This paper summary is based on the article ['Effects of microstructure and casting defects on the fatigue behavior of the high-pressure die-cast AlSi9Cu3(Fe) alloy'] presented at the ['Procedia Structural Integrity']
1. Overview:
- Title: 高圧ダイカストAlSi9Cu3(Fe)合金の疲労挙動に及ぼすミクロ組織と鋳造欠陥の影響 (Effects of microstructure and casting defects on the fatigue behavior of the high-pressure die-cast AlSi9Cu3(Fe) alloy)
- Author: L. Lattanzi, A. Fabrizi, A. Fortini, M. Merlin, G. Timelli
- Publication Year: 2017年
- Publishing Journal/Academic Society: Procedia Structural Integrity
- Keywords: die cast aluminum alloy; casting defects; microstructure. (ダイカストアルミニウム合金、鋳造欠陥、ミクロ組織)
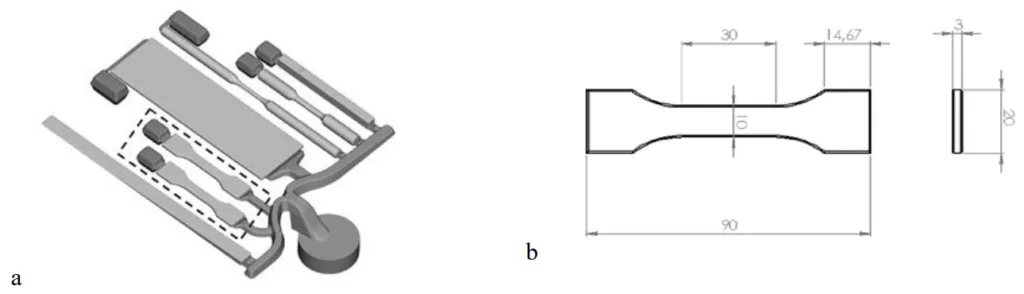
2. Research Background:
Background of the Research Topic: (研究背景)
近年、高圧ダイカスト(HPDC)部品は、「優れた柔軟性と高い生産性」により、自動車産業を中心に大量生産部品への適用が拡大しています。HPDCプロセスは、「金型の急速充填と高い冷却速度」を特徴とするため、本質的に「気孔率や酸化皮膜」、「冷間凝着(cold joints)」など、「PD CEN/TR 16749:2014規格およびFioreseら(2015年)によって定義される」多種多様な鋳造欠陥が発生しやすいという課題があります。これらの鋳造欠陥は、機械的特性に悪影響を及ぼし、「疲労亀裂の起点となり、鋳物の疲労挙動を劣化させる」可能性があります。したがって、自動車部品のような複雑形状の鋳物の性能評価において、ダイカストアルミニウム合金の疲労挙動を理解することは非常に重要です。
Status of Existing Research: (既存研究の状況)
