この紹介論文は、Int. J. Corros. Scale Inhib.誌に掲載された論文「Improvement and stabilization of the electrochemical properties of zinc alloys during casting」の研究内容です。
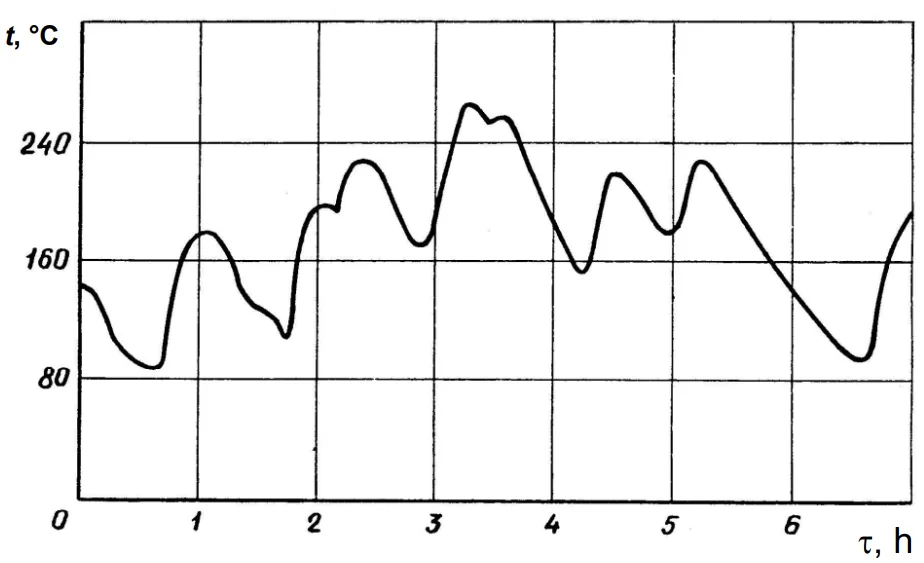
1. 概要:
- タイトル: Improvement and stabilization of the electrochemical properties of zinc alloys during casting (鋳造中の亜鉛合金の電気化学的特性の改善と安定化)
- 著者: V.A. Kechin, E.Y. Lyublinski, A.V.Kireev and E.S. Prusov
- 出版年: 2019年
- 掲載ジャーナル/学会: Int. J. Corros. Scale Inhib.
- キーワード: 犠牲陽極(sacrificial anodes)、構造(structure)、鋳造(foundry)、電気化学(electrochemistry)
2. 概要 (Abstract)
鋳造犠牲ガルバニック陽極合金の「金属-電解質」系における電気化学的不均一性が出現する主な理由は、金属の性質、組成、構造などに関連する内部要因です。鋳造陽極製造技術を開発する際には、合金の構造的均質性を確保することに特別な注意を払う必要があります。鋳造陽極の構造と基本特性の形成に主要な役割を果たすのは、鋳型内の溶融物の凝固条件に影響を与える熱的プロセスです。この論文では、冷却条件に応じた鋳造亜鉛犠牲合金(ZSA)の構造と基本的な電気化学的特性に関する研究結果を提示します。さまざまな冷却強度での凝固する金属(金属が冷却されるとき)と形状(鋳型が加熱されるとき)の温度場解析により、鋳造サイクル時間を最適化することができました。これは、鋳型の初期温度によって決定される冷却条件を考慮して、トレッド全体の厚さにわたって材料の均一な構造と安定した電気化学的特性を保証します。