この論文の概要は、[Japan Die Casting Congress]で発表された論文「[Added Value of Process Modelling in Development of Automotive Die Casting Parts]」に基づいています。
1. 概要:
- タイトル: 自動車用ダイカスト部品の開発におけるプロセスモデリングの付加価値
- 著者: アンドレ・ルネゼ、ニコラ・ドゥ・レヴィエール、ロイック・カルバ、バダリナート・カルクンテ
- 発表年: 2018年
- 発行ジャーナル/学会: 日本ダイカスト会議
- キーワード: ダイカスト、HPDC、部品設計、金型設計、鋳造開発ループ、デジタルチューニング、ダイサイクル、シミュレーション、気孔率、ワークフロー、マクロ、自動化、ルノー、ESI

2. 研究背景:
自動車市場では、機械的特性と構造的完全性に優れた高性能鋳造品への要求がますます高まっています。従来、このような用途には重力鋳造や低圧ダイカストが用いられてきましたが、高圧ダイカスト(HPDC)は、ショットタイムの短縮とコスト効率の高さから大量生産に有利です。しかし、HPDC固有のプロセス上の制約から、これらの高度な性能要求を安定的に満たすことは困難です。HPDCの能力を向上させ、競争力を維持するために、技術革新と技術開発が継続的に行われています。
従来、ダイカスト開発におけるプロセスシミュレーションソフトウェアの活用は限定的でした。グラフィカルユーザーインターフェース(GUI)は、ユーザーフレンドリーではなく、プロセス指向でもなかったため、普及を妨げていました。その結果、シミュレーションは、設計段階で問題を予防する(予防的措置)よりも、問題発生後の問題解決(事後的措置)に主に使用されていました。
コンピュータハードウェアの進化、ユーザーフレンドリーで鋳造現場に特化したGUI設計の進歩、そして軽量鋳造品のための製品設計と材料の複雑化により、プロセスシミュレーションの重要性が高まっています。製品開発サイクルの初期段階にシミュレーションを組み込むことは、リードタイムの短縮、コストの最適化、高品質な鋳造品の製造を確実にするために不可欠となっています。
3. 研究目的と研究課題:
本研究は、自動車用ダイカスト部品の開発におけるプロセスモデリングの付加価値を実証することを目的としています。具体的には、ルノーの手法に代表される最先端のシミュレーション手法を適用し、部品と金型の両方の設計のデジタルチューニングを実現することを検証します。
主な研究課題は、最新のシミュレーション手法は、物理的な試行錯誤から、より予測可能で効率的なデジタルアプローチへと移行することで、自動車用ダイカスト部品の開発プロセスをどのように強化できるか?ということです。
根底にある仮説は、プロセスモデリングを設計の初期段階に統合することで、鋳造エンジニアは欠陥を予測し、プロセスパラメータを最適化し、最終的にHPDC部品の設計と最終品質の両方を向上させることができるということです。
4. 研究方法:
本論文では、ルノーが開発した2011年型AlSi9Cu3ギアボックスハウジングをケーススタディとした研究を紹介します。研究では、ESI ProCAST 2018.0ソフトウェアを用いた4段階のデジタルスタディ手法を採用しています。この手法は、以下のように構成されています。
- ステップ1:製造可能性チェック(ベアキャスティング): この初期段階では、簡略化された金型表現で充填プロセスをシミュレーションすることにより、部品の製造可能性を評価します。目的は、製品設計の初期段階で、エア巻き込みやホットスポットなどの潜在的な問題を迅速に特定することです。
- ステップ2:射出システム設計(ビスケット/ランナー/インゲート/オーバーフロー): このステップでは、ランナー、インゲート、オーバーフローなどの射出システムの設計と検証に焦点を当てます。この段階でのシミュレーションでは、充填パターンと、射出システム設計に関連するエア巻き込みや引け巣のリスクを評価します。
- ステップ3:金型設計(冷却ラインなし): ここでは、冷却システムを初期段階では除外して、完全な金型形状を設計します。熱サイクルシミュレーションを実施して、金型温度分布を把握し、冷却が必要となるホットスポットを特定します。
- ステップ4:金型設計とプロセス検証(フル金型設計): 最終ステップでは、冷却システムを金型設計に組み込みます。熱サイクル、充填、凝固などの包括的なシミュレーションを実施して、完全な金型設計とプロセスパラメータを検証し、部品品質を予測します。
データ収集方法: 本研究は、方法論の各ステップでESI ProCAST 2018.0によって生成されたシミュレーションデータに依存しています。
分析方法: 分析は主に定性的であり、充填時間、引け巣、温度分布のプロットを通して視覚化されたシミュレーション結果の解釈に焦点を当てています。各設計反復の有効性は、これらのシミュレーション出力に基づいて評価されます。シミュレーション結果を検証するために、シミュレーションされた引け巣と実際の部品切断面との視覚的な比較も提示されています。
研究対象と範囲: 本研究は、ルノープロセスエンジニアリングにおける自動車用HPDC部品の開発プロセスに焦点を当てており、特定のギアボックスハウジングをケーススタディとして使用しています。範囲は、ESI ProCASTを使用した、記述された4段階のデジタルシミュレーション手法の適用に限定されています。
5. 主な研究結果:
4段階のシミュレーション手法により、ダイカスト部品開発プロセスの各段階で貴重な洞察が得られました。
- ステップ1:製造可能性チェック(ベアキャスティング): キャビティ充填時間のシミュレーション(図1a)により、最後に充填される領域が特定され、エア抜きを容易にするオーバーフローの適切な位置が示唆されました。引け巣解析(図1b)では、鋳造品に重大なホットスポットが強調表示され、引け巣のリスクの可能性が示されました。「図1aは、最後に充填される領域を示しています。」「図1bは、引け巣につながる可能性のある大規模なホットスポットを強調表示しています。」
