この論文サマリーは、['自動車アプリケーション向け電気モーターハウジングの高圧ダイカストのシミュレーションと検証']と題された論文を基に、['トリノ工科大学']で発表されたものです。
1. 概要:
- タイトル:自動車アプリケーション向け電気モーターハウジングの高圧ダイカストのシミュレーションと検証 (Simulation and validation of high-pressure die casting of an electric motor housing for automotive application)
- 著者:ジャンルイジ・ランツォーニ (Gianluigi Lanzoni)
- 発行年:A.A.2020/2021
- 発行ジャーナル/学会:トリノ工科大学、自動車工学コース (Politecnico di Torino, Course of automotive engineering) (修士論文)
- キーワード:高圧ダイカスト (High-Pressure Die Casting, HPDC)、電気モーターハウジング (Electric Motor Housing)、自動車アプリケーション (Automotive Application)、プロセスシミュレーション (Process Simulation)、検証 (Validation)
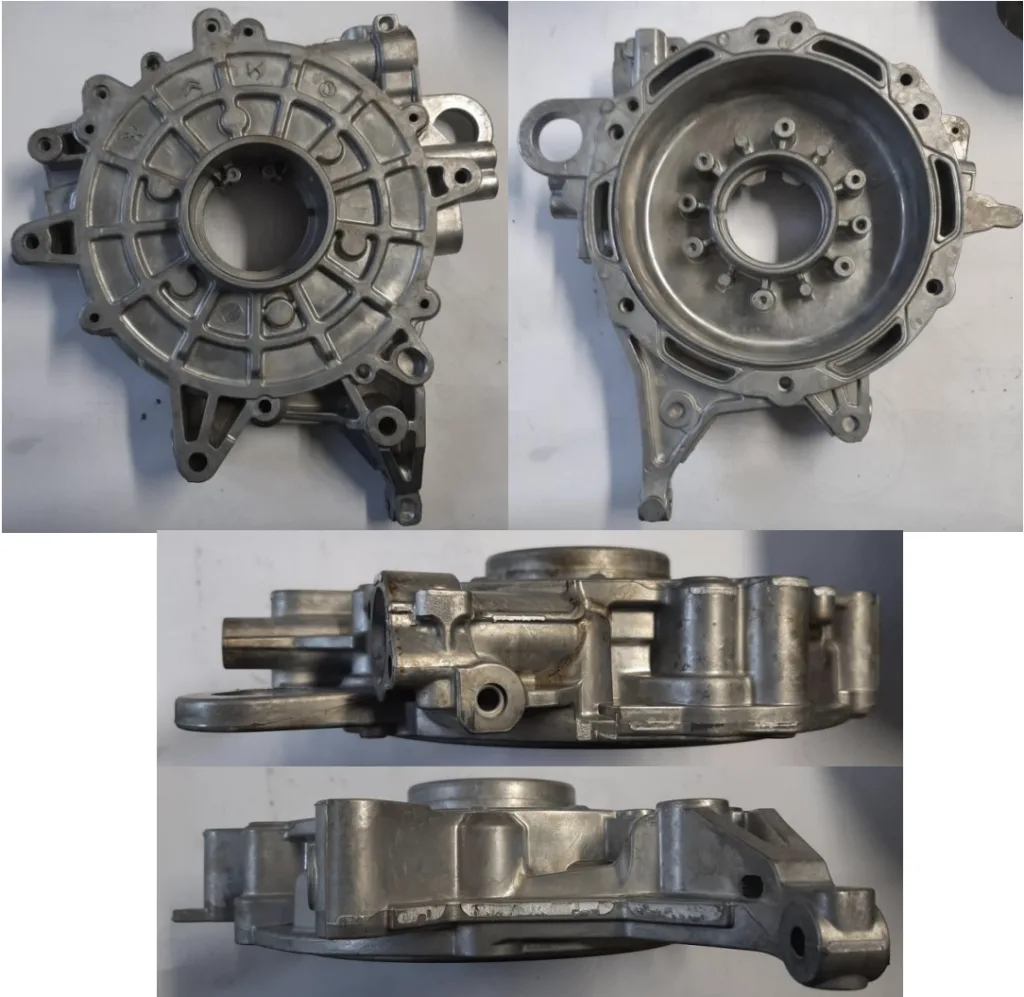
2. 研究背景:
研究テーマの背景:
軽量かつ複雑な自動車部品、特に電気自動車用部品の需要が増加するにつれて、高圧ダイカスト (HPDC) の重要性が増幅しています。本研究は、現代の自動車パワートレインの中核部品である電気モーターハウジングへのHPDCの適用に取り組んでいます。この研究は、HPDCプロセスの本質的な複雑さを強調し、プロセス最適化と欠陥軽減のための高度なシミュレーション技術の必要性を強調しています。
既存研究の現状:
現在のHPDCの実践は経験に根ざしており、より科学に基づいたアプローチへと進化していると説明されています。注入パラメータと結果として得られる鋳造品質との間の複雑な関係を完全に理解するには、大きな知識のギャップが存在します。特に、電気モーターハウジングのような新しい部品の製造には、確立された文献や経験的データが不足しており、体系的な調査の必要性を強調しています。
研究の必要性:
本研究は、HPDCを介して製造された電気モーターハウジングの製造ガイドラインを確立するために不可欠です。これらの部品は、HPDCの従来の製品範囲を超える新しい種類の鋳造品を表しています。本研究は、プロセスシミュレーションを活用して知識のギャップを埋め、これらの新しい自動車部品のための堅牢な製造戦略を開発します。最終的な目標は、シミュレーションの結果と実際の鋳造結果を関連付け、産業実装のためのベストプラクティスを定義することです。
3. 研究目的と研究課題:
研究目的:
本論文の主な目的は、電気モーターハウジング(カーター)の製造に使用される高圧ダイカストプロセスを分析することです。本研究は、この新しい部品に対するHPDCプロセスを予測および検証するために、複数のソフトウェアプラットフォームを利用して、プロセスシミュレーションの有効性を評価することを目的としています。包括的な目標は、将来の生産シナリオにおける同様の電気モーターハウジング部品の効率的かつ高品質な製造のためのガイドラインを設定することです。
主要な研究課題:
本研究は、以下の点に焦点を当てています。
- Flow-3D Cast、Inspire Cast、PIQ2 Castleの3つの異なるソフトウェアパッケージを使用したHPDCプロセスのシミュレーション。
- プロセスパラメータと予測される欠陥形成に焦点を当てて、各ソフトウェアから得られたシミュレーション結果の比較と対比。
- 実鋳造部品の実験的モールドサンプリングと分析によるシミュレーション予測の検証。
- 鋳造品質に対する主要なプロセスパラメータの影響の調査と、最適なパラメータ設定の特定。
- 一般的なダイカスト欠陥の形成メカニズムの分析と、これらの欠陥を予測するシミュレーションの精度評価。
研究仮説:
正式な仮説として明示的に述べられていませんが、研究は以下の暗黙の仮定の下で実施されます。
- プロセスシミュレーションは、複雑な電気モーターハウジングのHPDCプロセスを合理的に正確に表現できます。
