この要約は、ブルネル大学の博士号論文として提出されたFeng Yan氏の「Development of High Strength Al-Mg2Si-Mg Based Alloy for High Pressure Diecasting Process(高圧ダイカストプロセス用高強度Al-Mg2Si-Mg系合金の開発)」論文に基づいています。
1. 概要:
- タイトル: Development of High Strength Al-Mg2Si-Mg Based Alloy for High Pressure Diecasting Process (高圧ダイカストプロセス用高強度Al-Mg2Si-Mg系合金の開発)
- 著者: Feng Yan (フォン・ヤン)
- 発表年: 2013年10月
- 発表ジャーナル/学会: ブルネル大学 博士号論文
- キーワード: アルミニウム合金、軽量材料、自動車産業、燃費向上、CO2排出削減、高圧ダイカスト (HPDC)、Al-Mg2Si合金、ダイソルダー問題、亜共晶合金、過剰Mg、機械的特性、凝固、微細組織、自動車部品
2. 研究背景:
自動車産業では、燃費向上とCO2排出量削減のため、アルミニウム合金のような軽量材料の利用が増加しています。高圧ダイカスト (HPDC) は、ニアネットシェイプのエンジニアリング部品を経済的かつ迅速に製造する方法であり、現在、鋳造アルミニウム合金の製造量の約80%を占めています。HPDCプロセスによる構造部品の製造需要の増加に伴い、自動車産業向けの高強度アルミニウム合金が必要となっています。Al-Mg2Si合金は、Mg2Si粒子によって優れた強度を発揮することで知られていますが、深刻なダイソルダーリング問題のため、HPDCプロセスへの適用は制限されています。さらに、Al-Mg2Si合金に関する既存の研究は、主に過共晶組成に焦点を当てており、亜共晶合金に関する情報は不足しています。一般的に、Al合金の機械的特性は、合金組成、部品の欠陥レベル、および鋳造および熱処理プロセスによって主に制御される微細組織によって決定されます。HPDCプロセスの高い冷却速度は、ダイカストされたAl-Mg2Si合金の微細組織を微細化し、機械的特性を向上させる可能性があります。したがって、HPDCプロセスに適した高強度Al-Mg2Si系合金の開発は、高品質の自動車部品製造にとって非常に重要です。
3. 研究目的と研究課題:
本研究は、HPDCプロセス用のAl-Mg2Si系合金の開発に焦点を当てています。主な研究目的は、HPDCダイカストに適した、機械的特性が向上した高強度アルミニウム合金をAl-Mg2Si系合金に基づいて開発することです。主な研究課題は以下の通りです。
- 過剰なMg添加は、亜共晶Al-Mg2Si合金の微細組織と機械的特性にどのように影響するか、また、凝固、微細組織、機械的特性の関係は何か?
- 高強度と妥当な延性を両立するAl-Mg2Si-Mg合金の最適組成は何か?
- マンガン添加は、Al-Mg2Si-Mg合金の強度と延性のバランスにどのような影響を与えるか?
- ZnやCuなどの合金元素は、Al-Mg2Si-Mg系合金の凝固、微細組織、機械的特性にどのような影響を与えるか?
- 鉄不純物は微細組織と機械的特性にどのような影響を与えるか、また、鉄不純物の許容限界はどの程度か?
- 熱処理は合金の機械的特性にどのような影響を与えるか、特に溶体化処理と時効処理が微細組織と機械的特性に与える影響に焦点を当てる。
本研究では、過剰なMgが亜共晶Al-Mg2Si系を改質して機械的特性を向上させることができ、戦略的な合金化と熱処理によってHPDC用途に適するように合金性能をさらに向上させることができると仮説を立てています。
4. 研究方法
本研究では、熱力学的計算とHPDC実験的検証を組み合わせた合金開発アプローチを採用しました。
- 研究デザイン: CALPHAD (CALculation of PHAse Diagrams) 熱力学計算に導かれた実験的合金開発と特性評価。
- データ収集方法: 合金を製造し、高圧ダイカスト (HPDC) を適用しました。光学顕微鏡、走査型電子顕微鏡 (SEM)、透過型電子顕微鏡 (TEM) を使用して微細組織を特性評価しました。引張試験と硬さ試験を通じて機械的特性を評価しました。
- 分析方法: CALPHAD計算を用いて、相形成と凝固挙動を予測しました。微細組織分析には、画像分析、SEM/EDXによる組成分析、TEMによる詳細な析出物特性評価が含まれていました。合金元素添加と熱処理が機械的特性データに与える影響を統計的に分析しました。
- 研究対象と範囲: 本研究は、Al-Mg2Si系合金、特に過剰なMg (2-8wt.%)、Mn (0-1wt.%)、Fe (0-2wt.%)、Zn (0-5wt.%)、Cu (0-1.5wt.%) の添加量を変化させた亜共晶組成に焦点を当てました。研究範囲には、鋳造状態および熱処理 (急速T6熱処理) 条件での合金の調査が含まれていました。
5. 主な研究結果:
本研究では、HPDC用の高強度Al-Mg2Si-Mg合金の開発に関して、いくつかの重要な知見が得られました。
- 過剰Mgの影響: 亜共晶Al-Mg2Si合金中の過剰Mgは、共晶組成をより低いMg2Si含有量にシフトさせました。実験的トライアルでは、Al-8Mg2Si-6Mg合金が、鋳造状態のHPDC鋳物において、強度と延性の最適な組み合わせを提供することが示されました。
- Mn添加の影響: Al-8Mg2Si-6Mg合金に0.6wt.% Mnを添加すると、鋳造状態において、耐力189MPa、UTS 350MPa、伸び6.5%を示し、特性がさらに向上しました。
- Fe不純物の影響: Al-8Mg2Si-6Mg合金は、Fe不純物に対して比較的高い耐性を示し、Fe含有量が1.6wt.%であっても伸びが5%のレベルを維持しました。
- CuとZnの影響: Al-8Mg2Si-6Mg-0.6Mn合金へのCu添加 (0.31wt.%~0.92wt.%) は、耐力をわずかに増加させましたが、UTSと伸びを減少させ、これは熱間割れが原因であると考えられます。亜鉛添加 (最大4.3wt.%) は、特に急速T6熱処理後に引張強度を劇的に増加させました。
- 最適化された合金と熱処理: 急速T6熱処理 (490°Cで15分間の溶体化処理、180°Cで90分間の時効処理) を施したAl-8Mg2Si-6Mg-0.6Mn-4.3Zn合金は、耐力345MPa、UTS 425MPa、伸び3.2%を達成しました。
- 図表リスト:
- Fig. 2.1 Graphical illustration of hot chamber diecasting [5].
- Fig. 2.2 Graphical illustration of cold chamber diecasting [5].
- Fig. 2.3 Heterogeneous nucleation of a spherical cap on a flat substrate [43].
- Fig. 2.4 Schematic illustration of a portion of hypothetical binary phase diagram[43].
- Fig. 2.5 Illustration of principles for constitutional undercooling in constrained grown[45]. Solute rejection at the crystal interface and simultaneous release of latent heat of fusion generates a constitutional zone.
- Fig. 2.6 Hydrogen solubility in liquid pure aluminium and binary aluminium alloys at 1 atm. hydrogen partial pressure [49].
- Fig. 2.7 The equilibrium phase diagram of binary Al-Si alloy [69].
- Fig. 2.8 Mechanical properties of Al-Si alloy as a function of Si content in the alloy [71].
- Fig. 2.9 Crystal structure of Mg2Si.
- Fig. 2.10 Calculated equilibrium phase diagram of pseudo-binary Al-Mg2Si alloy [36].
- Fig. 2.11 Effect of cooling rate on the morphology of primary Mg2Si phase in a wedge casting from top to tip zone (a)-(d), the tip part has the highest cooling rate of ~1000°C/s [84].
- Fig. 2.12 Microstructure of the diecast Al-5Mg-2Si-0.6Mn alloy [94].
- Fig. 2.13 The effect of Mg on the transition reactions and corresponding temperatures of A390 alloys [95]. Critical points are at 4.2% and 7.2% Mg. The shaded zone shows the solidification interval of Mg2Si intermetallic phase for different Mg.
- Fig. 2.14 TEM images of (a) the as-cast structure showing large θ' precipitates and (b) the T6 treated structure, showing well distributed fine θ' precipitates in an A 380 alloy [106].
- Fig 3.1 The interactive interface in the CumpuThermal Pandat 8.2 software.
- Fig. 3.2 The interactive interface in the CumpuThermal Pandat 8.2 software for the 2D section calculation.
- Fig. 3.3 The interactive interface in the CumpuThermal Pandat 8.2 software for the solidification calculation and the calculation options.
- Fig. 3.4 The photo of the electric resistance furnace and the clay-graphite crucible used in the current study.
