この論文の要約は、[発行者]に掲載された論文「重力ダイカストAl合金部品における有機および無機コアバインダーの比較分析」に基づいています。
1. 概要:
- タイトル: 重力ダイカストAl合金部品における有機および無機コアバインダーの比較分析 (A COMPARATIVE ANALYSIS ON ORGANIC AND INORGANIC CORE BINDERS FOR A GRAVITY DIECASTING AL ALLOY COMPONENT)
- 著者: A. Fortini, M. Merlin, G. Raminella
- 発表年: 2022年
- 掲載ジャーナル/学会誌: International Journal of Metalcasting
- キーワード: 砂型コア, 光学測定, 重力ダイカスト, 吸湿試験, 保存安定性
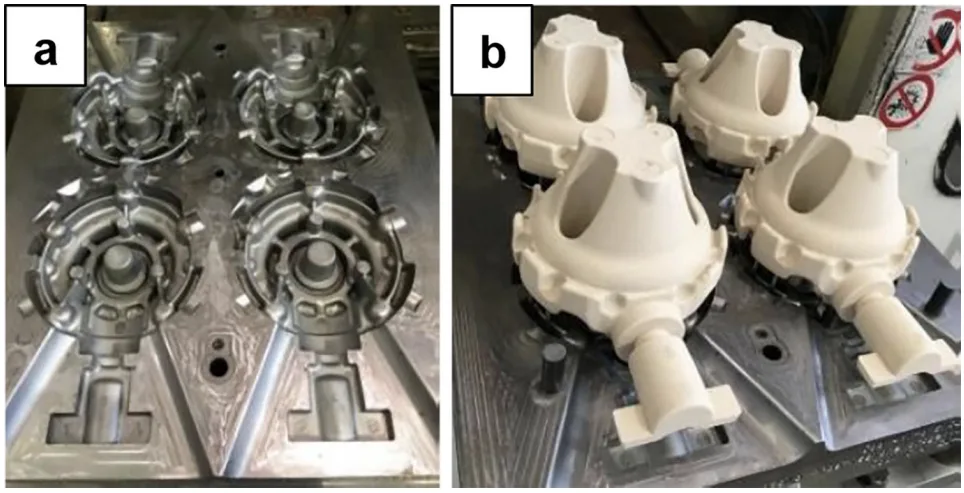
2. 研究背景:
金属鋳造業界では、過去20年間でコア製作における無機バインダーの使用が増加傾向にあります。この変化は主に、従来の有機バインダーと比較して、無機バインダーが健康と環境面で優れていることに起因しています。しかし、無機バインダーが商業用途で広く普及するためには、特に保存安定性に関する潜在的な固有の制限に対処するための継続的な技術改良が必要です。無機コアは保管中に劣化する可能性があることが知られており、有機コアの直接的な代替品としての適合性に懸念が生じています。既存の研究では、特に吸湿の影響を考慮した場合、鋳造環境内でのこれらのバインダーシステムの実際的な実装と性能を十分に調査していません。本研究は、重力ダイカストアルミニウム合金部品の製造において、有機コアバインダーの代替として無機コアバインダーを使用することの実現可能性を調査することにより、このギャップに対処します。特に、一般的な鋳造工場の保管条件下での吸湿感受性という重要な側面に着目しています。
3. 研究目的と研究課題:
本研究は、アルミニウム合金部品の重力ダイカストにおいて使用される有機および無機コアバインダーの性能を評価し、比較することを目的としています。本研究では、特に吸湿がコアの安定性に及ぼす影響、および最終的な鋳物の品質への影響を調査します。
本論文で取り上げられている主な研究課題は以下の通りです。
- 無機コアバインダーは、重力ダイカストアルミニウム合金部品の製造において、有機コアバインダーを効果的に代替できるか?
- 鋳造工場での保管中の吸湿は、有機コアと比較して無機コアの寸法安定性と構造的完全性にどのように影響するか?
- 有機コアと無機コアを使用して製造されたアルミニウム合金鋳物の機械的特性と微細構造にはどのような違いがあるか?
- 有機コアと無機コアを使用した場合、鋳造プロセス中に生成される有害な排出物のレベルにはどのような違いがあるか?
