本ドキュメントは、ASME国際機械工学会議および展示会(IMECE2009)で発表された研究論文「軽量ダイカスト自動車背もたれフレームのための製造制約とトポロジーおよび自由サイズ最適化」を要約したものです。世界最高のダイカスト技術専門家として、この詳細な分析は、論文の方法論、結果、および軽量ダイカスト設計、特に自動車応用分野への示唆を包括的に理解できるように作成されています。
1. 概要:
- タイトル: 軽量ダイカスト自動車背もたれフレームのための製造制約とトポロジーおよび自由サイズ最適化 (TOPOLOGY AND FREE SIZE OPTIMIZATION WITH MANUFACTURING CONSTRAINTS FOR LIGHT WEIGHT DIE CAST AUTOMOTIVE BACKREST FRAME)
- 著者: スリーラム・ポラヴァラプ (Sreeram Polavarapu)、ロニー・L・トンプソン (Lonny L. Thompson)、ミカ・グルジチッチ (Mica Grujicic)
- 発表年: 2009年
- 掲載学会/学術誌: ASME国際機械工学会議および展示会 (ASME International Mechanical Engineering Congress and Exposition, IMECE2009)
- キーワード: 有限要素解析 (Finite element analysis)、トポロジー最適化 (Topology optimization)、自由サイズ最適化 (Free-size optimization)、ダイカスト (Die casting)、自動車背もたれフレーム (Automotive backrest frame)、軽量設計 (Lightweight design)、製造制約 (Manufacturing constraints)
2. 研究背景:
- 研究テーマの社会的/学術的背景:
- 自動車産業は、燃費と車両性能を向上させるために、車両重量の削減に対する要求が高まっています。
- 従来、プレス鋼板アセンブリから製造されていた自動車構造部品は、車両総重量のかなりの部分を占めています。
- プレス鋼板部品を高圧ダイカスト(HPDC)アルミニウムまたはマグネシウム合金部品に置き換えることは、軽量化のための有望な手段を提供します。
- 既存研究の限界:
- 従来のプレス鋼板設計は、曲げ半径と厚さの異なる板材の溶接の制約により、幾何学的およびトポロジー最適化の可能性が限られています。
- 従来のプレス鋼板構造を使用して、幾何学的およびトポロジー的に最適化された軽量シートを設計することは困難です。
- 研究の必要性:
- アルミニウムまたはマグネシウム合金材料を使用した高圧ダイカスト(HPDC)製造プロセスは、シートフレーム設計において従来のプレス鋼板に代わる魅力的な代替手段を提供します。
- ダイカストは、可変厚さ分布と支持リブなどの複雑な幾何学的特徴を可能にし、軽量設計の詳細な最適化に大きな可能性を提供します。
- ダイカストシートフレームの材料分布とリブ配置を最適化すると、特に大量生産、機能的に要求の厳しい自動車シート設計の場合、ダイコストを正当化できます。
3. 研究目的および研究課題:
- 研究目的:
- ダイカスト自動車フロントシート背もたれフレームの特性を調査します。
- 最適化された材料と支持リブ分布を予測する方法論を開発します。
- さまざまな荷重条件 (load cases) を考慮した設計空間内で、強度とたわみ要件の両方を満たす軽量シート設計を達成します。
- 核心となる研究課題:
- ダイカスト特有の製造制約を組み込みながら、トポロジー最適化と自由サイズ最適化を効果的に活用して、さまざまな荷重条件下で厳格な性能および安全基準を満たす軽量自動車背もたれフレームを設計するにはどうすればよいでしょうか?