- Fig. 3.5 (a) Photo of the degassing machine used in experiments and (b) schematic diagram of the rotary degassing process.
- Fig. 3.6 The optical mass spectroscopy for alloy composition analysis.
- Fig. 3.7 The Frech DAK450-54 cold chamber HPDC machine used in experiments
- Fig. 3.8 Illustrate of the effective sleeve length [130].
- Fig. 3.9 Diagram of diecastings for the standard tensile testing samples of cast aluminium alloys according to the specification defined in the ASTM B557-06. The overflow and biscuit are designed in association with the cold chamber diecasting machine and the dimensions are in mm [131].
- Fig. 3.10 The programed injection velocity and pressure profiles for the Frech DAK450-54 450 tone cold chamber HPDC machine
- Fig. 3.11 The actual injection profiles of the piston forwarding along the shot sleeve and the pressure with the time after trigged at 430mm during HPDC process.
- Fig. 3.12 (a) Graphical illustration of the cutting position for the microstructure observation, and (b) the photo of Bakelite mounted specimens.
- Fig. 3.13 (a) The photo of the Buehler SimpliMet 1000 machine for sample Bakelite mounting, and (b) the photo of the Buehler Automat 250 machine.
- Fig. 3.14 The photo of Zeiss Optical Microscope (OM) with an AxioCam MRC digital camera.
- Fig. 3.15 The interactive interface of the automatic measurement program in the“Axioshop 2MaT0” software.
- Fig. 3.16 The photo of Zeiss Supera 35 FEG scanning electron microscope (SEM) equipped with an energy dispersive X-ray spectrometer (EDX) facility.
- Fig. 3.17 The photo of GEOL 2100F type transmission electron microscope.
- Fig. 3.18 The photo of Instron® 5569 universal materials testing machine.
- Fig. 3.19 The photo of CHV-10MD digital Vickers hardness tester
- Fig. 4.1 Sectional equilibrium phase diagram showing the effect of Mg on the eutectic point, reaction temperature in Al-Mg2Si system.
- Fig. 4.2 Effect of excess Mg on the phase formation of (a) Al-8wt.%Mg2Si alloy and (b) Al-10wt.% Mg2Si alloy.
- Fig.4.3 Effect of excess Mg on the solidification range of Al-Mg2Si alloys.
- Fig 4.4 Effect of excess Mg on the solid fraction of different phases in (a) Al-8Mg2Si alloy, (b) Al-10Mg2Si alloy, and (c) Al-13Mg2Si alloy.
- Fig.4.5 Optical micrographs showing the effect of excess Mg on the as-cast microstructure of Al-8Mg2Si alloy, (a) to (d) are with 2wt.%, 4wt.% , 6wt.% and 8wt.% excess Mg, respectively.
- Fig.4.6 Optical micrographs showing the effect of excess Mg on the as-cast microstructure of Al-10Mg2Si alloy, (a) to (d) are with 2wt.%, 3.7wt.% , 6wt.% and 8wt.% excess Mg, respectively.
- Fig. 4.7 Optical micrographs showing the effect of excess Mg on the as-cast microstructure of Al-13Mg2Si alloy, (a) to (d) are with 0.7wt.%, 2wt.%, 4wt.% , and 6wt.% excess Mg, respectively.
- Fig. 4.8 Quantification of the solid fraction of primary phases in (a) Al-8Mg2Si-Mg, (b) Al-10Mg2Si-Mg, and (c) Al-13Mg2Si-Mg alloys with different levels of excess Mg contents.
- Fig. 4.9 Quantification of the average size of primary phases in the Al-Mg2Si alloys with different levels of excess Mg, (a) Al-8Mg2Si-Mg (b) Al-10Mg2Si-Mg, and (c) Al-13Mg2Si-Mg.
- Fig. 4.10 SEM Backscattered electron image showing the effect of excess Mg on the eutectic morphology in Al-Mg2Si-Mg alloys, (a) eutectic microstructure of Al-8Mg2Si-4Mg alloy formed in the shot sleeve, (b) eutectic microstructure of Al-8Mg2Si-4Mg alloys solidified in the die cavity (c) eutectic microstructure of Al-8Mg2Si-6Mg alloy solidified in the shot sleeve, and (d) eutectic microstructure of Al-8Mg2Si-6Mg alloy solidified in the die cavity.
- Fig.4.11 SEM Backscattered electron image showing the Fe-rich and AlMg phases in Al-Mg2Si-Mg alloys.
- Fig 4.12 Effect of excess Mg on the porosity level in the Al-Mg2Si-Mg alloys.
- Fig.4.13 Effect of excess Mg on the mechanical properties of (a) Al-8Mg2Si-xMg, (b) Al-10Mg2Si-xMg, and (c) Al-13Mg2Si-xMg alloys under as-cast condition.
- Fig.4.14 Cross section of the equilibrium phase diagram of the Al-8Mg2Si-6Mg-xMn alloy.
- Fig. 4.15 Effect of Mn on the solidification range of the Al-8Mg2Si-6Mg alloy.
- Fig. 4.16 Backscattered SEM micrographs showing the microstructure of Al-8Mg2Si-6Mg alloy with different levels of Mn, (a) 0.19wt.% Mn, (b) 0.41wt.% Mn,(c) 0.6wt.% Mn, and (d) 0.78wt.%.
- Fig. 4.17 Effect of Mn on (a) the solid fraction of Mn-rich intermetallic phase, (b) the average size of Mn-rich intermetallics, and (c) porosity levels in Al-8Mg2Si-6Mg-xMn alloys.
- Fig 4.18 Backscattered SEM micrograph showing the morphology of Mn-rich intermetallics in the Al-8Mg2Si-6Mg alloy (a) 0.19wt.% Mn, and (b) 0.78wt.% Mn.
- Fig. 4.19 Mechanical properties of the Al-8Mg2Si-6Mg alloy with different levels of Mn under as-cast condition.
- Fig.4.20 Crosse section of the equilibrium phase diagram of the Al-8Mg2Si-6Mg-xFe alloy.
- Fig 4.21 Effect of Fe on the solidification range of the Al-8Mg2Si-6Mg-xFe alloy.
- Fig. 4.22 SEM Backscattered electron image showing the microstructure of the Al-8Mg2Si-6Mg alloy with different amount of Fe, (a) 0.3wt.% Fe, (b) 0.6wt.% Fe, (c) 1.2wt.% Fe, (d) 1.6wt.% Fe.
- Fig. 4.23 SEM Backscattered electron image showing the eutectic morphology in the Al-8Mg2Si-6Mg alloy with varied Fe, (a) 0.3wt.% Fe, (b) 0.6wt.% Fe, and (c) 1.6wt.% Fe.
- Fig. 4.24 Quantification of the solid fraction of Fe-rich phases in the Al-8Mg2Si-6Mg alloy with different levels of Fe content.
- Fig 4.25 Effect of Fe on the size of Fe-rich intermetallic phases in the Al-8Mg2Si-6Mg alloy.
- Fig 4.26 Effect of Fe on the porosity level in the Al-8Mg2Si-6Mg alloys.
- Fig. 4.27 Mechanical properties of the Al-8Mg2Si-6Mg alloy with different levels of extra Fe content under as-cast condition.
- Fig. 4.28 Equilibrium phase diagrams showing the effect of Fe content on the phase formation in (a) Al-8Mg2Si-6Mg-0.6Mn alloy, and (b) Al-8Mg2Si-6Mg-1Mn alloy.
- Fig 4.29 Effect of Fe content on the solidification range of (a) Al-8Mg2Si-6Mg-0.6Mn alloy, and (b) Al-8Mg2Si-6Mg-1Mn alloy
- Fig.4.30 shows the as-cast microstructure of Al-8Mg2Si-6Mg-0.6Mn alloy with different Fe contents.
- Fig. 4.31 Quantification of the solid fraction of Fe-rich phases in the Al-8Mg2Si-6Mg-0.6Mn-xFe alloys.
- Fig. 4.32 Effect of Fe in the Al-8Mg2Si-6Mg-0.6Mn alloy on (a) the solid fraction of Fe-rich phases, and (b) the average size of Fe-rich intermetallic phases solidified in the shot sleeve.
- Fig. 4.33 Effect of Fe in the Al-8Mg2Si-6Mg-0.6Mn alloy on (a) the average size, (b) the frequency of Fe-rich intermetallic phases solidified in the die cavity.
- Fig. 4.34 Effect of Fe on the porosity level in the Al-8Mg2Si-6Mg-0.6Mn alloy.
- Fig. 4.35 SEM Backscattered electron image showing the morphology of Fe intermetallics in the Al-8Mg2Si-6Mg-0.6Mn alloy with different levels of Fe, (a) 0.3wt.% and (b) 1.8 wt.% Fe.
- Fig 4.36 Mechanical properties of the Al-8Mg2Si-6Mg-0.6Mn alloy with different levels of Fe content under as-cast condition.
