この記事では、[ARPN Journal of Engineering and Applied Sciences]が発行した論文「Corrective and preventive actions of motor cycle cylinder component leak problem on casting process」を紹介します。
1. 概要:
- タイトル: Corrective and preventive actions of motor cycle cylinder component leak problem on casting process
- 著者: Rahmat Nurcahyo and Fathur Rohman Fauzi
- 出版年: 2016年1月
- 出版ジャーナル/学会: ARPN Journal of Engineering and Applied Sciences
- キーワード: PDCA, TQM, corrective action, die casting
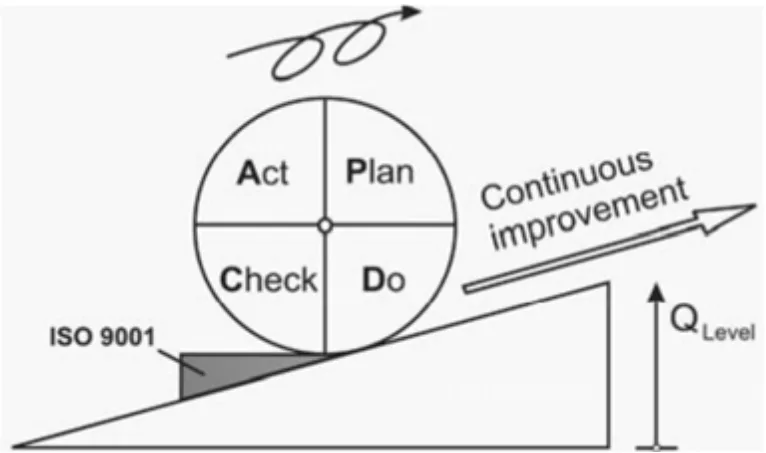
2. 概要またははじめに
不良品は、製造プロセスにおける望ましくない品質逸脱です。オートバイのシリンダー部品の鋳造プロセスにおいて、不良品問題は主要な問題の一つであり、その発生率は4.47%です。本研究は、目標値を3.6%に設定し、この問題を低減することを目的としています。問題分析と是正処置の開発には、品質補助ツールとしてのセブンツールを用いたPlan Do Check Action (PDCA)手法を使用しました。分析の結果、問題の原因はシリンダー部品のアンダーカットとポーラスであることが示されました。材料、機械、検査に関連する是正処置が実施されました。是正処置の結果、不良品率は3.17%に低下しました。予防処置は、将来の再発を防ぐために、不適合製品の潜在的な原因を減少させるために実施されました。
3. 研究背景:
研究トピックの背景:
今日、オートバイ産業は巨大な産業となり、製品品質に高い基準を適用しています。ファイゲンバウム(Feigenbaum, 1991)によれば、品質とは、マーケティング、エンジニアリング、製造、そして製品とサービスが顧客の期待を満たすために使用されるメンテナンスに至るまでの、製品とサービス全体の特性の組み合わせです。一方、ANSI/ASQC規格(1978)の定義に基づくと、品質とは、与えられた満足の必要性を保証できる製品またはサービスのすべての特徴と特性です。クロスビーは、トータルクオリティマネジメント(TQM)は、顧客満足度を高め、すべての管理者と従業員の関与を優先し、定量的な方法を使用する経営システムの戦略と統合であると主張しました(Bhat dan Cozzolino, 1993)。ISO 9001: 2008に基づき、品質マネジメントシステムの採用は、組織の戦略的意思決定として望ましいものです。組織における品質マネジメントシステムの設計と実施は、組織環境、さまざまな必要性、主な目的、利用可能な製品、適用されるプロセス、組織の規模と構造によって影響を受けます。
既存研究の状況:
組織は、品質方針、品質目標、監査結果、データ分析、是正処置および予防処置、および経営上の考慮事項を用いることによって、品質マネジメントシステムの有効性を継続的に改善する必要があります。組織は、再発を防止するために、不適合の原因を減少させるための是正処置を行う必要があります。予防処置は、起こりうる問題の予防に正確でなければなりません。PDCAサイクルは、継続的な改善を生み出すために使用される手法であり、作業プロセスまたはプログラムの実行に効果的に使用されます。PDCAサイクルは、一時的および永続的な改善という2種類の改善を行う可能性があります。セブンツール(7つの品質補助ツール)は日本発の用語であり、QCサークルおよび継続的改善と切り離すことはできません。セブンツールは、パレート図、特性要因図、チェックシート、ヒストグラム、散布図、フローチャート、管理図です。
研究の必要性:
不良品は、製造プロセスにおける望ましくない品質逸脱であり、産業における主要な問題の一つです。オートバイのシリンダー部品の鋳造プロセスでは、不良品問題が4.47%の割合で発生しており、これは企業の目標値である3.6%を上回っています。したがって、不良品率を目標値以下に低減するためには、是正処置と予防処置が必要です。
4. 研究目的と研究課題:
研究目的:
本研究の主な目的は、ダイカストプロセスにおけるシリンダー部品の不良品率を低減し、企業目標である3.6%を達成することです。
主な研究:
本研究は、ダイカストで製造されたオートバイのシリンダー部品のリーク問題の原因を分析し、PDCA手法とセブンツールを用いて是正処置と予防処置を実施し、不良品率を低減することに焦点を当てています。
研究仮説:
本論文では、研究仮説は明示的に述べられていません。しかし、PDCAとセブンツールを適用し、欠陥の根本原因(アンダーカットとポーラス)を特定し、是正処置と予防処置を実施することで、不良品率を4.47%から目標値の3.6%未満に低減できると暗黙のうちに仮説を立てています。
5. 研究方法
研究デザイン:
本研究では、PDCA手法とセブンツールを用いて、オートバイのシリンダー部品の鋳造プロセスにおけるリーク問題という不良問題を分析します。研究方法のステップは、問題の明確化、研究目的の決定、文献レビュー、研究範囲の確立、データ収集と計算、データ分析、是正処置の開発、予防処置の開発、研究結果の結論です。
データ収集方法:
予備データは、ダイカスト部門で10ヶ月間に発生したシリンダー部品の不良品データであり、生産プロセス生産システムデータベースから取得しました。研究と同じ年の10ヶ月間のA生産プロセス生産システムからのシリンダー部品のダイカストの不良プロセスのデータは、表1に示されています。
分析方法:
データ集計処理を行い、シリンダー部品の主要な不良タイプを特定しました。データ分析は、PDCA手法と品質補助ツールであるセブンツールを用いて、主要な不良製品、この場合はシリンダー部品のリーク問題のすべての原因因子を分析するために実施されました。5なぜ分析は、PICA-PAの説明における分析プロセスの一部として言及されています。パレート図は、是正処置で優先順位が付けられる不良品の種類を決定するために使用されます。特性要因図は、シリンダー部品のアンダーカットとポーラスの原因因子を理解するために使用されます。
研究対象と範囲:
本研究の問題範囲は、ダイカスト部門で製造されたシリンダー部品のみであり、仕上げ方法はPDCAとセブンツールである品質補助ツールと是正処置を使用することです。
6. 主な研究結果:
主な研究結果:
予備データは、10ヶ月間のシリンダー部品の不良品率が4.47%であり、目標値の3.6%を上回っていることを示しています。パレート図は、4つの不良カテゴリが合計67.57%の割合であることを示しています。スリーブ潤滑ボルトのリーク(26.92%)、スリーブからレッグシールドへのリーク(18.06%)、オイルパイプからレッグシールドへのリーク(14.24%)、リークテスター機のリーク(8.35%)です。分析の結果、問題の原因はシリンダー部品のアンダーカットとポーラスであることが示されました。是正処置は、シリンダー部品のリーク欠陥を引き起こす可能性のあるすべての要因を修正するために実施されました。是正処置後5ヶ月間の不良データを取得した結果、5ヶ月間のシリンダー部品の総不良率が3.17%となり、不良品率の最大制限値である3.60%を下回りました。
提示されたデータの分析:
表-1. シリンダー部品の製造上の欠陥
欠陥 | 数量 | % |
---|---|---|
スリーブ潤滑ボルトのリーク | 7426 | 1.20 |
スリーブからレッグシールドへのリーク | 4984 | 0.81 |
オイルパイプからレッグシールドへのリーク | 3930 | 0.64 |
部品分離 | 3068 | 0.50 |
リークテスター機のリーク | 2303 | 0.37 |
その他 * | 5879 | 0.95 |
合計 | 27590 | 4.47 |
図-2. シリンダー部品の欠陥のパレート図
[図-2. シリンダー部品の欠陥のパレート図は、論文で説明されているようにここに提示されます]
図-3. シリンダー部品のリークの主な原因の分析
[図-3. シリンダー部品のリークの主な原因の分析は、論文で説明されているようにここに提示されます]
図-4. アンダーカットシリンダー部品の特性要因図
[図-4. アンダーカットシリンダー部品の特性要因図は、論文で説明されているようにここに提示されます]
図-5. ポーラスシリンダー部品の特性要因図
[図-5. ポーラスシリンダー部品の特性要因図は、論文で説明されているようにここに提示されます]
表-2. リーク欠陥シリンダー部品の予防処置
メンテナンス項目 | 期間 | PIC |
---|---|---|
材料 | ||
保持炉温度の管理 | 1時間 | 溶解オペレーター |
保持炉の清掃 | 2週間 | 溶解オペレーター |
保持炉の交換 | 2年 | プロセスエンジニアリング |
機械 | ||
窒素圧のチェック | 1ヶ月 | 技術者 |
油圧オイルのチェック | 毎回生産開始時 | ダイカストオペレーター |
油圧オイルの交換 | 1年 | プロセスエンジニアリング |
プランジャーチップの交換 | 7,000ショット/NG | 技術者 |
プランジャースリーブの交換 | 60,000ショット/NG | 技術者 |
オートスプレーの交換 | 10,000ショット | 技術者 |
オートスプレーの清掃 | 10,000ショット | 技術者 |
スプレーポンプのチェック | 1ヶ月 | プロセスエンジニアリング |
金型 | ||
スライドコアと金型ピンのメンテナンス | 3,000ショット | 金型メンテナンス |
金型のメンテナンスと交換 | 10,000ショット | 金型メンテナンス |
オペレーター | ||
スキルアップ | 6ヶ月 | セクションリーダー |
表-3. 修理後のシリンダー部品の欠陥データ
欠陥 | 数量 | % |