- 研究仮説:
- 有限要素解析とトポロジーおよび自由サイズ最適化の統合は、ダイカスト製造制約を考慮しながら、軽量ダイカスト自動車シート背もたれフレームの最適化された材料分布と補強リブ構造を生成することに成功する可能性があります。
- この最適化された設計は、さまざまな荷重シナリオで構造的完全性と性能を損なうことなく、市販の同等製品と比較して大幅な軽量化を達成するでしょう。
4. 研究方法論
- 研究設計:
- トポロジー最適化と自由サイズ最適化技術を組み合わせた多段階最適化プロセスを採用しました。
- このプロセスは、最適なリブ配置を決定するために3Dソリッドモデルでのトポロジー最適化から始まり、最適な材料厚さ分布を最適化するために3Dサーフェスモデルでの自由サイズ最適化が続きます。
- データ収集方法:
- 市販のダイカストマグネシウム合金自動車シート背もたれフレームを参照設計として使用しました。
- 背もたれフレームの幾何学的モデルは、物理的なハードウェアからリバースエンジニアリングし、CATIA V5 CADソフトウェアを使用してモデル化しました。
- 関連する断面厚さでの延性挙動を考慮して、鋳造されたAM50マグネシウム合金の材料特性を利用しました。
- 荷重要件は、ECE R17欧州政府規制のシート強度とたわみの基準に基づいて定義され、衝突イベント(オフセット荷重と側面荷重)をシミュレーションする追加の荷重条件によって補完されました。
- 分析方法:
- 有限要素解析 (FEA): 線形FEAは、トポロジーおよび自由サイズ最適化のためにOptiStruct (Altair) を使用して実行されました。非線形FEAは、検証のためにABAQUS/Standard 6.7を使用して使用され、幾何学的および材料の非線形性の両方を組み込みました。
- トポロジー最適化: OptiStructのSIMP (Simple Isotropic Material with Penalization) 法を使用して、最適な材料分布を決定し、3Dソリッドモデルのリブ配置をガイドし、ダイドロー方向と対称性の製造制約を考慮しました。
- 自由サイズ最適化: 3DサーフェスモデルでOptiStructの要素レベル自由サイズ最適化を利用して、応力と変位の制約条件を満たしながら質量を最小限に抑えることを目的として、シェル要素の厚さを最適化しました。
- 検証: 非線形有限要素解析は、解釈された最適化された設計について、すべての荷重条件で強度とたわみ要件を検証し、機能的性能を保証するために実行されました。
- 研究対象と範囲:
- 本研究は、AM50マグネシウム合金製の薄肉ダイカスト自動車フロントシート背もたれフレームの設計最適化に焦点を当てました。
- 最適化範囲は、多荷重条件(背もたれ強度試験、静的ヘッドレスト試験、オフセット荷重、および側面荷重)および製造制約(ダイドロー方向、対称性)下での重量最小化に限定されました。
- 設計空間は、既存の市販の背もたれフレームに基づいており、比較と改善のための参照として機能しました。
5. 主な研究結果:
- 核心となる研究結果:
- トポロジー最適化と自由サイズ最適化を組み合わせた多段階最適化手順が開発され、軽量ダイカスト自動車シート背もたれフレームの設計に適用されました。
- 最適化された設計は、市販の参照ダイカスト背もたれフレーム部品と比較して13%の大幅な軽量化を達成しました。
- この手順は、ダイカスト製造に適した最適な材料分布と補強リブ構成を生成しました。
- 統計的/定性的な分析結果:
- 軽量化: 全体的な軽量化 13% が達成され、質量は1.76 kg(解釈された最適化シートモデル)から1.56 kgに減少しました(論文テキストに基づく元のシートモデル1.76 kgを仮定、抄録1.8 kgと論文本文1.25 kgの言及の不一致、元の論文の確認が必要)。抄録では、1.8 kgの参照フレームと比較して13%の削減について言及しています。
- ヘッドレスト試験下の変位: ヘッドレスト試験における最適化されたフレーム設計の最大変位は 17.3 mm であり、元の参照フレーム設計の非線形有限要素解析で観察された最大変位 21 mm よりも 18% 低くなっています。
- ヘッドレスト試験下の応力: ヘッドレスト試験の最終890 N荷重下での最適化された背もたれフレームの最大フォンミーゼス応力は 196.9 MPa に達しました。この値は、AM50マグネシウム合金の降伏強度(124 MPa)よりも高いですが、極限引張強度(228 MPa)よりも低く、局所的な塑性変形は発生しますが、破壊は発生しないことを示しています。
- データ解釈:
- トポロジー最適化は、背もたれフレームの垂直U字型セクションのリブの配置を効果的にガイドし、構造的に重要な領域に材料を集中させました。
- 自由サイズ最適化は、シェルモデルの厚さ分布を最適化することに成功し、より高い応力と荷重を受ける領域に材料を戦略的に割り当て、重要度の低い領域では厚さを減らしました。