- Fig. 4.37 Cross section of the equilibrium phase diagram of the Al-8Mg2Si-6Mg-0.6Mn-xZn alloy.
- Fig. 4.38 Effect of Zn on the solidification range of the Al-8Mg2Si-6Mg-0.6Mn alloy.
- Fig. 4.39 Effect of Zn on the non-equilibrium solidification of Al-8Mg2Si-6Mg-0.6Mn alloy.
- Fig. 4.40 SEM Backscattered electron image showing the microstructure of the Al-8Mg2Si-6Mg-0.6Mn alloy with different amount of Zn, (a), 1.2wt.% Zn (b)2.3wt.% Zn, (c) 3.2wt.% Zn, and (d) 4.3wt.% Zn.
- Fig. 4.41 Effect of Zn on the solid fraction of Zn-rich intermetallics in the Al-8Mg2Si-6Mg-0.6Mn alloy.
- Fig. 4.42 SEM Backscattered electron image showing the morphology of the AlMgZn intermetallics in the Al-8Mg2Si-6Mg-0.6Mn-4.3Zn alloy.
- Fig. 4.43 Effect of Zn on the porosity level in the Al-8Mg2Si-6Mg alloy.
- Fig. 4.44 Mechanical properties of the Al-8Mg2Si-6Mg-0.6Mn alloy with varied Zn under as-cast condition.
- Fig. 4.45 Cross section of the equilibrium phase diagram of the Al-8Mg2Si-6Mg-0.6Mn-xCu system.
- Fig. 4.46 Effect of Cu content on the solidification range of the Al-8Mg2Si-6Mg-0.6Mn alloy.
- Fig. 4.47 Effect of Cu on the non-equilibrium solidification of the Al-8Mg2Si-6Mg-0.6Mn alloy.
- Fig 4.48 SEM Backscattered electron image showing the microstructure of the Al-8Mg2Si-6Mg-0.6Mn alloy with different amount of Cu , (a) 0.31wt.% Cu, (b) 0.52wt.% Cu (c) 0.73wt.% Cu, and (d) 0.92wt.% Cu.
- Fig. 4.49 Effect of Cu on the solid fractions of Cu-rich intermetallics in the Al-8Mg2Si-6Mg-0.6Mn alloy.
- Fig. 4.50 SEM Backscattered electron image showing the morphology of AlMgCu intermetallic phase in the Al-8Mg2Si-6Mg-0.6Mn-0.9Cu alloy.
- Fig. 4.51 Effect of Cu on the porosity level in the Al-8Mg2Si-6Mg-0.6Mn alloy.
- Fig. 4.52 SEM Backscattered electron image showing the hot tearing formed in the Al-8Mg2Si-6Mg-0.6Mn-Cu alloys with (a) 0.7wt.% Cu, and (b) 0.92wt.% Cu.
- Fig. 4.53 Mechanical properties of the Al-8Mg2Si-6Mg-0.6Mn-Cu alloy with different levels of Cu under as-cast condition.
- Fig. 4.54 The surface quality of the diecast tensile samples for the evaluation of solution treatment.
- Fig. 4.55 The representative micrographs showing the porosity levels in the quick solution treated samples of the Al-8Mg2Si-6Mg-0.6Mn-4.3Zn alloy, (a) level 1 showing no obvious porosity, (b) level 2 showing that the porosity is visible but less than 50 µm, (c) level 3 showing that the
- Fig. 4.56 The relationship between the semi-macro hardness (HV) and the ageing time in the Al-8Mg2Si-6Mg-0.6Mn-0.43Zn alloy at (a) 160°C and (b) 180°C.
- Fig 4.59 The hardness on a cross section of the diecast Al-8Mg2Si-6Mg-0.6Mn-4.3Zn alloy from the surface to the centre, (a) under as-cast condition (b) after solution treatment at 490°C for 15 mins.
- Fig. 4.60 SEM Backscattered electron image showing the detailed microstructure of the Al-8Mg2Si-6Mg-0.6Mn-4.3Zn alloy (a) under as-cast condition and without solution treatment, (b) solution heat treated at 480°C for 15 mins, and (c) solution heat treated at 490 °C for 15 mins.
- Fig. 4.61 Effect of Zn content on the mechanical properties of the Al-8Mg2Si-6Mg-0.6Mn-xZn alloy after solution treatment at 490oC for 15mins.
- Fig. 4.62 The tensile test curves of the Al-8Mg2Si-6Mg-0.6Mn-4.3Zn alloy before and after solution treatment at 490oC for 15mins.
- Fig. 4.63 Semi-macro hardness (HV) of the Al-8Mg2Si-6Mg-0.6Mn-xZn alloys as a function of ageing time at ageing temperature of (a) 160 °C and (b) 180 °C.
- Fig. 4.64 Effect of Zn on the mechanical properties of the Al-8Mg2Si-6Mg-0.6Mn-xZn alloy after solution treated at 490°C for 15mins and aged at 180 °C for 90 min.
- Fig. 4.65 SEM Backscattered electron image showing the microstructure of the Al-8Mg2Si-6Mg-0.6Mn-4.3Zn alloy near the surface of samples (a) with and (b) without ageing treatment after solution treated at 490oC for 15 mins.
- Fig. 4.66 TEM micrographs showing the precipitates of AlMgZn phase in the primary α-Al phase of the Al-8Mg2Si-6Mg-0.6Mn-xZn alloy,(a) 0wt. % Zn under as-cast condition,(b) 0 wt. % Zn under solution and aged condition, (c) 2.3wt. % Zn under as-cast condition, (d) 2.3wt. % Zn under solution and aged condition, (e) 4.3wt. % Zn under as-cast condition, (f) 4.3wt. % Zn under solution and aged condition.
- Fig. 5.1 Calculated horizontal isothermal phase diagram of Al-Mg-Si system at 592°C. The dash line represents the weight percentage of Mg:Si at 1.73:1.
- Fig. 5.2 The calculated weight fraction ratio of α-Al:Mg2Si in the eutectics of Al-Mg2Si alloys with different levels of excess Mg.
- Fig. 5.3 The concentration variation of different elements during the non-equilibrium solidification of Al-8Mg2Si-6Mg-0.6Mn-xZn alloys , (a) 1.2wt.% Zn, (b)2.3wt.% Zn, (c) 3.2wt.% Zn, and (d) 4.3wt.% Zn.
- Fig. 5.4 The concentration variation of different elements during the non-equilibrium solidification of Al-8Mg2Si-6Mg-0.6Mn-xCu alloys, (a) 0.31wt.% Cu, (b) 0.52wt.% Cu, (c) 0.73wt.% Cu, and (d) 0.92wt.% Cu.
- Fig. 5.5 Schematic illustration of the solidification route of the Al-Mg2Si-Si alloy [20].
- Fig. 5.6 SEM Backscattered electron image showing Al halo around the primary Mg2Si phase in the Al-13Mg2Si-2Mg alloy solidified under as cast condition.
