本紹介記事は、[Special Casting & Nonferrous Alloys]誌に掲載された論文「Manufacturing of Thin-walled Impeller Based on Optimization of Sand Mold 3D Printing Forming Process」の研究内容を紹介するものです。
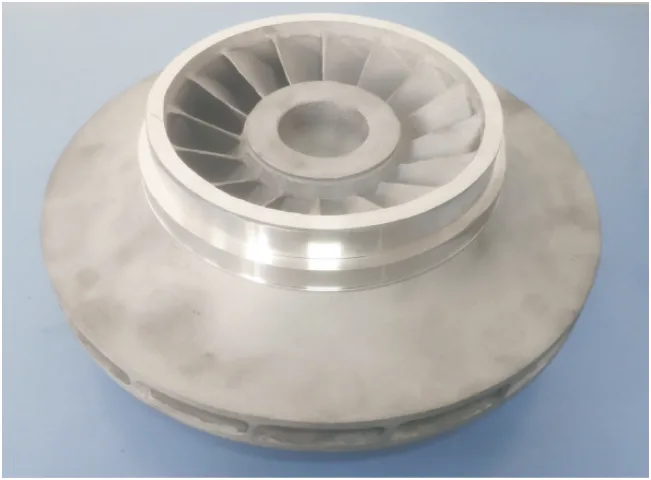
1. 概要:
- タイトル: 薄肉インペラーの砂型3Dプリント成形プロセス最適化による製造 (Manufacturing of Thin-walled Impeller Based on Optimization of Sand Mold 3D Printing Forming Process)
- 著者: AI Yumeng, YOU Zhiyong, LIU Shilong, ZHANG Shenghui, ZHANG Yaofeng, LI Chengkun, TAN Rui
- 発行年: 2025年
- 発行ジャーナル/学会: Special Casting & Nonferrous Alloys
- キーワード: 3D Printing Sand Mold, Forming Process, Response Surface Method, Low Pressure Die Casting (3Dプリント砂型、成形プロセス、応答曲面法、低圧鋳造)
2. 概要 / はじめに
本研究では、砂型3Dプリント成形プロセスを最適化するためにBox-Behnken応答曲面法を採用しました。引張強度とガス発生量を性能応答として、樹脂インクジェット量、硬化剤添加量、およびプリント層厚さの水平範囲を決定することに焦点を当てました。数値シミュレーションを用いて最適なプロセスパラメータの組み合わせを特定し、その後、薄肉インペラーの試作を低圧鋳造プロセスを用いて検証しました。その結果、樹脂インクジェット量が1.44%、硬化剤添加量が0.21%、プリント層厚さが0.30 mmの場合、プリントされた砂型は2.15 MPaの引張強度と8.92 mL/gのガス発生量を示し、予測値とほぼ一致することが示されました。これらの最適化された条件下では、インペラー鋳物は完全で明確な形状を示し、要求される技術仕様を満たしました。本研究は、高強度、低ガス発生量、および材料消費量の削減を達成するために3Dプリント砂型成形プロセスを最適化することにより、同様の製品の製造に貴重な参考資料を提供することを目的としています。
3. 研究背景:
研究トピックの背景:
