本紹介論文は、IOP Publishing が発行した「High strength aluminum alloys in car manufacturing(自動車製造における高強度アルミニウム合金)」の論文の研究内容です。
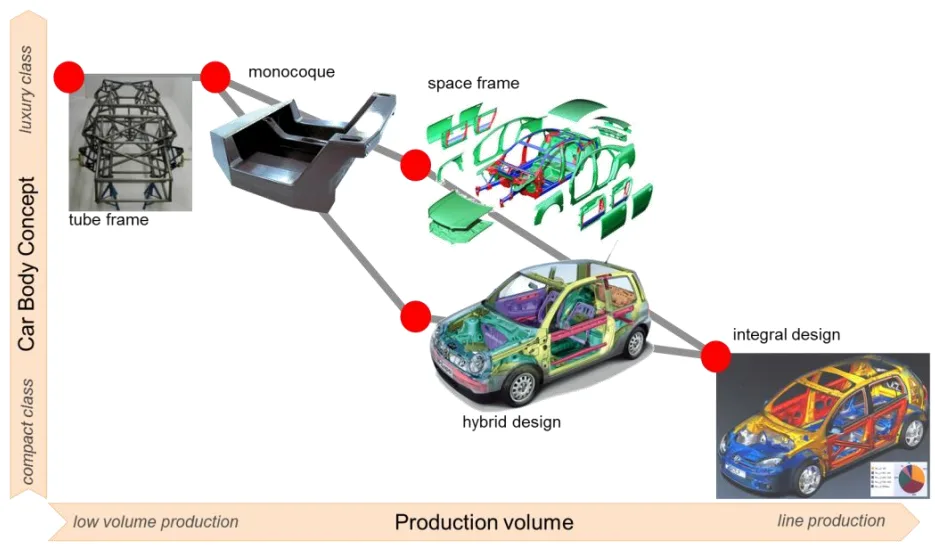
1. 概要:
- タイトル: High strength aluminum alloys in car manufacturing (自動車製造における高強度アルミニウム合金)
- 著者: M Tisza and Zs Lukács
- 出版年: 2018
- 掲載ジャーナル/学会: IOP Conference Series: Materials Science and Engineering, 418 (2018) 012033
- キーワード: aluminum alloys, lightweight design, car body construction, hot forming, formability, HFQ (アルミニウム合金、軽量設計、車体構造、熱間成形、成形性、HFQ)
2. 概要(Abstract)
近年、自動車製造に対しては、顧客側からの要求と、有害排出物を削減して環境保護を強化し、安全性、快適性、経済性を向上させるための法的要件の両面から、多くの要件が課せられています。これらのしばしば相反する要件を満たすために、軽量設計原則の適用が最も広く適用されている解決策の 1 つです。板金成形によって製造される車体要素に特に有効な、低コスト製造による軽量自動車構造物の製造には、2 つの主要なトレンドがあります。軽量合金材料、特にさまざまなアルミニウム合金の適用は、軽量車体構造の要件を満たすためのもう 1 つの可能な解決策と見なされています。アルミニウムは鋼材よりも軽量化の可能性がさらに高いですが、アルミニウムは鋼よりも成形性が低いです。アルミニウムのような軽い材料で鋼を置き換えることは、費用がかかり、簡単ではありません。これは、最近、アルミニウム合金の熱間成形が研究活動の最前線に登場した主な理由の 1 つです。この論文では、「軽量車両の大量生産のための低コスト材料処理技術」と題された共同欧州プロジェクト内で得られたいくつかの最近の結果を紹介します。
3. 研究背景:
研究テーマの背景:
自動車製造における主な開発トレンドは、顧客の要求 (低燃費、安全性、機能性、快適性の向上) と、より厳格な法的要件 (有害排出物の削減、衝突安全性の向上) によって推進されています [1]。軽量化は、これらの相反する要件を満たすための重要な戦略です。
以前の研究の現状:
従来、鋼は BIW (Body in White) 製造における主要な材料でした。しかし、高張力鋼 (DP 鋼、TRIP 鋼、XHSS、UHSS など) のさまざまな世代を含む開発が行われてきました [図 2]。特にアルミニウムのような軽量合金材料の適用は、効果的な解決策と見なされています。
