1. 概要:
- タイトル: 高圧ダイカストを用いたアルミニウム中空サブフレームの開発 (Development of Aluminium Hollow Subframe Using High-Pressure Die Casting)
- 著者:
- Akihiko Asami
- Tomoyuki Imanishi
- Yukio Okazaki
- Tomohiro Ono
- Kenichi Tetsuka
- 発行年: 2016年
- 発行学術誌/学会: SAE Technical Paper
- キーワード:
- 高圧ダイカスト (High-Pressure Die Casting, HPDC)
- アルミニウム中空サブフレーム (Aluminium Hollow Subframe)
- 軽量化 (Weight Saving)
- 砂中子 (Sand Core)
- Al-Mg-Si 合金 (Al-Mg-Si Alloy)
- 薄肉部品 (Thin-walled Parts)
2. 研究背景:
- 研究テーマの社会的/学術的背景:
- 自動車の軽量化に対する要求は、地球環境保護のために炭素排出量を削減し、エネルギーを節約するために今日高まっています。
- 軽量化は、燃費効率の向上とダイナミック性能の向上にも貢献します。
- 高張力鋼板と軽量アルミニウムは、自動車用サブフレームの軽量化を達成するために採用されている材料です。
- クローズドセクション構造は、オープンセクション構造と比較して部品の剛性を効率的に高めるために一般的に使用されています。
- アルミニウム中空サブフレームも実用化されており、砂中子を用いて重力ダイカスト (Gravity Die Casting, GDC) または低圧ダイカスト (Low-Pressure Die Casting, LPDC) プロセスで製造されています。
- 既存研究の限界:
- 砂中子を使用する従来のアルミニウム中空鋳造方式である GDC または LPDC は、製品の肉厚を薄くすることに限界があります。
- GDC または LPDC では、肉厚を薄くすると、鋳造中にアルミニウム溶湯の流速が低下します。金型と砂中子がアルミニウム溶湯から熱を奪い、アルミニウムが凝固する傾向があります。
- GDC および LPDC におけるこれらの肉厚減少の限界は、大幅な軽量化の達成を妨げています。
- 溶接アルミニウムサブフレームに関連する高コスト (材料費、金型費、溶接費を含む) は、その広範な採用を妨げています。
- 研究の必要性:
- 既存の方法の限界を克服し、車両重量をさらに削減するために、軽量薄肉アルミニウム中空サブフレームを製造できる製造方法が必要です。
- 大型中子を成形し、良好な流動性を示す材料を開発する技術が、この技術を実現するために不可欠です。
3. 研究目的及び研究質問:
- 研究目的:
- 薄肉化に適した製造方法である高圧ダイカスト (HPDC) を採用した軽量中空サブフレーム技術を開発すること。
- HPDC 条件に合わせて耐圧性と崩壊性のバランスをとる砂中子技術を開発し、サブフレームのような大型部品の中空鋳造を可能にすること。
- コストを削減しながら、サブフレームに適した鋳造性と機械的特性を確保するために、非熱処理 Al-Mg-Si 合金を使用すること。
- 核心研究質問:
- 最適化された砂中子技術と材料選択を組み合わせた HPDC は、従来の鋼製サブフレームと比較して大幅な軽量化を達成しながら、必要な構造的完全性と性能を維持する薄肉アルミニウム中空サブフレームを効果的に製造できるでしょうか?