砂型3Dプリント技術の鋳造分野での応用が拡大するにつれて、鋳物の設計概念は従来の造型技術の制約を受けなくなり、特に航空宇宙、自動車、造船などの産業において、より複雑、薄肉、軽量、高精度な鋳物設計へと進化しています[1-3]。これにより、高品質の部品成形を保証するために、優れた技術的性能を備えた3Dプリント鋳造砂型が必要となっています。従来の方法では、添加剤と生砂を混合・攪拌し、一定の強度の砂型を形成し、それを鋳型箱に入れ、手作業または機械的に砂型を突き固めて造型を完了していました。対照的に、砂型3Dプリントは、粉末ベースの離散堆積とマイクロドロップレット噴射の原理に基づいています[4]。
既存研究の現状:
既存の最適化手法は、多くの場合、単一変数アプローチを使用しており、パラメータ間の相互作用効果を捉えられていません。この制約から、多変量統計技術、特に応答曲面法(RSM)の採用が進んでいます。先行研究では、鋳造プロセス最適化におけるRSMの有効性が実証されています。例えば、Li Ningら[8]は、アルミニウム合金ホイールの低圧鋳造パラメータを最適化するためにRSMを使用し、鋳型寿命と鋳造効率を考慮しました。Wang Yanfengら[9]は、Box-Behnken RSMと数値シミュレーションを用いてA357アルミニウム合金の金型鋳造を最適化しました。Zhan Quan Quanら[10]は、引張強度を最大化するために、3Dプリントフラン樹脂砂の最適パラメータを決定するためにRSMを使用しました。
研究の必要性:
バインダーと硬化剤の含有量を増やすと、3Dプリント砂型の強度は向上しますが、ガス発生量も増加し、成形精度が低下する可能性があります[5]。さらに、材料消費量の増加は、印刷コストを上昇させます。逆に、砂敷きプロセスの層厚さを調整すると、印刷効率と鋳型強度の両方に影響を与えます[6]。層を薄くすると印刷時間が長くなり、層を厚くすると粒子間の結合力が弱まる可能性があります。したがって、性能、材料使用量、およびコスト効率のバランスを取るためには、3Dプリントプロセスを最適化することが重要です。
4. 研究目的と研究課題:
研究目的:
本研究は、応答曲面法(RSM)を用いて3Dプリント砂型の成形プロセスを最適化することを目的としています。目標は、薄肉インペラー鋳物用の高引張強度、低ガス発生量、および材料消費量の削減を達成するために、樹脂インクジェット量、硬化剤添加量、およびプリント層厚さの最適な組み合わせを特定することです。この研究はまた、インペラー試作品の低圧鋳造を通じて最適化されたプロセスを検証し、同様の用途への参考資料を提供することを目指しています。
主要な研究課題:
- 樹脂インクジェット量、硬化剤添加量、およびプリント層厚さが、3Dプリント砂型の引張強度とガス発生量に及ぼす影響を調査する。
