Paper Summary:この論文の要約は、"[Clinching of inductively heated aluminum die casting]"と題された論文を、"[Production Engineering]"にて発表された論文に基づいています。
1. 概要:
- タイトル: 誘導加熱アルミニウムダイカストのクリンチング (Clinching of inductively heated aluminum die casting)
- 著者: Sinan Yarcu, Bernd-Arno Behrens, Sven Huebner, Torsten Schuchardt, Klaus Dilger, Thomas Paul Meichsner
- 発表年: 2022年
- 掲載ジャーナル/学会誌: Production Engineering
- キーワード: 接合 (Joint), クリンチング (Clinching), ダイカスト (Die casting), 加熱クリンチング (Heated clinching), テンパリングクリンチング (Tempered clinching)
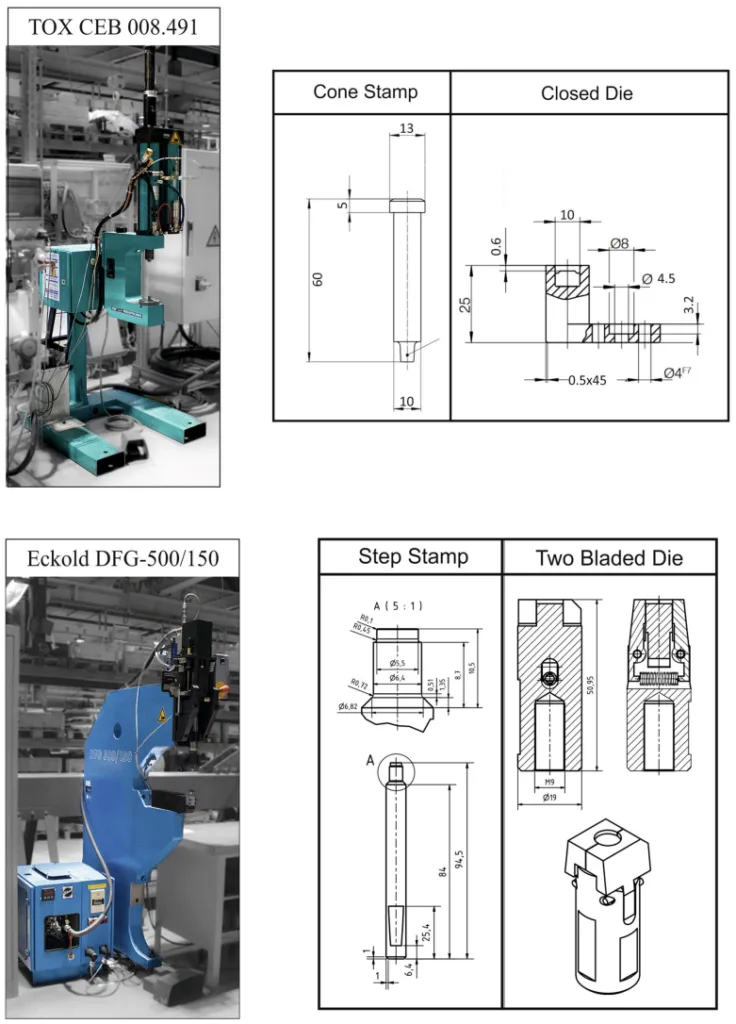
2. 研究背景:
- 研究トピックの社会的/学術的背景:
自動車産業において、マルチマテリアルボディ(MMB)の採用は、車両重量と性能を最適化するために増加傾向にあります。アルミニウムと鋼のような異種材料の接合は、熱特性の違いから、スポット溶接のような従来の方法では課題があります。クリンチングは、適切な代替技術として考えられています。しかし、アルミニウムダイカスト合金は、その脆さから、割れなしにクリンチングを行うことが困難です。先行研究では、マグネシウムダイカストの予熱が割れを防ぐことが示唆されていますが、アルミニウムダイカストのクリンチングへのこのアプローチは十分に研究されていませんでした。 - 既存研究の限界:
アルミニウムダイカスト合金のクリンチングに関する既存の研究は、材料固有の脆さに起因する割れの問題を明らかにしています。最適化された工具形状や、セルフピアスリベットや摩擦攪拌リベットのような代替手法も検討されてきましたが、多くの場合、インターロックの減少や、依然として割れが発生しやすいという課題が残ります。マグネシウムダイカストの割れを軽減するための予熱方法は知られていましたが、アルミニウムダイカストのクリンチングへの予熱、特に誘導加熱の応用は、十分に研究されていませんでした。 - 研究の必要性:
MMB構造におけるアルミニウムダイカスト合金の接合にクリンチングの適用範囲を拡大するためには、その脆さに関連する割れの問題を克服する必要があります。誘導加熱は、迅速かつ効率的な加熱方法として有望です。したがって、割れのない接合と接合強度向上のために、アルミニウムダイカスト合金のプロセス安全なクリンチングを可能にする誘導加熱戦略を調査し、最適化することが必要です。
3. 研究目的と研究課題:
- 研究目的:
本研究の主な目的は、プロセス安全な接合を実現するために局所的な熱処理を採用することにより、アルミニウムダイカスト合金のクリンチングプロセスを改善することです。焦点は、誘導加熱を使用してアルミニウムダイカスト合金の脆さを一時的に低減し、それによってクリンチング中の割れを防ぎ、接合性能を向上させることです。 - 主な研究課題:
- 局所的な誘導加熱は、アルミニウムダイカスト合金における割れのないクリンチポイントの形成にどのように影響するか?
