本稿は、「Euro PM2009 – Non-Ferrous Materials - Processing」に掲載された論文「Development of Platinum-Base Superalloy Components via Powder Metallurgy」に基づき作成されました。
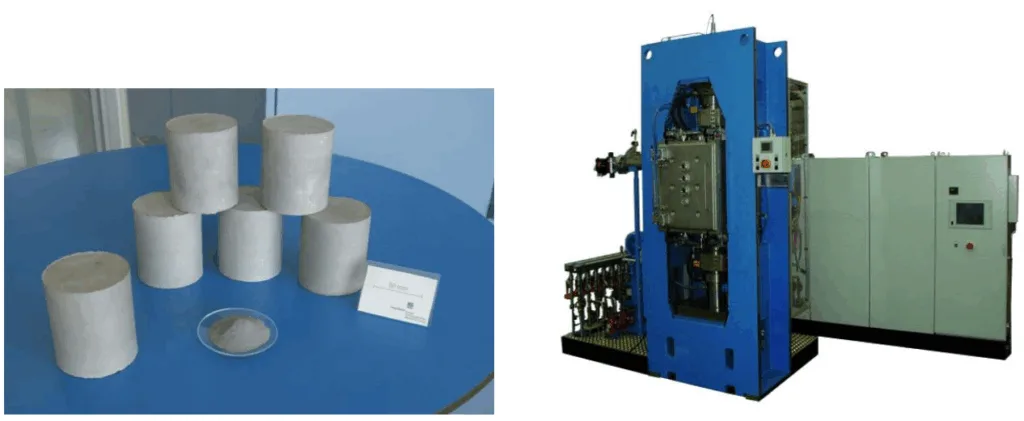
1. 概要:
- 論文名: Development of Platinum-Base Superalloy Components via Powder Metallurgy
- 著者: A. Mwamba, L.H. Chown and R. Süss
- 発行年: 2009
- 掲載学術誌・学会: Euro PM2009 – Non-Ferrous Materials - Processing
- キーワード: 論文中に明示的に記載なし。
2. 要旨:
ミンтек社は以前、白金基超合金を開発したが、これらの合金は鋳造が難しく成形性が限られているため、粉末冶金が潜在的な製造ルートとして検討された。本研究では、粉末冶金に基づく2つの方法を用いて、Pt₈₄:Al₁₁:Cr₃Ru₂の原子組成を持つ合金化白金粉末を製造した。最初の方法では、アルミニウム、クロム、ルテニウムの元素粉末を白金スポンジと共に溶融して予備合金を形成した。次に、この予備合金を再溶解し、水アトマイズ法で予備合金化白金粉末を製造した。2番目の方法では、水アトマイズ法で製造した純白金粉末を、アルミニウム、クロム、ルテニウムの元素粉末と混合し、機械的に合金化した。予備合金化粉末および機械的合金化粉末は、純白金粉末の形態、サイズ分布、密度を参照して特性評価され、一軸圧縮された。圧粉体は焼結された。光学顕微鏡、XRD、EDX分析を組み合わせて、焼結試料の粉末特性、微細構造、硬度を特性評価し、純白金圧粉体および同組成の鋳造合金と比較した。
3. 緒言:
白金は、自己触媒用途および宝飾品用途での使用でよく知られている。しかし、特定の合金元素の存在下でのニッケルとの特性の類似性から、構造用途向けの高温材料としての白金合金の使用に注目が集まっている。長年にわたり、ニッケル基超合金がこれらの用途の主要材料であった。航空機および陸上タービンのタービンブレードにおけるNBSAの使用は典型的な例である。しかし、より高い動作温度が要求される新しい用途のため、基材金属としてのニッケルはその温度限界に達しつつある。代替材料が必要とされ、イリジウム(1)、ロジウム(2)、白金(3)などの白金族金属は、より高い融点を持つという付加的な利点と共にニッケルと同様の挙動を示すため、有望な候補と見なされた。
