1. 概要:
- タイトル: Al-Siダイカストエンジンブロックの微細構造と機械的特性の相関 (Correlation between microstructure and mechanical properties of Al-Si diecast engine blocks)
- 著者: Fabio Grosselle, Giulio Timelli, Franco Bonollo, Roberto Molina
- 発行年: 2009年
- 発行学術誌/学会: Metallurgical Science and Technology
- キーワード:
- アルミニウム合金 (Aluminium alloys)
- EN-AC 46000
- 高圧ダイカスト (High-pressure die-casting)
- SDAS (二次デンドライトアーム間隔)
- 共晶Si (Eutectic Si)
- 微細構造 (Microstructure)
- エンジンブロック (Engine block)
2. 研究背景:
- 研究テーマの社会的/学術的背景:
- 乗用車において、シリンダーブロックは最も重い部品であり、燃費と車両の運転性に大きく影響します。
- アルミニウム合金鋳物は、軽量化と排出ガス削減の可能性から、現代の乗用車での使用が増加しています。
- シリンダーブロックを鋳鉄からアルミニウム合金に置き換えることで、ガソリンエンジンで最大45%の軽量化が可能です。
- アルミニウム合金は熱伝導率が高いため、局所的な温度制御が向上し、シリンダーサイズあたりのエンジン出力を向上させることができます。
- 量産エンジン向けには、複雑な形状と薄肉の部品を高い生産速度で製造でき、コストを削減できる高圧ダイカスト(HPDC)が広く使用されています。
- 亜共晶二次Al-Si合金は、優れた鋳造性、良好な機械的特性、および低コストのため、HPDCプロセスで一般的に使用されています。
- 既存研究の限界点:
- HPDC部品は、鋳造形状の複雑さとプロセスパラメータの変動性により、引け巣、湯回り不良、酸化膜、ドロス、巻き込み気泡などの欠陥が発生しやすいです。
- Al-Si鋳物中の微細構造(一次α-Al相と共晶Si粒子の分布、形態、寸法など)は、冷却条件と凝固履歴に影響されます。
- 鋳造品の壁面から中心線に向かうにつれて、微細構造は粗くなり、充填ダイナミクスと凝固時間の増加により欠陥が形成されやすくなります。
- Cu、Mg、およびトラップ元素の存在は、強化析出物や鉄系金属間化合物などの他の相の形成につながる可能性があります。
- 研究の必要性:
- Al-Siダイカストエンジンブロックの性能と信頼性を最適化するためには、微細構造と機械的特性の相関関係を理解することが重要です。
- プロセスパラメータ、微細構造の特徴、および欠陥はすべて、アルミニウム合金の最終的な機械的特性に影響を与えます。
- 欠陥のない部品では、脆性金属間化合物または共晶Si粒子の劈開によって破壊が開始され、SDAS値に応じて粒界またはセル境界に沿って主に伝播します。
- 欠陥は、破壊の開始と伝播に影響を与えることで、機械的特性を低下させる可能性があります。
- HPDCエンジンブロックにおけるSDAS、共晶Si粒子のサイズと形態などの微細構造の特徴と、機械的特性との関係を分析する必要があります。
3. 研究目的及び研究質問:
- 研究目的:
- HPDCエンジンブロックの微細構造と機械的特性の相関関係を分析すること。
- 特に、機械的特性と二次デンドライトアーム間隔(SDAS)、サイズ、共晶Si粒子の形態などの微細構造の特徴を関連付けること。
- 核心研究質問:
- HPDC Al-Si合金エンジンブロックの微細構造の特徴(SDAS、共晶Si粒子のサイズと形態)は、機械的特性(引張強さ(UTS)と破断伸び)とどのように相関しますか?
- 凝固速度と冷却条件は、エンジンブロックの微細構造と機械的特性にどのような影響を与えますか?
- これらのダイカスト部品において、微細構造パラメータと機械的特性の間に定量的な関係を確立できますか?