- 研究仮説:
- 新たに開発された砂中子技術と最適化された非熱処理 Al-Mg-Si 合金を HPDC と共に使用することにより、構造性能を損なうことなく、従来の溶接鋼板サブフレームよりも大幅に軽量な中空アルミニウムサブフレームを製造することが可能です。
4. 研究方法論
- 研究設計:
- 本研究は、HPDC を用いたアルミニウム中空サブフレームの新しい製造プロセスの開発と実験的検証に焦点を当てました。
- 研究には、量産サブフレームの形状に基づいて、中空アルミニウムサブフレーム用の製品金型と中子金型を設計および製造することが含まれていました。
- 開発された中空アルミニウムサブフレームの性能を、静的破壊試験および耐久試験を通じて、従来の鋼製サブフレームと比較しました。
- データ収集方法:
- 鋳造実験: さまざまな鋳造条件、砂中子材料、焼成条件、および Al-Mg-Si 合金組成で HPDC 実験を実施しました。
- 機械的特性試験:
- 引張試験を実施して、Si 含有量を変化させた開発された Al-Mg-Si 合金の強度と伸びを評価しました。
- 静的破壊試験および耐久試験を製造された中空ダイカストアルミニウムサブフレームに実施し、実際の車両入力条件をシミュレーションする条件下での構造性能を評価しました。
- 寸法精度測定: 鋳造製品の寸法精度を評価して、中子固定方法と溶湯流れ最適化の効果を評価しました。
- 分析方法:
- 機械的特性分析: 引張試験、静的破壊試験、および耐久試験の結果を分析して、開発された材料およびサブフレームの機械的性能を評価しました。
- 比較分析: 開発された中空アルミニウムサブフレームの重量と性能を従来の鋼製サブフレームと比較して、軽量化と性能特性を定量化しました。
- プロセスパラメータ最適化: 鋳造条件、砂中子パラメータ、および合金組成が鋳造サブフレームの品質と性能に及ぼす影響を分析して、製造プロセスを最適化しました。
- 研究対象及び範囲:
- 本研究は、自動車用アルミニウム中空サブフレームの開発に焦点を当てました。
- 範囲は以下を含みます:
- HPDC に適した砂中子成形技術の開発。
- HPDC 中空鋳造用の非熱処理 Al-Mg-Si 合金の材料選択と最適化。
- 中空サブフレームの HPDC 用金型の設計と製造。
- 静的破壊試験および耐久試験による開発されたサブフレームの機械的性能の実験的検証。
- 重量と性能の点で、開発されたアルミニウムサブフレームと従来の鋼製サブフレームの比較。
