本論文概要は、学術誌「CHINA FOUNDRY」に掲載された論文「超大型アルミニウム形状鋳造:機会と課題」に基づいて作成されました。
1. 概要:
- タイトル:超大型アルミニウム形状鋳造:機会と課題
- 著者:Qi-gui Wang, Andy Wang, Jason Coryell
- 発行年:2024年
- 発行ジャーナル/学会:CHINA FOUNDRY
- キーワード:超大型鋳造、アルミニウム、軽量化、品質、微細組織、材料特性
![Fig. 1: Growth of aluminum in North American light vehicle [2]](https://castman.co.kr/wp-content/uploads/image-609-png.webp)
2. 研究背景:
研究テーマの背景:
特に電気自動車における自動車の軽量化の要求の高まりにより、軽量アルミニウム形状鋳造の使用が急増しています。これらの鋳造品は、車両重量を削減し、内燃機関の燃料効率を向上させ、電気自動車のバッテリーエネルギー使用量を改善するために不可欠です。アルミニウム形状鋳造は、ニアネットシェイプ能力、高い強度対重量比、設計の柔軟性、および費用対効果の組み合わせを提供し、自動車用途にとって魅力的です。
既存研究の現状:
歴史的に、アルミニウム形状鋳造は、エンジンブロックやトランスミッションハウジングなどのパワートレイン部品に主に利用されており、二次合金である319やA380などの合金を使用していました。しかし、その用途は、車両のボディおよびシャーシ部品、特に高い延性のために一次アルミニウム合金が好まれるバッテリー式電気自動車(BEV)にまで拡大しています。超大型アルミニウム形状鋳造の製造には、高圧ダイカスト(HPDC)と低圧砂型鋳造(LPSC)の両方が採用されています。アルミニウム形状鋳造の最近の進歩は、参考文献[1, 3-4]に文書化されています。Al-Si-Mg合金およびその変形合金は、鋳造性、耐食性、および強度対重量比のために広く使用されています。
研究の必要性:
超大型シングルピース鋳造、別名メガキャストまたはギガキャストを使用した、よりシンプルな車両ボディ設計へのトレンドは、新たな課題を提示しています。これらの大型鋳造品は、部品点数と組立の複雑さを軽減する一方で、品質管理と性能予測に複雑さを加えています。変化する肉厚、増加した「ホットスポット」、より長い金属流動距離、および収縮空孔、巻き込み空気、酸化物、コールドシャット、およびミスランなどの潜在的な欠陥に関連する要因により、超大型アルミニウム鋳造の品質、微細組織、および材料特性に影響を与える要因をより深く理解する必要があります。
3. 研究目的と研究課題:
研究目的:
本論文は、超大型アルミニウム形状鋳造の品質、微細組織、および材料特性に影響を与える主要な要因を批判的に検討することを目的としています。また、鋳造品質と性能を向上させるための高度な技術を紹介し、仮想鋳造ツールを使用して高完全性鋳造の堅牢な設計と開発を実証することを目的としています。
主要な研究課題:
- 超大型アルミニウム鋳造の品質、微細組織、および機械的特性に影響を与える要因の評価。
- 鋳造品質と性能を向上させるための高度な技術の考察。
- 仮想鋳造ツールを使用した堅牢な設計と開発の実証。
- 超大型アルミニウム形状鋳造の冶金学的分析および機械的特性評価。
- 課題の強調と堅牢な設計および製造の改善のための提案。
研究仮説:
本論文は、研究仮説を明示的に述べていませんが、以下を暗示しています。
- 超大型アルミニウム形状鋳造の品質と性能は、鋳造プロセス、合金選択、および設計に関連する要因によって大きく影響を受けます。
