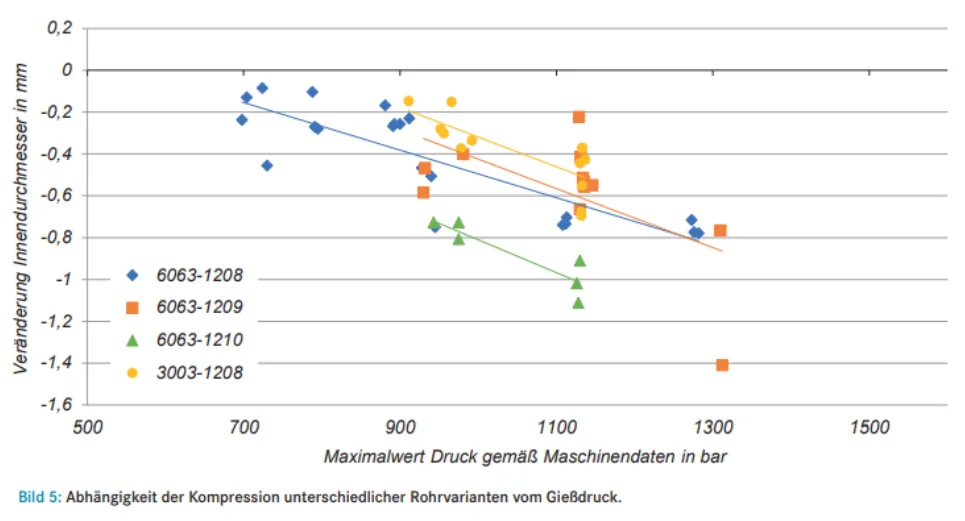
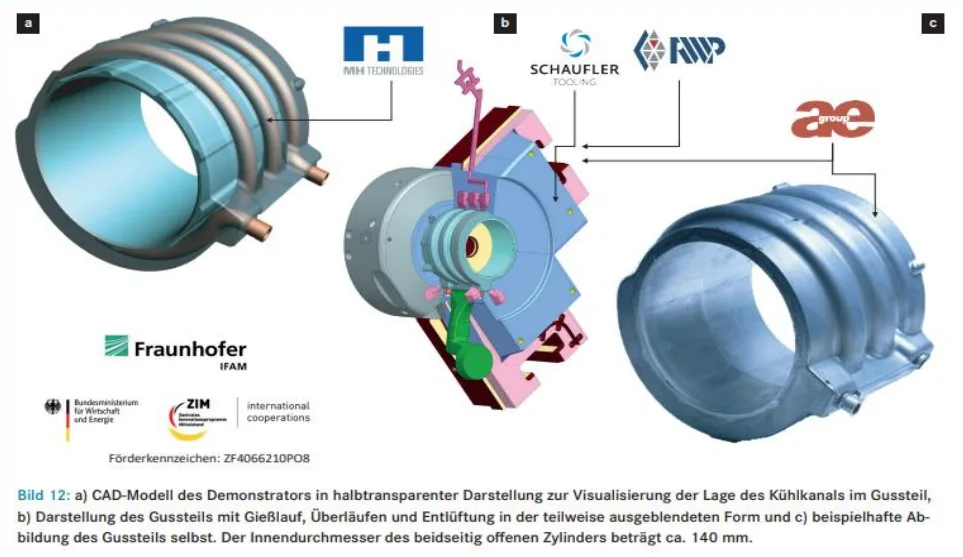
- Image 1: Pipes cast in for cooling engine components. The Steel pipe (left) withstands the manufacturing process; the aluminum tube (right) collapsed.
- Image 2: ZLeak Tube Technology: The two-component structure with a porous inner cross-section makes it much easier to remove the filler: a) Filled tube in cross section, b) a schematic representation of the principle of filler removal.
- Image 3: Mold inserts to determine the influence of different process parameters on stability, compression and deformation of ZLeak Tube pipes in the die casting process (developed and manufactured by Schaufler Tooling).
- Image 4: Validation of the simulation carried out by RWP GmbH using WinCast expert. The comparison was carried out using pouring tests with an interrupted shot.
- Image. 5: Dependency of the compression of different pipe variants on the casting pressure.
