本記事では、ResearchGateで発行された論文「New Generation of Brake Callipers to Improve Competitiveness and Energy Savings in Very High Performance Cars」をご紹介します。
1. 概要:
- タイトル: New Generation of Brake Callipers to Improve Competitiveness and Energy Savings in Very High Performance Cars (高性能車の競争力と省エネを向上させる新型ブレーキキャリパー)
- 著者: Ivano Gattelli, Gianluigi Chiarmetta, Marcello Boschini, Renzo Moschini, Mario Rosso, Ildiko Peter
- 出版年: 2014年9月
- 出版ジャーナル/学会: Solid State Phenomena
- キーワード: semi-solid casting (半凝固鋳造), rheocasting (レオキャスティング), brake callipers (ブレーキキャリパー), ceramic cores (セラミックコア), high performance cars (高性能車)
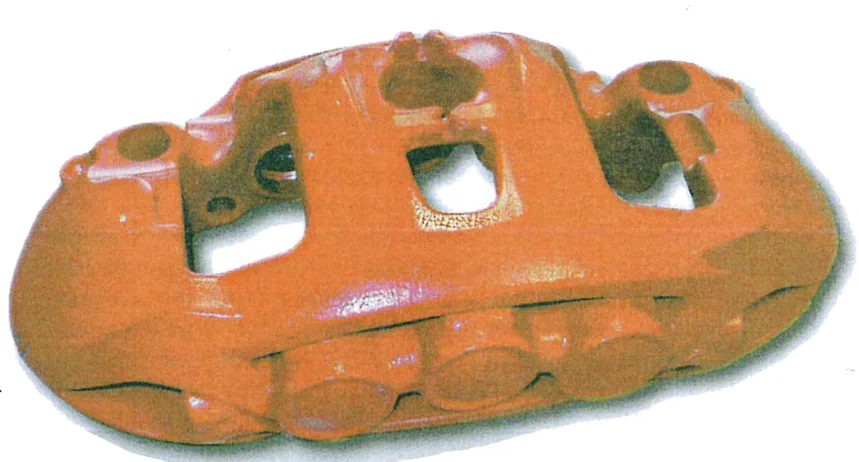
2. 概要または序論
近年の材料科学および製造プロセス研究は、エネルギー消費と軽量化に焦点が当てられています。軽合金と半凝固プロセスは、自動車および航空宇宙産業への応用において有望な技術として浮上しました。効果的な微細構造制御は、部品の機械的挙動にとって非常に重要です。鍛造は最適な方法ですが、コストも最も高くなります。鋳造はより経済的ですが、欠陥が発生する可能性があります。半凝固プロセスは、鋳造と鍛造の間のギャップを埋め、欠陥制御を改善します。スクイズキャスティング、チクソフォーミング、レオキャスティングなどの新しい半凝固法は、鍛造と同等の特性を持つ部品を製造できます。半世紀にわたる開発にもかかわらず、より詳細なレオロジーデータが必要です。これらのプロセスは、欠陥を減らし、表面品質と寸法精度を向上させます。主要な課題は、研究室の技術を手頃な価格での大量生産に移転することです。本論文では、高性能産業部品、特にブレーキキャリパーの競争力と省エネを向上させるために、特殊セラミックロストコアを使用したレオキャスティングプロセスのさらなる最適化段階を紹介します。この方法は、重力鋳造と比較して、機械的特性と美的特性を向上させながら、適切な強度を維持し、高性能車および将来の応用分野での使用を促進します。
3. 研究背景:
研究テーマの背景:
本研究は、特に産業用自動車および航空宇宙用途において、材料科学および製造プロセスにおけるエネルギー消費と軽量化に対する要求の高まりという背景の下で行われています。軽合金と半凝固プロセスは、これらの要求を満たす有望なソリューションとして特定されています。微細構造の制御は、製造された部品の機械的挙動を決定する上で非常に重要であることが強調されています。
既存研究の現状:
鍛造は高性能部品の製造に最適な方法として認識されていますが、最もコストのかかる方法でもあります。鋳造技術は経済的にはより競争力がありますが、伝統的にボイド、空洞、介在物、酸化物などの欠陥が発生しやすく、鍛造と同等の性能レベルを達成できません。半凝固プロセスは、このギャップを埋め、改善された欠陥制御を提供する手段として浮上しています。既存の研究では、スクイズキャスティング、チクソフォーミング、レオキャスティングなどの半凝固法を探求し、新しい製造ルートを通じて鍛造に匹敵する性能を達成しようとしています。しかし、これらのプロセスをさらに最適化するためには、より詳細なレオロジーデータに対する継続的なニーズがあります。
研究の必要性:
過去半世紀にわたる半凝固鋳造における著しい進歩にもかかわらず、これらのプロセスを最適化するためには、追加の、より詳細なレオロジーデータに対する需要が依然として存在します。研究室から産業界への技術移転は、手頃な価格での大量生産のための中心的な課題のままです。特にブレーキキャリパーのような高性能自動車用途において、競争力と省エネを向上させるために生産プロセスを最適化する必要があります。本研究は、高性能部品の大量生産に適したレオキャスティングプロセスをさらに開発および最適化することにより、これらのニーズに対処することを目的としています。
4. 研究目的と研究課題:
研究目的:
本研究の主な目的は、最適化されたレオキャスティングプロセスを使用して新世代のブレーキキャリパーを開発することにより、高性能車の競争力と省エネを向上させることです。これには、ブレーキキャリパーに適切な強度を維持しながら、重力鋳造と比較して、機械的特性の向上と優れた美的特性を達成することが含まれます。
主要な研究:
主要な研究は、レオキャスティングプロセスを使用したブレーキキャリパーの製造と、製造プロセスにおける特殊セラミックロストコアの実装に焦点を当てています。本研究では、これらのレオキャストブレーキキャリパーの機械的特性、微細構造、および大量生産の可能性を調査します。
5. 研究方法
研究デザイン:
本研究では、ブレーキキャリパー製造のためのレオキャスティングプロセスの開発と最適化に焦点を当てた実験的デザインを採用しています。これには、ATS Companyによって開発された革新的なレオキャスティングプロセスと、TCS垂直油圧プレスRotorone 400トンモデルを使用することが含まれます。プロセスでは、A357合金とセラミックロストコアを使用します。
データ収集方法:
データは、以下を通じて収集されました。
- 放射線透過分析: サンプルの完全性を検証し、欠陥を検出するため。
- 微細構造特性評価: 光学顕微鏡(OM、Zeiss Observer Dimモデル)を使用して、製造されたキャリパーの微細構造を分析するため。
- 機械的特性評価: 引張試験(Galdabini Sun 5モデル)を含めて機械的特性を評価し、非破壊検査(NDT、Bosello SRE MAX 225 KVtype)によって健全性を研究するため。
分析方法:
分析方法は以下を含みました。
- 微細構造の比較: 重力鋳造およびレオキャスティングによって製造されたブレーキキャリパーの微細構造を比較します。