例えば、18kgの亜鉛合金トレッドを鋳造する場合、鋳造前の鋳型温度は120〜160℃である必要があります。これらの条件下で、鋳造犠牲陽極合金の必要な品質が達成されます: 電流容量-効率 93–96%; 腐食電位 –Ec = 815–820 mV vs. SHE。必要な鋳造サイクル時間は10〜14分です。さまざまな形状とサイズの犠牲陽極についても同様のデータが得られました。数値シミュレーション法を用いた亜鉛陽極と鋳造鋳型(砂-粘土、鋳鉄、鋼鉄水冷式)の熱的相互作用に関する研究結果に基づいて、水冷式鋳型に陽極を鋳造することが妥当であり、熱除去と鋳造トレッドの均一な構造を得るための最も有利な条件を提供します。得られた結果に基づいて、さまざまなサイズの亜鉛陽極鋳造技術が開発され、高く安定した電気化学的特性を提供します。
3. 研究背景:
研究テーマの背景:
- 熱的プロセスは、溶融物の凝固中の鋳物のほとんどの特性形成に主要な役割を果たします[1-11]。
- 鋳型内の溶融物の凝固条件を研究することは、鋳造熱理論の最も重要な課題です。
先行研究の現状:
- 犠牲陽極(SA)鋳造時、金属鋳型の温度変動が激しい[12]。
- 亜鉛SA鋳造中の一連の鋳鉄鋳型の1つの温度の継続的なモニタリングにより、シフト中に初期鋳型温度が80℃から260℃に変化することが示されました(図1)。
- 鋳型温度が20℃から300℃に変化すると、亜鉛-アルミニウム合金の電流容量(CC)が96%から80%に低下します。
- 金属鋳型に充填されたZSAの巨視的構造を考慮すると、皮質、柱状、非配向結晶の3つの特徴的な領域が区別されます(図2)。
研究の必要性:
- 温度変動は、ZSAの電気化学的特性の不安定化と低下を説明することができます。
- 特にCCなどの保護特性のばらつきを避けるために、鋳造前に鋳型の温度を制御する必要があります。
- さまざまな冷却条件は、鋳造犠牲陽極断面の温度勾配変化を引き起こし、結晶構造と特性を変化させます。
4. 研究目的と研究課題:
研究目的:
- 冷却の熱条件に応じたZn-Al合金製の鋳造犠牲陽極の構造と基本的な電気化学的特性を研究する。
