1. 概要:
- タイトル: 部分圧搾および真空ダイカストプロセスの実現可能性に関する研究
- 著者: E.S. Kim、K.H. Lee、Y.H. Moon
- 出版年: 2000年
- 掲載誌: Journal of Materials Processing Technology
- キーワード: 部分圧搾真空ダイカスト、過共晶Al-Si合金、圧搾圧力、プランジャーストローク、注入圧力、注入速度
2. 研究背景:
軽量材料の需要、機能性と品質の向上、環境保護への要請の高まりから、アルミニウム合金の製造はますます重要になっています[1-3]。ダイカストは、短いサイクルタイムと高精度な鋳造物を提供しますが、高速注入による空気の混入が原因で欠陥が発生する可能性があります。高圧ダイカスト、ACCURADプロセス[4]、無孔隙ダイカスト[5]、無ガス真空ダイカスト[6]、スクイズ鋳造[7]などの既存の方法には、生産性と品質のバランスにおいてそれぞれ限界があります。本研究はこのような限界に対処することを目的としています。
3. 研究目的と研究課題:
- 目的:優れた機械的特性を備えた、欠陥のない鋳造物を製造するための、部分圧搾および真空ダイカストプロセスの実現可能性を調査する。
- 主要な研究課題:圧搾と真空の効果の組み合わせは、ダイカスト製品の欠陥と機械的特性にどのような影響を与えるか?
- 仮説:注入前の真空効果と注入後の圧搾効果の組み合わせにより、微細な針状共晶と共晶前シリコンの均一な分布を通じて、欠陥のないダイカスト製品と優れた機械的特性が得られる。
4. 研究方法:
- 研究設計:過共晶Al-15%Si合金を使用して反応軸支持体を製造する試験ダイカストプロセスを産業的に実施しました。
- データ収集:プランジャー注入システムを真空装置に取り付けて、圧搾と真空の効果を組み合わせました。従来のダイカスト(CD)、圧搾ダイカスト(SD)、真空ダイカスト(VD)、提案された部分圧搾真空ダイカスト(SVD)プロセスを比較しました。
- 分析方法:鋳造品の断面を検査して欠陥を分析しました。比重測定により緻密化度を評価しました。引張試験により機械的特性を測定しました。微細組織分析を実施しました。
- 対象と範囲:過共晶Al-15%Si合金を用いた反応軸支持体のダイカストプロセスに焦点を当てました。
5. 主要な研究結果:
- 重要な発見:SVDプロセスは、CD、SD、VDプロセスと比較して、欠陥が大幅に減少し、優れた機械的特性を示しました。圧搾圧力と時間遅れは緻密化に大きな影響を与え、最適な範囲が特定されました。
- 定量的/定性的結果:CDとSDでは多量の空隙が見られました(図4a、b)。VDでは収縮欠陥が発生しました(図4c)。SVDではほぼ欠陥のない鋳造物が得られました(図4d)。最適な緻密化(2.736 g/cm³)は、2000 kg/cm²の圧搾圧力と1.0秒の時間遅れで得られました(図5)。SVDは、最高の引張強度(24.92 kg/cm²)と伸び(0.26%)を示しました(表3)。微細組織分析では、SVDにおいて微細な針状共晶と共晶前シリコンが均一に分布していることがわかりました(図8)。
- データ解釈:真空処理による空気の除去と圧搾圧力による収縮の補償により、欠陥が減少しました。均一な微細組織が優れた機械的特性をもたらしました。
- Figure List:
- Fig. 1: Schematic drawing of the partial squeeze and vacuum die casting machinery.
- Fig. 2: Schematic drawing of the injection curve.
- Fig. 3: Photographs of the die cast trial product of a reaction shaft support.
- Fig. 4: Photographs showing sectional views of the reaction shaft support: (a) CD; (b) SD; (c) VD; and (d) SVD.
- Fig. 5: The effect of the squeeze pressure and time lag on the specific gravity of cast products.
- Fig. 6: The relationship between plunger stroke and squeeze pressure.
- Fig. 7: Local density variation at a squeeze pressure 2000 kg/cm ² and a time lag of: (a) 0.5 s; (b) 1.0 s; (c) 1.5 s; and (d) 2.0 s.
- Fig. 8: Typical microstructure at various squeeze pressures (time lag=1.0 s): (a) 1500 kg/cm ²; (b) 2000 kg/cm ²; (c) 2500 kg/cm ²; and (d) 3000 kg/cm ².
