この論文サマリーは、['自動車部品用圧力ダイカスト金型の設計と解析']という論文に基づいており、['Global Journal of Researches in Engineering: A Mechanical and Mechanics Engineering'] に発表されました。
1. 概要:
- タイトル: 自動車部品用圧力ダイカスト金型の設計と解析 (Design and Analysis of Pressure Die Casting Die for Automobile Component)
- 著者: Y. Abdulfatah Abdu, T. M. Shafii, K. K. Dubey & Prof U. K. Gupta
- 発行年: 2016年
- 発行ジャーナル/学会: Global Journal of Researches in Engineering: A Mechanical and Mechanics Engineering
- キーワード: 圧力ダイカスト, 自動車産業, アルミニウム合金, Solid Works, 3次元フロー, Pro-Engineer (pressure die casting, automobile industry, aluminium alloys, solid works, 3-diamensional flow, pro-engineer)
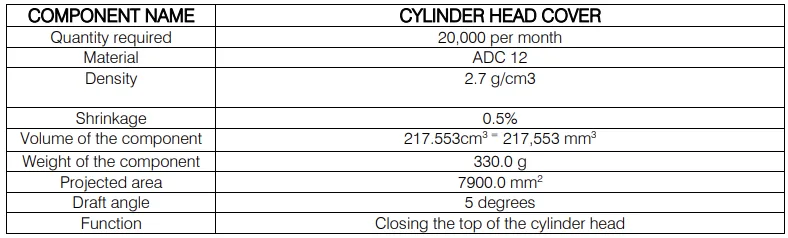
2. 研究背景:
研究トピックの背景:
本論文は、圧力ダイカストプロセスの技術における金型の設計と解析方法の一つについて記述しています。圧力ダイカストは、最も近い公差を維持し、すべての機械加工を削減し、少量生産に最適な選択肢となり得るプロセスです。正確で軽量な部品は自動車産業の前提条件の一つであり、軽量設計と正確な製品は自動車の燃料消費量に直接影響を与え、結果としてユーザーの満足度を高めます。これらの要求は、アルミニウム合金、高強度鋼、および構造部品用の繊維強化複合材料を使用して満たされます。
既存研究の現状:
既存の研究では、ダイカストにはコールドフィル、ドロス、アルミナスキンなどの鋳造欠陥が一般的に存在することが示されています。研究では、ランナーとスプルーの設計が疲労強度に与える影響、ダイ設計のリードタイムとサイクルタイムを短縮するための統合CAD/CAMシステム、および球状黒鉛鋳鉄で作られた重要な自動車部品であるフロントアクスルハウジングにおける収縮やガス気孔などの欠陥に対するゲートシステムの設計の影響が調査されています。さらに、エジェクター、ダイベース、およびゲート設計を最適化するためのコンピュータ支援ダイ設計システムが開発されました。不均一な冷却とランナーおよびゲートシステムの設計との相関関係も、フローシミュレーションを使用して調査されています。
研究の必要性:
本研究は、圧力ダイカストにおける収縮空洞、ガス欠陥、材料欠陥などの欠陥を最小限に抑える必要性から生まれました。論文では、鋳造プロセスのすべての側面を制御し、無駄を防止するための包括的な金型設計と解析の重要性を強調しています。特に、本研究はCAE(Computer Aided Engineering)ソフトウェアを使用して金型を設計し、ゲートシステムを開発し、これらの欠陥を特定して軽減することにより、鋳造品質と効率を向上させることを目的としています。
3. 研究目的と研究課題:
研究目的:
本研究の主な目的は、自動車部品用の圧力ダイカスト金型を設計および解析し、鋳造欠陥を最小限に抑え、効率的な生産のために金型設計を最適化することです。これには、収縮空洞、ガス欠陥、および注入材料の欠陥などの問題に対処するために、CAEソフトウェアを使用して金型およびゲートシステムを開発することが含まれます。
主要な研究課題:
主要な研究目標は以下のとおりです。
- 重要な寸法と充填解析を考慮して、自動車部品用の圧力ダイカスト金型を設計します。
- 鋳造欠陥を特定し、最小限に抑えるためのツールとゲートシステムを開発します。
- 設計、解析、およびテストのためにCAEソフトウェア(Solid Works, 3-Diamesional Flow, Pro-Engineer)を活用します。
- ランナーシステム設計、冷却システム、およびプロセスパラメータを含む、ダイカストに最適なパラメータを決定します。
