概要:
本論文は、耐熱性マグネシウム合金を用いた自動車用オイルパンのダイカストプロセスに関する研究です。現在使用されているアルミニウム合金の代替を目指し、最適なプロセスパラメータと材料特性を評価することで、欠陥を最小限に抑え、性能を最適化することを目的としています。アルミニウムとマグネシウム合金の熱特性の違いから生じる欠陥の軽減に重点が置かれています。
1. はじめに:
クランクケース下部に設置されるオイルパンは、循環した潤滑油が集まる部品です。高温環境下にあるため、耐熱性材料の使用が不可欠です。現在、アルミニウム合金(ADC12)が使用されています。本研究では、アルミニウムをマグネシウム合金に置き換えることで大幅な軽量化(アルミニウム(2.8g/cm³)と比較してマグネシウム(1.8g/cm³)の密度は約35%低い)を実現することを検討しています。しかし、マグネシウム合金はヤング率が低い(アルミニウム73GPaに対しマグネシウム45GPa)ため、十分な剛性を維持するために設計の最適化が必要です。マグネシウム合金は比強度と比弾性率において優れた特性を示しますが、アルミニウムと比較して絶対強度と延性が低く、耐熱性も劣ります。そのため、自動車部品への適用は、耐熱性がそれほど厳しくない部品(シリンダーヘッドカバー、ステアリングホイール、インストルメントパネル、シートフレームなど)に限定されています。
2. 背景と文献レビュー:
本論文では、耐熱性を維持しながらコスト効率の高い合金化戦略に焦点を当てた、マグネシウム合金開発の研究状況について簡単にレビューしています。先進国と比較して、韓国における耐熱性マグネシウム合金自動車部品の採用が比較的少ない現状が指摘されており、国際競争力の強化のためにこの技術の早期開発が急務であることが強調されています。
3. 研究目的と課題:
主な目的は、耐熱性マグネシウム合金を用いた自動車用オイルパンのダイカストプロセスを最適化し、最適なプロセスパラメータを提示することです。主な研究課題は、マグネシウム合金オイルパンのダイカストプロセスにおいて、金型設計、鋳造条件、材料特性などが製品品質に及ぼす影響を明らかにすること、そして、欠陥のない高品質なマグネシウムオイルパンをどのように生産できるかを探ることです。仮説としては、マグネシウム合金の特性を考慮した最適化された金型設計と鋳造条件を適用することで、欠陥のない高品質なマグネシウムオイルパンの生産が可能であるというものです。
4. 研究方法:
本研究では、シミュレーションと実験の両方を用いています。
- シミュレーション: CFDソフトウェア(FLOW-3D)を用いてダイカストプロセスをシミュレーションします。これには、様々な段階(充填、凝固、射出、冷却)における金型内の温度分布のモデル化と、鋳造キャビティ内での溶融マグネシウム合金の流動挙動の解析が含まれます。これにより、充填性を向上させ、欠陥を低減するためのランナー、ゲート、ベント、オーバーフローシステムを最適化することができます。シミュレーションでは、マグネシウム合金とアルミニウム合金の熱特性(熱容量、潜熱)の大きな違いが考慮されています。
- 実験: AE44とMRI153Mマグネシウム合金を用いたダイカスト実験を行い、シミュレーション結果を検証し、プロセスパラメータをさらに最適化します。検討された主要なプロセスパラメータには、スリーブ充填率、キャビティ充填時間、ショット速度、金型温度などがあります。X線検査と断面解析を用いて、鋳造品の品質を評価し、欠陥を特定します。
5. 結果:
- 金型温度分布解析: 解析の結果、マグネシウム合金はアルミニウム合金と比較して熱容量と潜熱が低いため、金型温度が大幅に速く低下することが明らかになりました。これにより、早期凝固や欠陥を防ぐために冷却システムの変更が必要となります。アルミニウム(水冷)とマグネシウム(油冷)の冷却方法の比較が行われました。
- ランナーとゲート設計の最適化: アルミニウム金型鋳造の既存設計を用いた初期シミュレーションでは、空気の巻き込みと酸化物の混入の可能性が示されました。その後の繰り返しシミュレーションにより、よりスムーズな金属の流れを促進し、空気抜きを改善し、酸化物の生成を最小限に抑えるために、ランナーとゲートの設計が改善されました(図6)。修正された設計により、充填効率と空気の巻き込みの低減がシミュレーションで確認されました(図7と図10)。
- 鋳造パラメータの影響: 鋳造パラメータ(ショット速度、冷却時間、ゲート速度、スリーブ充填率)が鋳造品の品質に及ぼす影響について調査されました。AE44とMRI153Mマグネシウム合金それぞれの最適なパラメータ設定が表2に示されています。
- AE44とMRI153M合金の比較: AE44とMRI153Mの両合金が試験されました。MRI153M合金は、凝固時間が長いため(AE44と比較して凝固温度範囲は約270℃異なる)、内部収縮気孔が発生する傾向がありました。しかし、鋳造パラメータの最適化により、この欠陥を大幅に低減することができました(図13、図14)。
- Figure 1: Current Al oil pan and cooling lines.
- Figure 2: Temperature distributions of oil pans (Cycling).
- Figure 3: Developed Mg oil pan and cooling lines.
- Figure 4: Temperature distributions of Mg oil pan for new cooling lines (Cycling).
- Figure 5: Filling pattern of current Al oil pan.
- Figure 6: Changes of runner and gate.
- Figure 7: Filling pattern of 1-st die casting process.
