本論文概要は、['ResearchGate'発行の「製造変動を含む自動車および航空宇宙複合材構造の設計および解析方法」]論文に基づいて作成されました。
1. 概要:
- タイトル:製造変動を含む自動車および航空宇宙複合材構造の設計および解析方法 (A Design and Analysis Method for Automotive and Aerospace Composite Structures including Manufacturing Variations)
- 著者:Dirk Lukaszewicz, Simon Hesse, Lavinia Graff, Stefan Kerscher, Lyle Deobald, Chul Y Park, Nihar Desai
- 発行年:2014年9月
- 発行ジャーナル/学会:会議論文、ResearchGate
- キーワード:製造変動 (Manufacturing variations), 複合材構造 (composite structures), 自動車 (automotive), 航空宇宙 (aerospace), 設計方法 (design method), 解析方法 (analysis method)
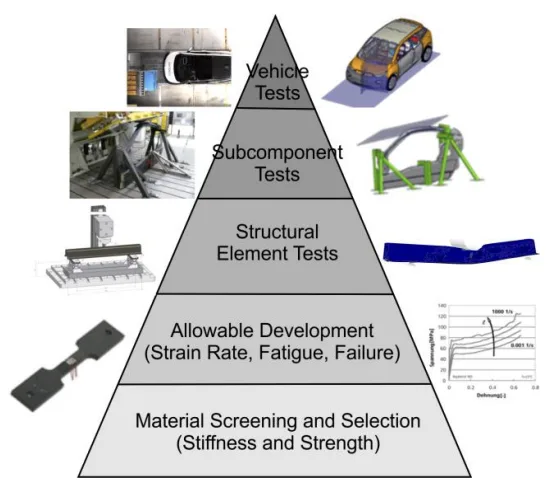
2. 抄録
本論文では、複合材自動車構造およびサブシステムの設計段階における製造および形状誘起変動(MV, Manufacturing and geometry-induced variations)の潜在的な相互作用をモデル化するためのアプローチを提示します。最初に、製造変動の取り扱いを中心に、一般的な設計プロセスについて議論します。次に、高度な複合材自動車サイドフレームを用いて、そのような変動の影響を実証します。自動車サイドフレームの耐衝撃性実証に適用される一般的な方法は、典型的な航空宇宙構造の強度予測に拡張できます。面外波状性(out-of-plane waviness)のような実際の製造変動は、部品内の位置とともに破壊試験によって記録され、その後、Abaqus Explicit [1] で設定されたFE(有限要素)モデルに導入されました。可変領域はノックダウン係数(knockdown factors)に関連付けられ、その一部は補完論文 [2] で導き出されました。異なるMVマップを持つ2つのFEモデルが実験結果に対して検証されました。
複数のMV特性のレベルは、確率的に同時に変化させられ、インパクタ侵入への影響が記録されました。これから、応答曲面モデル(RSM, Response Surface Model)が生成されました。すべてのノックダウン係数を分離し、MVの影響を個別に評価することを可能にする新しい最適化手法も使用されました。その結果は、各MVに対する最大許容特性です。この方法論は、スクラップ率の低減、高価な資格試験プログラムの削減、および未知の製造変動を考慮するための過剰な安全係数の使用の排除によって部品重量の削減を可能にするため、大量複合材製造および設計に大きな利点をもたらします。
3. 研究背景:
研究テーマの背景:
複合材の設計と製造は、部品製造の過程で必然的に製造変動(MV, Manufacturing Variations)を伴います。これらのMVは、部品の形状、レイアップシーケンス、および加工条件に依存し、剛性や強度などの複合材構造物の機械的特性に大きな影響を与える可能性があります。平板試験片から得られた機械的特性とは異なり、実際の部品はMVを示すため、保守的でない設計許容値につながる可能性があります。