- 機械的特性の評価: 引張試験データを分析して、レオキャストサンプルの強度と伸びを評価し、標準要件(UNI EN 1706/2010)と比較します。
- 放射線透過画像分析: 放射線透過画像を解釈して、鋳造品の欠陥を特定および評価します。
研究対象と範囲:
研究対象は、セラミックロストコアを用いたレオキャスティングプロセスによってA357アルミニウム合金を使用して製造されたブレーキキャリパーです。研究の範囲は、これらのブレーキキャリパーの大量生産のためのレオキャスティングプロセスを最適化し、それらの機械的および美的特性を評価することに焦点を当てています。
6. 主な研究結果:
主要な研究結果:
- セラミックコアを使用したレオキャスティングプロセスが、ブレーキキャリパーの製造に成功裏に実装されました。
- レオキャストブレーキキャリパーは、重力鋳造キャリパーの樹枝状微細構造とは対照的に、球状で微細な微細構造を示しました(Figure 2)。
- セラミックコアを使用して、剛性、曲げ、圧縮強度に関して、機械的特性が向上しました。
- 重力鋳造と比較して、優れた美的特性が得られました。
- 従来の方法と比較して、約5%の軽量化が達成されました。
- レオキャストA357 T6合金の引張試験結果は、砂型鋳造およびチル鋳造A357 T6熱処理合金の標準要件(UNI EN 1706/2010)を上回りました(Table 2)。
- 放射線透過分析により、レオキャスト部品の欠陥が減少したことが明らかになりました(Figure 3)。
- 検証ベンチテストと厳しい制動サイクルテストにより、わずかな欠陥が存在する場合でも、レオキャスト部品の高い破壊靭性と信頼性が実証されました。
提示されたデータの分析:
- Table 1は、ブレーキキャリパーの製造に使用されたA357合金の化学組成(重量%)を示しており、Si、Fe、Cu、Mn、Mg、Zn、Ti、およびAlの重量パーセントを指定しています。
- Table 2は、UTS(340±14 MPa)、耐力(302±4 MPa)、伸び(4.135±2.7%)を含む、レオキャストA357 T6サンプルの平均引張特性を示しています。これらの値は、砂型鋳造およびチル鋳造A357 T6熱処理合金の標準要件(UNI EN 1706/2010)と比較されており、測定値が標準閾値を超えていることを示しています。
- Figure 1は、レオキャスティングプロセスを使用して製造されたBremboブレーキキャリパーの写真です。
- Figure 2は、重力鋳造(a)およびレオキャスティング(b)によって製造されたブレーキキャリパーの微細構造を比較しており、(a)では樹枝状構造を、(b)では球状で微細な微細構造を示しています。
- Figure 3は、ブレーキキャリパーの放射線透過画像であり、調査対象のサンプルに有意な欠陥がないことを明らかにしています。
- Figure 4は、「最悪の場合」の鋳造品からのスクラップの微細構造を示しており、いくつかの欠陥(ビフィルム)の存在を示しています。
Figure名リスト:
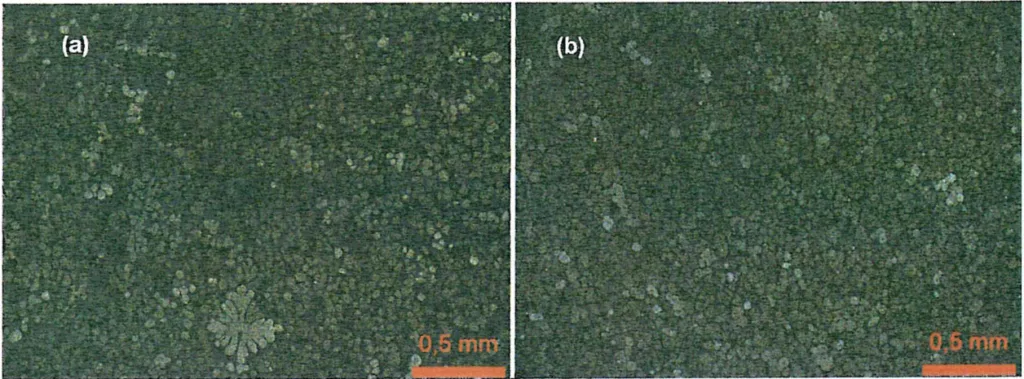
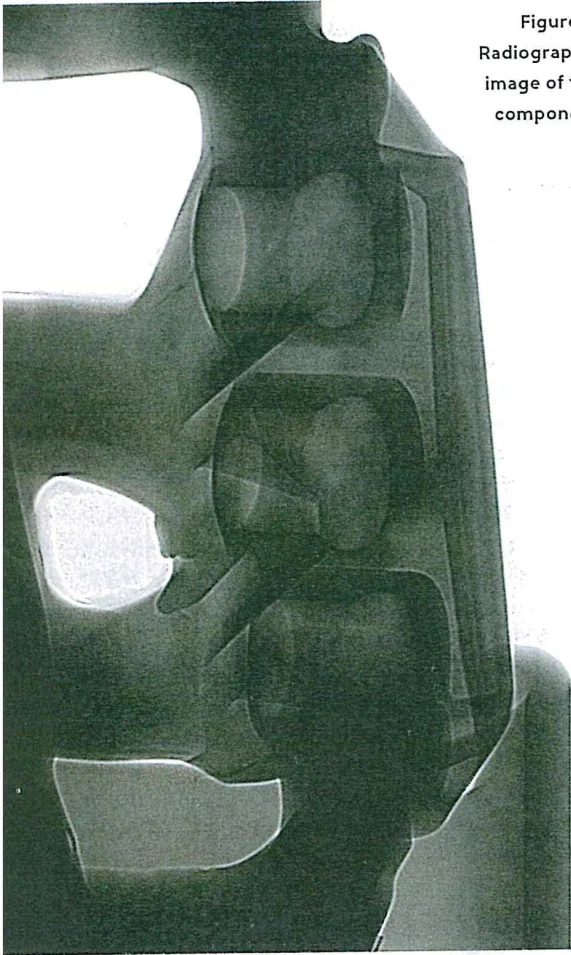
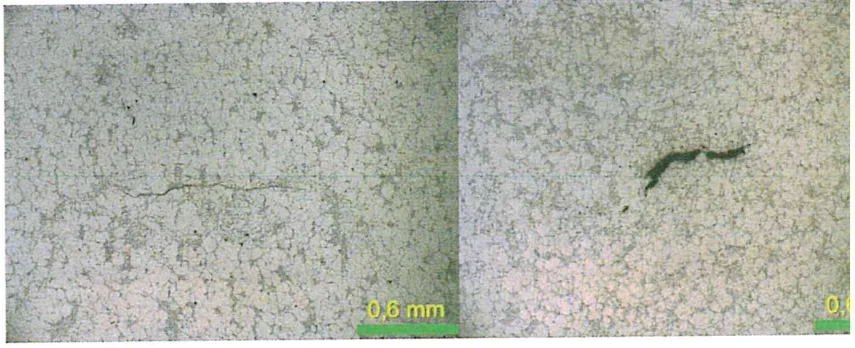