ダイカストアルミニウム合金部品の静的機械特性に関する研究は広範囲に実施されていますが、「高圧ダイカスト欠陥が疲労特性に及ぼす影響を調査した研究は非常に少ない」のが現状です。既存研究では、鋳造欠陥が静的強度に及ぼす影響はケースによって異なり、破断伸びにおいては大きな変動が見られることが報告されています。Avalleら(2002年)は、HPDC AlSi9Cu3(Fe) 材の静的特性が気孔率の増加とともに低下することを報告しました。疲労特性に関する研究では、Avalleら(2002年)やMayerら(2003年)の研究で、HPDC AlSi9Cu3(Fe) 合金やMg合金において、気孔や冷間凝着が疲労強度低下の要因となること、亀裂が気孔から発生することが示されています。Huら(2014年)のAlMg5Si2Mn合金の研究では、金型鋳造材と比較してHPDC材の方が疲労限度が高いことが示唆されています。砂型鋳造、金型鋳造、低圧ダイカストに関する研究でも、欠陥を含む材料の疲労強度は低下し、欠陥のサイズや表面からの距離が疲労寿命に影響を与えることが確認されています。これらの研究では主に、破壊表面解析や金属組織学的特性評価によって鋳造欠陥の疲労挙動への影響が調査されています。
Necessity of the Research: (研究の必要性)
鋳造欠陥と疲労に関する既存研究にもかかわらず、HPDC AlSi9Cu3(Fe) 合金において、ミクロ組織が疲労亀裂の発生と伝播にどのように影響するかについての詳細な理解が依然として不足しています。本研究は、このギャップを埋めることを目的とし、HPDC法で製造されたAlSi9Cu3(Fe)合金におけるミクロ組織の疲労挙動への影響を明らかにすることを目的としています。ミクロ組織評価と疲労試験、そして詳細な破壊表面解析を通じて、亀裂発生箇所と疲労破壊における欠陥の役割を特定します。
3. Research Purpose and Research Questions:
Research Purpose: (研究目的)
本研究の主な目的は、高圧ダイカストAlSi9Cu3(Fe)アルミニウム合金における「ミクロ組織が疲労亀裂の発生と伝播にどのように影響するかを記述すること」です。これは、予備的なミクロ組織評価、疲労試験、およびそれに続く詳細な破壊表面解析によって達成されます。
Key Research: (主要な研究内容)
主要な研究内容は以下の通りです。
- HPDC AlSi9Cu3(Fe) 合金試験片のミクロ組織特性評価。
- 疲労挙動を評価するための荷重制御下での一軸疲労試験の実施。
- 亀裂発生箇所を特定するための破壊表面および断面プロファイルの調査。
- 鋳造欠陥、特にミクロ組織が、疲労亀裂の発生と伝播、および全体的な疲労破壊に及ぼす影響の調査。
Research Hypotheses: (研究仮説)
明示的な仮説は述べられていませんが、研究は暗黙的に以下を検証しています。
- HPDCプロセスに内在する鋳造欠陥は、AlSi9Cu3(Fe)合金における疲労亀裂の主要な発生源として作用する。
- HPDCプロセスパラメータの影響を受けるミクロ組織的特徴は、合金の疲労挙動に大きな影響を与える。
- 鋳造欠陥の種類と位置(例:気孔率、酸化皮膜、冷間凝着、金属間化合物、偏析帯)は、疲労亀裂の発生および伝播メカニズムと直接的な相関関係がある。
4. Research Methodology
Research Design: (研究計画)