- 異なる工具システムを用いたアルミニウムダイカスト合金のクリンチングにおいて、誘導加熱に最適な加熱戦略(加熱時間、温度)は何か?
- 異なるクリンチング工具システム(フレキシブルダイとリジッドダイ)とインダクタ設計は、誘導加熱と組み合わせた場合に、クリンチングプロセスと接合特性にどのような影響を与えるか?
- 誘導加熱は、アルミニウムダイカスト合金におけるクリンチ接合の幾何学的寸法(インターロック、底厚、ネック厚)にどのような影響を与えるか?
- 誘導加熱は、アルミニウムダイカスト合金のクリンチ接合の引張強度にどのような影響を与えるか?
- 研究仮説:
- 局所的な誘導加熱は、アルミニウムダイカスト合金のクリンチング中の割れを低減する。
- 誘導加熱は、インターロック、ひいてはクリンチ接合の頭部引張強度を向上させる。
- 異なるインダクタと工具の設計は、加熱時間、割れ挙動、および接合部の形状にさまざまな影響を与える。
- 最適化された誘導加熱パラメータは、短いプロセス時間(6秒未満)でアルミニウムダイカスト合金の割れのないクリンチングを可能にする。
4. 研究方法
- 研究デザイン:
本研究では、誘導加熱がアルミニウムダイカスト合金のクリンチングに及ぼす影響を調査するために実験計画法を採用しています。この研究では、2つのクリンチング工具システム(フレキシブルダイとリジッドダイ)と、直径の異なる2つのインダクタ設計を比較します。独立変数は、加熱戦略(誘導加熱パラメータ)、工具システム、およびインダクタ設計です。従属変数は、加熱時間、割れ挙動、クリンチポイントの表面品質、接合部の形状(インターロック、底厚、ネック厚)、および頭部引張強度です。 - データ収集方法:
- 時間-温度曲線: K型熱電対をダイカスト材に挿入して測定し、異なる電力レベルとインダクタ構成での加熱時間を決定しました。
- 表面分析: 異なる加熱温度での割れ形成と表面品質を評価するために、クリンチポイントの顕微鏡観察を実施しました。
- 寸法測定: プロファイルプロジェクターまたは同様の測定ツールを使用して、クリンチポイントの形状(インターロック、底厚、ネック厚)の分析を行いました。
- 機械試験: 誘導加熱ありとなしでクリンチされたサンプルの接合強度を評価するために、DVS 3480規格に従って頭部引張試験を実施しました。
- 分析方法:
- 定性分析: クリンチポイントの目視検査による割れの検出と表面特性の評価。
- 定量分析: 時間-温度データ、寸法測定、および頭部引張強度試験結果の統計分析。平均値と標準偏差を算出しました。
- 比較分析: 異なる工具システム、インダクタ設計、および加熱パラメータで得られた結果を比較し、割れのないクリンチングと接合性能向上のための最適な条件を決定しました。
- 研究対象と範囲:
本研究は、アルミニウムダイカスト合金EN AC-AlSi9Mn(厚さ3 mm)を鋳造状態(F)でアルミニウムシートEN AW-5182(厚さ1.5 mm)に接合することに焦点を当てています。2つのクリンチングプレス(Eckold DFG-500/150およびTOX CEB 008)と、関連する工具システム(BTMフレキシブルダイおよびTOXリジッドダイ)を使用しました。小型リングインダクタは、各プレス用に設計および製造されました。範囲は、この特定の材料の組み合わせに対する誘導加熱クリンチングの実現可能性と利点を評価するための実験室実験と材料特性評価に限定されています。
5. 主な研究結果:
- 主な研究結果:
- 誘導加熱を局所的に使用することで、アルミニウムダイカスト合金EN AC-AlSi9Mnの割れのないクリンチングを、フレキシブル(BTM)およびリジッド(TOX)ダイシステムの両方で達成しました。
- 誘導加熱は、割れのないクリンチポイントを達成するために必要な時間を大幅に短縮し、6秒未満で良好な接合部を製造できました。
- リジッドダイシステム(TOX)は、割れのないクリンチングを達成するために、フレキシブルダイシステム(BTM)(260℃)と比較して、より低い加熱温度(220℃)を必要としました。
- 誘導加熱は、両方の工具システムでクリンチ接合部のインターロックを増加させました。
- 頭部引張強度は誘導加熱によって向上し、室温でのクリンチングと比較して、BTM工具システムで26%、TOX工具システムで25%の増加を示しました。
- ネック厚は誘導加熱によってほとんど変化せず、せん断引張強度は有意に影響を受けないことが示唆されました。
- 統計的/定性的な分析結果:
- 時間-温度曲線は、発電機出力が高いほど、またEckoldプレスで使用されるインダクタ(直径が大きい)ほど、加熱速度が速いことを示しました。
- 表面分析顕微鏡写真は、両方のダイシステムで特定の温度閾値を超える誘導加熱で製造されたクリンチポイントに割れがないことを確認しました。
- 寸法測定では、誘導加熱により、両方の工具システムでインターロック(f)が顕著に増加しました(TOXで最大+ 47%、BTMで+ 30%)。底厚(tb)は、特にフレキシブルダイの場合、誘導加熱により大幅に減少しました。ネック厚(tn)は比較的安定していました。
- 頭部引張試験は、誘導加熱されたサンプルの接合強度が、室温でクリンチされたサンプルと比較して統計的に有意な増加を示しました。
- データ解釈:
- 局所的な誘導加熱は、アルミニウムダイカスト合金の脆さを効果的に低減し、短いプロセス時間で割れのないクリンチングを可能にします。
- リジッドダイシステムのダイボディに集中した熱は、ブレードを通して熱損失が発生するフレキシブルダイシステムと比較して、より迅速かつ効率的な加熱を促進します。
- 誘導加熱によって達成されたインターロックの増加は、頭部引張強度の向上に寄与する主な要因です。
- ネック厚が一定であることは、接合強度の向上が、ネック領域の材料強度の増加よりも、主に形状閉鎖の強化(インターロック)によるものであることを示唆しています。
- 図のリスト:
- 図 1 Audi e-tron GT Coupé を例としたアルミニウムを多用した複合構造 [3]
- 図 2 Eckold 社(下)と TOX 社(上)のクリンチングプレス。BTM 社(下)と TOX 社(上)のクリンチング工具システムの使用例
- 図 3 Eckold クリンチングプレス(左)と TOX クリンチングプレス(右)用の小型リングインダクタの製造図面
- 図 4 Eckold クリンチングプレス(上)と TOX クリンチングプレス(下)の量産に適した誘導加熱コンセプトのセットアップ
- 図 5 サンプル位置(左)と測定された機械的特性を備えた鋳造部品
- 図 6 合金 EN AC-AlSi9Mn の早期に割れた引張試験片の破断面の全体図。コールドシャットのある領域が明確に確認できる(左)。ベントの隣にある引張試験片の細孔分析の 3D モデルレンダリング
- 図 7 磁力線の遮蔽の原理図
- 図 8 リジッドダイ(上)とフレキシブルダイ(下)のクリンチ要素の寸法 [13]
- 図 9 TOX クリンチングプレス(左)と Eckold クリンチングプレス(右)のインダクタに対する、操作変数(電力値)を変化させた誘導加熱の時間-温度曲線
