この論文概要は、['Solute micro-segregation profile and associated precipitation in cast Al-Mg-Si alloy']と題された論文に基づいており、['Philosophical Magazine']に掲載されました。
1. 概要:
- タイトル: 鋳造Al-Mg-Si合金における溶質ミクロ偏析プロファイルと関連する析出 (Solute micro-segregation profile and associated precipitation in cast Al-Mg-Si alloy)
- 著者: Artenis Bendo, Jonathan Fellowes, Matthew Smith, Masoud Moshtaghi, Zelong Jin, Kenji Matsuda, Zhongyun Fan & Xiaorong Zhou
- 発行年: 2024年
- 発行ジャーナル/学会: Philosophical Magazine
- キーワード: アルミニウム合金; 鋳造; 偏析; 金属間化合物; 析出; 透過型電子顕微鏡 (aluminium alloy; casting; segregation; intermetallic phases; precipitation; transmission electron microscopy)

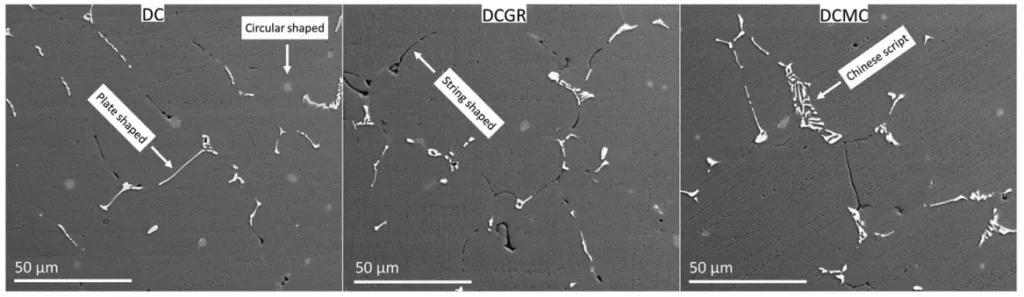
2. 研究背景:
研究トピックの背景:
溶質偏析は、アルミニウム合金の凝固過程において一般的な現象です。これは主に、高速冷却速度によって引き起こされる非平衡条件によるものであり[1]、多くの鋳造プロセスに特徴的です。凝固中の固液界面の進行は、溶融物中の溶質の継続的な蓄積を引き起こします[2]。各元素の分配係数は、このプロセス中に固体相または液体相のどちらに優先的に濃縮されるかを決定します。
既存研究の現状:
鋳造Al-Mg-Si合金におけるマクロ偏析に関する以前の研究では、ビレットの中心部におけるMgおよびSiの枯渇と、表面付近での濃縮が示唆されており[5]、これは中心線負偏析として知られる現象です。さらに、研究によると、Al-Mg-Si合金のミクロ偏析領域内には、Feリッチ金属間化合物に加えて、準安定相β'および安定相βが存在することが示唆されています[6–8,10,11]。しかし、既存の文献では、これらのミクロ偏析バンド内の詳細な濃度勾配および原子スケール構造に関する研究が不足しています。
研究の必要性:
Al-Mg-Si合金は、自動車部品の製造においてますます重要になっており[12]、AA6082アルミニウム合金は、従来のダウンストリーム熱機械処理[13]を受けると、優れた機械的性能を発揮します。産業界の動向は、ダウンストリーム熱機械プロセスに関連する製造コストを削減するために、部品を鋳造状態のまま使用する方向にシフトしています。鍛造Al-Mg-Si合金における強化相の析出は、MgおよびSi溶質元素に大きく依存しており、これらの濃度はミクロ偏析プロファイルによって大きく影響を受けます。したがって、これらの偏析バンドの構造に関する包括的な理解が最も重要です。
3. 研究目的と研究課題:
研究目的:
本研究は、鋳造AA6082アルミニウム合金におけるミクロ偏析の本質を解明するために、主要なミクロ偏析とマイナーなミクロ偏析を区別することを目的としています。主な焦点は、マイナーミクロ偏析バンドの微細構造を特性評価し、特にその分布パターン、濃度勾配、およびナノ構造を調査することです。さらに、本研究は、マイナーミクロ偏析バンドと主要なミクロ偏析フィーチャ間の関係を明らかにしようとしています。
主な研究課題:
- マイナーミクロ偏析バンド内の微細構造の詳細な特性評価。
- これらのバンド内の溶質元素の分布パターンと濃度勾配の分析。
- マイナーミクロ偏析バンドに存在するナノ構造の調査。
- マイナーミクロ偏析バンドと主要なミクロ偏析フィーチャ間の関係の解明。
研究仮説:
正式な仮説として明示されていませんが、本研究は、鋳造AA6082におけるミクロ偏析は、主要なタイプとマイナーなタイプに効果的に分類でき、各タイプは明確な特性と形成メカニズムを持つという前提で進められています。中心的な原則は、マイナーミクロ偏析バンドの詳細な理解が、強化相の析出を制御および最適化するために重要であり、それによって最終的な材料特性に影響を与えるということです。
4. 研究方法
研究デザイン:
本研究では、実験的研究デザインを採用し、従来の直接冷却鋳造(DC)、造粒微細化剤添加直接冷却鋳造(DCGR)、および溶融状態調整直接冷却鋳造(DCMC)の3つの異なる鋳造プロセスによって製造された鋳造AA6082アルミニウム合金サンプルを利用しました。この比較アプローチにより、さまざまな凝固条件下でのミクロ偏析パターンを調査することができました。