研究の必要性:
アルミニウムは室温での成形性が鋼よりも低いため、直接的な代替は困難で費用がかかります。これにより、アルミニウム合金の熱間成形に関する研究が推進されています。
4. 研究目的と研究課題:
研究目的:
材料およびプロセス開発を含む要件を満たすための主な可能性をレビューし、将来の自動車製造ソリューションの可能性と開発動向を比較すること。共同欧州プロジェクト (軽量車両の大量生産のための低コスト材料処理技術) で得られた最近の結果を紹介すること。
コア研究:
車体製造におけるアルミニウム合金の使用時に発生する課題、特に室温での鋼と比較したアルミニウムの低い成形性に対処することに焦点を当てています。
5. 研究方法
- 文献レビュー: 既存の車体コンセプト (一体型設計、スペースフレーム、ハイブリッド設計、チューブフレーム、モノコック) と生産量および経済性との関係のレビュー [図 1] [3]。高張力鋼およびアルミニウム合金を含む材料開発、およびそれらの軽量化の可能性のレビュー [図 2] [4]。アルミニウムの歴史的概要と多材料アプローチに関するレビュー。
- 材料および成形性試験: いくつかの材料および成形性試験。修正中島試験 (光学ひずみ測定システムを備えたコンピューター制御汎用板金成形性試験機) を使用して成形性調査を実施しました。さまざまな温度での AA7075 アルミニウム合金の流動曲線および成形限界曲線の決定 [図 6]。
- 実験データ分析: 特に AA7075 アルミニウム合金について、さまざまな高温およびひずみ速度での成形性パラメータの分析。
6. 主要な研究結果:
主要な研究結果と提示されたデータ分析:
- アルミニウム合金は、基準 HSLA 鋼と比較して、大幅な軽量化の可能性 (25〜40%) を提供します [図 2]。
- 熱間成形は、室温での成形性が低い高強度アルミニウム合金を可能にする重要な技術です。
- HFQTM プロセス [図 5] [19] は、ホウ素合金鋼の熱間成形との類似点と相違点を持ち、強調されています。
- AA7075 アルミニウム合金の成形性は温度とともに増加し、最適な熱間成形温度は約 400°C です。[図6]
- AA7075 は T=450°C で流動曲線を持ち [図 6.a]、この温度を超えると、熱間単軸試験での破断ひずみが減少しました [図 6.b]。
図名リスト:
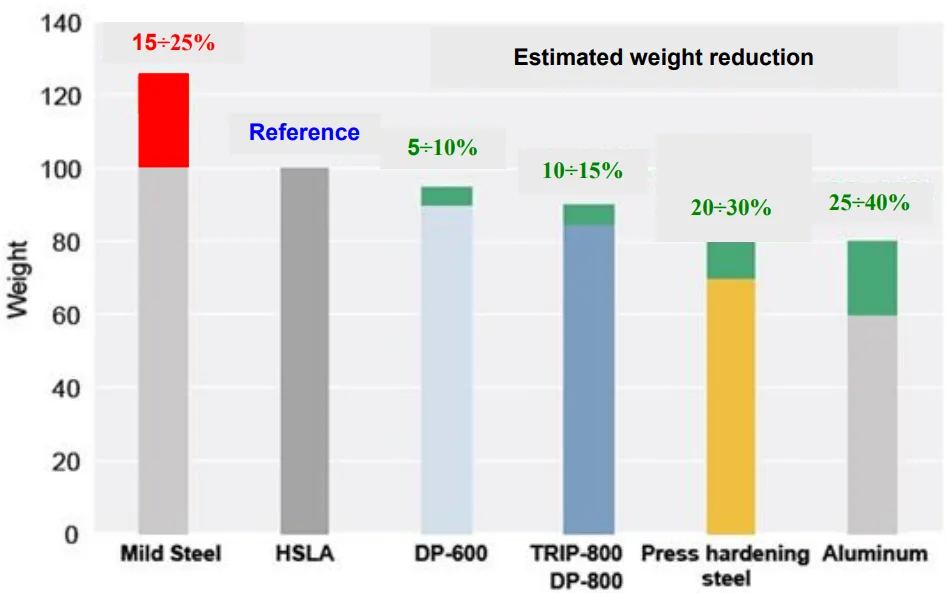

![Figure 4. Affordability of weight reduction using various multi-material concepts [15].](https://castman.co.kr/wp-content/uploads/image-1529-1024x539.webp)