主要な研究:
- 冷却条件が鋳造亜鉛犠牲合金の構造と電気化学的特性に及ぼす影響の調査。
- 鋳型の初期温度に基づく鋳造サイクル時間の最適化。
- 高く安定した電気化学的特性を持つ亜鉛陽極鋳造技術の開発。
5. 研究方法
- 研究デザイン: 実験的研究、温度測定および流し出し(pouring out)法の使用。数値シミュレーション法も採用。
- データ収集:
- 温度測定: 溶融凝固の冷却曲線からトレッドと形状の温度場を構築しました。12点電位差計を使用した熱電対配列(図3)を使用しました。
- 流し出し: 凝固の性質を決定するために、合金を一定の間隔で流し出しました。
- 電気化学的試験: サンプルは、陽極分極を伴う3% NaCl水溶液中で試験しました(図4)。電位は、電位差計モデルIPCと塩化銀参照電極を使用して測定しました。
- 分析方法: 温度場解析、巨視的構造検査(図2)、電気化学的試験。CCと鋳造温度/凝固速度の関係を記述するために回帰方程式を作成しました。
- 研究範囲: Zn-Al系のトレッド合金(表1)。鋳造温度は480℃に一定に保ちました。鋳鉄鋳型の初期温度は20、160、310℃でした。
6. 主要な研究結果:
主要な研究結果と提示されたデータ分析:
- さまざまな冷却条件は、鋳造犠牲陽極の結晶構造と特性に変化をもたらします。
- 方向性凝固に最適な条件は、より高い温度勾配(160℃以下の鋳型での凝固)で提供されます。
- 金属鋳型におけるZSAトレッドの完全凝固時間は、初期温度によって異なります(表2)。
- 18kgの亜鉛合金トレッドを鋳造する前の鋳型温度は、必要な品質(電流容量-効率 93–96%; 腐食電位 –Ec = 815–820 mV vs. SHE)を達成するために120〜160℃である必要があります。
- 必要な鋳造サイクル時間は10〜14分です(図7)。
- 合金のCCは凝固速度とともに増加します(図10)。
- 回帰方程式:
- CC = 127 – 0.072tc (式1)
- CC = 84.21 + 0.035 Vs (式2)