ミンтек社は、NBSAと同様の微細構造を持つ白金基超合金(PBSA)を開発した(4-6)。白金超合金の微細構造はPt-Al系に基づいている。この系は、Pt基γマトリックス中にγ' Pt₃Al粒子を含む微細構造で構成される。このPt-Al基系をNiとCr(7)またはRuとCr(8)で合金化することにより、Pt₃AlのL1₂構造を首尾よく安定化させた。Pt₈₄:Al₁₁:Ru₂:Cr₃の組成を持つ四元合金が開発され、最良の構造を示すように最適化された(7)。白金基超合金の高温腐食挙動に関する研究では、NBSAを上回る良好な結果が示されている(9)。白金基超合金のクリープ特性に関する調査でも、特定の白金基合金が高い高温応力破断強度と延性を持ち、潜在的な高温合金であることが示されている(10)。しかし、PBSAの鋳造性および成形性の悪さから、従来の鋳造および成形方法によるこれらの合金の製造は困難であり、粉末冶金ルートを検討する必要性が生じている(4)。
4. 研究の要約:
研究テーマの背景:
白金基超合金(PBSA)は、ニッケルと同様の合金化特性を示しながらより高い融点を提供するため、高温構造用途向けのニッケル基超合金(NBSA)の代替として検討されている。[緒言]
従来の研究状況:
ミンтек社は以前、Pt-Al系をベースとし、Pt基γマトリックス中にγ' Pt₃Al析出物を特徴とし、Ni、Cr、Ruなどの合金元素によって安定性が向上したPBSAを開発した。[緒言] これらのPBSAは、良好な高温耐食性とクリープ特性を示したが、鋳造性および成形性の悪さが課題であった。[緒言]
研究の目的:
本研究は、これらの先端合金の鋳造および成形に伴う課題を克服するために、特にPt₈₄:Al₁₁:Cr₃Ru₂組成を対象として、PBSAの実行可能な製造経路としての粉末冶金を調査することを目的とした。[要旨、緒言]
核心研究:
本研究は、2つの異なる粉末冶金技術に焦点を当てた。第一に、予備形成合金の水アトマイズ法、第二に、元素粉末と水アトマイズ法による純白金とのメカニカルアロイングである。[要旨] これらの方法で製造された粉末の特性、およびそれらの焼結体の特性を徹底的に評価し、比較した。[要旨]
5. 研究方法論
研究デザイン:
本研究は、2つの粉末冶金ルートを用いて、目標組成Pt₈₄:Al₁₁:Cr₃Ru₂を持つ合金化白金粉末を製造するように設計された。(i) 予備合金化後の水アトマイズ法、(ii) 純Pt粉末と元素添加物のメカニカルアロイング。[実験手順] その後、粉末を圧縮・焼結し、得られた材料を特性評価して各ルートの有効性を評価した。[実験手順]
データ収集・分析方法:
粉末製造には、Ptスポンジと元素成分を溶融して予備合金粉末を作製し、その後水アトマイズ法(水圧200バール、過熱度100℃)で処理し、150µm未満に篩分する工程が含まれた。[実験手順] メカニカルアロイング粉末は、水アトマイズ法で作製した純Pt粉末(500µm未満)を元素Al、Cr、Ruと共にミリングして調製した。[実験手順]
粉末特性評価には、アーノルドメーターを用いた見かけ密度の測定、マルバーンマスターサイザー2000、光学顕微鏡、SEM、XRD、EDXを用いた粒子形状、サイズ、分布の評価が含まれた。[実験手順]
予備合金粉末の粉末圧縮は、MPIF標準41に従って80トン一軸プレスを用いて行い、メカニカルアロイング粉末は17.50mmの金型を用いて10~35MPa(表1に詳細記載)の中程度の圧力で圧縮した。[実験手順、表1]