既存研究の現状:
現在の航空宇宙産業の実践では、MVを考慮するために、設計プロセスにいくつかの要素を組み込んで、ロバスト性を確保しています。重要な要素は、ノックダウン係数(knockdown factors)を公称材料特性に適用して導き出された許容値(allowables)の使用です。「ビルディングブロックアプローチ(Building Block Approach)」に基づいたこの方法は、広範な試験と非破壊検査(NDI, Non-Destructive Inspection)に依存しています。しかし、大量生産の自動車製造環境では、NDIは時間とコストの制約のために非現実的な場合が多くあります。既存の方法では、MVを考慮するために構造強度を全体的に減少させる方法を使用していますが、これは過度に保守的である可能性があります。
研究の必要性:
航空宇宙産業のアプローチは効果的ですが、生産量とコストの考慮事項から、大量生産の自動車複合材製造に直接適用することは困難です。製品開発プロセスにおいてMVを考慮し、設計プロセスと製造プロセスの両方に情報を提供する方法論が必要です。これには、重要なMVを特定し、ダイカストアルミニウム部品の設計で多孔性を明示的に考慮するアプローチと同様に、MVの影響を軽減するために製造プロセスを最適化することが含まれます。
4. 研究目的と研究課題:
研究目的:
本研究の主な目的は、複合材自動車および航空宇宙構造物の設計段階において、製造変動(MV, Manufacturing Variations)を明示的に組み込む設計および解析方法論を開発し、実証することです。この方法論は、構造的性能を維持しながら製造プロセスを最適化し、過度に保守的な安全係数への依存を減らすために、MVに対する許容限界を定義することを目的としています。
主要な研究課題:
- 設計段階で製造および形状誘起変動の相互作用をモデル化する方法は何か?
- 高度な複合材自動車サイドフレームを使用してMVの影響を実証し、航空宇宙構造に方法論を拡張する方法は何か?
- 面外波状性(out-of-plane waviness)のような実際のMVを記録し、FE(有限要素)モデルに統合する方法は何か?
- ノックダウン係数(knockdown factors)を分離し、個々のMVの影響を評価するために、応答曲面モデル(RSM, Response Surface Model)と新しい最適化技術を活用する方法は何か?
- 設計および製造プロセス最適化を導くために、各MVに対する最大許容特性を定義する方法は何か?
研究仮説:
本研究は、以下の仮説を暗黙的に含んでいます。
- FE(有限要素)シミュレーションでMVを明示的にモデル化すると、全体的なノックダウン係数(knockdown factors)を使用するよりも、複合材構造性能をより正確に予測できるはずである。
- 特定のMVが構造性能に及ぼす影響に基づいて製造プロセスを最適化すると、スクラップ率の低減、資格費用削減、および部品重量の削減につながるはずである。
- RSM(応答曲面モデル, Response Surface Model)および分離されたノックダウン係数(knockdown factors)に基づいた方法論は、複合材構造におけるMVに対する許容限界を効果的に定義できるはずである。
5. 研究方法論
研究デザイン:
本研究では、実験的試験と数値シミュレーションを組み合わせたアプローチを採用しています。複合材自動車サイドフレームのケーススタディを使用して、方法論を実証します。設計は、複合材車両に合わせて調整された「ビルディングブロックアプローチ(Building Block Approach)」を使用して反復されます。