本研究では、材料製造、ミクロ組織評価、機械試験、および破面解析を含む実験計画法を採用しています。専用に設計された金型を用いてダイカストAlSi9Cu3(Fe)試験片を作製し、ミクロ組織を評価しました。一軸疲労試験を実施し、その後、破壊表面を分析して、ミクロ組織と欠陥と疲労挙動の相関関係を調べました。
Data Collection Method: (データ収集方法)
- 材料製造: ダイカストAlSi9Cu3(Fe) 試験片は、特定のパラメータ(型締力 2.9 MN、金型温度 ~230 °C、ショットチャンバー充填率 0.28、プランジャ速度 0.2 m/s および 2.7 m/s、増圧圧力 40 MPa)を備えたコールドチャンバーダイカストマシンを使用して製造されました。合金の化学組成は「Table 1」に示されています。
- ミクロ組織評価: 予備的なミクロ組織調査は、「光学顕微鏡(OM)および走査型電子顕微鏡(SEM)」を用いて実施されました。相の同定は「X線回折(XRD)法」を用いて行われました。結晶粒径およびテクスチャ評価は、「電子後方散乱回折(EBSD)法」を用いて実施されました。
- 疲労試験: 一軸疲労試験は、「LM10 Italsigma 試験機」を用いて、「50 Hz」の周波数と「80 MPa」の応力振幅の荷重制御下で実施されました。「R = 0.1」の応力比が使用されました。疲労寿命(破壊までのサイクル数)は、3つの試験片について記録されました。
- 破面解析: 疲労試験後、「光学顕微鏡および走査型電子顕微鏡」を用いて破壊表面および断面プロファイルを調べ、亀裂発生箇所、伝播領域、および疲労破壊における欠陥の役割を特定しました。
Analysis Method: (分析方法)
- ミクロ組織分析: OM、SEM、XRD、およびEBSDを用いて、結晶粒径、形態、相分布、金属間化合物、および鋳造欠陥(気孔率、酸化皮膜、冷間凝着、偏析帯)を評価しました。「EDSスペクトルおよび元素マッピング」を用いて金属間化合物を特定しました。
- 疲労データ分析: 疲労寿命データ(破壊までのサイクル数)を記録し、疲労性能のばらつきを評価するために分析しました。
- 破面解析: SEM 像による破壊表面を分析し、亀裂発生箇所、伝播領域(安定伝播および静的破壊)、および関連する欠陥を特定しました。光学顕微鏡を用いて破壊断面プロファイルを調べ、亀裂経路と遷移領域を評価しました。
Research Subjects and Scope: (研究対象と範囲)
研究対象は、「ダイカストAlSi9Cu3(Fe)(EN AC-46000)合金」製の試験片でした。研究範囲は以下に限定されます。
- 応力比 R=0.1、単一応力振幅レベル 80 MPa の一軸荷重条件下での疲労挙動。
- 疲労試験後の試験片のミクロ組織および破面解析。
- この特定のHPDCアルミニウム合金における疲労亀裂の発生と伝播に対するミクロ組織および鋳造欠陥の影響の調査。
5. Main Research Results:
Key Research Results: (主な研究結果)
