本論文概要は、['A356-T6アルミニウム鋳造合金の疲労挙動。パートI:鋳造欠陥の影響']と題された論文に基づいており、['Journal of Light Metals']誌に掲載されました。
1. 概要:
- タイトル:鋳造欠陥の影響。パートI:A356-T6アルミニウム鋳造合金の疲労挙動 (Fatigue behavior of A356-T6 aluminum cast alloys. Part I. Effect of casting defects)
- 著者:Q.G. Wang, D. Apelian, D.A. Lados
- 出版年:2001年
- 出版ジャーナル/学会:Journal of Light Metals
- キーワード:アルミニウム鋳物、疲労寿命、鋳造欠陥、破壊力学、ワイブル統計 (Aluminum castings; Fatigue life; Casting defects; Fracture mechanics; Weibull statistics)
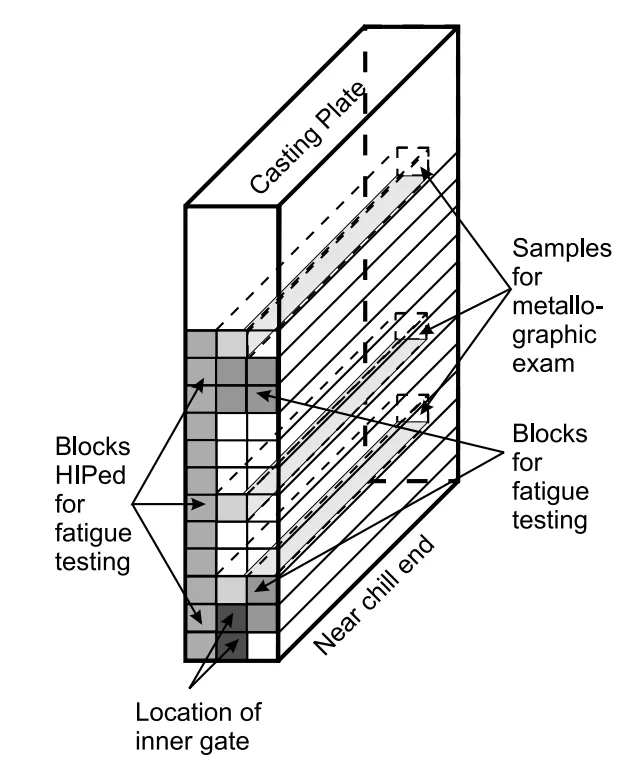
2. 研究背景:
研究トピックの背景:
鋳造アルミニウム合金は、その優れた鋳造性、耐食性、特に高い強度対重量比により、自動車産業での使用が増加しています。繰り返しサイクル荷重下での高信頼性が要求される形状鋳造アルミニウム部品の使用増加は、鋳造Al-Si合金の疲労特性に大きな関心を寄せています。鋳造アルミニウム部品の疲労特性は、鋳造欠陥および微細組織特性に大きく依存します。
既存研究の現状:
一部の研究では、引張延性と同様に、疲労抵抗はデンドライトアーム間隔および共晶シリコン粒子のサイズを微細化することによって向上するという見解を支持していますが [1,2]、鋳造欠陥の有害な影響も認識されています [3]。液体アルミニウムは水素吸着および酸化を受けやすいため、アルミニウム鋳物にはガス気孔および酸化物介在物が不可避的に存在します。さらに、鋳造が適切に供給されない場合、収縮気孔が発生し、これも疲労特性に有害です。疲労寿命と欠陥サイズの関係を予測する定量的な方法が最近開発されましたが [4–8]、気孔形状および欠陥タイプが疲労寿命に及ぼす影響について、実験データに基づいて包括的に理解することは依然として困難です。
研究の必要性:
実際のアプリケーションでは、一定レベルの気孔が鋳物で許容されており、これは特定のアプリケーションによって異なります。欠陥およびその他の微細組織パラメータが疲労寿命に及ぼす具体的な役割を特定することが重要です。さらに、欠陥の役割に関する定量的な理解は、設計仕様と品質管理 [9] の両方に対する欠陥許容基準を設定するために不可欠です。
3. 研究目的と研究課題:
研究目的:
