1. 概要
- タイトル: 高解像度多相シミュレーションを用いた大型ダイカスト部品の複合欠陥予測 (Combined defect prediction for large-area die-cast components using high-resolution multi-phase simulation)
- 著者: J. Jakumeit, Η Behnken, R Laqua, J. Gänz, L. Becker, M. Fehlbier, O. Middelmann
- 発表年: 2023年
- 発表学術誌/学会: IOP Conference Series: Materials Science and Engineering
- キーワード: 高圧ダイカストプロセス (HPDC), 多相シミュレーション, 鋳造欠陥, 気孔, 空気巻き込み, 凝固, 検証
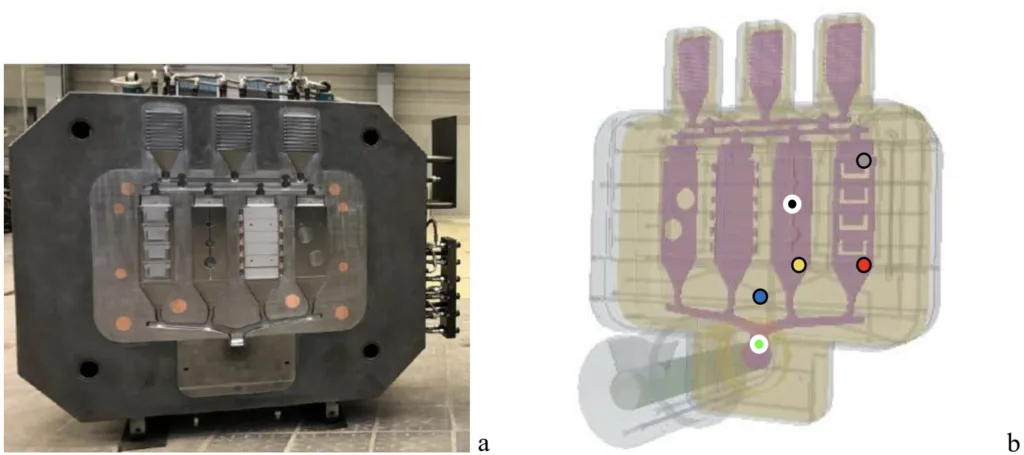
2. 研究背景
- 研究テーマの社会的/学術的背景:
- 自動車産業では、コストとエネルギーの節約のため、従来の溶接部品を単一のダイカスト部品に置き換える大型部品の製造傾向があります。
- 大型HPDC部品の場合、金型充填中の初期凝固が発生する可能性がある点が重要な課題です。
- コールドランニング、エアポケット、気孔などの鋳造欠陥は、空間的、時間的に分離できず、相互に影響を及ぼします。
- 既存研究の限界:
- 既存のダイカストシミュレーションモデルは、計算時間を短縮するために近似値を使用することがよくあります。
- 空気の影響や溶融凝固停止などの現象がモデルで単純化されて表現されます。
- 薄肉領域は、メッシュセル数の制限により正確に分析することが難しい場合があります。
- 既存の気孔モデルであるNiyama基準は、HPDCアプリケーションの気孔予測には適していないことが判明しています。
- 以前のモデルは、ガスと収縮気孔間の相互作用を単純化する傾向がありました。
- 研究の必要性:
- さまざまな鋳造欠陥間の相互作用を正確に描写するには、鋳造プロセスをより現実的にシミュレーションする必要があります。
- 空気を圧縮性ガスとして扱い、凝固による溶融流れの減少を考慮し、体積収縮による気孔形成を連成的に処理できる多相アプローチが必要です。
- このような多相アプローチを実際の鋳造実験および産業応用分野に適用して検証することが、実用的な活用に非常に重要です。
3. 研究目的および研究質問
- 研究目的:
- 高解像度多相シミュレーションを使用して、空気巻き込みと収縮気孔形成を連成的に予測する高圧ダイカスト (HPDC) アプリケーション向けの連成気孔モデルを開発し、検証することです。
- 主要な研究質問:
- 空気を圧縮性ガスとして、溶融凝固を多孔質媒体アプローチとして扱う多相シミュレーションアプローチは、大型ダイカスト部品の鋳造欠陥を正確に予測できるでしょうか?