データ収集方法:
- 破壊試験(Destructive Testing): 面外波状性(out-of-plane waviness)のような実際の製造変動(MV, Manufacturing Variations)は、製造された複合材サイドフレームの破壊試験を通じて記録されました。
- 目視検査(Visual Inspection): MV特性は、グリッド投影法を使用して製造された部品の各層について目視で検査し、記録しました。品質検査担当者が欠陥を分類し、特性評価しました。
- 実験的検証(Experimental Validation): 異なるMVマップを持つ2つのFE(有限要素)モデルが、実際の衝突試験の実験結果に対して検証されました。
分析方法:
- 有限要素(FE, Finite Element)モデリング: FEモデルは、Abaqus Explicitで開発され、動的衝撃下での複合材サイドフレームの構造的挙動をシミュレーションし、記録されたMVマップを統合しました。
- 応答曲面モデル(RSM, Response Surface Model): RSMは、確率的に変化させたMV特性が構造的性能(インパクタ侵入)に及ぼす影響を分析するために、モンテカルロシミュレーション(Monte Carlo simulations)に基づいて生成されました。
- モンテカルロシミュレーション(Monte Carlo Simulation): モンテカルロサンプリング(Monte Carlo sampling)は、MV特性が構造的性能に及ぼす影響を評価するために、FEモデルでMV特性を変化させるために使用されました。
- 最適化アルゴリズム(Optimization Algorithm): 新しい最適化アルゴリズムは、ノックダウン係数(knockdown factors)を分離し、各MVに対する最大許容特性を決定するために使用されました。
研究対象と範囲:
本研究は、自動車および航空宇宙用途の複合材構造に焦点を当てており、特に自動車サイドフレームをケーススタディとして使用しています。範囲には、面内および面外波状性(in-plane and out-of-plane waviness)、縦方向および横方向の折り畳み(longitudinal and transverse folding)などの製造変動が含まれます。本研究は、考慮されたMVタイプと自動車サイドフレームの特定の形状に限定されます。
6. 主な研究成果:
主要な研究成果:
- 測定された製造変動(MV, Manufacturing Variations)を複合材構造のFE(有限要素)モデルに組み込むための方法論が開発および検証されました。
- MVマップを統合したFEモデルは、動的衝撃試験に対する実験結果と良好な相関関係を示しました。
- さまざまなMV特性が構造的性能(インパクタ侵入)に及ぼす影響を定量化するために、応答曲面モデル(RSM, Response Surface Model)が生成されました。
- ノックダウン係数(knockdown factors)を分離する新しい最適化アプローチを使用して、各MVタイプに対する最大許容特性が決定されました。
- 本研究は、特定のMVの組み合わせが衝撃中の最大侵入の減少につながる可能性があることを実証しました。これは、潜在的に剛性の増加または変更された破壊モードによる可能性があります。
提示されたデータの分析:
- 表 1:変化させたMVと特性範囲 (Table 1: Varied MVs and characteristic range): この表は、考慮された製造変動のタイプ(面外波状性、面内波状性、縦方向の折り畳み、横方向の折り畳み)とその特性サイズ範囲(1〜6)をリストしています。
- 図 3:インパクタと支持部を備えたFEモデルの画像、マッピングされたMVも表示 (Figure 3: Image of the FE-model with Impactor and supports, mapped MVs are also shown): この図は、インパクタ、支持部、および複合材サイドフレームにマッピングされた製造変動を含むFEモデルの設定を視覚的に示しています。
- 図 4:ベースラインFEシミュレーションとMVマップAおよびBの荷重-変位曲線の比較 (Figure 4: Comparison of load-displacement curves for the baseline FE Simulation and MV map A and B): この図は、FEシミュレーションの荷重-変位曲線を比較しています。MVのないベースラインシミュレーションと、2つの異なるMVマップ(AおよびB)を統合したシミュレーションです。MVが構造応答に及ぼす影響を示しています。
- 表 2:3点曲げ動的衝撃試験の変動性 (Table 2: Variability of 3-point-bending dynamic impact tests): この表は、公称上同一の試験片に関する変動性試験の結果を示しており、最大侵入と平均侵入と標準偏差を示しています。このデータは、MVによる許容可能な変化を定義するために使用されます。
- 表 3:モンテカルロシミュレーションの結果と臨界限界を超える設計数 (Table 3: Monte Carlo Simulation Results and No of designs above the critical limit): この表は、反復にわたるモンテカルロシミュレーションの結果を要約し、RSMのR²値、外れ値設計数、および外れ値の割合を示しています。RSMの収束と品質を示しています。
- 表 4:MV特性に関するコリドー制限 (Table 4: Corridor Limits on MV Characteristics): この表は、最適化プロセスのさまざまな反復にわたって、各MVタイプ(面外波状性、面内波状性、縦方向の折り畳み、横方向の折り畳み)に対するコリドー制限(最大許容MV特性)を示しています。許容限界がどのように改善されるかを示しています。
図リスト:
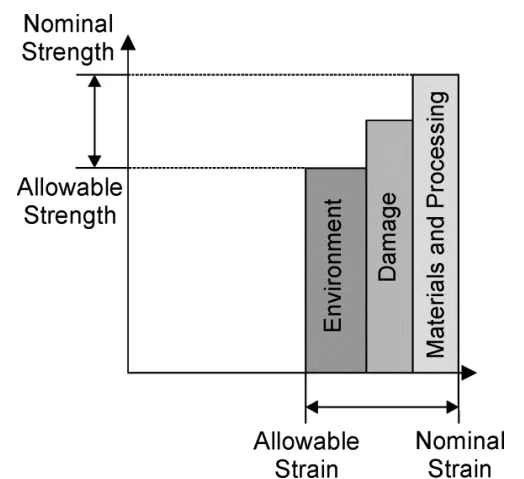
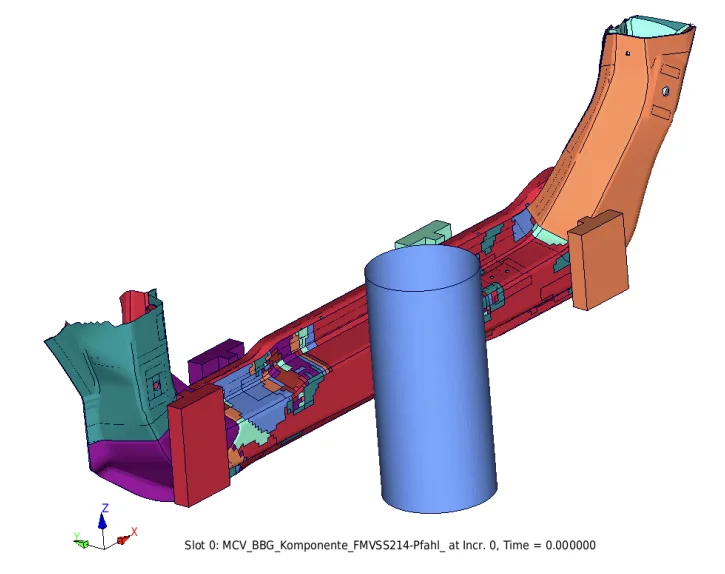
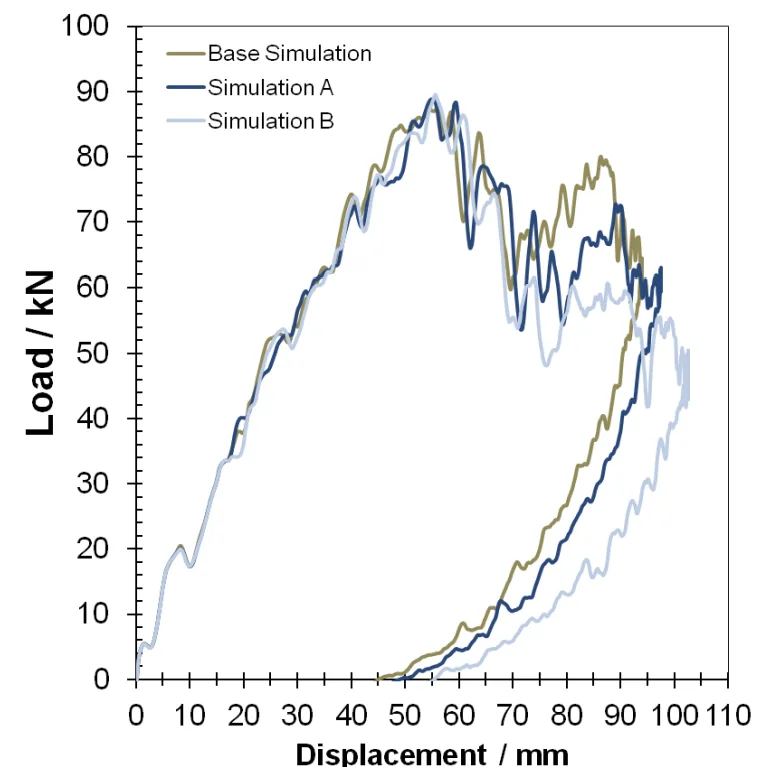
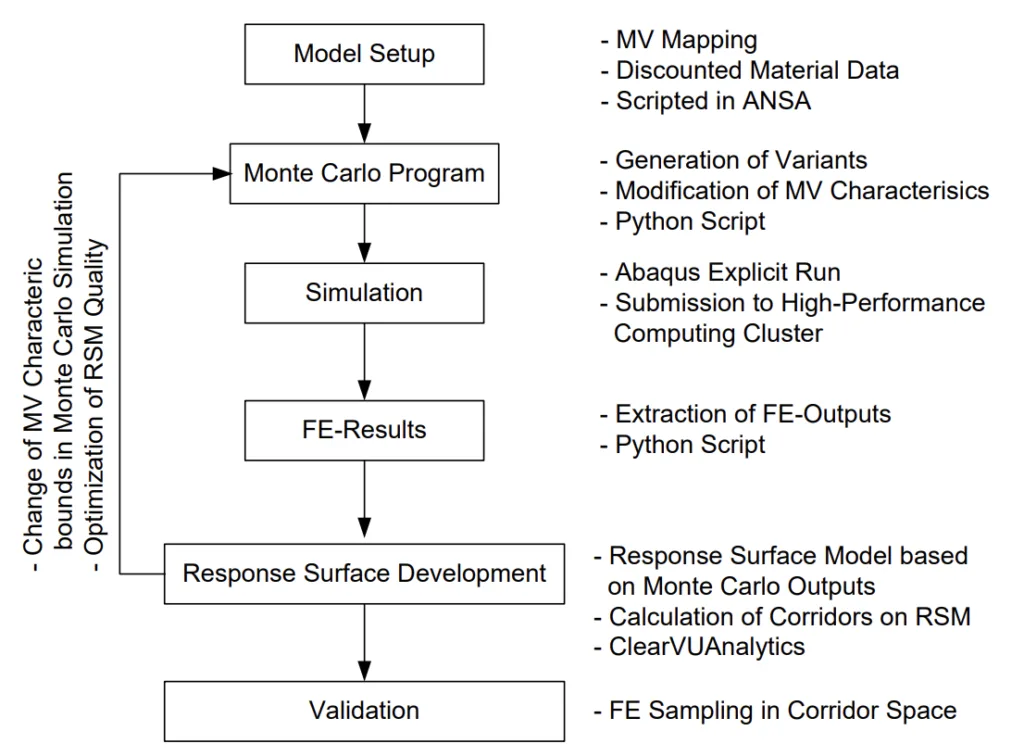
- 図 1:複合材料の公称値と導き出された設計許容値の定義 (Figure 1: Definition of nominal values for a composite material and derived design allowables)。
- 図 2:複合材車両のビルディングブロックアプローチ (Figure 2: Building Block approach for a composite vehicle)。