![Figure 5. Basic principle of Hot Forming and QuenchingTM of aluminum alloys [19].](https://castman.co.kr/wp-content/uploads/image-1530-1024x344.webp)
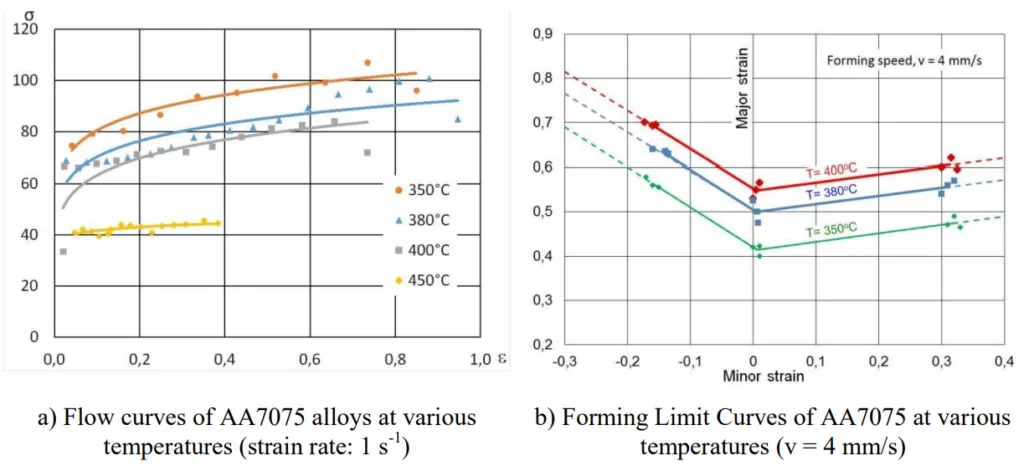
- 図 1. 生産量の関数としての車体コンセプト。
- 図 2. 車体製造におけるさまざまな高強度材料の軽量化の可能性。
- 図 3. 車体製造における多材料コンセプト。
- 図 4. さまざまな多材料コンセプトを使用した軽量化の実現可能性 [15]。
- 図 5. アルミニウム合金の熱間成形および焼入れ™ の基本原理 [19]。
- 図 6. さまざまな温度での AA7075 合金の流動曲線と成形限界曲線。
7. 結論:
主要な調査結果の要約:
- 高張力鋼およびアルミニウム合金の使用を含む軽量構造の原則は、現代の自動車の要件を満たすために非常に重要です。
- HFQ などの熱間成形プロセスは、高強度アルミニウム合金を効果的に利用するために不可欠です。
- アルミニウム合金の材料特性と成形限界は、熱間成形中の温度とひずみ速度に大きく依存します。
- 高強度アルミニウム合金の適用は大幅に増加しています。
今後の研究の可能性のある分野:
- 急速加熱/冷却および他の製造プロセス (塗装ベーキングなど) との統合によるサイクル時間の短縮を含む、熱間成形プロセスのさらなる最適化。
- 自動車用途向けのさまざまなアルミニウム合金の継続的な調査と特性評価。
- 多材料軽量構造に関するさらなる研究。
8. 参考文献:
- [1] Tisza M (2015) Metal Forming in the automotive industry, Miskolc University Press, p. 294 ISBN 978-963-358-082-0
- [2] Czinege I (2017) Comparative analysis of steel and aluminum sheets, Proc. 16th Metal Forming Conf. Miskolc-Hungary
- [3] Liewald M and Schleich R (2007) Robust processes in sheet metal forming in car body manufacturing with regard to production volume, Proc. of IDDRG 2007, Győr, Hungary, 21-23. May 2007. pp. 11-20.