本研究の目的は、さまざまな応力条件下でのA356アルミニウム鋳造合金の疲労性能に及ぼす鋳造欠陥(気孔および酸化物皮膜)および二次デンドライトアーム間隔(SDAS)の影響を実験的に調査することです。また、疲労亀裂の開始に対する臨界欠陥(気孔/酸化物)サイズの存在を調べることも目的としています。
主な研究課題:
- 鋳造欠陥、特に気孔および酸化物皮膜がA356-T6アルミニウム合金の疲労寿命に及ぼす有害な影響を定量化すること。
- 鋳造欠陥サイズと疲労寿命の関係を決定すること。
- 鋳造欠陥と組み合わせて疲労性能に及ぼす二次デンドライトアーム間隔(SDAS)の役割を調査すること。
- 欠陥のある鋳物の疲労寿命を予測するための破壊力学およびワイブル統計の適用可能性を探求すること。
- A356-T6合金で疲労亀裂を開始する欠陥の種類を特定し、特性評価すること。
研究仮説:
- 鋳造欠陥は、A356-T6アルミニウム合金の疲労寿命を著しく短縮するであろう。
- 疲労寿命は、鋳造欠陥サイズが増加するにつれて減少するであろう。
- 疲労亀裂の開始に対する臨界欠陥サイズが存在し、このサイズ未満では、他の微細組織的特徴が主要な開始点になるであろう。
- 破壊力学の原理を使用して、欠陥サイズに基づいて鋳物の疲労寿命を定量的に予測できるであろう。
- ワイブル統計は、欠陥のあるアルミニウム鋳物の疲労破壊挙動を効果的に説明できるであろう。
4. 研究方法
研究デザイン:
A356アルミニウム鋳造合金を使用して実験的研究を実施しました。水素レベルと鋳型充填を制御することにより、さまざまな程度の気孔と酸化物皮膜で製造された試験鋳物から円筒形試験片を準備しました。一部の試験片は、気孔のない条件を作成するためにHIP処理およびDensal™処理を受け、比較しました。疲労試験は、さまざまな応力振幅と応力比(R = 0.1、0.2、-1)で実施されました。
データ収集方法:
疲労試験は、55 Hzでプルプルおよびプルプッシュ正弦波荷重制御下でサーボ油圧式インストロンマシンを使用して実施されました。円筒形試験片は室温で試験されました。各試験片の破壊までのサイクル数(Nf)を記録しました。破断面は、走査型電子顕微鏡(SEM)を使用して疲労亀裂の開始点を特定し、欠陥サイズを測定するために検査しました。定量的な金属組織分析を実施してSDASを測定しました。
分析方法:
- 疲労亀裂成長分析: パリ・エルドガン方程式 (Paris-Erdogon equation) を用いて、鋳造欠陥からの疲労亀裂成長をモデル化しました。亀裂閉口効果を組み込んだ有効応力拡大係数範囲(ΔKeff)を考慮しました。
- ワイブル統計分析: 2パラメータワイブル分布 (Weibull distribution) を使用して、疲労寿命データを統計的に分析し、疲労性能のばらつきを特性評価しました。線形回帰を適用して、ワイブル係数(b)と特性疲労寿命(N₀)を推定しました。
- 破壊力学的アプローチ: 破断面で鋳造欠陥のサイズを測定し、破壊力学モデルで初期亀裂サイズ(aᵢ)として使用して疲労寿命を予測しました。