- 研究仮説:
- 機械的特性、特にUTSと破断伸びは、Al-Siダイカストエンジンブロックの微細構造に大きく影響されます。
- SDAS値が低く、小さくコンパクトな共晶Si粒子によって特徴付けられる微細構造は、優れた機械的特性を示すでしょう。
- UTSとSDAS、等価直径、およびSi粒子の形状比の積の間には線形相関が存在し、破断伸びは微細構造の変化に対して指数関数的な傾向を示すでしょう。
4. 研究方法論:
- 研究設計:
- 二次AlSi9Cu3鋳造合金(EN AC-46000-UNI EN 1706合金)製のHPDC 4気筒直列エンジンブロックの徹底的な分析。
- エンジンブロック鋳造品内の異なる場所における機械的特性と微細構造の特徴の相関研究。
- データ収集方法:
- 化学組成分析: 別途鋳造されたサンプルで測定(方法不明、表1参照)。
- 熱分析: 液相線温度(Tliq = 585℃)を熱分析により測定。
- X線検査: 鋳造品全体の巨視的欠陥を検出するために実施。
- 機械試験:
- ASTM-B577に準拠して、切断されたエンジンブロックの異なる場所から機械加工された平型引張試験片を使用した引張試験。
- 降伏応力(YS)、引張強さ(UTS)、および破断伸び(Sf)は、クロスヘッド速度2 mm/min(ひずみ速度〜10⁻³ s⁻¹)のコンピュータ制御式引張試験機MTS 810を使用して測定。
- ASTM E-384に準拠して、荷重0.2 kgf、保持時間30秒で、研磨されたサンプルに対してビッカースマイクロ硬さ測定を実施。
- 微細構造分析:
- 光学顕微鏡およびエネルギー分散型分光器(EDS)を備えた走査型電子顕微鏡(SEM)。
- 画像解析装置を用いた定量的な画像解析により、以下を測定:
- 線分法を用いた二次デンドライトアーム間隔(SDAS)。
- 共晶シリコン粒子のサイズ(等価円直径d)と形状比(α)。
- 分析方法:
- 鋳造欠陥の影響を最小限に抑えるために最良値を平均化した実験データの統計分析。
- 微細構造パラメータ(SDAS、共晶Si粒子のサイズと形状比)と機械的特性(UTS、Sf、マイクロ硬さ)の間の関係を決定するための相関分析。
- 相関の種類(線形、指数関数的)を確立し、適合度を評価するための決定係数(R²)を計算するための回帰分析。
- 研究対象と範囲:
- ダイナミックショット制御および真空システムを備えたコールドチャンバーダイカストマシンで製造されたHPDC 4気筒直列エンジンブロック。
- 材料:二次AlSi9Cu3合金(EN AC-46000-UNI EN 1706合金)。
- 凝固条件の変動を考慮して、エンジンブロック鋳造品の異なる領域における微細構造と機械的特性の相関関係に焦点を当てる。
5. 主な研究結果:
- 核心研究結果:
- HPDCエンジンブロックの機械的特性は、微細構造に大きく影響されます。
- より高い凝固速度(例:鋳造壁面付近および薄肉部)で達成されるより微細な微細構造は、より高いUTSと破断伸びを示します。
- より遅い凝固(例:厚肉部およびバルクヘッドサポート)に起因するより粗い微細構造は、より低い機械的特性と欠陥の増加を示します。
- UTSと破断伸びは、SDASと共晶Si粒子のサイズの増加とともに減少します。
- UTSとSDAS、等価直径、および共晶Si粒子の形状比の積との間に線形相関が見られました。
- 破断伸びは、SDASと共晶Si粒子のサイズの増加とともに指数関数的に減少し、UTSよりも微細構造の変化に対する感度が高いことを示しています。
- 統計的/定性的分析結果:
- X線検査では、真空システムのおかげで、重大な欠陥が最小限に抑えられ、鋳造品の良好な健全性が示されました。小さなマクロポロシティが、円形断面、バルクヘッドサポート、およびライナーの下、特に真空ラインの近くで観察されました。
- 微細構造は鋳造品全体で変化しました:
- 壁面付近:より微細で、気孔のない微細構造。
- 中心に向かって:より粗い微細構造、より大きなα-Al相、より粗い共晶Si粒子、およびより多くの欠陥。
- α-Al相の形態:壁面付近では等軸晶粒状、中心に向かってデンドライト状。
- 共晶Siの形態:壁面付近では繊維状で微細、厚肉部では粗い板状。
- マイクロ硬度は、鋳造断面のエッジから中心に向かって減少しました。
- YS値は、異なるゾーン間で有意な変動を示しませんでした。
- UTSと破断伸びの値は、鋳鉄ライナー間の領域(UTS:274±10MPa、伸び:2.5±0.4%)で、ライナーとバルクヘッドサポートの下のゾーン(UTS:236 MPa、伸び:1.4%)よりも高くなりました。
- UTSとSDAS、および破断伸びとSDASの相関関係の決定係数(R²)は0.52でした。
- UTSと共晶Si粒子のサイズ、および破断伸びと共晶Si粒子のサイズの相関関係のR²は、それぞれ0.83と0.89でした。
- UTSと複合パラメータ(SDAS x 等価直径 x 形状比)の相関関係のR²は0.50であり、破断伸びでは0.55でした。
- データ解釈:
- 凝固速度と冷却条件は、微細構造、ひいては機械的特性に影響を与える主要な要因です。
- 急速凝固によって達成されるより微細な微細構造は、機械的強度と延性を向上させます。
- 共晶Si粒子のサイズと形態は、UTSよりも破断伸びに顕著な影響を与えます。
- SDASと共晶Si粒子の特性の複合的な影響は、機械的特性への影響を包括的に理解するのに役立ちます。
- 図表リスト:
- Fig. 1: 6つのインゲートと真空チャンネルを備えたエンジンブロックの図 (Illustration of engine block with 6 ingates and the vacuum channels.)