研究仮説:
本論文では明示的な研究仮説は述べられていませんが、暗黙の仮説として以下を推測できます。
- CAEソフトウェアで解析された適切に設計された金型およびゲートシステムは、自動車部品の鋳造欠陥を大幅に削減するでしょう。
- 最適化されたランナーおよびゲートシステムの設計は、ダイキャビティの完全かつバランスの取れた充填を保証し、鋳造品質を向上させるでしょう。
- CAEソフトウェアシミュレーションは、潜在的な鋳造欠陥を正確に予測し、軽減するのに役立ち、より効率的な金型設計プロセスにつながるでしょう。
4. 研究方法:
研究デザイン:
本研究では、CAEソフトウェアを利用して圧力ダイカストプロセスをシミュレーションおよび最適化する設計および解析方法論を採用しています。設計プロセスには、部品の特定とデータ収集から、Solid Worksソフトウェアを使用した3次元モデリングと2次元図面の作成まで、いくつかのステップが含まれます。設計には、材料の収縮率の考慮が含まれており、ランナーシステム設計と充填解析には3次元フロー解析を使用しています。
データ収集方法:
本研究では、主に理論計算とCAEソフトウェアシミュレーションをデータ生成方法として利用しています。部品の詳細、材料特性(ADC 12アルミニウム合金)、および80T機械の機械仕様は、設計計算およびシミュレーションの入力パラメータとして使用されます。本論文では、実験的データ収集は明示的に言及されていません。
分析方法:
分析方法は次のとおりです。
- 設計計算: キャビティ数、トン数要求量、ショット重量、充填率、充填時間、ドライショット流量、金属圧力、およびランナー寸法を決定するための手動計算。これらの計算は、確立されたダイカストの原理と公式に基づいています。
- 3次元フローシミュレーション: 「3次元フロー」ソフトウェアを活用して、垂直および水平部品配置の両方で充填プロセスをシミュレーションします。この解析は、溶融金属の流動挙動を可視化し、気孔などの潜在的な欠陥を特定することを目的としています。
- P-Q²ダイアグラム分析: ゲートシステム設計を最適化するために、金属圧力と流量の関係を分析するためにP-Q²ダイアグラムを使用します。
研究対象と範囲:
本研究は、特定の自動車部品であるADC 12アルミニウム合金製の「シリンダーヘッドカバー」用の圧力ダイカスト金型の設計に焦点を当てています。範囲は、ゲートシステムとランナーの設計、冷却システムの考慮事項、およびシミュレーションによる欠陥分析を含む、金型設計と解析の側面に限定されています。設計および解析作業は、ハリヤナ州グルガオンのAutomotive Private Limitedで実施されました。
5. 主な研究成果:
主要な研究成果:
主な研究成果は、最適化された金型設計パラメータを概説する表2「結果の概要」に要約されています。
- キャビティ数: 1
- トン数要求量: 80 T
- ショット重量: 0.9kg
- 充填率: 0.6
- 充填時間: 54ミリ秒
- 最大静圧: 838.02kgf/cm2
- ドライショット流量: 10,692.62 cm3/sec
- 最大金属圧力: 131.5 kgf/cm2
- 最小金属圧力: 51.4 kgf/cm2
- 流量: 4,834.5 cm3/sec
- 金属圧力 (P): 91.5 kgf/cm2
- 流量 (Q): 7,255.7 cm3/sec
- ゲート面積: 69 mm2
- ゲート長: 23mm
- ランナーサイズ: L=86.7 mm2, D= 10.42mm, W= 20.84 mm
フローシミュレーション解析の結果、水平部品配置は垂直配置よりも気孔欠陥率が低いことが示されました。充填パターンシミュレーションは、溶融アルミニウムがゲートに入り、0.5秒後にキャビティを効果的に充填し始めることを示しました。
データ解釈:
設計計算とシミュレーションの結果は、シリンダーヘッドカバー用の圧力ダイカスト金型を製造するための包括的なパラメータセットを提供します。P-Q²ダイアグラム分析(図2.1)とフローシミュレーションの可視化(図3.01および3.02)は、最適化された設計パラメータを裏付けています。結果は、設計された金型およびゲートシステムが、欠陥を最小限に抑えた鋳造品を製造できることを示唆しています。水平部品配置の選択は、気孔の減少のために好ましいです。
