1. 概要:
- タイトル: Benchmarking aluminium die casting operations (アルミニウムダイカスト工程のベンチマーキング)
- 著者: A. Tharumarajah
- 発行年: 2008年
- 発行学術誌/学会: Resources, Conservation and Recycling 52 (2008) 1185-1189
- キーワード: Die casting, Aluminium, Benchmarking, Recycling, Environment (ダイカスト、アルミニウム、ベンチマーキング、リサイクル、環境)
2. 研究背景:
- 世界の自動車市場におけるアルミニウムダイカスト部品の需要増加は、グローバルプレーヤーとしての地位を確立しようとしているオーストラリアの産業界にとって、重要な機会と課題をもたらしています。これらの課題に対応するため、産業界はコスト削減と温室効果ガス(GHG)排出量削減を目的として、全体的な資源効率の継続的な改善を追求しています。特に、HPDC(High-Pressure Die Casting、高圧ダイカスト)工程は、エネルギーと水の消費量が多くなる可能性があり、トリム廃棄物の形で高価なアルミニウムの損失が多量に発生する可能性があります。
- 既存の研究は、主にコスト、納期、品質などの伝統的な決定要因に焦点を当ててきました。しかし、製造プロセスから生じる環境負荷、特にGHG排出量に対する懸念の高まりから、GHG排出量削減の必要性が高まっています。
- このため、アルミニウムダイカスト産業における資源の流れと廃棄物発生量をベンチマークし、資源効率、コスト、GHG影響の側面から現状を評価する研究の必要性が提起されました。特に、一般的に良い慣行とされている社内アルミニウムリサイクルの、資源効率、コスト、GHG影響に対する潜在的な負の影響に関する詳細な分析が求められています。
3. 研究目的および研究質問:
- 研究目的: 本研究は、オーストラリア市場の約10%を占める代表的なアルミニウムHPDC施設を対象に、アルミニウムおよび主要な運転資源の使用量をベンチマークし、資源効率、コスト、GHG排出量の側面から現状を評価し、改善領域を発掘することを目的としています。特に、社内アルミニウムリサイクルの流れの詳細な分析を通じて、隠れた非効率性を明らかにし、改善策を提示することを目指しています。
- 核心研究質問:
- アルミニウムHPDC工程における資源(アルミニウム、水、電気、ガス、ダイリューブ)の流れと廃棄物発生量はどのように構成されているか?
- 社内アルミニウムリサイクルの流れは、資源効率、コスト、GHG排出量にどのような影響を与えるか?
- アルミニウムHPDC工程の資源効率および環境性能を向上させるための技術的、システム的な改善策は何か?
- 研究仮説: 本論文では、明確な研究仮説を提示していませんが、次のような仮説を暗黙的に検証しようとしています。
- 社内アルミニウムリサイクルは、表面的には資源効率を高めるように見えるが、実際には工程全体の資源効率を低下させ、コストおよびGHG排出量を増加させる可能性がある。
- アルミニウムHPDC工程の資源効率および環境性能を向上させるためには、技術的な改善だけでなく、教育訓練、メンテナンス、品質保証、現場情報および管理システムのようなシステム的な改善が必要である。
4. 研究方法論:
- 研究設計: ケーススタディ(事例研究)。オーストラリア国内の代表的なアルミニウムHPDC施設1箇所を選定し、詳細な分析を実施しました。
- データ収集方法:
- 物質フロー分析(Material Flow Analysis, MFA): HPDC工程の製品、リサイクル、廃棄物の流れをモデル化し、アルミニウムおよび主要な運転資源(水、電気、ガス、ダイリューブ)の投入量と産出量を測定および推定しました。
- 現場データ収集: 2006年4月から2007年3月までの日々の生産データおよび設計データを収集し、分析に活用しました。特に、アルミニウムの流れは部品レベルで追跡し、電気使用量は工程別または設備別の消費量として分類してデータを収集しました。
- コストおよびGHG影響計算: 直接コスト、追加コスト、GHG影響などを計算するためにデータ分析を実施しました。
- 分析方法:
- 資源効率指標の計算: 1次パス材料効率(1st pass material efficiency)、運転材料効率(operational material efficiency)、資源コスト効率(resource cost efficiency)などの指標を計算し、資源使用効率を評価しました。
- コスト分析: アルミニウム廃棄物に関連するコストを追加コスト(added cost of waste)と廃棄物処理および輸送コスト(cost of handling and transport of waste)に区分して分析し、製造コストに対する廃棄物関連コストの割合を算出しました。