- 微視的破面解析: SEMおよびEDSを使用して、疲労亀裂の開始点(気孔、酸化物皮膜)を特定し、破壊特徴を特性評価しました。
研究対象と範囲:
本研究は、Sr改質されたA356-T6アルミニウム鋳造合金に焦点を当てました。試験片は、さまざまな二次デンドライトアーム間隔(SDAS)と鋳造欠陥(気孔および酸化物皮膜)レベルで準備されました。本研究では、欠陥サイズ(最大400〜500 µm)と応力比(R = 0.1、-1)が室温疲労性能に及ぼす影響を調査しました。HIP処理およびDensal™処理された試験片を含めて、欠陥のない状態を表しました。
5. 主な研究結果:
主な研究結果:
- 鋳造欠陥は、欠陥のない(HIP処理された)試験片と比較して、疲労寿命を少なくとも1桁以上著しく短縮しました。
- 疲労寿命は、鋳造欠陥サイズが増加するにつれて減少しました。
- HIP処理された試験片は、非HIP処理された試験片よりも有意に長い疲労寿命を示しました。
- 疲労亀裂の開始に対する臨界欠陥サイズが存在するように見え、このサイズ未満では、疲労亀裂は共晶粒子やすべり帯などの他の発生源から開始されました。
- 疲労亀裂は、主に試験片表面または表面近くに位置する気孔および酸化物皮膜から開始されました。
- 気孔は、酸化物皮膜よりも疲労寿命に有害であることがわかりました。
- 疲労寿命データは、2パラメータワイブル分布によってよく説明されました。
- 欠陥のある鋳物の疲労寿命は、欠陥サイズに基づいて破壊力学を使用して定量的に予測できました。
データ解釈:
- 鋳造欠陥、特に気孔および酸化物皮膜の存在は、A356-T6合金の疲労寿命を制御する主要な要因です。
- より大きな欠陥は、応力集中の増加と加速された亀裂伝播により、より早い疲労破壊につながります。
- HIPなどのプロセスを通じて鋳造欠陥を排除または削減すると、疲労性能が大幅に向上します。
- ワイブル分布は、欠陥特性の変動性を考慮して、鋳造アルミニウム合金の疲労破壊の統計的性質を効果的に捉えています。
- 破壊力学は、欠陥サイズに基づいて疲労寿命を予測するための実行可能なアプローチを提供し、これは欠陥からの亀裂伝播がこれらの材料の疲労破壊の支配的な段階であることを示唆しています。
- 気孔および酸化物皮膜から発生した亀裂に対するワイブル係数と特性疲労寿命の違いは、異なる欠陥タイプに関連する明確な疲労挙動を示しています。
図リスト:
- 図 5. さまざまな欠陥サイズを持つSr改質A356合金のS-Nデータ。2つの異なる応力比(a)R = 0.1および(b)R = -1で試験。「→」はランアウト – 試験片が最大10⁷サイクルまで破壊しなかったことを示します。
- 図 6. Sr改質A356鋳物で疲労亀裂を開始するさまざまな欠陥を示すSEM顕微鏡写真:(a)気孔、(b)酸化物皮膜。