データ収集方法:
多面的なデータ収集アプローチが採用され、高度な分析技術のスイートが使用されました。
- 走査型電子顕微鏡(SEM): 後方散乱電子イメージング(BSE)およびエネルギー分散型X線分光法(EDS)は、FEI Quanta 250 FEG、FEI Quanta 650 FEG、およびTescan Mirai3LC FEG SEMを使用して実施されました。
- 電子プローブマイクロアナリシス(EPMA): 定量的な元素マッピングは、FEG、SXES、およびEDS検出器を備えたJEOL JXA-8530Fを使用して実行されました。
- 透過型電子顕微鏡(TEM)および走査透過型電子顕微鏡(STEM): 詳細な微細構造および原子スケール特性評価は、FEI Tecnai TF30 FEG TEM、FEI Talos F200 X-Field Emission Gun(X-FEG)STEM、およびFEI Titan G2 80-200収差補正STEMを使用して達成されました。
- スパーク発光分光法(SES): 全体的な化学組成は、Thermo Scientific ARL iSpark光学スパーク発光分光計を使用して決定されました。
分析方法:
収集されたデータは、厳密な分析を受けました。
- 顕微鏡画像分析: ミクロ偏析形態および析出物分布を特性評価するためのSEM、TEM、およびSTEM画像の定性的および定量的分析。
- 元素マッピングおよびラインスキャン: EPMAおよびEDSデータを使用して、元素マップおよび濃度プロファイルを作成し、ミクロ偏析バンド内の溶質偏析を定量化しました。
- 電子回折: TEMで得られた選択領域電子回折(SAED)パターンを相識別に使用しました。
- 原子スケール分解能イメージング: HAADF-STEMイメージングおよび高速フーリエ変換(FFT)を使用して、析出物の原子構造を分析しました。
- 熱力学計算: Scheil凝固計算を実行して、凝固中の相形成シーケンスを予測しました。
研究対象と範囲:
研究は、鋳造AA6082アルミニウム合金サンプルに焦点を当てました。サンプルは、DC、DCGR、およびDCMC鋳造法によって製造されたビレットから準備されました。研究の範囲は、これらの鋳造状態材料内のミクロおよびナノスケールでのミクロ偏析現象の調査に限定され、特にミクロ偏析バンドおよび関連する析出物の特性評価に焦点を当てました。
5. 主な研究結果:
主な研究結果:
調査の結果、鋳造AA6082アルミニウム合金におけるミクロ偏析は、結晶粒界およびデンドライト間チャネルに沿って相互接続されたネットワークを形成することが明らかになりました。ミクロ偏析は、2つの異なるタイプに分類されました。
- 主要なミクロ偏析: 主に結晶粒界に位置し、鉄含有金属間化合物が存在することが特徴です。
- マイナーミクロ偏析: 結晶粒界とデンドライト間チャネルの両方に沿って観察され、主にMgおよびSi合金元素で構成されています。
原子スケールイメージングにより、マイナー偏析バンドは析出物形成部位であることが明らかになりました。これらの析出物は、2つのメカニズムを介して核生成します。
- 不均一核生成: 転位ネットワークで発生します。これらの析出物は、析出シーケンス全体を通して形成された相の混合物で構成されています。
- 均一核生成: アルミニウムマトリックス内で発生します。これらの析出物は、析出シーケンスの初期段階に現れる個別の相です。
データ解釈:
主要偏析 vs マイナー偏析: SEM分析(図1)の結果、板状、漢字状、ストリング状、円形の形状など、主要偏析に関連する粗い特徴が明らかになりました。元素マッピング(図2)は、これらの主要な偏析フィーチャがSi、Fe、およびMnに富んでいることを示しました。対照的に、EPMA(図3)によって明らかにされたマイナー偏析バンドは、幅が約5〜15 µmとより細かく、MgとSiが豊富です。
マイナー偏析バンドにおける析出: EPMAマップ(図3)およびTEM/STEM分析(図4〜8)は、マイナー偏析バンドが析出の優先部位として機能することを示しました。転位線上の不均一核生成は、混合相を持つより粗い析出物の形成を誘導します(図6および7)。Alマトリックス内の均一核生成は、より微細で個別の析出物を生成し、主にβ"およびType-B/U2相の前駆体です(図8)。
偏析ネットワーク: マイナー偏析バンドの相互接続された性質は、EPMAマップ(図9)によって強調されており、これらのバンドは結晶粒界とデンドライト間チャネルに沿ってネットワークを形成し、SiとMgの高濃度領域を接続していることを示しています。
図リスト:
- 図 1. 鋳造DC、DCGR、DCMC条件下でのAA6082 Al合金の微細構造の後方散乱電子SEM像。板状、漢字状、ストリング状、円形の形状の特徴の析出が起こっています。
- 図 2. 3つの鋳造条件の後方散乱電子像と対応する元素マップ。ラベルは、示された相の主な元素組成を示しています。
- 図 3. 3つの異なる鋳造条件におけるSiおよびMg偏析の定性的な電子プローブマイクロアナリシス(EPMA)マップ。EPMAマップは、マイナー偏析バンドを明らかにするために意図的に強調されています。ラインスキャンは白い点線で示されています。濃度(at.%)対距離(µm)プロットは、EPMAマップの対応するラインスキャンに対応しています。
- 図 4. DCGR鋳造におけるミクロ偏析バンドで観察された形態。六角形のアルファ相鉄リッチ粒子のTEM像、対応する電子回折、元素マップ、および立方晶アルファ相鉄リッチ相の(111)ゾーン軸に沿ったノイズフィルタリングされた原子スケールHAADF-STEM像。
- 図 5. (A0) DCGR鋳造における粗いデンドライト状フィーチャの隣の[001]アルミニウムゾーン軸に沿った微細構造のHAADF-STEM像。(A1) A0画像で白い点線でマークされた拡大領域。(A2) A1画像で白い点線でマークされた領域と対応する元素マップ。
- 図 6. DCGR鋳造におけるミクロ偏析バンド内の粗い金属間化合物の隣の[001]アルミニウムゾーン軸に沿ったTEMおよびSTEMイメージング。(A0) 粗い金属間化合物の隣の微細構造のTEM像。(A1) A0画像で黒い点線でマークされた領域の拡大TEM像。(A2) A1画像の上部で黒い点線でマークされた領域のHAADF-STEM像。(1 & 2) HAADF-STEMモードを使用して全体的にイメージングされた析出物1と2。白い点線でマークされた析出物1と2の断面のフィルタリングされていない原子スケール画像。緑色のSiリッチ原子カラムと青色のCuリッチ原子カラムのオーバーレイ、および対応するFFT。FFTでは、白い円はAlマトリックスを示し、白い点線の円はSiネットワーク反射を示しています。
- 図 7. (a, b) [001]アルミニウムゾーン軸に沿ったフィルタリングされていない原子スケールHAADF-STEM像で、不均一核生成された析出物の断面を示しています。(I, II, III, IV) さまざまな析出物断面領域と対応する準安定相から拡大された部分。入射ビーム(z座標)と平行な原子カラムの原子座標は無視されます。
- 図 8. DCGR鋳造におけるミクロ偏析バンド内の微細構造のTEMおよびSTEM像。(A0) 図6 (A1)と同じ領域のTEM像。(A1) A0画像で黒い点線でマークされた領域の拡大HAADF-STEM像。均一な析出が起こっています。(a, b) Alマトリックス内で均一核生成された析出物とその対応するFFTのフィルタリングされていない原子スケールHAADF-STEM像。
- 図 9. DCGR鋳造における偏析パターンのEPMAマップ。(a) Si偏析マップとその概略図。(b) Mg偏析マップとその概略図。(c) Mn偏析マップとその概略図。Mn偏析マップはFe偏析マップと同等です。付録を確認してください。(d) マイナー偏析バンドの微細構造の図。(e) アルミニウムデンドライト境界にぶつかる前の2つのアルミニウムデンドライト。
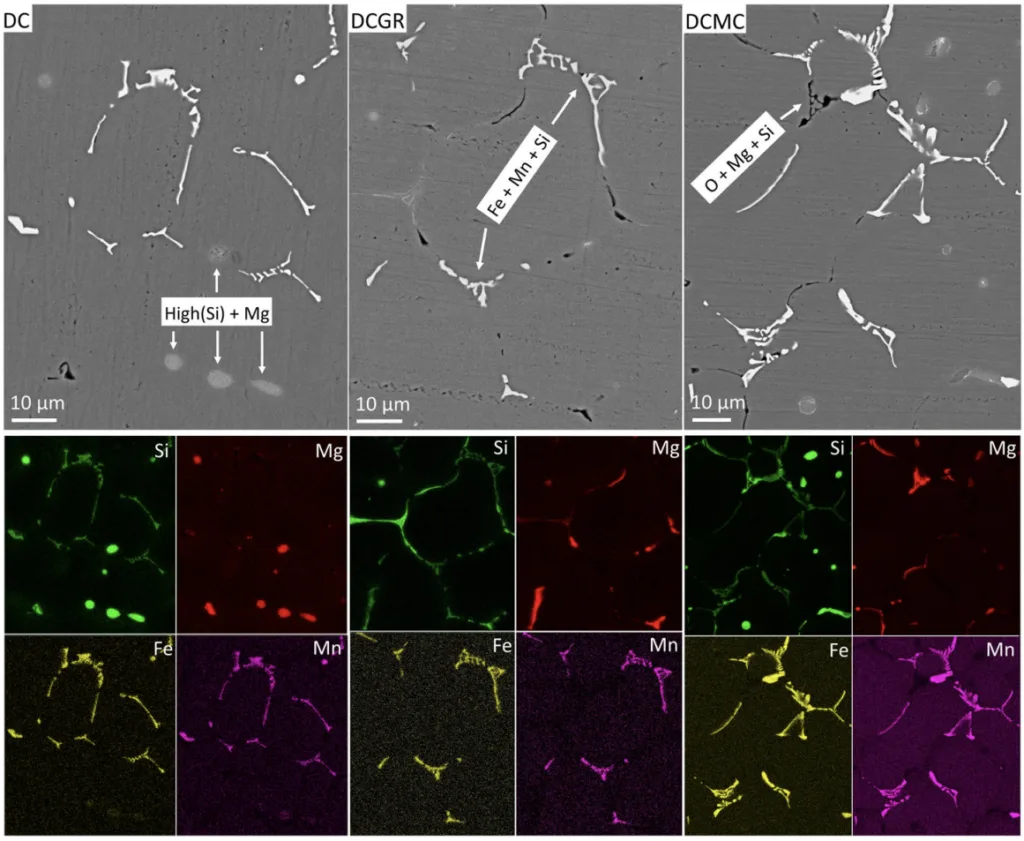
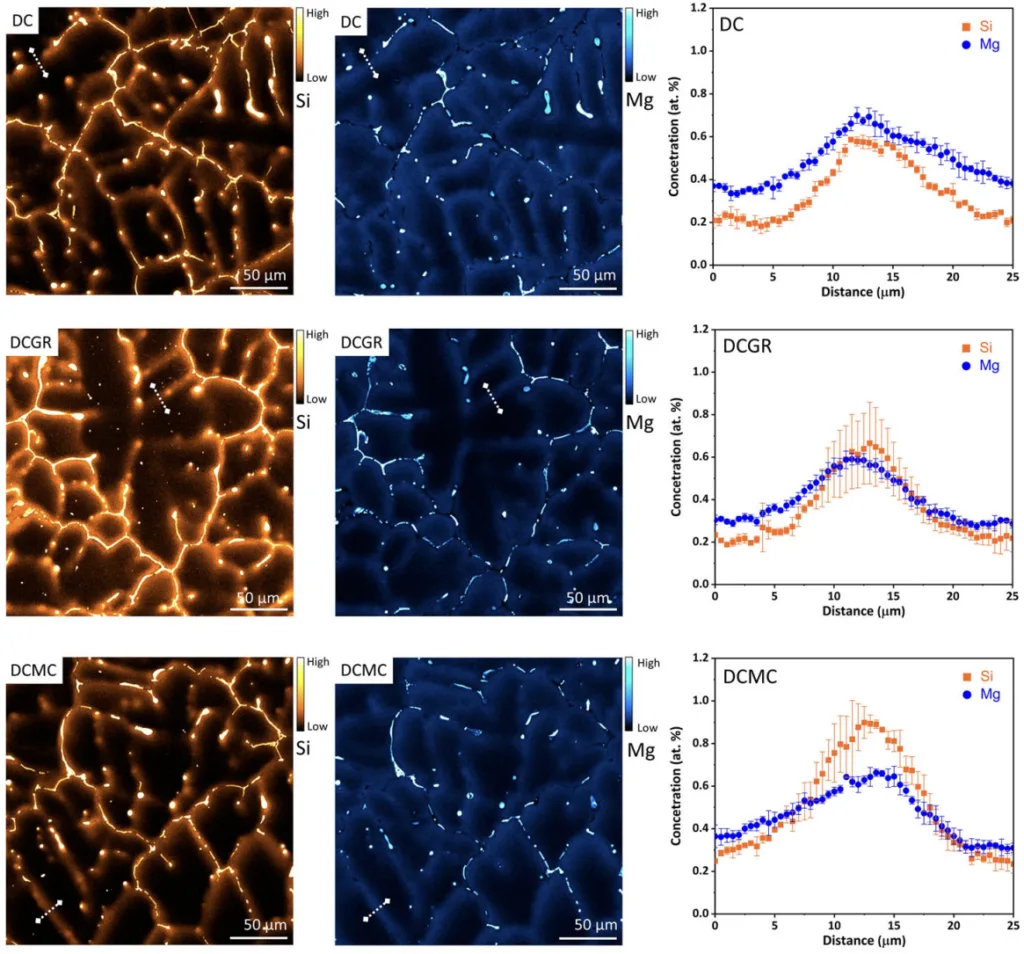
6. Conclusion:
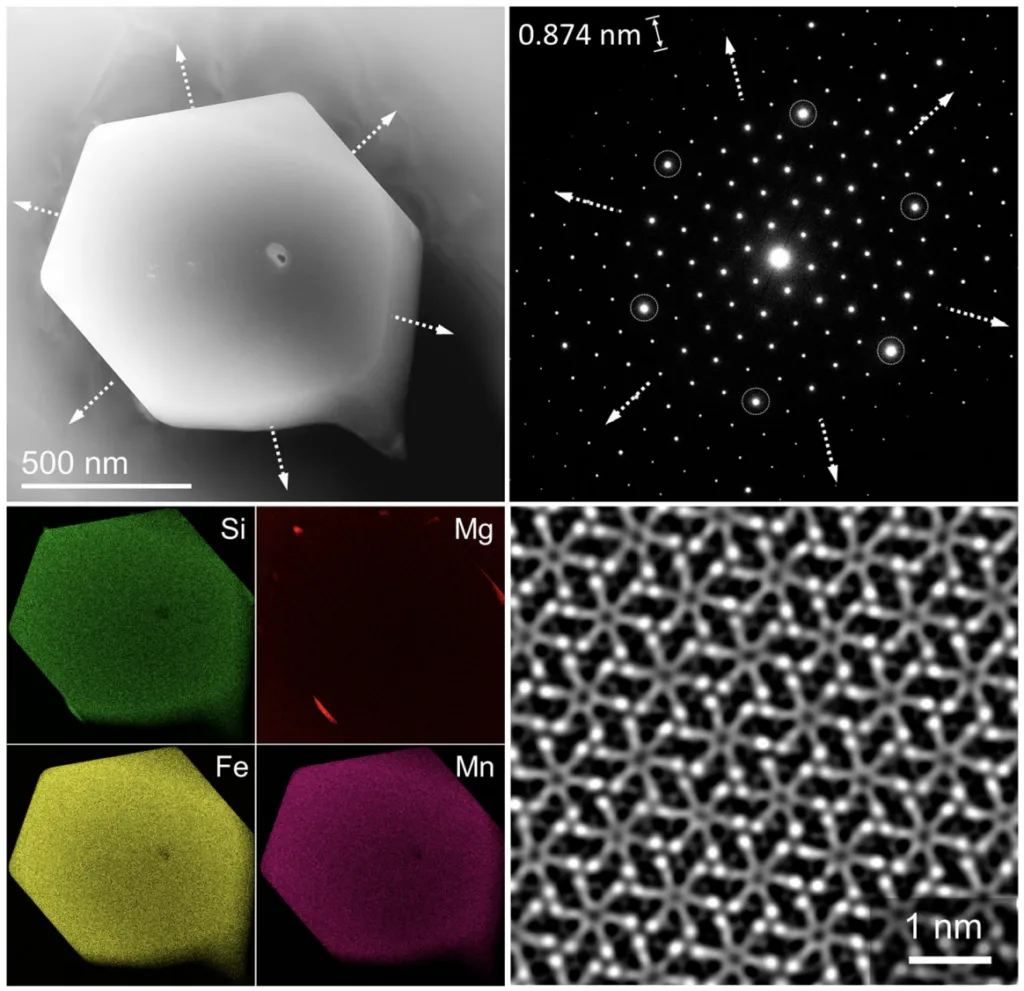
![Figure 5. (A0) The HAADF-STEM image of the microstructure along the [001] aluminium zone axis, next to a coarse dendritic feature in the DCGR cast. (A1) The enlarged area marked with dashed white lines in the AO image. (A2) The area marked with white dashed lines in the A1 image and the corresponding elemental maps.](https://castman.co.kr/wp-content/uploads/image-563-1024x719.webp)