- Fig. 2: 引張試験片を機械加工した位置 (Position from which tensile specimens were machined.)
- Fig. 3: 気孔率の存在を示すバルクヘッドサポートのX線画像 (Radiographic image of the bulkhead support showing the presence of porosity.)
- Fig. 4: 厚肉部に対応する微細構造 (Microstructure in correspondence of a thick section.)
- Fig. 5: (a)繊維状および(b)層状形状の共晶シリコン粒子(それぞれ高冷却速度および低冷却速度のゾーン) (Eutectic silicon particles with (a) fibrous and (b) lamellar shape in the zones with high and low cooling rates respectively.)
- Fig. 6: SDASの関数としての共晶Si粒子の平均直径と形状比 (Average diameter and aspect ratio of the eutectic Si particles as a function of SDAS.)
- Fig. 7: ダイカストAlSi9Cu3エンジンブロックの微細構造 (Microstructure of die-cast AlSi9Cu3 engine block.)
- Fig. 8: 試験片の断面に沿って測定されたビッカースマイクロ硬さ (Vickers microharness measured along the cross section of a specimen.)
- Fig. 9: (a)酸化物介在物と膜、(b)気孔率、(c)ダイカストで観察された湯じわ (Oxide inclusions and films, (b) porosities and (c) cold shots observed in diecastings.)
- Fig. 10: 低凝固速度領域における共晶シリコンの偏析帯 (Segregation bands of eutectic silicon in regions with low solidification rate.)
- Fig. 11: SDASの関数としてのUTSと破断伸び (UTS and elongation to fracture as function of SDAS.)
- Fig. 12: 共晶Si粒子の等価直径の関数としてのUTSと破断伸び (UTS and elongation to fracture as function of equivalent diameter of the eutectic Si particles.)
- Fig. 13: 複合パラメータSDAS x 等価直径 x 形状比の関数としてのUTSと破断伸びの値 (UTS and elongation values as function of the combined parameter SDAS x Equivalent diameter x Aspect ratio of eutectic Si particles.)
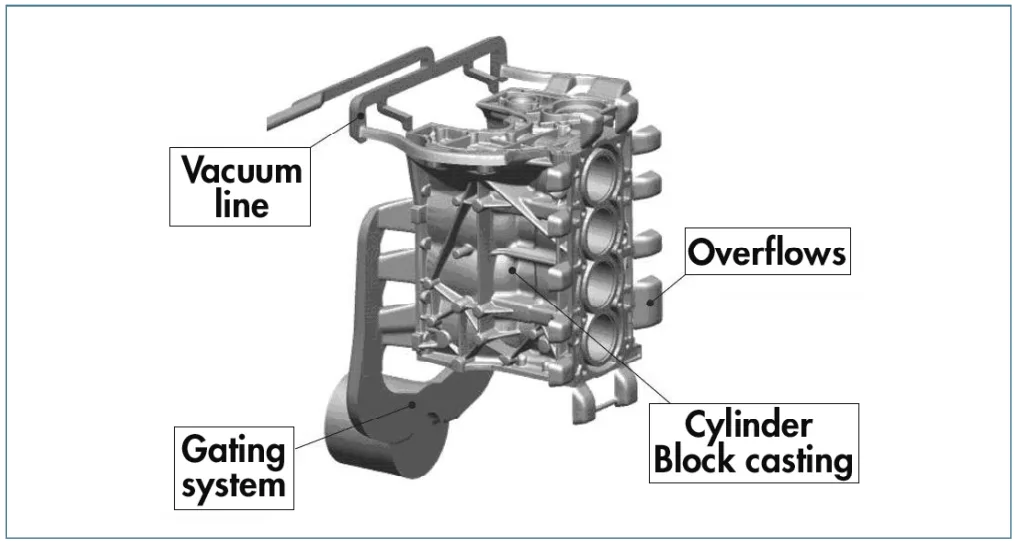
6. 結論及び考察:
- 主な結果の要約:
- HPDC 4気筒直列シリンダーブロックの微細構造と機械的特性は強く相関しています。
- より高い凝固速度は、より微細な微細構造と改善された機械的特性(UTSと破断伸び)につながります。
- 凝固時間の増加は、より大きなSDAS、より粗い共晶Si粒子、およびより高い割合のブロック状α-Al(Mn、Fe、Cr)Si相を備えた、より粗い微細構造をもたらし、機械的特性の低下につながります。
- 機械的特性は微細構造の影響を受け、最高のUTSと伸びの値は、低いSDASと小さくコンパクトな共晶Si粒子に対して得られます。
- より粗い微細構造とより多くの欠陥量は、合金強度を低下させ、破壊核生成を促進します。
- UTSとSDAS、共晶Si粒子のサイズと形状比の複合パラメータの間には線形相関が存在し、破断伸びはこれらの微細構造の変化に対して指数関数的な感度を示します。
- 研究の学術的意義:
- この研究は、HPDC Al-Si合金エンジンブロックにおける主要な微細構造の特徴(SDAS、共晶Si粒子の特性)と機械的特性(UTS、破断伸び)の間の定量的なデータと相関関係を提供します。
- 凝固条件と微細構造がダイカストアルミニウム部品の性能にどのように影響するかについての理解を深めます。
- この研究は、HPDC部品の機械的特性を最適化するために、凝固速度と微細構造を制御することの重要性を強調しています。
- 実務的示唆:
- この知見は、エンジンブロックや同様の部品で望ましい微細構造と機械的特性を達成するために、HPDCプロセスパラメータ(例:金型温度、射出速度、冷却戦略)の最適化を導くことができます。
- プロセス制御を通じてSDASと共晶Si粒子の特性を制御することで、Al-Siダイカストエンジンブロックの信頼性と性能を向上させることができます。
- 確立された相関関係は、品質管理や微細構造分析に基づく機械的特性の予測に使用できます。
- 研究の限界点:
- この研究は、特定のHPDCエンジンブロックの設計と合金組成に焦点を当てています。
- 相関分析は有意ですが、HPDC部品に固有の欠陥と、個々の微細構造効果を分離することの複雑さにより、データにばらつきが見られます。
- この研究では、主にSDASと共晶Si粒子を考慮しましたが、他の微細構造の特徴や欠陥も機械的特性の変動に寄与している可能性があります。
7. 今後の後続研究:
- 後続研究の方向性:
- 気孔率、金属間化合物相、結晶粒径など、他の微細構造の特徴が機械的特性に及ぼす影響に関するさらなる調査。
- 特定のHPDCプロセスパラメータが微細構造の発達と機械的特性の変動に及ぼす影響の詳細な分析。
- HPDC Al-Si合金のプロセスパラメータ、微細構造、および機械的性能をリンクする予測モデルの開発。
- ダイカスト部品の品質評価のための高度な微細構造特性評価技術と非破壊検査法の探求。
- HPDCエンジンブロックにおける微細構造に関連する疲労および破壊挙動の調査。
- 追加探求が必要な領域:
- 異なる合金元素の役割と、HPDC Al-Si合金の微細構造と機械的特性への影響。
- ダイカストエンジンブロックの性能をさらに向上させるための合金組成と熱処理戦略の最適化。
- これらの知見の他の複雑なHPDC部品および産業への応用。
8. 参考文献:
[1] Colás, R., A. Rodríguez, J. Talamantes, and S. Valtierra. Solidification analysis of aluminium engine block. Int. J. Cast Metals Res., 17 (2004), 332-338.
[2] Verran, G.O., R.P.K. Mendes and M.A. Rossi. Influence of injection parameters on defects formation in die casting Al12Si1,3Cu alloy: experimental results and numeric simulation. J. Mater. Process Technol., 179 (2006), 190-195.
[3] Avalle, M., G. Bellingardi, M.P. Cavatorta and R. Doglione. Casting defects and fatigue strength of a die cast aluminium alloy: a comparison between standard specimens and production components. Int. J. Fatigue 24 (2002), 1-9.
[4] Timelli, G. and F. Bonollo. Quality mapping of aluminium alloy diecastings. Metal. Sci. Tech., 26 (2008), 2-8.
[5] Shabestari, S.G. and F. Shari. Influence of modification, solidification conditions and heat treatment on the microstructure and mechanical properties of A356 aluminum alloy. J. Mater. Sci., 39 (2004), 2023-2032.