![Fig. 2.2 Graphical illustration of cold chamber diecasting [5].](https://castman.co.kr/wp-content/uploads/image-223-png.webp)
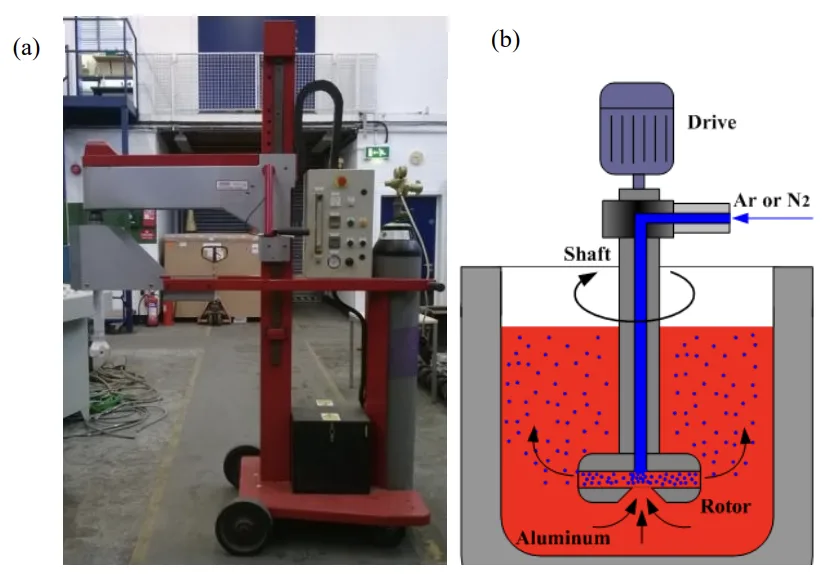
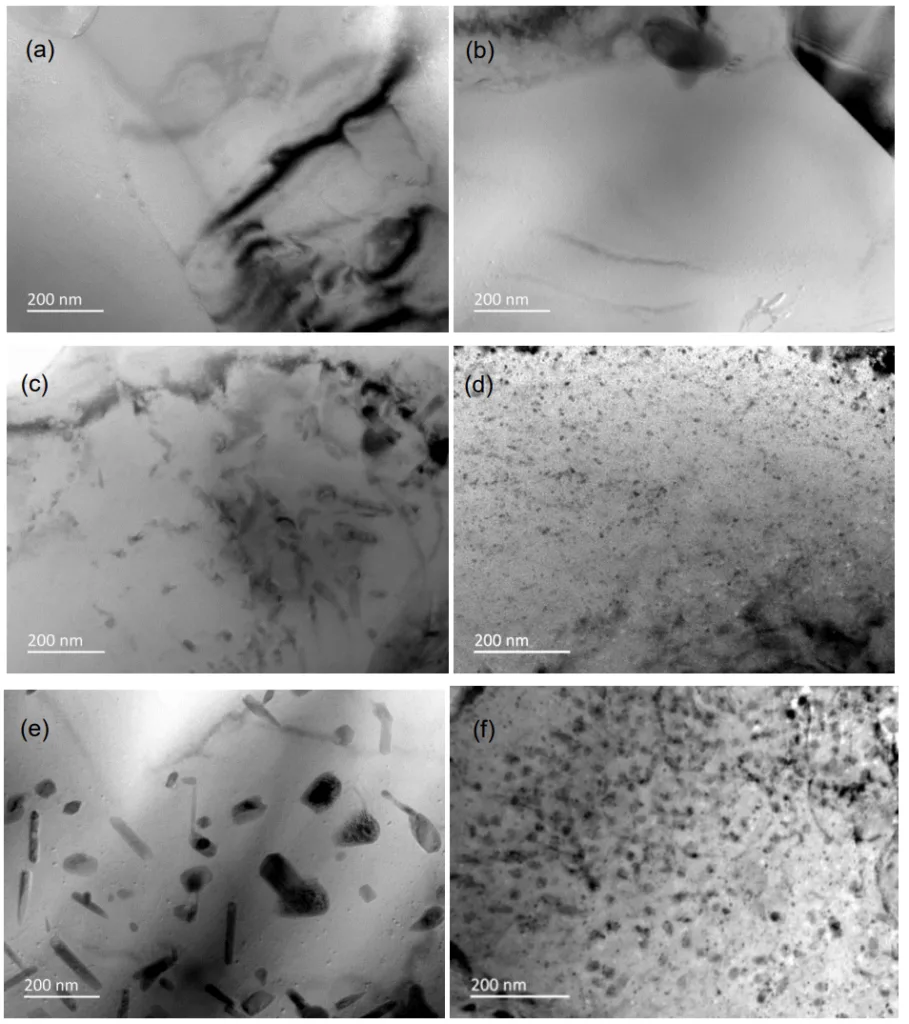
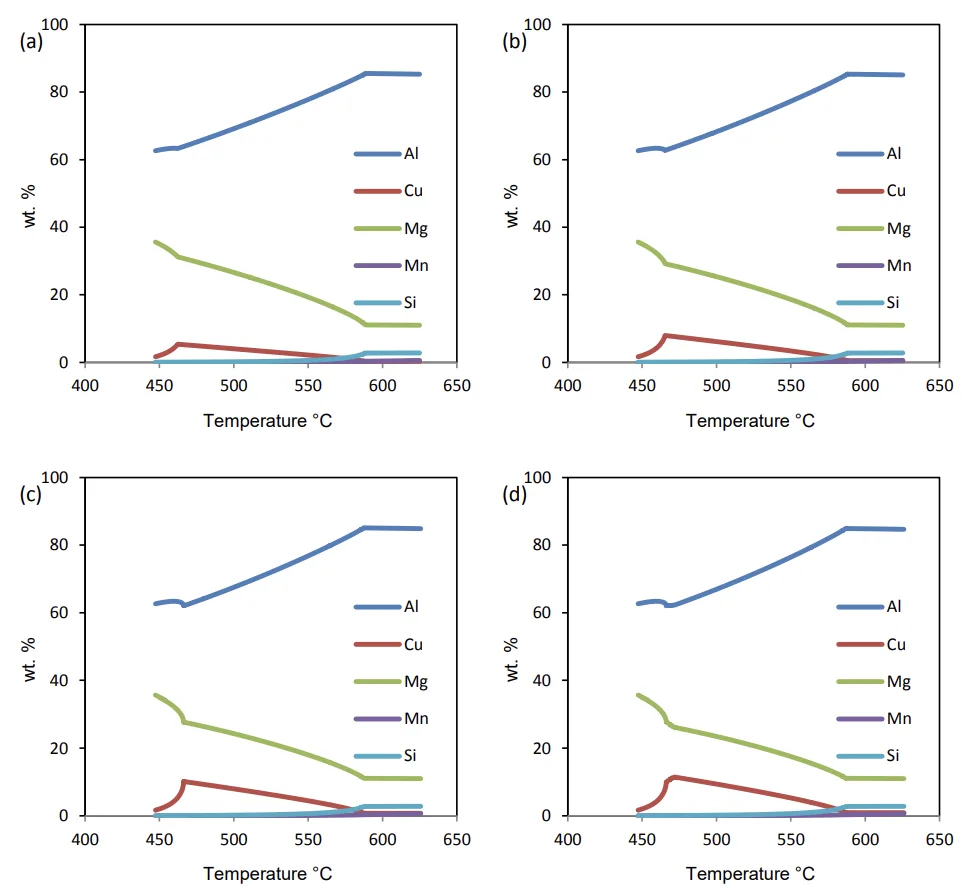
6. 結論と考察:
本研究では、HPDC用の高強度Al-Mg2Si系アルミニウム合金の開発に成功しました。本研究では、過剰なMg含有量と、MnおよびZnの戦略的な合金元素添加、および急速T6熱処理を組み合わせることで、亜共晶Al-Mg2Si合金の機械的特性を大幅に向上させることができることを実証しました。
- 主な結果の要約: HPDCおよび急速T6熱処理プロセスを経たAl-8Mg2Si-6Mg-0.6Mn-4.3Zn合金は、優れた耐力、UTS、および妥当な延性の組み合わせを示し、自動車構造部品の有望な候補材料となります。
- 学術的意義: 本研究は、HPDC条件下でのAl-Mg2Si-Mg合金の凝固挙動と微細組織発達に関する基礎的な理解に貢献します。また、過剰なMgと合金元素が相形成と機械的特性に与える影響に関する貴重な洞察を提供します。
- 実用的意義: 開発された合金は、軽量で高強度の材料に対する自動車産業の需要に対する実用的なソリューションを提供します。特に急速T6処理後のダイカスト性と向上した機械的特性により、高品質の自動車構造部品の製造に適しており、軽量化と燃費向上につながる可能性があります。
- 研究の限界: 本研究は、特定の合金組成と加工パラメータに焦点を当てています。より広範囲な組成を調査し、熱処理パラメータを最適化し、長期性能と工業規模での拡張性を評価するために、さらなる研究が必要です。
7. 今後のフォローアップ研究:
論文で示唆されている今後の研究方向は以下の通りです。
- 密度をさらに低減し、合金の流動性を最適化するために、Mg含有量が高くSi含有量が低いAl合金の研究。
- 鋳造中の過熱が微細組織と機械的特性に与える影響の研究。
- Ti、Ni、Cr、Sr、Naなどの微量合金元素の影響の探求。
- 機械的特性を潜在的に向上させるための共晶組織のさらなる微細化。
- Feリッチ金属間化合物とAl3Mg2相間の界面の詳細なTEM分析。
- ピーク時効状態での析出相を特定するための、Zn添加量を変化させたAl-8Mg2Si-6Mg-0.6Mn合金における析出の詳細なTEM調査。
8. 参考文献:
- Green, J. A. S. 2007. Aluminum recycling and processing for energy conservation and
sustainability, Materials Park, Ohio, ASM International. - Nadca 2009. Aluminum Cast Alloys: Enabling Tools for Improved Performance, NADCA,
NADCA. - Butler, W. A. 2008. High-Pressure Die Casting. ASM handbook: Vol 15 Casting. United
States of American: ASM International, Materials Park, OH : ASM International. - Ji, S., Wang, Y., Watson, D. & Fan, Z. 2013. Microstructural Evolution and Solidification
Behavior of Al-Mg-Si Alloy in High-Pressure Die Casting. Metallurgical and Materials
Transactions A, (1). - Vinarcik, E. J. 2003. High integrity die casting processes, New York, Wiley.