- Box-Behnken計画(BBD)と応答曲面法(RSM)を用いて、引張強度とガス発生量の予測モデルを確立する。
- 薄肉インペラー鋳造において、引張強度とガス発生量のバランスが取れた3Dプリント砂型の最適なプロセスパラメータを決定する。
- 低圧鋳造を用いて薄肉インペラーを製造および試験することにより、最適化されたプロセスパラメータを検証する。
5. 研究方法
研究計画:
本研究では、3Dプリントプロセスを最適化するために、応答曲面法(RSM)内のBox-Behnken計画(BBD)アプローチを採用しました。樹脂インクジェット量(A)、硬化剤添加量(B)、およびプリント層厚さ(C)を独立変数として、3因子3水準の実験計画を利用しました。引張強度とガス発生量を応答変数として選択しました。
データ収集方法:
BBDマトリックス(論文中の表5)に従ってパラメータを変化させながら、ExOne S-Max Pro 3Dプリンターを使用して「8」の字型の試験片を印刷しました。原材料はシリカ砂、バインダーは3Dプリントフラン樹脂、硬化剤は3Dプリント硬化剤でした(仕様は表1〜3を参照)。
分析方法:
分散分析(ANOVA)を用いて、モデルとプロセスパラメータの有意性を評価しました。応答曲面プロットと等高線プロットを作成して、変数と応答間の関係を視覚化しました。数値最適化を実行して、最適なプロセスパラメータの組み合わせを予測しました。引張強度はSWY-Bデジタル表示油圧強度試験機を使用して試験し、ガス発生量はGET-IIインテリジェントガス発生試験機を使用して測定しました。
研究対象と範囲:
本研究は、ZL101A合金製の薄肉インペラーの鋳造に使用される砂型の3Dプリントプロセス最適化に焦点を当てました。この研究は、特定の材料(シリカ砂、フラン樹脂、および硬化剤)と装置(ExOne S-Max Proプリンター、SWY-B引張試験機、GET-IIガス発生試験機)を使用して実施されました。調査結果は、試験されたパラメータ範囲と材料系に固有のものです。
6. 主な研究成果:
主要な研究成果:
- 最適パラメータ: 最適化されたプロセスパラメータは、樹脂インクジェット量1.44%、硬化剤添加量0.21%、およびプリント層厚さ0.30 mmと決定されました。
- 引張強度とガス発生量: これらの最適化された条件下では、プリントされた砂型は2.15 MPaの引張強度と8.92 mL/gのガス発生量を達成し、予測値とほぼ一致しました。
- インペラー鋳物の品質: 最適化された3Dプリント砂型を使用して製造された薄肉インペラー鋳物は、完全で明確な形状を示し、技術的要件を満たしました。X線検査では、重要な領域に鋳造欠陥は見られず、寸法精度は±0.9 mm以内で、DCTG6公差規格を満たしていました(図8)。