根底にある仮説は、無機コアは環境上の利点を提供する一方で、その吸湿感受性が実際の鋳造工場での応用に課題をもたらす可能性があるということです。本研究は、これらの課題を定量化し、持続可能な有機コアの代替としての無機コアの全体的な実現可能性を評価することを目的としています。
4. 研究方法
本研究では、有機および無機コアバインダーを評価するために、比較実験研究デザインを採用しました。研究方法論は、以下の主要なステップを含みます。
- 研究デザイン: フェノールウレタンコールドボックス法を用いて製造された有機コアと、市販のケイ酸ナトリウム系コーディスバインダーシステムを用いて製造された無機コアを対比する比較分析を実施しました。
- データ収集方法:
- 吸湿試験: 砂サンプルと完成したコアを様々な湿度条件にさらしました。点火減量と、制御された湿度環境(40℃、相対湿度100%の恒温恒湿槽、および鋳造工場の倉庫条件)での重量増加を測定し、吸湿性を評価しました。
- 3D光学測定: 吸湿による無機コアの寸法変化を、GOM Atos ScanBox 4105光学式3D測定機を用いて正確に測定し、測定値をCADモデルと比較しました。
- 鋳造試験: A356アルミニウム合金と有機および無機コアの両方を用いて重力ダイカスト試験を実施し、ドライブトレインのオートバイ部品を製造しました。
- 機械試験: 鋳物の引張特性(耐力Rp0.2、引張強さRm、伸びA%)をガルダビニQuasar 50試験機を用いて評価しました。
- 微細構造解析: 二次デンドライトアーム間隔(SDAS)と気孔率を、ZEISS Axioscope 7光学顕微鏡とZen Core 2.7画像解析ソフトウェアを用いて解析しました。
- 排出物分析: 鋳造中のガス状有機化合物排出物を採取し、UNI CEN/TS 13649規格に従ってガスクロマトグラフィー法を用いて分析しました。鋳造サイクル後の鋳型空洞の状態の目視検査も実施しました。
- 分析方法: 重量測定、寸法偏差、引張特性、SDAS、気孔率、および排出物濃度の定量データ分析を実施しました。砂、コア外観、および鋳型状態の目視検査に基づいて定性評価を行いました。
- 研究対象と範囲: 本研究では、自動車用途向けのA356アルミニウム合金部品の重力ダイカストで使用される砂型コアの製造において、特定の有機バインダーシステム(フェノールウレタンコールドボックス)と無機バインダーシステム(ケイ酸ナトリウム系コーディス)の比較に焦点を当てました。範囲には、鋳造工場の操業に関連する様々な保管湿度条件下でのコア性能の評価が含まれていました。
5. 主な研究結果:
実験結果は、有機および無機コアバインダーの性能に関する包括的な比較を提供しました。主な調査結果を以下にまとめます。
- 吸湿性:
- 点火減量 (WL): 表2は、両方のコアタイプの点火減量を示しています。有機コアは1.068〜1.187%のWL値を示しましたが、無機コアは0.184〜0.332%のWL値を示しました。有機コアの場合、WL値にはバインダー蒸発による約1.06%が含まれていることに注意が必要です。
- 恒温恒湿槽での吸湿 (MA): 図3は、無機コアが有機コアと比較して、恒温恒湿槽(40℃、相対湿度100%)でより大きな吸湿傾向を示したことを示しており、MA%が高くなっています。
- 鋳造工場の倉庫での吸湿: 図5bは、鋳造工場の倉庫(18℃、相対湿度32%)での保管中の無機コアの吸湿増加が、到着後14日間で無視できる程度であったことを示しており、MAは0.191%から0.245%に増加しました。
- 寸法安定性:
- 3D光学測定により、無機コアは恒温恒湿槽内の高湿度条件下で寸法変化を起こし(図7a、b)、幅方向の偏差が0.3mmを超える領域があることが明らかになりました。
- しかし、鋳造工場の倉庫(18℃、相対湿度32%)で14日間保管した後、無機コアの寸法偏差は最小限であり(図7c、d)、一般的な鋳造工場の保管条件下での寸法安定性を示しています。
- より極端な模擬保管条件(-8℃〜2℃、相対湿度80%の屋根付きの場所での保管)下でも、寸法変化は限定的であり、構造的にも48時間まで健全であることが確認されました(図8)。
- 鋳物の機械的特性:
- 引張試験(図9)では、有機コアと無機コアの両方で製造された鋳物で、同等またはわずかに改善された耐力(Rp0.2)と引張強さ(Rm)の値が示されました。
- 無機コアで作られた鋳物の伸び(A%)の値は、有機コアで作られた鋳物と比較して、平均してわずかに高く、ばらつきが少なくなりました。
- 鋳物の微細構造:
- 微細構造解析(図10b)により、無機コアで製造された鋳物は、有機コア(30〜33μm)と比較して、わずかに低い二次デンドライトアーム間隔(SDAS)値(22〜27μm)を示し、より微細な微細構造を示唆しました。
- 気孔率レベル(表3)は、両方のコアタイプで製造された鋳物で類似しており、低く(0.08%未満)なっています。
- 排出物と鋳型状態:
- 排出物分析(表4)により、無機コアを使用した鋳造では、有機コアと比較して、鋳造中に排出される有害な有機化合物の質量濃度が大幅に低いことが明らかになりました。
- 目視検査(図11)では、無機コアで使用された鋳型空洞は、200サイクル後も、有機コアで使用された鋳型に見られる暗い樹脂コーティングと比較して、残留物が最小限で、よりきれいな状態を維持していることが示されました。
図表リスト:
- 図1. コールドボックス法による有機コアの製造: (a) ハーフコアボックス, (b) 有機コア.