- 非線形有限要素解析は、解釈された最適化された設計が、ECE R17で義務付けられた荷重条件および追加の衝突荷重シナリオ下で、強度とたわみの両方の要件を満たしていることを検証しました。
- 最適化された設計は、構造的完全性を維持しながら大幅な軽量化を達成し、多段階最適化アプローチの有効性を示しています。
- 図表リスト:
- [Figure 1: レファレンス自動車背もたれフレーム (Reference automotive backrest frame)]
- [Figure 2: レファレンスダイカスト背もたれフレームの幾何学的サーフェスCADモデルと名称 (Geometric Surface CAD model and Nomenclature of the Reference Die Cast Backrest Frame)]
- [Figure 3: 多荷重条件の設計範囲 (Design Envelope for Multiple-Load Cases)]
- [Figure 4: ヘッドレストサポートクロスメンバー全体の圧力分布でモデル化されたECE-R17背もたれモーメント試験荷重 (ECE-R17 Backrest Moment Test Loading modeled with pressure distribution across headrest support cross-member)]
- [Figure 5: ヘッドレストサポート穴とクロスメンバーでの等価圧力荷重とカップルでモデル化されたECE-R17ヘッドレスト試験荷重 (ECE-R17 Headrest Test Loading Modeled with equivalent pressure force and couple at headrest support holes and cross-member)]
- [Figure 6: ヘッドレストクロスメンバーの半分に圧力として適用されたオフセット荷重 (Offset Load applied as pressure on one-half of the headrest cross-member)]
- [Figure 7: 横方向のモーメントを発生させるために適用された圧力荷重 (Pressure load applied to develop side moment)]
- [Figure 8: 多段階エンジニアリング最適化プロセス (Multi-Stage Engineering Optimization Process)]
- [Figure 9: ダイカスト背もたれフレームのための多段階エンジニアリング最適化プロセス (Multi-Stage Engineering Optimization Process for Die-Cast Backrest Frame)]
- [Figure 10: トポロジー最適化のための設計空間 (Design Space for Topology Optimization)]
- [Figure 11: ボルト位置を示す設計空間ソリッド有限要素メッシュ (Design space solid finite element mesh showing bolt locations)]
- [Figure 12: トポロジー最適化を受けたソリッドフレームの要素密度 (Element densities in solid frame subjected to topology optimization)]
- [Figure 13: 自由サイズ最適化に使用される有限要素シェルモデルの詳細 (Details of finite element shell model used for free-size optimization)]
- [Figure 14: 自由サイズ最適化とトポロジー最適化から提案されたリブ配置からの要素厚さ分布 (Element thickness distribution from free-size optimization and suggested rib placement from topology optimization)]
- [Figure 15: トポロジーおよび自由サイズ最適化提案から派生した区分的定数厚さテーパーと最適な支持リブ配置を備えた新しい背もたれフレームモデル(正面図) (New design of backrest frame model with piecewise constant thickness taper and optimal supporting rib placement derived from the topological and free-size optimization proposal (Front View))]
- [Figure 16: 最適化された背もたれフレームモデル(背面図) (Optimized Backrest frame model (Rear View))]