- ミクロ組織: 合金のミクロ組織は、球状晶粒構造に典型的な「ロゼット状の形態」を示すα-Alデンドライトを示しました。結晶粒径と二次デンドライトアーム間隔(SDAS)は、コア領域で類似していました。「Table 2」は、平均結晶粒径(「17 ± 8 µm」)とSDAS(「12 ± 2 µm」)を示しています。d/SDAS比は1.6未満であり、球状または球状の結晶粒形態を示しています。「Fig. 3b」は、優先的な結晶方位がないことを示しています。特定された金属間化合物相には、「β-Al5FeSi」、「θ-Al2Cu」、およびブロック状の「α-Al(Fe,Mn, Cr)Si (スラッジ)」相が含まれていました。「Fig. 4b」は、スラッジ相を示しています。「共晶偏析帯」が観察され、「正の巨視的偏析」と局所的なAl-Si共晶濃縮を示唆しています。「Fig. 6a」は、共晶偏析領域を示しています。「Fig. 6b」は、偏析帯領域におけるガス気孔率の集中を示しています。
- 疲労寿命: ダイカスト試験片の疲労寿命は、応力レベル 80 MPa で「4×10⁴サイクル」を超え、「8.7×10⁴サイクル、4.4×10⁴サイクル、および 10×10⁴サイクル」で破壊しました。データのばらつきは、疲労寿命がダイカスト欠陥に依存することを示唆しています。
- 破面解析: 疲労亀裂は、断面の鋭角コーナー部から発生し、多くの場合、単一の起点から発生しました。「Fig. 7a」は、亀裂発生領域を示しています。破壊表面は、「限られた明るい領域」(安定亀裂伝播)と「不規則な表面領域」(静的破壊)を示しました。発生箇所は、「Fig. 7b」に見られるように、断面コーナー部の「酸化皮膜と冷間凝着」に関連していました。「スラッジ粒子とガス気孔」は、不規則領域で観察されました(「Fig. 8a および Fig. 8b」)。破壊断面プロファイルは、安定伝播に対応する滑らかな領域と、静的破壊に対応する粗い領域を示しました(「Fig. 9」)。
Data Interpretation: (データ解釈)
- 球状晶粒構造と優先方位の欠如は、均一な凝固を示唆していますが、HPDCプロセスによって誘起された偏析帯とガス気孔の存在は、動的機械特性に大きな影響を与えます。
- 疲労寿命のばらつきは、鋳造欠陥が亀裂伝播を制御し、ひいては疲労挙動を支配する上で主要な役割を果たしていることを示唆しています。しかし、亀裂発生は、幾何学的特性(鋭角コーナー)の影響を受けているようです。
- 鋭角コーナー部の酸化皮膜と冷間凝着は、主要な亀裂発生源として作用します。これらの欠陥は材料の不連続性を生み出し、疲労亀裂の発生を促進します。
- スラッジ粒子とガス気孔は、不規則な静的破壊領域に寄与しており、亀裂伝播後の最終破壊プロセスにおける役割を示しています。
- 亀裂経路は、伝播中にデンドライト間共晶領域とデンドライトの両方を通過しますが、静的破壊はデンドライト構造プロファイルに従い、デンドライト間構成要素の破壊が亀裂伝播を促進することを示唆しています。