- Image 6: Dependence of the displacement of different pipe variants on the parameters or boundary conditions: a) recompression pressure, b) plunger speed, c) preheating temperature of the pipes, d) type of bearing.
- Image. 7: The simulation allows the determination of temperature-time curves for any position both in the cast part and in the depositors. In this specific case, temperatures of up to 530°C occur in the area of the pipe during the course of the mold filling and solidification, with a corresponding loss of strength.
- Image. 8: Comparison between the predicted and measured displacement of the pipe next to the gate under standard conditions, which is predicted by the casting simulation, meaning Pipe material EN AW-6063, wall thickness 2 mm (6063-1208), casting pressure nominal 800 bar, casting piston speed 2.5 m / s, temperature of mold and melt 220° C respectively 730 ° C, no preheating of the pipes, both side fixed bearing.
- Image. 9: Functional principle of the test setup for determining the heat transfer coefficient between pipe and casting. The embedded sketch illustrates which section of the casting was used for the measurements.
- Image. 10: Measurement results for the dependence of the heat transfer coefficient on the compression pressure, casting piston speed and preheating for the material variant EN AW-6063 and on the compression pressure for EN AW-3003.
- Image. 11: Problem of gap formation and its influence on the effective heat transfer coefficient.
- Image 12: a) CAD model of the demonstrator in a semi-transparent representation to visualize the position of the cooling channel in the casting, b) Representation of the cast part with pouring runner, overflows and ventilation in the partially hidden form and c) exemplary illustration of the cast part itself. The inner diameter of the cylinder, which is open on both sides, is approx. 140 mm.
- Image 13: CT-shot of the demonstrator with clearly visible gap between pipe and cast (compare enlarged detail on the right). The embedded picture shows the position of the cutting plane.
7. 結論 (Conclusion):
CoolCastプロジェクトの結果は、ダイカストにおけるZLeakチューブ技術の実現可能性と予測可能性を証明しています。この新しいソリューションは、ダイカストコンポーネントにアルミニウムチューブベースの媒体輸送チャネルを実装するために使用でき、精密な温度制御を必要とする電気駆動系の中心部品の製造に有望な展望を開きます。パイプは最大1200 barの再圧縮圧力まで安定しています。直径のわずかな減少とパイプの熱的移動は、鋳造シミュレーションによって正確に予測でき、したがって部品設計に反映させることができます。この技術は設計者により大きな自由を与え、材料の節約とより大きな冷却チャネル直径を可能にします。チャネルと鋳物との間の熱的接続についてはさらなる最適化が可能ですが、この技術はすでに目標要件を満たしており、Eモビリティ用途におけるHPDCの魅力を高めています。
8. 参考文献 (References):
- [1] Giesserei 105 (2018), [No.3], pp. 32-37
- [2] Heiselbetz, C.; Feikus, F. J.; Kniewallner, L.; Rafetzeder, M.; Luszczak, M. Challenges posed by E-Drive components:Casting solutions. Conference fee Casting technology in engine construction 2017, 01.-02. February 2017, Magdeburg.
- [3] SAE International Journal of Engines 2(2009), [No. 1], pp. 314-326.
- [4] Lahaye-Geusen, M. Light and compact housing for eight-speed automatic transmission lots of functionalities in a small space. https://automobilgestaltung.industrie. de / general / much-function-in-little space / (accessed 19.07.2021)
- [5] Foundry experience exchange 3/4 (2013) pp. 6-9.
- [6] www.mhrnd.com (accessed July 19, 2021)
- [7] Kim, J. S.; Yoo, J. High Pressure Die Casting Core and Preparation Method of High Pressure Die Casting Core. Korean patent KR101965669B1, date of Publication 04/04 2019.
専門家Q&A:よくある質問への回答
Q1: なぜこのZLeakチューブ技術は、単なる中空アルミニウムチューブを鋳込むよりも優れているのですか?