図のリスト:
- 図 2.1: P-Q2 ダイアグラム
- 図 2.1.1: コアインサート
- 図 2.1.2: キャビティインサート
- 図 2.1.3: 金型キャビティとコアアセンブリ
- 図 2.1.4: 組み立てられた金型ツール
- 図 3.01: 部品の垂直配置
- 図 3.02: 部品の水平配置
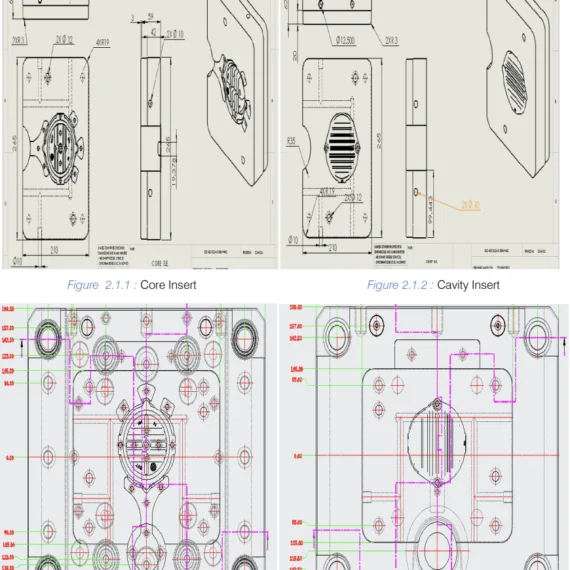
6. 結論:
主な結果の要約:
本研究では、CAEソフトウェアを使用して自動車用シリンダーヘッドカバー用の圧力ダイカスト金型を設計および解析することに成功しました。この研究では、鋳造欠陥を最小限に抑えることを目的として、計算とフローシミュレーションを通じて最適な金型設計パラメータを決定しました。水平部品配置は、垂直配置と比較して気孔を削減するのに優れていることがわかりました。シミュレーション結果は、設計されたゲートシステムと充填プロセスの有効性を検証しました。
研究の学術的意義:
本研究は、CAEツールを使用した設計最適化と欠陥最小化のための体系的なアプローチを示すことにより、ダイカスト金型設計の知識体系に貢献しています。特定の自動車部品用の圧力ダイカスト金型を設計する際に、理論計算とシミュレーション技術を適用した実用的な例を提供します。この研究は、気孔を軽減するために金型設計において部品の向き(垂直対水平)を考慮することの重要性を強調しています。
研究の実践的意義:
本研究の知見は、特に自動車産業のダイカストメーカーにとって直接的な実用的な意味を持ちます。最適化された金型設計パラメータと提示された方法論は、シリンダーヘッドカバー用の金型製造に直接適用でき、潜在的に鋳造品質の向上、欠陥の削減、および生産効率の向上につながる可能性があります。設計プロセスでCAEソフトウェアを使用すると、試行錯誤的な金型製作に関連する開発時間とコストを大幅に削減できます。
研究の限界:
本研究は、単一の自動車部品(シリンダーヘッドカバー)および材料(ADC 12)用の金型設計および解析の範囲に限定されています。解析は主にシミュレーションに依存しており、金型設計および鋳造プロセスの実験的検証は本論文では提示されていません。さらに、最適化では限られたプロセスパラメータセットのみが考慮されました。
7. 今後のフォローアップ研究:
- 今後のフォローアップ研究の方向性
今後の研究方向には以下が含まれます。- シミュレーション結果を確認し、実際の鋳造品質と欠陥率を評価するための、設計された金型と鋳造プロセスの実験的検証。
- より包括的な最適化のためにpq²関係を組み込むことにより、溶融金属温度、射出速度、吐出圧力、キャビティ充填速度、および冷却速度などのより広範囲なプロセスパラメータを含めるように最適化研究を拡大します。
- この設計および解析方法論の他の自動車部品および異なるダイカスト合金への適用を調査します。
- さらなる探求が必要な分野
さらなる探求が必要な分野は次のとおりです。- 冷却システム設計とその鋳造凝固および欠陥形成への影響に関する詳細な分析。
- 従来の設計と比較して、最適化された金型設計を通じて達成された欠陥削減の定量的評価。
- 圧力ダイカスト製造におけるCAE駆動型金型設計の実装の費用便益分析。
8. 参考文献:
- 1. http://www.custompartnet.com/wu/die-casting (2015年5月20日アクセス).
- 2. Kong, L.X., She, F.H., Gao, W.M., Nahavandi, S., Hodgson, P.D. (2008). Integrated optimization system for high pressure dies casting processes. Journal of materials processing technology 201, 629-634.
- 3. Schey, A. J., Introduction to Manufacturing Processes, McGraw-Hill, Singapore, 1987.