- HPDCシミュレーションモデルで空気巻き込みと収縮気孔形成をどのように連成させて相互作用を考慮できるでしょうか?
- 溶融金属の供給が凝固によって制限される領域において、圧力計算と溶融金属の圧縮性に基づく連成気孔モデルは気孔形成を予測できるでしょうか?
- 開発された多相アプローチおよび連成気孔モデルは、実験的鋳造試験および産業応用分野とどの程度よく一致するでしょうか?
- 研究仮説:
- 圧縮性空気、凝固効果、連成気孔モデルを統合した多相シミュレーションアプローチは、単純化されたモデルと比較してHPDC鋳造欠陥をより現実的に予測できるでしょう。
- 凝固による圧力変化とガス蒸発を考慮する連成気孔モデルは、溶融金属の供給が制限された領域における収縮気孔形成を正確に予測するでしょう。
- 開発されたモデルを使用したシミュレーション結果は、実験的鋳造試験および産業ケーススタディとよく一致し、HPDCアプリケーションに対するモデルの妥当性を証明するでしょう。
4. 研究方法論
- 研究デザイン:
- 流体解析ソフトウェアSTAR-CCM+を用いたHPDCプロセスの多相シミュレーションアプローチの開発。
- 空気巻き込みと収縮気孔を考慮した連成気孔モデルの実装。
- 特別に設計されたテスト形状を用いた鋳造実験によるシミュレーションアプローチの検証。
- 検証されたモデルを産業用鋳造部品に適用。
- データ収集方法:
- GTKコールドチャンバーダイカストマシン (Bühler Carat 1400 t) とAlSi9Cu3合金を使用して実験的鋳造試験を実施しました。
- 鋳造サイクル中にテスト形状に配置された6つの熱電対を使用して温度測定値を収集しました。
- 産業応用分野の検証のために、鋳造品の気孔率をCTスキャンを使用して分析しました。
- 分析方法:
- シミュレーションで計算された温度曲線と測定された温度データを比較して、熱設定の有効性を検証しました。
- 予測された気孔位置と実験鋳造および産業部品で観察された気孔位置を質的に比較しました。
- 欠陥形成メカニズムを理解するために、シミュレーション結果から速度、空気分布、圧力、固相率、および気孔ガス分布を分析しました。
- 研究対象および範囲:
- ミスラン、コールドシャット、空気巻き込み、および気孔を調査するための4つのテストケース (2穴、ステップ、3カム、U字型プロファイル) を持つ特別に設計されたHPDCテスト形状。
- 詳細な気孔シミュレーションのためにテスト形状から抽出された単純化された3カム形状。
- 産業応用分野の検証のためのKSM Castings Group GmbHの産業構造部品。
- アルミニウムHPDCアプリケーションに焦点を当て、AlSi9Cu3合金を使用して検証。
5. 主な研究結果
- 主な研究結果:
- HPDC用の多相シミュレーションアプローチを開発しました。このアプローチは、空気と溶融金属を圧縮性流体として扱い、VoF (Volume of Fluid) 法とHRIC (High-Resolution-Interface-Capturing) スキームを使用してSTAR-CCM+でシャープな界面を捉えます。
- 空気巻き込みと収縮気孔の両方を予測するために、圧力蓄積、凝固、およびガス蒸発を考慮する連成気孔モデルを実装しました。