- シミュレーション研究から導き出された最適化されたプロセスパラメータは、鋳造品質の実質的な改善、欠陥率の低減、および生産効率の向上につながります。
- シミュレーション予測と実際の鋳造結果の間の相関関係を確立して、電気モーターハウジングのHPDCにおける予測ツールとしてのシミュレーションの使用を検証できます。
4. 研究方法論
研究デザイン:
本研究では、特定の自動車部品であるPSAフロント電気モーターハウジングのHPDCプロセスに関するシミュレーションと検証を中心としたケーススタディのアプローチを採用しています。この方法論は、包括的な分析を提供するために、計算シミュレーションと実験的検証を統合しています。
データ収集方法:
データ収集は多面的であり、以下を含みます。
- シミュレーションデータ: Flow-3D Cast、Inspire Cast、PIQ2 Castleソフトウェアを使用して実施されたプロセスシミュレーションから生成された数値データ。これには、温度分布、エア巻き込み、ダイエロージョン、凝固時間、およびPQ2ダイアグラムに関するデータが含まれます。
- 実験データ: 実際のモールドサンプリングおよび部品分析から収集された経験的データ。以下を含みます。
- サーモグラフィー: 鋳造サイクル中のダイ温度変化を捉えるサーモグラフィーイメージングデータ。
- X線分析: 鋳造部品内の内部気孔と欠陥を特定する非破壊評価データ。
- 寸法測定: 設計仕様に対する鋳造部品の寸法精度を検証するデータ。
分析方法:
本研究では、比較および検証中心の分析アプローチを採用しています。
- ソフトウェア比較: HPDCプロセス現象を予測する上での各ソフトウェアプラットフォームの機能と限界を評価するための、3つのソフトウェアプラットフォーム間のシミュレーション結果の比較分析。
- メッシュ感度調査: さまざまなメッシュ寸法 (7.5 mm、3.7 mm、2.5 mm、2 mm) にわたる結果を分析することにより、メッシュ密度関数としてのシミュレーション精度評価。
- シミュレーション-実験検証: シミュレーションモデルの精度と信頼性を検証するために、サーモグラフィーおよびX線分析からの実験データとシミュレーション予測の相関関係分析。
- プロセスパラメータ分析: 鋳造品質と欠陥形成に対する、充填時間、流量、ゲート厚さなどの主要なプロセスパラメータの影響の調査。
- PQ2ダイアグラム分析: HPDCマシンとモールド間の相互作用を分析し、プロセスの動作ウィンドウを評価するためのPQ2ダイアグラムの活用。
研究対象と範囲:
本研究は、以下のHPDCプロセスに特化しています。
- 部品: PSAフロント電気モーターハウジング (Figure 26: PSA front housing model, Figure 27: PSA front housing die model)
- 材料: アルミニウム43400合金 (Figure 28: alloy composition)
- プロセス: Fondalpress S.p.a (Figure 1: Fondalpress S.p.a plant) で採用されている水平コールドチャンバーHPDCプロセス。
- ソフトウェア: プロセスシミュレーション用のFlow-3D Cast、Inspire Cast、PIQ2 Castle。
- 検証方法: 実験的検証のためのモールドサンプリング、サーモグラフィー、およびX線分析。
5. 主な研究結果:
主要な研究結果:
この研究では、さまざまなメッシュ寸法とソフトウェアプラットフォームにわたって包括的なシミュレーション結果が得られました。主な調査結果は次のとおりです。
- メッシュ寸法の影響: 7.5 mmメッシュを使用したシミュレーションは信頼性が低いと見なされました。 2.5 mmメッシュは、精度と計算効率の最適なバランスを提供することが確認されており、これは部品の平均厚さの約3分の1のメッシュ寸法を推奨する業界ガイドラインと一致しています。(Figure 29: geometry approximation plan view, Figure 30: intricate geometry approximation)
- 温度分布: 温度シミュレーションは、注入シリンダー出口とゲート付近でより高い温度を示す、さまざまなメッシュ密度で一貫したパターンを示しました。より細かいメッシュは、より微妙な温度勾配を提供しました。(Figure 31: temperature results with various mesh dimension part 1, Figure 32: temperature results with various mesh dimension part 2)