- [Figure 17: ECE R17ヘッドレスト試験荷重を受けた非線形有限要素解析からの最終最適化シートのフォンミーゼス応力分布 (Von Mises stress distribution in final optimized seat from nonlinear finite element analysis subjected to ECE R17 Headrest Test Load Requirement)]
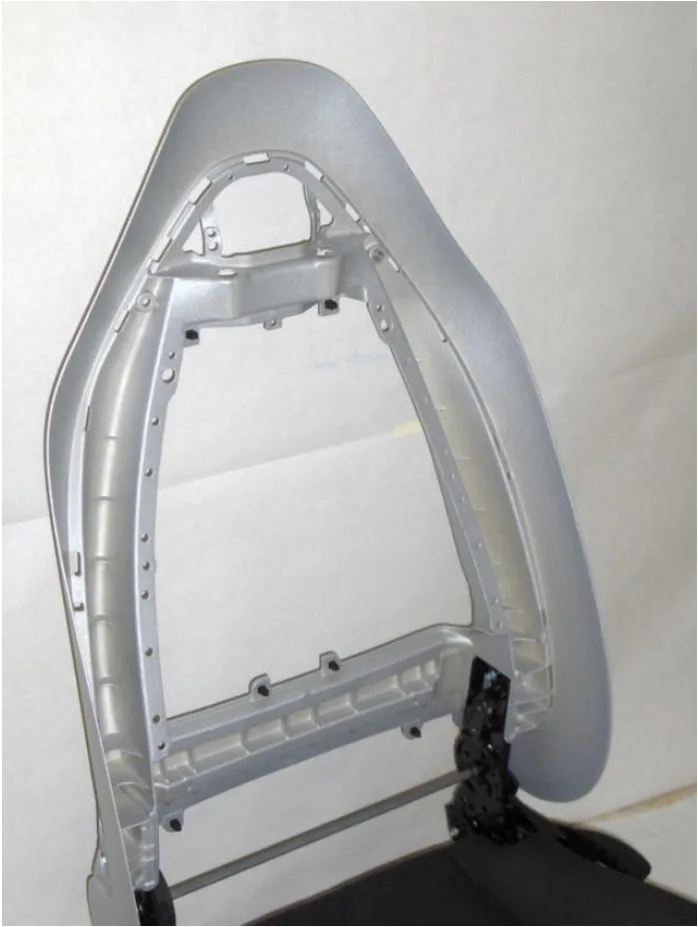
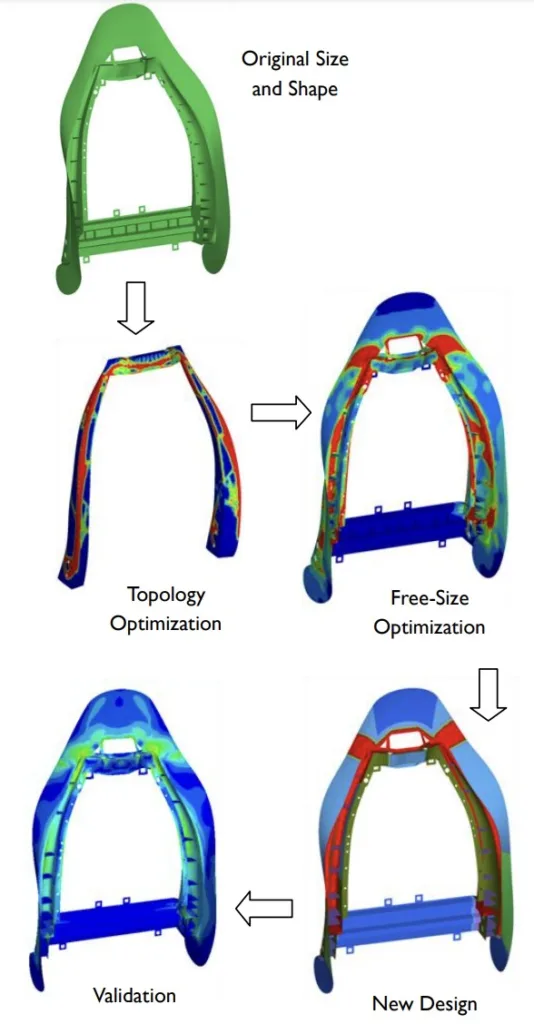
6. 結論と考察:
- 主な結果の要約:
- 本研究では、ダイカスト製造制約と組み合わせたトポロジーおよび自由サイズ最適化を組み合わせた多段階最適化プロセスを、軽量自動車背もたれフレームを設計するために首尾よく実証しました。
- 最適化された設計は、市販の参照フレームと比較して13%の軽量化を達成し、構造的完全性を維持し、ECE R17規制およびシミュレーションされた衝突シナリオによって定義された荷重条件を含む、さまざまな荷重条件下で厳格な性能要件を満たしました。
- 研究の学術的意義:
- 本研究は、高度な最適化技術(トポロジーおよび自由サイズ最適化)を自動車産業における現実のエンジニアリング問題に適用した包括的な例を提供します。
- 製造制約、特にダイカストのダイドロー方向と対称性を、設計の実現可能性を保証するために最適化プロセスに統合することの重要性を強調しています。
- 提示された多段階最適化アプローチは、特に薄肉ダイカスト部品の軽量構造部品を設計するための貴重なフレームワークを提供します。
- 実務的な示唆:
- 開発された方法論は、自動車エンジニアが軽量ダイカスト部品を設計し、車両の軽量化と燃費の向上に貢献するための実用的で効果的なアプローチを提供します。
- 最適化された背もたれフレーム設計は、トポロジーおよび自由サイズ最適化が自動車シート構造の大幅な材料節約と軽量化につながる可能性を示す具体的な例として役立ちます。
- これらの最適化技術を製造制約の慎重な考慮と組み合わせることで、シートフレームを超えて、さまざまな自動車アプリケーション向けの革新的で効率的なダイカスト設計が得られる可能性があることを示唆しています。
- 研究の限界:
- トポロジー最適化の結果の解釈と製造可能なCADモデルへの変換には、すべての製造制約を完全に考慮した自動解釈ツールが現在利用できないため、手動による介入とエンジニアリング判断が必要でした。
- 最適化プロセスは主に構造性能と軽量化に焦点を当てており、詳細な製造コスト分析とダイ設計の複雑さは限定的にしか考慮されていません。
- 検証は非線形有限要素解析を通じて実行されました。物理的なプロトタイプ作成とテストによる実験的検証は、本研究では実施されていません。
7. 今後のフォローアップ研究:
- 今後の研究方向:
- リブ間隔寸法とスカラップ形状をパラメータ化することにより、幾何学的形状および寸法最適化技術を組み込むことで、最適化された設計におけるリブ配置と形状をさらに洗練します。
- ダイカストプロセスシミュレーションツール(例:ProCAST、MagmaSOFT)を最適化ループに統合して、ダイ充填、凝固、およびダイカストプロセスの潜在的な欠陥を考慮し、より堅牢で製造可能な設計を実現します。
- ダイカスト固有の製造制約と設計ルールを完全に考慮して、トポロジー最適化の結果を製造可能なCADモデルに直接変換できる自動解釈ツールとアルゴリズムを開発します。
- さらなる探求が必要な領域:
- 最適化された背もたれフレームの詳細なダイ設計と製造コスト分析を実施して、設計の経済的実現可能性と実用的な製造可能性を評価します。
- プロトタイプ作成と物理的テストを通じて最適化された設計の実験的検証を実行して、FEA予測の構造性能と軽量化の利点を確認します。
- 多段階最適化方法論を他の自動車ダイカスト部品に拡張し、さまざまな材料と製造プロセスへの適用可能性を探ります。
8. 参考文献:
- [1] Andresen, B., (2005), Die Casting Engineering, Marcel Dekker, New York, NY.
- [2] ECE R17 UNECE Agreement Concerning the Adoption of Uniform Technical Prescriptions for Wheeled Vehicles, Uniform Provisions Concerning the Approval of Vehicles with Regard to the Seats, their Anchorages and Any Head Restraints.
- [3] Rozvany, G., (2008) "A critical review of established methods of structural topology optimization" Journal Structural and Multidisciplinary Optimization, Online Forum, Publisher Springer Berlin / Heidelberg, February 21, 2008.