- シミュレーションアプローチは、計算された温度曲線と鋳造試験から得られた測定データを比較することにより検証され、良好な一致を示しました。「図2aは、熱電対位置で計算された温度曲線と測定結果を比較しています。」
- 連成気孔モデルを使用した3カム形状の高解像度シミュレーションは、実験結果と一致してカムの中央での気孔形成を予測しました。「図7は、4ステップ後の最終的な気孔分布を示しています。純粋な熱気孔モデルは、カムの中央付近に気孔を与えます…」および「気孔ガス分布とともに、図7は実際の鋳造で見つかった気孔を示しています。連成気孔モデルによる気孔予測は、実験結果とよく一致しています…」
- 産業用鋳造部品に適用した結果、シミュレーションはCTスキャンで特定された位置で収縮気孔を予測できましたが、いくつかの不一致が観察されました。「収縮気孔は、CTスキャン (図9cおよび9d) によって明らかにされた鋳造の2つの位置 (C5、B2、図9aおよび9bを参照) で特定されました。シミュレーションは、これまでのところ、これらの気孔位置を予測できませんでした。」そして後で「収縮気孔は、実際にはステップ4の終わりに純粋な熱気孔モデルによって2つの位置C5およびB2 (図9eおよび9f) で示されました。」
- シミュレーション結果は、適切に設計されたゲートシステムでは、収縮気孔が空気巻き込みによる気孔よりも優勢であることを示しています。「テストケースと産業アプリケーションの気孔予測を見ると、収縮気孔が空気巻き込みによる気孔よりも優勢です。」
- 統計的/質的分析結果:
- シミュレーションと測定された温度曲線間の質的一致が観察されました (図2a)。
- 3カム形状で予測された気孔位置と実験的に観察された気孔間の質的一致 (図7および図9)。
- 産業用鋳造におけるCTスキャンとシミュレーション結果間の気孔位置に関する質的比較 (図9)。
- データ解釈:
- 検証された多相シミュレーションアプローチと連成気孔モデルは、HPDCプロセスにおける温度分布と気孔形成を効果的に予測できます。
- 連成気孔モデルは、空気巻き込みと収縮気孔の間の複雑な相互作用を捉え、従来のモデルと比較して欠陥予測能力を向上させます。
- 高解像度多相シミュレーション方法論は、特に大型で複雑な部品のHPDCプロセスを理解し、最適化するための貴重なツールを提供します。
- モデルは実験とよく一致していますが、産業応用分野における気孔予測の精度を向上させるためには、さらなる改善が必要となる可能性があり、特にモデルの過敏性および現在の気孔モデルで扱われていない要因に関して改善が必要です。
- 図リスト:
- 図 1: 可動金型の内側 (a) と、2穴、ステップ、3カム、U字型プロファイル (b) の4つのテストケースを持つ形状、およびa) に示されているもの
- 図 2: 6つの測定ポイント (a) (図1b参照) で測定および計算された温度曲線の比較と、較正された温度依存HTC (b)
- 図 3: 簡単な入口と出口 (a) と、2.4 Mioセル、部品領域に1.8 Mioセルを持つ高解像度メッシュを備えた3カムテスト形状。溶融物/金型界面での高い速度と温度勾配の解像度には、3つのプリズムレイヤーが使用されました。
- 図 4: 充填ステップの終わりに0.055秒後の速度 (a) と巻き込まれた空気 (b) の分布。