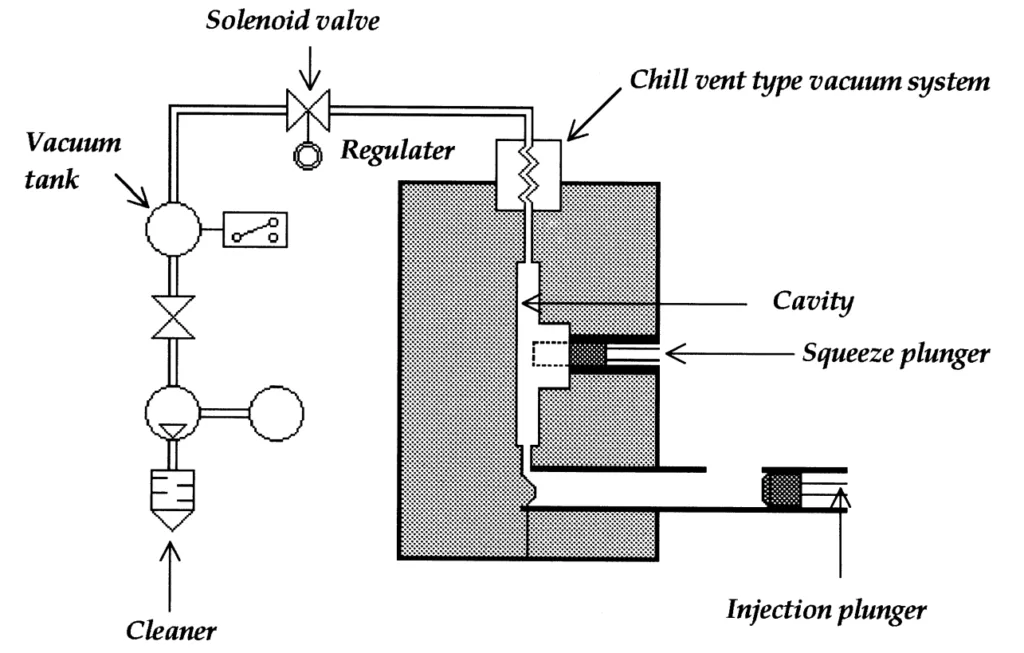
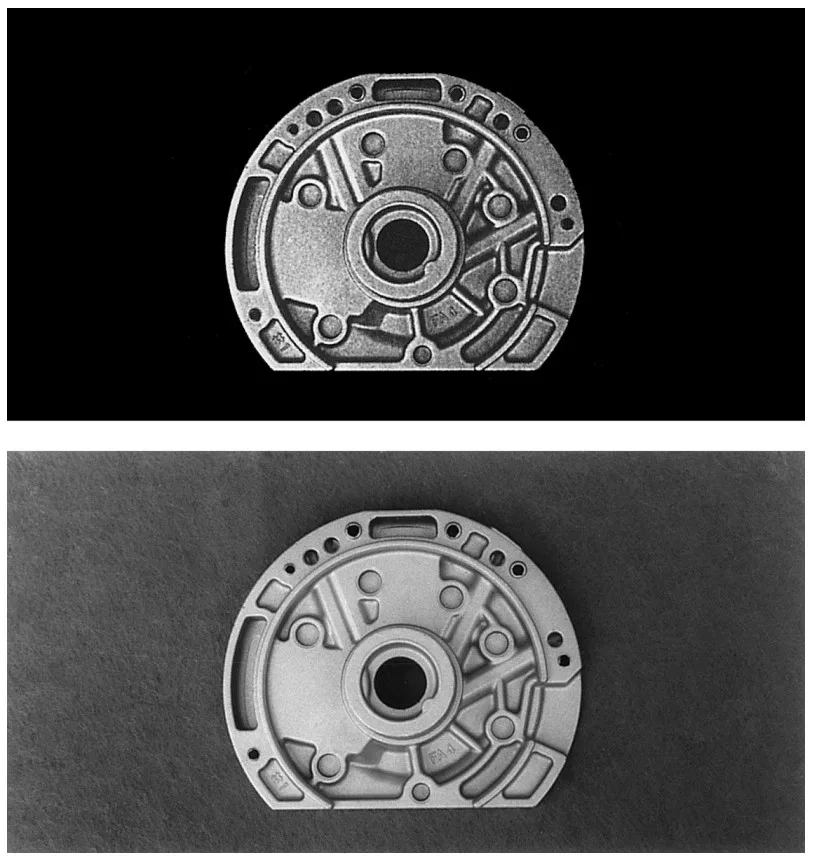
6. 結論と考察:
部分圧搾と真空ダイカストのハイブリッド技術は、優れた機械的特性を備えた欠陥のない鋳造物を製造しました。真空効果と圧搾効果の組み合わせは、空隙と収縮を効果的に防止しました。最適なプロセスパラメータ(圧搾圧力と時間遅れ)が特定されました。この研究は、高品質なダイカスト製品の製造に関する実用的な示唆を与えます。限界としては、特定の合金と製品形状に限定されている点が挙げられます。
7. 今後の研究:
さまざまな合金と製品形状に関する研究が必要です。圧搾圧力と時間遅れの最適化に関する追加の研究が必要です。プロセスパラメータ間の相互作用に関する更なる調査が必要です。
8. 参考文献の概要:
- [1] K. Fukizawa, H. Shiina, J. Soc. Auto. Eng. Jpn. 46 (5) (1992) 66.
- [2] D.O. Kennedy, Mod. Cast. 2 (1992) 34.
- [3] Metals Handbook, Vol. 15, 9th Edition, ASM, New York, 1988, p. 204.
- [4] L. Maclaren, Die Cast. 31 (1967) 7.
- [5] T. Kan, T. Uehara, Die Casting of Aluminum Alloy, Japan Light Metals Press Co., Japan, 1988, p. 438.
- [6] Technical History of Die Casting, Japan Die Casting Association, Light Metal Communication Co., Japan, 1995, p. 11.
- [7] R.F. Lynch, R.P. Olley, P.C.J. Gallagher, AFS Transactions Paper No. 75±122, 1975, p. 569.
- [8] I.J. Polmear, Light Alloys Ð Metallurgy of the Light Metals, Arnold, UK, 1981.
- [9] F. King, Aluminum and its Alloys, Wiley, New York, 1987.
著作権:
この要約は、E.S. Kim、K.H. Lee、Y.H. Moonによる研究論文「部分圧搾および真空ダイカストプロセスの実現可能性に関する研究」に基づいて作成されました。
商用目的での無断使用は禁止されています。
Copyright © 2025 CASTMAN. All rights reserved.