- エア巻き込み予測: シミュレーションは、潜在的なエア巻き込みゾーン、特に鋳造の上部領域で強調しました。より細かいメッシュは、エアポケット形成のより洗練された表現を示しました。(Figure 33: air trapped with various mesh dimensions part 1, Figure 34: air trapped with various mesh dimensions part 2)
- ダイエロージョン分析: ダイエロージョンシミュレーションは、ゲートおよびランナー-モールドキャビティインターフェースでより高いエロージョンポテンシャルを示しており、これは高い合金速度の領域と相関関係があります。(Figure 35: die erosion with various mesh dimensions)
- 凝固時間予測: 凝固シミュレーションは、収縮供給に重要なビスケットが最後に凝固する領域であることを一貫して特定しました。(Figure 36: solidification times with various mesh dimensions)
- ソフトウェア比較: Flow-3D Castは、ダイサイクリングや詳細な酸化物追跡などの高度な機能を提供する、最も包括的で正確なソフトウェアとして認識されました。 Inspire Castはユーザーフレンドリーであると評価され、PIQ2 Castleは使いやすさとマシン固有のパラメータ統合のバランスを提供しました。(Figure 37: Inspire Cast and Castle modeling interface, Figure 38: Flow-3D Cast thermal die cycling, Figure 39: Thermal die cycling length (Flow-3D Cast), Figure 40: Filling setup with the three software)
- 実験的検証: ダイ温度のサーモグラフィー測定は、シミュレーション予測と質的に一致しましたが、実験条件により絶対温度値は異なりました。鋳造品のX線分析では、シミュレーションされた気孔リスク領域と概ね一致する気孔分布が明らかになりました。(Figure 79: thermograph fixed side die open, Figure 80: thermograph and simulation results part 1, Figure 81: thermograph and simulation results part 2, Figure 82: X-ray with porosities, Figure 83: porosity risk and X-ray results part 1, Figure 84: porosity risk and X-ray results part 2, Figure 85: porosity risk and X-ray results part 3)
- PQ2ダイアグラム分析: PQ2ダイアグラム分析は、実際の鋳造プロセスが最適ゾーン外で動作していることを示しており、鋳造品質と効率を向上させるためのプロセス最適化の可能性を示唆しています。(Figure 86: example of Pq^2 diagram, Figure 87: Pq^2 diagram actual condition, Figure 88: Pq^2 diagram on optimal machine)
データ解釈:
シミュレーション結果は、潜在的な欠陥位置とプロセスボトルネックを効果的に予測しました。実験的検証は、絶対値にいくつかの食い違いを示しましたが、特に気孔が発生しやすい領域を特定する上で、一般的にシミュレーションの結果を裏付けました。 PQ2ダイアグラム分析は、鋳造品質と効率を向上させるためのプロセス最適化の機会を強調しました。本研究は、正確なシミュレーション結果を得るためのメッシュ改良の重要性と、包括的なHPDCプロセス分析のためのさまざまなシミュレーションソフトウェアの補完的な強みを強調しています。
図面名リスト:
- Figure 1: Fondalpress S.p.a 工場 (Figure 1: Fondalpress S.p.a plant)