- 図 7. さまざまな欠陥を含むSr改質A356鋳造合金の疲労寿命データに関する2パラメータワイブルプロット。
- 図 8. 気孔サイズの関数としてのSr改質A356-T6合金の疲労寿命。(a)SDAS:20-25 µm、(b)SDAS:70-75 µm。
- 図 9. さまざまなSDAS値に対する酸化物皮膜サイズの関数としてのSr改質A356-T6合金の疲労寿命。
- 図 10. (a)R = 0.1および(b)R = -1での試験に対する欠陥サイズ√Aの影響を含む修正された疲労寿命プロット。
- 図 11. (a)R = 0.1および(b)R = -1での試験に対する実際の疲労寿命(Nf)と計算された亀裂伝播寿命(Np)の比較。
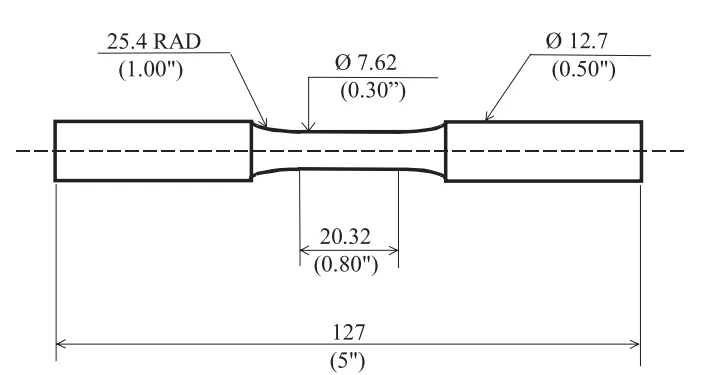
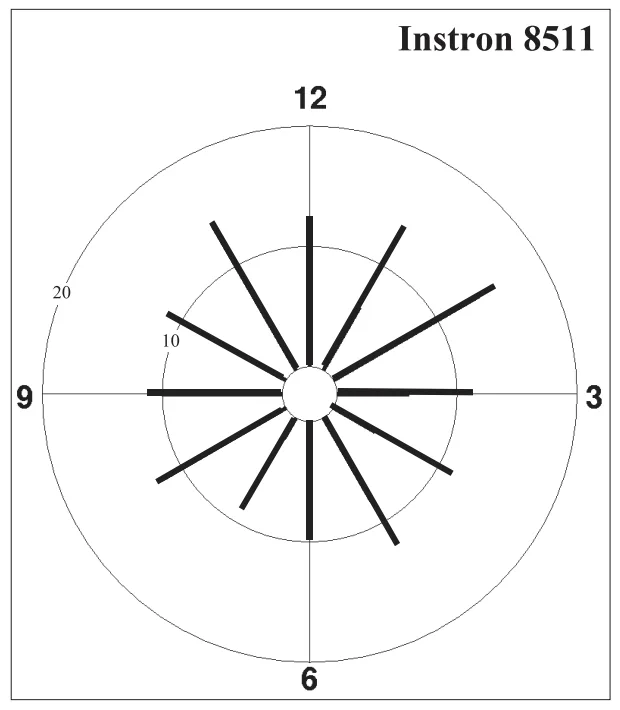
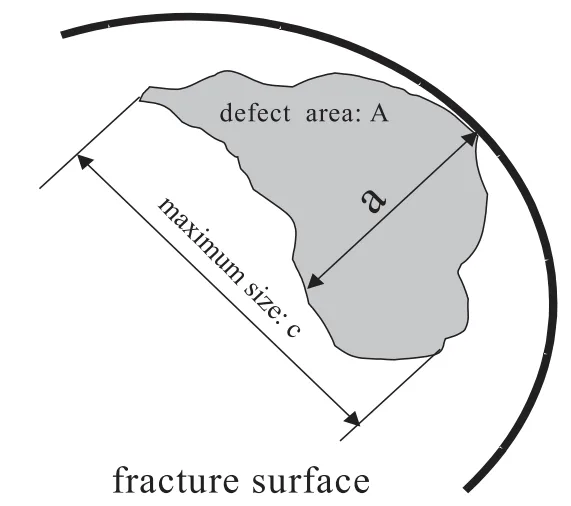
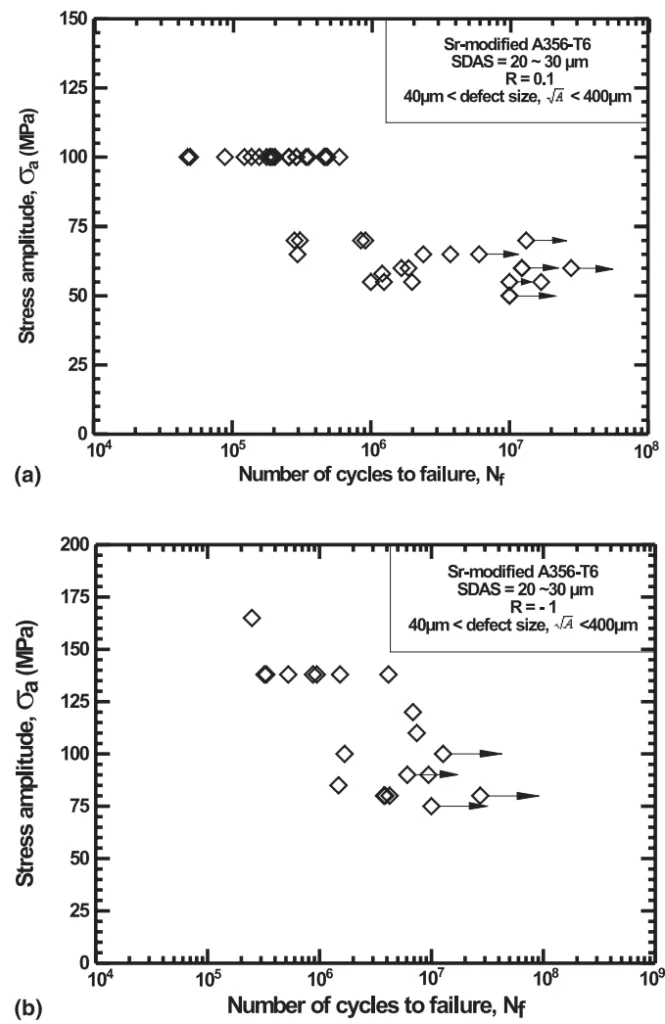
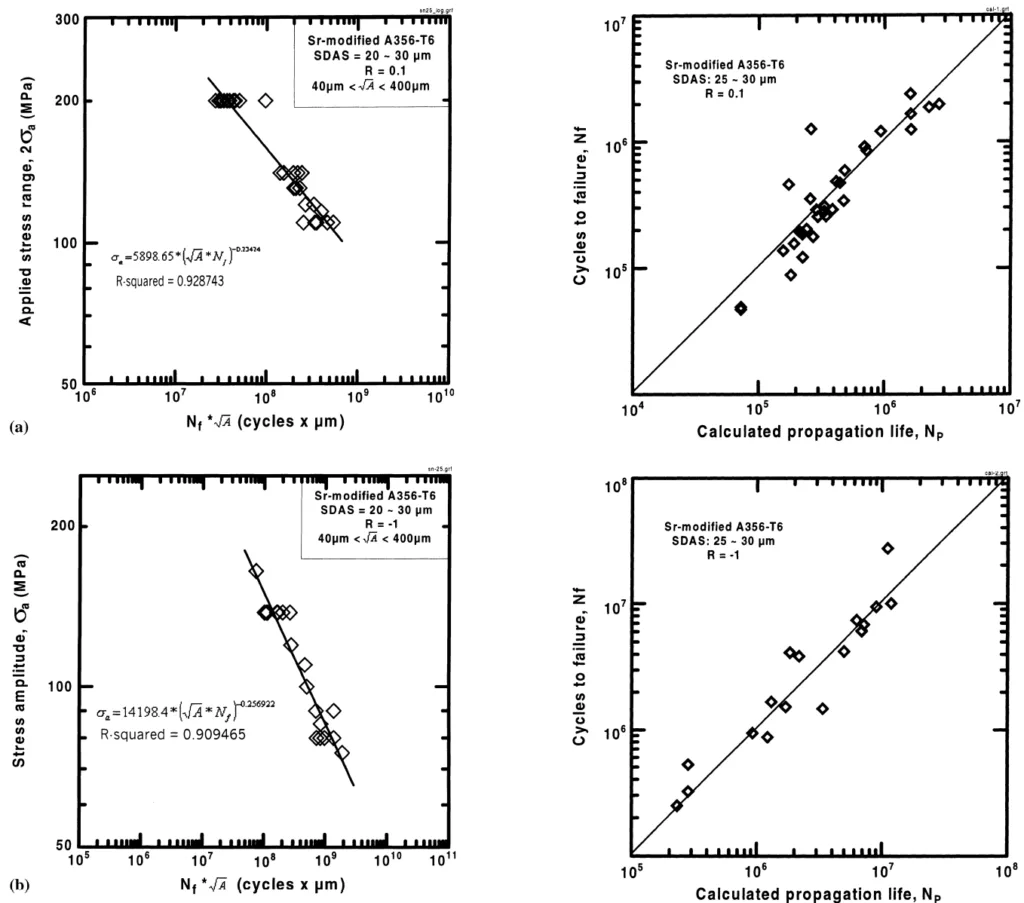
6. 結論:
主な結果の要約:
本研究は、鋳造欠陥、特に気孔および酸化物皮膜が、A356-T6アルミニウム鋳造合金の疲労挙動に重大な有害影響を及ぼすことを決定的に示しています。これらの欠陥は、疲労寿命の亀裂伝播段階だけでなく、亀裂開始段階も短縮します。鋳造欠陥サイズは、疲労寿命の減少と直接的な相関関係があります。臨界欠陥サイズ未満では、疲労亀裂は他の微細組織的特徴から開始されます。破壊力学およびワイブル統計は、これらの材料の疲労寿命を分析および予測するための効果的なツールです。気孔は、疲労性能の点で酸化物皮膜よりも重要な欠陥タイプとして特定されました。
研究の学術的意義:
本研究は、自動車産業で広く使用されている材料であるA356-T6合金の疲労性能に及ぼす鋳造欠陥の影響に関する貴重な定量的データを提供します。欠陥のある鋳造アルミニウム合金の疲労寿命予測に対する破壊力学およびワイブル統計の適用可能性を検証します。本研究は、鋳造欠陥の存在下での疲労亀裂の開始および伝播メカニズムに関するより深い理解に貢献し、気孔と酸化物皮膜の役割を区別します。
実用的な意味合い:
本研究の結果は、ダイカスト産業に重要な実用的な意味合いを持っています。欠陥サイズと疲労寿命の間に確立された相関関係は、鋳造アルミニウム部品の欠陥許容基準および品質管理基準の開発に情報を提供できます。臨界欠陥サイズの特定は、望ましい疲労性能を達成するために欠陥レベルを最小限に抑えるための目標を提供します。本研究は、特に鋳造プロセス中の気孔を削減することの重要性を強調しています。予測モデルは、部品設計および寿命評価に活用でき、疲労に重要なアプリケーションにおける鋳造アルミニウム部品の信頼性を向上させることができます。