焼結および熱処理はアルゴン雰囲気中で行い、試料を毎分8℃の昇温速度で1450℃まで加熱し、5時間保持した。[実験手順] 焼結後の熱処理には、一部の予備合金およびメカニカルアロイング圧粉体を1450℃で100時間再加熱し、メカニカルアロイング圧粉体を1250℃で100時間再加熱する工程が含まれた。[実験手順]
圧粉体の特性評価には、純粋なバルク白金密度に対する圧粉体密度の評価が含まれた。焼結圧粉体は、焼結密度、微細構造(光学顕微鏡およびEDX使用)、硬度について分析し、同組成の鋳造合金と比較した。[実験手順]
研究トピックと範囲:
本研究は、粉末冶金によるPt基超合金部品(Pt₈₄:Al₁₁:Cr₃Ru₂)の開発に焦点を当て、予備合金化ルートとメカニカルアロイングルートの粉末製造法を比較した。[要旨、緒言] 研究範囲には、粉末特性の評価、および焼結圧粉体の微細構造と機械的特性の評価が含まれた。[要旨、緒言]
6. 主要な結果:
主要な結果:
粉末特性: 予備合金粉末は単峰性の粒子径分布を示し、粒子の50%が43.8µmより大きかった(図1および表2参照)。対照的に、メカニカルアロイング粉末はより微細で、粒子の50%が6.7µmより小さく、その粒子径分布は単峰性と二峰性の間であった(図1、表2)。両方の粉末タイプは丸みを帯びた不規則な形態を示した(図2)。EDX分析により、両方の粉末で合金化が成功したことが確認された(表3)。しかし、予備合金粉末では酸素が検出され、水アトマイズ中に酸化が起こったことを示唆する一方、ミリング粉末は無酸素であった。[粉末化学組成、表3] 両方の粉末のXRDパターンは歪んだ白金格子を示し、Pt₃Alピークも同定された(図3)。[相特定]
粉末圧縮と焼結: 予備合金粉末(150µm未満)は、純Pt粉末(500µm未満)が約17.5g/cm³に達したのに対し、約15.0g/cm³の圧粉体密度しか達成できず、劣った圧縮挙動を示した。[粉末の圧縮と焼結への応答] メカニカルアロイング粉末は低い見かけ密度(約3.5g/cm³)を持ち、結果として低い圧粉体密度(約10.0g/cm³)を示した(表5に詳細記載)。[粉末の圧縮と焼結への応答、表5] 焼結により、予備合金圧粉体では約7%、純Pt圧粉体では約5%の密度増加が見られた。[粉末の圧縮と焼結への応答] 10~20MPaで圧縮されたメカニカルアロイング圧粉体では、焼結後に30~35%というより大幅な密度増加が観察された。[焼結後…]
焼結圧粉体の微細構造: 焼結された予備合金白金圧粉体は、約500nmサイズの立方晶Pt₃Al析出物と、約10~50nmの非常に微細な析出物を含む白金固溶体マトリックスを特徴としていた(図4(a)および(b))。[焼結圧粉体の微細構造] メカニカルアロイング圧粉体試料を1450℃で100時間時効処理した際に液体が形成されたことは興味深い観察結果であった。[焼結圧粉体の微細構造] 焼結状態のメカニカルアロイング圧粉体(図4(c))およびその後1250℃で100時間熱処理された圧粉体(図4(d))は、ランダムに分布した大きな析出物を持つ灰色がかったマトリックスを示した。1250℃の熱処理後には100nm未満の析出物が観察された。[焼結圧粉体の微細構造]
