本紹介資料は、[Hindawi Publishing Corporation] が発行した ["Experimental and Theoretical Studies on the Effect of Die Temperature on the Quality of the Products in High-Pressure Die-Casting Process"] 論文の研究内容です。
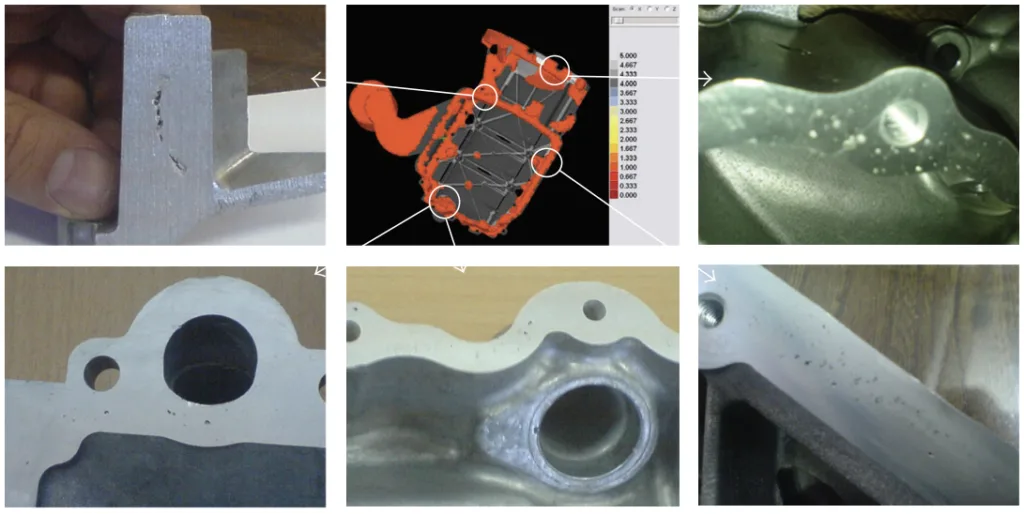
1. 概要:
- タイトル: 高圧ダイカストプロセスにおける金型温度が製品品質に及ぼす影響に関する実験的および理論的研究 (Experimental and Theoretical Studies on the Effect of Die Temperature on the Quality of the Products in High-Pressure Die-Casting Process)
- 著者: Mohammad Sadeghi and Jafar Mahmoudi
- 出版年: 2012
- 掲載ジャーナル/学会: Advances in Materials Science and Engineering
- キーワード: 高圧ダイカスト (HPDC)、金型温度、A380 合金、数値シミュレーション、ProCAST、凝固、鋳造欠陥。
2. 要約