- Twarog, D. 2011. State of the Die Casting Industry Available:
http://www.diecasting.org/information/soi/soi2012.pdf. - Qin, Q. D., Li, W. X., Zhao, K. W., Qiu, S. L. & Zhao, Y. G. 2010. Effect of modification
and aging treatment on mechanical properties of Mg2Si/Al composite. Materials Science
and Engineering: A, 527(9), 2253-2257. - Cao, W., Chen, S. L., Zhang, F., Wu, K., Yang, Y., Chang, Y. A., Schmid-Fetzer, R. &
Oates, W. A. 2009. PANDAT software with PanEngine, PanOptimizer and
PanPrecipitation for multi-component phase diagram calculation and materials property
simulation. Calphad, 33(2), 328-342. - Apelian, D. 2004. High integrity aluminum die casting (Alloys, processes, & melt
preparation) Rosemount, IL : North American Die Casting Association, North American
Die Casting Association. - Wang, L., Makhlouf, M. & Apelian, D. 1995. Aluminium die casting alloys: alloy
composition, microstructure, and properties-performance relationships. International
Materials Reviews, 40(6), 221-238. - Barekar, N. S., Dhindaw, B. K. & Fan, Z. 2010. Improvement in silicon morphology and
mechanical properties of Al–17Si alloy by melt conditioning shear technology.
International Journal of Cast Metals Research, 23(4), 225-230. - Tzamtzis, S., Zhang, H., Hari Babu, N. & Fan, Z. 2010. Microstructural refinement of
AZ91D die-cast alloy by intensive shearing. Materials Science & Engineering: A, 527(12),
2929-2934. - Gunasegaram, D. R., Givord, M. O., Donnell, R. G. & Finnin, B. R. 2008. Improved
Quality and Reduced Cost through ATM High Pressure Die Casting. Die casting engineer,
52(1), 42-47. - Thirugnanam, M. 2013. Modern High Pressure Die-Casting Processes for Aluminium
Castings. Indian Foundry Journal, 59(7), 36-41. - Schmid, E. E., Von Oldenburg, K. & Frommeyer, G. 1990. Microstructure and properties
of as-cast intermetallic Mg2Si-Al alloys. Zeitschrift für Metallkunde 81. - Frommeyer, G., Beer, S. & Von Oldenburg, K. 1994. Microstructure and mechanical
properties of mechanically al-loyed intermetallic Mg2Si-Al alloys. Zeitschrift für
Metallkunde 85(4), 372. - Zhang, J., Fan, Z., Wang, Y. & Zhou, B. 1999. Microstructural refinement in Al–Mg2Si in
situ composites. Journal of Materials Science Letters, 18(10), 783-784. - Li, C., Liu, X. & Wu, Y. 2008. Refinement and modification performance of Al–P master
alloy on primary Mg2Si in Al–Mg–Si alloys. Journal of Alloys and Compounds, 465(1–2),
145-150. - Li, C., Wu, Y., Li, H. & Liu, X. 2009. Microstructural formation in hypereutectic Al–
Mg2Si with extra Si. Journal of Alloys and Compounds, 477(1–2), 212-216. - Zhang, J., Fan, Z., Wang, Y. Q. & Zhou, B. L. 2000. Microstructural evolution of the in
situ Al-15wt.%Mg2Si composite with extra Si contents. Scripta Materialia, 42(11), 1101- - Zhao, Y. G., Qin, Q. D., Zhao, Y. Q., Liang, Y. H. & Jiang, Q. C. 2004. In situ Mg2Si/Al–
Si composite modified by K2TiF6. Materials Letters, 58(16), 2192-2194. - Qin, Q. D., Zhao, Y. G., Xiu, K., Zhou, W. & Liang, Y. H. 2005. Microstructure evolution
of in situ Mg2Si/Al–Si–Cu composite in semisolid remelting processing. Materials Science
and Engineering: A, 407(1–2), 196-200. - Zhao, Y. G., Qin, Q. D., Zhou, W. & Liang, Y. H. 2005. Microstructure of the Ce modified in situ Mg2Si/Al–Si–Cu composite. Journal of Alloys and Compounds, 389(1–2),
L1-L4. - Qin, Q. D., Zhao, Y. G., Zhou, W. & Cong, P. J. 2007. Effect of phosphorus on
microstructure and growth manner of primary Mg2Si crystal in Mg2Si/Al composite.
Materials Science and Engineering: A, 447(1–2), 186-191. - Hadian, R., Emamy, M., Varahram, N. & Nemati, N. 2008. The effect of Li on the tensile
properties of cast Al–Mg2Si metal matrix composite. Materials Science and Engineering:
A, 490(1–2), 250-257. - Azarbarmas, M., Emamy, M., karamouz, M., Alipour, M. & Rassizadehghani, J. 2011. The
effects of boron additions on the microstructure, hardness and tensile properties of in situ
Al–15%Mg2Si composite. Materials & Design, 32(10), 5049-5054. - Emamy, M., Jafari Nodooshan, H. R. & Malekan, A. 2011. The microstructure, hardness
and tensile properties of Al–15%Mg2Si in situ composite with yttrium addition. Materials
& Design, 32(8–9), 4559-4566. - Emamy, M., Khorshidi, R. & Raouf, A. H. 2011. The influence of pure Na on the
microstructure and tensile properties of Al-Mg2Si metal matrix composite. Materials
Science and Engineering: A, 528(13–14), 4337-4342. - Khorshidi, R., Honarbakhsh Raouf, A., Emamy, M. & Campbell, J. 2011. The study of Li
effect on the microstructure and tensile properties of cast Al–Mg2Si metal matrix
composite. Journal of Alloys and Compounds, 509(37), 9026-9033. - Ghorbani, M. R., Emamy, M. & Nemati, N. 2011. Microstructural and mechanical
characterization of Al–15%Mg2Si composite containing chromium. Materials & Design,
32(8–9), 4262-4269. - Nasiri, N., Emamy, M. & Malekan, A. 2012. Microstructural evolution and tensile
properties of the in situ Al–15%Mg2Si composite with extra Si contents. Materials &
Design, 37, 215-222. - Georgatis, E., Lekatou, A., Karantzalis, A. E., Petropoulos, H., Katsamakis, S. & Poulia, A.
- Development of a Cast Al-Mg2Si-Si In Situ Composite: Microstructure, Heat
Treatment, and Mechanical Properties. Journal of Materials Engineering and Performance,
1-13. - Li, H. T., Scamans, G. & Fan, Z. y. 2013. Refinement of the Microstructure of an Al Mg2Si Hypereutectic Alloy by Intensive Melt Shearing. Materials Science Forum, 765, 97-
- Emamy, M., Emami, A. R. & Tavighi, K. 2013. The effect of Cu addition and solution
heat treatment on the microstructure, hardness and tensile properties of Al–15%Mg2Si–
0.15%Li composite. Materials Science and Engineering: A, 576, 36-44. - Zhao, Y. h., Wang, X. b., Du, X. h. & Wang, C. 2013. Effects of Sb and heat treatment on
the microstructure of Al-15.5wt%Mg2Si alloy. International Journal of Minerals,
Metallurgy, and Materials, 20(7), 653-658. - Zhang, J., Fan, Z., Wang, Y. Q. & Zhou, B. L. 2000. Microstructure and mechanical
properties of in situ Al-Mg2Si composites. materials science and technology, 16, 913-918. - Kaye, A. & Street, A. 1982. Die Casting Metallurgy, London UK, Butterworths Scientific.
- Upton, B. 1982. Pressure diecasting. Pt.1, Metals, machines, furnaces, Headinton Hill
Hall, Oxford OX30BW, England, Pergamon Press Ltd. - Butler, B. 2001. Die casting handbook Rosemont, IL : North American Die Casting
Association, North American Die Casting Association. - Laukli, H. I. S. P. L. 2012. Recent Developments in Aluminum High Pressure Die Casting.
Die casting engineer, 56(3), 20-23. - Fan, Z., Xia, M., Zhang, H., Liu, G., Patel, J. B., Bian, Z., Bayandorian, I., Wang, Y., Li, H.
T. & Scamans, G. M. 2009. Melt conditioning by advanced shear technology (MCAST)
for refining solidification microstructures. International Journal of Cast Metals Research,
22(1-4), 103-107. - Rometsch, P. A., Arnberg, L. & Zhang, D. L. 1999. Modelling dissolution of Mg2Si and
homogenisation in Al-Si-Mg casting alloys. International Journal of Cast Metals Research,
12(1), 1-8. - Porter, D. A. & Easterling, K. E. 1992. Phase transformations in metals and alloys,
London; New York, Chapman & Hall. - Chen, S. L., Daniel, S., Zhang, F., Chang, Y. A., Yan, X. Y., Xie, F. Y., Schmid-Fetzer, R.
& Oates, W. A. 2002. The PANDAT software package and its applications. Calphad,
26(2), 175-188. - Hartman, P. 1973. Crystal growth: an introduction, Amsterdam; New York, North Holland Pub. Co.; American Elsevier.