- 図2. 吸湿試験中の砂の外観画像。有機コア: (a) 初期状態, (b) 2時間点火減量後, (c) 3時間点火減量後, (d) 4時間点火減量後。無機コア: (e) 初期状態, (f) 1時間点火減量後, (g) 2時間点火減量後, (h) 3時間点火減量後。
- 図3. 恒温恒湿槽での保管時間による有機および無機コアのMA (%)の棒グラフ。
- 図4. 恒温恒湿槽での吸湿試験後のコアの画像: (a) 60分間調整後の有機コア, (b) 60分間調整後の無機コア, (c) および (d) (b) の無機コアの破損。
- 図5. 鋳造工場の倉庫での無機コアの吸湿試験: (a) コア保管状態の画像, (b) 保管時間によるMA (%) の棒グラフ。
- 図6. 初期状態の無機コアの3Dデジタルカラープロット: (a) 正面等角図, (b) 背面等角図。
- 図7. 吸湿後の無機コアの3Dデジタルカラープロット: (a) 正面および (b) 背面等角図 (恒温恒湿槽で40℃、相対湿度100%で60分間保管後), (c) 正面および (d) 背面等角図 (鋳造工場の倉庫で18℃、相対湿度32%で14日間保管後)。
- 図8. 吸湿後の無機コアの3Dデジタルカラープロット: (a) 正面および (b) 背面等角図 (鋳造工場の屋根付きの場所で24時間保管後), (c) 正面および (d) 背面等角図 (鋳造工場の屋根付きの場所で48時間保管後)。
- 図9. コアバインダーシステムが引張特性に及ぼす影響: (a) 引張試験片の位置, (b) 有機コアを使用した鋳造試験の引張特性, (c) 無機コアを使用した鋳造試験の引張特性。
- 図10. コアバインダーシステムがSDAS値に及ぼす影響: (a) 試験片の位置, (b) 位置別の有機および無機コアのSDASの棒グラフ。
- 図11. 200サイクル後の上型半分の画像: (a) 有機コア, (b) 無機コア。
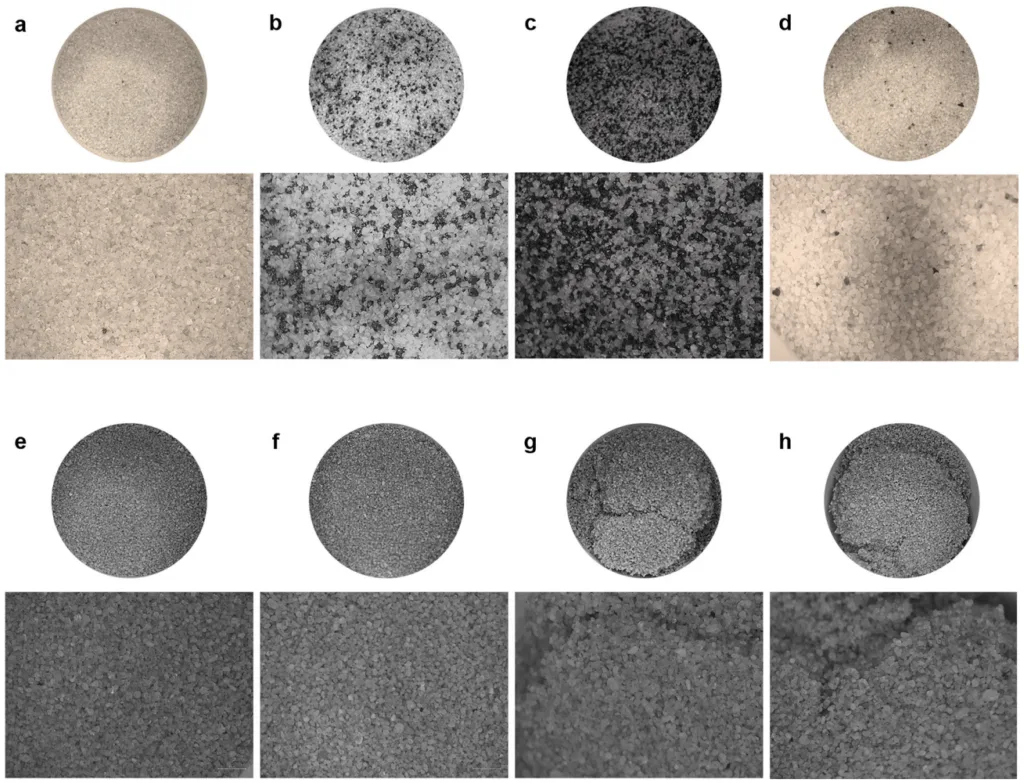
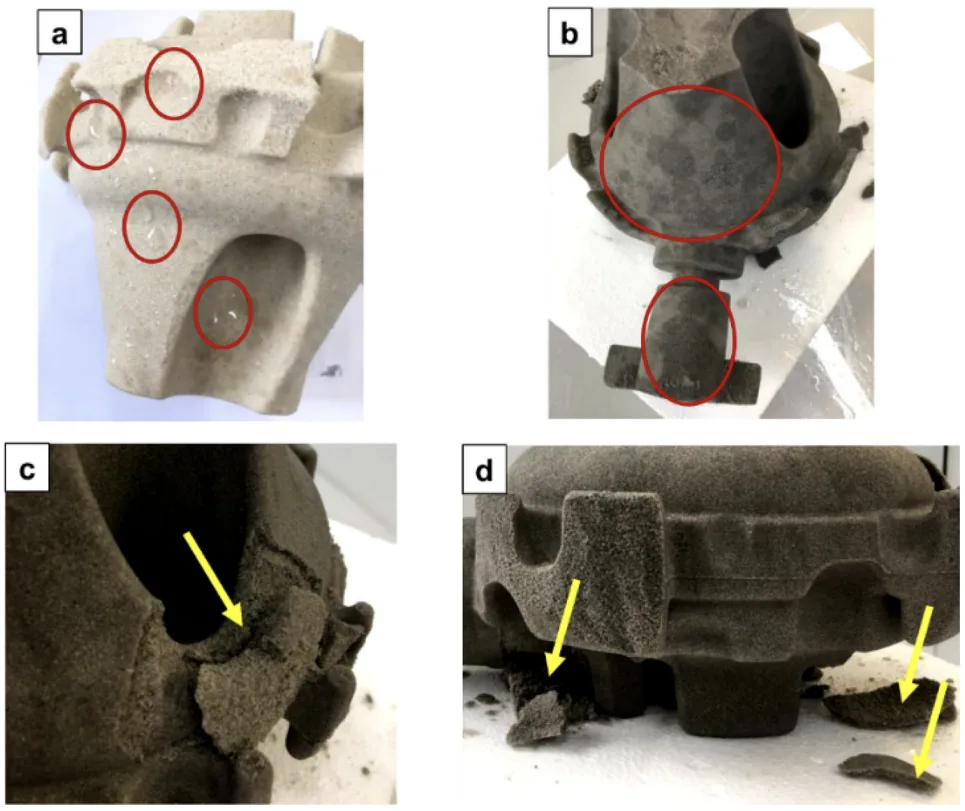
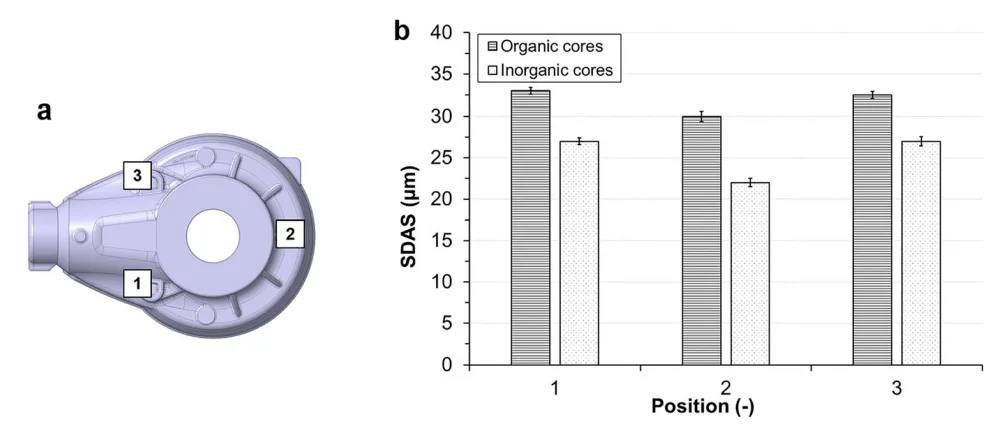
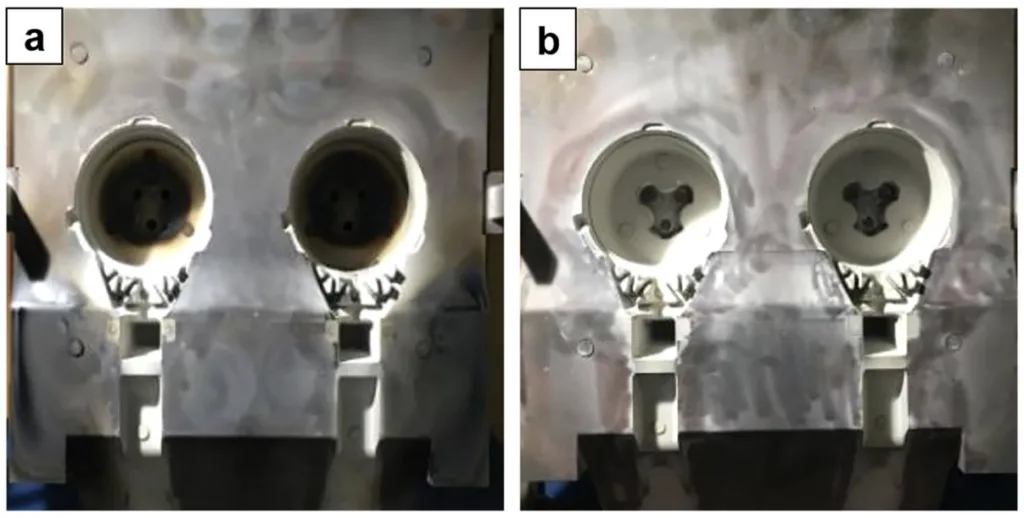
6. 結論と考察:
主な研究結果の要約: 本研究は、無機コアバインダー、特にケイ酸ナトリウム系システムが、アルミニウム合金の重力ダイカストにおいて、従来の有機バインダーの実行可能な代替案となることを結論付けました。無機コアは極端な湿度条件下では吸湿性が高いものの、一般的な鋳造工場の倉庫保管条件(最大14日間)下では十分な安定性と寸法完全性を示します。無機コアで製造された鋳物は、有機コアで作られた鋳物と比較して、同等またはわずかに改善された機械的特性と、より微細な微細構造を実現しています。重要なことに、無機コアは、鋳造中の有害なガス状排出物を大幅に削減し、長期の鋳造サイクルにわたって鋳型をよりきれいな状態に保つことで、環境上の大きな利点を提供します。
研究の学術的意義: 本研究は、金属鋳造における無機バインダーに関する知識の蓄積に貴重な実証データを提供します。吸湿性に関する懸念に直接的に対処し、重力ダイカストにおける鋳造工場での応用の成功事例を示しています。本研究は、無機コアシステムの性能を評価する際に、現実的な鋳造工場の保管条件を考慮することの重要性を強調しています。
実用的な意義: 本研究の知見は、鋳造工場が持続可能性を高め、作業環境を改善するために、鋳物の品質を損なうことなく、重力ダイカストに無機コアバインダーを自信を持って採用できることを強く示唆しています。無機コアに関連する排出量の削減と鋳型の清浄化は、環境および健康上の利点だけでなく、メンテナンスと清掃の削減による潜在的なコスト削減にもつながります。本研究は、無機コアの吸湿性に関連する保管不安定性に関する懸念は、特に倉庫条件下での最大14日間の保管期間であれば、一般的な鋳造工場の慣行の下で管理可能であることを示しています。
研究の限界: 本研究では、使用された有機および無機バインダーシステムの正確な組成が機密情報であるため、限界があることを認識しています。さらに、鋳造工場の倉庫条件下での14日を超える無機コアの長期保管安定性については、広範囲には調査されていません。
7. 今後のフォローアップ研究:
今後のフォローアップ研究の方向性: 今後の研究では、固有の耐湿性を高めるために、特定の添加剤を組み込むなどして、無機バインダーの組成をさらに最適化することに焦点を当てる必要があります。