- Figure 2: 合金標準インゴット (Figure 2: alloy standard ingots)
- Figure 3: 合金溶融経路 (Figure 3: alloy melting path)
- Figure 4: 溶解炉 (Figure 4: melting furnace)
- Figure 5: アルミニウム中の水素溶解度 (Figure 5: hydrogen solubilization in the aluminum)
- Figure 6: バケットでのピッキング (Figure 6: picking with the bucket)
- Figure 7: 脱ガスステーション (Figure 7: degassing station)
- Figure 8: 保持炉 (Figure 8: holder furnaces)
- Figure 9: 高圧ダイカストマシン (Figure 9: high-pressure die casting machine)
- Figure 10: ダイ固定側 (Figure 10: die fixed side)
- Figure 11: ダイ可動側 (Figure 11: die moving side)
- Figure 12: アルミニウムと潤滑剤の相互作用 (Figure 12: interaction between aluminum and lubricant)
- Figure 13: ダイ潤滑 (Figure 13: Die lubrication)
- Figure 14: 潤滑剤滴下と熱い金型の相互作用 (Figure 14: interaction between lubricant drop and the hot mold)
- Figure 15: ダイの濡れ性に対する異なる噴霧の効果 (Figure 15: effects of different pulverizations on die wettability)
- Figure 16: 3つの射出段階 (Figure 16: three injection phases)
- Figure 17: 鋳造品をトリミングマシンに搬送するロボット (Figure 17: robot transporting the cast to the trimming machine)
- Figure 18: トリミングマシン (Figure 18: trimming machine)
- Figure 19: 閉じ込められた空気の欠陥 (Figure 19: trapped air defects)
- Figure 20: 水素介在物の欠陥 (Figure 20: hydrogen inclusions defects)
- Figure 21: 収縮欠陥 (Figure 21: shrinkage defects)
- Figure 22: ホットクラック (Figure 22: hot cracks)
- Figure 23: コールドジョイント (Figure 23: cold joints)
- Figure 24: 酸化 (Figure 24: oxidations)
- Figure 25: 鋳造における欠陥の平均頻度 (Figure 25: mean frequency of defects in the cast)
- Figure 26: PSAフロントハウジングモデル (Figure 26: PSA front housing model)
- Figure 27: PSAフロントハウジングダイモデル (Figure 27: PSA front housing die model)
- Figure 28: 合金組成 (Figure 28: alloy composition)
- Figure 29: 形状近似平面図 (Figure 29: geometry approximation plan view)
- Figure 30: 複雑な形状近似 (Figure 30: intricate geometry approximation)
- Figure 31: さまざまなメッシュ寸法パート1での温度結果 (Figure 31: temperature results with various mesh dimension part 1)