Figure Name List: (図のリスト)
- Fig. 1. (a) Geometry of the die casting, the investigated specimens are indicated by the dashed line rectangle; (b) technical design of the tensile specimen. (ダイカストの形状、調査対象の試験片は点線で示す;(b) 引張試験片の技術設計)
- Fig. 2. Typical OM micrograph of a specimen: (a) near the surface; (b) at the center. (試験片の代表的なOM顕微鏡写真:(a) 表面付近;(b) 中心部)
- Fig. 3. (a) α-Al grain size dimension distribution; (b) EBSD orientation map obtained in the central cross-section of the specimen. (a) α-Al 結晶粒径寸法分布;(b) 試験片中央断面で得られたEBSD方位マップ)
- Fig. 4. Analyses of secondary phases: (a) XRD spectrum; (b) SEM micrograph of blocky sludge phases. (二次相の分析:(a) XRDスペクトル;(b) ブロック状スラッジ相のSEM顕微鏡写真)
- Fig. 5. SEM image of the specimen cross-section. (試験片断面のSEM像)
- Fig. 6. (a) eutectic segregation region in the specimen cross-section; (b) porosity in the tensile specimen cross-section. (a) 試験片断面における共晶偏析領域;(b) 引張試験片断面における気孔率)
- Fig. 7. SEM images of the specimen that failed at 8.7×10⁴ cycles: (a) crack initiation region. The red arrow indicates the crack initiation site while the dashed line highlights the transition region; (b) particular of the crack origin site. (8.7×10⁴サイクルで破壊した試験片のSEM像:(a) 亀裂発生領域。赤矢印は亀裂発生箇所を示し、点線は遷移領域を強調表示;(b) 亀裂発生源の詳細)
- Fig. 8. SEM images of surface features: (a) gas porosity; (b) fractured sludge particles. (表面特徴のSEM像:(a) ガス気孔;(b) 破砕したスラッジ粒子)