5. 主要研究結果:
- 核心研究結果:
- 大型薄肉部品用の HPDC を用いた軽量中空サブフレーム技術が首尾よく開発されました。
- HPDC に適した砂中子成形技術が確立され、砂中子の耐圧性と崩壊性のバランスの問題に対処しました。
- 最適化された非熱処理 Al-Mg-Si 合金に Si を添加して開発し、HPDC 中空鋳造用の鋳造性と機械的特性を向上させました。
- 開発された中空アルミニウムサブフレームは、従来の溶接鋼板サブフレームと比較して約 40% の軽量化を達成しました (図 1)。
- 開発された中空ダイカストアルミニウムサブフレームは、静的破壊試験および耐久試験ですべての設定条件をクリアし、量産部品としての適合性を実証しました。
- 統計的/定性的分析結果:
- 静的破壊試験結果 (表 1): 中空ダイカストアルミニウムサブフレームは、さまざまな位置と方向での静的破壊試験で、設定条件を超えるクリアランス率を示しました。たとえば、「ロアアーム取り付け部 FT+」では、クリアランス率は最大および降伏条件の両方で 207% でした。
- 耐久試験結果 (表 2): 中空ダイカストアルミニウムサブフレームは、サスペンションアセンブリ耐久性、トルクロッド取り付け部、ステアリングギアボックス取り付け部、スタビライザー取り付け部、およびサスペンション衝撃試験を含むすべての耐久試験で設定条件をクリアしました。すべての結果は「OK」とマークされました。
- Al-Mg-Si 合金の機械的特性 (図 10, 図 15):
- Al-5Mg 材料に Si を添加すると、機械的特性が向上しました。
- Al-5Mg-1.8Si 組成は、伸びと強度のバランスをとる最適な組成であることがわかりました。この組成により、5% 以上の伸びと 150MPa 以上の強度を安定的に実現することができました。
- 板状試験金型を用いた鋳造試験では、約 2.0% の Si 添加で、強度と伸びのバランスがサブフレームに最適であると判断されました (図 10)。
- データ解釈:
- HPDC は、開発された砂中子技術と最適化された Al-Mg-Si 合金と組み合わせると、軽量で高性能なアルミニウム中空サブフレームを製造するための実行可能で効果的な方法です。
- 開発された中空アルミニウムサブフレームによって達成された 40% の軽量化は、従来の鋼製サブフレームと比較して大幅な改善を示しており、車両の軽量化と燃費向上に貢献しています。