焼結の問題点: 粒子脱落やクレーター(図5)などの不完全な焼結の証拠が観察された。これは、粉末粒子表面に存在する酸化アルミニウム層が粒子間結合を妨げたためと考えられた。[焼結圧粉体の微細構造]
硬度: 予備合金焼結圧粉体の微小硬度値(焼結状態343±50 HV₀.₅、時効処理369±37 HV₀.₅、表8)は、同組成の鋳造合金について報告されている一般的な範囲(300~400 HV₁₀)内であった。[焼結圧粉体の硬度] 同様に、これらの予備合金圧粉体のマクロ硬度(焼結状態336±11 HV₁₀、時効処理365±23 HV₁₀、表9)も鋳造合金の値と一致した。[焼結圧粉体の硬度] メカニカルアロイング圧粉体はより低いマクロ硬度(焼結状態139±16 HV₁₀、時効処理199±15 HV₁₀、表9)を示したが、時効処理により大幅に増加した。[焼結圧粉体の硬度] 対照的に、メカニカルアロイング圧粉体の微小硬度は時効処理後に減少し(316±25から240±22 HV₀.₅へ、表8)、これはおそらく応力緩和と粒子緩和によるものであった。[焼結圧粉体の硬度]
図のリスト:
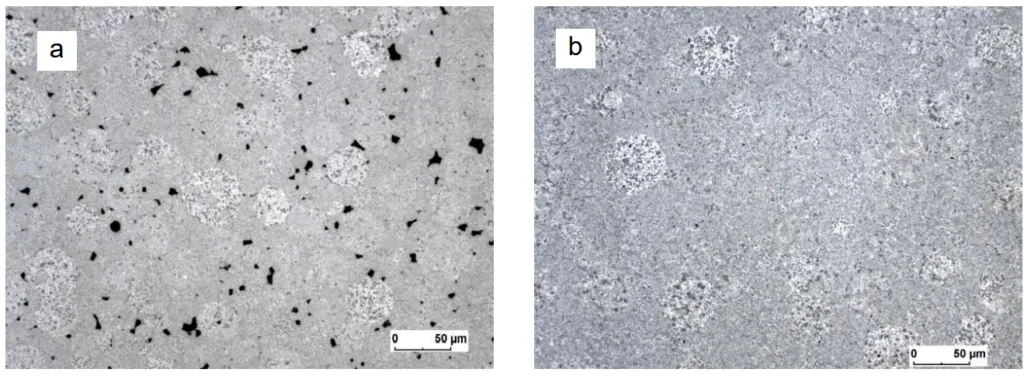
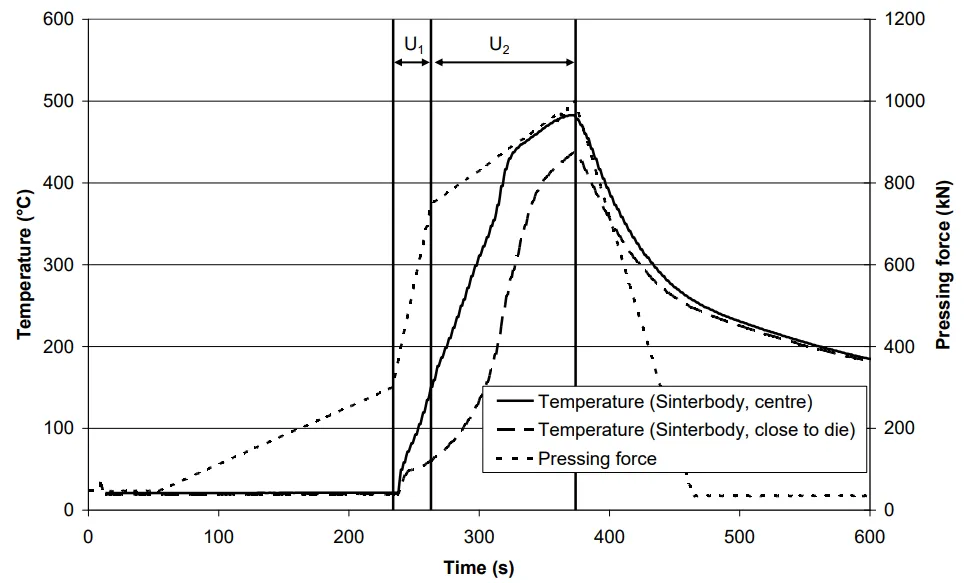
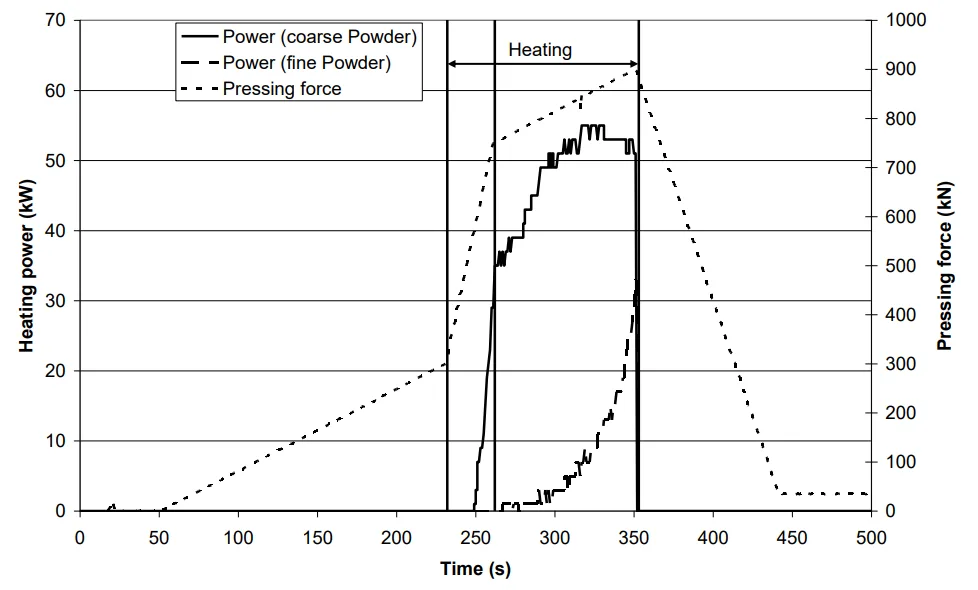
![Fig. 4. Microstructures of a consolidated MA sample (left) and a gas-atomized sample (right) with composition Mo–9Si–8B [10]. The Mo matrix is the brightest appearing phase, and the grey and dark grey appearing phases are Mo3Si and Mo5SiB2, respectively.](https://castman.co.kr/wp-content/uploads/image-2459-1024x378.webp)
![Fig. 6: Double-logarithmic plot of strain rate vs. applied stress for various Mo-9Si-8B alloys. Data for a single-crystalline Nickelbase superalloy CMSX-4 are shown for comparison [14].](https://castman.co.kr/wp-content/uploads/image-2454.webp)
- Figure 1. Particle size distribution for two powders.
