本紹介論文は、「[INTERNATIONAL JOURNAL OF INNOVATIONS IN ENGINEERING RESEARCH AND TECHNOLOGY [IJIERT] (NOVATEUR PUBLICATIONS)]」によって発行された論文「[DEVELOPMENT AND APPLICATION OF CASTING DISTORTION & COMPENSATION TECHNOLOGY BASED ON AUTOMATIC ITERATION METHOD]」に基づいています。
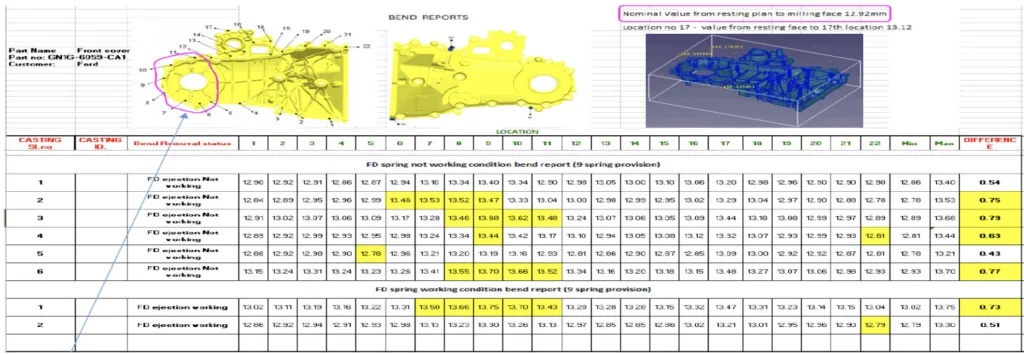
1. 概要:
- タイトル: DEVELOPMENT AND APPLICATION OF CASTING DISTORTION & COMPENSATION TECHNOLOGY BASED ON AUTOMATIC ITERATION METHOD (自動繰り返し法に基づく鋳造変形および補正技術の開発と応用)
- 著者: DR. XIAOJUN YANG, MS. RAJESHWARI SANJAY RAWAL
- 発行年: 2020
- 発行学術誌/学会: INTERNATIONAL JOURNAL OF INNOVATIONS IN ENGINEERING RESEARCH AND TECHNOLOGY [IJIERT] (NOVATEUR PUBLICATIONS)
- キーワード: Die-casting, casting warp, distortion, compensation, automatic iteration, Cast-Designer, DCS (Distortion Compensation Solver), thermal stress, mechanical stress, finite element method.
2. 抄録:
鋳造のそりや変形は、ダイカスト生産においてしばしば遭遇する主要な欠陥の一つであり、解決が非常に困難です。従来の方法には、低効率、重労働、劣悪な作業環境といった問題がありました。本稿では、Cast-Designerが新たに開発した変形補正ソルバーDCS(Distortion Compensation Solver)を紹介します。これは、事前に鋳造の変形やそりを予測し、自動繰り返し最適化技術によって公差要件を満たす鋳造製品を見つけることができます。このようなツールと技術により、鋳造変形を効果的に低減し、直接的に機械加工要件を満たすことが可能になります。
3. 緒言:
先進的な製造技術として、ダイカストは高い寸法精度、良好な機械的特性、高い生産効率という利点を持っています。自動車用アルミニウムおよびアルミニウム-マグネシウム合金部品の生産において、強力な技術的・経済的優位性があります。しかし、様々な理由から、多くのダイカストアルミニウム部品では、初期設計段階で製造要因がほとんど考慮されていません。複雑な構造、大きな肉厚差、高い精度要求は、ダイカストの開発と生産において大きな課題となります。中でも、変形やそりの欠陥は、複雑な鋳造品において一般的で制御が難しい問題の一つです。鋳造変形欠陥は、不適切な鋳造品設計、突き出し時のアンバランス、金型温度の不均衡など、多くの原因によって引き起こされます。変形欠陥が鋳造品の品質に与える影響は主に以下の通りです:1) 鋳造品の寸法精度への影響;2) 後工程の機械加工への影響;3) 鋳造後に深い機械加工が必要な部品の場合、鋳造品表面の緻密層が除去されることで内部の巣欠陥(気孔や収縮など)が露出し、鋳造品の外観やシール性能(シール要件のある部品の場合)に影響を与える。
4. 研究の概要:
研究テーマの背景:
鋳造変形(そり)は、ダイカスト生産における重要かつ解決困難な欠陥です。これは、不適切な鋳造品設計、突き出し時の不均衡な力、不均一な金型温度など、様々な原因から生じます。この欠陥は、鋳造品の寸法精度を損ない、必要な後工程の機械加工を複雑にします。鋳造後に大幅な材料除去が必要な部品の場合、変形によって気孔や収縮といった内部欠陥が露呈する可能性があります。
従来の研究状況:
鋳造変形を管理するための従来の方法には以下が含まれます:
- 方法1:プロセスパラメータ調整: 金型設計、スプレー冷却、ダイカストプロセスパラメータの調整などを通じて変形を技術要件内に制御します。この方法では、指定された値内の変形を持つ完全に許容可能な鋳造部品を常に得られるとは限りません。また、この方法の別の問題は加工安定性です。
- 方法2:鋳造代の増加: 機械加工が必要な部品に対して、鋳造代を増やし、機械加工後に必要な寸法精度を確保します。この方法の結果は明らかです。加工代を増やすことは、鋳造品の肉厚を増やすことと同等です。ダイカスト中の鋳造品の気孔や収縮などの内部欠陥が増加し、後工程の機械加工後に巣欠陥が露呈する確率が高まります。したがって、ダイカストの変形を解決するために加工代を増やすことは、正しい方法ではありません。
- 方法3:人手による矯正方法: 変形限界を超える鋳造品に対して、通常、寸法修正のために矯正方法が用いられます。従来の木製ナイフ、木槌、木製スツールなどの道具を用いて鋳物を叩き、鋳造品の冷却後、湯口やランナー、オーバーフロー、バリを除去した後に、鋳物の変形度を強制的に低減させます。この方法は非効率的で、重労働、騒音、結果が悪く、製品を叩くプロセスは亀裂を引き起こす可能性があり、実際の生産でスプリングバックしやすいです。
- 方法4:ホットオルソティックス: 機械加工前に矯正を行い、鋳造変形を低減し、すべての機械加工面に十分な加工代を確保します。ダイカストのホットオルソティック作業は、金型から突き出されたばかりの高温(約200℃)と良好な塑性の特性を利用し、機械と矯正金型を通して強制的に押し付けて変形を低減させます。この方法は非常に複雑なプロセスと強力な水冷を必要とします。
これらの従来のアプローチは、しばしば低効率、重労働、劣悪な作業環境を伴います。
研究の目的:
本稿では、Cast-Designerが新たに開発したDistortion Compensation Solver (DCS)を紹介します。この研究は、事前に鋳造の変形やそりを予測し、自動繰り返し最適化を利用して公差要件を満たす鋳造製品を見つける技術を実証することを目的としています。目標は、鋳造変形を効果的に低減し、従来の方法の限界を克服して、直接的に機械加工要件を満たすことです。
中核研究:
研究の中核は、Cast-Designerソフトウェアスイート内で開発されたDistortion Compensation Solver (DCS)技術に焦点を当てています。この技術は自動繰り返し法を採用しています。まず、有限要素解析を用いて熱応力と機械的応力、およびそれによって生じる変形を計算する、鋳造プロセスの正確なシミュレーションから始まります。予測された変形に基づいて、DCSは予測された変形の反対方向に補正を適用することにより、金型キャビティ形状を繰り返し修正します。このプロセスは、凝固および冷却後の最終的な鋳造品が指定された寸法公差内に収まるようにすることを目的としています。
5. 研究方法論
研究設計:
研究方法論には、Cast-Designerソフトウェアを使用して特定の自動車部品のダイカストプロセスをシミュレーションすることが含まれていました。シミュレーションは、熱応力と機械的応力、およびそれによって生じる変形を正確に予測することに焦点を当てました。これらのシミュレーション結果は、実際の鋳造部品から測定された平坦度測定値と比較することによって検証されました。その後、予測された変形に基づいて部品形状を修正するために自動繰り返しアプローチを使用するDistortion Compensation Solver (DCS)が適用され、最終的な鋳造部品の変形を最小限に抑えることを目指しました。