- 静的破壊試験および耐久試験条件の首尾よいクリアランスは、自動車用途向けの開発された中空アルミニウムサブフレームの構造的完全性と信頼性を検証します。
- Figure Name List:
- Figure 1. 開発された中空アルミニウムサブフレーム (Developed hollow aluminum subframe)
- Figure 2. オートバイフレーム部品 (CBR600RR) (Motorcycle frame parts (CBR600RR))
- Figure 3. 各製造方法の鋳造条件の比較 (Comparison of casting conditions for each manufacturing method)
- Figure 4. 製造プロセス (Manufacturing process)
- Figure 5. 一次焼成後のコア断面 (Section of core following primary baking)
- Figure 6. 温度変化とフェノール樹脂溶融粘度 (Change in temperature and phenol resin melt viscosity)
- Figure 7. 温度変化と残留フェノール樹脂量 (Change in temperature and amount of residual phenol resin)
- Figure 8. 厚肉部コア中心部の焼成時間 (Time to baking of center of thick part of core)
- Figure 9. ゲート速度と強度の関係 (Relationship between gate speed and strength)
- Figure 10. Al-Mg 材料の機械的特性の変化に対する Si 添加量の影響 (Effect of amount of added Si on change in mechanical properties of Al-Mg material)
- Figure 11. 製品形状とコア形状 (Shape of product and shape of core)
- Figure 12. ボードの位置 (Position of boards)
- Figure 13. コア保持ピンと砂抜き窓の位置 (Position of core holding pin and sand removal window)