![Figure 7. (a, b) The unfiltered atomic-scale HAADF-STEM images along the [001] aluminium zone axis, revealing the precipitate cross-sections of the heterogeneously nucleated precipitates. (I, II, III, IV) The enlarged parts from the different precipitate cross-section areas and the respective metastable phases. The atomic coordinates of the atomic columns parallel with the incident beam (z-coordinates) are neglected.](https://castman.co.kr/wp-content/uploads/image-564-1024x991.webp)
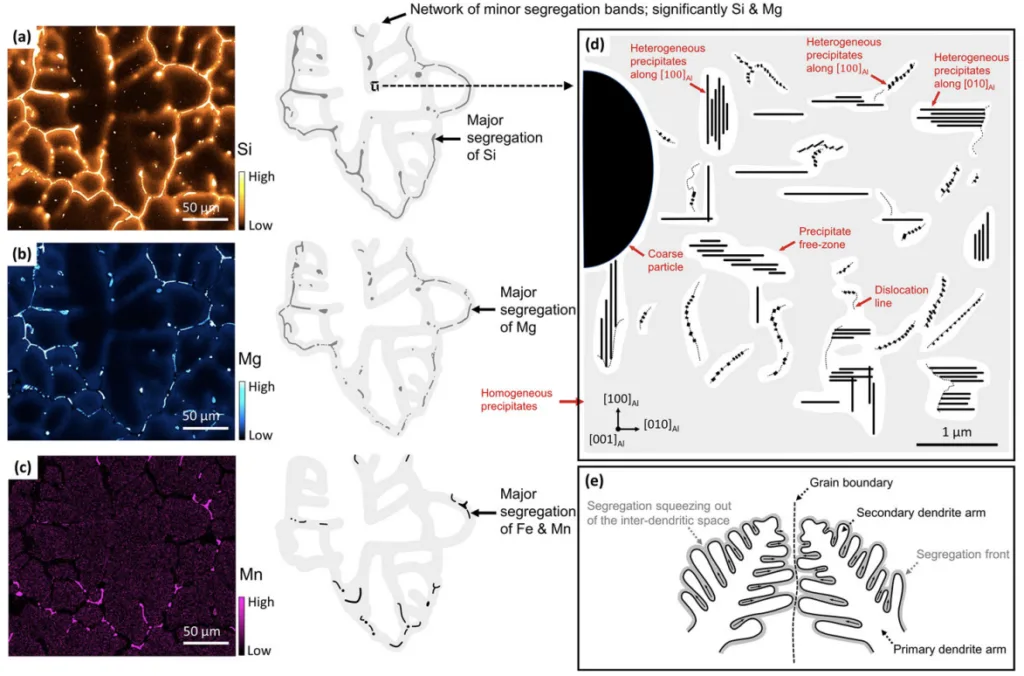
6. 結論:
主な結果の要約:
本研究は、造粒微細化剤および溶融状態調整の有無にかかわらず、直接冷却鋳造によって製造された鋳造AA6082アルミニウム合金のミクロ偏析パターンに関する包括的な調査を提供します。本研究では、主要なミクロ偏析バンドとマイナーなミクロ偏析バンドを区別することに成功しました。Fe、Mn、およびSiに富む主要なバンドは主に結晶粒界に位置する一方、SiおよびMgに富むマイナーなバンドは、デンドライト間チャネルおよび結晶粒界に沿っています。アルファ-Al15(FeMn)3Si2金属間化合物相は、主要な偏析バンドの主な構成要素として特定されました。一般的な幅が5〜15 µmで、Mg/Si濃度が0.6〜0.8 at.%でピークに達するマイナー偏析バンドは、析出の優先部位として機能します。鋳造状態の微細構造内の転位ネットワークは不規則で不均一に分布しており、不均一析出に影響を与えます。転位上の不均一析出とアルミニウムマトリックス内の均一析出の両方が、マイナー偏析バンド内で観察されました。
研究の学術的意義:
本研究は、鋳造アルミニウム合金におけるミクロ偏析の基礎的な理解に大きく貢献します。マクロな偏析パターンから原子スケールの析出物構造まで、詳細な多重スケール特性評価を提供します。主要なミクロ偏析とマイナーなミクロ偏析の区別と、それらの明確な特性と形成メカニズムの解明は、Al-Mg-Si合金の凝固現象に関する貴重な洞察を提供します。
実用的な意味合い:
本研究の知見は、アルミニウム鋳造業界に直接的な実用的な意味合いを持ちます。ミクロ偏析バンドおよび関連する析出物の形成と特性を理解することは、鋳造プロセスと後続の熱処理を最適化するために非常に重要です。ミクロ偏析を制御することにより、強化相の析出を調整することが可能になり、最終的には、特に自動車分野やそれ以降の要求の厳しい用途向けのAl-Mg-Si合金部品の機械的特性を向上させることができます。
研究の限界:
本研究では、ミクロ偏析パターンの固有の変動性と、使用された比較的小さなサンプリングボリュームから生じる限界を認識しています。これらの要因により、3つの鋳造方法間のミクロ偏析特性への影響に関して、統計的に有意な差を区別することができませんでした。より大きなサンプルサイズとより広範な統計分析による今後の研究が、この限界を克服するために必要となる可能性があります。
7. 今後のフォローアップ研究:
- フォローアップ研究の方向性:
- 観察された不規則な転位ネットワークの形成メカニズムと、不均一析出を促進する正確な役割に関するさらなる調査。
- 相進化に関するより詳細な理解を確立するために、主要な偏析バンドとマイナーな偏析バンド内に存在するさまざまな析出相の定量的分析。
- 冷却速度や溶融温度などの特定の鋳造パラメータが、結果として得られるミクロ偏析パターンと析出物特性に及ぼす影響の探求。
- さらなる探求が必要な領域:
- 凝固の最終段階で、溶質が豊富な溶融物が結晶粒界およびデンドライト間チャネルに押し出される正確なメカニズム。
- 主要な偏析バンドとマイナーな偏析バンド間の相互作用と、全体的な微細構造および材料特性に対するそれらの複合効果。
- さまざまな鋳造条件下でのAl-Mg-Si合金におけるミクロ偏析形成および析出物進化をシミュレーションするための予測モデルの開発。
8. 参考文献:
- [1] D.G. Eskin, R. Nadella, and L. Katgerman, Effect of different grain structures on center-line macrosegregation during direct-chill casting. Acta Mater. 56 (2008), pp. 1358–1365. doi:10.1016/j.actamat.2007.11.021.