A380 合金の高圧ダイカストにおける金型温度は、実験的観察と数値シミュレーションによって最適化されました。非常に複雑な形状を持つラダーフレーム (新しいモーター EF7 の一部) が実験サンプルとして選択されました。良好な部品を製造するために、金型温度と溶湯温度を調査しました。初期段階と最終充填位置での金型温度を測定し、これらの値の差を計算しました。ProCAST ソフトウェアを使用して部品の流体流れと凝固段階をシミュレーションし、その結果は実験測定によって検証されました。この合金に適した金型温度は 200°C 以上であることが示されました。
3. 研究背景:
研究テーマの背景:
高圧ダイカスト (HPDC) は、特に自動車産業において、高い寸法精度と生産性を持つ部品を製造するために広く使用されている製造プロセスです [1-7]。
先行研究の現状:
以前の研究は、プロセスパラメータの最適化 [14-16]、充填と凝固のシミュレーション [10, 11, 12]、プロセスパラメータが欠陥に及ぼす影響の研究 [6, 7, 8, 9, 13] に焦点を当てていました。しかし、産業用途で見られるような複雑な形状に関する研究は限られています。
研究の必要性:
品質を改善し、欠陥を減らすために、複雑な自動車部品、特に金型温度に対するプロセスパラメータの最適化が必要です。
4. 研究目的と研究課題:
研究目的:
A380 合金で作られた複雑な自動車部品 (ラダーフレーム) に対する HPDC プロセスにおける金型温度を最適化する。
主要な研究:
金型温度が鋳造製品の品質、特に欠陥形成に及ぼす影響を調査する。
5. 研究方法
- 研究デザイン: 実験と数値シミュレーションの組み合わせ。