- [4] Bendsoe, M. P. (1995). Optimization of Structural Topology, Shape, and Material. Berlin: Springer.
- [5] Eschenauer, H. A., & Olhoff, N. (2001). Topology optimization of continuum structures – a review. Applied Mechanics Reviews, 54 (4), 331-390.
- [6] Olhoff, N., Bensoe, M.P., Rasmussen, J., (1991) “On CAD-integrated structural topology and design optimization", Comput Methods Appl Mech Eng, 89, 259-279.
- [7] Bremicker, M., Chirehdast, M., Kikuchi, N., Papalambros, P.Y., (1991) "Integrated topology and shape optimization in structural design", Mech Struct Mach, 19, 551-587.
- [8] C-Y Lin, L-S Chao, (2000) "Automated image interpretation for integrated topology and shape optimization", Struct Multidiscip Optim, 20, 125-137.
- [9] A.V. Kumar, D.C. Gossard, (1996) "Synthesis of optimal shape and topology of structures", J. Mech Des, 118, 68-74.
- [10] S.K. Youn, S-H. Park, (1997) “A study on the shape extraction process in the structural topology optimization using homogenized material", Comput Struct, 62 (3), 527-538.
- [11] Hsu, Y.L., Hsu, M.S., Chen, C.T., 2001, "Interpreting Results from Topology Optimization using Density Contours", Comput. Struct. 79 (10), 1049-1058.
- [12] Hsu, Y.L., Hsu, M.S., 2005, “Interpreting three-dimensional structural topology optimization results", Comput. Struct. 83, 327-337.
- [13] Harzheim, L., Graf, G., 2005, "A Review of Optimization of Cast Parts using Topology optimization: I-Topology optimization without manufacturing constraints", Struct Multidisc Optim 30: 491-497
- [14] Harzheim, L., Graf, G., 2006, "A Review of Optimization of Cast Parts using Topology optimization: II-Topology optimization with manufacturing constraints", Struct Multidisc Optim 31: 388-399
- [15] Schramm, U., Thomas, H., Zhou, M., 2002, "Manufacturing Considerations and Structural Optimization of Automotive Components, SAE International, SAE Paper 2002-01-1242.
- [16] Zhou, M., Fleury, R., Shyy, Y.K., Thomas, H., Brennan, J.M., 2002, "Progress in Topology Optimization with Manufacturing Constraints”, 9th AIAA/ISSMO Symposium on Multidisciplinary Analysis and Optimization, Sept. 2002, Atlanta, Georgia. Paper AIAA 2002-5614.