- 図 10 小型インダクタを使用した可動 BTM ダイ(青色のボックス)とリジッドダイ(緑色のボックス)の表面分析の概要表(オンラインカラー図)
- 図 11 小型インダクタを使用した可動 BTM ダイ(青色のボックス)とリジッドダイ(緑色のボックス)の表面分析のクローズアップ(オンラインカラー図)
- 図 12 リジッドダイ(TOX)とフレキシブルダイ(BTM)の室温および 220℃ におけるクリンチ接合部の頭部引張強度
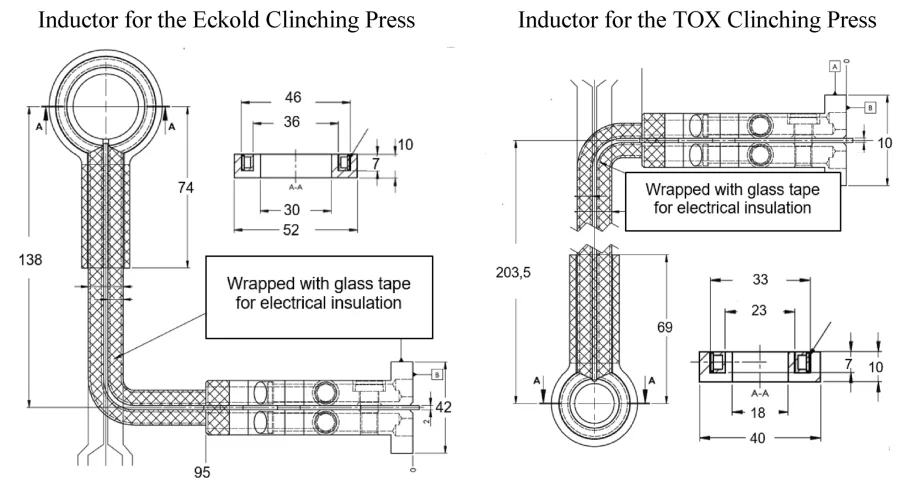
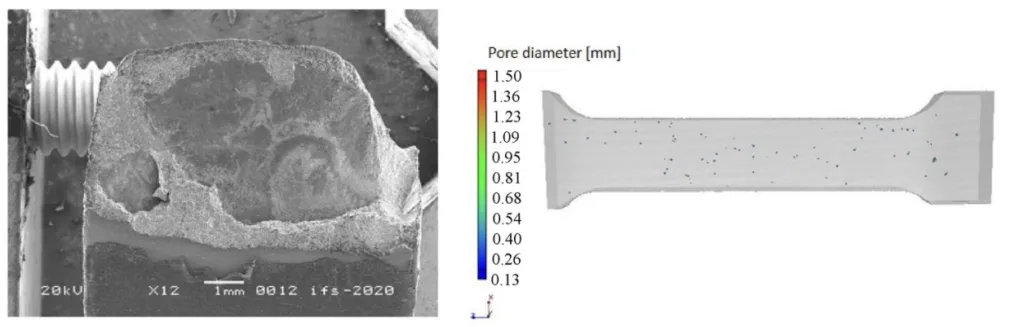
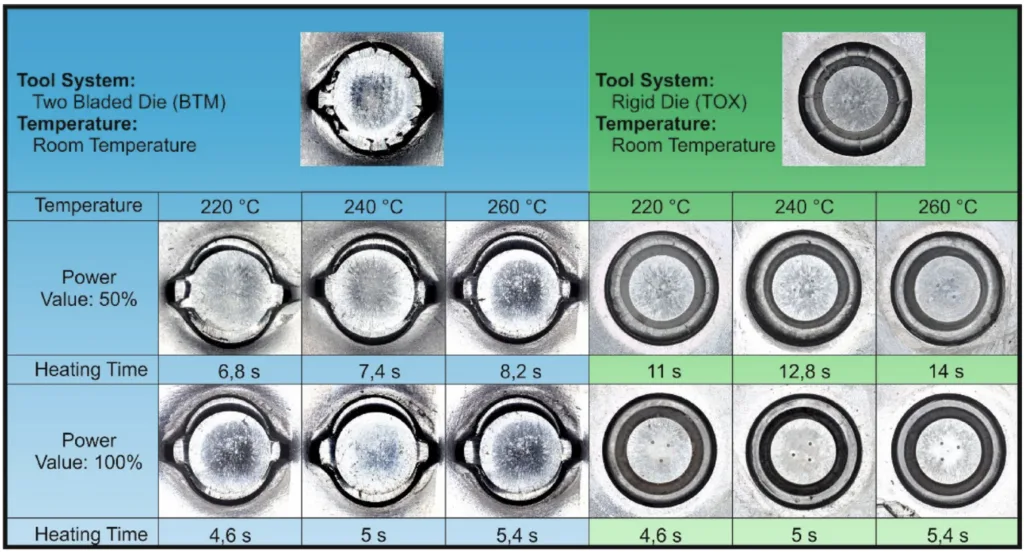
6. 結論と考察:
- 主な結果の要約:
本研究では、局所的な誘導加熱が、短いサイクル時間(6秒未満)でアルミニウムダイカスト合金EN AC-AlSi9Mnの割れのないクリンチングを可能にすることを実証しました。リジッドダイシステムとフレキシブルダイシステムの両方が、誘導加熱と組み合わせることで、インターロックと頭部引張強度が向上した改善されたクリンチ接合部を生成しました。リジッドダイシステムは、加熱温度要件の点でより効率的であることが証明されました。 - 研究の学術的意義:
本研究は、アルミニウムダイカスト合金のような脆性材料の接合に関する基礎的な理解に貢献します。誘導加熱をクリンチングプロセスを強化するために応用することに関する貴重な洞察を提供します。この研究は、工具システムの設計と加熱戦略が接合品質とプロセス効率に及ぼす影響を強調しています。この知見は、軽量自動車構造向けの加熱クリンチングプロセスのさらなる最適化の基礎として使用できます。 - 実用的な意義:
開発された誘導加熱クリンチング法は、自動車製造やその他の産業におけるアルミニウムダイカスト部品の接合に実用的なソリューションを提供します。このプロセスは、従来の接合技術の限界を克服することにより、複雑な設計で軽量材料の使用を可能にします。誘導加熱で達成された短いサイクル時間は、大量生産に適しています。接合強度の向上は、マルチマテリアル構造の信頼性と耐久性を高めます。 - 研究の限界:
この研究は、特定のアルミニウムダイカスト合金とシート材の組み合わせに限定されています。この方法の他のアルミニウム合金および材料の組み合わせへの適用性を評価するには、さらなる研究が必要です。誘導加熱されたクリンチ接合部の長期耐久性と腐食挙動は、本研究では調査されていません。インダクタ設計と加熱パラメータの最適化は、異なる部品形状と生産シナリオに合わせてさらに検討することができます。
7. 今後のフォローアップ研究:
- フォローアップ研究の方向性:
- 誘導加熱クリンチングの、より広範囲なアルミニウムダイカスト合金および異種材料の組み合わせ(例:アルミニウムと鋼)への応用を調査する。
- エネルギー効率とプロセスの堅牢性を向上させるために、異なる部品形状と厚さに対してインダクタ設計と加熱パラメータを最適化する。
- さまざまな環境条件下での誘導加熱されたクリンチ接合部の長期性能を評価するために、耐久性試験(疲労、腐食)を実施する。
- プロセスの安定性と接合品質をさらに向上させるために、誘導加熱中の温度制御のための高度な制御戦略を検討する。
- この技術の産業生産ラインへの統合を調査し、その拡張性と費用対効果を評価する。
- さらなる探求が必要な分野:
- 誘導加熱クリンチングプロセスと接合性能に対する異なる表面処理とコーティングの影響。