- Figure 1: Photograph of the produced Brembo brake calliper (製造されたBremboブレーキキャリパーの写真)
- Figure 2: Microstructure of the brake calliper produced by gravity casting process (a) and by rheocasting process (b) (重力鋳造プロセス(a)およびレオキャスティングプロセス(b)によって製造されたブレーキキャリパーの微細構造)
- Figure 3: Radiographic image of the component (部品の放射線透過画像)
- Figure 4: Microctructures of scraps showing the presence of some defects (bifilms) (いくつかの欠陥(ビフィルム)の存在を示すスクラップの微細構造)
7. 結論:
主な調査結果の要約:
本研究では、セラミックロストコアを使用した最適化されたレオキャスティングプロセスによる新世代ブレーキキャリパーの製造に成功しました。レオキャストキャリパーは、重力鋳造部品と比較して、微細構造の改善、機械的特性の向上、優れた美観、および軽量化を示しました。セラミックコアを使用することで、複雑な形状と構造的完全性の向上が可能になりました。試験により、わずかな欠陥があっても、高い破壊靭性と信頼性が確認されました。
研究の学術的意義:
本研究は、高性能自動車部品の製造におけるレオキャスティングおよびセラミックコア技術の応用に関するさらなる洞察を提供することにより、学術分野に貢献しています。半凝固プロセスが鋳造と鍛造の間の性能ギャップを縮小する上で効果的であることを実証しています。また、本研究は、レオキャストA357合金の機械的特性と微細構造に関する貴重なデータを提供し、半凝固冶金における知識体系を拡充します。
実用的な意味:
本研究の実用的な意味は、自動車産業、特に高性能車製造にとって重要です。開発されたレオキャスティングプロセスは、エネルギー効率と競争力が向上した軽量で高性能なブレーキキャリパーの大量生産のための実行可能なルートを提供します。セラミックコアを使用することで、より複雑で最適化された設計が可能になり、ブレーキシステムの性能と美観が向上します。
研究の限界と今後の研究分野:
本論文では、研究の限界や今後の研究分野を明示的に述べていません。ただし、暗黙のうちに、今後の研究は以下に焦点を当てる可能性があります。
- さまざまな合金および部品形状に対するレオキャスティングプロセスパラメータのさらなる最適化。
- 実世界の運転条件下でのレオキャストブレーキキャリパーの長期耐久性と性能の調査。
- 従来の方法と比較したセラミックコアとレオキャスティングを使用した大量生産の費用対効果の調査。
- このプロセスの他の高性能自動車部品および産業への応用拡大。
8. 参考文献:
- [1] Campbell F.C., Manufacturing technology for aerospace structural materials. Elsevier; 2006.