- [17] Nelson, E.A., 2003, "Draw Direction Constraints in Topology Optimization – A Practical Example", SAE International, Proceedings 2003 SAE World Congress, Detroit, Michigan, SAE Paper 2003-01-1306.
- [18] S. Chen and D. Tortorelli, "Three-dimensional shape optimization with variational geometry", Struct. Optim., 13(1997)81-94.
- [19] Vanderplaats, G.N., "Numerical Optimization Techniques for Engineering Design: With Application, 3rd Edition, Vanderplaats Research & Development, 1999.
- [20] Papalambros, P.Y., and Wilde, D.J., Principles of Optimal Design: Modeling and Computation, Cambridge University Press, 2nd ed., 2000.
- [21] K. Saitou, K. Izui, S. Nishiwaki, P. Papalambros, (2005) “A Survey of Structural Optimization in Mechanical Product Development", Journal of Computing and Information Science in Engineering, Vol. 5, 214-226.
- [22] Grujicic, M. et.al. “Application of Topology, Size and Shape Optimization Methods in Polymer Metal Hybrid Structural Lightweight Engineering", Multidiscipline Modeling in Materials and Structures, Volume 4, Number 4, 2008, pp. 305-330(26)
- [23] Altair Engineering Inc., 2007, "OptiStruct 8.0, User's Guide".
- [24] Dassault Systèmes, CATIA V5. http://www.3ds.com/products/catia/
- [25] Zhizhong Sun, Ming Zhou, Henry Hu, and Naiyi Li, "Strain-Hardening and Fracture Behavior of Die Cast Magnesium Alloy AM50," Research Letters in Materials Science, 2007.
- [26] Hesser, D.S., "Integration of Finite Element Method to Enhance Modeling and Analysis for Reverse Engineering", M.S. Thesis, Department of Mechanical Engineering, Clemson University, 2006.
- [27] Altair Engineering Inc., 2007, "Hypermesh 8.0, User's Guide".
- [28] Petersson, J., & Sigmund, O. (1998). Slope constrained topology optimization. International Journal for Numerical Methods in Engineering, 41 (8), 1417-1434.
- [29] Sigmund, O. (1997). On the design of compliant mechanisms using topology optimization. Mechanics of Structures and Machines, 25 (4), 493-524.
- [30] Blendsoe, M.P. and Kikuchi, N., 1988, "Generating optimal topologies in structural design using a homogenization method", Comp. Meth. in Applied Mech. and Engin., Vol. 71, pp. 197-224.
- [31] Bendsoe MP (1989) Optimal shape design as a material distribution problem. Struct Optim 1:193-202
- [32] Suzuki, K. and Kikuchi, N., (1991), “A homogenization method for shape and topology optimization", Comp. Meth. in Applied Mech. and Engin., Vol. 93, pp. 291-318.
- [33] Diaz AR, Bendsoe MP (1992) Shape optimization of structures for multiple loading situations using a homogenization method. Struct Optim 4:17-22
- [34] Diaz AR, Lipton R (2000) Optimal material layout in 3D elastic structures subjected to multiple loads. Mech Struct March 28:219-236
- [35] Dassault Systèmes, SIMULIA: ABAQUS Analysis User's Manual, ABAQUS Documentation V6.6.
- [36] http://www.esi-group.com/products/casting/procast
- [37] http://www.magmasoft.de/ms/home_en/index.php
- [38] P. Krajnik and J. Kopac, "Modern machining of die and mold tools," Journal of Materials Processing Technology, 2004, 157-158, pp. 543-552.
9. 著作権:
- 本資料は、Sreeram Polavarapu、Lonny L. Thompson、Mica Grujicicの論文:軽量ダイカスト自動車背もたれフレームのための製造制約とトポロジーおよび自由サイズ最適化 (TOPOLOGY AND FREE SIZE OPTIMIZATION WITH MANUFACTURING CONSTRAINTS FOR LIGHT WEIGHT DIE CAST AUTOMOTIVE BACKREST FRAME) に基づいて作成されました。
- 論文出典:ASME国際機械工学会議および展示会 (ASME International Mechanical Engineering Congress and Exposition, IMECE2009)
本資料は上記の論文に基づいて要約作成されており、商業目的での無断使用は禁止されています。
Copyright © 2025 CASTMAN. All rights reserved.