- GHG影響評価: アルミニウム生産および運転資源の使用によるGHG排出量を計算し、各資源のGHG排出寄与度を分析しました。
- 研究対象および範囲:
- 研究対象: オーストラリア国内の代表的なアルミニウムHPDC施設1箇所(オーストラリア市場の約10%のシェア)。多様なトン数のHPDC機械(800T x 5、1250T x 4、2250T x 2、2500T x 2)を保有。
- 研究範囲: アルミニウム(ADC12合金)および主要な運転資源(水、電気、ガス、ダイリューブ)のHPDC工程投入から製品出荷までの全工程。社内アルミニウムリサイクルの流れを重点的に分析。
5. 主要な研究結果:
- 核心的な発見事項:
- 社内アルミニウムリサイクルは、一般的に良い慣行と見なされていますが、実際には相当量の隠れたアルミニウム損失を発生させ、これはコストおよびGHG排出量増加の主な原因となる可能性があります。
- 1次パス材料効率は93.87%と高く示されましたが、社内リサイクルを含む運転材料効率は47.7%に大幅に減少し、工程過程で相当量のアルミニウム損失が発生していることを示唆しています。
- アルミニウム溶融損失、工程損失(予熱、不良発生など)、歩留まり損失(ランナー、ビスケット、フラッシュなど)など、多様な形態のアルミニウム損失が発生しており、特に歩留まり損失が最も大きな割合を占めています。
- アルミニウム廃棄物関連コストは、総製造コストの44.1%に達し、このうち歩留まり損失関連コストが29.5%で最も高く、工程損失関連コストが13.1%を占めています。
- GHG排出量の側面からも、アルミニウム損失が大きな影響を与え、総GHG排出量の約49%がアルミニウム損失によって発生しています。
- 主要な運転資源の中で、電気と水の使用量が多く、GHG排出量寄与度も高く示されました。特に、電気は全体のGHG排出量の約51%、水は約37%を占めています。
- 統計的/定性的な分析結果:
- 1次パス材料効率: 93.87%
- 運転材料効率: 47.7%
- アルミニウム廃棄物関連コスト: 総製造コストの44.1%
- 工程損失: 13.1%
- 歩留まり損失: 29.5%
- 販売された廃棄物: 0.25%
- 追加アルミニウムコスト: 1.46%
- アルミニウム損失によるGHG排出量: 総GHG排出量の約49%
- 運転資源別GHG排出量寄与度:
- 電気: 約51%
- 水: 約37%
- 天然ガスおよびダイリューブ: わずかな水準
- 資源使用強度(アルミニウム販売量トン当たり):
- 電気: 1.54 kWh/トン
- 天然ガス: 0.02 MJ/トン
- ダイリューブ: 0.01 L/トン
- 水: 4.32 L/トン
- データ解釈:
- 高い1次パス材料効率にもかかわらず、低い運転材料効率は、社内リサイクル過程で相当な損失が発生していることを意味します。これは、表面的には現れない隠れた非効率性を示唆しています。
- アルミニウム廃棄物関連コストが製造コストの半分近くを占めることは、アルミニウム損失管理がコスト削減に非常に重要であることを強調しています。
- GHG排出量分析の結果は、アルミニウム損失削減およびエネルギー効率向上を通じて、環境影響を大幅に削減できることを示しています。
- 図表リスト (Figure Name List):
- Fig. 1. Flow of aluminium and others through HPDC process. (HPDC工程を通るアルミニウムおよびその他の資源の流れ)
- Fig. 2. Electricity consumption by category of use. (用途別電気消費量)
- Fig. 3. Primary and secondary factors influencing part quality and shop-floor efficiency. (部品品質および現場効率に影響を与える一次および二次要因)
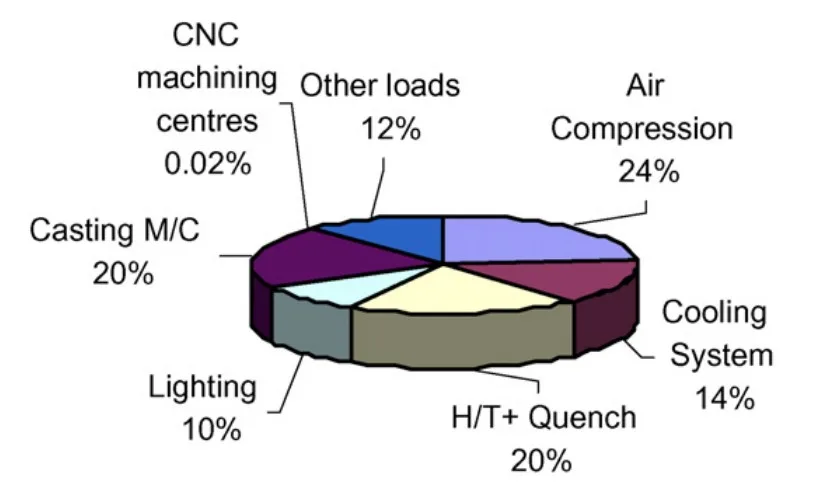
6. 結論および考察:
- 主要な結果の要約: 本研究は、アルミニウムHPDC工程の資源効率、コスト、GHG影響をベンチマークし、社内アルミニウムリサイクルの隠れた非効率性を明らかにしました。研究の結果、社内アルミニウムリサイクルは相当量のアルミニウム損失を引き起こし、これはコストおよびGHG排出量増加の主な原因となる可能性があることを確認しました。特に、歩留まり損失と工程損失がアルミニウム損失の主な原因であり、電気や水のような運転資源の使用量もアルミニウム生産量に大きく依存していることがわかりました。
- 研究の学術的意義: 本研究は、MFA技法を活用してアルミニウムHPDC工程の資源の流れを詳細に分析し、社内リサイクルの隠れた非効率性を定量的に提示することで、循環経済システムの効率性評価に関する学術的理解を広げました。また、資源効率指標、コスト分析、GHG影響評価を統合的に実施し、多角的な視点から製造工程の持続可能性を評価する方法論を提示しました。