- Fig. 9. Fracture profile of the specimen that failed at 8.7×10⁴ cycles. (a) the red arrow indicates the crack initiation point and the dashed arrow indicates the transition region; (b) crack propagation region at high magnification; (c) static failure region at high magnification. (8.7×10⁴サイクルで破壊した試験片の破壊断面プロファイル。(a) 赤矢印は亀裂発生箇所を示し、点線は遷移領域を示す;(b) 高倍率での亀裂伝播領域;(c) 高倍率での静的破壊領域)
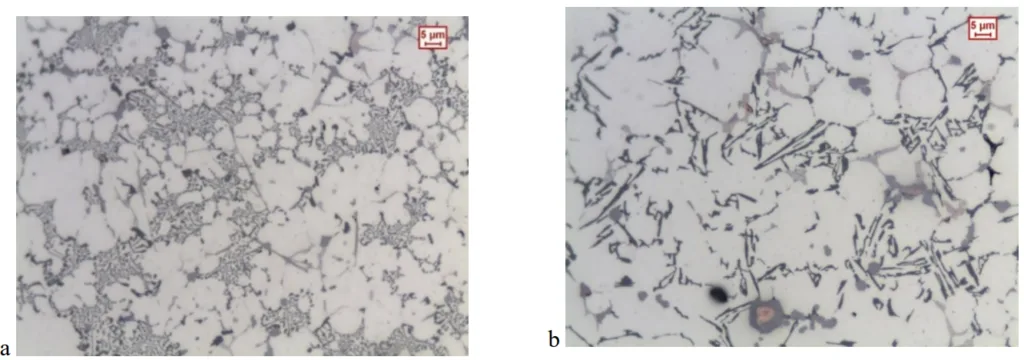
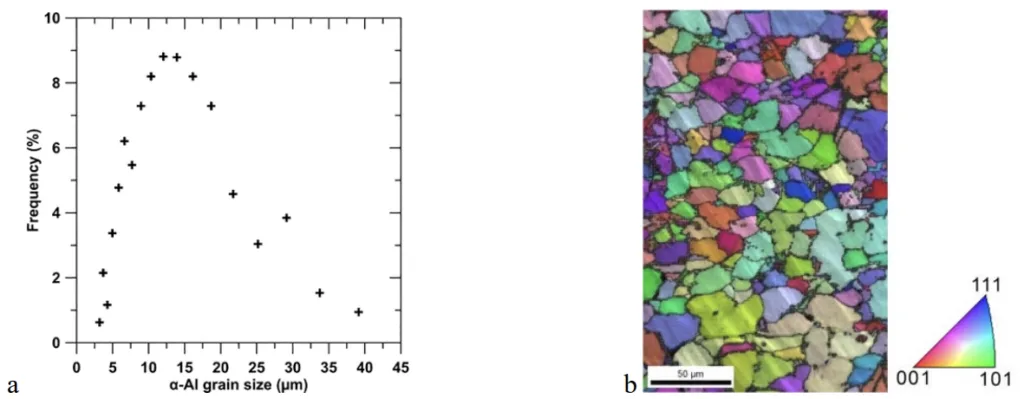
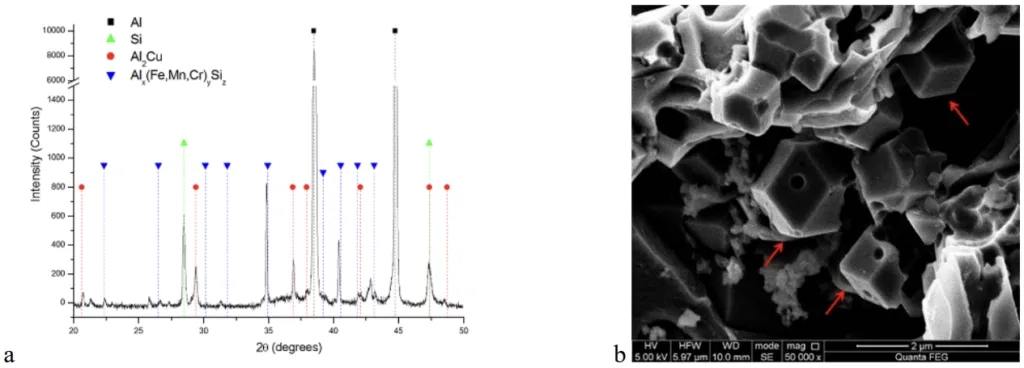

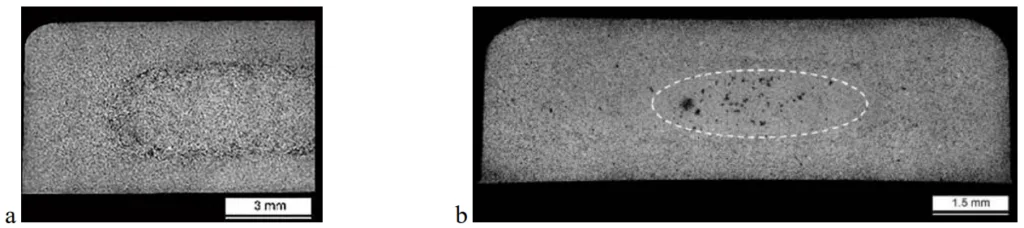
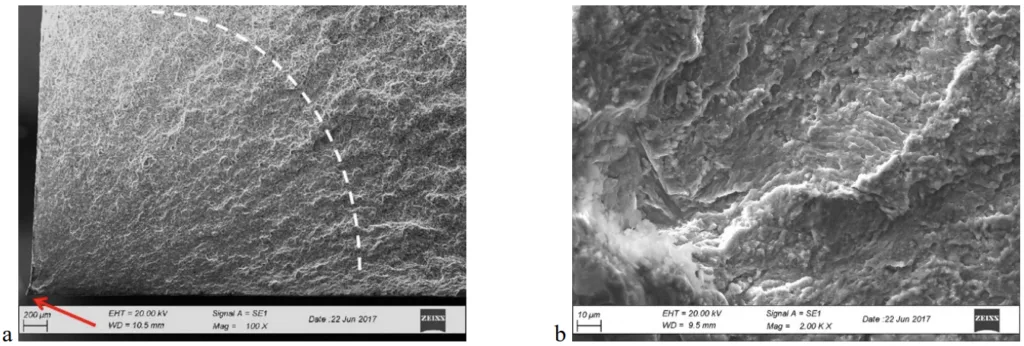
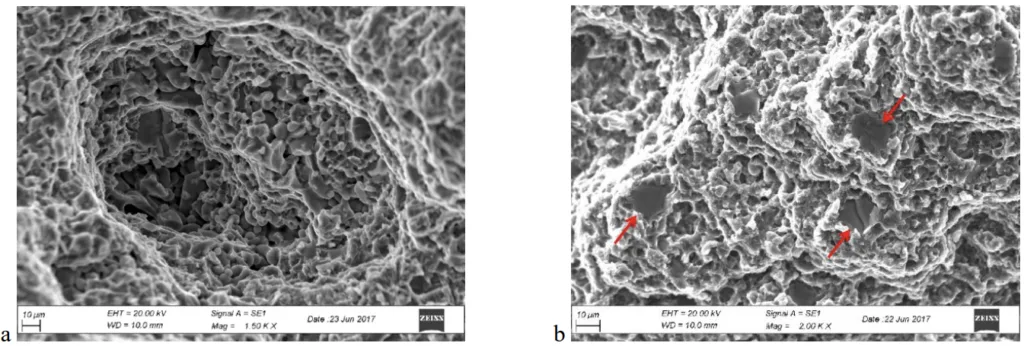
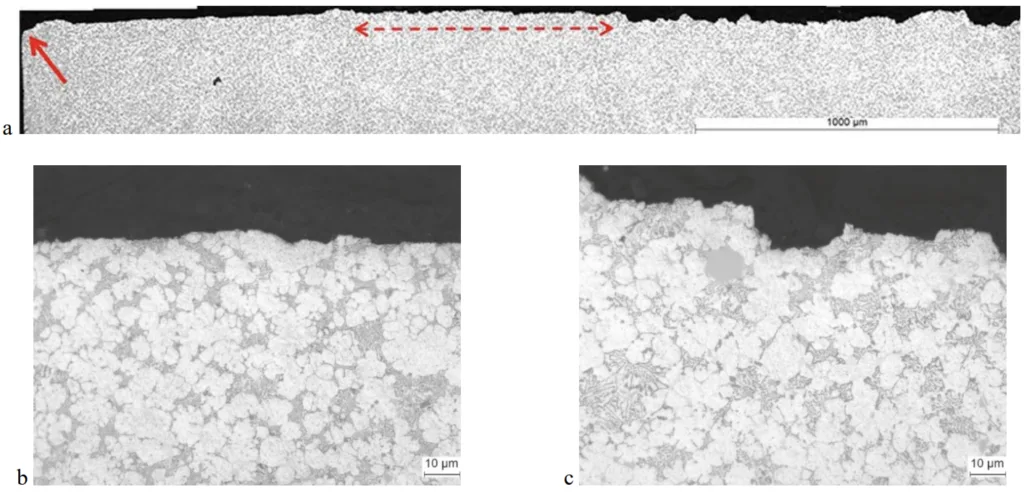
6. Conclusion:
Summary of Main Results: (主な結果の要約)
本研究では、HPDC EN AC 46000 合金の疲労挙動に対するミクロ組織と鋳造欠陥の影響を調査しました。一軸疲労試験とミクロ組織/破面解析により、以下のことが明らかになりました。
- HPDCプロセスにより、偏析帯とガス気孔が存在する。
- 疲労寿命はばらつきを示し、欠陥制御の亀裂伝播を示唆する。
- 亀裂発生は、鋭角コーナーに位置する酸化皮膜と冷間凝着で発生する。
- 破壊表面は、安定伝播領域と静的破壊領域で構成され、後者にはスラッジ粒子とガス気孔が存在する。
- 破壊断面プロファイルは、亀裂経路の滑らかな部分(伝播)と粗い部分(静的破壊)を区別する。
Academic Significance of the Research: (研究の学術的意義)
本研究は、ミクロ組織と鋳造欠陥を疲労亀裂の発生および伝播メカニズムに直接結び付けることにより、HPDCアルミニウム合金の疲労挙動に関する基礎的な理解に貢献します。欠陥の種類とその位置の詳細な特性評価を提供し、HPDCプロセスによって誘起された欠陥が疲労性能にどのように影響するかについての洞察を提供します。この研究はまた、ダイカスト部品の疲労設計において、幾何学的特徴と材料欠陥の両方を考慮することの重要性を強調しています。
Practical Implications: (実用的な意義)