- Figure 32: さまざまなメッシュ寸法パート2での温度結果 (Figure 32: temperature results with various mesh dimension part 2)
- Figure 33: さまざまなメッシュ寸法パート1で閉じ込められた空気 (Figure 33: air trapped with various mesh dimensions part 1)
- Figure 34: さまざまなメッシュ寸法パート2で閉じ込められた空気 (Figure 34: air trapped with various mesh dimensions part 2)
- Figure 35: さまざまなメッシュ寸法でのダイエロージョン (Figure 35: die erosion with various mesh dimensions)
- Figure 36: さまざまなメッシュ寸法での凝固時間 (Figure 36: solidification times with various mesh dimensions)
- Figure 37: Inspire CastとCastleのモデリングインターフェース (Figure 37: Inspire Cast and Castle modeling interface)
- Figure 38: Flow-3D Cast熱ダイサイクル (Figure 38: Flow-3D Cast thermal die cycling)
- Figure 39: 熱ダイサイクル長(Flow-3D Cast) (Figure 39: Thermal die cycling length (Flow-3D Cast))
- Figure 40: 3つのソフトウェアでの充填設定 (Figure 40: Filling setup with the three software)
- Figure 41: 最適なマシンパラメータの迅速な評価 (Figure 41: Rapid evaluation of the best machine parameters)
- Figure 42: 充填中の温度 (Figure 42: temperature during filling)
- Figure 43: 潤滑前のダイ温度 (Figure 43: die temperature before lubrication)
- Figure 44: 潤滑後のダイ温度 (Figure 44: die temperature after lubrication)
- Figure 45: 充填終了時および固相率で閉じ込められた空気 (Figure 45: air trapped at the end of filling and solid fraction)
- Figure 46: 正味欠陥体積 (Figure 46: defect net volume)
- Figure 47: 充填終了時の温度分布 (Figure 47: temperature distribution at the end of filling)
- Figure 48: 基本シミュレーションのさまざまな結果 (Figure 48: various results of base simulation)
- Figure 49: 充填および凝固中の金型温度 (Figure 49: mould temperature during filling and solidification)
- Figure 50: 閉じ込められた空気 (Figure 50: air trapped)
- Figure 51: 充填後の温度分布 (Figure 51: temperature distribution after filling)
- Figure 52: 閉じ込められた空気のシミュレーション (Figure 52: air trapped simulation)
- Figure 53: 充填時間 (Figure 53: filling time)
- Figure 54: 充填および凝固中の金型温度 (Figure 54: mould temperature during filling and solidification)
- Figure 55: 冷却システムレイアウト (Figure 55: cooling system layout)
- Figure 56: 冷却システムレイアウト、側面図 (Figure 56: cooling system layout, lateral views)