---|---|---|
スリーブからレッグシールドへのリーク | 2,683 | 0.92 |
スリーブ潤滑ボルトのリーク | 1,288 | 0.44 |
オイルパイプからレッグシールドへのリーク | 559 | 0.19 |
部品分離 | 1,117 | 0.38 |
リークテスター機のリーク | 695 | 0.24 |
その他 | 2,922 | 1.00 |
合計 | 9,264 | 3.17 |
図のリスト:
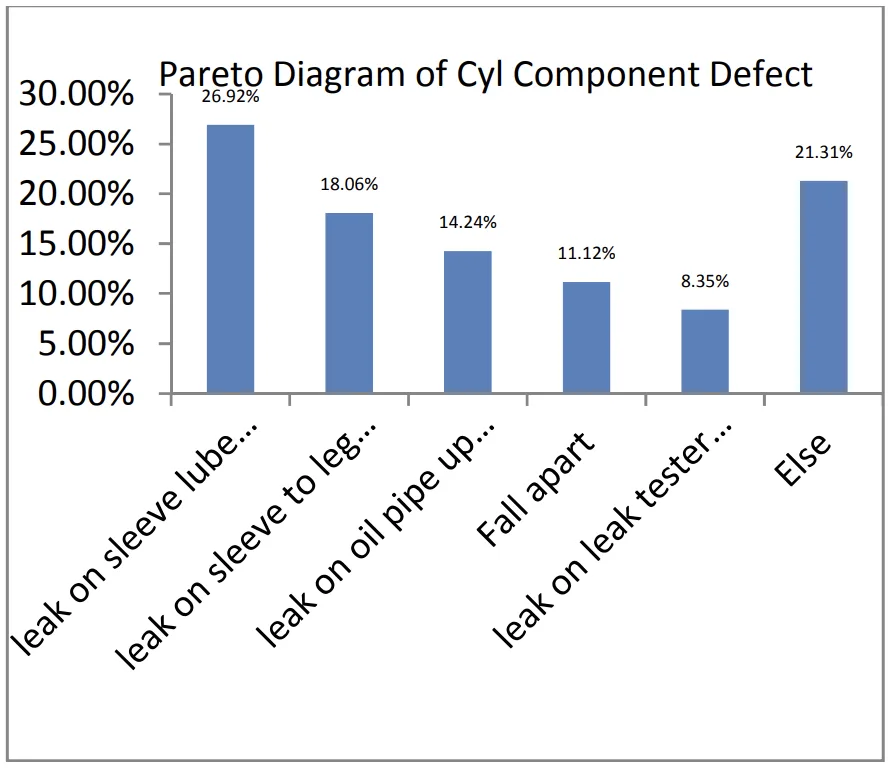
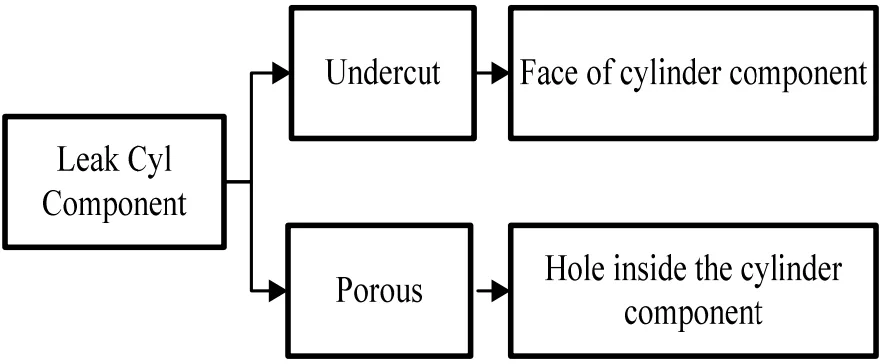
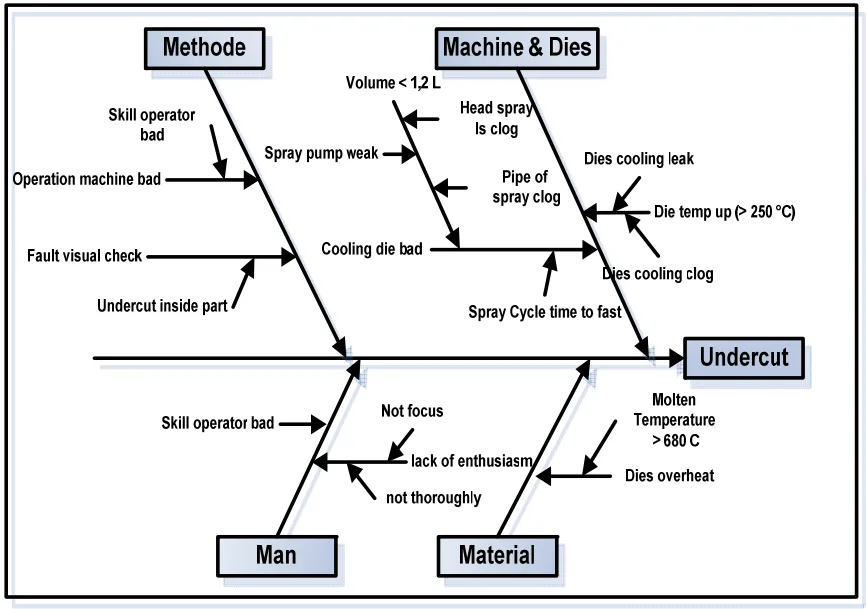
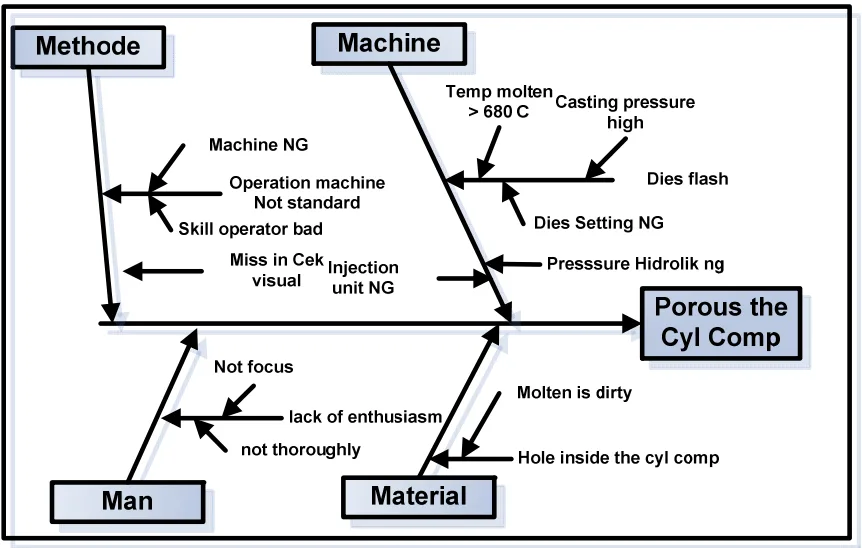
- 図-1. 持続可能な改善におけるPDCAサイクル。
- 図-2. シリンダー部品の欠陥のパレート図。
- 図-3. シリンダー部品のリークの主な原因の分析。
- 図-4. アンダーカットシリンダー部品の特性要因図。
- 図-5. ポーラスシリンダー部品の特性要因図。
7. 結論:
主な調査結果の要約:
本研究では、PDCAとセブンツールを用いた是正処置と予防処置が、シリンダー部品の不良率を4.47%から3.17%に低減し、目標値の3.6%未満を達成するのに効果的であったと結論付けました。欠陥の主な原因は、アンダーカットとポーラスであり、材料品質(汚れた溶融材料、温度)、機械の状態(オートスプレーユニット、射出圧力、金型オーバーヘッド)、およびオペレータースキルに関連する問題に起因することが特定されました。
研究の学術的意義:
本研究は、ダイカストプロセスにおける品質問題を体系的に分析し、解決するためのPDCAとセブンツールの実用的な応用を示しています。製造業、特にダイカストおよびオートバイ部品製造の分野における品質管理に関する知識体系に貢献します。
実務上の意義:
本研究の知見は、ダイカスト産業が製品品質を向上させ、不良率を低減するための実用的なフレームワークを提供します。溶融金属温度の維持、スプレーユニット性能の最適化、定期的な金型メンテナンスなど、本論文で特定された具体的な是正処置と予防処置は、シリンダー部品のリーク欠陥に対処するために直接実施できます。本論文で概説されているPICA-PA(問題特定、是正処置、予防処置)アプローチは、ISO 9000規格に準拠した、生産プロセスにおける問題解決と文書化のための構造化された方法を提供します。
研究の限界と今後の研究分野:
本研究では、オペレーターの一貫性、機械の安定性、金型設計など、十分に分析されていない要因がいくつかあることを認めています。今後の研究では、これらの要因をより深く掘り下げて、ダイカストプロセスをさらに最適化し、欠陥を最小限に抑えることができます。リーク欠陥を検出するための高度な検査方法に関するさらなる調査も有益となる可能性があります。
8. 参考文献:
- Baldwin R.M. Corrective/Preventive Actio (CAPA) Guide lines. http://www.rmbimedical.com/regulatoryAffairs/CAPAMai n.aspx.
