本紹介記事は、STM Journals が発行した論文「Injection Parameters Setting in High-Pressure Die Casting」の研究内容です。
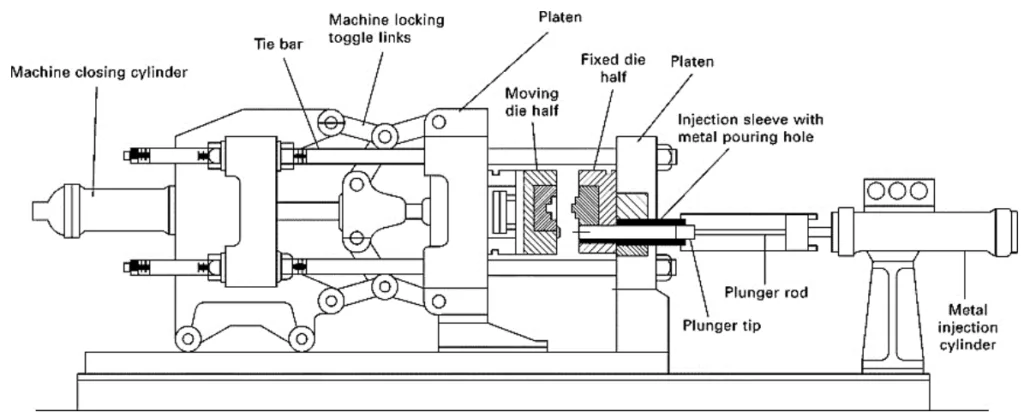
1. 概要:
- タイトル: Injection Parameters Setting in High-Pressure Die Casting (高圧ダイカストにおける射出パラメータの設定)
- 著者: Rahul B., Bhaskar M. Reddy, Tamilselvam Nallusamy, W. Brightlin Abisha, Suresh P.
- 出版年: 2023年
- 掲載ジャーナル/学会: Journal of Polymer & Composites (Volume 11, Special Issue 13)
- キーワード: Casting defects (鋳造欠陥), Cavity pressure (キャビティ圧力), Fill time (充填時間), Gate area (ゲート面積), Injection velocity (射出速度)
2. 概要 (Abstract)
科学および加工技術の進歩は非常に重要です。アルミニウムダイカスト部品は広く使用されています。適切なプロセスパラメータが必要です。この論文では、最適な射出パラメータを研究します。高圧ダイカストプロセス (HPDC) でよく見られる欠陥は、コールドシャット、フローライン、ブローホール、ピンホール、収縮、ガス巻き込みポロシティなどです。本研究では、低速、高速、および増圧機能の効果を分析します。第1段階の長さ、第1段階の速度、第2段階の長さ、第2段階の速度、第3段階のキャビティ圧力と保持時間などの射出パラメータの最適値を推定します。
3. 研究背景:
研究テーマの背景:
アルミニウムなどの金属および合金は、高い比強度や耐食性などの特性により、自動車、複合材料、航空宇宙などのエンジニアリング用途で広く使用されています[1-6]。ダイカストプロセスは、重力ダイカスト (GDC)、低圧ダイカスト (LPDC)、高圧ダイカスト (HPDC) に分類されます[7–9]。
従来の研究の状況:
- 重力ダイカスト (GDC): 重力と大気圧を使用します。肉厚が 6mm より大きく、鋳造重量が 3 ~ 25kg の部品に推奨されますが、HPDC よりも生産速度が遅くなります[10–14]。
- 低圧ダイカスト (LPDC): 加圧ガス (0.1 ~ 0.3 bar) を使用して金型キャビティを充填します[9, 17]。ホイールやシリンダーヘッドなどの自動車部品に使用されます[18]。
- 高圧ダイカスト (HPDC): ピストンが高圧と高速で溶融金属を駆動します[19–23]。ダイセットは H13 鋼で作られ、44 ~ 46 HRC に硬化され、多くの場合窒化処理されます[24, 25, 26]。
研究の必要性:
射出パラメータ (低速、高速、増圧など) の変動は、鋳造欠陥につながる可能性があります。高品質で欠陥のない鋳物を得るには、適切な設定が不可欠です。
4. 研究目的と研究課題:
研究目的:
HPDC における射出パラメータを研究および最適化し、鋳造欠陥を低減すること。
主要な研究:
射出の 3 つの段階 (低速、高速、増圧) の効果を分析し、以下の最適値を決定すること。
- 第 1 段階の長さと速度
- 第 2 段階の長さと速度
- 第 3 段階のキャビティ圧力と保持時間
5. 研究方法
この研究では、HPDC における 3 段階射出システム (図 2) を分析し、以下に焦点を当てています。
- 充填率 (Filling Ratio): 注入された液体金属の体積と射出スリーブ全体の体積の比率。ガス巻き込みポロシティを最小限に抑えるために、60 ~ 70% の充填率が推奨されます[33–36]。
- 第 1 段階 (事前充填段階): プランジャーは、溶融金属を低速 (0.1m/sec ~ 0.6m/sec) でインゲート付近に移動させます[37]。第 1 段階の長さと速度は、北米ダイカスト協会 (NADCA) が提供する式を使用して計算されます。
- 第 2 段階 (ダイキャビティ充填段階): 液体金属が高速 (0.4m/sec ~ 6m/sec) で注入されます。金型充填時間は非常に短いです (5 ~ 100 ミリ秒)。第 2 段階の長さと速度は、ダイ設計データ、ゲート面積、ゲート速度に基づいて計算されます。
- 第 3 段階 (増圧段階): 凝固中に収縮を補うために、追加の金属が押し込まれます。増圧 (キャビティ圧力) が計算され、さまざまな種類の鋳造に対して異なる圧力が推奨されます[38-42]。
この研究では、これらの原理を使用してエンジンハウジングコンポーネントを分析し、ショット重量、鋳造重量、ゲート面積、プランジャー直径、およびアクティブスリーブ長に関する特定のデータが提供されます。
6. 主要な研究結果:
主要な研究結果と提示されたデータ分析:
この研究では、エンジンハウジングコンポーネントの射出パラメータを段階的に計算しました。
- ショット重量体積、鋳造重量体積、およびショットスリーブ体積: 提供されたデータに基づいて計算。
- 充填率: 58.53% と計算され、最適な 60 ~ 70% に近いです。
- 第 2 段階の長さ: 12.03cm と計算。
- 第 1 段階の長さ: 16.97cm と計算。
- 第 1 段階の速度: 0.077m/sec と計算され、推奨範囲内です。
- 第 2 段階の速度: 1.55m/sec と計算。
- 増圧 (キャビティ圧力): 933kg/cm² と計算され、圧力気密鋳造の推奨範囲内です。
これらの最適化されたパラメータは、生産現場で実装されました。
表 1 は、研究前後のパラメータをまとめたもので、空気巻き込み、キャビティ充填時間、圧力気密性が改善され、不良率が 8% から 1.2% に減少したことを示しています。
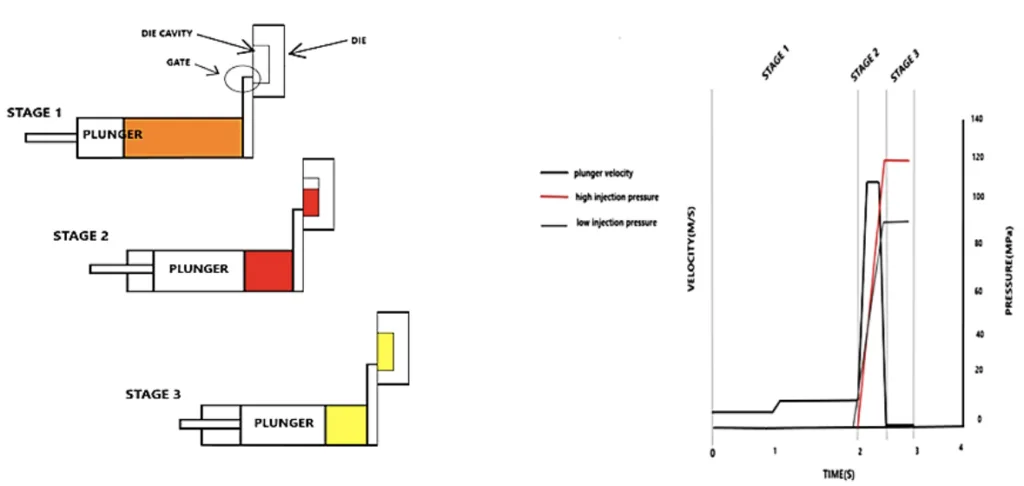
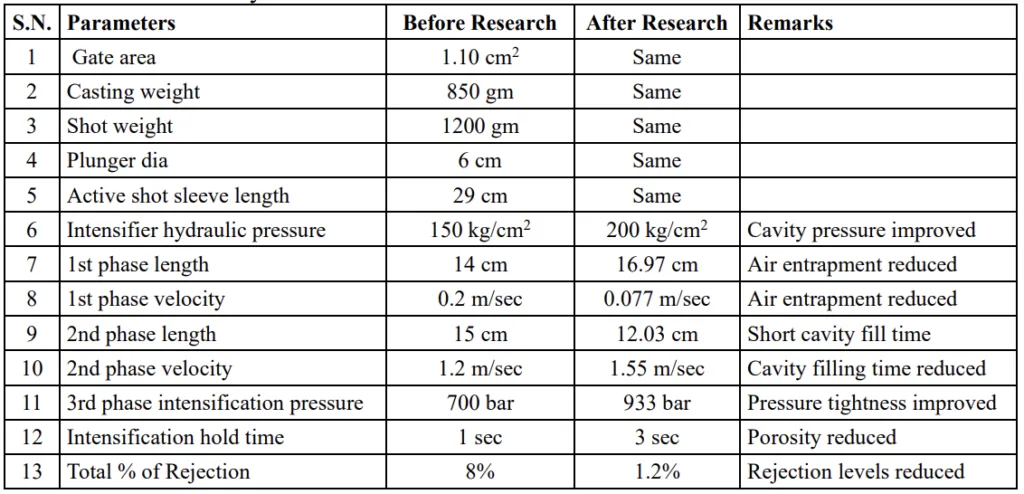
図の名称リスト:
- 図 1. コールドチャンバー水平高圧ダイカストマシン。
- 図 2. 3 段階射出システム。
7. 結論:
主要な調査結果の要約:
射出パラメータ (第 1 段階の長さと速度、第 2 段階の長さと速度、第 3 段階のキャビティ圧力と保持時間) を最適化することにより、鋳物の不良率が 8% から 1.2% に大幅に減少しました。
{研究結果の要約。研究の学術的意義、研究の実際的な意味}
この研究は、HPDC における射出パラメータの慎重な制御と計算が、高品質で欠陥のない鋳物を製造するために重要であることを示しています。実際的な意味は、スクラップの大幅な削減と生産効率の向上であり、利益と顧客満足度の向上につながります。
8. 参考文献:
- [1] Koli D K, Agnihotri G, Purohit R. Advanced aluminium matrix composites: the critical need of automotive and aerospace engineering fields. Materials Today: Proceedings. 2015; 2(4-5): 3032-041p.
- [2] Sharma A K, Rakesh Bhandari, Amit Aherwar, et al. A study of advancement in application opportunities of aluminum metal matrix composites. Materials Today: Proceedings. 2020; 26: 2419-2424p.
- [3] Eliasson J, Sandström R. Applications of Aluminium Matrix Composites. Key Engineering Materials. 1995; 104–107: 3-36p.
- [4] Ashkenazi D. How aluminum changed the world: A metallurgical revolution through technological and cultural perspectives. Technological Forecasting and Social Change. 2019; 143: 101–113р.
- [5] Richards J W. Aluminium: its history, occurrence, properties, metallurgy and applications, including its alloys. Walnut Street, U S A: HC Baird & Company; 1890.
- [6] Sukiman N L, Zhou X, Birbilis N, et al. Durability and corrosion of aluminium and its alloys: overview, property space, techniques and developments. In: Zaki Ahmad, editor. Aluminium Alloys-New Trends in Fabrication and Applications. London: Intech Open Limited; 2012; 5: 47–97p.
