この紹介資料は、「ARCHIVES of FOUNDRY ENGINEERING」に掲載された論文「Anodization of cast aluminium alloys produced by different casting methods」に基づいています。
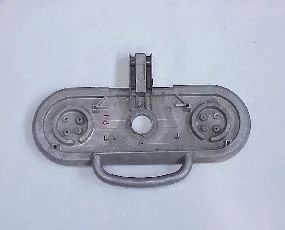
1. 概要:
- タイトル: Anodization of cast aluminium alloys produced by different casting methods (異なる鋳造法により製造された鋳造アルミニウム合金のアノード酸化)
- 著者: K. Labisz, L.A. Dobrzański, J. Konieczny
- 発行年: 2008
- 掲載学術誌/学会: ARCHIVES of FOUNDRY ENGINEERING (Published quarterly as the organ of the Foundry Commission of the Polish Academy of Sciences)
- キーワード: Aluminium cast alloys, Mechanical properties, Surface treatment, Alumina layer, Anodization (アルミニウム鋳造合金、機械的特性、表面処理、アルミナ層、アノード酸化)
2. アブストラクト (Abstract):
本稿では、AlSi12およびAlSi9Cu3アルミニウム鋳造合金のアノード酸化に対する、砂型鋳造と高圧鋳造という2つの鋳造法の有用性を調査した。電解液組成、温度、電流タイプ、電流値などの定義されたアノード酸化パラメータを用いて、陽極酸化アルミナ表面層を生成した。選択したアルミニウム鋳造合金のアノード酸化後の陽極酸化層の品質、寸法、特性を調査した。アルミナ層は光学顕微鏡を用いて観察し、機械的特性も測定し、摩耗試験はABR-8251装置を用いて行った。研究には、アルミニウム鋳物に得られた陽極酸化層の化学組成、形状、粗さの影響分析が含まれた。実施された調査は、今後の研究分野、特にアルミニウム鋳造合金のアノード酸化プロセスの最適化の方向性を示している。例えば、建築構造物、電子部品、航空および自動車産業の構造部品などの過酷な環境での用途を増やすために、元素の耐食性を向上させ、適切な陽極表面層を得る範囲などである。
3. 導入 (Introduction):
環境条件下では、アルミニウム部品の表面は自然に薄いアルミナAl2O3層で覆われる。この層の厚さは、材料、環境、暴露時間に応じて数十ナノメートル程度である。適切なアノード酸化技術を選択することにより、層の厚さを数マイクロメートルの値まで増加させることができる。この方法を用いると、表面は塩水、酸性溶液、外部からの機械的影響などの環境要因に対してより高い耐性を持つようになる。アノード酸化はアルミニウム合金部品の腐食保護に一般的に使用されており、そのため陽極表面層の特性と品質を決定するためのISO 7599やDIN 17611などの国際規格が存在する。材料工学の進歩により、構造材料と工具材料の両方に関して、金属材料の強度に関する問題を満足に解決することが可能になった。近年、様々な産業分野でのアルミニウム合金の使用が継続的に増加しており、アルミニウムおよびその合金、アルミニウムマトリックス複合材料の製造技術の開発が多くの科学機関で観察されている[6-9]。陽極酸化層は、アルミニウム電子部品、家庭用品、器具部品、庭園家具、観光およびスポーツ用品、自動車付属品、アルミニウム建具の要素に適用され、保護的および装飾的な機能を持つ。酸化物層はコンデンサの電極用アルミニウム箔にも生成される。硬質陽極酸化層は航空および自動車産業に適用できる[10-12]。しかし、陰極部位として作用する銅の金属間化合物の存在は、銅含有アルミニウム合金を腐食攻撃に対してより脆弱にする。高い銅含有量は、アルミニウム合金をアノード酸化するのが最も困難な合金の一つにする。厚い陽極酸化皮膜の生成は硬質アノード酸化条件下でのみ可能であるが、この合金は局所的な焼損(バーニング)を起こしやすい。厚い多孔質酸化物が生成される際、Al-Cu合金のアノード酸化プロセス中に酸素発生による皮膜割れも観察される。この合金の特有の特徴は、合金/皮膜界面に比較的狭い銅濃化領域が形成された後、アノード酸化中に銅の酸化が起こることである。これは皮膜形成中の電流効率の低下をもたらす。この低下は、銅リッチ領域上での酸素発生にも起因しており、確立された銅腐食抑制剤が電流効率を改善するために使用されてきた[13-16]。