提示されたデータの分析:
- 引張強度の最適化: RSM分析により、樹脂インクジェット量とプリント層厚さが引張強度に大きく影響することが示されました(表6、図2、図3)。樹脂含有量が多いほど一般的に引張強度は向上しますが、層厚が増加すると低下する傾向があります。硬化剤添加量は、試験範囲内では有意な影響を示しませんでした。
- ガス発生量の最適化: RSM分析により、樹脂インクジェット量がガス発生量に最も大きな影響を与える要因であることが示されました(表7、図4、図5)。ガス発生量は樹脂含有量が多いほど増加します。プリント層厚さと硬化剤添加量は、ガス発生量への影響はそれほど顕著ではありませんでした。
- モデルの検証: 引張強度とガス発生量の両方に対するRSMモデルからの予測値は、最適化された条件下で実験的に測定された値とほぼ一致しており、モデルの精度が検証されました(表8)。
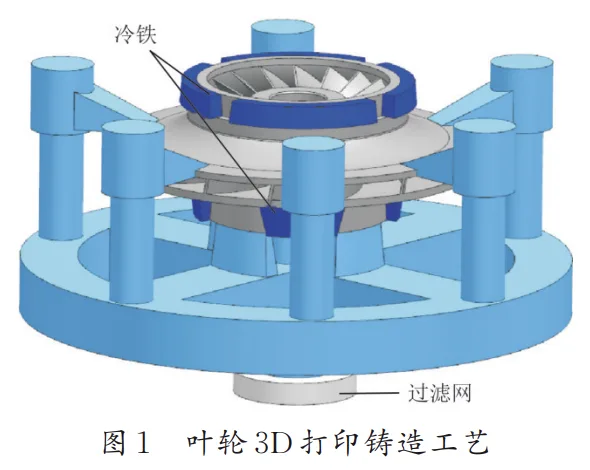
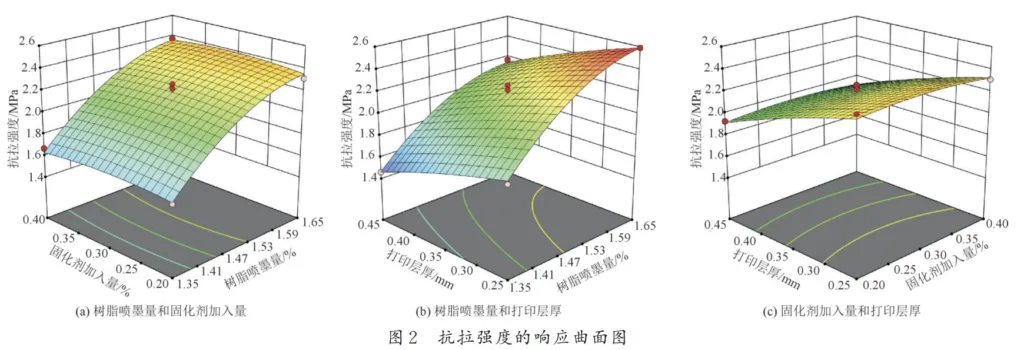
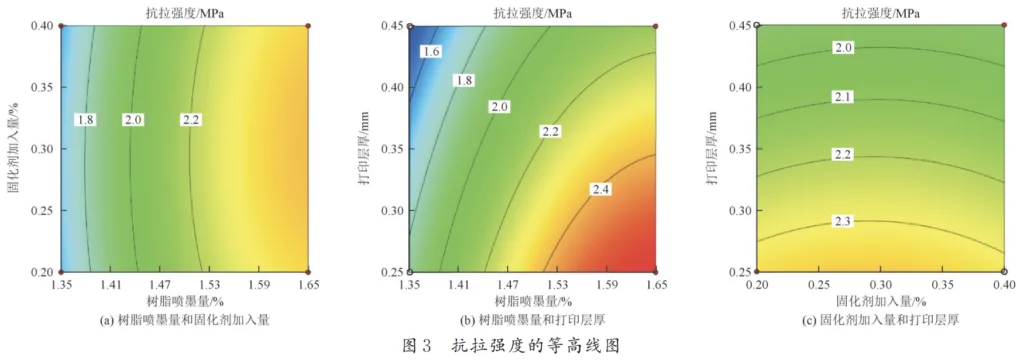
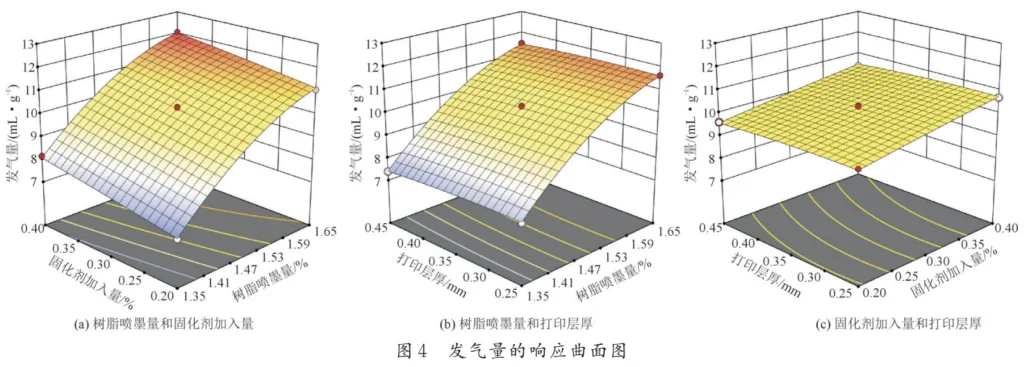
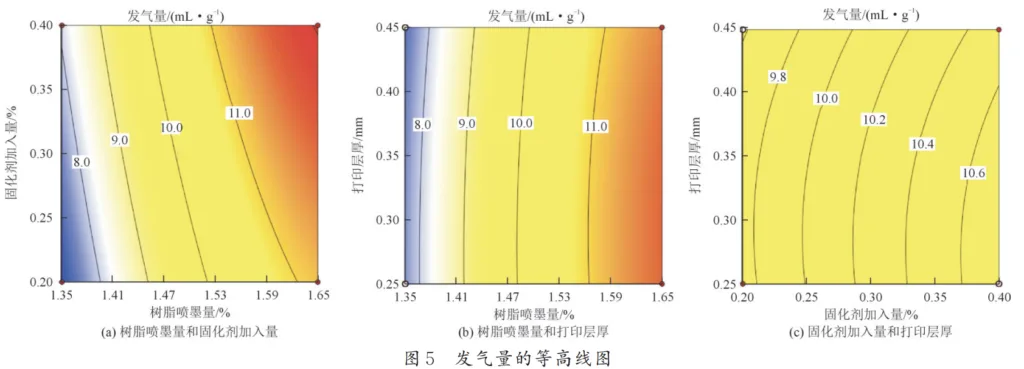
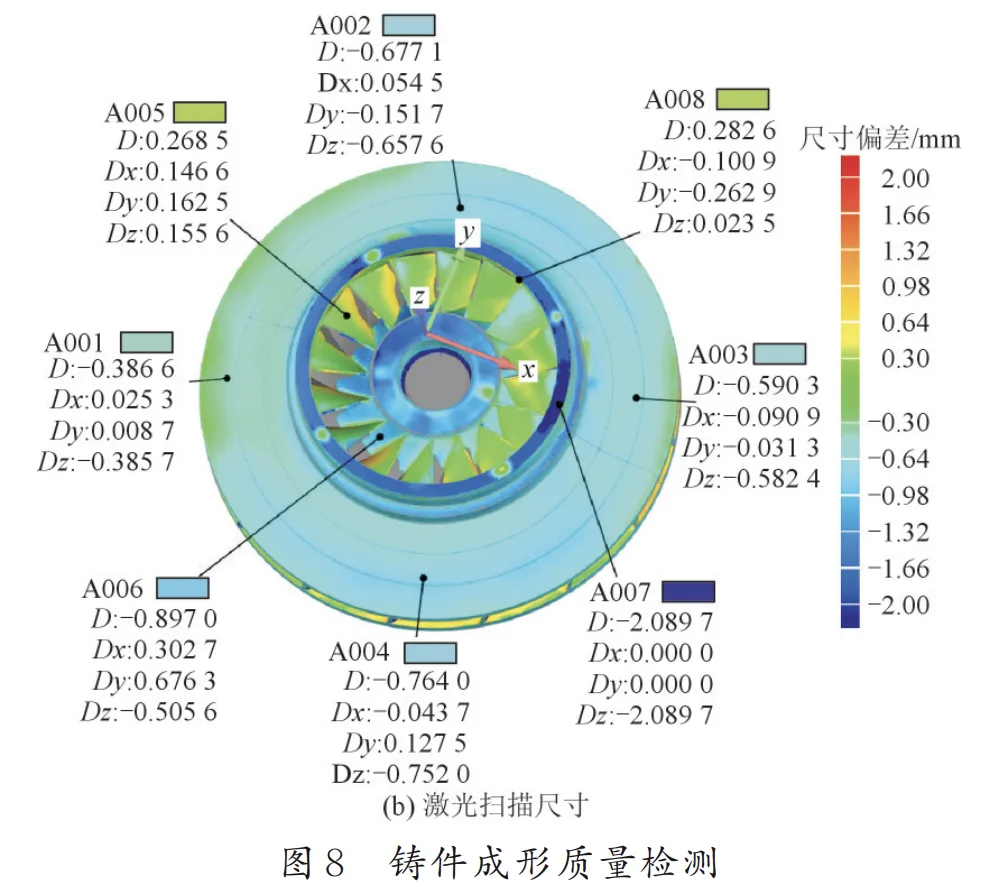
図のリスト:
- Fig.1 インペラーの3Dプリント鋳造技術 (3D printing casting technique for impeller)
- Fig.2 引張強度の応答曲面プロット (Response surface plot of tensile strength)
- Fig.3 引張強度の等高線プロット (Contour plot of tensile strength)
- Fig.4 ガス発生量の応答曲面プロット (Response surface plot of gas evolution)
- Fig.5 ガス発生量の等高線プロット (Contour plot of gas evolution)
- Fig.6 インペラー鋳造用3Dプリント砂型コア構造の設計 (Design of 3D printed sand core structure for impeller casting)
- Fig.7 インペラー鋳物の製品 (Product of impeller casting)
- Fig.8 鋳物の成形品質検査 (Quality inspection of casting forming)
7. 結論:
主な調査結果の要約:
本研究では、Box-Behnken応答曲面法を用いて、薄肉インペラー鋳造に使用される砂型の3Dプリントプロセスを最適化することに成功しました。特定された最適パラメータは、樹脂インクジェット量1.44%、硬化剤添加量0.21%、およびプリント層厚さ0.30 mmでした。これらのパラメータにより、2.14 MPaの引張強度と8.92 mL/gのガス発生量を持つ砂型が得られました。薄肉インペラーの低圧鋳造による検証により、最適化されたプロセスが、良好な寸法精度と最小限の欠陥を備えた高品質の鋳物を製造する上で効果的であることが実証されました。
研究の学術的意義:
本研究は、砂型3Dプリントにおけるプロセスパラメータ最適化の理解に貢献します。鋳造用アディティブマニュファクチャリングにおいて、複数の相反する性能指標(引張強度とガス発生量)を最適化する上で、RSMの効果的な応用を実証しています。この研究は、主要なプロセスパラメータの個々の影響と相互作用の影響に関する貴重な洞察を提供し、この分野における科学的知識基盤を強化します。
実用的な意義:
最適化された3Dプリントプロセスは、薄肉インペラー鋳物や同様の部品の製造に実用的な利点をもたらします。材料消費量(樹脂と硬化剤)を削減し、印刷効率(層厚の増加)を向上させることで、プロセスはより費用対効果が高く、環境に優しいものになります。達成された鋳型強度と低ガス発生量は、高い鋳造品質を保証し、欠陥を減らし、全体的な生産歩留まりを向上させます。
研究の限界と今後の研究分野:
本研究は、特定の材料系(シリカ砂、フラン樹脂、および硬化剤)と特定の3Dプリンターモデルに限定されています。今後の研究では、これらの調査結果の他の材料や印刷システムへの適用可能性を検討することができます。さらに、今後の研究では、表面仕上げや透磁率などの他の性能指標を調査し、3Dプリント砂型の後処理ステップの最適化を検討することができます。最適化された3Dプリント鋳型で製造された鋳物の長期的な性能と耐久性も、今後の調査分野となる可能性があります。
8. 参考文献:
- [1] MOHIUDDEN M V, HUSSAINY SF, KRISHNAIAH A, et al. Experimental investigation to produce thin-walled sand casting using combination of casting simulation and additive manufacturing techniques [J]. The International Journal of Advanced Manufacturing Technology, 2017, 90(9-12): 3 147-3 157.