- [7] Alok Singh Chauhan, Boddapati Anirudh, Satyanarayana A, et al. FEA optimization of injection parameters in ceramic core development for investment casting of a gas turbine blade. Materials Today: Proceedings. 2020; 26: 2190–2199p.
- [8] He Li, Yongsheng Liu, Yansong Liu, et al. Influence of debinding holding time on mechanical properties of 3D-printed alumina ceramic cores. Ceramics International. 2021; 47(4): 4884–4894p.
- [9] Bonollo F, Urban J, Bonatto B, et al. Gravity and low pressure die casting of aluminium alloys: a technical and economical benchmark. la metallurgia italiana. 2005; 6: 23–31р.
- [10] Prosenjit Das, Bikash Bhuniya, Sudip K. Samanta, et al. Studies on die filling of A356 Al alloy and development of a steering knuckle component using rheo pressure die casting system. Journal of Materials Processing Technology. 2019; 271: 293-311p.
- [11] Byoung Hee Choi, Young Soo Jang, Jae Gi Sim, et al. Application of rheo-diecasting of a high strength Al-Si-Mg alloy to automotive suspension arms. ISIJ international. 2013; 53(3): 502-510p.
- [12] Reddy A C, Rajanna C. Design of gravity die casting process parameters of Al-Si-Mg alloys. Journal of Machining and Forming Technologies. 2009; 1(1/2): 1–25p.
- [13] Malhotra V, Kumar Y. Study of process parameters of gravity die casting defects. Int. J. Mech. Eng. Technol. 2016; 7: 208-211p.
- [14] Teng X, Mae H, Bai Y, et al. Pore size and fracture ductility of aluminum low pressure die casting. Engineering Fracture Mechanics. 2009; 76(8): 983–996p.
- [15] Dou K, Lordan E, Zhang Y J, et al. A complete computer aided engineering (CAE) modelling and optimization of high pressure die casting (HPDC) process. Journal of Manufacturing Processes. 2020; 60: 435-446p.
- [16] Yang H, Ji S, Watson D, et al. Repeatability of tensile properties in high pressure die-castings of an Al-Mg-Si-Mn alloy. Metals and Materials International. 2015; 21(5): 936–943p.
- [17] Fu M W, Zheng J Y. Die Casting for Fabrication of Metallic Components and Structures. In: Encyclopedia of Materials-Metals and Alloys. Elsevier; 2021: 54–72p.
- [18] Chen Hu, Haidong Zhao, Xueling Wang, et al. Microstructure and properties of AlSi12Fe alloy high pressure die-castings under different vacuum levels. Vacuит. 2020; 180: 109561p.
- [19] Jadhav A R, Hujare D P, Hujare P P. Design and optimization of gating system, modification of cooling system position and flow simulation for cold chamber high pressure die casting machine. Materials Today: Proceedings. 2021; 46(17): 7175–7181p.
- [20] Patnaik L, Saravanan I, Kumar S. Die casting parameters and simulations for crankcase of automobile using MAGMAsoft. Materials Today: Proceedings. 2020; 22: 563-571p.
- [21] Chavan R and Kulkarni P. Die design and optimization of cooling channel position for cold chamber high pressure die casting machine. IOP Conference Series: Materials Science and Engineering. 2020; 810: 012017р.
- [22] Niu X P, Hu B H, Pinwill I, et al. Vacuum assisted high pressure die casting of aluminium alloys. Journal of Materials Processing Technology. 2000; 105(1-2): 119–127р.
- [23] Bonollo F, Gramegna N, Timelli G. High-pressure die-casting: contradictions and challenges. JOM. 2015; 67(5): 901–908p.
- [24] Kohlstädt S, Vynnycky M, Jäckel J. Towards the modelling of fluid-structure interactive lost core deformation in high-pressure die casting. Applied Mathematical Modelling. 2020; 80: 319–333p.
- [25] Kohlstädt S, Vynnycky M, Neubauer A, et al. Comparative RANS turbulence modelling of lost salt core viability in high pressure die casting. Progress in Computational Fluid Dynamics, an International Journal. 2019; 19(5): 316–327р.
- [26] Kohlstädt S, Vynnycky M, Goeke S, et al. On Determining the Critical Velocity in the Shot Sleeve of a High-Pressure Die Casting Machine Using Open Source CFD. Fluids. 2021; 6(11): 386p.