- Figure 14. 試験片切断位置 (Position for cutting of test piece)
- Figure 15. サブフレームから切り出した試験片の機械的特性 (Mechanical properties of test pieces cut from subframe)
- Figure 16. 静的破壊試験と耐久試験 (Static fracture test and durability test)
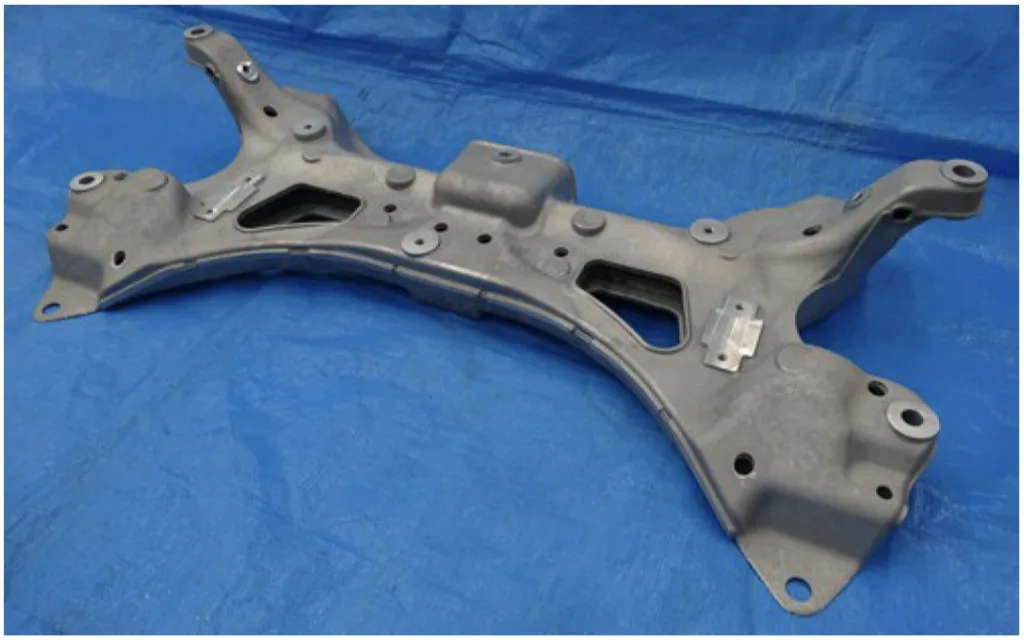
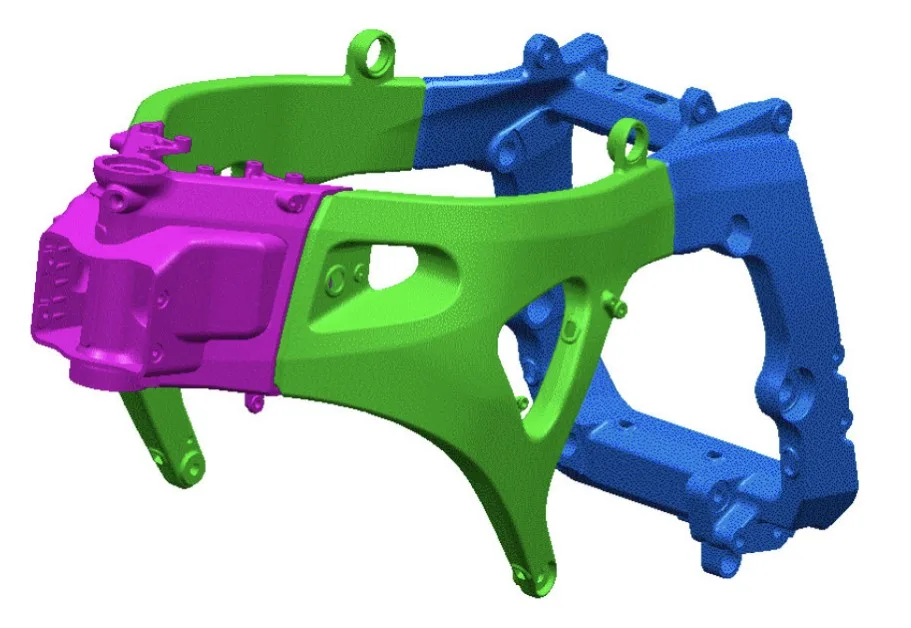
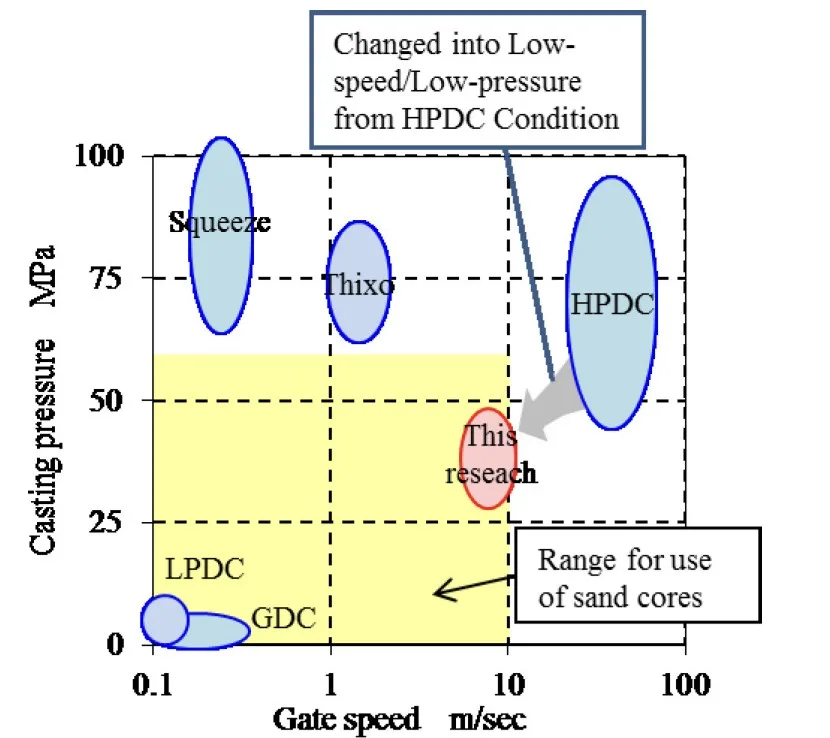
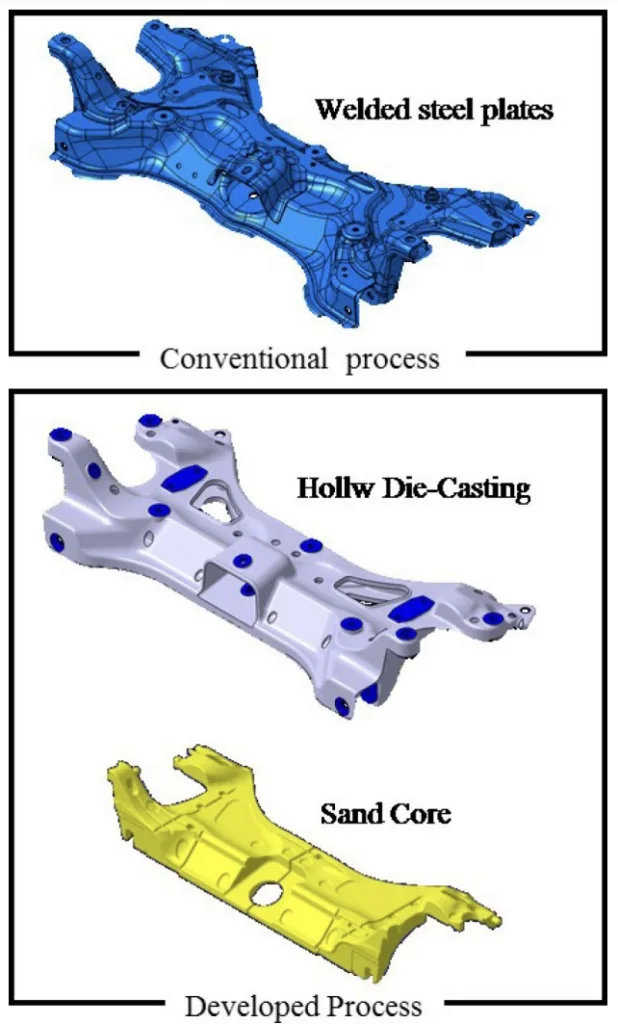
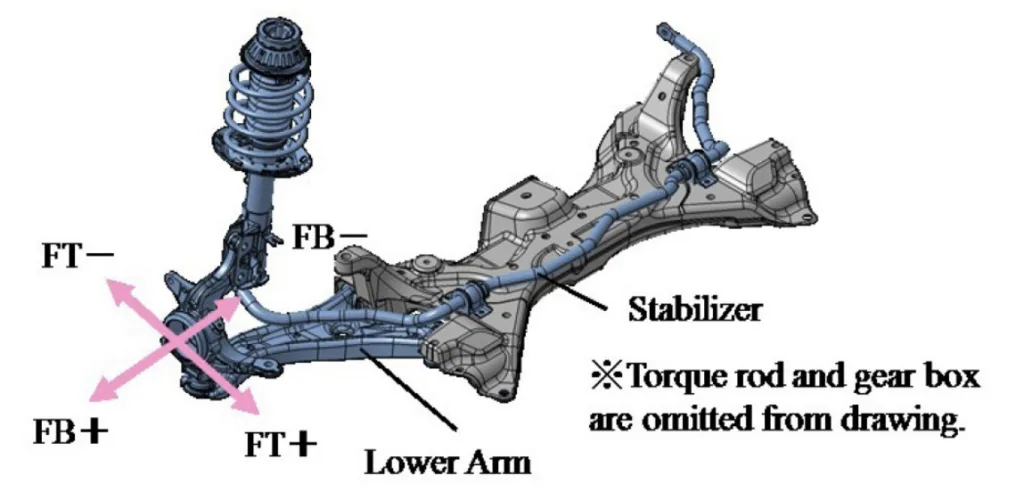
6. 結論及び考察:
- 主要結果の要約:
- 本研究では、大型薄肉アルミニウムサブフレームの製造に HPDC を用いた中空鋳造技術を首尾よく開発しました。
- 主な革新には、HPDC に適した砂中子成形技術と、Si 添加された非熱処理 Al-Mg-Si 合金の最適化が含まれます。
- 開発された中空アルミニウムサブフレームは、静的破壊試験および耐久試験ですべての性能要件を満たしながら、従来の鋼製サブフレームと比較して大幅な 40% の軽量化を達成しました。
- 研究の学術的意義:
- 本研究は、HPDC がサブフレームのような複雑な中空自動車構造部品の製造に使用できる可能性と有効性を実証しています。
- HPDC 専用に調整された砂中子技術の開発は、この生産性の高い鋳造方法の適用範囲を拡大します。
- 最適化された Al-Mg-Si 合金は、鋳造性、機械的特性、およびコストのバランスをとる軽量アルミニウム鋳物用の費用対効果の高い材料ソリューションを提供します。
- 実務的示唆:
- 開発された HPDC 中空鋳造技術は、自動車産業向けの軽量アルミニウムサブフレームを製造するための実行可能な製造ソリューションを提供します。
- 達成された大幅な軽量化は、燃費の向上、炭素排出量の削減、および車両性能の向上に貢献します。
- 非熱処理 Al-Mg-Si 合金の使用は、製造コストを最小限に抑えるのに役立ち、アルミニウム中空サブフレームをより広く採用するために経済的に魅力的にします。
- 研究の限界:
- 本研究は、特定のサブフレーム設計と材料組成に焦点を当てました。開発された技術の他のサブフレーム設計またはアルミニウム合金への一般化可能性は、さらなる調査が必要になる場合があります。
- 本研究は主に機械的性能に焦点を当てました。腐食抵抗や実際の車両運転条件での長期耐久性などの他の側面は、さらに調査することができます。
7. 今後のフォローアップ研究:
- 今後の研究方向:
- 生産性と鋳造品質を向上させるための、射出速度、鋳造圧力、および冷却条件を含む HPDC プロセスパラメータのさらなる最適化。
- HPDC 中空鋳造サブフレームの機械的特性、鋳造性、および費用対効果をさらに向上させるための、他のアルミニウム合金および組成の探求。
- 開発された HPDC 中空鋳造技術を他の自動車部品および構造部品に適用して、車両全体の軽量化と性能上の利点を最大化します。
- 追加探求が必要な領域:
- 開発された中空アルミニウムサブフレームの長期性能と信頼性を検証するための、長期耐久性研究と実際の車両テストの実施。
- 材料費、製造費、および性能上の利点を考慮して、量産の経済的実現可能性を評価するための包括的な費用対効果分析の実施。
- 中空サブフレーム構造とトポロジの設計最適化を通じて、さらなる軽量化の可能性の調査。
8. 参考文献:
- Koya, E., Suzuki, T., Nakagawa, M., Fujimoto, G. et al., "Development of Hollow, Weld-able Die-Cast Parts for Aluminum Motorcycle Frames," SAE Technical Paper 2003-32-0055, 2003, doi:10.4271/2003-32-0055.
9. Copyright:
- 本資料は、Akihiko Asami, Tomoyuki Imanishi, Yukio Okazaki, Tomohiro Ono, and Kenichi Tetsuka の論文: Development of Aluminium Hollow Subframe Using High-Pressure Die Casting を基に作成されました。
- 論文出典: doi:10.4271/2016-01-0406
本資料は上記論文を基に要約作成されたものであり、商業目的での無断使用は禁止されています。
Copyright © 2025 CASTMAN. All rights reserved.