データ収集および分析方法:
- データ収集:
- シミュレーションデータは、Cast-Designerの応力モジュールを使用して生成され、熱、流動、応力現象の完全連成解析(full-coupling analysis)を実行しました。シミュレーションでは、金型拘束、金型開閉、材料特性(弾塑性モデル)、プロセスパラメータ(例:金型開閉時間、突き出し温度、冷却)が考慮されました。
- 物理データは、1つのバッチからランダムに選択された6つの鋳造部品の平坦度を、定義された22の測定点を使用して測定することによって収集されました。
- 分析方法:
- シミュレーションされた変形(平坦度)結果は、物理テストピース(具体的にはサンプルNo. 2、3、4)からの実際の平坦度測定値と比較され、シミュレーションの精度が検証されました。
- DCSは自動繰り返し補正法を利用しました。1回の繰り返しで計算された変形に基づいて、次の繰り返しのためのメッシュ節点座標を調整するために補正係数が適用されました。このプロセスは、最終的な鋳造品の予測変形がユーザー定義の公差要件を満たすまで繰り返されました。
研究トピックと範囲:
- 研究トピック: この研究では、高圧ダイカストにおける鋳造変形とそりの予測、およびこれらの欠陥を最小化するための自動繰り返し補正法(DCS)の適用を調査しました。主要なトピックには、正確な応力/ひずみシミュレーション(熱的および機械的)、シミュレーション検証、補正のための形状修正が含まれていました。
- 範囲: 研究は、Ford向けの「Front cover」(部品番号:GN1G-6059-CA1)として特定された特定の複雑な自動車鋳造部品に適用されました。部品寸法は438 X 350 X 145 mmで、平均肉厚は3.3mmでした。研究は、鋳造および冷却後の特定の表面で0.5mmの平坦度要件を達成することに焦点を当てました。
6. 主な結果:
主な結果:
- Cast-Designerを使用して、熱伝達、凝固、金型拘束、金型開閉などの要因を考慮した、ダイカストプロセス中の応力(熱的および機械的)と変形の正確なシミュレーションが達成されました。
- 部品の平坦度に関するシミュレーション結果は、物理テストピース(No. 2、3、4)から得られた実際の平坦度測定値と非常によく一致し、シミュレーションモデルが検証されました(Figure 3)。
- Distortion Compensation Solver (DCS)は、自動繰り返し補正法を成功裏に適用しました。初期のシミュレーションされた変形は0.5mmの平坦度公差を超えていました(0.8mm以上に達しました)。
- DCSを使用した4回の自動繰り返し計算の後、室温まで冷却された後の鋳造品の最終的な予測平坦度は0.05mmから0.15mmの間に維持されました。
- この結果は、補正された金型形状を使用して鋳造された製品が、指定された公差内で直接供給の機械加工生産要件を100%満たすことを示しています。
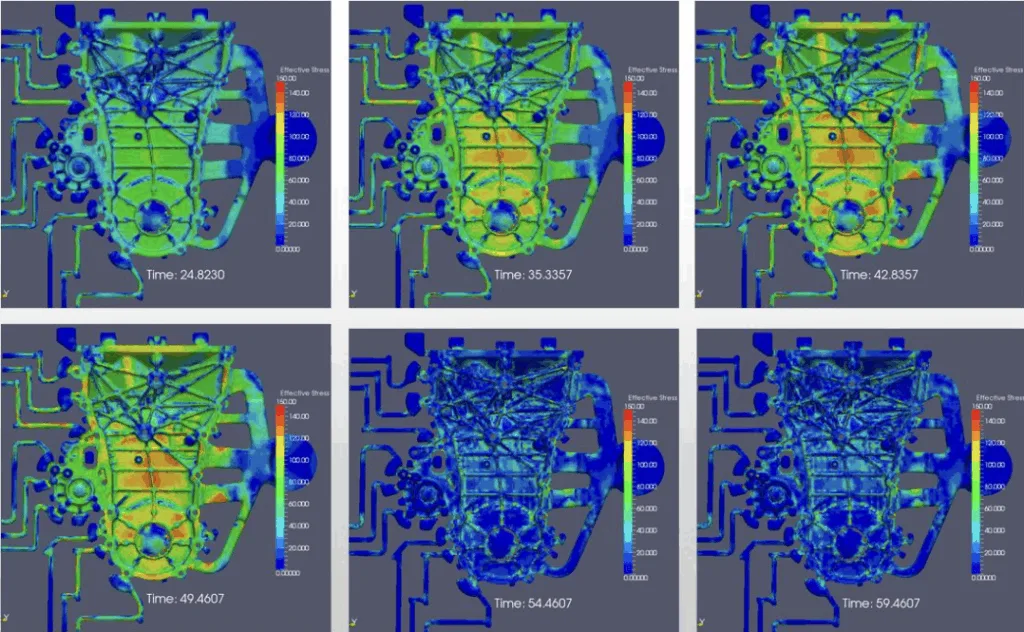
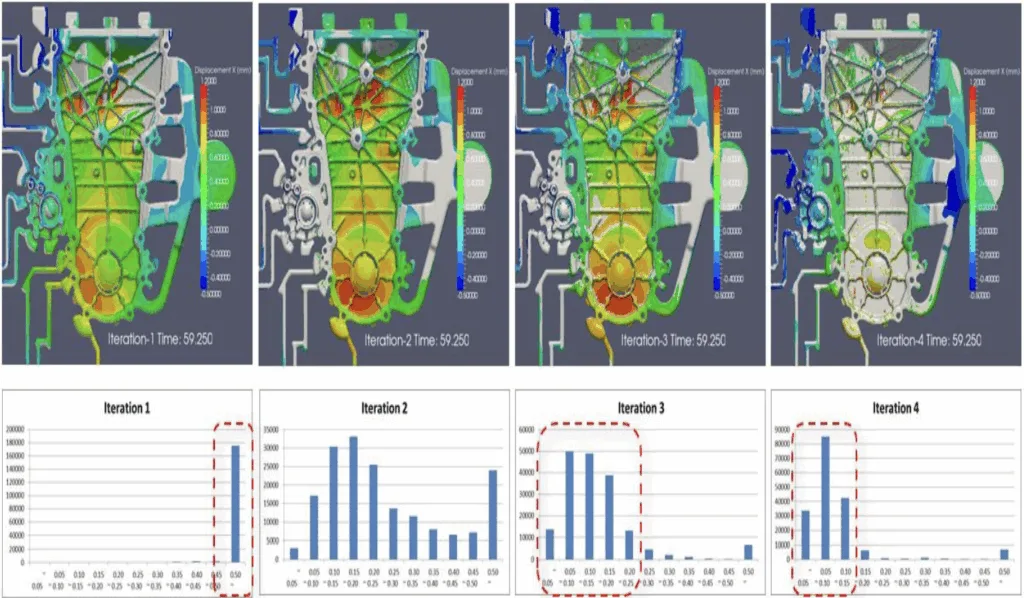
図の名称リスト:
- Figure 1 Casting part and dimension after casting, the yellow cells are out of tolerance
- Figure 2 Effective stress contours vs. Time
- Figure 3 Part flatness analysis (simulation results vs. the actual measurement results)
