本紹介資料は、La Metallurgia Italiana誌に掲載された「Numerical and experimental analysis of a high pressure die casting Aluminum suspension cross beam for light commercial vehicles(軽量商用車用高圧ダイカストアルミニウムサスペンションクロスビームの数値解析と実験解析)」の論文の研究内容です。
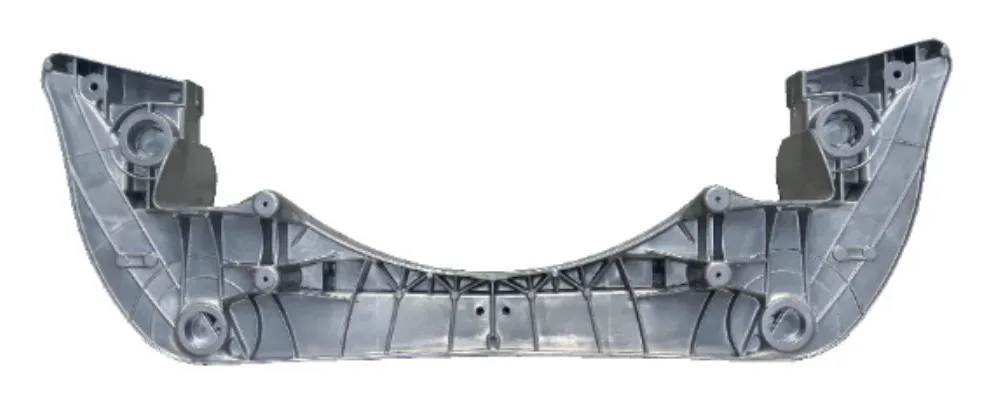
1. 概要:
- タイトル: 軽量商用車用高圧ダイカストアルミニウムサスペンションクロスビームの数値解析と実験解析 (Numerical and experimental analysis of a high pressure die casting Aluminum suspension cross beam for light commercial vehicles)
- 著者: S. Cecchel, D. Ferrario
- 出版年: 2016年
- 発表ジャーナル/学会: La Metallurgia Italiana
- キーワード: アルミニウム - 高圧ダイカスト - サスペンション - クロスビーム - 商用車 - 軽量化 - 自動車 (ALUMINUM - HIGH PRESSURE DIE CASTING - SUSPENSION - CROSS BEAM - COMMERCIAL VEHICLE - LIGHTWEIGHT - AUTOMOTIVE)
2. 要約
本論文の目的は、自動車、特に商用車およびバスの軽量化最適化を改善および深化させることです。具体的には、この研究の目的は、アルミニウム合金製の軽量商用車(LCV)用の、技術的に信頼性が高く、費用対効果の高い安全コンポーネントを開発することです。LCV用の独立懸架式フロントサスペンション用のさまざまなアルミニウムクロスビームソリューションが分析されており、従来の溶接鋼板構造と比較して約40/50%の軽量化目標が設定されています。さらに、耐食性の向上、塗装やカチオン電着が不要、リサイクル性や寿命末期の残存価値などの追加の環境上の利点も考慮する必要があります。このプロジェクトの目標は、次の方法によって達成されました。さまざまな軽量化ソリューションの技術的および経済的調査と最良事例の選択。構造FEAおよび鋳造プロセスシミュレーション、ゆりかごから墓場までのライフサイクルアセスメント(ここでは説明しません)、プロトタイプ実現、予備実験相関による、選択されたソリューションの改善。
3. 研究背景:
研究テーマの背景:
車両重量の削減は、燃料消費量と環境排出量を削減することにより、自動車の二酸化炭素排出量を削減するための注目すべき方法です。さらに、軽量化は出力重量比と乗客の安全性を向上させ、ペイロードの増加を可能にします[1]。
先行研究の現状:
近年、自動車の軽量化設計は飛躍的に増加しています。しかし、「鋼」と「鉄」の使用は、特に安全関連コンポーネントの場合、商用車やバスでは依然として優勢です[2]。商用車用サスペンションクロスビームは、通常、板金部品または鋼管を溶接し、腐食を防ぐために保護されています。主な技術トレンドは、特定の自動車分野に応じて、高張力鋼、軽合金、複合材料などの代替材料に注目しています。
研究の必要性:
軽合金や複合材料が最良の軽量化メリットを提供する場合でも、これらの技術のLCVへの使用は、破断時の応力と剛性が高く、コスト制限があるため、制限されています。特に、現在知られている技術水準では、アルミニウム製のサスペンションクロスビームは、これらの範囲の車両では開発されていません。
4. 研究目的と研究課題:
研究目的:
アルミニウム合金製の軽量商用車(LCV)用の、技術的に信頼性が高く、費用対効果の高い安全関連サスペンションコンポーネントを開発することにより、これらの技術水準を克服すること。完全なサスペンションアセンブリの予備ベンチマークを実施して、より高い軽量化メリットを提供する要素を評価し、サスペンションクロスビーム要素の研究対象を概説します。
主要な研究:
これらの限界を克服するために、本研究では、研究対象コンポーネントの形状と製造技術を、機械的特性を最適化し、使用材料を削減することによって完全に考案しました。
5. 研究方法
さまざまなサスペンションクロスビーム軽量化ソリューションが開発されました(Fig. 1)。各ソリューションについて、材料、プロセス、技術、ビジネスケースを詳細に分析し、予備有限要素解析(構造MSC/MarcMentatおよびプロセスESI PROCAST)を実施しました。主要な荷重設定条件の力を決定するために、サスペンションシステムの弾性運動学的多体モデルを定義し、MSC/AdamsCarで実行しました。これらの荷重は、MSC Marc/Mentatで実行された構造FEAの入力として使用され、結果はESI/PROCASTプロセスFEAの出力と比較されました。金型が製造され、いくつかのプロトタイプが鋳造されました(Fig. 3)。設計中に実施された有限要素解析は、金型製造(局所冷却、スクイズ、チルベント、ゲートインジェクションなど)および初期プロセスパラメータの定義に役立ちました。鋳造品は、適切なX線装置と3Dスキャナー装置を使用して分析され、巨視的欠陥(多孔性および変形)が特定されました。
6. 主要な研究結果:
主要な研究結果と提示されたデータ分析:
さまざまな解析結果を比較した結果、最も軽量で経済的な可能性のあるソリューションは高圧ダイカストアルミニウムであるという結論に至りました。このソリューションの実現可能性は、適切な材料を使用し、導入部で説明した構造的限界を克服できる新しい設計コンセプトによって達成されました。生産用に選択された合金はAlSi9MgMn(Tab. 1)であり、鋳放し状態で高い機械的特性を保証します(Tab.1)。コンポーネントの全長にわたってスライダーを追加することによって得られる完全中空構造(Fig. 2)。スライダーはアンダーカットを回避するために広く使用されている技術ですが、特にLCVの分野では、中空構造コンポーネントの製造には適用されません。このソリューションにより、主要な垂直荷重の方向で、コンポーネントの剛性が鋼のベースラインと比較して約40%向上します。
このコンポーネントの製造には、高トン数(少なくとも3000 t)の真空機械が必要です。
一連のステップにより、サスペンションクロスビームの軽量化が向上しました(当初の35%から47%へ)。
X線結果は、FEMシミュレーション中にすでに評価された最も厚い部分にいくつかの多孔性があることを確認しました(Fig. 4)。
多孔性は最小限に抑えられ、正確なハードポイントアライメントが達成されました。


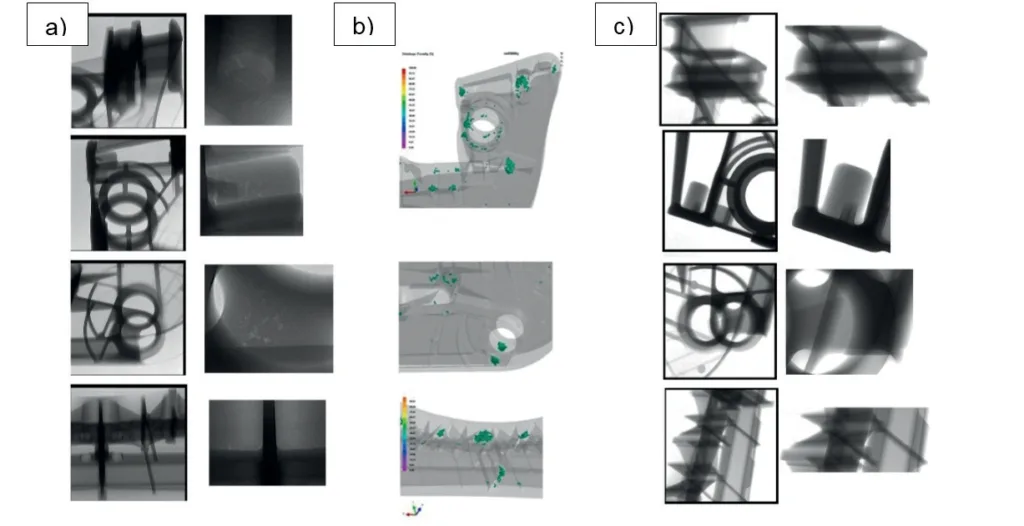