- 高度な技術と仮想鋳造ツールは、高完全性超大型アルミニウム鋳造の製造に関連する課題に効果的に対処できます。
- 溶湯清浄度、ゲートシステム設計、金型表面処理、および鋳造プロセスパラメータなどの要因を理解し、制御することは、望ましい品質と特性を達成するために非常に重要です。
4. 研究方法
研究デザイン:
本論文はレビュー論文であり、超大型アルミニウム形状鋳造における既存の知識と最近の開発動向をまとめることに焦点を当てています。機会と課題を説明するために、既存の文献および業界慣行からの応用事例、冶金学的分析、および機械的特性評価を使用しています。
データ収集方法:
本論文は主に文献レビュー、業界レポート、および事例研究に依存しています。データは、アルミニウム鋳造、特に自動車用途における超大型鋳造に関連する公開された論文、特許、会議議事録、および業界出版物から収集されます。
分析方法:
分析は記述的かつ定性的であり、超大型アルミニウム形状鋳造に関連する主要な要因、課題、および機会を特定し、考察することに焦点を当てています。さまざまな情報源からの情報を要約および統合して、トピックに関する包括的な概要を提供します。また、引張特性の変化や気孔率の観察例を用いて、その主張を裏付けています。
研究対象と範囲:
本論文の範囲は、自動車用途、特に電気自動車の構造部品に使用される超大型アルミニウム形状鋳造に焦点を当てています。本論文では、合金選択や鋳造プロセスから設計上の考慮事項や持続可能性まで、さまざまな側面について考察しています。
5. 主な研究結果:
主要な研究結果:
- 超大型アルミニウム鋳造の機会: 超大型アルミニウム鋳造は、部品点数の削減(60点以上の部品を代替)、金型コストの削減(40%)、エネルギーの節約(30%)、質量の削減(30%)、およびリードタイムの短縮などの利点を提供します。また、統合バッテリーケースなどのより広範な用途も可能にします(表1)。
- 製造上の課題: 高品質の超大型アルミニウム鋳造の製造は、サイズ、金型の複雑さ、熱管理、および欠陥の発生しやすさ(収縮空孔、酸化物、コールドシャット、ミスラン)のために困難です。大型鋳造品内部の材料特性は均一ではない可能性があります(図5)。寸法安定性と修理可能性も重要な課題です。
- 鋳造品質に影響を与える要因:
- 鋳造アルミニウム合金: 〜7%Si合金(例:C611、Aural 5)は、バランスの取れた鋳造性と引張伸びのためにHPDCメガキャストに使用されます。Al-Si-Mg合金中のCu含有量は、気孔率を増加させ、耐食性を低下させる有害な影響を与える可能性があります(図9、図11)。
- 溶湯清浄度: 清浄な溶湯は非常に重要です。スクラップチャージを予熱し、フラックスコーティングすると、酸化物と汚染を減らすことができます(図12、図13)。
- ゲートシステム設計: 乱流と巻き込み空気を最小限に抑えるには、最適なゲートシステム設計が不可欠です(図14、図15)。
- 金型表面処理: 適切な金型表面処理は、表面仕上げと鋳造スキン層の品質に影響を与えます。
- 鋳造プロセス: 金型温度(理想的には溶湯注入温度の〜1/3)、注入温度(液相線温度より50〜100℃高い)、注入速度、およびショットプロファイル(図17、図18)を含む最適な鋳造プロセス制御は、品質にとって不可欠です。
データ解釈:
- 図1: 北米の軽自動車におけるアルミニウム使用量の増加を示しており、鋳造が主要な用途であることを強調しています。
- 図2および3: テスラモデルYおよびキャデラックセレスティックにおける超大型アルミニウム鋳造の事例を示し、業界での採用を実証しています。
- 図4: ギガアルミニウム鋳造で観察された巨視的な収縮空孔を描写し、課題を強調しています。
