研究の核心目的: 高圧ダイカストプロセスにおける金型内圧力センサを用いて、プロセス変数(集約圧力、遅延時間、鋳造速度)が最終製品の完全性に及ぼす影響、特にダイキャビティ内の状態とプロセスパラメータ間の関係を解明し、従来の高速度機械加工から高圧ダイカストへの移行過程で発生する気孔問題を解決するための最適なプロセスパラメータを導き出すこと。
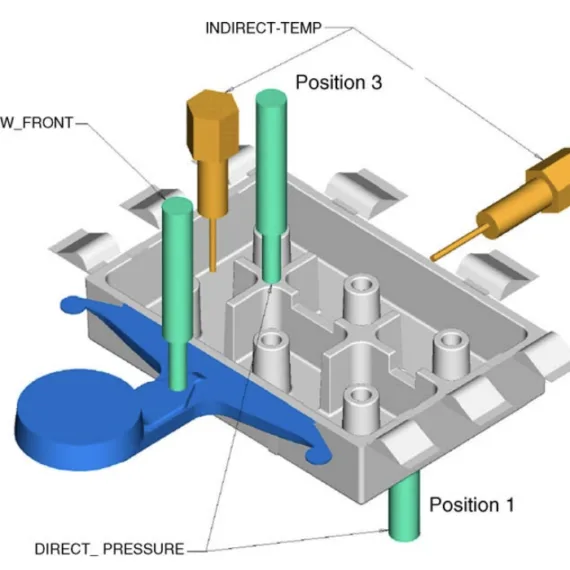
主要な方法論:
本研究では、金型内に圧力センサを設置し、高圧ダイカストプロセス中のリアルタイムの圧力変化を測定する実験的手法を用いた。集約圧力、遅延時間、鋳造速度などの様々なプロセス変数を変化させながら得られたデータを分析し、最終製品の気孔率との相関関係を調査。2種類の異なるアルミニウム合金(DA 401とCA 313)を用いて実験を行い、製造された部品の気孔率を定量的に測定して分析に用いた。実験には、ビューラー53 D エボリューション530トン冷間チャンバ高圧ダイカストマシンとビューラーショットコントロールシステムを用いた。
主要な結果:
- 集約圧力の影響: 集約圧力の増加に伴い、気孔率は減少する傾向を示した。これは、高圧が気孔の形成を抑制する効果があることを示唆している。合金の種類によって多少の違いが見られ、CA 313合金では圧力増加に伴う気孔率の減少効果がDA 401合金よりも不規則であった。
- 遅延時間の影響: 集約圧力の適用前の遅延時間は、気孔率に大きな影響を与えなかった。しかし、CA 313合金では遅延時間の増加に伴い気孔率が増加する傾向が観察されたものの、統計的に有意なレベルではなかった。
- 鋳造速度の影響: 鋳造速度の増加に伴い、気孔率が増加する傾向が観察された。これは、高速鋳造時に乱流が発生し、気孔が発生する可能性が高まることを示唆している。しかし、高圧力下では鋳造速度の影響は比較的減少した。
- 設定値と実測値の比較: 設定圧力と金型内圧力の実際測定値の間には差異が存在した。圧力の増加に伴い、この差異は大きくなった。また、設定鋳造速度と実際鋳造速度の間にも差異が見られたが、その差異は小さかった。
研究者情報:
- 所属機関: ªCRC for Cast Metals Manufacturing (CAST), クイーンズランド大学, オーストラリア; ᵇアルビ=カルモー鉱山学校, フランス; ᶜフェラエンジニアリング プライベート リミテッド, オーストラリア; ᵈCRC for Cast Metals Manufacturing (CAST), CSIRO製造インフラストラクチャ技術, オーストラリア
- 著者: Matthew S. Dargusch, G. Dour, N. Schauer, C.M. Dinnis, G. Savage
- 主要研究分野: 高圧ダイカスト、金型設計、鋳造プロセス最適化、材料科学
研究背景と目的:
アルミニウム自動車部品の生産には高圧ダイカストが広く用いられているが、寸法公差が厳しく表面品質の高い通信部品の生産には、従来、高速機械加工が主に用いられてきた。高速機械加工は少量生産には適しているが、大量生産には非効率的でコスト高となる。本研究は、高圧ダイカストによる通信部品の生産性向上と製造コスト削減を目指し、気孔問題などの技術的課題を解決するための最適なプロセスパラメータを見出すことを目的とした。
論文の主要な目的と研究内容:
本研究の主な目的は、高圧ダイカストプロセスの最適化を通じて、高品質なアルミニウム通信部品を生産することである。これは以下のステップで行われた:
- 金型内圧力測定: 金型内に圧力センサを設置し、ダイキャビティ内の圧力をリアルタイムで測定することで、プロセス変数と最終製品の品質の関係を正確に把握しようとした。
- プロセス変数の最適化: 集約圧力、遅延時間、鋳造速度といった様々なプロセス変数を系統的に変化させ、各変数が気孔形成に及ぼす影響を分析。最適なプロセス条件を導き出すことを目指した。
- 合金の種類による影響分析: 2種類の異なるアルミニウム合金(DA 401とCA 313)を用いて実験を行い、合金の種類によるプロセス変数の影響の違いを比較分析した。
- 結果分析と最適化: 得られた実験データを分析し、各プロセス変数と気孔率の相関関係を定量的に分析。その結果に基づき、最適なプロセス条件を提示した。
主要な図表:
- 図3: 金型内圧力センサの測定結果。時間に対する圧力変化を示す。
- 図4: 設定集約圧力と実測最大キャビティ圧力の比較グラフ。
- 図5: 設定注入速度と実測注入速度の比較グラフ。
- 図6, 7: 遅延時間と気孔率の関係を示すグラフ(DA 401、CA 313合金)。
- 図8, 9: キャビティ位置1における最大圧力と気孔率の関係を示すグラフ(CA 313、DA 401合金)。
- 図10, 11: キャビティ位置3における最大圧力と気孔率の関係を示すグラフ(DA 401、CA 313合金)。
- 図12, 13: 設定集約圧力と気孔率の関係を示すグラフ(DA 401、CA 313合金)。
- 図14, 15: 実測鋳造速度と気孔率の関係を示すグラフ(DA 401、CA 313合金)。
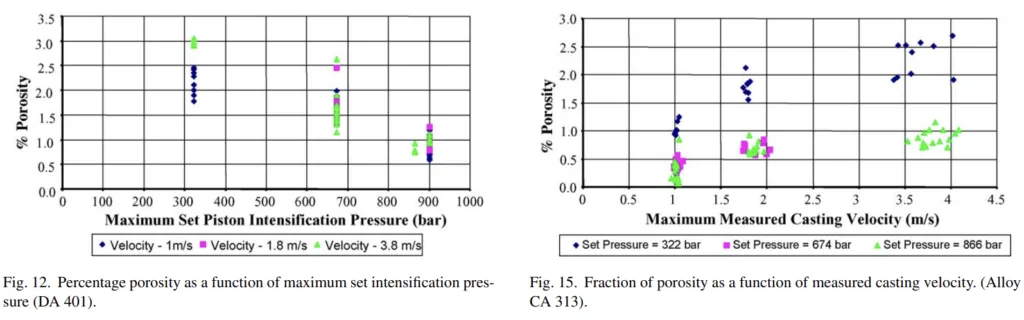
結果と成果:
- 定量的結果: 様々なプロセス変数条件下で測定された気孔率データから、集約圧力の増加による気孔率の減少、鋳造速度の増加による気孔率の増加などの定量的関係を示した。設定圧力と実測圧力の差も定量的に分析。
- 定性的結果: 金型内圧力センサを用いたリアルタイム圧力測定により、高圧ダイカストプロセスの理解を深めた。設定プロセス変数と実際プロセス変数の差異を分析し、プロセス制御の重要性を強調。最終的に、実験で製造された部品は均一な機械的特性を示した。
- 技術的成果: 本研究は、高圧ダイカストプロセスの最適化のための新しい方法論を示した。金型内圧力センサによるリアルタイムモニタリングと制御により、気孔などの欠陥を最小限に抑え、製品品質を向上できることを示した。これは、高品質アルミニウム通信部品の大量生産に貢献する技術的成果と言える。
著作権と参考文献:
この要約は、Matthew S. Darguschらの論文 "The influence of pressure during solidification of high pressure die cast aluminium telecommunications components"に基づいて作成されました。
出典: DOI: 10.1016/j.jmatprotec.2006.05.001
論文著作権 © 2006 Elsevier B.V. 全著作権所有。この要約は上記論文に基づいて要約されており、著作権者の許可なく商業目的で使用することはできません。