- データ収集:
- 実験: 熱電対とレーザー高温計 (モデル chy 110) を使用した金型および溶湯温度の測定。IDRA1600 ダイカストマシンを使用した鋳造試験の実施。
- 数値: ProCAST ソフトウェアを使用した流体流れと凝固のシミュレーション。
- 分析方法: 実験温度測定値とシミュレーション結果の比較。金型温度に関連する欠陥形成の分析。
- 研究対象と範囲: 複雑な形状を持つ A380 アルミニウム合金製のラダーフレーム (新しいモーター EF7 の部品)。この研究は金型温度の影響に焦点を当てています。
- 支配方程式:
一連の偏微分方程式が解かれます。
質量保存則。式(1)。
運動量保存則。式(2)。
エンタルピー形式で記述されたエネルギー保存則。式(3)。
凝固を考慮に入れるために、ph は式(4)のように記述されます。
自由表面モデリングは、スカラー変数 Φ を使用して達成されます。式(5)。
6. 主要な研究結果:
主要な研究結果と提示されたデータ分析:
- この用途における A380 合金の最適な金型温度は 200°C 以上です。
- 低い金型温度 (例: 150°C) は、冷え流れ欠陥および気孔欠陥の可能性を増加させます (図 1-3, 5)。
- ProCAST を使用したシミュレーション結果は、実験観察によって検証された欠陥位置を正確に予測しました (図 9, 11, 12)。
- 注入開始時と終了時の溶湯温度の差は、低い金型温度で大幅に増加しました (図 4)。