- [2] Z. Yao, Y. Huo, M. Li, and J. Allison, A quantitative study of microsegregation in aluminum-copper alloys. Metall. Mater. Trans. A 53 (2022), pp. 2383–2401. doi:10.1007/s11661-022-06669-3.
- [3] R. Nadella, D.G. Eskin, Q. Du, and L. Katgerman, Macrosegregation in direct-chill casting of aluminium alloys. Prog. Mater. Sci. 53 (2008), pp. 421–480. doi:10.1016/j.pmatsci.2007.10.001.
- [4] X. Doré, H. Combeau, and M. Rappaz, Modelling of microsegregation in ternary alloys: applications to the solidification of Al-Mg-Si. Acta Mater. 48 (2000), pp. 3951–3962. doi:10.1016/S1359-6454(00)00177-4.
- [5] Q. Dong, X. Chen, J. Xia, X. Li, B. Zhang, and H. Nagaumi, Floating grain characterization and its effects on centerline segregation of direct-chill cast Al-Mg-Si alloy billets. Mater. Trans. 61(12) (2020), pp. 2386–2392. doi:10.2320/matertrans.MT-M2020229.
- [6] L. Lodgaard and N. Ryum, Precipitation of dispersoids containing Mn and/or Cr in Al–Mg-Si alloys. Mater. Sci. Eng. 283 (2000), pp. 144–152. doi:10.1016/S0921-5093(00)00734-6.
- [7] R. Hu, T. Ogura, H. Tezuka, T. Sato, and Q. Liu, Dispersoid formation and recrystallization behavior in an Al-Mg-Si-Mn alloy. J. Mater. Sci. Technol. 26(3) (2010), pp. 237–243. doi:10.1016/S1005-0302(10)60040-0.
- [8] M. Kenyon, J. Robson, J. Fellowes, and Z. Liang, Effect of dispersoids on the microstructure evolution in Al-Mg-Si alloys. Adv. Eng. Mater. 21 (2019), pp. 1800494. doi:10.1002/adem.201800494.
- [9] T. Dorin, M. Ramajayam, S. Babaniaris, and T.J. Langan, Micro-segregation and precipitates in as-solidified Al-Sc-Zr-(Mg)-(Si)-(Cu) alloys. Mater. Charact. 154 (2019), pp. 353-362. doi:10.1016/j.matchar.2019.06.021.
- [10] Y.S. Park, S.B. Lee, and N.J. Kim, Microstructure and mechanical properties of strip cast Al-Mg-Si-X alloys. Mater. Trans. 44(12) (2003), pp. 2617-2624. doi:10.2320/matertrans.44.2617.
- [11] M. Ganesan, L. Thuinet, D. Dye, and P.D. Lee, Quantification of microsegregation in cast Al-Si-Cu alloys. Metall. Mater. Trans. 38 (2007), pp. 557–566. doi:10.1007/s11663-007-9071-0.
- [12] G. Scamans, Electric vehicle spike demand for high strength aluminum extrusions. Light Met. Age 76 (2018), pp. 6-12.
- [13] C.D. Marioara, S.J. Andersen, J. Jansen, and H.W. Zandbergen, The influence of temperature and storage time at RT on nucleation of the β" phase in a 6082 Al-Mg-Si alloy. Acta Mater. 51 (2003), pp. 789–796. doi:10.1016/S1359-6454(02)00470-6.
- [14] A. Cibula, The grain refinement of aluminium alloy castings by additions of titatnium and boron. J. Inst. Met. 80 (1951), pp. 1–16.
- [15] Z. Fan, Y. Wang, Y. Zhang, T. Qin, X.R. Zhou, G.E. Thompson, T. Pennycook, and T. Hashimoto, Grain refining mechanism in the Al/Al-Ti-B system. Acta Mater. 84 (2015), pp. 292-304. doi:10.1016/j.actamat.2014.10.055.
- [16] Z. Fan, An epitaxial model for heterogenous nucleation on potent substrates. Metall. Mater. Trans. A 44 (2013), pp. 1409–1418. doi:10.1007/s11661-012-1495-8.
- [17] Z. Fan, B. Jiang, and Y. Zuo. Apparatus and method for liquid metals treatment. WO/2012/035357 and 2013 US 20130228045 A1.
- [18] G. Scamans, H.T. Li, J.L. Nebreda, J. Patel, I. Stone, Y. Wang, X. Yang, and Z. Fan, Advanced casting technologies using high shear melt conditioning. Fundam. Alum. Metall., Chapter 8 (2018), pp. 249–277. doi:10.1016/B978-0-08-102063-0.00008-4.
- [19] J.B. Patel, H.T. Li, X. Mingxu, and S. Jones, Melt conditioned direct chill casting (MC-DC) process for production of high-quality aluminum alloy billets. Mater. Sci. Forum 794-796 (2014), pp. 149–154. doi:10.4028/www.scientific.net/MSF.794-796.149.
- [20] K.M.S. Manu, N.S. Barekar, J.L. Nebreda, J.B. Patel, and Z. Fan, In-situ microstructural control of A6082 alloy to modify second phase particles by melt conditioned direct chill
- [21] G. Scamans, H.T. Li, and Z. Fan, Melt conditioned casting of aluminum alloys, 13th International Conference on Aluminum Alloys (ICAA13), 2012. doi:10.1007/978-3-319-48761-8_213.
- [22] S. Kumar and K.A.Q. O'Reilly, Influence of Al grain structure on Fe bearing intermetallics during DC casting of an Al-Mg-Si alloy. Mater. Charact. 120 (2016), pp. 311–322. doi:10.1016/j.matchar.2016.09.017.