- Figure 57: 充填中の温度分布 (Figure 57: temperature distribution during filling)
- Figure 58: 閉じ込められた空気 (Figure 58: air trapped)
- Figure 59: 充填および凝固中の金型温度 (Figure 59: mould temperature during filling and solidification)
- Figure 60: 部品取り出しおよびダイ再閉鎖前の充填終了時のダイ温度 (Figure 60: die temperature at filling end, before part extraction and die reclosing)
- Figure 61: 鋳造抽出時の固相率と温度 (Figure 61: solid fraction and temperature at cast extraction)
- Figure 62: 気孔率リスク (Figure 62: porosities risk)
- Figure 63: 充填温度パート1 (Figure 63: filling temperature part 1)
- Figure 64: 充填温度パート2 (Figure 64: filling temperature part 2)
- Figure 65: 閉じ込められた空気 (Figure 65: air trapped)
- Figure 66: 充填温度、充填時間、総体積制限 (Figure 66: filling temperature, filling time and total volume restriction)
- Figure 67: 充填温度 (Figure 67: filling temperature)
- Figure 68: 充填中に閉じ込められた空気 (Figure 68: trapped air during filling)
- Figure 69: 正味欠陥体積と充填中の二相 (Figure 69: net defect volume and dual phase during filling)
- Figure 70: ダイエロージョン (Figure 70: die erosion)
- Figure 71: 速度軌跡 (Figure 71: velocity trajectories)
- Figure 72: チャネル厚さ (Figure 72: channels thickness)
- Figure 73: シール壁厚さ (Figure 73: sealing wall thickness)
- Figure 74: 熱機関トランスミッションパート1のシミュレーション例 (Figure 74: example of simulation of thermal engine transmission part 1)
- Figure 75: 熱機関トランスミッションパート2のシミュレーション例 (Figure 75: example of simulation of thermal engine transmission part 2)
- Figure 76: 壁厚さ (Figure 76: wall thickness)
- Figure 77: サンプリング前のダイ (Figure 77: die before sampling)
- Figure 78: 設置前のトリミングマシン金型 (Figure 78: trimming machine mould before installation)
- Figure 79: サーモグラフ固定側ダイオープン (Figure 79: thermograph fixed side die open)
- Figure 80: サーモグラフとシミュレーション結果パート1 (Figure 80: thermograph and simulation results part 1)
- Figure 81: サーモグラフとシミュレーション結果パート2 (Figure 81: thermograph and simulation results part 2)
- Figure 82: 気孔率のあるX線 (Figure 82: X-ray with porosities)