A1: 通常の中空アルミニウムチューブは、Image 1で示されているように、HPDCプロセスの極端な圧力と温度下で潰れてしまいます。ZLeakチューブの革新的な二層式充填材は、鋳造中にこれらの力に耐えるために必要な内部の構造的支持を提供します。その後、充填材は簡単かつ完全に洗い流せるように設計されており、完璧に形成された漏れのないチャネルが残ります(Image 2)。
Q2: 鋳造中にパイプが動くのが心配です。制御すべき最大の要因は何ですか?
A2: 研究によると、パイプの変位に最も大きな影響を与える要因は、溶湯流れによる熱的影響と、パイプの保持方法(ベアリング)の機械的制約です。この研究は、パイプインサートを予熱し、片側に可動ベアリングを備えた設計を使用することが、変位を減らすのに非常に効果的であることを明確に示しています。これらの要因は、再圧縮圧力を調整するよりも大きな影響を与えました(Image 6)。
Q3: 特定の金型設計でこれらのチューブインサートがどのように動作するかを、シミュレーションで予測することは信頼できますか?
A3: はい、信頼できます。このプロジェクトの重要な成果の1つは、鋳造シミュレーションソフトウェアの強力な検証でした。この研究では、WinCast expertソフトウェアによって予測されたパイプの変位と、実際の鋳造物から測定された結果との間に優れた相関関係があることがわかりました(Image 8)。これは、シミュレーションがこれらのインサートの挙動を予測するための信頼できるツールであり、自信を持って金型設計とプロセスパラメータを最適化できることを証明しています。
Q4: これらの充填されたチューブは、どのくらいの再圧縮圧力に耐えられますか?
A4: この研究では、最大1200 barの再圧縮圧力がテストされました。ZLeakチューブはこの全範囲で安定性を保ちました。結果は、圧力の増加に伴い予測可能でほぼ線形の圧縮(直径の減少)を示しており(Image 5)、これは設計段階で考慮することができます。これにより、要求の厳しい高圧ダイカストプロセスへの適合性が確認されます。
Q5: チューブ用のアルミニウム合金の選択は、鋳造性能にどのように影響しますか?
A5: 論文でEN AW-6063とEN AW-3003合金を比較したところ、重要な違いが明らかになりました。同じ形状の場合、EN AW-3003チューブは圧力下での圧縮が少なく(Image 5)、鋳物への熱伝達係数が高かった(Image 10)。これは、チューブ合金の選択が、最大の安定性または熱性能のために最適化できる重要な設計パラメータであることを示唆しています。
Q6: チューブの肉厚は、鋳造中の安定性に大きな影響を与えますか?
A6: EN AW-6063合金について研究された範囲内では、1.5mmと2mmのバージョンを比較した場合、安定性は肉厚に大きく依存しませんでした。しかし、はるかに薄い1mmの壁は、より顕著な直径の減少を示しました(Image 5)。これは、与えられた安定性要件に対して、鋳造プロセス中のインサートの完全性を損なうことなく、材料を節約したり、より大きな内部チャネル直径を設計したりするために、より薄い壁(例:1.5mm)を使用できる可能性があることを示唆しています。
結論と次のステップ
この研究は、Eモビリティの未来にとって重要な原動力であるHPDCコンポーネントの熱管理を強化するための貴重なロードマップを提供します。この発見は、ZLeakチューブ技術を、複雑で統合された冷却チャネルを作成するための堅牢で予測可能な方法として検証し、電気駆動系コンポーネントの品質を向上させ、製造の複雑さを軽減し、性能を最適化するための明確でデータに基づいた道筋を提供します。
CASTMANでは、お客様の最も困難なダイカスト問題を解決するために、最新の業界研究を応用することに専念しています。この論文で議論されている問題がお客様の運用目標と共鳴する場合、当社のエンジニアリングチームにご連絡いただき、お客様のコンポーネントにこれらの先進的な原則をどのように適用できるかご相談ください。
著作権
- この資料は、「Dirk Lehmhus, Christoph Pille, Dustin Borheck, et al.」による論文です。「Leakage-free cooling channels for Die-cast housing components」に基づいています。
- 論文の出典: https://www.ifam.fraunhofer.de/ (CoolCastプロジェクトの一部、ファンディングコード ZF4066210PO8)
この資料は情報提供のみを目的としています。無断での商業利用は禁じられています。Copyright © 2025 CASTMAN. All rights reserved.