- Kaufman, J. G., Rooy, E. L. & American Foundry, S. 2004. Aluminum alloy castings
properties, processes, and applications, Materials Park, OH, ASM International. - Eskin, D. G., Suyitno & Katgerman, L. 2004. Mechanical properties in the semi-solid state
and hot tearing of aluminium alloys. Progress in Materials Science, 49(5), 629-711. - Couture, A. 1981. Iron in aluminium casting alloys – a literature survey. AFS International
Cast Metals Journal,, 6(4), 9-17. - Fruehan, R. J. 2008. Gases in metal. ASM handbook: Vol 15 Casting. ASM International,
Materials Park, OH : ASM International. - Chaijaruwanich, A., Lee, P. D., Dashwood, R. J., Youssef, Y. M. & Nagaumi, H. 2007.
Evolution of pore morphology and distribution during the homogenization of direct chill
cast Al–Mg alloys. Acta Materialia, 55(1), 285-293. - Campbell, J. 2006. Entrainment defects. Materials Science & Technology, 22(2), 127-145.
- Arnberg, L. 2008. Castability-Fluidity and Hot Tearing. ASM handbook: Vol 15 Casting.
United States of American: ASM International, Materials Park, OH : ASM International. - Bishop, H. F., Ackerlind, C. G. & Pellini, W. S. 1957. Investigation of Metallurgical and
Mechanical Effects in the Development of Hot Tearing. AFS Trans, 65, 247-258. - Sjölander, E. & Seifeddine, S. 2010. The heat treatment of Al–Si–Cu–Mg casting alloys.
Journal of Materials Processing Technology, 210(10), 1249-1259. - Gourlay, C. M., Laukli, H. I. & Dahle, A. K. 2007. Defect band characteristics in Mg-Al
and Al-Si high-pressure die castings. Metallurgical and Materials Transactions: A, 38(8),
1833-1844. - Knott, J., Beeley, P. R., Griffiths, J. R., Green, N. R., Newton, C. J. & Campbell, J. 2006.
Commentaries on 'Entrainment defects' by J. Campbell. Materials Science and Technology,
22(8), 999-1008. - Otarawanna, S. 2009. High Pressure Die Casting of Aluminium and Magnesium
Alloys:Formation of Microstructure and Defects. Dissertation/Thesis, The University of
Queensland, School of Mechanical and Mining Engineering. - Gourlay, C. M., Laukli, H. I. & Dahle, A. K. 2004. Segregation Band Formation in Al-Si
Die Castings. Metallurgical and Materials Transactions: A, 35(9), 2881-2891. - Cao, H. & Wessén, M. 2005. Characteristics of microstructure and banded defects in die
cast AM50 magnesium components. International Journal of Cast Metals Research, 18(6),
377-384. - Gourlay, C. M. & Dahle, A. K. 2007. Dilatant shear bands in solidifying metals. Nature,
445(7123), 70-73. - Dahle, A. K. & StJohn, D. H. 1999. Rheological behaviour of the mushy zone and its
effect on the formation of casting defects during solidification. Acta Materialia, 47(1), 31- - Chen, Z. W. & Jahedi, M. Z. 1999. Die erosion and its effect on soldering formation in
high pressure die casting of aluminium alloys. Materials & Design, 20(6), 303-309. - Fraser, D. 2000. Soldering in high pressure die casting and its prevention by lubricant and
oxide coating. Ph. D., The University of Queensland. - Shankar, S. A. D. 2002. Die soldering: Mechanism of the interface reaction between
molten aluminum alloy and tool steel. Metallurgical and Materials Transactions B, 33(3),
465-476. - Riabov, V. R. 1985. Aluminizing of steel, New Delhi, Oxonian Press.
- Tang, C. 2007. Soldering in Magnesium High Pressure Die Casting and its Prevention by
Surface Engineering. Swinburne University of Technology. - Koch, H., Hielscher, U., Sternau, H. & Franke, A. J. 1996. "Magsimal™-59, an Al
MgMnSi-Type Squeeze-Casting Alloy designed for temper F". Light Metals. TMS. - Mondolfo, L. F. 1976. Aluminum alloys : structure and properties, London; Boston,
Butterworths. - Murray, J. L. & McAlister, A. J. 1984. The Al-Si (Aluminum-Silicon) system. Bulletin of
Alloy Phase Diagrams, 5(1), 74-84. - Polmear, I. J. 2006. Light alloys from traditional alloys to nanocrystals. Amsterdam;
Boston: Elsevier/Butterworth-Heinemann. - Mondolfo, L. F. 1943. Metallography of aluminum alloys, New York, J. Wiley & Sons;
Chapman & Hall. - Belov, N. A., Aksenov, A. A. & Eskin, D. G. 2002. Iron in aluminium alloys: impurity and
alloying element, London, Taylor & Francis. - Abouei, V., Saghafian, H., Shabestari, S. G. & Zarghami, M. 2010. Effect of Fe-rich
intermetallics on the wear behavior of eutectic Al-Si piston alloy (LM13). Materials &
Design, 31(7), 3518-3524. - Darvishi, A., Maleki, A., Atabaki, M. M. & Zargami, M. 2010. The mutual effect of iron
and manganese on microstructure and mechanical properties of aluminum-silicon alloy.
Association of Metallurgical Engineers of Serbia, 16(1), 11-24. - Burapa, R., Janudom, S., Chucheep, T., Canyook, R. & Wannasin, J. 2010. Effects of
primary phase morphology on mechanical properties of Al-Si-Mg-Fe alloy in semi-solid
slurry casting process. Transactions of Nonferrous Metals Society of China,
20(Supplement 3), s857-s861. - Zedan, Y., Samuel, F. H., Samuel, A. M. & Doty, H. W. 2010. Effects of Fe intermetallics
on the machinability of heat-treated Al-(7-11)% Si alloys. Journal of Materials Processing
Technology, 210(2), 245-257. - Zhang, W., Lin, B., Zhang, D. & Li, Y. 2013. Microstructures and mechanical properties
of squeeze cast Al–5.0Cu–0.6Mn alloys with different Fe content. Materials & Design, 52,
225-233. - Eklund, J. E. 1991. On the Effects of Impurities on the Solidification and Mechanical
Behavior of Primary and Secondary Commercial Purity Aluminum and Aluminum Alloys.
PhD, Helsinki University of Technology. - Suárez-Peña, B. & Asensio-Lozano, J. 2006. Influence of Sr modification and Ti grain
refinement on the morphology of Fe-rich precipitates in eutectic Al-Si die cast alloys.
Scripta Materialia, 54(9), 1543-1548. - Dinnis, C. M., Taylor, J. A. & Dahle, A. K. 2006. Iron-related porosity in Al-Si-(Cu)
foundry alloys. Materials Science and Engineering: A, 425(1-2), 286-296. - Shabestari, S. G. 2004. The effect of iron and manganese on the formation of intermetallic
compounds in aluminum–silicon alloys. Materials Science and Engineering: A, 383(2),
289-298. - Hatch, J. E. 1984. Aluminum : properties and physical metallurgy, United States of
American, Metals Park, Ohio : American Society for Metals. - Kaufman, J. G. 2004. Aluminum alloy castings : properties, processes, and applications,
United States of American, Materials Park, OH : ASM International. - Zhang, J., Fan, Z., Wang, Y. Q. & Zhou, B. L. 2000. Effect of cooling rate on the
microstructure of hypereutectic Al-Mg2Si alloys. Journal of Materials Science Letters,
19(20), 1825-1828. - Li Shunpu, Zhao Shengxu, Pan Mingxiang, Zhao Deqian, Chen Xichen, M., B. O. & I., B.