- [4] Tisza M (2013) Recent development trends in sheet metal forming, Int. J. Microstructure and Material Prop. 8. No. 1-2. pp. 125-139.
- [5] Tisza, M (2014) Advanced materials in sheet metal forming, Key Engineering Materials, 581 pp. 137-142. DOI:10.4028/www.scientific.net/KEM.581.137
- [6] Ghassemieh E (2011) Materials in Automotive Application – State of the Art and Prospects, in New Trends and Developments in Automotive Industry, InTech Open Publications, DOI: 10.5772/1821
- [7] Banik J et. al (2013) Warmumformung im Automobilbau, Süddeutsche Verlag, Munich, p. 84.
- [8] Lin Jianguo et. al (2011) A method of forming a component of complex shape from aluminum alloy sheet, GB 2473298 British Patent
- [9] Keeler S, Kimchi M and Mooney, P (2017) Advanced High Strength Steels – Application Guidelines 6.0, World Auto Steel April, pp. 314.
- [10] Tisza M (2015) Material and technological developments in sheet metal forming with special regards to the needs of the automotive industry, Archives of Materials Science and Engineering, 71 No.1. pp. 36-45.
- [11] Audi AG.: Historical background on use of aluminium at Audi, https://www.audiworld.com/news/02/aluminum/content1.shtml
- [12] European Aluminium Association (2012) Aluminium in cars-unlocking – The light weighting potential http://www.alueurope.eu/publications-automotive/
- [13] Kelkar A, Roth R and Clark J (2001) Automobile Bodies: Can Aluminum Be an Economical Alternative to Steel, Journal of Manufacturing 53 No. 8. pp. 28-32.
- [14] Lotus Engineering (2010) An assessment of mass reduction opportunities for 2017-2020 model year vehicle program, The International Council on Clean Transportation
- [15] Goede M et. al (2009) Super Light Car - lightweight construction thanks to a multi-material design and function integration, European Transp. Res. Rev No.1. pp. 5-10. DOI 10.1007/s12544-008-0001-2
- [16] Budai D and Tisza M (2017) Investigation of EN AW 5754 Aluminum Alloy's Formability at Elevated Temperatures Material Science Forum, 885, pp 98-103.
- [17] Budai D, Kovács P and Lukács Zs (2016) Formability investigations of Aluminum alloys at elevated temperatures, IDDRG 2016 Conference, Linz, 12-15. June 2016
- [18] Bach, R.: Aluminium in transport industry, https://www.aluminiumleader.com/application/transport/
- [19] LoCoMaTech (2016) Low Cost Materials Processing Technologies for Mass Production of Lightweight Vehicles EU H-2020 project 2016-2019, ID No: 723517.
- [20] Tisza M (2001) Physical Metallurgy for Engineers, ASM Publisher, 2001, Ohio-London, p.405.
9. 著作権:
- この資料は、「M Tisza and Zs Lukács」による「High strength aluminum alloys in car manufacturing」の論文に基づいています。
- 論文出典: doi:10.1088/1757-899X/418/1/012033
この資料は上記の論文を紹介するために作成されたものであり、商業目的での無断使用を禁じます。Copyright © 2025 CASTMAN. All rights reserved.