本研究の知見は、特に自動車用途におけるダイカスト産業に実用的な意義をもたらします。酸化皮膜、冷間凝着、偏析帯、および気孔率の疲労破壊における役割を理解することで、欠陥形成を最小限に抑え、部品の信頼性を向上させるためのプロセス最適化を導くことができます。具体的には、偏析と気孔率を低減するための金型充填および冷却速度の制御、および鋭角コーナーのような重要な位置での冷間凝着形成を最小限に抑えるための金型設計の最適化は、HPDC AlSi9Cu3(Fe) 合金部品の疲労性能を向上させることができます。
Limitations of the Research (研究の限界)
本研究は「予備的研究」であり、以下のような限界があります。
- 疲労試験は、単一の応力振幅レベルと応力比で実施されており、疲労寿命データのより広範囲な荷重条件への一般化可能性が制限されます。
- 試験した疲労試験片の数(3つ)が少ないため、疲労寿命のばらつきの統計的有意性、および欠陥特性と疲労寿命の定量的な相関関係が制限されます。
- 研究は特定の合金とHPDCプロセスパラメータに焦点を当てており、結果が他の合金または鋳造条件に直接転用できるとは限りません。
7. Future Follow-up Research:
- Directions for Follow-up Research (今後の研究の方向性)
今後の研究では、「ミクロ組織構成要素の役割をより包括的に調査するために、より深く掘り下げる必要があります」。「さらに、欠陥がサイクル数に及ぼす影響の統計的評価を可能にするために、より多くの疲労試験を実施する必要があります。」これには以下が含まれます。- S-N曲線を生成し、疲労強度を評価するために、複数の応力レベルで疲労試験を実施する。
- 欠陥特性(サイズ、種類、位置)と疲労寿命の間の関係を定量化するために、より大きなデータセットで統計分析を実施する。
- ミクロ組織、欠陥形成、および疲労挙動に対する異なるHPDCプロセスパラメータの影響を調査する。
- HPDC部品における欠陥特性評価と品質管理のための高度な非破壊検査法を検討する。
- Areas Requiring Further Exploration (さらなる探求が必要な分野)
さらなる探求が必要な分野は以下の通りです。- 酸化皮膜と冷間凝着における疲労亀裂発生の正確なメカニズム。
- 疲労亀裂伝播における異なる種類の金属間化合物の役割。
- 偏析帯、気孔率、および疲労性能の間の相互作用。
- HPDC部品のミクロ組織および欠陥特性に基づいて疲労寿命を予測する予測モデルの開発。
8. References:
- Ammar H.R., Samuel A.M., Samuel F.H., 2008. Porosity and the fatigue behavior of hypoeutectic and hypereutectic aluminum-silicon casting alloys. International Journal of Fatigue 30, 1024-1035.