さらなる探求が必要な分野: より広範な鋳造条件における無機コアの長期保管挙動を調査し、重力ダイカスト以外の様々なアルミニウム合金および鋳造プロセスでの性能を評価することが推奨されます。無機コアに関連する鋳型メンテナンスと清掃の削減による経済的利点を調査することも、将来の研究にとって価値のある分野となるでしょう。
8. 参考文献:
[1] F. Czerwinski, M. Mir, W. Kasprzak, Application of cores and binders in metalcasting. Int. J. Cast Met. Res. 28, 129-139 (2015). https://doi.org/10.1179/1743133614Y.0000000140
[2] A. Kmita, C. Fischer, K. Hodor, M. Holtzer, A. Roczniak, Thermal decomposition of foundry resins: a determination of organic products by thermogravimetry-gas chromatography-mass spectrometry (TG–GC-MS). Arab. J. Chem. 11, 380–387 (2018). https://doi.org/10.1016/j.arabjc.2016.11.003
[3] S.M. Glowacki, C.R. Crandell, G.R. Cannon, F.S. Clobes, J.K. Voigt, R.C. Furness, J.C. McComb, B.A. Knight, Emissions studies at a test foundry using an advanced oxidation-clear water system. AFS Trans. 111, 579-598 (2003)
[4] Y. Wang, F.S. Cannon, M. Salama, J. Goudzwaard, J.C. Furness, Characterization of hydrocarbon emissions from green sand foundry core binders by analytical pyrolysis. Environ. Sci. Technol. 41, 7922–7927 (2007). https://doi.org/10.1021/es0716570
[5] S.M. Dobosz, K. Major-Gabryś, A. Grabarczyk, New materials in the production of moulding and core sands. Arch. Foundry Eng. 15, 25–28 (2015). https://doi.org/10.1515/afe-2015-0073
[6] R. Ramakrishnan, B. Griebel, W. Volk, D. Günther, J. Günther, 3D printing of inorganic sand moulds for casting applications. Adv. Mater. Res. 1018, 441-449 (2014)
[7] H. Polzin, Inorganic Binders: For Mould and Core Production in the Foundry (Schiele & Schön, Berlin, 2014).
[8] P. Lechner, G. Fuchs, C. Hartmann, F. Steinlehner, F. Ettemeyer, W. Volk, Acoustical and optical determination of mechanical properties of inorganically-bound foundry core materials. Materials (Basel) 13, 2531 (2020). https://doi.org/10.3390/ma13112531
[9] B.J. Stauder, H. Kerber, P. Schumacher, Foundry sand core property assessment by 3-point bending test evaluation. J. Mater. Process. Technol. 237, 188-196 (2016). https://doi.org/10.1016/j.jmatprotec.2016.06.010