- 加熱効率と接合特性に対するインダクタとワークピース間のエアギャップの変化の影響。
- プロセス監視および品質管理システムを誘導加熱クリンチングプロセスに統合する可能性。
- プロセスパラメータと工具設計を最適化するための、誘導加熱クリンチング中の電磁気現象、熱現象、および機械現象の連成シミュレーションとモデリング。
8. 参考文献:
- [1] Hirsch J (2011) Aluminium in innovative light-weight car design. Mater Trans 52(5):818-824
- [2] Taub AL, Krajewski PE, Luo AA et al (2007) The evolution of technology for materials processing over the last 50 years: the automotive example. JOM 59(2):48-57
- [3] Audi MediaCenter (2021) https://www.audi-mediacenter.com/de/hightech-trifft-handarbeitdie-produktion-des-audi-e-tron-gt-in-den-boellinger-hoefen-13242/leidenschaft-fuer-qualitaet-und-progressivitaet-der-neue-audi-e-tron-gt-13243
- [4] Behrens B-A, Bouguecha A, Vucetic M, Hübner S, Yilkiran D, Jin Y, Peshekhodov I (2015) FEA-based optimisation of a clinching process with an open multiple-part die aimed at damage minimisation in CR240BH-AlSi10MnMg joints. Mater Sci Eng Chem 21:1-7
- [5] Zhao X, Meng D, Zhang J, Han Q (2020) The effect of heat treatment on die casting aluminum to apply self-pierce riveting. Int J Adv Manuf Technol 109:2409-2419
- [6] Zhao X (2019) Research on applying the self-pierce riveting (SPR) for die casting aluminum alloys. A Dissertation submitted to the Faculty of Purdue University
- [7] Böllhoff (2021) Joining of aluminium cast with new ring groove die, Homepage. https://www.boellhoff.com/de-en/news/news/2017/rivset-ring-groove-die.php