4. 研究の概要 (Summary of the study):
研究テーマの背景 (Background of the research topic):
アノード酸化はアルミニウム合金の重要な表面処理であり、耐食性と耐摩耗性を向上させる。結果として得られる陽極酸化層の特性は、合金組成、その製造プロセス(鋳造法)、およびアノード酸化パラメータに依存する。合金中の銅含有量はアノード酸化プロセスを複雑にする可能性がある。
従来の研究状況 (Status of previous research):
アノード酸化は、既存の国際規格と既知の用途を持つ、確立されたプロセスである。これまでの研究では、合金の種類、アノード酸化パラメータ(電解液、電流、温度)の影響、および特定の合金組成(例:高銅含有量)に関連する課題が、結果として得られる陽極酸化層の特性と形成メカニズムに及ぼす影響が調査されてきた[1-16]。
研究の目的 (Purpose of the study):
AlSi12およびAlSi9Cu3アルミニウム鋳造合金のアノード酸化に対して、砂型鋳造と高圧ダイカストという2つの異なる鋳造法の有用性を調査すること。本研究は、形成されたアルミナ層の構造と厚さを調べ、鋳造法が結果として得られる陽極酸化層に及ぼす影響を比較することを目的とした。
中核となる研究 (Core study):
2つのアルミニウム合金、EN AC-AlSi12(b)およびEN AC-AlSi9Cu3(Fe)を、高圧鋳造法と砂型鋳造法の両方を用いて製造した。これらの鋳造サンプルを、特別に定義されたパラメータ(H2SO4電解液、制御された温度、パルス電流)の下でアノード酸化プロセスにかけた。得られた陽極酸化アルミナ層は、光学顕微鏡を使用して構造と均一性を評価し、その厚さを測定した。耐摩耗性は、標準化された試験(ISO 8251)を用いて質量損失を測定することによって評価し、アノード酸化されたサンプルをアノード酸化されていないサンプルと比較した。
5. 研究方法論 (Research Methodology)
研究デザイン (Research Design):
比較実験研究を実施した。2つの一般的な鋳造アルミニウム合金(AlSi12、AlSi9Cu3)を、2つの異なる鋳造法(砂型鋳造、高圧鋳造)を用いて準備した。各グループのサンプルを、同一の制御された条件下でアノード酸化した。得られた表面層を、微細構造、厚さ、および耐摩耗性に基づいて分析し、比較した。アノード酸化されていないサンプルを摩耗比較の基準線として使用した。
データ収集および分析方法 (Data Collection and Analysis Methods):
- 材料準備: 標準的な金属組織学的手順を用いて、サンプルの切断、マウント、研削、研磨。
- アノード酸化: H2SO4電解液、特定の温度範囲(-4~2℃)、定義されたパルス電流レジーム(表2)を用いて実施。
- 微細構造調査: 光学顕微鏡(Olympus BX60M)を使用し、500~1000倍の倍率で陽極酸化層構造および下地合金の微細構造を観察。
- 層厚測定: 顕微鏡写真から評価(結果はFig. 6に提示)。
- 摩耗試験: ISO 8251規格に従い、ABR-8251テスターを用いて実施。4.9Nの荷重下で400ステップ後の質量損失[mg]を測定(表3)。制御された条件下で5回繰り返し試験(表4)。
- 初期表面形状: MicroProfレーザーゲージを用いた分析について言及されているが、結果の議論では詳述されていない。
研究トピックと範囲 (Research Topics and Scope):
この研究は主に、鋳造法(砂型対高圧)がAlSi12およびAlSi9Cu3鋳造合金のアノード酸化性と結果として得られる特性(層構造、厚さ、均一性、耐摩耗性)に及ぼす影響に焦点を当てた。範囲は、詳述された特定の合金、鋳造法、およびアノード酸化パラメータに限定された(表1および表2)。
6. 主要な結果 (Key Results):
主要な結果 (Key Results):
- 高圧鋳造法および砂型鋳造法の両方で鋳造されたAlSi12およびAlSi9Cu3合金の両方に、陽極酸化アルミナ層が成功裏に生成された。
- 金属組織学的検査の結果、いずれのサンプルグループの陽極酸化層にも不連続性は見られなかった(Fig. 7-12)。
- 陽極酸化層の厚さは、両合金において、高圧鋳造材と比較して砂型鋳造材の方が著しく厚かった(約5倍)(Fig. 6)。
- 層の均一性は様々であった:高圧鋳造部品の場合、AlSi12はAlSi9Cu3よりも均一な(ただし薄い)層を生成した。砂型鋳造部品の場合、AlSi9Cu3はより良好な均一性(砂型鋳造AlSi12と比較して全体的に薄い)を示した。AlSi12の微細化された共晶組織が、より良好な均一性をもたらすことが指摘された。