[10] B. Grabowska, S. Żymankowska-Kumon, S. Cukrowicz, K. Kaczmarska, A. Bobrowski, B. Tyliszczak, Thermoanalytical tests (TG-DTG-DSC, Py-GC/MS) of foundry binders on the example of polymer composition of poly(acrylic acid)-sodium carboxymethylcellulose. J. Therm. Anal. Calorim. 138, 4427-4436 (2019). https://doi.org/10.1007/s10973-019-08883-5
[11] B.J. Stauder, D. Gruber, P. Schumacher, Specific fracture energy and de-agglomeration rate of silicate-bonded foundry sand cores. Prod. Eng. 12, 807-816 (2018). https://doi.org/10.1007/s11740-018-0854-8
[12] H. Bargaoui, F. Azzouz, D. Thibault, G. Cailletaud, Thermomechanical behavior of resin bonded foundry sand cores during casting. J. Mater. Process. Technol. 246, 30-41 (2017). https://doi.org/10.1016/j.jmatprotec.2017.03.002
[13] C. Menet, P. Reynaud, G. Fantozzi, D. Thibault, A. Laforêt, Thermomechanical properties and fracture of resin-bonded-sand cores – experimental study and application in aluminium foundry. EPJ Web Conf. 140, 08006 (2017). https://doi.org/10.1051/epjconf/201714008006
[14] P. Lechner, J. Stahl, F. Ettemeyer, B. Himmel, B. Tananau-Blumenschein, W. Volk, Fracture statistics for inorganically-bound core materials. Materials (Basel) 11, 2306 (2018). https://doi.org/10.3390/ma11112306
[15] J.T. Fox, F.S. Cannon, N.R. Brown, H. Huang, J.C. Furness, Comparison of a new, green foundry binder with conventional foundry binders. Int. J. Adhes. Adhes. 34, 38–45 (2012). https://doi.org/10.1016/j.ijadhadh.2011.11.011
[16] A. Bobrowski, S. Żymankowska-Kumon, K. Kaczmarska, D. Drożyński, B. Grabowska, Studies on the gases emission of moulding and core sands with an inorganic binder containing a relaxation additive. Arch. Foundry Eng. (2020). https://doi.org/10.24425/afe.2020.131296
[17] K. Major-Gabryś, Environmentally friendly foundry molding and core sands. J. Mater. Eng. Perform. 28, 3905–3911 (2019). https://doi.org/10.1007/s11665-019-03947-x