- 特に穴などの形状周辺の乱流パターンは、空気の巻き込みと気孔形成に寄与します (図 8)。
- 表1:材料特性。
- 表2:初期条件と境界条件。
- 表3:ショットスリーブの初期注入時および最終注入終了充填位置での溶湯温度。
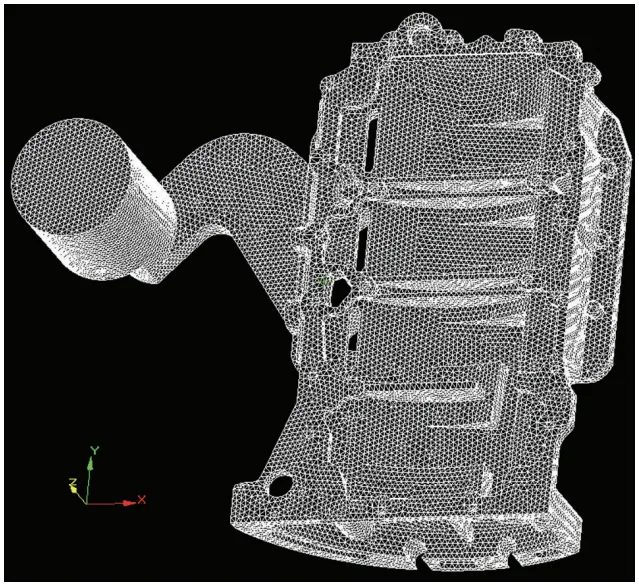
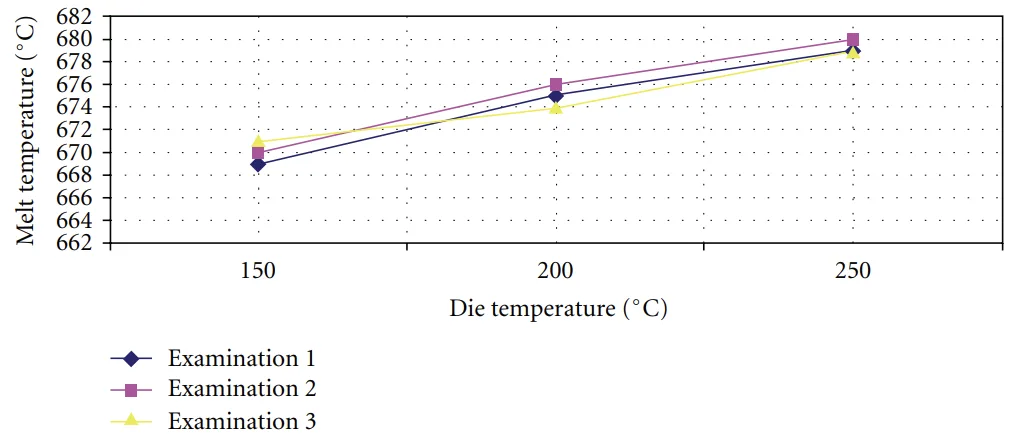
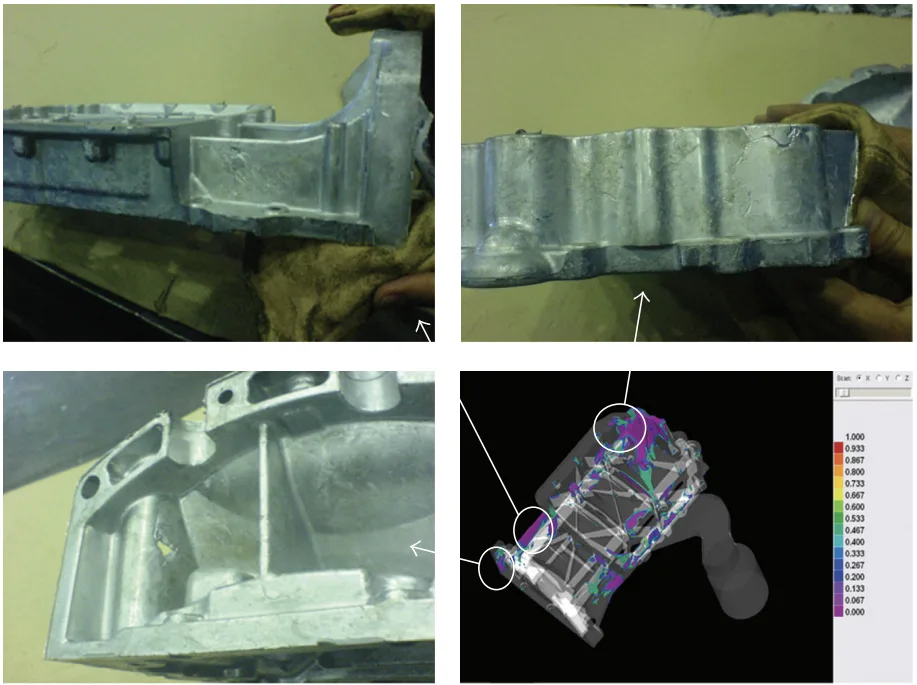
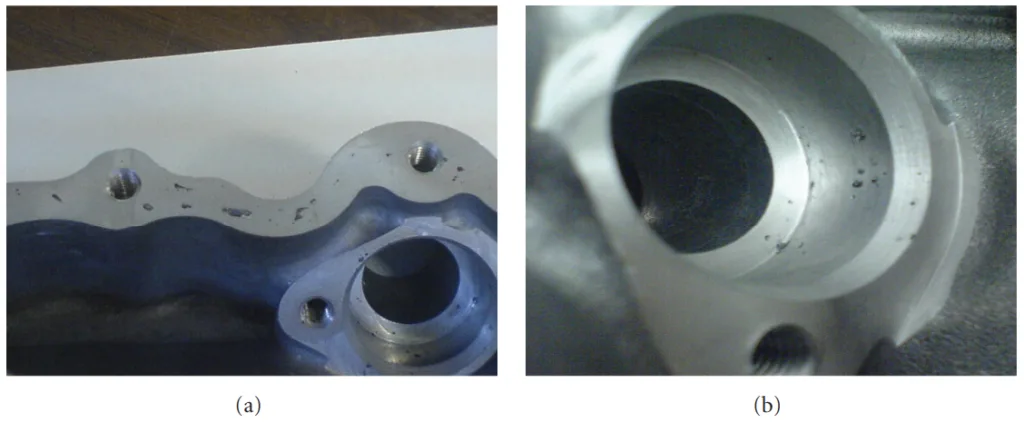
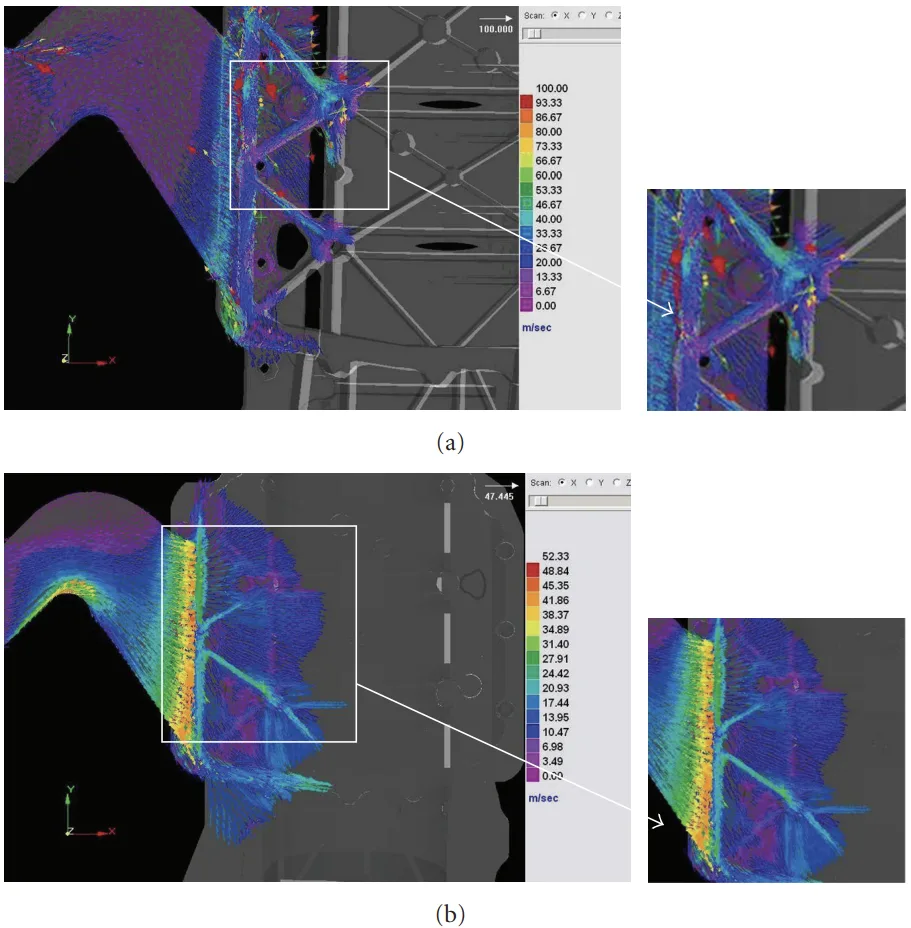
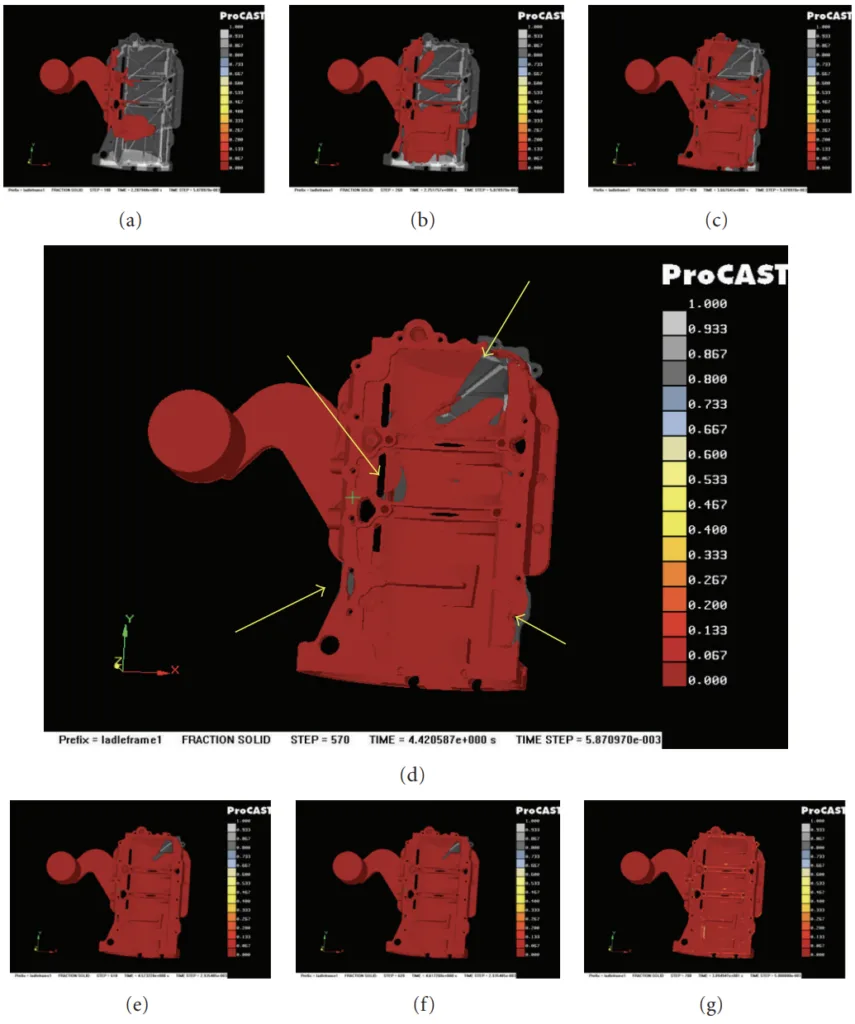
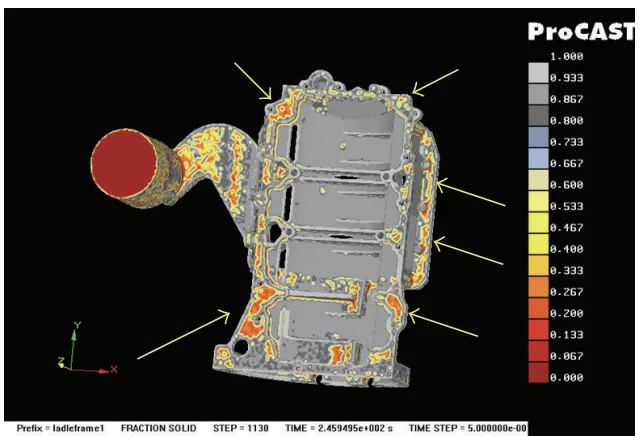
図のリスト:
- 図 1: ラダーフレーム製品の形状。
- 図 2: 金型入口および注入開始時の溶湯温度 対 金型温度。
- 図 3: 金型端部および注入終了時の溶湯温度 対 金型温度。
- 図 4: 初期および注入終了時のさまざまな金型温度における溶湯温度の低下。
- 図 5: 最終充填位置における冷え流れ表面欠陥。
- 図 6: 金型に追加されたオーバーフロー位置。
- 図 7: いくつかの気孔欠陥。
- 図 8: ゲート前面の 3 つの穴における溶湯の速度ベクトル。
- 図 9: 溶湯によって満たされた金型ステップと終点の表示。