- [2] Warren A.S., Developments and challenges for aluminium - A Boeing perspective. Mater Forum 2004, 28 pp. 24-31.
- [3] Blanco M.I., The economics of wind energy. Renewable and Sustainable Energy Reviews 2009, 13, pp. 1372-1382.
- [4] Atkinson H.V., Liu D., (2008) "Microstructural coarsening of semi-solid aluminium alloys" Materials Science and Engineering A, Volume 496, 1-2, 25, pp. 439-446.
- [5] Barnes H., (1997) "Thixotropy - a review", Journal of Non-Newtonian Fluid Mechanics, 70, pp.1-33.
- [6] Cetin, A., Kalkanli, A., (2009) " Investigation of microporosity formation mechanisms in A356 aluminium alloy castings", International Journal of Microstructure and Materials Properties, Vol. 4, No.3, pp.377-385.
- [7] Curle U. A., Govender G., (2010), "Semi-solid rheocasting of grain refined aluminum alloy 7075", Transaction of nonferrous metals. Society of China 20, pp 832-836.
- [8] Rosso M., Peter I., Villa, R., (2008), "Effects of T5 and T6 heat treatments applied to rheocast A356 parts for automotive applications", Journal of Solid State Phenomena Vol. 141-143, pp. 237-242.
- [9] Rosso M., Peter I., "New frontiers for thixoforming", International Journal of Microstructure and Materials Properties, Vol. 8, Issue 1-2, 2013, pp. 113-124
- [10] Zhen Z., Ma Qian, Ji S., Fan Z., "The effects of rheo-diecasting on the integrity and mechanical properties of Mg-6Al-1Zn", Scripta Materialia 54 (2006), 207-211, ISSN 1359-6462.
- [11] Kaufmann H., Wabusses H., Uggowitzer J., "Aspects of the NRC semi-solid casting technology", Journal of Metallurgical and processing Technology, vol. 76, no1-2, pp. 70-75.
- [12] Rosso, M., Peter, I., Chiarmetta, G., Gattelli, 1., (2010), "Development of industrial components by advanced squeeze casting", Proceedings of the 11th International Conference on Semi-Solid Processing of Alloys and Composites, Beijing, 16th - 18th September.
- [13] Rosso M., Peter I., Chiarmetta G., Gatelli I., "Extremely light weight rheocast components for auto motive", Diffusion and Defect Data Pt.B: Solid State Phenomena 192-193, 2012, pp. 545-550.
- [14] Moschini R., Molina R., "Production of hollow components in high pressure die casting through the use of ceramic cores". HTDC, Vicenza Feb 2012.
- [15] Campbell J., Castings 2nd edn., pp. 443-452; 2003, Oxford, Butterworth-Heinemann.
- [16] Campbell J., Casting practice, 2004, Oxford, Butterworth Heinemann.
9. 著作権:
- この資料は、"[Ivano Gattelli]"氏の論文:「New Generation of Brake Callipers to Improve Competitiveness and Energy Savings in Very High Performance Cars」に基づいています。
- 論文ソース: DOI: 10.4028/www.scientific.net/SSP.217-218.471
この資料は上記の論文に基づいて要約されたものであり、商業目的での無断使用は禁止されています。
Copyright © 2025 CASTMAN. All rights reserved.