- [23] S. Kumar, P.S. Grant, and K.A.Q. O'Reilly, Evolution of Fe bearing intermetallics during DC casting and homogenization of an Al-Mg-Si Al alloy. Metall. Mater. Trans. A 47 (2016), pp. 3000–3014. doi:10.1007/s11661-016-3451-5.
- [24] S. Kumar, P.S. Grant, and K.A.Q. O'Reilly, Fe bearing intermetallic phase formation in a wrought Al-Mg-Si alloy. Trans. Indian Inst. Met. 65(6) (2012), pp. 553–557. doi:10.1007/s12666-012-0221-y.
- [25] A. Verma, S. Kumar, P.S. Grant, and K.A.Q. O'Reilly, Influence of cooling rate on the Fe intermetallic formation in an AA6063 Al alloy. J. Alloys Compd. 555 (2013), pp. 274–282. doi:10.1016/j.jallcom.2012.12.077.
- [26] T. Hashimoto, G.E. Thompson, M. Curioni, X. Zhou, and P. Skeldon, Three-dimensional imaging of light metals using serial block face scanning electron microscopy (SBFSEM). Mat. Sci. Forum 765 (2013), pp. 501–505. doi:10.4028/www.scientific.net/MSF.765.501.
- [27] J.M. Yu, T. Hashimoto, H.T. Li, N. Wanderka, Z. Zhang, C. Cai, X.L. Zhong, J. Qin, Q.P. Dong, H. Nagaumi, and X.N. Wang, Formation of intermetallic phases in unrefined and refined AA6082 Al alloys investigated by using SEM-based ultramicrotomy tomography. J. Mater. Sci. Technol. 120 (2022), pp. 118–128. doi:10.1016/j.jmst.2022.02.007.
- [28] C.M. Dinnis, J.A. Taylor, and A.K. Dahle, As-cast morphology of iron-intermetallics in Al-Si foundry alloys. Scr. Mater. 53 (2005), pp. 955–958. doi:10.1016/j.scriptamat.2005.06.028.
- [29] Z. Que and C.L. Mendis, Heterogenous nucleation and phase transformation of Fe-rich intermetallic compounds in Al-Mg-Si alloys. J. Alloys Compd. 836 (2020), pp. 155515. doi:10.1016/j.jallcom.2020.155515.
- [30] Z. Que, Y. Wang, and Z. Fan, Formation of the Fe-containing intermetallic compounds during solidification of Al-5Mg-2Si-0.7Mn-1.1Fe alloy. Metall. Mater. Trans. A 49 (2018), pp. 2173–2181. doi:10.1007/s11661-018-4591-6.
- [31] Y.L. Liu and S.B. Kang, The solidification process of Al-Mg-Si alloys. J. Mater. Sci. 32 (1997), pp. 1443–1447. doi:10.1023/A:1018545732009.
- [32] Y.L. Liu, S.B. Kang, and H.W. Kim, The complex microstructures in an as-cast Al-Mg-Si alloy. Mater. Lett. 41 (1999), pp. 267–272. doi:10.1016/S0167-577X(99)00141-X.
- [33] Z. Fan, M. Xia, H. Zhang, G. Liu, J.B. Patel, Z. Bian, I. Bayandorian, Y. Wang, H.T. Li, and G.M. Scamans, Melt conditioning by advanced shear technology (MCAST) for refining solidification microstructure. Int. J. Cast Met. Res. 22(1-4) (2009), pp. 103–107. doi:10.1179/136404609X367443.
- [34] Z. Fan, Y. Wang, Z.F. Zhang, M. Xia, H.T. Li, J. Xu, L. Granas, and G.M. Scamans, Shear enhanced heterogenous nucleation in some Mg-and Al-alloys. Int. J. Cast Met. Res. 22(1-4) (2009), pp. 318–322. doi:10.1179/136404609X367452.
- [35] D. Luo, I. Chang, J.B. Patel, K. Al-Helal, Y. Huang, G.M. Scamans, and Z. Fan, Microstructure and mechanical properties of recycled AA6111 alloy processed by melt conditioned direct chill (MC-DC) casting. M&Ns-19 (17-19 July 2019), pp. 81–85.
- [36] S.H. Oh, Y. Kauffmann, C. Scheu, W.D. Kaplan, and M. Rühle, Ordered liquid aluminum at the interface with sapphire. Science 310(5748) (2005), pp. 661-663. doi:10.1126/science.1118611.
- [37] H.T. Li, Y. Wang, and Z. Fan, Enhanced heterogeneous nucleation on oxides in Al alloys by intensive shearing. IOP Conf. Ser.: Mater. Sci. Eng. 27 (2012), pp. 012047. doi:10.1088/1757-899X/27/1/012047.
- [38] J.L. Nebreda, J.B. Patel, I. Stone, and G.M. Scamans, De-ironing of aluminium alloy scrap by high shear melt conditioning technology, Proceedings of the 6th Decennial International Conference on Solidification Processing, Old Windsor, July 2017. doi:10.3390/met12101579.
- [39] Z.P. Que, Y.P. Zhou, Y. Wang, and Z. Fan, Effect of MgO on phase selection in Al-Mg-Si-Fe-Mn alloys. Trans. Indian Inst. Met. 68(6) (2015), pp. 1167–1172. doi:10.1007/s12666-015-0664-z.
- [40] H.T. Li, S. Ji, Y. Wang, M. Xia, and Z. Fan, Effect of intensive melt shearing on the formation of Fe-containing intermetallics in LM24 Al-alloy. IOP Conf. Ser.: Mater. Sci. Eng. 27 (2012), pp. 012075. doi:10.1088/1757-899X/27/1/012075.
- [41] H.T. Li, M. Xia, P. Jarry, G.M. Scamans, and Z. Fan, Grain refinement in a AlZnMgCuTi alloy by intensive melt shearing: A multi-step nucleation mechanism. J. Cryst. Growth 314 (2011), pp. 285–292. doi:10.1016/j.jcrysgro.2010.10.168.
- [42] M. Cooper, The crystal structure of the ternary alloy a(AlFeSi). Acta Cryst. 23 (1967), pp. 1106-1107. doi:10.1107/S0365110X67004372.
- [43] K. Matsuda, T. Kawabata, Y. Uetani, T. Sato, and S. Ikeno, Hexagonal tabular β-phase in Al-Mg-Si-Cu alloy. Scr. Mater. 47 (2002), pp. 467-471. doi:10.1016/S1359-6462(02)00173-2.
- [44] C. Li, Y.Y. Wu, H. Li, and X.F. Liu, Morphological evolution and growth mechanism of primary Mg2Si phase in Al-Mg2Si alloys. Acta Mater. 59 (2011), pp. 1058–1067. doi:10.1016/j.actamat.2010.10.036.
- [45] E. Cinkilic, M. Moodispaw, J. Zhang, J. Miao, and A.A. Luo, A new recycled Al-Si-Mg alloy for sustainable structural die casting applications. Metall. Mater. Trans. A 53 (2022), pp. 2861–2873. doi:10.1007/s11661-022-06711-4.
- [46] C.J. Simensen, P. Fartum, and A. Andersen, Analysis of intermetallic particles in aluminium by dissolution of the sample in butanol. Fresenius Z. Anal. Chem. 319 (1984), pp. 286-292. doi:10.1007/BF00487273.