- ステップ2:射出システム設計(ビスケット/ランナー/インゲート/オーバーフロー): 段階的な充填シミュレーション(図2a)により、初期オーバーフローの位置決めが検証されました。充填時間解析(図2b左)により、オーバーフロー位置の有効性が確認されました。引け巣予測(図2b右)は、ステップ1と同様のリスク領域を示しましたが、シミュレーションにビスケットとランナーを含めたことによる熱勾配と充填プロファイルの変更により、引け巣領域が追加される可能性がありました。「図2aの段階的な充填は、初期オーバーフローの適切な位置決めを確認しています…」「図2b(右)の引け巣プロットは、ステップ1で観察されたものとほぼ同様のリスクを示しています。」
- ステップ3:金型設計(冷却ラインなし): 熱サイクルシミュレーション(図3a)は、最も高温の金型/鋳造界面での温度プロファイルを提供し、サイクル全体での金型温度の安定化を示しました。ホットスポット解析(図3b)では、可動金型と固定金型の両方におけるホットスポットの位置、および2011年の金型設計からの既存の冷却回路の位置が明らかになりました。「図3aは、最も高温の金型/鋳造界面で撮影されたショットを通る温度プロファイルを示しています。」「図3bは、可動金型と固定金型の両方のホットスポットを示しています…」
- ステップ4:金型設計とプロセス検証(フル金型設計): 冷却回路を備えた熱サイクルシミュレーション(図4b左)は、金型の熱定常状態が冷却システムなしのシミュレーションとほぼ同様に達成されることを示しました。ただし、内部金型冷却により、ホットスポット領域の金型表面で約70℃の顕著な温度低下が見られました。段階的な充填シミュレーション(図4c)は、スリーブ充填が乱流を最小限に抑えてスムーズに行われることを示しました。エア巻き込み解析(図4d)は、コアピンとオーバーフロー付近のエア巻き込みの可能性のある位置を示しました。部品充填時間プロット(図4e左)は、シミュレーションステップ全体で一貫した充填挙動を示しました。
- 現実との比較: 3つの重要なゾーン(ボス)について、シミュレーションされた引け巣と実際の部品切断面との比較(図5b)は、良好な一致を示し、シミュレーション手法の予測能力を検証しました。「図5bは、シミュレーションループのさまざまなステップにおける3つのボスすべての引け巣の比較と現実を要約し、現実との良好な整合を確認しています。」
図のリスト:
- 図1a:キャビティ充填時間
- 図1b:鋳造における主なホットスポットを強調表示する引け巣プロット
- 図2a:キャビティ内の段階的な充填
- 図2b:(左)オーバーフロー位置が最後に充填されたことを確認する充填時間プロット、(右)鋳造におけるホットスポットを強調表示する引け巣プロット
- 図3a:最も高温の金型/鋳造界面で撮影された金型温度プロファイル
- 図3b:8サイクル(ショット)終了時の可動金型(上)および固定金型(下)の金型温度プロファイル。水色の円とバーは、2011年の金型の冷却回路を示しています。
- 図4a:金型冷却回路
- 図4b:(左)最も高温の金型/鋳造界面で撮影された金型温度プロファイル、(右)金型が開かれる直前の冷却水の影響を示す金型の断面
- 図4c:スリーブ充填とスリーブ内のプランジャーの動きから始まる段階的な充填