- 図5: ギガ鋳造品内部の引張特性の変化を示し、不均一性を示しています。
- 図6および7: 持続可能性におけるアルミニウムのパラドックスと、リサイクルアルミニウムのCO2排出量削減の可能性を示しています。
- 図8: 超大型アルミニウム鋳造に使用される合金の計算された凝固順序を示し、相変態を示しています。
- 図9: Al-Si-Mg合金におけるCu含有量と気孔率の関係を示し、Cuの負の影響を実証しています。
- 図10: CuおよびSi含有量の関数として予測された割れ感受性係数(CSC)を示しています。
- 図11: Cu、Mg、Fe、およびSrが耐食性に及ぼす影響を示し、Cuの有害な影響を強調しています。
- 図12および13: 溶融塩と界面張力を使用してアルミニウム酸化物剥離プロセスを概略的に説明しています。
- 図14および15: ゲートシステム設計とその巻き込み空気に及ぼす影響を示し、設計の重要性を強調しています。
- 図16: 適切な金型表面処理による表面欠陥の除去を実証しています。
- 図17および18: ショットプロファイルとその巻き込み空気に及ぼす影響を示し、プロセスパラメータの最適化を強調しています。
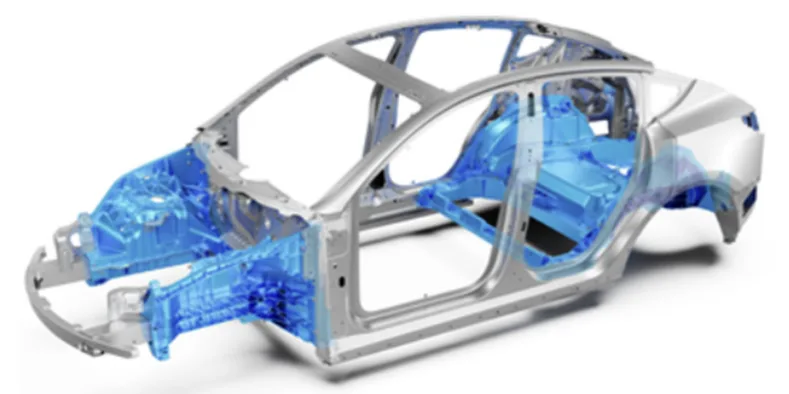
![Fig. 3: Six mega aluminum shape castings forming the entire lower body structure for Cadillac Celestiq vehicles [13]](https://castman.co.kr/wp-content/uploads/Six-mega-aluminum-shape-castings-forming-the-entire-lower-body-structure-for-Cadillac-Celestiq-vehicles.png)
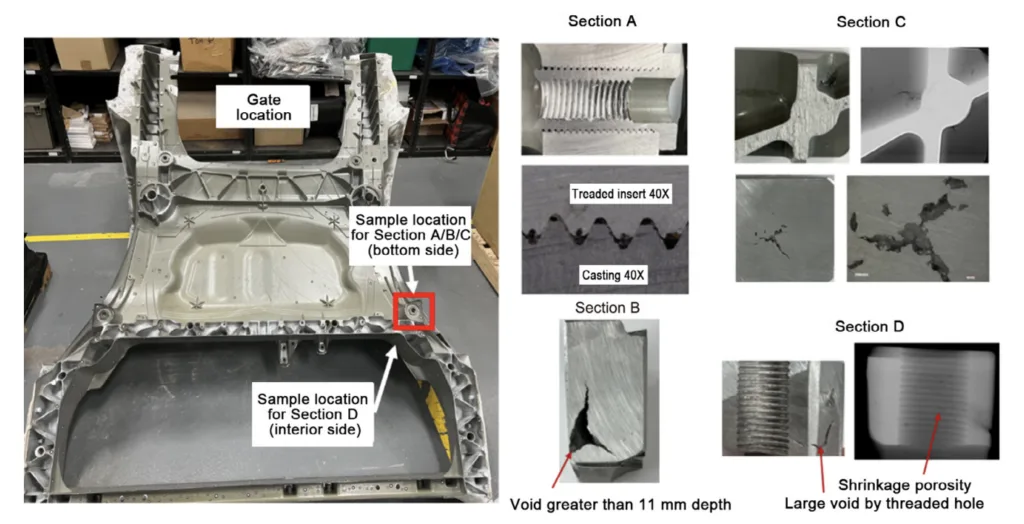
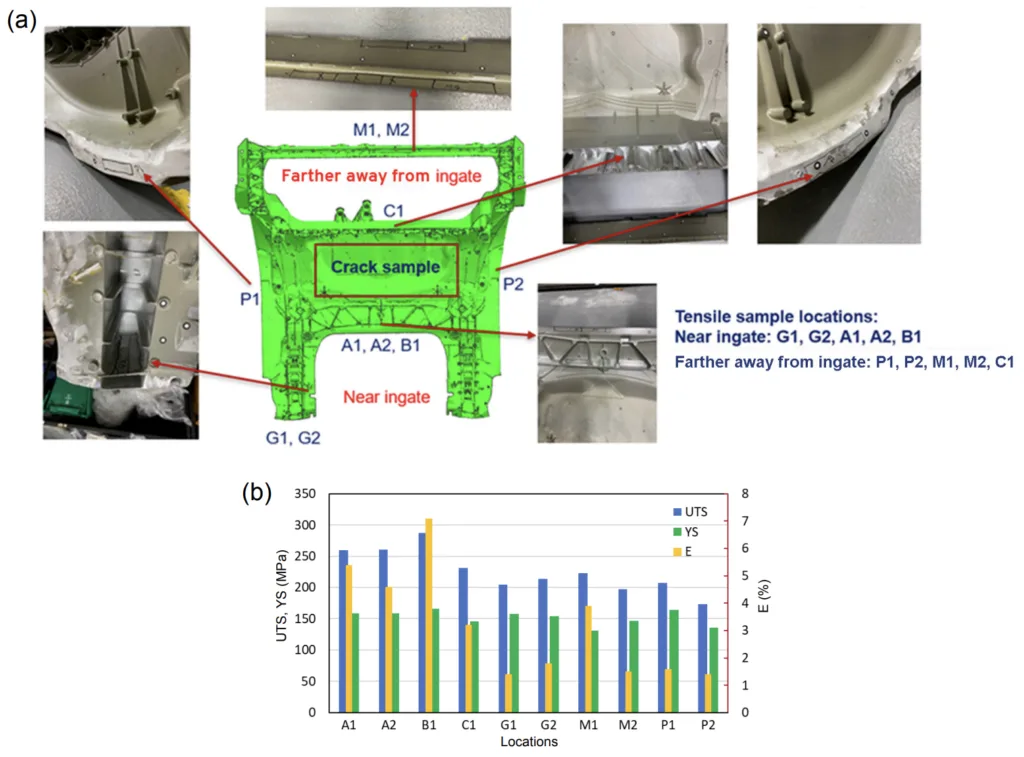
![Fig. 6: Aluminum paradox from sustainability aspect [19]](https://castman.co.kr/wp-content/uploads/image-613-1024x381.webp)
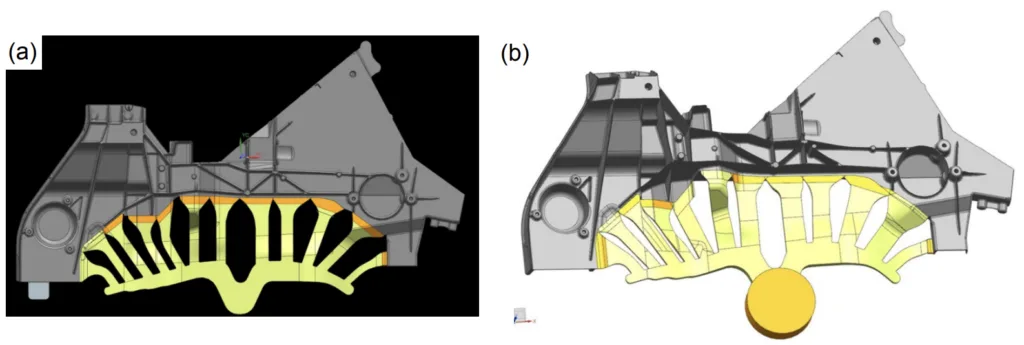
図のリスト:
- Fig. 1: Growth of aluminum in North American light vehicle [2]
- Fig. 2: A Tesla Model Y giga-casting [10]
- Fig. 3: Six mega aluminum shape castings forming the entire lower body structure for Cadillac Celestiq vehicles [13]
- Fig. 4: Large macro shrinkage porosity observed in a giga aluminum casting
- Fig. 5: Sampling locations (a) and tensile properties (b) of an aluminum giga casting in various locations
- Fig. 6: Aluminum paradox from sustainability aspect [19]
- Fig. 7: Comparison of CO2 production during various aluminum manufacturing processes [19]