- Bhat, V. And J Cozzolino. 1993. Total Quality: An Effective Management Tool. www.casact.org.pp. 101-123. Agustus 2005.
- Dahlgaard Jens J., Kanji, Gopal K and Kristensen Kai. 2002. Fundamentals of Total Quality Management. London and New York: Taylor and Francis Group.
- Feigenbaum, A.V.1991. Total Quality Control. New York: McGraw-Hill.
- ISO. 2008. Quality Management System Requirement (4th edition). Switzerland: Author.
- Montgomery, Douglas. 2005. Introduction to Statistical Quality Control. Hoboken, New Jersey: John Wiley andSons, Inc.
- Nazlina. 2005. Studi Pengendalian Jumlah Cacat dengan Menggunakan Metode Poka Yoke di PT. Morawa Electric Transbuana. Jurnal Sistem Teknik Industri. 6(4).
- Pipan K. Kern., Pavletic D. and Sokovic M. 2010. Quality Improvement Methodologies – PDCA Cycle, RADAR Matrix, DMAIC and DFSS. Journal of Achievements in Materials and Manufacturing Engineering. 1: 476-483.
- Schneiderman Arthur M. 1998. Are There Limits to Total Quality Management. Journal of Strategy Management Competition. (11): 35-45.
- Sokovic M., Pavletic, D. and Krulcic D. 2006. Six Sigma Process Improvements in Automotive Parts Production. Journal of Achievements in Materials and Manufacturing Engineering. 19: 96-102.
9. 著作権:
- この資料は、"Rahmat Nurcahyo"氏の論文「Corrective and preventive actions of motor cycle cylinder component leak problem on casting process」に基づいています。
- 論文ソース: https://www.researchgate.net/publication/312062708
この資料は上記の論文を紹介するために作成されたものであり、商業目的での無断使用は禁止されています。
Copyright © 2025 CASTMAN. All rights reserved.