- 図4d:エア巻き込み
- 図4e:(左)充填時間プロット、(右)引け巣
- 図5a:気孔率がないと見なされる部品に必須の3つの主要ゾーン(ボス)を示す
- 図5b:3つの主要ゾーンすべてのシミュレーションと実際の切断面の引け巣の比較を示す
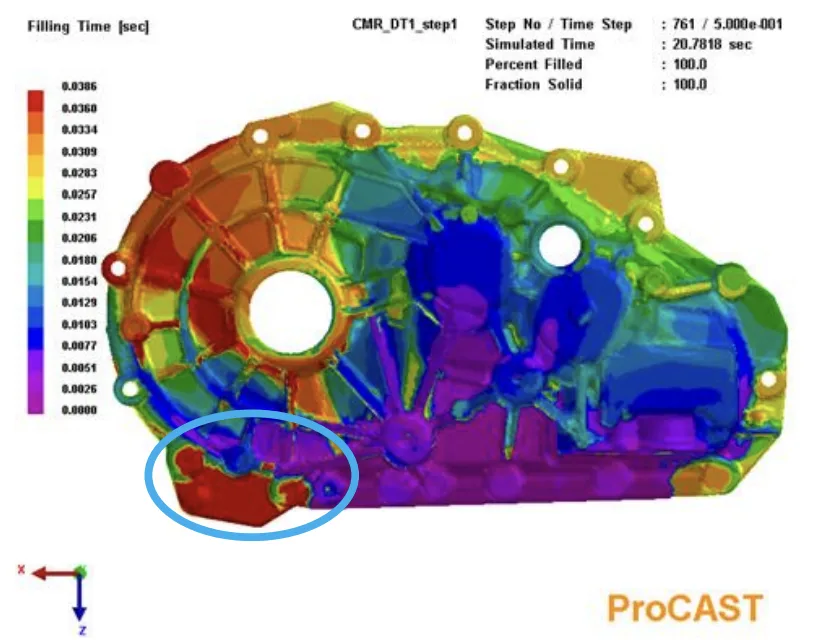
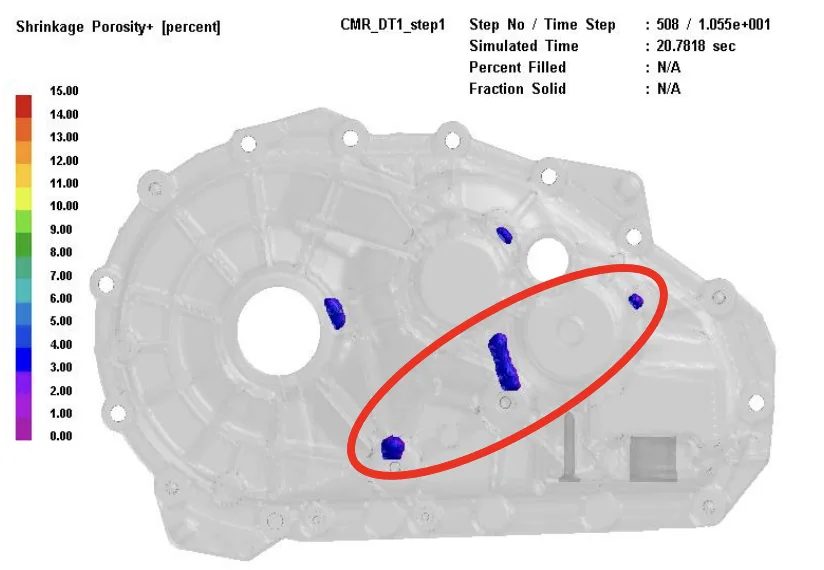
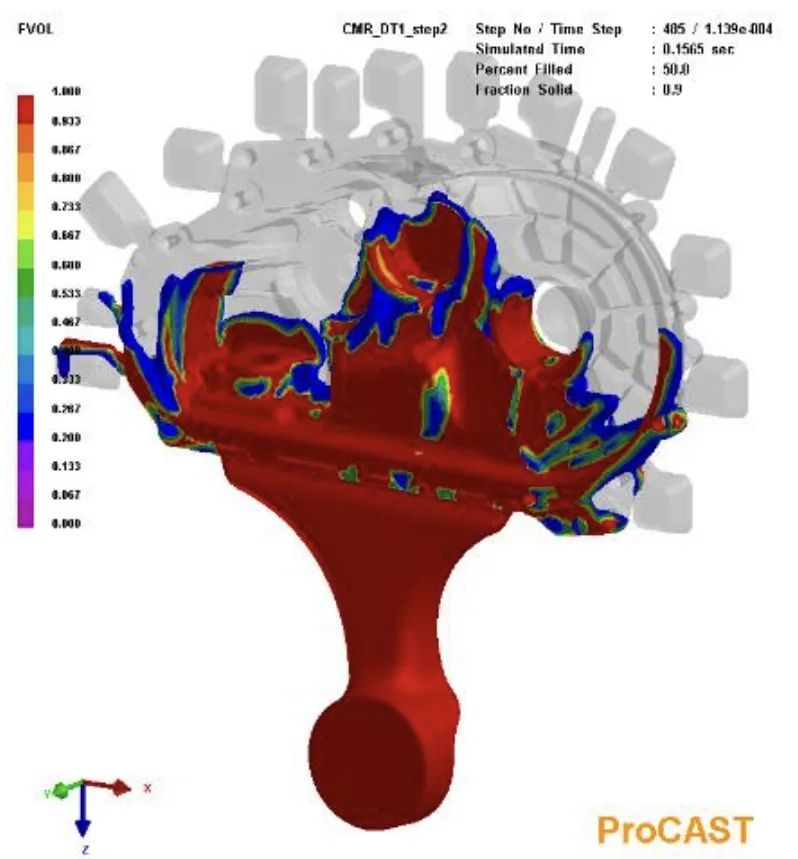
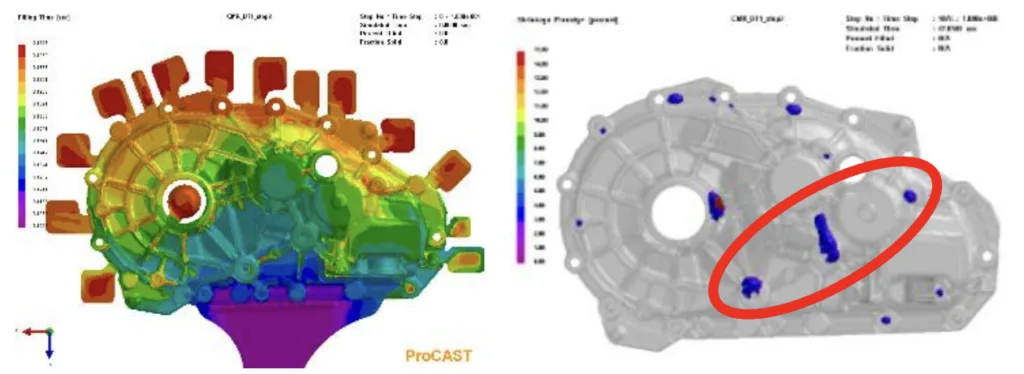
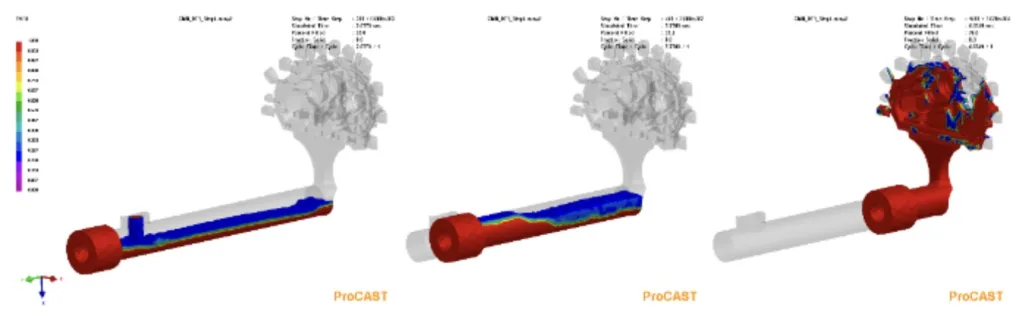
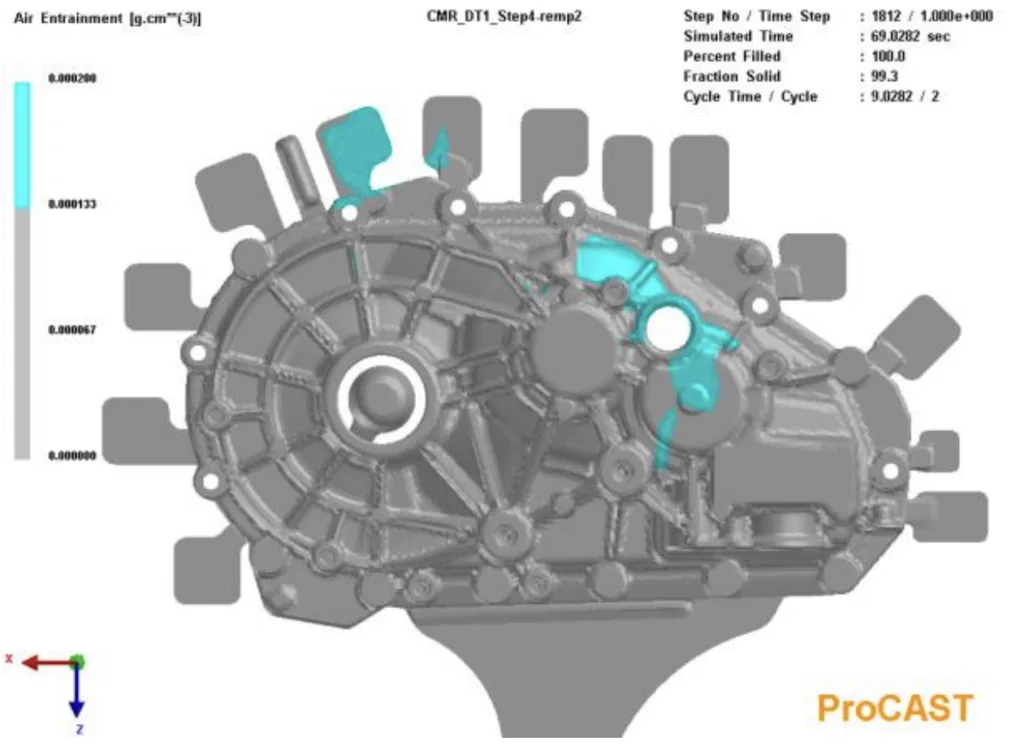
6. 結論と考察:
主な結果の要約: 本論文では、ESI ProCASTを用いた構造化された4段階のシミュレーション手法を通じて、自動車用HPDC部品開発におけるプロセスモデリングの付加価値を実証することに成功しました。製造可能性チェックから完全な金型設計検証まで、各ステップは部品と金型の設計を最適化するための重要な洞察を提供します。シミュレーション結果は、現実世界の観察と良好な相関関係を示しており、アプローチの精度と予測能力を強調しています。
研究の学術的意義: 本研究は、ダイカスト開発の初期段階にプロセスシミュレーションを統合することの学術的意義を強調しています。物理的な試行錯誤への依存を減らし、より効率的で堅牢な設計プロセスへの道を開く、デジタルチューニング手法の有効性を検証します。
実用的な意義: 提示された4段階の手法は、自動車産業のダイカストエンジニアにとって実用的で価値のあるフレームワークを提供します。このアプローチを採用することにより、製造業者は次のことが可能になります。
- 部品品質の向上: 気孔率やエア巻き込みなどの潜在的な欠陥を事前に特定して軽減します。
- 開発期間の短縮: 物理的な反復を仮想シミュレーションに置き換えることで、開発サイクルを短縮します。
- コストの最適化: 事前のシミュレーションベースの設計最適化を通じて、コストのかかる金型手直しや生産遅延を最小限に抑えます。
初期の製造可能性チェック(ステップ1)と、冷却システムの戦略的な設計(ステップ3および4)は、高品質のHPDC部品を実現するために特に重要であることが強調されています。
研究の限界: 本研究は、単一のケーススタディ(ギアボックスハウジング)に基づいており、調査結果の一般化可能性が制限される可能性があります。この手法は、ルノーのプロセスとESI ProCASTソフトウェアの使用にも固有です。多様な部品形状や異なるシミュレーションツールを用いたさらなる研究が有益でしょう。
7. 今後のフォローアップ研究:
本論文では、今後の研究の方向性をいくつか示しています。
- プロセス変動の管理: 合金温度変動などの製造プロセス変動が部品品質に与える影響を調査し、これらの変動の影響を受けにくい堅牢な設計を開発します。