研究の限界
本研究は、特定の荷重条件(正弦波荷重、R=0.1、-1)下でのA356-T6合金の室温疲労挙動に焦点を当てました。研究結果は、この合金およびこれらの試験条件に特有である可能性があります。本研究では、主に気孔および酸化物皮膜を鋳造欠陥として考慮しており、他のタイプの欠陥とその相互作用に関する追加の研究が必要です。破壊力学モデルの亀裂閉口の仮定(Kopening = 0)は単純化であり、特に負の応力比で寿命予測にある程度の近似誤差をもたらす可能性があります。
7. 今後のフォローアップ研究:
- フォローアップ研究の方向性
今後の研究では、気孔形状と形態、および異なるタイプの酸化物皮膜(若いものと古いもの)が疲労寿命に及ぼす影響を調査する必要があります。可変振幅荷重下および高温での疲労挙動を調査すると、研究結果の適用範囲が広がります。特に負の応力比で、亀裂閉口効果をより正確に説明するために破壊力学モデルを改良し、より堅牢な疲労寿命予測のために欠陥サイズとタイプの統計分布を組み込むための追加研究が必要です。 - さらなる探求が必要な領域
疲労亀裂の開始に対する鋳造欠陥と、共晶シリコン粒子や金属間化合物相などの他の微細組織的特徴との間の相互作用を完全に理解するためには、さらなる探求が必要です。サイズ、形状、分布を含む鋳造欠陥の正確な特性評価のための高度な非破壊検査(NDE)技術を開発することは、産業現場で欠陥ベースの疲労寿命予測モデルを実装するために不可欠です。疲労性能の向上に対するさまざまな欠陥低減戦略と鋳造後処理の効果を調査することは、今後の研究にとって重要な領域のままです。
8. 参考文献:
- [1] A.Wickberg, G. Gustafsson, L.E. Larsson, Microstructural effects on the fatigue properties of a cast Al7SiMg alloy, SAE Technical Publication #840121, 1984.
- [2] T.L. Reinhart, ASM Handbook, vol. 19, ASM International, Materials Park, OH, 1996, pp. 813-822.
- [3] N.E. Promisel, Evaluation of non-ferrous materials, 1956 (cited by H.E. Boyer, Atlas of fatigue curves, American Society of Metals, 1986).
- [4] M.J. Couper, A.E. Neeson, J.R. Griffiths, Casting defects and the fatigue life of an aluminum casting alloy, Fatigue Fract. Eng. Mater. Struct. 13 (1990) 213-227.