- 図 5: 加圧ステップの終わりに0.1秒後の速度 (a) と巻き込まれた空気 (b) の分布。
- 図 6: 連成流れと凝固ステップの終わりに1.1秒後の固相率 (a)、速度 (b)、圧力 (c)、および気孔率 (d) の分布。
- 図 7: 連成気孔モデルと実験結果による気孔予測の比較。
- 図 8: 形状 a)、多面体メッシュ b)、0.75秒後の充填中の温度と溶融物の分布 c)、および完全充填と加圧後の空気巻き込み d)。
- 図 9: CT分析 (c) および (d) によって明らかにされた鋳造の2つの位置C5 (a) およびB2 (b) における気孔率を示す産業用HPDCアプリケーション、および位置C5 (e) およびB2 (f) に対する連成シミュレーションモデルによる気孔予測。
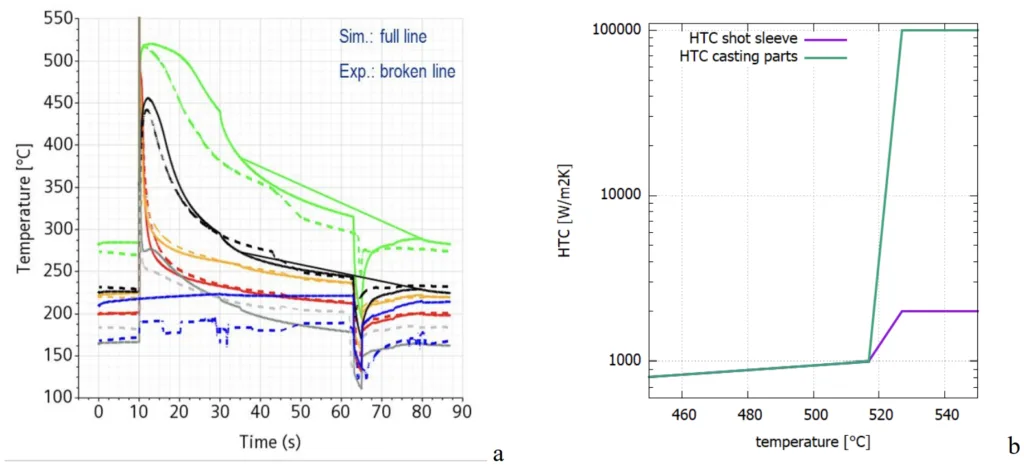
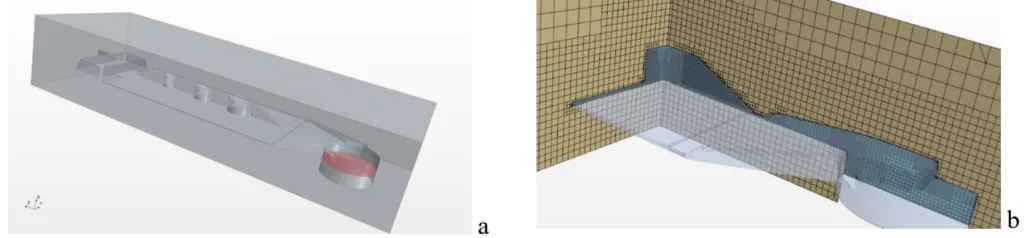
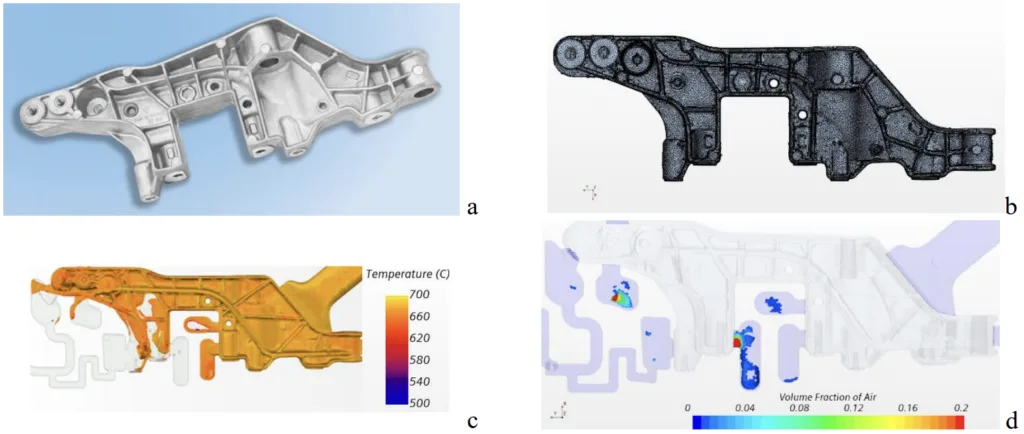
6. 結論と考察
- 主な結果の要約:
- 本研究では、空気巻き込みと収縮気孔の予測のための連成気孔モデルを組み込んだHPDC用の多相流および凝固シミュレーションアプローチを開発し、検証することに成功しました。
- このモデルは、液体溶融物とガスを圧縮性流体として扱い、温度依存性粘度と多孔質媒体アプローチを使用して溶融流に対する凝固効果を考慮し、圧力変化とガス蒸発に基づいて気孔形成をシミュレーションします。
- 実験的鋳造試験および産業応用分野に対する検証は、HPDC部品における温度分布と気孔形成を予測するモデルの能力を実証しました。
- 研究の学術的意義:
- 本研究は、鋳造欠陥をより現実的かつ包括的に予測するアプローチを提供することにより、ダイカストシミュレーション技術の進歩に貢献します。
- 連成気孔モデルは、空気巻き込みと収縮気孔の間の複雑な相互作用に対処し、従来のモデルと比較して欠陥予測の精度を向上させます。
- 高解像度多相シミュレーション方法論は、特に大型で複雑な部品のHPDCプロセスを理解し、最適化するための貴重なツールを提供します。
- 研究の実践的意義:
- 検証されたシミュレーションアプローチは、ダイカストエンジニアがプロセスパラメータ、金型設計、およびゲートシステムを最適化して、鋳造欠陥を最小限に抑え、部品品質を向上させるために使用できます。
- 気孔やその他の欠陥を正確に予測することにより、モデルはスクラップ率を削減し、プロセス開発時間を短縮し、HPDC製造の全体的な効率を向上させるのに役立ちます。
- 産業応用分野は、実際の鋳造問題を解決し、高品質のダイカスト部品の生産を改善するモデルの可能性を実証しています。
- 研究の限界:
- モデルは実験データとよく一致していますが、産業応用分野における気孔予測には依然として不一致があり、さらなる改善の余地があることを示唆しています。
- モデルは特定のパラメータに過敏である可能性があり、一部のケースでは気孔を過剰に予測する可能性があります。
- Beckermann [13] が言及したように、現在の気孔モデルで明示的に扱われていない要因が、シミュレーション予測と実際の鋳造結果の間の差異に寄与している可能性があります。
7. 今後のフォローアップ研究