R. 1997. Solidification and Structural Characteristics of α(Al)-Mg2Si Eutectic. Material
Transaction, JIM,, 36(6), 553-559. - Li, C., Wu, Y. Y., Li, H. & Liu, X. F. 2011. Morphological evolution and growth
mechanism of primary Mg2Si phase in Al–Mg2Si alloys. Acta Materialia, 59(3), 1058- - Ren, B., Liu, Z., Zhao, R., Zhang, T., Liu, Z., Wang, M. & Weng, Y. 2010. Effect of Sb on
microstructure and mechanical properties of Mg2Si/Al-Si composites. Transactions of
Nonferrous Metals Society of China, 20(8), 1367-1373. - Miao, W. F. & Laughlin, D. E. 2000. Effects of Cu Content and Preaging on Precipitation
Characteristics in Aluminum Alloy 6022. Metallurgical and Materials Transactions A,
31A, 361. - Liu, H., Zhao, G., Liu, C.-m. & Zuo, L. 2007. Effects of different tempers on precipitation
hardening of 6000 series aluminium alloys. Transactions of Nonferrous Metals Society of
China, 17(1), 122-127. - Jinta, M., Sakai, Y., Oyagi, M., Yoshizawa, S., Matsui, K. & Noda, K. 2000. Press forming
analysis of aluminum auto body panel: wrinkle behavior in 5000 and 6000 series
aluminum alloy sheet forming. JSAE Review, 21(3), 407-409. - Jaafar, A., Rahmat, A., Hussain, Z. & Zainol, I. 2011. Effect of Mg, Si and Cu content on
the microstructure of dilute 6000 series aluminium alloys. Journal of Alloys and
Compounds, 509(35), 8632-8640. - Liang, W. J., Rometsch, P. A., Cao, L. F. & Birbilis, N. 2013. General aspects related to
the corrosion of 6xxx series aluminium alloys: Exploring the influence of Mg/Si ratio and
Cu. Corrosion Science, 76, 119-128. - Wang, Z., Li, H., Miao, F., Sun, W., Fang, B., Song, R. & Zheng, Z. 2014. Improving the
intergranular corrosion resistance of Al–Mg–Si–Cu alloys without strength loss by a two step aging treatment. Materials Science and Engineering: A, 590, 267-273. - Ji, S., Watson, D., Fan, Z. & White, M. 2012. Development of a super ductile diecast Al–
Mg–Si alloy. Materials Science and Engineering: A, 556(0), 824-833. - Hekmat-Ardakan, A. & Ajersch, F. 2010. Thermodynamic evaluation of hypereutectic Al–
Si (A390) alloy with addition of Mg. Acta Materialia, 58(9), 3422-3428. - Lin, X., Liu, C., Zhai, Y. & Wang, K. 2011. Influences of Si and Mg contents on
microstructures of Al–xSi–yMg functionally gradient composites reinforced with in situ
primary Si and Mg2Si particles by centrifugal casting. Journal of Materials Science, 46(4),
1058-1075. - Jayakumar, E., Rajan, T. P. D. & Pai, B. C. 2012. Effect of Mg on Solidification
Microstructures of Homogenous and Functionally Graded A390 Aluminum Alloys.
Transactions of the Indian Institute of Metals, 65(6), 677-681. - Lumley, R., Deeva, N., Larsen, R., Gembarovic, J. & Freeman, J. 2013. The Role of Alloy
Composition and T7 Heat Treatment in Enhancing Thermal Conductivity of Aluminum
High Pressure Diecastings. Metallurgical and Materials Transactions A, 44(2), 1074-1086. - Donahue, R. J. 2012. T6 heat treatment of real high pressure die castings an alternative ot
the high cost of permanent mold castings. Die casting engineer [Online]. Available:
www.diecasting.org/ [Accessed Nov. 2012]. - Herring, D. H. 2011. Innovations in Aluminum Heat Treatment. Available:
IndustrialHeating.com. - Lumley, R. N., Polmear, I. J. & Curtis, P. R. 2009. Rapid Heat Treatment of Aluminum
High-Pressure Diecastings. Metallurgical and Materials Transactions A, 40(7), 1716-1726. - Timelli, G., Lohne, O., Arnberg, L. & Laukli, H. I. 2008. Effect of Solution Heat
Treatments on the Microstructure and Mechanical Properties of a Die-Cast AlSi7MgMn
Alloy. Metallurgical and Materials Transactions A, 39(7), 1747-1758. - Lumley, R. N., Polmear, I. J., Groot, H. & Ferrier, J. 2008. Thermal characteristics of heat treated aluminum high-pressure die-castings. Scripta Materialia, 58(11), 1006-1009.
- Lumley, R. N., O'Donnell, R. G., Gunasegaram, D. R., Kittel-Sherri, T., Gershenzon, M.,
Yob, A. C. & Polmear, I. J. 2008. The role of alloy composition in the heat treatment of
aluminium high pressure die castings. Metallurgical science and technology, 26(2). - Sadrossadat, M. & Johansson, S. The effect of heat treatment on the mechanical properties
and residual stresses in a HPDC component of Al-Si-Mn alloy. 5th International
Conference on Mechanical Stress Evaluation by Neutrons and Synchrotron Radiation,
September 24-26 2007 Vienna, Austria. - Lumley, R. N., O‟Donnell, R. G., Gunasegaram, D. R. & Givord, M. 2007. Heat Treatment
of High-Pressure Die Castings. Metallurgical and Materials Transactions A, 38(10), 2564- - Shivkumar, S., Ricci, S., Keller, C. & Apelian, D. 1990. Effect of solution treatment
parameters on tensile properties of cast aluminum alloys. Journal of Heat Treating, 8(1),
63-70. - Zhang, D. L. & StJohn, D. H. 1995. The effect of composition and heat treatment on the
microstructure and mechanical properties of cast Al-7wt%Si-Mg alloys, Gold Coast,
IMMA. - Taylor, J. A., St John, D. H., Barresi, J. & Couper, M. J. 2000. An empirical analysis of
trends in mechanical properties of T6 heat treated Al-Si-Mg casting alloys. International
Journal of Cast Metals Research, 12(6), 419-430. - Li, X. M. & Starink, M. J. 2001. Effect of compositional variations on characteristics of
coarse intermetallic particles in overaged 7000 aluminium alloys. Materials Science and
Technology, 17(11), 1324-1328. - Ogris, E., Wahlen, A., Lüchinger, H. & Uggowitzer, P. J. 2002. On the silicon
spheroidization in Al-Si alloys. Journal of Light Metals, 2(4), 263-269. - Samuel, F. H. 1998. Incipient melting of Al5Mg8Si6Cu2 and Al2Cu intermetallics in
unmodified and strontium-modified Al-Si-Cu-Mg (319) alloys during solution heat
treatment. Journal of Materials Science, 33(9), 2283-2297. - Zhang, D. L., Zheng, L. H. & StJohn, D. H. 2002. Effect of a short solution treatment time
on microstructure and mechanical properties of modified Al–7wt.%Si–0.3wt.%Mg alloy.
Journal of Light Metals, 2(1), 27-36. - Mohamed, A. M. A. & Samuel, F. H. 2012. A Review on the Heat Treatment of Al-Si Cu/Mg Casting Alloys.
- Crowell, N. & Shivkumar, S. 1995. Solution treatment effects in cast Al–Si–Cu alloys.
AFS Trans, 107, 721-726. - Xu, D. K., Rometsch, P. A. & Birbilis, N. 2012. Improved solution treatment for an as rolled Al–Zn–Mg–Cu alloy. Part I. Characterisation of constituent particles and
overheating. Materials Science and Engineering: A, 534, 234-243. - Xu, D. K., Rometsch, P. A. & Birbilis, N. 2012. Improved solution treatment for an as rolled Al–Zn–Mg–Cu alloy. Part II. Microstructure and mechanical properties. Materials
Science and Engineering: A, 534(0), 244-252. - Starink, M. J. & Wang, S. C. 2003. A model for the yield strength of overaged Al–Zn–
Mg–Cu alloys. Acta Materialia, 51(17), 5131-5150. - Engdahl, T., Hansen, V., Warren, P. J. & Stiller, K. 2002. Investigation of fine scale
precipitates in Al-Zn-Mg alloys after various heat treatments. Materials Science and
Engineering: A, 327(1), 59-64. - Chinh, N. Q., Kovács, Z., Reich, L., Székely, F., Illy, J. & Lendvai, J. 1996. Precipitation
and work hardening in high strength AlZnMg(Cu,Zr) alloys. - Wang, T., Yin, Z. m. & Sun, Q. 2007. Effect of homogenization treatment on
microstructure and hot workability of high strength 7B04 aluminium alloy. Transactions of
Nonferrous Metals Society of China (English Edition), 17(2), 335-339. - Lim, S. T., Lee, Y. Y. & Eun, I. S. 2006. Microstructural evolution during ingot preheat in
7xxx aluminum alloys for thick semiproduct applications. - Li, N. k. & Cui, J. Z. 2008. Microstructural evolution of high strength 7B04 ingot during
homogenization treatment. Transactions of Nonferrous Metals Society of China (English
Edition), 18(4), 769-773. - Chen, K., Liu, H., Zhang, Z., Li, S. & Todd, R. I. 2003. The improvement of constituent
dissolution and mechanical properties of 7055 aluminum alloy by stepped heat treatments.
Journal of Materials Processing Technology, 142(1), 190-196. - Mohamed, A. M. A. & Samuel, F. H. 2012. A Review on the Heat Treatment of Al-Si Cu/Mg Casting Alloys. In: Czerwinski, D. F. (ed.) Heat Treatment - Conventional and
Novel Applications. InTech. - Shivkumar, S., Keller, C. & Apelian, D. 1990. Aging behavior in cast Al–Si–Mg alloys.
AFS Trans, 98, 905–911. - Eskin, D. G. 2003. Decomposition of supersaturated solid solutions in Al-Cu-Mg-Si alloys.