- Avalle M., Belingardi G., Cavatorta M.P., Doglione R., 2002. Casting defects and fatigue strength of a die cast aluminium alloy: a comparison between standard specimens and production components. International Journal of Fatigue 24, 1-9.
- Fabrizi A., Ferraro S., Timelli G., 2013. The influence of Sr, Mg and Cu addition on the microstructural properties of a secondary AlSiCu3(Fe) die casting alloy. Materials Characterization 85, 13-25.
- Fiorese E., Bonollo F., Timelli G., Arnberg L., Gariboldi E., 2015. New classificationof defects and imperfections for aluminum alloy castings. International Journal of Metalcasting 9, 55-66.
- Hu Z., Wan L., Lu S., Zhu P., Wu S., 2014. Research on the microstructure, fatigue and corrosion behavior of permanent mold and die cast aluminum alloy. Materials and Design 55, 353-360.
- Mayer H., Papakyriacou M., Zettl B., Stanzl-Tschegg S.E., 2003. Influence of porosity on the fatigue limit of die cast magnesium and aluminium alloys. International Journal of Fatigue 25, 245-256.
- Meneghetti G., Susmel L., Tovo R., 2007. High-cycle fatigue crack paths in specimens having different stress concentration features. Engineering Failure Analysis 14, 656-672.
- Mu P., Nadot Y., Nadot-Martin C., Chabod A., Serrano-Munoz I., Verdu C., 2014. Influence of casting defects on the fatigue behavior of cast aluminum AS7G06-T6. International Journal of Fatigue 63, 97-109.
- Serrano-Munoz I., Buffiere J.-Y., Verdu C., Gaillard Y., Mu P., Nadot Y., 2016. Influence of surface and internal casting defects on the fatigue behaviour of A357-T6 cast aluminium alloy. International Journal of Fatigue 82, 361-370.
- Timelli G., Ferraro S., Grosselle F., Bonollo F., Voltazza F., Capra L., 2011. Caratterizzazione meccanica e microstrutturale di leghe di alluminio pressocolate. La Metallurgia Italiana 1, 5-17.
- Wang Q.G., Apelian D., Lados D.A., 2001. Fatigue behavior of A356-T6 aluminum cast alloys. Part I. Effect of casting defects. Journal of Light Metals 1, 73-84.
9. Copyright:
- This material is "The Authors"'s paper: Based on "Effects of microstructure and casting defects on the fatigue behavior of the high-pressure die-cast AlSi9Cu3(Fe) alloy". (この資料は「著者ら」の論文:「高圧ダイカストAlSi9Cu3(Fe)合金の疲労挙動に及ぼすミクロ組織と鋳造欠陥の影響」に基づいています。)
- Paper Source: 10.1016/j.prostr.2017.11.119 (論文ソース: 10.1016/j.prostr.2017.11.119)
This material was summarized based on the above paper, and unauthorized use for commercial purposes is prohibited. (この資料は上記の論文に基づいて要約されたものであり、商業目的での無断使用は禁止されています。)
Copyright © 2025 CASTMAN. All rights reserved. (Copyright © 2025 CASTMAN. 無断複写・転載を禁じます。)