- [27] Li Zixin, Li Dejiang, Zhou Wenke, et al. Characterization on the formation of porosity and tensile properties prediction in die casting Mg alloys. Journal of Magnesium and Alloys. 2022; 10(7): 1857-1867p.
- [28] Ewan Lordan, Jaime Lazaro-Nebreda, Yijie Zhang, et al. On the relationship between internal porosity and the tensile ductility of aluminium alloy die-castings. Materials Science and Engineering: A. 2020; 778; 139107p.
- [29] Mahesh N Adke, Shrikant V Karanjkar. Optimization of die-casting process parameters to identify optimized level for cycle time using Taguchi method. International Journal of Innovations in Engineering and Technology. 2014; 4(4): 365–375p.
- [30] Singh R. Modeling of surface hardness in hot chamber die casting using Buckingham's π approach. Journal of Mechanical Science and Technology. 2014; 28(2): 699–704p.
- [31] Dańko J, Stojek J, Dańko R. Model testing of casting process in cold-chamber die casting machine. Archives of Metallurgy and Materials. 2007; 52(3): 503–513p.
- [32] Singh R, Singh H. Effect of Some Parameters on the Cast Component Properties in Hot Chamber Die Casting. Journal of The Institution of Engineers (India): Series C. 2016; 97(2): 131–139p.
- [33] Lee J, Lee Y C, Kim J T. Migration from the traditional to the smart factory in the die casting industry: Novel process data acquisition and fault detection based on artificial neural network. Journal of Materials Processing Technology. 2021; 290: 116972p.
- [34] Bataineh O, Al-Dwairi A. Application of statistical process control tools to improve product quality in manufacturing processes. Applied Mechanics and Materials. 2012; 110–116: 4023-4027р.
- [35] Bruckmeier L, Ringel A, Vroomen U. Influence of High-Pressure Die Casting Process Parameters on the Compound Strength of Hybrid Components with Undercut Sheet Metal. Metals. 2023; 13(10): 1717р.
- [36] Wan Mahmood W H, Mohd Rosdi M N H, Muhamad M R. A Conceptual Framework in Determining Manufacturing Complexity. Applied Mechanics and Materials. 2015; 761: 550–554p.
- [37] Outmani, I, Laurence Fouilland-Paille, Jérôme Isselin, et al. Effect of Si, Cu and processing parameters on Al-Si-Cu HPDC castings. Journal of Materials Processing Technology. 2017; 249: 559-569p.
- [38] Rathinam N, Dhinakaran R, Sharath E. Optimizing process parameters to reduce blowholes in high pressure die casting using Taguchi methodology. Materials Today: Proceedings. 2021; 38: 2871–2877р.
- [39] Mohd U, Pandulu G, Jayaseelan R. Strength evaluation of eco-friendly concrete using Taguchi method. Materials Today: Proceedings. 2020; 22: 937–947p.
- [40] Balikai V G, Siddlingeshwar I, Gorwar M. Optimization of process parameters of High Pressure Die Casting process for ADC12 Aluminium alloy using Taguchi method. International Journal of Pure and Applied Mathematics. 2018; 120(6): 959–969p.
- [41] Anilchandra R. Adamane, Lars Arnberg, Elena Fiorese, et al. Influence of injection parameters on the porosity and tensile properties of highpressure die cast Al-Si alloys: a review. International Journal of Metalcasting. 2015; 9(1): 43–53р.
- [42] Karthik A, Karunanithi R, Srinivasan S A, et al. The optimization of squeeze casting process parameter for AA2219 alloy by using the Taguchi method. Materials Today: Proceedings. 2020; 27: 2556-2561р.
9. 著作権:
- この資料は、「Rahul B., Bhaskar M. Reddy, Tamilselvam Nallusamy, W. Brightlin Abisha, Suresh P.」による「Injection Parameters Setting in High-Pressure Die Casting」論文に基づいています。
- 論文の出典: DOI (Journal): 10.37591/JoPC
この資料は、上記の論文を紹介するために作成されたものであり、商業目的での無断使用を禁じます。Copyright © 2025 CASTMAN. All rights reserved.