- [47] J. Gjønnes, V. Hansen, S.J. Andersen, C.D. Marioara, and X.Z. Li, Electron crystallography of aluminum alloy phases. Z. Kristallogr. 218 (2003), pp. 293–307. doi:10.1524/zkri.218.4.293.20745.
- [48] N.C.W. Kuijpers, F.J. Vermolen, C. Vuik, P.T.G. Koenis, K.E. Nilsen, and S. van der Zwaag, The dependence of the β-AlFeSi to a-Al(FeMn)Si transformation kinetics in Al-Mg-Si alloys on the alloying elements. Mat. Sci. Eng. A 394 (2005), pp. 9–19. doi:10.1016/j.msea.2004.09.073.
- [49] K. Al-Helal, J.L. Nebreda, J.B. Patel, and G.M. Scamans, High-shear de-gassing and de-ironing of an aluminum casting alloy made directly from aluminum end-of-life vehicle scrap. Recycling 6 (2021), pp. 66. doi:10.3390/recycling6040066.
- [50] N.C.W. Kuijpers, W.H. Kool, P.T.G. Koenis, K.E. Nilsen, I. Todd, and S. van der Zwaag, Assessment of different techniques for quantification of a-Al(FeMn)Si and β-AlFeSi intermetallics in AA6xxx alloys. Mater. Charact. 49 (2002), pp. 409–420. doi:10.1016/S1044-5803(03)00036-6.
- [51] N.C.W. Kuijpers, F.J. Vermolen, K. Vuik, and S. van der Zwaag, A model of the β-AlFeSi to a-Al(FeMn)Si transformation in Al-Mg-Si alloys. Mater. Trans. 44(7) (2003), pp. 1448–1456. doi:10.2320/matertrans.44.1448.
- [52] H. Tanihata, T. Sugawara, K. Matsuda, and S. Ikeno, Effect of casting and homogenizing treatment conditions on the formation of Al-Fe-Si intermetallic compounds in 6063 Al-Mg-Si alloys. J. Mater. Sci. 34 (1999), pp. 1205–1210. doi:10.1023/A:1004504805781.
- [53] D.T.L. Alexander and A.L. Greer, Solid-state intermetallic phase tranformations in 3XXX aluminium alloys. Acta Mater. 50 (2002), pp. 2571–2583. doi:10.1016/S1359-6454(02)00085-X.
- [54] V.S. Zolotorevsky, N.A. Belov, and M.V. Glazoff, Casting Aluminum Alloys, Chapter 2, Elsevier Science Ltd., Amsterdam, 2007.
- [55] S.J. Andersen, C.D. Marioara, J. Friis, R. Bjørge, Q. Du, I.G. Ringdalen, S. Wenner, E.A. Mørtsell, R. Holmestad, T. Saito, J. Røyset, and O. Reiso, Directionality and column arrangement principles of precipiatetes in Al-Mg-Si-(Cu) and Al-Mg-Cu linked to line defect in Al. Mater. Sci. Forum 877 (2016), pp. 461–470. doi:10.4028/www.scientific.net/MSF.877.461.
- [56] T. Saito, E.A. Mørtsell, S. Wenner, C.D. Marioara, S.J. Andersen, J. Friis, K. Matsuda, and R. Holmestad, Atomic structures of precipitates in Al-Mg-Si alloys with small additions of other elements. Adv. Eng. Mater. 20 (2018), pp. 180015. doi:10.1002/adem.201800125.
- [57] S. Pogatscher, H. Antrekowitsch, M. Werinos, F. Moszner, S.S.A. Gerstl, M.F. Francis, W.A. Curtin, J.F. Löffler, and P.J. Uggowitzer, Diffusion on demand to control precipitation aging: application to Al-Mg-Si alloys. Phys. Rev. Lett. 112 (2014), pp. 225701. doi:10.1103/PhysRevLett.112.225701.
- [58] S. Pogatscher, H. Antrekowitsch, H. Leitner, D. Pöschmann, Z.L. Zhang, and P.J. Uggowitzer, Influence of interrupted quenching on artificial aging of Al-Mg-Si alloys. Acta Mater. 60 (2012), pp. 4496–4505. doi:10.1016/j.actamat.2012.04.026.
- [59] S. Pogatscher, H. Antrekowitsch, H. Leitner, T. Ebner, and P.J. Uggowitzer, Mechanisms controlling the artificial aging of Al-Mg-Si alloys. Acta Mater. 59 (2011), pp. 3352-3363. doi:10.1016/j.actamat.2011.02.010.
- [60] S. Qin, A. Bendo, T. Tsuchiya, S. Lee, and K. Matsuda, Effect of cooling rate on precipitation during homogenization cooling in excess Si type Al-Mg-Si alloy. Mater. Lett. 278 (2020), pp. 128363. doi:10.1016/j.matlet.2020.128363.
- [61] S. Qin, A. Bendo, T. Tsuchiya, S. Lee, Y. Zou, and K. Matsuda, Effect of cooling rate on precipitation during homogenization cooling in balanced Al-Mg2Si alloy. Mater. Trans. 61(11) (2020), pp. 2115–2120. doi:10.2320/matertrans.MT-M2020189.
- [62] M.R. Gazizov, A.V. Dubina, D.A. Zhemchuzhnikova, and R.O. Kaibyshev, Effect of equal channel angular pressing and aging on the microstructure and mechanical properties of an Al-Cu-Mg-Si alloy. Phys. Met. Metallogr. 116(7) (2015), pp. 718–729. doi:10.1134/S0031918X15070066.
- [63] M. Gazizov, C.D. Marioara, J. Friis, S. Wenner, R. Holmestad, and R. Kaibyshev, Precipitation behavior in an Al-Cu-Mg-Si alloy during ageing. Mater. Sci. Eng. A 767 (2019), pp. 138369. doi:10.1016/j.msea.2019.138369.
- [64] Y.X. Lai, W. Fan, M.J. Yin, C.L. Wu, and J.H. Chen, Structures and formation mechanisms of dislocation-induced precipitates in relation to the age-hardening responses of Al-Mg-Si alloys. J. Mater. Sci. Technol. 41 (2020), pp. 127–138. doi:10.1016/j.jmst.2019.11.001.
- [65] K. Matsuda, S. Shimizu, H. Gamada, Y. Uetani, F. Shinagawa, and S. Ikeno, Effect of deformation on the precipitates in Al-Mg2Si alloys containing silicon in excess. Mater. Des. Eng. 48(1) (1999), pp. 10–15. doi:10.2472/jsms.48.10.
- [66] E. Thronsen, C.D. Marioara, J.K. Sunde, K. Minakuchi, T. Katsumi, I. Erga, S.J. Andersen, J. Friis, K. Marthinsen, K. Matsuda, and R. Holmestad, The effect of
- [67] E. Thronsen, H. Morkeseth, C.D. Marioara, K. Minakuchi, T. Katsumi, K. Marthinsen, K. Matsuda, and R. Holmestad, The effect of small additions of Fe and heavy deformation on the precipitation in an Al-1.1Mg-0.5Cu-0.3Si at.% alloy. Metall. Mater. Trans. 53 (2022), pp. 3296–3310. doi:10.1007/s11661-022-06744-9.