- [8] Jäckel M, Coppieters S, Hofmann M, Vandermeiren N, Landgrebe D, Debruyne D, Wallmersberger T, Faes K (2017) Mechanical joining of materials with limited ductility: analysis of process-induced defects. In: Proceedings of the 20th international ESA-FORM conference on material forming, AIP conference proceedings, vol 1896, pp 110009-1-110009-6
- [9] Hovanski Y, Upadyay P, Kleinbaum S, Carlson B, Boettcher E, Ruokolainen R (2017) Enabling dissimilar material joining using friction stir scribe. JOM 69(6):1060-1064
- [10] Ang HQ (2021) An overview of self-piercing riveting process with focus on joint failures, corrosion issues and optimisation techniques. Chin J Mech Eng 34:2. https://doi.org/10.1186/$10033-020-00526-3
- [11] Wang JW, Liu ZX, Shang Y et al (2011) Self-piercing riveting of wrought magnesium AZ31 sheets. J Manuf Sci Eng 133(3):031009
- [12] Yarcu S, Huebner S, Yilkiran D, Brunotte K, Behrens B-A, Schuchardt T, Mueller S, Dilger K (2021) Clinching of heated aluminium die cast. In: Journal: proceedings of the 11th congress of the German Academic Association for Production Technology
- [13] Merkblatt DVS/EFB 3420: Clinchen-Überblick / Clinching basics (2018) DVS-Deutscher Verband für Schweißen und Verwandte Verfahren e.V., EFB-Europäische Forschungsgesellschaft für Blechverarbeitung e. V
- [14] Varis J (2006) Ensuring the integrity in clinching process. J Mater Process Technol 174:277-285
9. 著作権:
*この資料は Sinan Yarcu 氏の論文:「誘導加熱アルミニウムダイカストのクリンチング (Clinching of inductively heated aluminum die casting)」に基づいています。
*論文ソース: https://doi.org/10.1007/s11740-022-01116-z
この資料は上記の論文に基づいて要約されたものであり、商業目的での無断使用は禁止されています。
Copyright © 2025 CASTMAN. All rights reserved.