- [5] B. Skallerud, T. Iveland, G. Härkegård, Fatigue life assessment of aluminum alloys with casting defects, Eng. Fracture Mech. 44 (1993) 857-874.
- [6] J.A. Odegard, K. Pedersen, Fatigue properties of an A356 (AlSi7Mg) aluminium alloy for automotive applications - fatigue life prediction, SAE technical paper SAE-940811, 1994, pp. 25-32.
- [7] Chih-Hsien Ting, A model for the long-life fatigue behaviour of small notches, Ph.D. Dissertation, University of Illinois at Urbana-Champaign, 1991.
- [8] D.L McLellan, M.M. McLellan, An approach to fatigue design for aluminum castings, AFS Trans. 104 (1996) 445-449.
- [9] J.F. Major, Porosity control and fatigue behaviour in A356T61 aluminum alloy, AFS Trans. 105 (1997) 901-906.
- [10] W. Elber, Fatigue crack closure under cyclic tension, Eng. Fracture Mech. 2 (1970) 37-45.
- [11] N.E. Dowling, ASTM STP 637 (1977) 97–121.
- [12] D. Wilhem, J. FitzGerald, J. Carter, D. Dittmer, An empirical approach to determining K for surface cracks, in: Proceedings of the Fifth International Conference on Fracture, vol. 1, Cannes, 1981, pp. 11-21.
- [13] W. Weibull, A statistical distribution function of wide applicability, J. App. Mech. 18 (1951) 293-297.