- [2] HAWALDAR N, ZHANG J. A comparative study of fabrication of sand casting mold using additive manufacturing and conventional process [J]. The International Journal of Advanced Manufacturing Technology, 2018, 97(1-4): 1037-1 045.
- [3] 李彬, 廖慧敏, 曾明, 等. 3D打印在砂型铸造中的应用及发展现状[J]. 特种铸造及有色合金, 2020, 40(9): 953-957.
- [4] MITRA S, EL MANSORI M, RODRINUEZ DE CASTRO A, et al. Study of the evolution of transport properties induced by additive processing sand mold using X-ray computed tomography [J]. Journal of Materials Processing Technology, 2020, 277: 116 495.
- [5] 余洛生, 刘丰, 刘丽敏, 等. 3D打印呋喃树脂砂型成形精度研究与控制[J]. 铸造, 2022, 71(11): 1407-1412.
- [6] 高桂丽, 张伟坤, 杜志敏, 等. 基于喷墨3D打印的铸造砂型(芯)成形工艺参数应用研究[J]. 铸造, 2020, 69(6): 627-631.
- [7] BEZERA MA, SANTELLI RE, OLOVEIRA E P, et al. Response surface methodology (RSM) as a tool for optimization in analytical chemistry[J]. Talanta, 2008, 76(5): 965-977.
- [8] 李宁, 朱培浩, 胡亚辉, 等. 铝合金轮毂低压铸造的模具设计及工艺优化[J]. 特种铸造及有色合金, 2017, 37(5): 494-497.
- [9] 王彦凤, 杨正, 邱常明, 等. 基于响应面法的A357铝合金金属型铸造工艺优化[J]. 特种铸造及有色合金, 2019, 39(10): 1 137-1 142.
- [10] 詹泉泉, 朱德智, 陈维平, 等. 响应面法优化3D打印呋喃树脂砂工艺条件[J]. 特种铸造及有色合金, 2019, 39(9): 981-983.
- [11] 吴士平, 王晔, 吴光然, 等. ZL205A合金壳体铸件低压铸造工艺研究[J]. 特种铸造及有色合金, 2012, 32(9): 811-813.
- [12] 韩雯雯, 杨洪英, 张勤, 等. 响应曲面法优化黄金氰渣亚硫酸钠-空气氧化法脱氰工艺[J]. 中国有色金属学报, 2023, 33(4): 1278-1 286.
- [13] MITRA S, ANTONIO RDC, MOHAMED E M. On the rapid manufacturing process of functional 3D printed sand molds [J]. Journal of Manufacturing Processes, 2019, 42: 202-212.
- [14] BRYANT N, FRUSH T, THIEL J, et al. Influence of machine parameters on the physical characteristics of 3D-printed sand molds for metal casting [J]. International Journal of Metalcasting, 2021, 15 (2): 361-372.
- [15] WANG Y, YU R L, YIN S K, et al. Effect of gel time of 3D sand printing binder system on quality of sand mold/core [J]. China Foundry, 2021, 18(6): 581-586.
- [16] 彭倩, 陈晓龙, 田超, 等. 不同固化剂加入量对自硬呋喃树脂砂性能的影响[J]. 铸造, 2020, 69(7): 748-751.
- [17] VAEZIM, CHUA C K. Effects of layer thickness and binder saturation level parameters on 3D printing process [J]. The International Journal of Advanced Manufacturing Technology, 2011, 53 (1-4): 275-284.
9. 著作権:
- この資料は、"AI Yumeng, YOU Zhiyong, LIU Shilong, ZHANG Shenghui, ZHANG Yaofeng, LI Chengkun, TAN Rui" の論文「Manufacturing of Thin-walled Impeller Based on Optimization of Sand Mold 3D Printing Forming Process」に基づいています。
- 論文ソース: DOI: 10.15980/j.tzzz.T20240194
この資料は上記論文を紹介するために作成されたものであり、商業目的での無断使用は禁止されています。
Copyright © 2025 CASTMAN. All rights reserved.