- Figure 83: 気孔率リスクとX線結果パート1 (Figure 83: porosity risk and X-ray results part 1)
- Figure 84: 気孔率リスクとX線結果パート2 (Figure 84: porosity risk and X-ray results part 2)
- Figure 85: 気孔率リスクとX線結果パート3 (Figure 85: porosity risk and X-ray results part 3)
- Figure 86: Pq^2ダイアグラムの例 (Figure 86: example of Pq^2 diagram)
- Figure 87: Pq^2ダイアグラムの実際の状態 (Figure 87: Pq^2 diagram actual condition)
- Figure 88: 最適なマシンでのPq^2ダイアグラム (Figure 88: Pq^2 diagram on optimal machine)
- Figure 89: ダイ抽出時の実際の部品 (Figure 89: real component at die extraction)
- Figure 90: トリミング後の実際の部品 (Figure 90: real component after trimming)
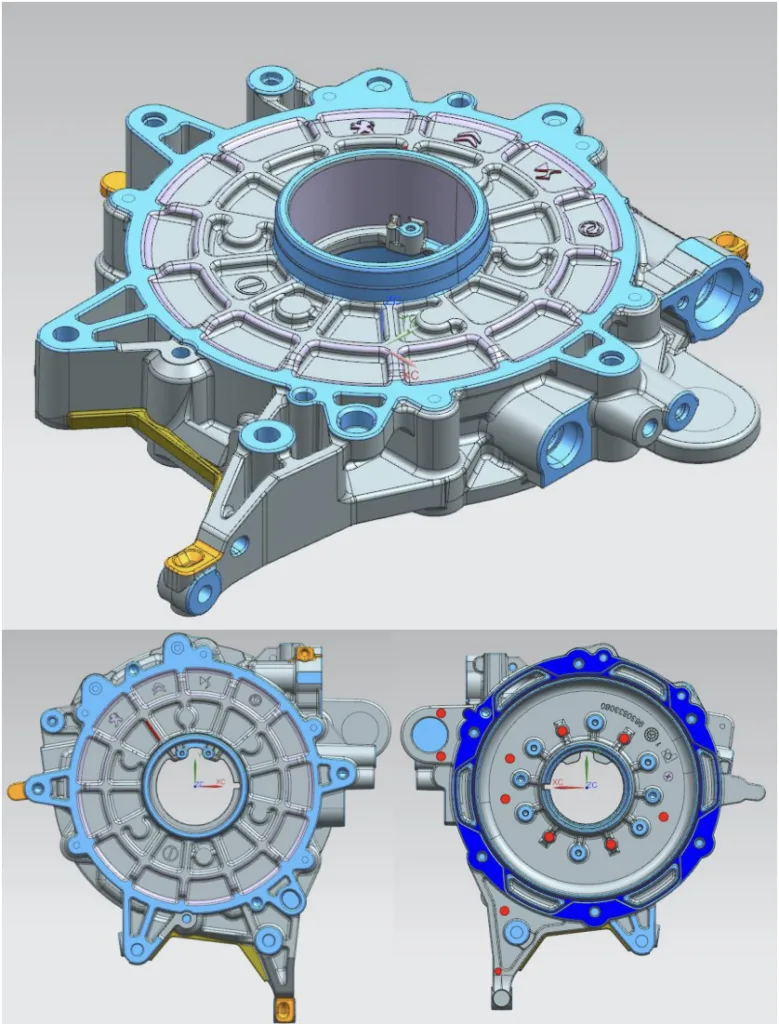
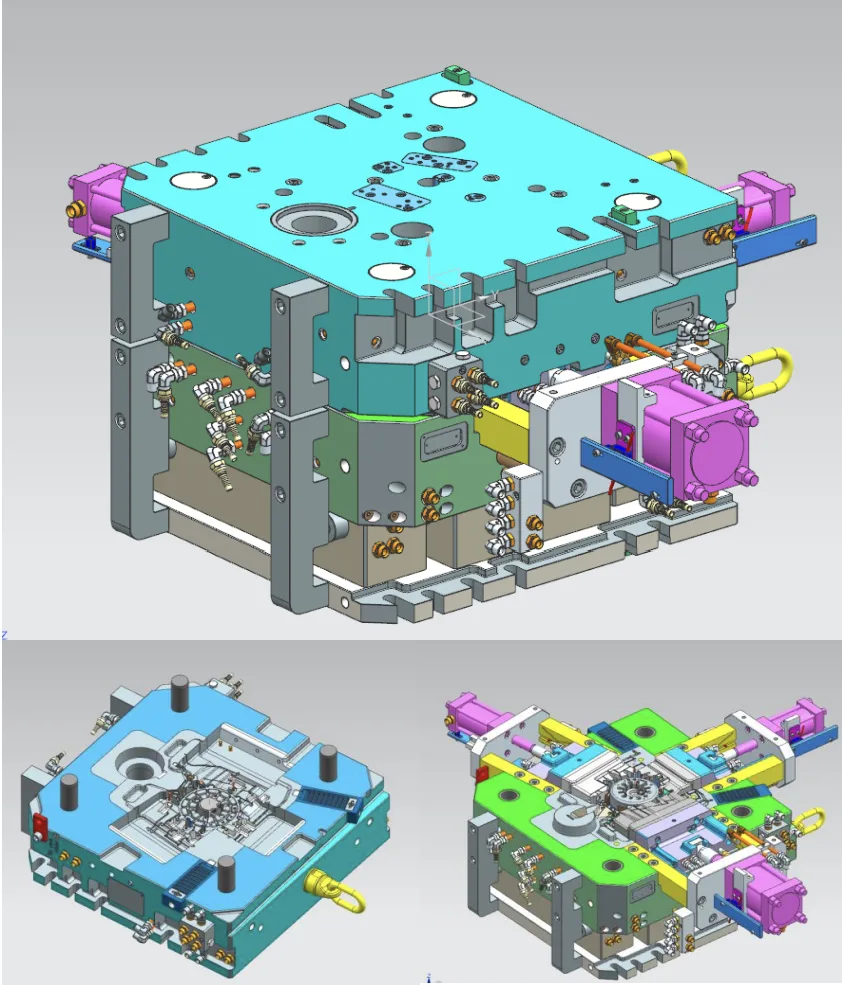
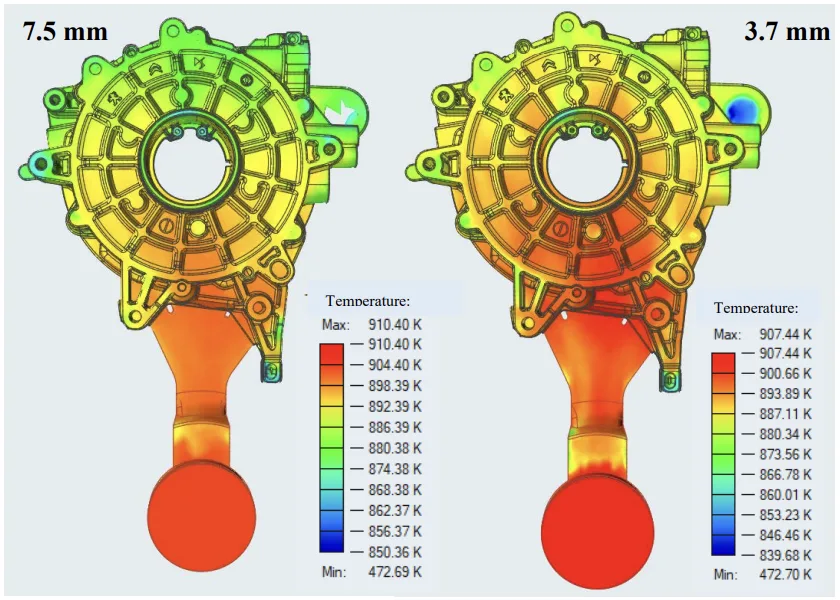
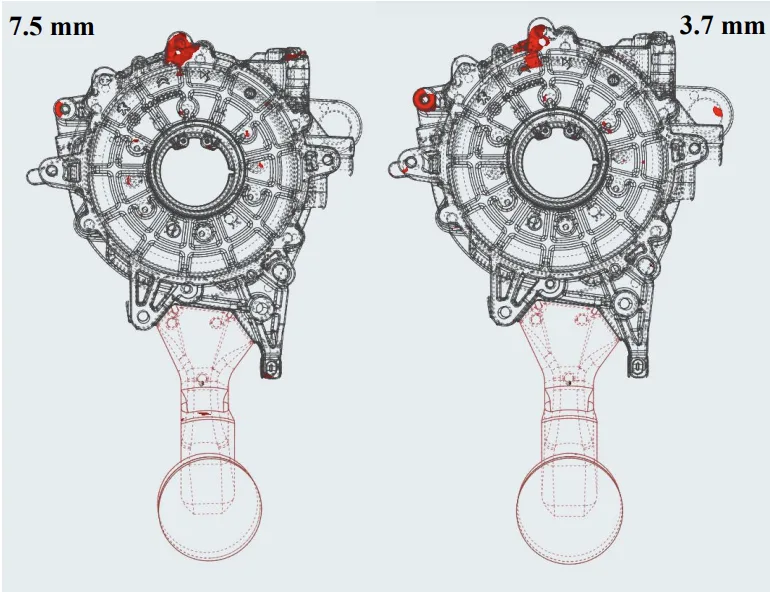
6. Conclusion:
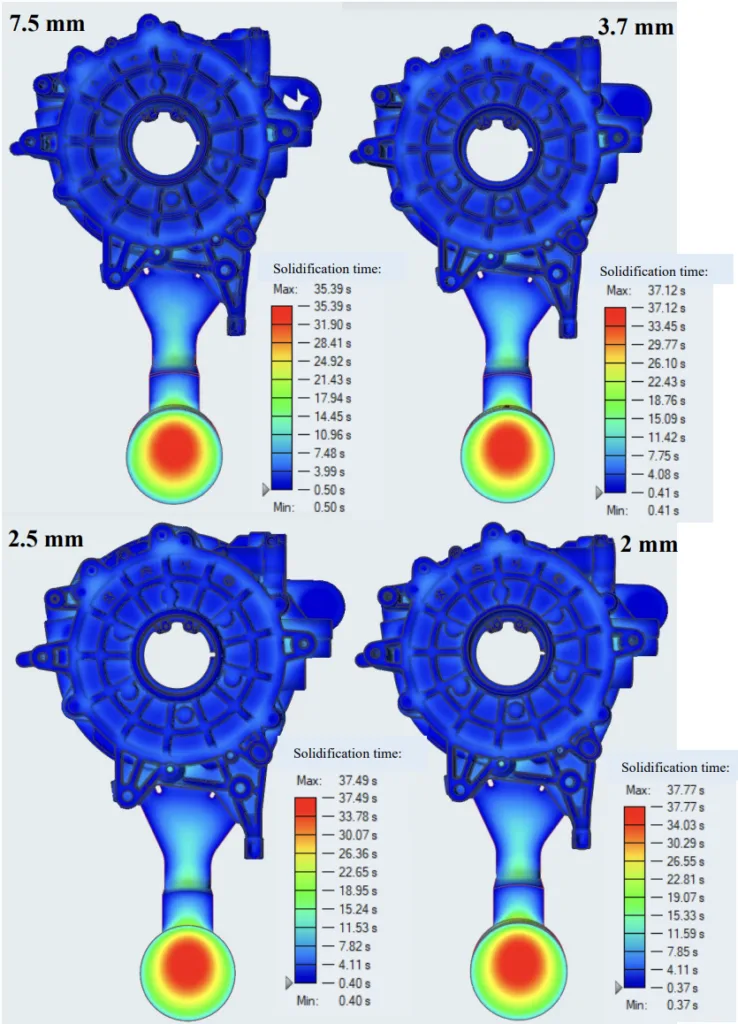
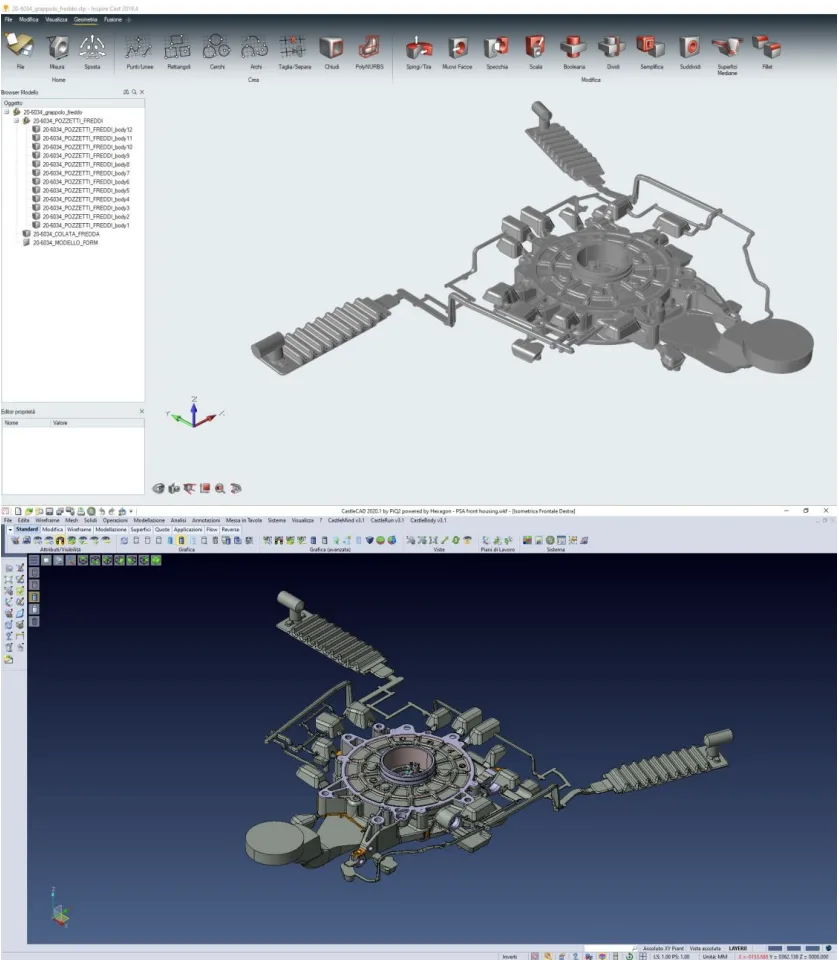
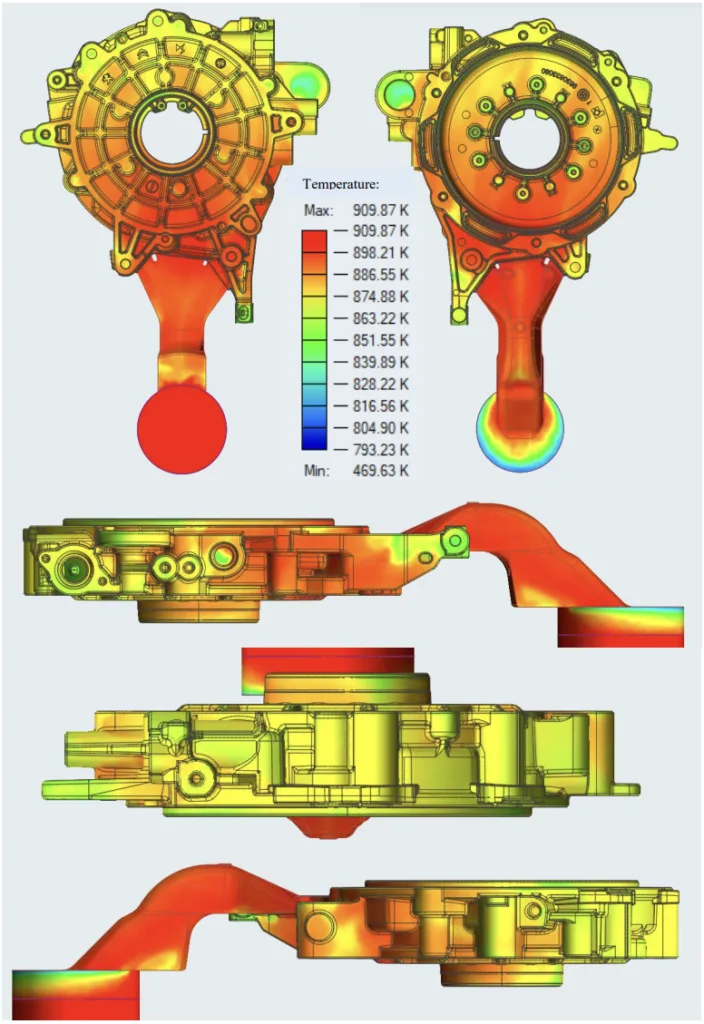
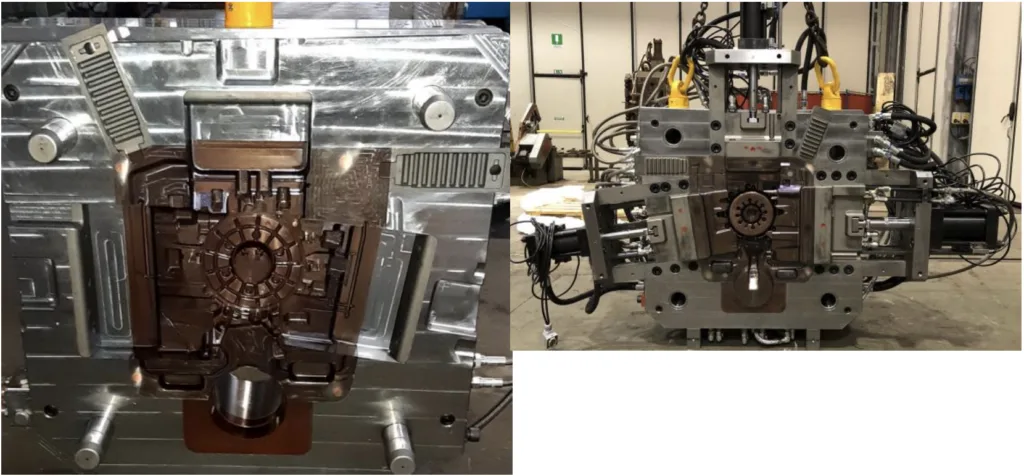
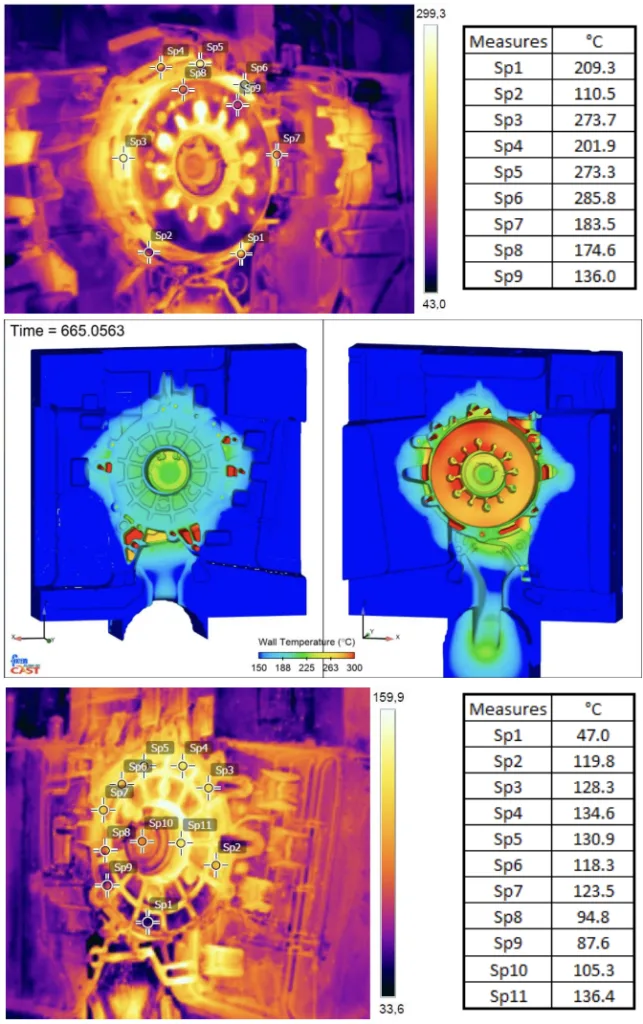
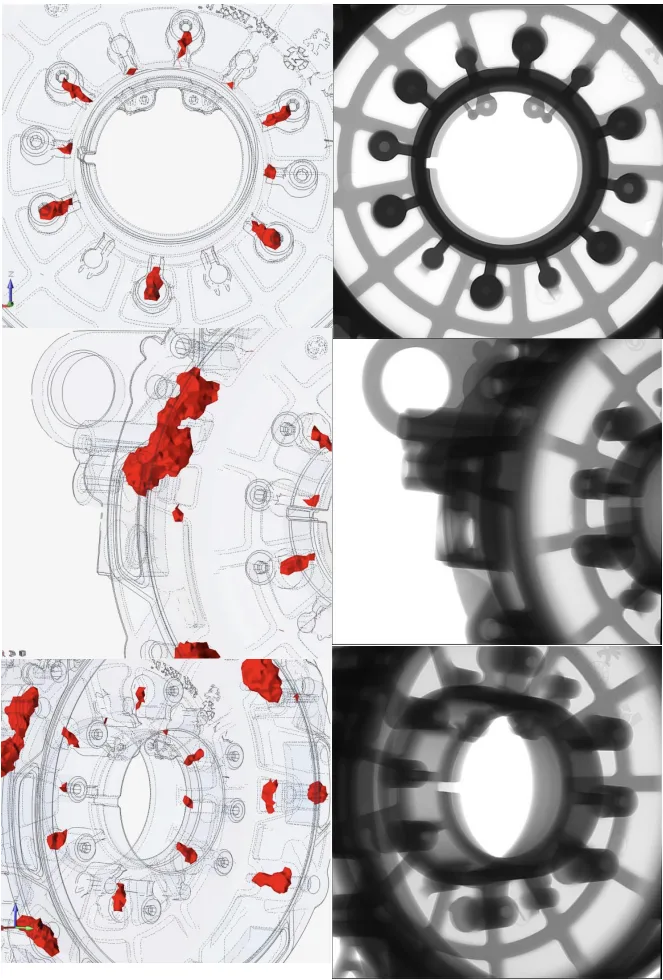
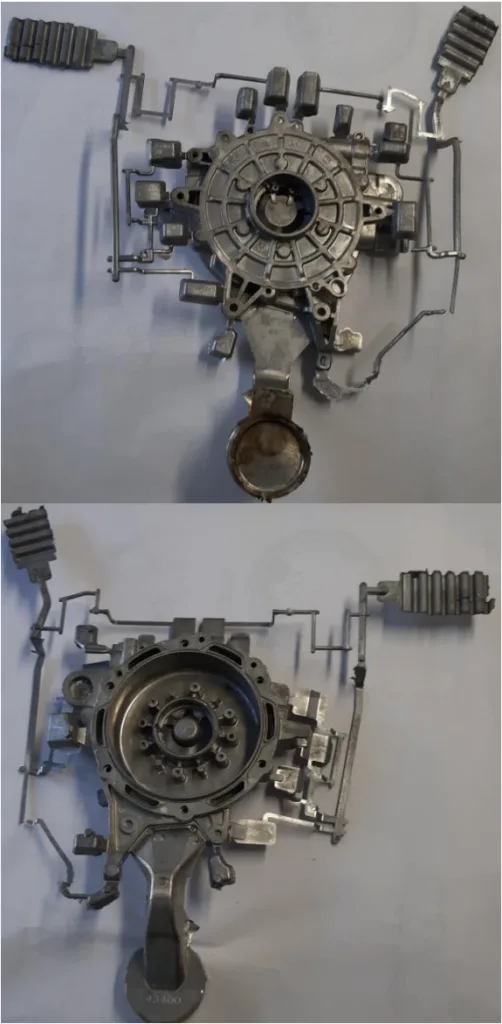
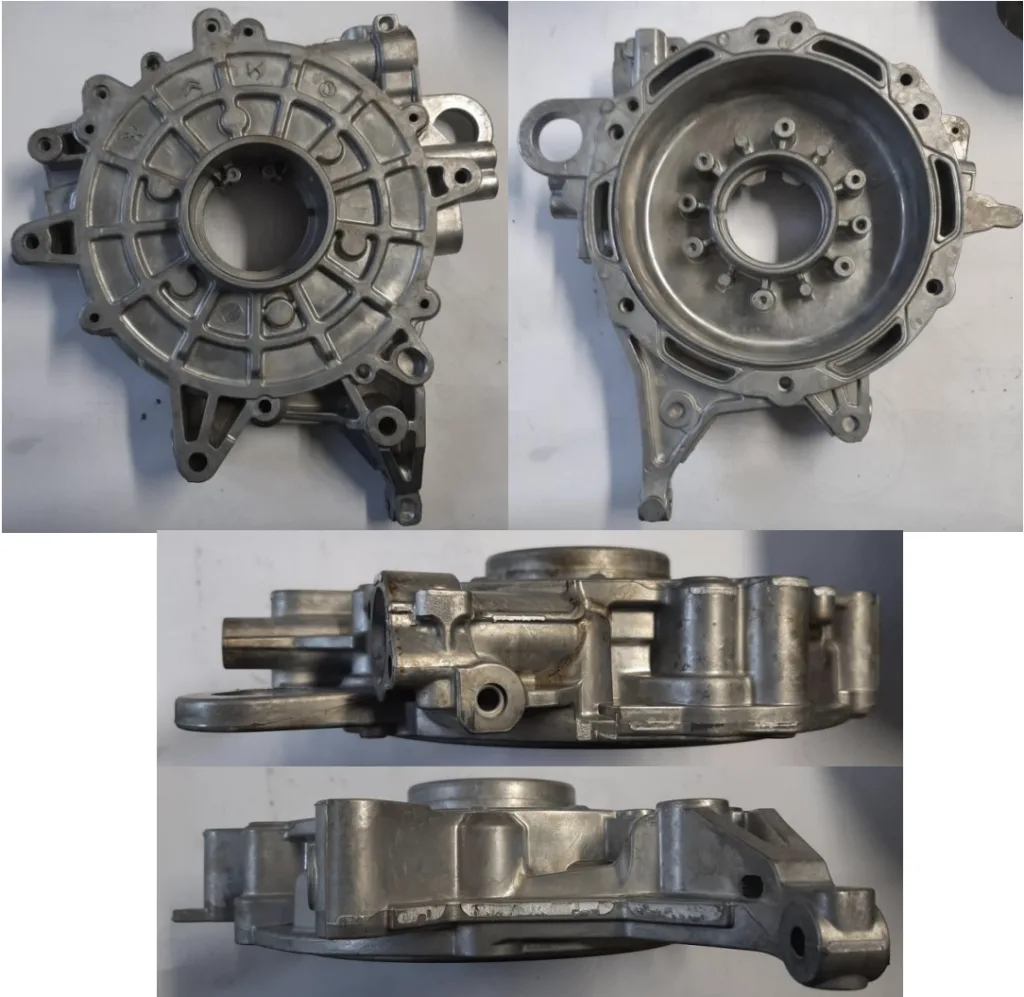
6. 結論:
主な結果の要約:
本研究では、複数のソフトウェアプラットフォームを使用して、電気モーターハウジングのHPDCプロセスをシミュレーションし、検証することに成功しました。この研究では、最適なメッシュ設定を特定し、ソフトウェア機能を比較し、実験データでシミュレーション予測を検証しました。主な調査結果には、潜在的な欠陥領域の特定、ダイの熱的挙動を考慮することの重要性、およびプロセス最適化のためのPQ2ダイアグラムの有用性が含まれます。本研究は、新しい自動車部品のHPDCを最適化する上でのシミュレーションツールの価値を実証しています。
研究の学術的意義:
本論文は、HPDC、特に電気モーターハウジングのような新しい自動車部品の文脈における学術的理解に貢献しています。従来の経験に基づいたHPDCの実践と、最新のシミュレーション駆動型アプローチとの間のギャップを埋めます。比較ソフトウェア分析は、ダイカストアプリケーションに適したシミュレーションツールを選択する上で、研究者や実務家にとって貴重な洞察を提供します。
実際的な意味合い:
調査結果は、HPDCを介した電気トランスミッション部品の持続可能な生産のための実用的なガイドラインを提供します。本研究は、プロセスパラメータを最適化し、欠陥を最小限に抑え、生産リードタイムとコストを削減する上でのシミュレーションの有効性を実証しています。シミュレーションと実験的検証を組み合わせた確立されたワークフローは、新規で複雑な部品をダイカストする産業実装のための貴重なテンプレートとして機能します。
研究の限界
研究は、いくつかの制限事項を認識しています。
- シミュレーション精度: シミュレーションは本質的に現実世界のプロセスの近似であり、HPDCのすべての複雑さを捉えているわけではありません。
- 計算コスト: 特に細かいメッシュと複雑なモデルを使用した高忠実度シミュレーションは、かなりの計算リソースと時間を必要とします。