[18] M. Holtzer, R. Dańko, A. Kmita, D. Drożyński, M. Kubecki, M. Skrzyński, A. Roczniak, Environmental impact of the reclaimed sand addition to molding sand with furan and phenol-formaldehyde resin—a comparison. Materials (Basel) 13, 4395 (2020). https://doi.org/10.3390/ma13194395
[19] Y.S. Zhang, L. Xia, J. Huang, Study on a new inorganic binder for fabricating casting mold and core. Adv. Mater. Res. 287–290, 1603–1606 (2011)
[20] W. Liu, T. Wang, Y. Li, Y. Ren, W. Huo, Preparation of a new animal glue binder for foundry use. China Foundry. 13, 238–242 (2016). https://doi.org/10.1007/s41230-016-6029-3
[21] K. Major-Gabrys, A. Grabarczyk, M. Dobosz, Modification of foundry binders by biodegradable material. Arch. Foundry Eng. 18, 31-34 (2018). https://doi.org/10.24425/122498
[22] I. Vasková, L. Varga, I. Prass, V. Dargai, M. Conev, M. Hrubovčáková, M. Bartošová, B. Bul'ko, P. Demeter, Examination of behavior from selected foundry sands with alkali silicate-based inorganic binders. Metals (Basel) 10, 235 (2020). https://doi.org/10.3390/met10020235
[23] L. Song, W. Liu, F. Xin, Y. Li, Effect of silica fume on humidity resistance of sodium silicate binder for core-making process. Int. J. Met. 14, 977–986 (2020). https://doi.org/10.1007/s40962-019-00405-1
[24] L. Zaretskiy, Modified silicate binders new developments and applications. Int. J. Met. 10, 88–99 (2016). https://doi.org/10.1007/s40962-015-0005-3
[25] J. Weise, J. Hilbers, F. Handels, D. Lehmhus, M. Busse, M. Heuser, New core technology for light metal casting. Adv. Eng. Mater. 21, 1800608 (2019). https://doi.org/10.1002/adem.201800608
[26] L. Zaretskiy, Hydrous solid silicates in new foundry binders. Int. J. Met. 12, 275–291 (2018). https://doi.org/10.1007/s40962-017-0155-6
[27] T. Sivarupan, M. El Mansori, N. Coniglio, M. Dargusch, Effect of process parameters on flexure strength and gas permeability of 3D printed sand molds. J. Manuf. Process. 54, 420–437 (2020). https://doi.org/10.1016/j.jmapro.2020.02.043