図表名リスト:
- Fig. 1 - クロスビーム:-1)HPDCアルミニウム、2)LPDCおよび押出アルミニウム、3)LPDCおよびCFRP、4)押出アルミニウム
- Tab. 1 - AlSi9MgMnの化学組成(左)[5]、AlSi9MgMnの機械的特性(右)[5]
- Fig. 2 - a)スライダーレイアウト b)クロスビーム中空長手方向断面 c)注目すべき中空断面
- Fig. 3 - 金型とプロトタイプ
- Fig. 4 - a)最初の実験活動のコンポーネントのX線、b)FEMシミュレーション、c)最終実験活動(プロセスパラメータの最適化)のコンポーネントのX線による多孔性の特定
7. 結論:
主要な調査結果の要約:
この論文は、アルミニウム合金製の軽量商用車(LCV)用の、技術的に信頼性が高く、費用対効果の高い安全コンポーネントを開発することにより、商用車の軽量化最適化を強化します。最良のソリューションは、高圧ダイカストアルミニウムコンポーネントです。研究対象コンポーネントの形状と製造技術は、機械的特性を最適化し、使用材料を削減することによって完全に考案されました。設計は、構造およびプロセス有限要素解析のさらなる反復のおかげで強化されました。適切なコンポーネント抵抗は、一次AlSi9MgMn合金を選択し、従来の平面または「U」字型の高圧ダイカストを、コンポーネントの全長にわたってスライダーを追加することによって得られる完全中空構造に置き換えることによって達成されました。
研究結果の要約。研究の学術的意義、研究の実用的意義
プロトタイプの製造は、鋳造品の寸法(約1260x450 mm)とスライダー(ほぼ部品と同じ)、および金型(部品の約2倍)が大きいため、高トン数(少なくとも3000 t)の真空機械で行われました。
いくつかの金型修正と適切なプロセスパラメータの慎重な反復選択のおかげで、多孔性は最小限に抑えられ、正確なハードポイントアライメントが達成されました。
8. 参考文献:
- [1] J. HIRSCH, Materials forum volume 28, (2004), p 15.
- [2] S.DAS, JOM, 8, (2000), p.41-44.
- [3] L. KALLIEN, T. WEIDLER, M. BECKER, International found-ry research, 4, (2014), p. 20-27.
- [4] R.MOSCHINI, R.MOLINA, XXXI Congresso tecnico di fon-deria ASSOFOND, (2012).
- [5] RHEINFELDEN, Leghe d'alluminio da pressocolata.
9. 著作権:
- この資料は、「S. Cecchel, D. Ferrario」による論文です:「Numerical and experimental analysis of a high pressure die casting Aluminum suspension cross beam for light commercial vehicles」に基づく。
- 論文出典:La Metallurgia Italiana - n. 6 2016
この資料は、上記の論文を紹介するために作成されたものであり、商業目的での無断使用を禁じます。Copyright © 2025 CASTMAN. All rights reserved.