- 4. Seo, P.K., Kim, D.U., Kang, C.G., (2006). Effects of die shape and injection conditions proposed with numerical integration design on liquid segregation and mechanical properties in semi-solid die casting process. Journal of Materials Processing Technology 176, 45–54.
- 5. Avalle, M., Belingardi, G., Cavatorta, M.P., Doglione, R., 2002. Casting defects and fatigue strength of a die cast aluminium alloy: a comparison between standard specimens and production components. International Journal of Fatigue 24, 1–9.
- 6. Yue, S., Wang, G., Yin, F., Wang, Y., Yang, J., (2003). Application of an integrated CAD/CAE/CAM system for die casting dies. Journal of Materials Processing Technology 139, 465-468.
- 7. Lin, J. C. (2002). 'Selection of the Optimal Gate Location for a Die-Casting Die with a Freeform Surface,' Int J Adv Manuf Technol, 19(4), pp.278-284.
- 8. Manjunath Swamy H. M., J. R. Nataraj, C. S. Prasad (2012) "Design Optimization of Gating System by Fluid Flow and Solidification Simulation for Front Axle Housing” International Journal of Engineering Research and Development, Vol. 4, Issue 6, pp. 83-88.
- 9. Woon, Y. K. and Lee, K. S. (2004), 'Development of a die design system for die casting,' Int J Adv Manuf Technol, Vol. 23, Issue (5-6), pp.399-411.
- B. Vijaya R., C.E., Vishal C., A. Arun K., S. M. Asif, G. Riyaz M., D. V. Raj, C. Suresh K. (2014). Analysis and Optimization of Gating System for Commutator End Bracket. Procedia Materials Science 6, 1312 – 1328.
- Abdu Y A. (2016). Implementation of Lean Manufacturing: A Case Study at ASK Automotive Private Limited (India), Int. J. Adv. Res. Sci. Technol. 5(1), 556-562.
9. 著作権:
- この資料は、"[Y. Abdulfatah Abdu, T. M. Shafii, K. K. Dubey & Prof U. K. Gupta]"の論文:「[自動車部品用圧力ダイカスト金型の設計と解析]」に基づいています。
- 論文ソース: https://www.researchgate.net/publication/314175819
この資料は上記の論文に基づいて要約されており、商業目的での無断使用は禁止されています。
Copyright © 2025 CASTMAN. All rights reserved.