- 水冷式鋳型は、熱除去と均一な構造を得るための最も有利な条件を提供します。
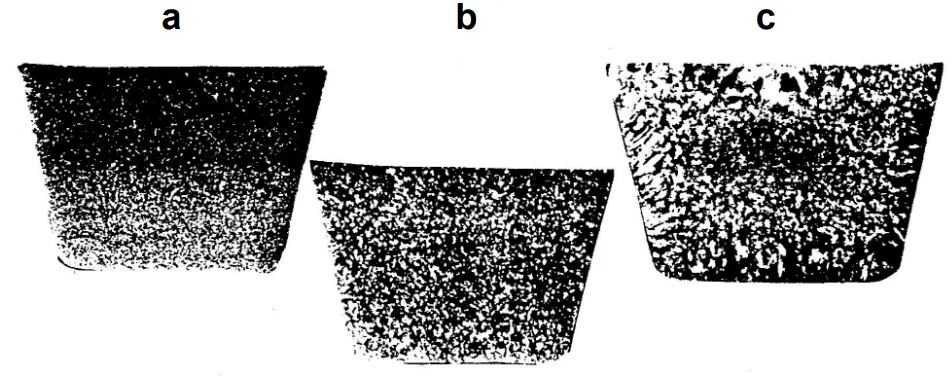

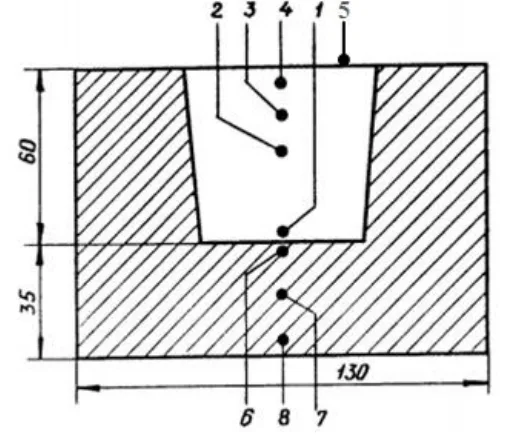

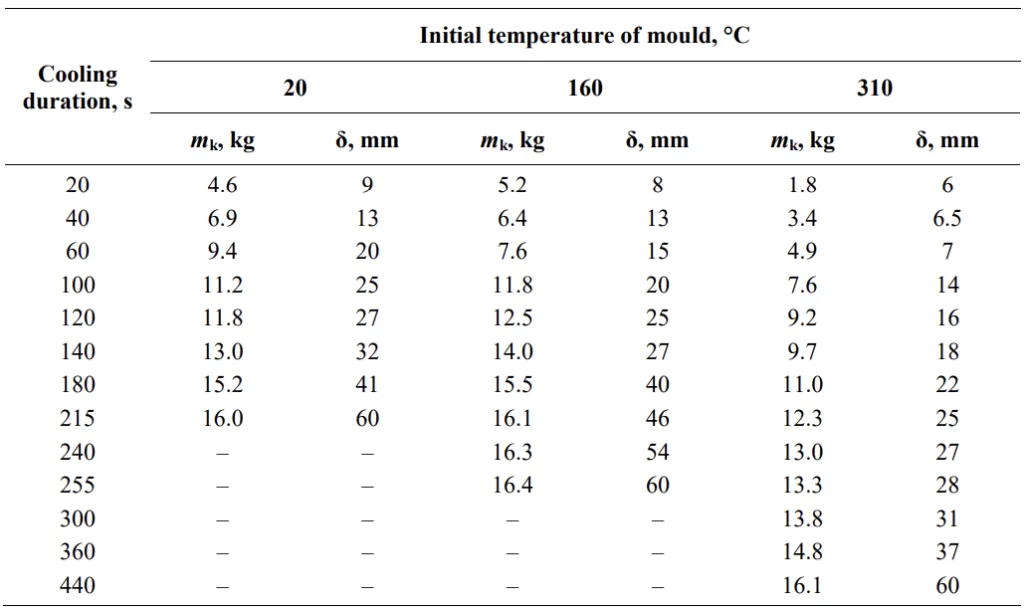
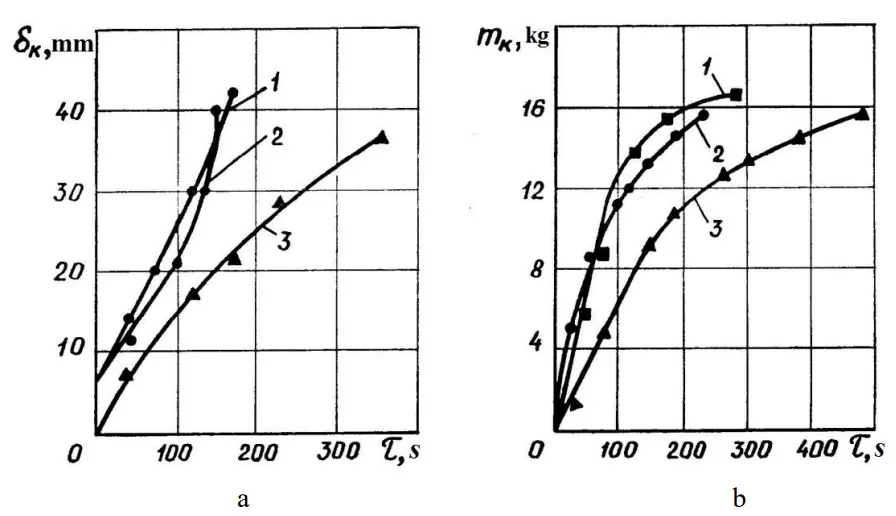
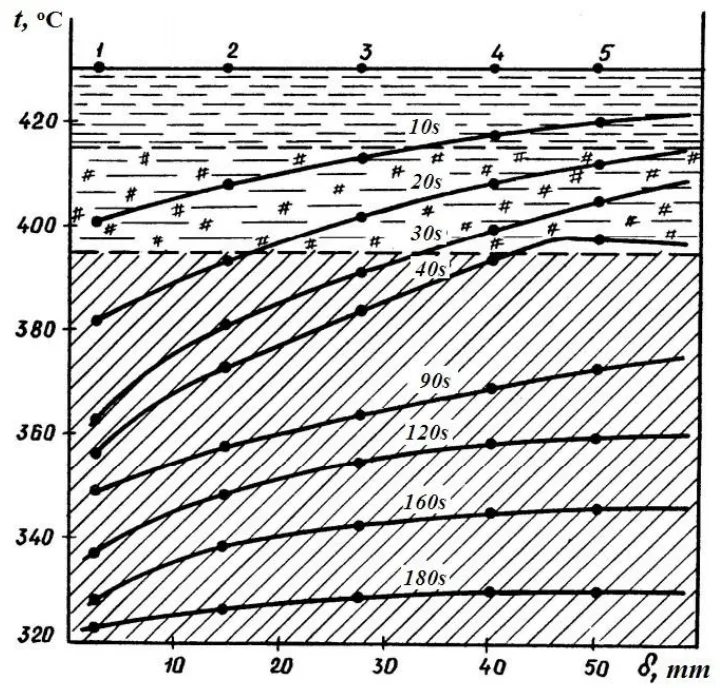
図の名称リスト:
- 図1. ZSA鋳造中の鋳型温度変化。
- 図2. 鋳型初期温度20℃(a)、160℃(b)、310℃(c)でのさまざまな凝固および冷却条件下での亜鉛犠牲陽極の巨視的構造。
- 図3. 硬化合金(1-5)および鋳鉄鋳型(6-8)の温度場測定のための熱電対設置構成。
- 図4. ホルダーに固定され、ビチューメンとパラフィンの混合物でコーティングされた電気化学的試験用サンプル: 1 銅ホルダー、2 – PVCパイプ、3 – コーティング、4 – 試験サンプル。
- 図5. 20℃(I)、160℃(II)、310℃(III)の鋳型温度での凝固合金と鋳鉄鋳型の高さ方向の温度変化: a, b – それぞれ冷却曲線と加熱曲線; c, d – 凝固合金と形状の温度場。
- 図6. さまざまな冷却条件下での金属の厚さ(a)と質量(b)の変化。1, 2, 3 – それぞれ20、160、310℃の鋳型初期温度。
- 図7. 鋳型内鋳物の冷却時間t1、設定温度t2までの鋳型冷却、および鋳型初期温度からの総鋳造サイクルtcの依存性。
- 図8. 非金属(a)および金属鋳型(b)への鋳造による亜鉛合金CCの変化に対する鋳造温度の影響。
- 図9. 非金属および金属(VII, VIII, IX)鋳型に以下の鋳造温度で鋳造した場合のCP1(I, II, III), CP2(IV, V, VI)合金の微細構造: I, IV, VII – 450°C; II, V, VII – 500°C; III, VI, IX – 550°C (×100).