- Figure 2: Particle shape in different powders.
- Figure 3. XRD pattern of pre-alloyed platinum powder showing (a) slightly shifted Pt peaks; (b) slightly shifted Pt₃Al peaks
- Figure 4: Typical microstructure of sintered pre-alloyed platinum compact.
- Figure 5: Typical features of poor-sintering area.
7. 結論:
- 予備合金粉末の粒子径および粒子径分布は、比較的小さな平均径で狭かった。予備合金粉末は、溶融物中のアルミニウムが空気および/または水からの酸素と反応した結果である不連続な酸化アルミニウム層で覆われていた。予備合金粉末から得られた圧粉体は、焼結中の結合を妨げる酸化アルミニウム層の存在により、未結合粒子が多く多孔質であり、焼結品質が悪かった。焼結圧粉体の微細構造は、Pt₃Al析出物を有する白金固溶体マトリックスからなる鋳造合金の微細構造と類似していた。焼結圧粉体の硬度は、同組成の鋳造合金で見られる硬度範囲(300~400 HV₁₀)であった。予備合金合金圧粉体を焼結温度で100時間再加熱・保持しても、焼結品質や微細構造は変化せず、硬度がわずかに増加しただけであった。
- 白金、アルミニウム、クロム、ルテニウムの元素粉末を白金基超合金の組成に機械的に合金化することは可能である。機械的合金化によって製造された粉末は、薄片状であり、平均径5µm未満の微細粒子を多く含み、凝集度が高く、単峰性分布と二峰性分布の間の粒子径分布を有していた。見かけ密度は非常に低かった。機械的合金化粉末は、圧縮に対する応答は悪かったが、焼結に対する応答は良好であった。圧粉体の微細構造は、異なるサイズおよび形態のPt₃Al析出物が分布した白金固溶体マトリックスからなっていた。圧粉体の硬度は、粉末を固化するために使用された圧縮圧力が低かったため、鋳造合金よりも低かった。時効処理中に微細構造に大きな変化が生じ、サイズ100nm未満のPt₃Al析出物が形成された。時効処理後の微細構造の変化により、硬度が大幅に増加した。
8. 参考文献:
- [論文に引用されている通りに参考文献を正確に記載してください - 原論文参照]
- . YAMABE-MITARAI, Y., KOIZUMI, Y., MURAKAMI, R, Y., MARUKO, T., and HARADA, H., Scripta Materialia, Vol. 35, No. 2, 1996, pp. 211-215.
- . YAMABE-MITARAI, Y., KOIZUMI, Y., MURAKAMI, Ro, Y., MARUKO, T., and HARADA, H., Scripta Materialia, Vol. 36, No. 4, 1997, pp. 393-398.
- . WOLFF, I.M., and HILL, P.J., Plat. Metals Rev., 44(4) (2000) 158-166.
- . CORNISH, L.A., SÜSS, R., CHOWN, L.H., DOUGLAS, A., and GLANER, L., Plat. Metals Rev. (2009), 53, pp 2-10.
- . WENDEROTH, M., CORNISH, L.A., SÜSS, R., VORBERG, S., FISCHER, B., GLATZEL, U., and VÖLK, R., Metal. And Mat. Transactions A, Vol. 36 A, pp 567-575.
- . DOUGLAS, A., HILL, P.J., MURAKUMO, T., CORNISH, L.A. and SÜSS, R., Plat. Metals Rev.2009, 53, pp 69-77.
- . VÖLK, R., WENDEROTH, M., PREUSSNER, J., VORBERG, S., FISCHER, B., YAMABE-MITARI, Y., HARADA, H., and GLATZEL, U., Mater. Sci. Eng. A 510, (2009), pp 328-331.
- . HILL, P.J., CORNISH, L.A., ELLIS, P., WITCOMB, M.J., J. Alloys Comp. 322 (2001) 166-17.
- . MALEDI, N.B., POTGIETER, J.H., SEPHTON, M., CORNISH, L.A., CHOWN, L.H., and SÜSS, R., Int. Plat. Conf., The SAIMM 2006, pp 81-90.