[28] L. Song, W. Liu, Y. Li, F. Xin, Humidity-resistant inorganic binder for sand core making in foundry practice. China Foundry 16, 267–271 (2019). https://doi.org/10.1007/s41230-019-8169-8
[29] F. Liu, Z. Fan, X. Liu, H. Wang, J. He, Research on humidity resistance of sodium silicate sand hardened by twice microwave heating process. Mater. Manuf. Process. 29, 184–187 (2014). https://doi.org/10.1080/10426914.2013.872260
[30] F. Liu, Z. Fan, X. Liu, Y. Huang, P. Jiang, Effect of surface coating strengthening on humidity resistance of sodium silicate bonded sand cured by microwave heating. Mater. Manuf. Process. 31, 1639–1642 (2016). https://doi.org/10.1080/10426914.2015.1117631
[31] Z. Chun-Xi, Recent advances in waterglass sand technologies. China Foundry 4, 13–17 (2007)
[32] J.F. Allen, F.S. Cannon, C. Nieto-Delgado, R.C. Voigt, J.T. Fox, J. Lamonski, J.D. Kirby, Full-scale air emissions monitoring and casting quality demonstration of a hybrid hydrolyzed collagen-alkali silicate core binder. Int. J. Met. 10, 172–189 (2016). https://doi.org/10.1007/s40962-016-0021-y
[33] J.T. Fox, J.F. Allen, F.S. Cannon, C.C. Cash, R.C. Voigt, J.A. DeVenne, J.C. Furness, J.S. Lamonski, P. Farver, Full-scale demonstration of a hybrid hydrolyzed collagen-alkali silicate core binder. Int. J. Met. 9, 51-61 (2015). https://doi.org/10.1007/BF03355623
[34] X.J. Li, Z.T. Fan, H.F. Wang, Strength and humidity resistance of sodium silicate sand by ester-microwave composite curing. Zhuzao/Foundry 61, 147–151 (2012)
[35] M. Stachowicz, K. Granat, Long-term effects of relative humidity on properties of microwave hardened moulding sand with sodium silicate. Arch. Foundry Eng. (2017). https://doi.org/10.1515/afe-2017-0104
[36] C. Lustig, M. Baldy, E. Müller, M.L. Reinold, S.M. Anderten, M. Schweinefuß, R. Vargovic, Method for producing a moulding material mixture and a moulded body thereof in the casting industry and kit for use in this method. US 2020/0130049 A1, (2020)