[6] Viswanathan, S., A.J. Duncan, S.A. Sabau, Q. Han, W.D. Porter and B.W. Riemer. Modeling of Solidification and Porosity in Aluminum Alloy Castings. AFS Transactions, 98-103 (1998), 411-417.
[7] Rontó, V. and A. Roósz. The effect of the cooling rate or the local solidification time and composition on the secondary dendrite arm spacing during solidification Part II: Al-Mg-Si alloys. Int. J. Cast Metals Res., 13 (2001), 337-342.
[8] Grosselle, F., G. Timelli, F. Bonollo, A. Tiziani and E. Della Corte. Correlation between microstructure and mechanical properties of Al-Si cast alloys. Metall. Ital., 6 (2009), 25-32.
[9] Chen, Z.W. Skin solidification during high pressure die casting of Al-11 Si-2 Cu-1Fe alloy. Mater. Sci. Eng., A348 (2003), 145-153.
[10] Ye, H. An overview of the development of Al-Si alloy based material for engine applications. J. Mater. Eng. Perf., 12(3) (2003), 288-297.
[11] Samuel, F.H., A.M. Samuel and H.W. Doty. Factors controlling the type and morphology of Cu-containing phases in 319 Al alloy. AFS Trans., 104 (1996), 893-901.
[12] Νίυ, Χ.P, B.H. Hu and S.W. Hao. Effect of iron on the microstructure and mechanical properties of Al die-casting alloys. J. Mater. Sci. Letters, 17 (1998), 1727-1729
[13] Wang, Q.G. and C.H. Cáceres. Fracture mode in Al-Si-Mg casting alloys. Mater. Sci. Eng, A241 (1998), 72-82
[14] Wang, Q.G., C.H. Cáceres and J.R. Griffiths. Damage by eutectic particle cracking in aluminum casting alloys A356/357. Metall. Mater. Trans. A, 34 (2003), 2901-2912
[15] Cáceres, C.H. and J.R. Griffiths. Damage by the cracking of silicon particles in an Al-7Si-0.4Mg casting alloy. Acta Mater. 44 (1996), 25-33.
[16] Cáceres, C.H. and B.I. Selling. Casting defects and the tensile properties of an Al-Si-Mg alloy. Mater. Sci. Eng., A220 (1996), 109-116.
[17] Gokhale, A.M. and G.R. Patel. Origins of Variability in the fracture related mechanical properties of a tilt-pour-permanent-mold cast Al-alloy. Scripta Mater., 52 (2004), 237-241.
[18] Shankar, S. and D. Apelian. Die soldering: Mechanism of the interface reaction between molten aluminum alloy and tool steel. Mater. Trans., 33B (2002), 465-476.
[19] Jorstad, J.L. Understanding "Sludge". Die Casting Eng., November/December (1986), 30-36.
[20] Ghomashchi, M.R. Intermetallic compounds in an Al-Si Alloy used in high pressure diecasting. Z. Metallkunde, 78 (1987), 784-787.
[21] Seifeddine, S., T. Sjögren and I.L. Svensson. Variations in microstructure and mechanical properties of cast aluminium EN AC 43100 alloy. Proc. High Tech Die Casting, AIM, (2006), Vicenza.
[22] Zovi, A. and F. Casarotto. Silafont-36, the low iron ductile die casting alloy development and applications. Metall. Ital. 6 (2007), vol., 33-38.
[23] Asensio-Lozano, J. and B. Suárez-Peña. Microstructure-properties correlation of pressure die cast eutectic aluminum-silicon alloys for escalator steps (Part I). Mater. Characterization, 56 (2006), 169-177.
[24] Mondolfo, L.F. Manganese in Aluminum Alloys. The Manganese Center, (1978).
[25] Μο, Α., M. M'Handi and H.I. Laukly. Modelling defect bend formation in Al-Si die casting. Proc. High Tech Die Casting, AIM, (2006), Vicenza.
9. 著作権:
- 本資料は、Fabio Grosselle, Giulio Timelli, Franco Bonollo, Roberto Molinaの論文「Correlation between microstructure and mechanical properties of Al-Si diecast engine blocks」に基づいて作成されました。
- 論文出典: https://www.metallurgical.org.rs/uploads/editor/files/Metals_and_Technology/Vol_27_2/Grosselle.pdf
本資料は上記の論文に基づいて要約作成されており、商業目的での無断使用は禁止されています。
Copyright © 2025 CASTMAN. All rights reserved.