- Figure 8: Temperature distribution at t=1.825sec.
- Figure 9: 2-nd die shape for Mg oil pan.
- Figure 10: Filling pattern of 2-nd die casting process.
- Figure 11: Temperature distribution at t=1.825sec.
- Figure 12: Cutting position.
- Figure 13: Photos of A-A' section.
- Figure 14: Photos of B-B' section.
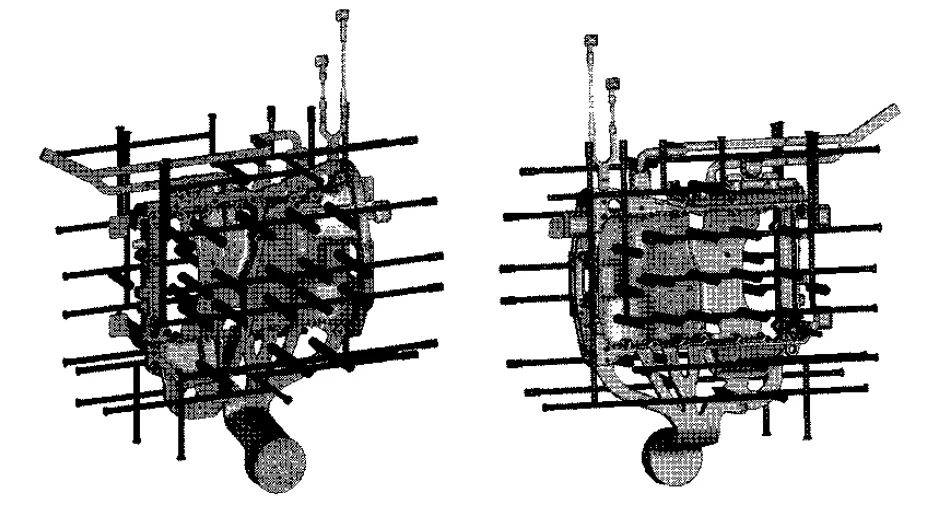
6. 考察と結論:
この研究結果は、アルミニウム合金とマグネシウム合金の熱特性の違いがダイカストプロセスに大きな影響を与えることを示しています。最適化された金型設計と鋳造パラメータを用いることで、欠陥のない高品質なマグネシウムオイルパンの生産が可能であることが確認されました。本研究の貢献は、CFDシミュレーションと実験的検証を含むダイカストプロセスの詳細な解析を行い、マグネシウム合金のプロセス最適化に関する知見を提供したことです。これにより、燃料効率の向上と排出ガスの削減に繋がる大幅な軽量化が実現します。
7. 制限事項:
本研究の範囲は、調査された特定のマグネシウム合金とオイルパンの形状に限定されています。より広範囲のマグネシウム合金や様々な形状への適用を検証するためには、さらなる研究が必要です。様々な動作条件下での耐久性試験を行うことで、マグネシウムオイルパンの実用性に関する結論がより強固なものとなります。
8. 今後の研究:
今後の研究としては、より広範囲のマグネシウム合金の検討、様々な金型設計の調査、実際の動作条件下での長期間性能試験の実施などを通して、マグネシウムオイルパンの長期的な性能と耐久性を評価する必要があります。様々な合金元素が鋳造特性と結果として得られる機械的性能に及ぼす影響についても、さらに調査する必要があります。試験された範囲を超える鋳造条件(より広い温度範囲や圧力範囲など)の変化の影響についても検討することができます。
参考文献:
- D. M. Kim, H. S. Kim, and S. I. Park, "Magnesium for Automotive Application," Journal of KSAE, vol. 18, no. 5, pp. 53-67, 1996.
- J. Hwang and D. Kang, "FE Analysis on the press forging of AZ31 Magnesium alloys,” Transactions of KSAE, vol. 14, no. 1, pp. 86-91, 2006.
- P. Lyon, J. F. King, and K. Nuttal, "A New Magnesium HPDC Alloy for Elevated Temperature Use," Proceedings of the 3rd International Magnesium Conference, ed. G. W. Lorimer, Manchester, UK, pp. 10-12, 1996.
- F. von Buch, S. Schumann, H. Friedrich, E. Aghion, B. Bronfin, B. L. Mordike, M. Bamberger, and D. Eliezer, "New Die Casting Alloy MRI 153 for Power Train Applications," Magnesium Technology 2002, pp. 61-68, 2002.
- M. C. Kang and K. Y. Sohn, "The Trend and Prospects of Magnesium Alloys Consumption for Automotive Parts in Europe," Proceedings of KSAE Autumn Conference, pp. 1569-1576, 2003.
- S. Schumann and H. Friedrich, "The Use of Mg in Cars Today and in Future," Conference Paper at Mg Alloys and Their Applications, Wolfsburg, Germany, 1998.
- W. Sebastian, K. Droder, and S. Schumann, "Properties and Processing of Magnesium Wrought Products for Automotive Applications," Conference Paper at Magnesium Alloys and Their Applications, Munich, Germany, 2000.
- S. Koike, K. Washizu, S. Tanaka, K. Kikawa, and T. Baba, "Development of Lightweight Oil Pans Made of a Heat-Resistant Magnesium Alloy for Hybrid Engines," SAE 2000-01-1117, 2000.
著作権:
本資料は、Shin, Chung, and Kangによる研究論文に基づいて要約を作成したものです。
無断での商業利用は禁止されています。
Copyright © 2024 CASTMAN. All rights reserved.