- . SÜSS, R, FREUND, D., VÖLK, R., FISCHER, B., HILL, P.J., ELLIS, P., and WOLFF, I.M., Mat.Sc. Eng. A 338, 2002, pp 133-141.
- . SURYANARAYANA, C., Marcel Dekker, NY, USA (2004), ISBN 0-8247-4103-X, pp 269-315.
- . SHERIF EL-ESKANDARANY, M.,William Andrew Publishing, Norwich, NY, USA, (2001) ISBN 0-8155-1462-X.
- . MÖLLER, H.J., WELSCH, G., J. Am. Ceramic Society, Vol. 68-6, pp 320-325.
- . SERCOMBE, T.B., Mat. Science & Eng A 341, pp 163-168.
- . BONDYKE, K.J., and DUDAS, J.H. United States Patent 3,796,566, June 1972.
9. 著作権:
- 本資料は、「A. Mwamba, L.H. Chown and R. Süss」の論文です。「Development of Platinum-Base Superalloy Components via Powder Metallurgy」に基づいています。
- 論文の出典:論文中にDOIの記載なし。
本資料は上記論文に基づいて要約されており、商業目的での無断使用を禁じます。
Copyright © 2025 CASTMAN. All rights reserved.
論文要約:
研究に関する主な質疑応答:
本研究は、鋳造性の低い白金基超合金(Pt₈₄:Al₁₁:Cr₃Ru₂)を粉末冶金法を用いて開発することを目的とし、予備合金化水アトマイズ粉末とメカニカルアロイング粉末を比較した。研究の結果、両方法とも合金粉末を製造できたが、予備合金化ルートは酸化物汚染により焼結性が悪く、一方メカニカルアロイングルートは圧粉体密度が低いにもかかわらず良好な焼結応答を示した。Pt₃Al析出物を有する微細構造が得られ、予備合金化圧粉体の硬度値は鋳造合金と同等であったのに対し、メカニカルアロイング圧粉体は硬度が低かったが時効処理により大幅に改善した。
Q1. Pt₈₄:Al₁₁:Cr₃Ru₂合金粉末の製造のために調査された2つの粉末冶金法は何でしたか?
A1. 2つの方法は次の通りです:1) 白金スポンジと元素粉末を溶融して予備合金を作製し、その後水アトマイズ法で処理する方法、2) 水アトマイズ法で作製した純白金粉末とアルミニウム、クロム、ルテニウムの元素粉末をメカニカルアロイングする方法。[要旨;実験手順]
Q2. 予備合金化白金粉末の焼結品質に影響を与えた主な問題は何でしたか?
A2. 主な問題は、予備合金化粉末粒子表面に存在する不連続な酸化アルミニウム層であり、これは溶融物中のアルミニウムがアトマイズ中に空気および/または水からの酸素と反応した結果であり、焼結中の良好な結合を妨げました。[結論1;焼結圧粉体の微細構造]
Q3. メカニカルアロイング粉末は、予備合金化粉末と比較して圧縮および焼結にどのように応答しましたか?
A3. メカニカルアロイング粉末は、見かけ密度が低く加工硬化が起こるため、圧縮に対する応答は悪かった(圧粉体密度が低い)が、密度が大幅に増加するなど、焼結に対する応答は良好でした。[粉末の圧縮と焼結への応答;結論2]
Q4. 両方の粉末ルートから得られた焼結圧粉体で観察された典型的な微細構造は何でしたか?
A4. 両方のルートから得られた焼結圧粉体は、一般的に、様々なサイズおよび形態のPt₃Al析出物を有する白金固溶体マトリックスから構成されていました。[焼結圧粉体の微細構造;結論1、2]
Q5. 焼結された粉末冶金圧粉体の硬度は、同組成の鋳造合金と比較してどうでしたか?
A5. 焼結された予備合金化圧粉体の硬度は鋳造合金の範囲(300~400 HV₁₀)であったのに対し、メカニカルアロイング圧粉体の硬度は、主に使用された圧縮圧力が低かったため低かったが、時効処理により大幅に増加しました。[焼結圧粉体の硬度;結論1、2]
Q6. メカニカルアロイング圧粉体試料を1450℃で100時間時効処理した際に、どのような興味深い現象が観察されましたか?
A6. メカニカルアロイング圧粉体試料を1450℃で100時間時効処理した結果、液体が形成され、これは純白金の融点よりも低い温度で液相焼結が可能であることを示唆しています。[焼結圧粉体の微細構造]