- 最適化ツール: ProCASTに統合されたESI PAM-OPTなどの最適化ツールを活用して、プロセス制御と部品品質を向上させるための製造パラメータを体系的に定義および最適化する方法を検討します。
- インダストリー4.0統合: シミュレーションと最適化ツールの統合をさらに進めて、ダイカストプロセスのインダストリー4.0標準への移行を促進し、より自動化されたデータ駆動型の製造を可能にします。
堅牢な設計手法、シミュレーションと最適化アルゴリズムのシームレスな統合、およびダイカスト分野におけるインダストリー4.0原則のより広範な実装には、さらなる探求が必要です。
8. 参考文献:
- [1] Ch. Pequet, M. Gremaud, and M. Rappaz, "Modelling of microporosity, macroporosity, and pipe-phrinkage formation during the solidification of alloys using a mushy-zone refinement method: applications to aluminium alloys", Met. Mater. Trans., 33A (2002) 2095.
- [2] Imad Khan, M & Frayman, Yakov & Nahavandi, Saeid. (2012). Modelling of porosity defects in high pressure die casting with a neural network.
- [3] G. Couturier, and M. Rappaz, "Effect of volatile elements on porosity formation in solidifying alloys", Mod. Sim. Mater. Sc. Engng., (2005)
- [4] Wang, LH & Nguyen, T & Savage, G & Davidson, C. (2003). Thermal and flow modelling of ladling and injection in high pressure die casting process. International Journal of Cast Metals Research. 16. 409-417. 10.1179/136404603225007863.
- [5] Karban, Robert. (2000). The effects of intensification pressure, gate velocity, and intermediate shot velocity on the internal quality of aluminum die castings. ETD Collection for Purdue University.
- [6] G. Couturier, J.-L. Desbiolles, and M. Rappaz, "A Porosity Model for Multi-Gas Systems in Multi-Component Alloys", MCWASP, Edited by TMS Publ., Warrendale, USA, 2006)