- Fig. 8: Calculated friction of solid and solidification sequences of alloys currently used in ultra-large aluminum castings
- Fig. 9: Volume fraction of porosity as a function of Cu content in a cast Al-Si-Mg alloy [24]
- Fig. 10: Predicted cracking susceptibility coefficient (CSC) as a function of Cu and Si contents [25]
- Fig. 11: Effect of Cu, Mg, Fe, and Sr contents on corrosion resistance of Al-Si-Mg alloy
- Fig. 12: A schematic illustrating aluminum oxide detachment process [29]
- Fig. 13: Interfacial tension forces acting on the aluminum liquid droplet and aluminum oxide substrate [29]
- Fig. 14: Two gating designs for a large HPDC structural part: (a) Design 1; (b) Design 2
- Fig. 15: Trapped air integral comparison between two gating designs (in casting only)
- Fig. 16: An example showing cast surface defects eliminated with the proper die surface treatment [32]: (a) casting surface defects; (b) surface defect eliminated with die surface treatment
- Fig. 17: Two shot profiles for a large HPDC structure casting
- Fig. 18: Accumulation of the trapped air calculated for the four combinations of two gating designs and two shot profiles
6. 結論:
超大型アルミニウム形状鋳造は、自動車産業における軽量化と製造コスト削減に大きく貢献する可能性がありますが、品質、寸法安定性、持続可能性、修理の容易さという点でいくつかの課題が存在します。本研究で提示された解決策により、これらの課題に対処し、超大型アルミニウム形状鋳造の成功的な適用のための基盤を築くことができると期待されます。今後の研究では、より高度なシミュレーション手法を用い、実際の鋳造実験を通して研究結果を検証することが必要です。
7. References:
- [1] Luo A A, Sachdev A, Apelian D. Alloy development and process innovations for light metals casting. Journal of Materials Processing Technology, 2022, 306: 117606.