- 実務的な示唆:
- アルミニウムHPDC産業は、社内アルミニウムリサイクルの効率性を再検討し、アルミニウム損失削減のための取り組みを強化する必要があります。特に、歩留まり損失と工程損失を削減するための技術的、運営的な改善策を模索する必要があります。
- エネルギー効率向上および水使用量削減を通じて、コスト削減とGHG排出量削減効果を同時に達成できます。
- 技術的な改善だけでなく、作業者教育訓練、メンテナンス、品質保証システム強化、現場情報管理システム構築など、システム的な改善努力が重要です。
- 研究の限界:
- 単一事例研究であるという点で、研究結果を一般化することには限界があります。今後、多様なHPDC施設を対象に研究範囲を拡大する必要があります。
- 研究対象資源は、アルミニウムおよび主要な運転資源に限定されました。今後、ダイカスト工程で使用される多様な化学物質およびその他の資源を含めて研究範囲を拡張する必要があります。
- GHG排出量評価は、本研究で考慮した運転資源に限定されました。アルミニウム生産全工程および廃棄物処理工程で発生するGHG排出量を含むライフサイクルアセスメント(Life Cycle Assessment, LCA)研究が必要です。
7. 今後の後続研究:
- 多様な規模と技術レベルのHPDC施設を対象にベンチマーキング研究を拡大し、産業全体の資源効率の現状を把握し、施設タイプ別の最適な改善戦略を導出する研究が必要です。
- ATM(Advanced Thixotropic Metallurgy、先進チクソトロピー冶金)のような新しいダイカスト技術が資源効率および環境性能に与える影響を評価し、既存のHPDC工程との比較分析を通じて技術導入の妥当性を検討する研究が必要です。
- 作業者教育訓練、現場情報管理システム、品質保証システムなど、システム的な改善策が資源効率向上に与える効果を定量的に分析し、最適なシステム構築策を提示する研究が必要です。
- アルミニウムHPDC製品のLCA研究を実施し、製品のライフサイクル全体を通して環境影響を評価し、持続可能性を向上させるための対策を模索する研究が必要です。
8. 参考文献:
- Brunner PH, Rechberger H. Practical handbook of material flow analysis. Boca Raton: Lewis Publishers; 2004.
- Gunesegaram D, Givord M, O'Donnell RG, Finnin BR. ATM high pressure die casting and its benefits. In: Proceedings of the 111th NADCA metalcasting congress; 2007.
- Ramakrishnan S, Tharumarajah A, Koltun P, Roberts MJ. Eco-efficient light-metals component manufacturing. In: Proceedings of the first international light metal technology conference; 2003. p. 125-30.
- Sustainability Victoria, Resource efficiency measurement-guidance notes, http://www.sustainability.vic.gov.au/resources/documents/2-SV-Resource_Efficiency_guidance_notes1.doc, 21 January 2008.
- Tharumarajah A, Koltun P, Ramakrishnan S, Roberts M. Improving the environmental performance of aluminium die casting production. In: 9th international conference on manufacturing excellence (ICME 2003); 2003.
- Young K, Eisen P. New die casting technologies-markets and applications. In: Die casting 2000 conference; 2000.
9. Copyright:
本資料は、A. Tharumarajahの論文: Benchmarking aluminium die casting operations を基に作成されました。
論文出典: doi:10.1016/j.resconrec.2008.06.007
本資料は上記論文に基づいて要約作成されたものであり、商業目的での無断使用は禁止されています。
Copyright © 2025 CASTMAN. All rights reserved.