- アノード酸化処理は、アノード酸化されていないサンプルと比較して、摩耗(質量損失)を減少させた(表5)。
- 耐摩耗性の最大の改善(質量損失約50%減少)は、砂型鋳造で製造されたアノード酸化EN AC-AlSi9Cu3(Fe)合金で観察された。他のアノード酸化サンプルは、30%から47%の間の質量損失減少を示した。
- 砂型鋳造合金は、アノード酸化後、一般に高圧鋳造合金と比較して低い質量損失(より高い耐摩耗性)を示した。
- 砂型鋳造AlSi9Cu3合金と高圧鋳造AlSi12合金の組み合わせが、テストされたグループの中で最大の耐摩耗性を示した。
図の名称リスト (Figure Name List):
- Fig. 1. Scheme of the anodization process including the anodized part, electrolyte, power supply and the alumina surface layer.
- Fig. 2. Stages in the development of the alumina surface layer, a) barrier layer development, b) growth of small inhomogenities, c) continuously grow of pores, d) stabilization of the interpore distances (JPK Instruments AG, 2003).
- Fig. 3. Non anodized element made from the AC-AlSi12 aluminium alloy, produced by the Pressure Cast method
- Fig. 4. Anodized element made from the AC-AlSi9Cu3 aluminium alloy, produced by the Pressure Cast method
- Fig. 5. Overanodized element made from the AC-AlSi9Cu3 aluminium alloy, produced by the Pressure Cast method
- Fig. 6. Results of the anodic layer thickness measurement
- Fig. 7. Anodic alumina layer generated on the AlSi9Cu3 alloy, high pressure cast
- Fig. 8. Anodic alumina layer generated on the AlSi12 alloy, sand cast
- Fig. 9. Microstructure of the AlSi9Cu3 alloy, high pressure cast
- Fig. 10. Microstructure of the AlSi12 alloy, sand cast
- Fig. 11. Microstructure of the AlSi12 alloy, high pressure cast
- Fig. 12. Microstructure of the AlSi9Cu3 alloy, sand cast
7. 結論 (Conclusion):
本研究は、砂型鋳造法と高圧ダイカスト法の両方が、アノード酸化に適したAlSi12およびAlSi9Cu3合金部品の製造に実行可能であることを示した。最も高い耐摩耗性をもたらす組み合わせは、砂型鋳造法で製造されたAlSi9Cu3合金であり、次いで高圧ダイカスト法で製造されたAlSi12合金であった。逆に、砂型鋳造されたAlSi12および高圧鋳造されたAlSi9Cu3部品は、より低い耐摩耗性を示した。アノード酸化は、アノード酸化されていない合金と比較して、摩耗による重量損失を著しく減少させる。鋳造法はアノード酸化された層の耐摩耗性に影響を与え、本研究では一般的に砂型鋳造合金がより大きな耐摩耗性を示した。
8. 参考文献 (References):
- [1] M.H. Robert, D. Delbin: Production of cellular A2011 alloy from semi-solid state, Journal of Achievements in Materials and Manufacturing Engineering, 17, (2006), pp. 137-140.