Journal of Materials Science, 38(2), 279-290. - Ouellet, P. & Samuel, F. H. 1999. Effect of Mg on the ageing behaviour of Al-Si-Cu 319
type aluminium casting alloys. Journal of Materials Science, 34(19), 4671-4697. - Chen, S. L., Zhang, F., Xie, F. Y., Daniel, S., Yan, X. Y., Chang, Y. A., Schmid-Fetzer, R.
& Oates, W. A. 2003. Calculating phase diagrams using PANDAT and panengine. JOM,
55(12), 48-51. - Frech 2010. The Frech DAK450-54 450 tone cold chamber HPDC machine operation
instructions, Germeny, Frech - Ji, S., Yang, W., Gao, F., Watson, D. & Fan, Z. 2013. Effect of iron on the microstructure
and mechanical property of Al–Mg–Si–Mn and Al–Mg–Si diecast alloys. Materials
Science and Engineering: A, 564(1), 130-139. - Wiley, V. C. H. 1988. Particle & particle systems characterization. Available:
http://onlinelibrary.wiley.com/journal/10.1002/(ISSN)1521-4117. - Kuhn, H. M., D. eds. 2000. ''Mechanical properties'', ASM handbook. Volume 8, Materials
Park, OH, ASM International. - Nam, S. & Lee, D. 2000. The effect of Mn on the mechanical behavior of Al alloys. Metals
and Materials, 6(1), 13-16. - Taylor, J. A. Iron-Containing Intermetallic Phases in Al-Si Based Casting Alloys. 11th
International Congress on Metallurgy & Materials SAM/CONAMET 2011, 2011. 19-33. - Zhang, W.-w., Lin, B., Cheng, P., Zhang, D.-t. & Li, Y.-y. 2013. Effects of Mn content on
microstructures and mechanical properties of Al-5.0Cu-0.5Fe alloys prepared by squeeze
casting. Transactions of Nonferrous Metals Society of China, 23(6), 1525-1531. - Laukli, H. I., Gourlay, C. M. & Dahle, A. K. 2005. Migration of crystals during the filling
of semi-solid castings. Metallurgical and Materials Transactions A, 36(3), 805-818. - Ghomashchi, M. R. 1995. High-pressure die casting: effect of fluid flow on the
microstructure of LM24 die-casting alloy. Journal of Materials Processing Technology,
52(2-4), 193-206. - Tsai, D. C., Sheng, L. T. & Hui, C. L. 2002. Effect of Silicon Particles on the EDM
Characteristics of Al-Si Alloys. Materials transactions, JIM., 43(2), 199. - Jian X, H. Q. 2013. Formation of hypereutectic silicon particles in hypoeutectic Al-Si
alloys under the influence of high-intensity ultrasonic vibration. China Foundry China
Foundry, 10(2), 118-123. - Wang, S., Ma, R., Wang, Y., Wang, Y. & Yang, L. 2012. Growth mechanism of primary
silicon in cast hypoeutectic Al-Si alloys. Transactions of Nonferrous Metals Society of
China, 22(6), 1264-1269. - Taylor, J. A., Schaffer, G. B., StJohn, D. H. 1999. The role of iron in the formation of
porosity in Al-Si-Cu-based casting alloys. Part 1: Initial experimental observations.
Metallurgical and Materials Transactions: A, 30(6). - Wang, E. R., Hui, X. D. & Chen, G. L. 2011. Eutectic Al–Si–Cu–Fe–Mn alloys with
enhanced mechanical properties at room and elevated temperature. Materials & Design,
32(8–9), 4333-4340. - Emamy, M., Emami, A. R., Khorshidi, R. & Ghorbani, M. R. 2013. The effect of Fe-rich
intermetallics on the microstructure, hardness and tensile properties of Al–Mg2Si die-cast
composite. Materials & Design, 46, 881-888. - Kovács, I. 1990. Effect of iron and silicon in aluminium and its alloys : International
workshop : Papers. - Löffler, H. & Jürgen, B. D. 1995. Structure and structure development of Al-Zn alloys,
Berlin, Akademie. - Grard, C., Phillips, C. M. & Phillips, H. W. L. 1921. Aluminium and its alloys, their
properties, thermal treatment and industrial application, [London, Constable & Co. Ltd. - Zhang, J., Fan, Z., Wang, Y. Q. & Zhou, B. L. 2001. Equilibrium paseudobinary Al-Mg2Si
phase diagram. Materials science and technology, 17, 494. - Villeneuve, C., Samuel, A. M., Samuel, F. H., Doty, H. W., Valtierra, S. 2001. Role of
Trace Elements in Enhancing the Performance of 319 Aluminium Foundry Alloys. AFS
Transactions, 109, 287-300. - Fruehan, R. J. & Anyalebechi, P. N. 2008. Gases in metals. ASM handbook: Vol 15
Casting. United States of American: ASM International, Materials Park, OH : ASM
International. - Chamberlain, B. & Watanabe, S. 1977. A Natural Aging Aluminum Alloy, Designed for
Permanent Mold use. AFS Trans, 85, 133-142. - Sigworth, G. K., Rios, O., Howell, J. & Kaufman, M. 2004. Development Program on
Natural Aging Alloys. AFS Trans, 112, 387-408. - Cáceres, C. H., Djurdjevic, M. B., Stockwell, T. J. & Sokolowski, J. H. 1999. The effect of
Cu content on the level of microporosity in Al-Si-Cu-Mg casting alloys. Scripta Materialia,
40(5), 631-637. - Shabestari, S. G. & Moemeni, H. 2004. Effect of copper and solidification conditions on
the microstructure and mechanical properties of Al–Si–Mg alloys. Journal of Materials
Processing Technology, 153–154, 193-198. - Anyalebechi, P. N. 1995. Analysis of the effects of alloying elements on hydrogen
solubility in liquid aluminum alloys. Scripta Metallurgica et Materialia, 33(8), 1209-1216. - Seifeddine, S., Johansson, S. & Svensson, I. L. 2008. The influence of cooling rate and
manganese content on the β-Al5FeSi phase formation and mechanical properties of Al–Si based alloys. Materials Science and Engineering: A, 490(1–2), 385-390. - Raghavan, V. 2007. Al-Mg-Si (Aluminum-Magnesium-Silicon). Journal of Phase
Equilibria and Diffusion, 28(2), 189-191. - Tavitas-Medrano, F. J., Mohamed, A. M. A., Gruzleski, J. E., Samuel, F. H. & Doty, H. W.
- Precipitation-hardening in cast AL–Si–Cu–Mg alloys. Journal of Materials Science,
45(3), 641-651. - Wang, G., Bian, X., Liu, X. & Zhang, J. 2004. Effect of Mg on age hardening and
precipitation behavior of an AlSiCuMg cast alloy. Journal of Materials Science, 39(7),
2535-2537. - Yao, J. Y., Graham, D. A., Rinderer, B. & Couper, M. J. 2001. A TEM study of
precipitation in Al–Mg–Si alloys. Micron, 32(8), 865-870. - Yang, W., Huang, L., Zhang, R., Wang, M., Li, Z., Jia, Y., Lei, R. & Sheng, X. 2012.
Electron microscopy studies of the age-hardening behaviors in 6005A alloy and
microstructural characterizations of precipitates. Journal of Alloys and Compounds, 514,
220-233. - Kang, H. G., Kida, M., Miyahara, H. & Ogi, K. 1999. Age-hardening characteristics of Al Si-Cu-base cast alloys. AFS Transactions, 107, 507-515.
- Reif, W., Dutkiewicz, J., Ciach, R., Yu, S. & Król, J. 1997. Effect of ageing on the
evolution of precipitates in AlSiCuMg alloys. Materials Science and Engineering: A, 234-
236(30), 165-168. - Stiller, W. 1989. Arrhenius equation and non-equilibrium kinetics : 100 years Arrhenius
equation, Leipzig, John Wiley & Sons Incorporated. - Brechet, Y., Embury, J. D., Tao, S. & Luo, L. 1991. Damage initiation in metal matrix
composites. Acta Metallurgica et Materialia, 39(8), 1781-1786. - Caceres, C. H. & Griffiths, J. R. 1996. Damage by the cracking of silicon particles in an
Al-7Si-0.4Mg casting alloy. Acta Materialia, 44(1), 25-33. - Zhang, J., Fan, Z., Wang, Y. Q. & Zhou, B. L. 2000. Microstructural development of Al–
15wt.%Mg2Si in situ composite with mischmetal addition. Materials Science and
Engineering: A, 281(1–2), 104-112.
9. 著作権:
この資料は、Feng Yan氏の論文:「Development of High Strength Al-Mg2Si-Mg Based Alloy for High Pressure Diecasting Process」に基づいています。
論文ソース:
この資料は上記の論文に基づいて要約されており、商業目的での無断使用は禁止されています。
Copyright © 2025 CASTMAN. All rights reserved.