- ソフトウェアの制限: 各ソフトウェアプラットフォームには、PIQ2 Castleの簡略化された熱ダイサイクルモデルやInspire Castの制限されたメッシュ制御など、固有の制限があります。
- 簡略化された金型モデル: シミュレーションされた金型は、実際のダイの簡略化された表現であり、熱シミュレーションの精度に影響を与える可能性があります。
- 実験的な不一致: 実験条件と測定の限界に起因する、シミュレーションされたダイ温度と測定されたダイ温度の間に差異が観察されました。
7. 今後のフォローアップ研究:
- フォローアップ研究の方向性
今後の研究方向には、以下が含まれます。 - 高度なオーバーフロー最適化: シミュレーションの洞察に基づいてオーバーフロー設計をさらに改良し、空気排出を強化し、気孔率を最小限に抑えます。
- 冷却システムの最適化: 熱管理を改善し、凝固時間を短縮するために、さまざまな冷却チャネル構成と冷却戦略を調査および最適化します。
- ダイエロージョン緩和: ダイエロージョンメカニズムの詳細な分析を実施し、ダイ摩耗を最小限に抑え、ダイ寿命を延ばすための戦略を検討します。
- 応力解析の統合: 冷却中の残留応力と潜在的な部品変形を予測するために、応力解析シミュレーションを組み込みます。
- ソフトウェアの機能強化: 現在の制限に対処するために、シミュレーションソフトウェアをさらに開発します。たとえば、改善された熱ダイサイクルモデルや、よりユーザーフレンドリーなメッシュ生成ツールなどがあります。
- さらなる探求が必要な領域
さらなる探求が必要な領域には、以下が含まれます。 - 改善されたダイ熱シミュレーション: より詳細な金型形状と熱伝達モデルを組み込むことにより、ダイ熱シミュレーションの精度を高めます。
- 洗練されたメッシュ生成技術: 複雑なダイカスト形状を処理し、メッシュ品質を向上させるために、より自動化され堅牢なメッシュ生成技術を開発します。
- 堅牢なシミュレーションワークフロー: 産業環境におけるHPDCプロセス設計と最適化のための標準化され検証されたシミュレーションワークフローを確立します。
- マルチフィジックスシミュレーション: 流体流れ、熱伝達、および凝固を、応力や変形などの他の関連現象と結合するために、マルチフィジックスシミュレーションを統合します。
8. 参考文献:
- Luigi Andreoni, “Quaderni della colata a pressione delle leghe d’alluminio”, EDIMET, 1993
- Buhler, “Ottimizzazione di processo”
- Andrea Manente, “Igiene delle leghe di alluminio”
- Altair University, “Learn Casting and Solidification with Altair Inspire Cast”
- Top 18 Die-Casting Defects and How to Fix Them, Five-Star Tooling, https://www.fstooling.com/what-cause-die-casting-defects-and-how-to-fix-them/
- EN AC-46000 (46000-F, AISi9Cu3(Fe)) Cast Aluminum, https://www.makeitfrom.com/material-properties/EN-AC-46000-46000-F-AISi9Cu3Fe-Cast-Aluminum/
- Flow 3D-cast, XC engineering, https://www.xceng.com/it/servizi/software-commerciali/flow-3d-cast/
- PIQ2, Castle, https://piq2.com/
- Fondalpress S.p.a, https://fondalpress.it/
9. 著作権:
- この資料は、"ジャンルイジ・ランツォーニ"の論文:"自動車アプリケーション向け電気モーターハウジングの高圧ダイカストのシミュレーションと検証"に基づいています。
- 論文ソース:[DOI URL]
この資料は上記の論文に基づいて要約されたものであり、商業目的での無断使用は禁止されています。
Copyright © 2025 CASTMAN. All rights reserved.