- [2] Ducker Frontier, 2020. 2020 North America light vehicle aluminum content and outlook. Final Report Summary: July 2020.
- [3] Wang Q G, Apelian D and Griffiths J R. Microstructural effects on the fatigue properties of aluminum castings, in advances in aluminum casting technology. Eds.: M. Tiryakioglu and J. Campbell, ASM International, Materials Park, OH, 1998: 217-224.
- [4] Wang Q G. Latest advances and developments in aluminum shape casting. China Foundry, 2013, 10(1): 43-49.
- [5] Wang L, Makhlouf M and Apelian D. Aluminum die casting alloys-Alloy composition, microstructure, and properties/performance relationships. Int. Materials Reviews, 1995, 40: 221-238.
- [6] Cáceres C H, Davidson C J, Griffiths J R, et al. Hypoeutectic Al-Si-Mg foundry alloys. Materials Forum, 1997, 21: 27-43.
- [7] Taylor J. Metal related castability effects in aluminium foundry alloys. Cast Metals, 1996, 8: 225-252.
- [8] Wang Q G. Fatigue fracture mechanism and fatigue life assessment of aluminum castings. In: Proceedings of Materials Lifetime Science & Engineering, edited by P. K. Liaw, R. A. Buchanan, D. L. Klarstrom, R. P. Wei, D. G. Harlow, and P. F. Tortorelli, TMS (The Minerals, Metals & Materials Society), 2003, Warrendale, PA: 211-222.
- [9] Hartlieb A and Hartlieb M. The impact of giga-castings on car manufacturing and aluminum content. https://www.lightmetalage.com/news/industry-news/automotive/the-impact-of-giga-castings-on-car-manufacturing-and-aluminum-content, July 10, 2023.
- [10] Hardigree M. How Tesla made 'gigacasting', the most important word in the car industry. https://www.theautopian.com/how-tesla-made-gigacasting-the-most-important-word-in-the-car-industry, Sept. 14, 2023.
- [11] Hart C, Afseth A, and Zuidema B. Aluminum value in battery electric vehicles. The Aluminum Association, 2022.
- [12] Abraham A K. Automotive materials in an evolving landscape. Ducker Carlisle, January 24, 2023.
- [13] Mihalascu D. Cadillac takes a page from Tesla's book, uses mega castings on Celestiq. https://insideevs.com/news/617108/cadillac-takes-page-from-tesla-book-uses-mega-castings-on-celestiq, October 18, 2022.
- [14] Phelan K. Casting of the year: Planets aligned for clean-sheet cadillac casting design. Modern Casting, May 2023: 24-31.
- [15] Panday A. What do Toyota's announcements on battery technologies, giga castings mean? Aug. 2, 2023. https://www.linkedin.com/pulse/what-do-toyotas-announcements-battery-technologies-giga-castings/
- [16] Schuh G, Bergweiler G, Dworog L, et al. Opportunities and risks of mega-casting in automotive production - The aluminum die-cast body in white. Düsseldorf: VDI Fachmedien, www.researchgate.net/publication/363880399, September 2022.
- [17] Wärmefjord K, Hansen J, and Söderberg R. Challenges in geometry assurance of megacasting in the automotive industry. ASME, Journal Computing and Information Science in Engineering, 2023, 23(6). https://doi.org/10.1115/1.4062269.
- [18] Giga Presses. The giant die casts that are reshaping car manufacturing. Reuters/Automotive News Europe, February 10, 2023.