- 図10. 凝固速度に応じたZSA1(a)およびZSA2(b)合金のCCと微細構造の変化。
- 図11. 亜鉛トレッド(犠牲陽極)製造用鋳型構造。
- 図12. 水冷式鋳型に鋳造する際の鋳造トレッドの温度変化。
7. 結論:
主要な調査結果の要約:
- さまざまな冷却条件は、鋳造亜鉛犠牲陽極の電気化学的特性に大きく影響します。
- 方向性凝固は、160℃を超えない鋳型温度で最もよく達成されます。
- 注入前に一定の鋳型温度を維持することは、一貫した鋳造品質のために非常に重要です。
- 指向性熱シンクを備えた水冷式鋳型は、凝固と製品品質の制御を向上させます。
- 振動開放型鋳鉄鋳型を使用することで、鋳造工程の複雑さが軽減されました。
今後の研究の可能性:
- この論文では今後の研究を明示的に示唆していませんが、さまざまな合金組成とさまざまな冷却条件に対する反応をさらに調査することが有益である可能性があります。
8. 参考文献:
- [1] D.M. Stefanescu, Science and Engineering of Casting Solidification, 3rd ed., 2015, Springer International Publishing AG, Switzerland, p. 559.
- [2] J. Dantzig and M. Rappaz, Solidification, 2009, Taylor & Francis Group, CRS Press, p. 621.
- [3] J. Campbell, Casting, 2nd ed., 2003, Butterworth-Heinemann, Elsevier, p. 335.
- [4] F.S. Yang and F. Ni, Effect of Cooling Rate on the Solidification of Zn-5wt%Al Alloy, Adv. Mater. Res., 2012, 366, 502-505.
- [5] M. Krupiński, B. Krupińska, K. Labisz, Z. Rdzawski and W. Borek, Influence of cooling rate on crystallization kinetics on microstructure of cast zinc alloys, J. Therm. Anal. Calorim., 2014, 118, no. 2, 1361–1367.
- [6] R.-N. Ma, Y.-Z. Fan, A. Du and P.-P. Zhang, Effect of cooling rate on morphology and corrosion resistance of Zn-Al-Mg alloy, Cailiao Rechuli Xuebao/Transactions of Materials and Heat Treatment, 2015, 36, no. 4, 49–55.
- [7] V.A. Kechin and E.Y. Lyublinski, New Sacrificial Anodic Alloys, NACE International, 2018, Phoenix, USA, Paper C2018–11388.
- [8] C. Jennings, A comparison of the structure and Consumption Rate for Centrifugally Cast Anodes Compared with Die-Cast Anodes, NACE International, 2018, Phoenix, USA, Paper C2018–10954.
- [9] E. Lyublinski and V. Kechin, Formation of basic properties of galvanic anodes during the industrial production, EUROCORR 2017, Prague, Czhech Republic, Paper 72701.
- [10] A. Aghajani, M. Atapour and R. Alibek, Passivation of Zinc Anodes in Marine Conditions, Mater. Perform., 2016, 55, no. 9, 34.
- [11] V.A. Kechin and E. Lyublinski, New Sacrificial Anodic Alloys, EUROCORR 2016, Montpellier, France, Paper 0-6242.
- [12] V.A. Kechin, Theory and Technology of Cast Sacrificial Materials, Vladimir State University, 2004, p. 181 (in Russian).
- [13] V.A. Kechin and E.Y. Lyublinski, Zinc Alloys, Moscow, Metallurgiya, 1986, p. 247 (in Russian).
- [14] V.A. Kechin and A.B.Kireev, Riser for the production of cast treads sacrificial anodes, RF Patent No. 2492020, 2013 (in Russian).
9. 著作権:
- この資料は、「V.A. Kechin, E.Y. Lyublinski, A.V.Kireev and E.S. Prusov」による論文「Improvement and stabilization of the electrochemical properties of zinc alloys during casting」に基づいています。
- 論文出典: doi: 10.17675/2305-6894-2019-8-1-7
この資料は、上記の論文を紹介するために作成されたものであり、商業目的での無断使用を禁じます。Copyright © 2025 CASTMAN. All rights reserved.