- 図 3:インパクタと支持部を備えたFEモデルの画像、マッピングされたMVも表示 (Figure 3: Image of the FE-model with Impactor and supports, mapped MVs are also shown)。
- 図 4:ベースラインFEシミュレーションとMVマップAおよびBの荷重-変位曲線の比較 (Figure 4: Comparison of load-displacement curves for the baseline FE Simulation and MV map A and B)
- 図 5:MVコリドーと最大許容特性に関するシミュレーションワークフロー (Figure 5: Simulation Workflow for the MV corridors and the maximum allowable characteristic)。
7. 結論:
主な研究成果の要約:
本研究では、製造変動(MV, Manufacturing Variations)を明示的に考慮した複合材構造の設計方法論を首尾よく開発し、検証しました。測定されたMVをFE(有限要素)モデルに統合し、RSM(応答曲面モデル, Response Surface Model)および新しい最適化技術を使用することにより、構造的完全性を維持しながらMVに対する許容限界を定義しました。この方法論は、自動車複合材サイドフレームで実証され、シミュレーションと実験結果の間で良好な相関関係を示しました。
研究の学術的意義:
本研究は、製造のばらつきを設計プロセスに直接組み込むための堅牢な方法論を提供することにより、複合材構造設計の分野に貢献します。全体的なノックダウン係数(knockdown factors)に依存する従来のアプローチから脱却し、MVが存在する場合の構造的性能を予測するための、より洗練された正確な方法を提供します。RSM(応答曲面モデル, Response Surface Model)と分離されたノックダウン係数(knockdown factors)の使用は、製造の不確実性のある複合材構造の解析と最適化における進歩を表しています。
実用的な意味:
開発された方法論は、特に自動車および航空宇宙産業における大量複合材製造に大きな実用的な意味を持ちます。MVを明示的に考慮して複合材部品を設計できるようにすることにより、次のことが可能になります。
- 最適化された製造プロセスによるスクラップ率の低減。
- 広範な物理的試験の必要性を減らすことによる資格費用の削減。
- 過剰な安全係数の使用を最小限に抑えることによる部品重量の削減。
- 製造と設計間の改善された連携、同時最適化の促進。
研究の限界と今後の研究分野:
本研究は、特定のタイプの製造変動と特定の自動車部品に限定されています。今後の研究では、以下を行う必要があります。
- より広範囲なMVタイプと複合材料を含めるように方法論を拡張する。
- 航空宇宙構造を含む、さまざまな構造形状と荷重条件に方法論を適用する。
- さまざまなMVタイプの相互作用と複合効果が構造的性能に及ぼす影響に関する追加調査。
- 特定された重要なMVとその許容限界に基づいて製造プロセスの最適化を検討する。
- 方法論をさらに改善するために、結果で観察された数値ノイズとドメイン分解効果を調査する。
8. 参考文献:
- [1] Dassault Simulia. Abaqus 6.11-2A; 2013.