- 図 10: 金型温度 (a) 150°C および (b) 250°C (同時刻) における溶湯の流れパターン。時間 a1 = b1, a2 = b2, a3 = b3。
- 図 11: 鋳造欠陥の影響を受けやすい凝固段階終了時のホットスポット。
- 図 12: 最終凝固位置で発生した欠陥。
7. 結論:
主要な調査結果の要約:
- 実験結果とシミュレーション結果の比較により、部品の欠陥はシミュレーションで予測された位置に配置されることが示されています。
- H13 金型材料に対する A380 合金の最適な金型温度は、約 200°C です。
- 金型温度が最適温度範囲から低下すると、冷え流れ欠陥および気孔欠陥の可能性が増加します。
- シミュレーションによるオーバーフローの最適化された位置の決定により、冷え込みや気孔などの一部の鋳造欠陥が減少しました。
- 金型設計において、これらの欠陥領域の近くにオーバーフローを配置することで、冷え流れ欠陥および気孔を低減できます。
8. 参考文献:
- [1] M. S. Dargusch, G. Dour, N. Schauer, C. M. Dinnis, and G. Savage, "The influence of pressure during solidification of high pressure die cast aluminium telecommunications components," Journal of Materials Processing Technology, vol. 180, no. 1-3, pp. 37–43, 2006.