- [14] A. Khalili, K. Kromp, Statistical properties of weibull estimators, J. Mater. Sci. 26 (1991) 6741-6752.
- [15] J. Campbell, The origin of porosity in castings, in: Proceedings of the fourth Asia Foundry Congress incorporated in 32nd Annual Convention of Australian Foundry Institute, 1996, pp. 33-50.
- [16] Q.G. Wang, Microstructure and tensile fracture behavior of Al-Si-Mg casting alloys, Ph.D. Thesis, The University of Queensland, Brisbane, Australia, 1997.
- [17] C.H. Cáceres, C.J. Davidson, J.R. Griffiths, The deformation and fracture behaviour of an Al-Si-Mg casting alloy, Mater. Sci. Eng. A A197 (1995) 171-179.
- [18] Q.G. Wang, C.H. Cáceres, The fracture mode in Al-Si-Mg casting alloys, Mater. Sci. Eng. A A241 (1998) 72-82.
- [19] Q.G. Wang, C.H. Cáceres, On the strain hardening behavior of Al-Si-Mg casting alloys, Mater. Sci. Eng. A 234-236A (1997) 106-109.
- [20] C.H. Cáceres, Q.G. Wang, J.R. Griffiths, C.J. Davidson, The effect of Mg on the microstructure and mechanical behavior of two commercial Al-Si-Mg casting alloys, Metall. Trans. A 30A (1999) 2611-2618.
- [21] Q.G. Wang, C.H. Cáceres, J.R. Griffiths, The cracking of Fe-rich and eutectic Si particles in an Al-7Si-0.7Mg casting alloy, AFS Trans. 106 (1998) 131-136.
- [22] D.S. Saunders, J.R. Griffiths, B.A. Parker, The fracture toughness of an aluminum casting alloy, J. Aust. Inst. Metals 20 (1975) 33-38.
- [23] D.A. Gerard, D.A. Koss, The dependence of crack initiation on porosity during low cycle fatigue, Mater. Sci. Eng. A 129 (1990) 77-85.
- [24] D.A. Gerard, The influence of porosity on low cycle fatigue, Ph.D. Dissertation, Michigan Technological University, Houghton, MI, 1989, pp. 1–167.
- [25] J.C. Ting, The long-life regime fatigue analysis for lost foam cast Al-Si Alloy 319, Ph.D. Dissertation, University of Illinois-Champaign, IL, 1991, pp. 1–186.
- [26] J. Campbell, C. Nyahumwa, N.R. Green, The concept of the fatigue potential of cast alloys, in: Proceedings of Materials Solution Conference '98 on Advances in Aluminum Casting Technology, 12-15 October 1998, pp. 225-233.
- [27] C. Nyahumwa, N.R. Green, J. Campbell, Effect of mold filling turbulence on fatigue properties of cast aluminum alloys, AFS Trans. 106 (1998) 215-223.
- [28] J.C. Newman Jr., A crack opening stress equation for fatigue crack growth, Int. J. Fracture 24 (1984) 131-135.
- [29] J.C. Newman Jr., A crack closure model for prediction of fatigue crack growth under aircraft spectrum loading, ASTM STP 748 (1982) 53-84.
- [30] N.E. Dowling, N.S. Iyyer, Fatigue crack growth and closure at high cyclic strains, Mater. Sci. Eng. 96 (1987) 99-107.
- [31] I. Gustavson, A. Melander, A finite element study of the early growth of fatigue cracks emanating from a spherical pore, in: Proceedings of the Fifth International Conference on Numerical Methods in Fracture Mechanics, Germany, 1990, pp. 225-236.
- [32] Y. Verremen, J.P. Ballon, J. Masounave, Fatigue short crack propagation and plasticity-induced crack closure at the toe of a fillet welded joint, in: The Behavior of Short Fatigue Cracks, EGF publication 1, 1986, pp. 387-404 (Mechanical Engineering Publication, London).
9. 著作権:
- この資料は、"[Q.G. Wang, D. Apelian, D.A. Lados]"の論文:「[鋳造欠陥の影響。パートI:A356-T6アルミニウム鋳造合金の疲労挙動]」に基づいています。
- 論文ソース:https://doi.org/10.1016/S1471-5317(00)00008-0
この資料は上記の論文に基づいて要約されており、商業目的での無断使用は禁止されています。
Copyright © 2025 CASTMAN. All rights reserved.