- [19] Zhan H, Zeng G, Wang Q, et al. Unified cast (UniCast) aluminum alloy - Resolving sustainability paradox material solution for vehicle lightweighting. Journal of Materials Science & Technology, 2023, 154: 251-268.
- [20] Wilson D J, Wang L, Wang Q, et al. Repair ultra-large casting. US Patent Application No.: 20230356293.
- [21] Wilson D J, Wang L, Wang Q, et al. Method of in-situ repair of an ultra-large single-piece casting. US Patent Application No.: 20230339052.
- [22] Ravi K R. Fluidity of aluminum alloys and composites: A review. Journal of Alloys & Compounds, 2008, 456(1-2): 201-210.
- [23] Gao Y, Liao H, Suo X, et al. Prediction of fluidity of casting aluminum alloys using artificial neural network. In: Proceedings of Materials Science & Technology (MS&T2019), Sept. 29-Oct. 3, 2019, Portland USA.
- [24] Cáceres C H, Djurdjevic M B, Stockwell T J, et al. The effect of Cu content on the level of microporosity in Al-Si-Cu-Mg casting alloys. Scripta Materialia, 1999, 40(5): 631-637.
- [25] Edwards G A, Sigworth GK, Cáceres C H, et al. Microporosity formation in Al-Si-Cu-Mg casting alloys. AFS Transaction, 1997: 809-818.
- [26] Liao H, Wang Q, Suo X, et al. Modeling of solute-dependent fluidity and hot tearing sensitivity of conductive aluminum alloys. TMS 2018, 147th Annual Meeting & Exhibition Supplemental Proceedings, Feb. 2018, https://doi.org/10.1007/978-3-319-72526-0_34.
- [27] Lei Z, Liao H, Wang Q, et al. In-situ observation of porosity formation during directional solidification of Al-Si casting alloys. China Foundry, 2011, 8(1): 14-18.
- [28] Liao H, Wu Y, Fan R, et al. Effect of Sr content on porosity formation in directionally solidified Al-12.3wt.%Si alloy. China Foundry, 2014, 11(5): 435-439.
- [29] Liao H, Zhao L, Wu Y, et al. Investigation on formation mechanism of irregular shape porosity in hypoeutectic aluminum alloy by X-ray real time observation. Metall. Mater. Trans., 2012, 43A: 2587-2590.
- [30] Wang Q, Gerard D. Methods of reducing old oxides in aluminum castings. US Patent No. 9574252 (Feb 21, 2017).
- [31] Lee B D, Baek U H, Han J W. Optimization of gating system design for die casting of thin magnesium alloy-based multi-cavity LCD housings. Journal of Materials Engineering and Performance, 2012, 21: 1893-1903.
- [32] Campbell J. Castings, 2nd edition. Butterworth-Heinemann, June 12, 2003.
- [33] Wang Q, Xu Y, Rubin A, et al. Methods to improve surface appearance and quality of high pressure die castings and permanent mold castings. Research Disclosure, 2023.
9. Copyright:著作権と参考文献
本資料は、Qi-gui Wang、Andy Wang、およびJason Coryell著の論文「Ultra-large aluminum shape casting: Opportunities and challenges」に基づいて作成されました。
論文出典: https://doi.org/10.1007/s41230-024-4111-9
本資料は上記の論文に基づいて要約・作成されたものであり、商業目的での無断使用は禁じられています。
Copyright © 2025 CASTMAN. All rights reserved.
Qi-gui Wang, Andy Wang & Jason Coryell
Abstract
Ultra-large aluminum shape castings have been increasingly used in automotive vehicles, particularly in electric vehicles for light-weighting and vehicle manufacturing cost reduction. As most of them are structural components subject to both quasi-static, dynamic and cyclic loading, the quality and quantifiable performance of the ultra-large aluminum shape castings is critical to their success in both design and manufacturing. This paper briefly reviews some application examples of ultra-large aluminum castings in automotive industry and outlines their advantages and benefits. Factors affecting quality, microstructure and mechanical properties of ultra-large aluminum castings are evaluated and discussed as aluminum shape casting processing is very complex and often involves many competing mechanisms, multi-physics phenomena, and potentially large uncertainties that significantly influence the casting quality and performance. Metallurgical analysis and mechanical property assessment of an ultra-large aluminum shape casting are presented. Challenges are highlighted and suggestions are made for robust design and manufacturing of ultra-large aluminum castings.