- [7] Tsoukalas, Vasilios. (2003). The Effect of Die Casting Machine Parameters on Porosity of Aluminum Die Castings. International Journal of Cast Metals Research. 15. 581-588. 10.1080/13640461.2003.11819544.
- [8] S. Dargusch, Matthew & Dour, Gilles & Schauer, N & M. Dinnis, C & M. Savage, George. (2006). The influence of pressure during solidification of high pressure die cast aluminium telecommunications components. Journal of Materials Processing Technology. 180. 10.1016/j.jmatprotec.2006.05.001.
- [9] N. Obiekea, Kenneth & Y. Aku, Shekarau & S. Yawas, Danjuma. (2014). Effects of Pressure on the Mechanical Properties and Microstructure of Die Cast Aluminum A380 Alloy. Journal of Minerals and Materials Characterization and Engineering. 02. 248-258. 10.4236/jmmce.2014.23029.
- [10] G. Couturier and M. Rappaz, “Modelling of porosity formation in multicomponent alloys in the presence of several dissolved gases and volatile solute elements", Symposium on Simulation of Aluminum Shape Casting
- [11] ESI ProCAST 2018.0 User Manual 2006
9. 著作権:
- この資料は、アンドレ・ルネゼ、ニコラ・ドゥ・レヴィエール、ロイック・カルバ、バダリナート・カルクンテの論文:「自動車用ダイカスト部品の開発におけるプロセスモデリングの付加価値」に基づいています。
- 論文ソース: [DOI URL - 論文のDOI URLが利用可能な場合は追加してください]
- Copyright © 2025 CASTMAN. All rights reserved.
この資料は上記の論文に基づいて要約されたものであり、商業目的での無断使用は禁止されています。