- Figure 4 The first line: left: before casting right: after casting The second line with compensation: left: before casting right: after casting
- Figure 5 The compensation result after four iterations
7. 結論:
コンピュータシミュレーションと自動繰り返し補正法を使用することで、鋳造の変形や歪みの問題を効果的に解決できます。この方法は、通信製品、ヒートシンク、カバー、自動車部品などの複雑な形状の鋳造に有効です。
大量注文の場合、またはチェーンカバー、オイルパネル、電気自動車の電気カバー、その他の鋳造品のように、製品が大きな平坦構造と平坦度要件を持つ自動車部品の場合、変形補正技術の適用は効率を向上させ、人件費を削減することができます。
8. 参考文献:
- [1] A.A. Luo, “Magnesium casting technology for structure applications," Journal of Magnesium and Alloys, vol. 1, pp. 2–22, 2013.
- [2] K.K.S. Thong, B.H. Hu, X.P. Nui and I. Pinwill, “Cavity pressure measurements and process monitoring for magnesium die casting of a thin-wall-hand-phone component to improve quality,” J. Mater. Process. Tech., vol. 127, pp. 238–241, 2002.
- [3] Piyanut Meethum, Chakrit Suvanjumrat,“Evaluate of Chill Vent Performance for High Pressure Die-Casting Production and Simulation of Motorcycle Fuel Caps”, MATEC Web of Conferences 95, 07025 (2017) DOI: 10.1051/matecconf/2017950 ,ICMME 2016
- [4] P. Meethum, C. Suvanjumrat, “Porosities Comparison between Production and Simulation in Motorcycle Fuel Caps of Aluminum High Pressure Die Casting", World Academy of Science, Engineering and Technology International Journal of Mechanical and Mechatronics Engineering Vol:9, No:3, 2015.
9. 著作権:
- 本資料は「DR. XIAOJUN YANG, MS. RAJESHWARI SANJAY RAWAL」による論文です。「DEVELOPMENT AND APPLICATION OF CASTING DISTORTION & COMPENSATION TECHNOLOGY BASED ON AUTOMATIC ITERATION METHOD」に基づいています。
- 論文の出典: [論文中にDOI URLの記載なし]
本資料は上記の論文に基づいて要約されており、商業目的での無断使用は禁じられています。
Copyright © 2025 CASTMAN. All rights reserved.