[37] T. Pabel, C. Kneißl, P. Schumacher, J. Brotzki, J. Müller, Improved properties of aluminium cast parts through the use of inorganic cores. Foundry Trade J. Int. 186, 257-261 (2012)
[38] N. Ünlü, A. Odabaş, Development and evaluation of a new eco-friendly sodium silicate-based binder system. Int. J. Met. 12, 765–771 (2018). https://doi.org/10.1007/s40962-018-0210-y
[39] K. Lochte, The inorganic binder system properties and experience. Cast. Plant Technol. Int. 21(32), 6 (2005)
[40] J. Peng, X. Tang, J. He, D. Xu, Effect of heat treatment on microstructure and tensile properties of A356 alloys. Trans. Nonferrous Met. Soc. China 21, 1950–1956 (2011). https://doi.org/10.1016/S1003-6326(11)60955-2
[41] J. Pezda, A. Jarco, Effect of T6 heat treatment parameters on technological quality of the AlSi7Mg alloy. Arch. Foundry Eng. 16, 95–100 (2016). https://doi.org/10.1515/afe-2016-0091
[42] J. Pezda, Influence of heat treatment parameters on the mechanical properties of hypoeutectic al-si-mg alloy. Metalurgija. 53, 221–224 (2014)
[43] F. Xin, W. Liu, L. Song, Y. Li, Modification of inorganic binder used for sand core-making in foundry practice. China Foundry 17, 341–346 (2020). https://doi.org/10.1007/s41230-020-0018-2
[44] P. Jelínek, H. Polzin, R. Škuta, Utilization of physical dehydradion for hardening of cores bonded with colloidal solutions of alkaline silicates. Acta Metall. Slovaca. 10, 10–23 (2004)
[45] R. Krishnaraj, Control of pollution emitted by foundries. Environ. Chem. Lett. 13, 149–156 (2015). https://doi.org/10.1007/s10311-015-0500-z
[46] D.K. Ghosh, Comparison of molding sand technology between alphaset (ApNB) and furan (FNB). Arch. Foundry Eng. (2019). https://doi.org/10.24425/afe.2019.129623
9. 著作権:
この資料は、A. Fortini, M. Merlin, G. Raminellaの論文「重力ダイカストAl合金部品における有機および無機コアバインダーの比較分析」に基づいています。
論文ソース: https://doi.org/10.1007/s40962-021-00628-1
この資料は上記の論文に基づいて要約されたものであり、商業目的での無断使用は禁止されています。
Copyright © 2025 CASTMAN. All rights reserved.