- [2] M. Wierzbińska, J. Sieniawski: Effect of morphology of eutectic silicon crystals on mechanical properties and cleavage fracture toughness of AlSi5Cu1 alloy, Journal of Achievements in Materials and Manufacturing Engineering, 14, (2006), pp. 31-36
- [3] Ι. Tsangaraki-Kaplanoglou, S. Theohari, Th. Dimogerontakis, Y. Wang, H. Kuo, S. Kia: Effect of alloy types on the anodizing process of aluminum, Surface & Coatings Technology, 200, (2006), pp. 2634 - 2641
- [4] K. P. Han, J. L. Fang: Decorative-protective coatings on aluminium, Surface and Coathings Technology, 88 (1996) pp. 178-182
- [5] H. Konno, K. Utaka, R. Furuichi: Two step of anodizing process of aluminium as a means of improving the chemical and physical properties of oxide films, Corrosion Science, 38, (1996), pp. 2247-2256
- [6] M. Maejima, K. Saruwatari, M. Takaya: Friction behaviour of anodic oxide film on aluminum impregnated with molybdenum sulfide compounds, Surface and Coatings Technology, 132 (2000), pp. 105-110
- [7] I. Vrublevsky, V. Parkoun, V. Sokol, J. Schreckenbach: Study of chemical dissolution of the barrier oxide layer of porous alumina films formed in oxalic acid using a re-anodizing technique, Applied Surface Science 236 (2004) pp. 270-277
- [8] J. Konieczny, L.A. Dobrzański, K. Labisz, J. Duszczyk: The influence of cast method and anodizing parameters on structure and layer thickness of aluminum alloys, Journal of Materials Processing Technology, 157-158 (2004), pp. 718-723
- [9] L.E. Fratila-Apachitei, J. Duszczyk, L. Katgerman: AlSi(Cu) anodic oxide layers formed in H2SO4 at low temperature using different current waveforms, Surface and Coatings Technology, 165, (2003), pp. 232-240
- [10] S.J. Garcia-Vergara, P. Skeldon, G.E. Thompson, H. Habazaki: Pore development during anodizing of Al-3.5 at.%W alloy in phosphoric acid, Surface & Coatings Technology, 201, (2007), pp. 9506-9511
- [11] M. Shahid, A.Q. Khan: Mechanism of film growth during anodizing of Al-alloy-8090/SiC metal matrix composite in sulphuric acid electrolyte, Journal of Materials Science, 32, (1997), pp. 3775-3781
- [12] T. Haga, H. Sakaguchi, H. Inui, H. Watari, S. Kumai, Aluminum alloy semisolid strip casting using an unequal diameter twin roll caster, Journal of Achievements in Materials and Manufacturing Engineering, 14, (2006), pp. 157-162
- [13] D. Djozan, M. Amir-Zehni, Anodizing of inner surface of long and small-bore aluminum tube, Surface and Coatings Technology, 173, 2003, pp. 185-191
- [14] L.E. Fratila-Apachitei, J. Duszczyk, L. Katgerman, Voltage transients and morphology of AlSi(Cu) anodic oxide layers formed in H2SO4 at low temperature, Surface and Coatings Technology, 157 (2002) pp. 80-92
- [15] J. Zhang, X. Zhao, Y. Zuo, J. Xiong, The bonding strength and corrosion resistance of aluminum alloy by anodizing treatment in a phosphoric acid modified boric acid/sulfuric acid bath, Surface & Coatings Technology, 202, 2008, pp. 3149-3156
- [16] T. Dimogerontakis, L. Kompotiatis, I. Kaplanoglou, oxygen evolution during the formation of barrier type anodic film on 2024-T3 aluminium alloy, Corrosion Science, 39, (1998), 1939-1951
9. 著作権 (Copyright):
- この資料は、「K. Labisz, L.A. Dobrzański, J. Konieczny」による論文です。「Anodization of cast aluminium alloys produced by different casting methods」に基づいています。
- 論文の出典:[DOI URLがあれば挿入、なければ「DOI情報なし」と記載]
この資料は上記の論文に基づいて要約されており、商業目的での無断使用は禁じられています。
Copyright © 2025 CASTMAN. All rights reserved.