- [2] Deobald L, Park C, Desai N, et al. Simulation of Composite Manufacturing Variations to Determine Stiffness and Strength Reductions in Automotive and Aerospace Structure. ACS 29th Technical Conferences. San Diego 2014.
- [3] Potter K. In: (unpublished), 2013.
- [4] Huang H, Talreja R. Effects of void geometry on elastic properties of unidirectional fiber reinforced composites. Comp Sci Tech. 2005;65(13):1964-81.
- [5] Feraboli P. Composite Materials Strength Determination Within the Current Certification Methodology for Aircraft Structures. 2009;46(4):1365-74.
- [6] Graff L. Stochastic Algorithm for the identification of solution spaces in high-dimensional design spaces [PhD Thesis]: University of Basel, 2013.
- [7] Baxter B. The interpolation theory of radial basis functions [PhD Thesis]: Cambridge University, 1992.
- [8] Piret C. Analytical and numerical advances in radial basis functions [PhD Thesis]: University of Colorado, 2007.
- [9] Zimmermann M, von Hoessle J. Computing solution spaces for robust design. Int J Num Methods Eng. 2013;94(3):290-307.
- [10] Lukaszewicz D. Automotive Composite Design Process. FISITA World Automotive Congress. Maastricht, The Netherlands, 2014.
- [11] Beta CAE. ANSA; 2014.
- [12] Divis. ClearVU Analytics; 2014.
9. 著作権:
- 本資料は、"[Dirk Lukaszewicz et al.]"の論文:「[製造変動を含む自動車および航空宇宙複合材構造の設計および解析方法 (A Design and Analysis Method for Automotive and Aerospace Composite Structures including Manufacturing Variations)]」に基づいています。
- 論文ソース:https://www.researchgate.net/publication/268925382
本資料は上記の論文を要約したものであり、商業目的で無断使用することを禁じます。
Copyright © 2025 CASTMAN. All rights reserved.