- [2] Z. W. Chen and M. Z. Jahedi, "Die erosion and its effect on soldering formation in high pressure die casting of aluminium alloys," Materials and Design, vol. 20, no. 6, pp. 303–309, 1999.
- [3] P. W. Cleary, J. Ha, M. Prakash, and T. Nguyen, "3D SPH flow predictions and validation for high pressure die casting of automotive components," Applied Mathematical Modelling, vol. 30, no. 11, pp. 1406–1427, 2006.
- [4] K. J. Laws, B. Gun, and M. Ferry, "Effect of die-casting parameters on the production of high quality bulk metallic glass samples," Materials Science and Engineering A, vol. 425, no. 1-2, pp. 114–120, 2006.
- [5] D. McBride, T. N. Croft, and M. Cross, "A coupled finite volume method for the computational modelling of mould filling in very complex geometries," Computers & Fluids, vol. 37, no. 2, pp. 170–180, 2008.
- [6] C. C. Tai and J. C. Lin, “The optimal position for the injection gate of a die-casting die,” Journal of Materials Processing Technology, vol. 86, no. 1-3, pp. 87–100, 1998.
- [7] S. W. Youn, C. G. Kang, and P. K. Seo, "Thermal fluid/solidification analysis of automobile part by horizontal squeeze casting process and experimental evaluation," Journal of Materials Processing Technology, vol. 146, no. 3, pp. 294–302, 2004.
- [8] J. X. Zhou, L. L. Chen, D. M. Liao, and R. X. Liu, "High pressure diecasting module of InteCAST software and its applications," Journal of Materials Processing Technology, vol. 192-193, pp. 249–254, 2007.
- [9] S. Yue, G. Wang, F. Yin, Y. Wang, and J. Yang, “Application of an integrated CAD/CAE/CAM system for die casting dies,” Journal of Materials Processing Technology, vol. 139, no. 1-3, pp. 465–468, 2003.
- [10] A. Kermanpur, S. Mahmoudi, and A. Hajipour, "Numerical simulation of metal flow and solidification in the multi-cavity casting moulds of automotive components," Journal of Materials Processing Technology, vol. 206, no. 1-3, pp. 62–68, 2008.
- [11] S. Schneiderbauer, S. Pirker, C. Chimani, and R. Kretz, "Studies on flow characteristics at high-pressure die-casting," in Proceedings of the 3rd International Conference on Advances in Solidification Processes.
- [12] M. F. V. T. Pereira, M. Williams, and W. B. du Preez, "Reducing non value adding aluminium alloy in production of parts through high pressure die casting," in Proceedings of the Light Metals Conference, 2010.
- [13] J. K. Rai, A. M. Lajimi, and P. Xirouchakis, "An intelligent system for predicting HPDC process variables in interactive environment," Journal of Materials Processing Technology, vol. 203, no. 1-3, pp. 72–79, 2008.
- [14] B. S. Sung and I. S. Kim, “The molding analysis of automobile parts using the die-casting system,” Journal of Materials Processing Technology, vol. 201, pp. 635–639, 2008.
- [15] V. Ilotte, "Die casting for chassis components," in Proceedings of the 4th International High Tech Die Casting Conference, Montichiari, Italy, April 2008.
- [16] Z. Brown, C. Barnes, J. Bigelow, and U. S. Contech, "Squeeze cast automotive applications and design considerations," in Proceedings of the 4th International High Tech Die Casting Conference, Montichiari, Italy, April 2008.
- [17] J. P. Papai, Contact heat transfer coefficients in aluminum alloy die casting: an experimental and numerical investigation? [Ph.D. thesis], The Ohio State University, 1994.
9. 著作権:
- 本資料は、[著者] の論文: [論文タイトル] を基にしています。
- 論文出典: [DOI URL]
本資料は上記論文を紹介するために作成されたものであり、商業目的での無断使用を禁じます。Copyright © 2025 CASTMAN. All rights reserved.