- 今後の研究方向:
- 産業応用分野における精度と堅牢性を向上させるために、連成気孔モデルをさらに改良します。
- モデルの過敏性と、潜在的なキャリブレーションまたはモデルパラメータの調整を調査します。
- Beckermann [13] などによって特定された、HPDC気孔形成に影響を与える追加の要因をモデルに組み込みます。
- より広範囲の鋳造形状、合金、およびプロセス条件でモデルをさらに検証します。
- 高解像度多相シミュレーションの産業現場でのより広範な採用を可能にするために、シミュレーション時間を短縮するより効率的な計算方法を開発します。
- さらなる探求が必要な領域:
- ガス蒸発の臨界圧力レベルとその材料特性およびプロセス条件への依存性に関する詳細な調査。
- 溶融物に溶解した水素または空気が気孔形成およびガス蒸発に及ぼす影響の研究。
- HPDCにおける多相流シミュレーションの精度をさらに向上させるための高度な乱流モデルと界面捕捉技術の探求。
- ダイカストエンジニアによる連成気孔モデルの適用を容易にするためのユーザーフレンドリーなシミュレーションツールとガイドラインの開発。
8. 参考文献
- [1] Duan H Z, Shen J N, & Li Y P (2012). Comparative analysis of HPDC process of an auto part with ProCAST and FLOW-3D. In Applied Mechanics and Materials (Vol. 184, pp. 90-94). Trans Tech Publications Ltd.
- [2] Bodhayana M R and Ramesha N 2014 Int. J. Research in Engineering and Technology 03 (11) 1163
- [3] Aghion E, Moscovitch N and Arnon A (2007). The correlation between wall thickness and properties of HPDC Magnesium alloys. Materials Science and Engineering: A, 447(1-2), 341-346.
- [4] Wang T, Huang J, Fu H, Yu K and Yao S (2022). Influence of Process Parameters on Filling and Feeding Capacity during High-Pressure Die-Casting Process. Applied Sciences, 12(9), 4757.
- [5] Simcenter STAR-CCM+: https://www.plm.automation.siemens.com/global/de/products/simcenter/STAR-CCM.html
- [6] Jana S, Kättlitz O, Hediger F, Jakumeit J and Aguilar J (2012). MCWASP XIII, IOP Publishing, IOP Conf. Series: Materials Science and Engineering.