- [68] K. Matsuda, S. Tada, S. Ikeno, T. Sato, and A. Kamio, Crystal system of rod-shaped precipitates in an Al-1.0mass%Mg2Si-0.4mass%Si alloy. Scr. Metall. Mater. 32(8) (1995), pp. 1175-1180. doi:10.1016/0956-716X(95)00121-B.
- [69] K. Matsuda, S. Ikeno, T. Sato, and A. Kamio, A metastable phase having the orthorhombic crystal lattice in an Al-1.0mass% Mg2Si-0.4mass% Si alloy. Scr. Mater. 34(11) (1996), pp. 1797–1802. doi:10.1016/1359-6462(96)00057-7.
- [70] K. Matsuda, S. Ikeno, T. Sato, and A. Kamio, Classification of metastable phases in Al-Mg2Si alloys by HRTEM. Mater. Sci. Forum 217-222 (1996), pp. 707–712. doi:10.4028/www.scientific.net/MSF.217-222.707.
- [71] S.J. Andersen, C.D. Marioara, R. Vissers, A. Frøseth, and H.W. Zandbergen, The structural relation between precipitates in Al-Mg-Si alloys, the Al-matrix and diamond silicon, with emphasis on the trigonal phase U1-MgAl2Si2. Mater. Sci. Eng. A 444 (2007), pp. 157–169. doi:10.1016/j.msea.2006.08.084.
- [72] S.J. Andersen, C.D. Marioara, A. Frøseth, R. Vissers, and H.W. Zandbergen, Crystal structure of the orthorhombic U2-Al4Mg4Si4 precipitate in the Al-Mg-Si alloy system and its relation to the β' and β” phases. Mater. Sci. Eng. A 390 (2005), pp. 127–138. doi:10.1016/j.msea.2004.09.019.
- [73] S.J. Andersen, C.D. Marioara, A. Frøseth, R. Vissers, and H.W. Zandbergen, Crystal structures of the trigonal U1-MgAl2Si2 and orthorhombic U2-Mg4Al4Si4 precipitates in the Al-Mg-Si alloy system. I. Phys. Conf. Ser. 179 (2003), pp. 225.
- [74] K. Matsuda, Y. Uetani, T. Sato, and S. Ikeno, Metastable phases in an Al-Mg-Si alloy containing copper. Metall. Mater. Trans. A 32 (2001), pp. 1293–1299. doi:10.1007/s11661-001-0219-2.
- [75] K. Matsuda, D. Teguri, Y. Uetani, T. Sato, and S. Ikeno, Cu-seggregation at the Q'/α-Al interface in Al-Mg-Si-Cu alloy. Scr. Mater. 47 (2002), pp. 833–837. doi:10.1016/S1359-6462(02)00325-1.
- [76] S. Wenner, C.D. Marioara, S.J. Andersen, and R. Holmestad, Effect of room temperature storage time on precipitation in Al-Mg-Si(-Cu) alloys with different Mg/Si ratios. Int. J. Mater. Res. 103 (2012), pp. 948–954. doi:10.3139/146.110795.
- [77] H.S. Hasting, J.C. Walmsley, A.T.J. Van Helvoort, C.D. Marioara, S.J. Andersen, and R. Holmestad, Z-contrast imaging of the arrangement of Cu in precipitates in 6XXX-series aluminium alloys. Philos. Mag. Lett. 86(9) (2006), pp. 589–597. doi:10.1080/09500830600938340.
- [78] C.D. Marioara, S.J. Andersen, T.N. Stene, H. Hasting, J. Walmsley, A.T.J. Van Helvoort, and R. Holmestad, The effect of Cu on precipitation in Al-Mg-Si alloys. Philos. Mag. 87(23) (2007), pp. 3385–3413. doi:10.1080/14786430701287377.
- [79] L. Arnberg and B. Aurivillius, The crystal structure of AlxCu2Mg12-xSi7 (h-AlCuMgSi). Acta Chem. Scand. 34a (1980), pp. 1–5.
- [80] M. Torsaeter, R. Vissers, C.D. Marioara, S.J. Andersen, and R. Holmestad, Crystal structure determination of the Q' and C-type plate precipitates in Al-Mg-Si-Cu (6xxx) alloys, in Jürgen Hirsch, Birgit Skrotzki, Günter Gottstein (Eds.), Aluminium Alloys: Their Physical and Mechanical Properties, vol. 2, Wiley-VHC, Aachen, 2008.
- [81] M. Fiawoo, X. Gao, L. Bourgeois, N. Parson, X.Q. Zhang, M. Couper, and J.F. Nie, Formation of multiple orientation relationships of Q precipitates in Al-Mg-Si-Cu alloys. Scr. Mater. 88 (2014), pp. 53–56. doi:10.1016/j.scriptamat.2014.05.013.
- [82] M. Torsaeter, W. Lefebvre, C.D. Marioara, S.J. Andersen, J.C. Walmsley, and R. Holmestad, Study of intergrown L and Q' precipitates in Al-Mg-Si-Cu alloys. Scr. Mater. 64 (2011), pp. 817–820. doi:10.1016/j.scriptamat.2011.01.008.
- [83] G.M. Scamans, N.J.H. Holroyd, and C.D.S. Tuck, The role of magnesium segregation in the intergranular stress corrosion cracking of aluminium alloy. Corros. Sci. 27(4) (1987), pp. 329–347. doi:10.1016/0010-938X(87)90076-Χ.
- [84] X. Sauvage, N. Enikeev, R. Valiev, Y. Nasedkina, and M. Murashkin, Atomic-scale analysis of the segregation and precipitation mechanisms in a severely deformed Al-Mg alloy. Acta Mater. 72 (2014), pp. 125–136. doi:10.1016/j.actamat.2014.03.033.
- [85] M. de Hass and J.T.M. De Hosson, Grain boundary segregation and precipitation in aluminium alloys. Scripta Mater. 44 (2001), pp. 281-286. doi:10.1016/S1359-6462(00)00577-7.
- [86] K. Teichmann, C.D. Marioara, S.J. Andersen, and K. Marthinsen, The effect of preaging deformation on the precipitation behavior of an Al-Mg-Si alloy. Metall. Mater. Trans. A 43 (2012), pp. 4006–4014. doi:10.1007/s11661-012-1235-0.
9. 著作権:
- この資料は、"Artenis Bendo, Jonathan Fellowes, Matthew Smith, Masoud Moshtaghi, Zelong Jin, Kenji Matsuda, Zhongyun Fan & Xiaorong Zhou"の論文:"Solute micro-segregation profile and associated precipitation in cast Al-Mg-Si alloy"に基づいています。
- 論文ソース:https://doi.org/10.1080/14786435.2024.2336012
この資料は上記の論文に基づいて要約されたものであり、商業目的での無断使用は禁止されています。
Copyright © 2025 CASTMAN. All rights reserved.