- [7] Stefanescu, D. M. (2005). Computer simulation of shrinkage related defects in metal castings-a review. International Journal of Cast Metals Research, 18(3), 129-143.
- [8] Beech J, Barkhudarov M, Changands K, Chin B (1998) in ‘Modelling of casting, welding and advanced solidificationprocesses VIII', (ed. B. G. Thomas and C. Beckerman), 1071; Warrendale, PA, TMS.
- [9] Jakumeit J, Behnken H, Laqua R, Mbewou S, Fehlbier M, Gänz J, & Becker, L. (2021). Coupled Modeling of Misrun, Cold Shut, Air Entrainment, and Porosity for High-Pressure Die Casting Applications. In Light Metals 2021 (pp. 865-870). Springer, Cham.
- [10] Niyama T, Uchida M, Morika W A, Saito S (1982) Int. cast metals journal 7:52-63
- [11] Carlson K D and Beckermann C (2009). Metallurgical and Materials Transactions A, 40(1), 163-175.
- [12] Jakumeit, J., Jana, S., Böttger, B., Laqua, R., Jouani, M. Y., & Bührig-Polaczek, A. (2012, January). In IOP Conference Series: Materials Science and Engineering (27, No. 1, p. 012066). IOP Publishing.
- [13] Beckermann C and Monroe A 2009 Porosity simulation for high pressure die castings Die Casting Engineer (The North American Die Casting Association) ISSN 0012-25JX
- [14] Carlson K D, Lin Z and Beckermann C (2007). Modeling the effect of finite-rate hydrogen diffusion on porosity formation in aluminum alloys. Metallurgical and Materials Transactions B, 38(4), 541-555.
- [15] Khalajzadeh V, Goettsch, D D and Beckermann C (2016). In Shape Casting: 6th International Symposium (pp. 35-42). Springer, Cham
- [16] Khalajzadeh V and Beckermann C (2020). Simulation of shrinkage porosity formation during alloy solidification. Metallurgical and Materials Transactions A, 51(5), 2239-2254.
- [17] Ferziger J H and Peric M (ed) 2002 Computational Methods for Fluid Dynamics (McGraw-Hill) ISBN 2-540-42074-6
- [18] Teskeredzic A, Demirdzic I and Muzaferija S 2002 Num. Heat Trans. B 42 43
- [19] Demirdzic I and Muzaferija S 1995 Computer Methods in Appl. Mech. and Eng. 125 235-255.
- [20] Muzaferija S and Peric M 1999 Computation of free surface flows using interface-tracking and interface-capturing methods. Nonlinear Water Wave Interaction, ed O Mahrenholtz and M. Markiewicz, (Southampton: WIP Press) 59-100
- [21] Sabau S and Viswanath S 2002 Met. Mat. Trans. B 33B 131
- [22] Poirier D R (1987). Permeability for flow of interdendritic liquid in columnar-dendritic alloys. Metallurgical Transactions B, 18(1), 245-255.Poirier D R, Yeum K and Mapples A L 1987 Metall. Mater. Trans. A 18 1979
- [23] Jakumeit, J., Subasic, E., & Bünck, M. (2016). Prediction of misruns in thin wall castings using computational simulation. In Shape Casting: 5th International Symposium 2014 (pp. 253-260). Springer International Publishing.
9. 著作権
- 本資料は、J. Jakumeit, Η Behnken, R Laqua, J. Gänz, L. Becker, M. Fehlbier, O. Middelmannの論文「高解像度多相シミュレーションを用いた大型ダイカスト部品の複合欠陥予測 (Combined defect prediction for large-area die-cast components using high-resolution multi-phase simulation)」に基づき作成されました。
- 論文ソース: http://dx.doi.org/10.1088/1757-899X/1281/1/012027
本資料は上記の論文に基づいて要約されたものであり、商業目的での無断使用は禁止されています。
Copyright © 2025 CASTMAN. All rights reserved.