本記事では、[電気製鋼]が発行した論文「Prediction and Evaluation of Ejecting Stress Distribution at Die Surface of Die-Casting through Numerical Analyses」を紹介します。
1. 概要:
- タイトル: Prediction and Evaluation of Ejecting Stress Distribution at Die Surface of Die-Casting through Numerical Analyses
- 著者: Masamichi KAWANO, Satoshi UNO and Naoki YOKOI
- 発行年: 2017年
- 発行ジャーナル/学会: 電気製鋼, 第88巻, 1号, pp. 33-38
- キーワード: Die casting, Ejecting stress, Soldering, Numerical analysis, MAGMASOFT, Fe-Al compound layer, AMICOAT®-D
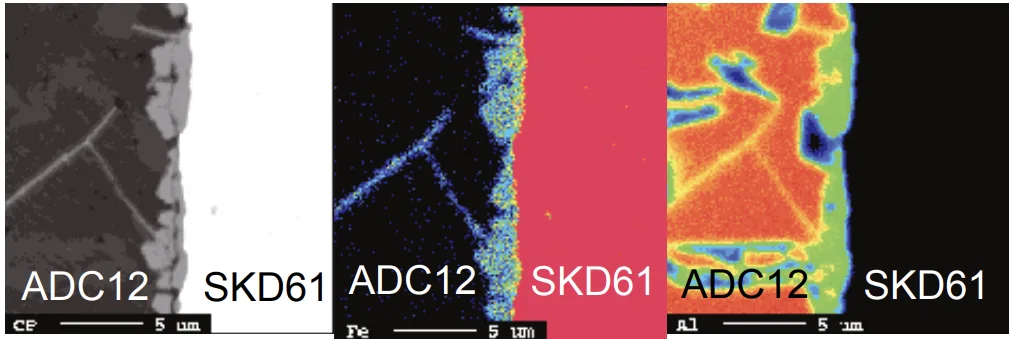
2. 概要またははじめに
ダイカスト鋳造法は、アルミニウム合金などの溶融金属(以下、溶湯という)を金型のキャビティ内に短時間で圧入し急速凝固させることで、寸法精度の高い複雑形状品を高効率で製造する方法である。しかし、ダイカスト金型のキャビティ面は、600~700℃の溶湯との接触によって450~550℃に加熱されることがある。このような高温となる部位では、鋳造品取り出し時にアルミニウム合金が金型に溶着して残存する「焼付き」が発生しやすい。焼付き部では、鋳造品と金型の界面に Fe/Al 反応層が形成されている。
焼付きは製品の表面品質や寸法精度を害するため、金型に付着したアルミニウム合金は除去しなければならない。そのために鋳造の一時停止を余儀なくされ、生産性が大きく低下する。また、焼付きが顕著で除去し切れない場合は金型の交換が必要となり、型費の増加を招く。以上の理由から、焼付き回避がダイカストの重要課題となっている。鋳造方案の策定においては、焼付きやすい部位の把握と、焼付き回避策を講じておくことが求められる。
焼付きへの影響因子は、表面処理の種類、内冷回路の位置と水量、溶湯温度、射出条件など多岐にわたる。これらの要因を鋳造の試行錯誤で適正化する試みは非効率的であるうえ、最適解を得ることも容易ではない。そこで、焼付き回避策の検討には、諸条件を系統的かつ容易に変化させられる湯流れ解析を積極的に利用することが多い。
湯流れ解析による焼付き回避策の検討においては、工程設計の確度を高めるため、冶金現象(拡散による Fe/Al 反応層形成)に準じた指標が必要と考えられる。そこで、本論文では、鋳造品を金型から取り出す際の「離型抵抗」に着目し、反応層形成との相関づけを試みた。本論文では、実験で求めた離型抵抗の予測式を湯流れ解析に組み込み、焼付き評価指標としての有効性を検証する。
3. 研究背景:
研究トピックの背景:
ダイカストにおける焼付きは、製品の品質と寸法精度を損ない、金型からアルミニウムを除去するために生産を停止する必要があり、場合によっては高価な金型交換が必要になるため、重大な問題です。したがって、焼付きを回避することは、ダイカスト作業における重要な目標です。焼付きが発生しやすい領域を特定し、効果的な対策を実施することは、堅牢なプロセス設計に不可欠です。
既存研究の状況:
従来の焼付き軽減アプローチは、多くの場合、非効率的な試行錯誤による鋳造パラメータの調整に頼っていました。湯流れ解析は焼付き対策を検討するためにますます利用されていますが、これらの手法は、焼付きの冶金学的メカニズムに基づいた定量的に堅牢な指標を欠いていることがよくあります。鋳造試験による最適化は非効率的であり、最適な解決策が得られない可能性があります。湯流れ解析は、焼付き対策を検討するために、条件を系統的かつ容易に変更するために積極的に使用されています。
研究の必要性:
焼付き対策のための湯流れ解析を用いたプロセス設計の精度を向上させるためには、冶金現象、特に Fe/Al 反応層の形成に合致する指標が必要です。ダイカスト界面での基礎となる冶金学的反応に基づいて、焼付きの程度を反映する信頼性の高い指標が必要です。
4. 研究目的と研究課題:
研究目的:
本研究の目的は、焼付きの根本原因である Fe/Al 反応層の形成に基づいて、ダイカストにおける金型表面の離型抵抗分布を予測および評価する方法を開発することです。実験的に導き出された離型抵抗の式を湯流れ解析ソフトウェアに組み込むことで、離型抵抗を焼付きポテンシャルを評価するための効果的な指標として検証することを目的としています。
主な研究課題:
主な研究課題は、離型抵抗をダイカストにおける焼付きリスクを評価するための定量的な指標として確立することです。これには以下が含まれます。
- Fe/Al 反応層の形成に基づいて離型抵抗を予測する式を導き出す。
- この式を湯流れ解析に統合する。
- 数値解析と実験的検証を通じて、離型抵抗を焼付きの信頼できる指標として検証する。
5. 研究方法
研究デザイン:
本研究では、MAGMASOFT ソフトウェアを用いた数値解析アプローチを採用し、ダイカスト中の溶湯の流れと温度分布をシミュレーションしました。Fe/Al 化合物層の形成に基づいた導出された離型抵抗式をソフトウェアに統合し、金型表面の離型抵抗分布を予測しました。
データ収集方法:
離型抵抗を定量化するために、東芝機械株式会社製 DC-135JT 135トン ダイカストマシンを用いて実験を実施しました。SKD61 製のコアピン状試験片を使用し、ADC12 アルミニウム合金を鋳造しました。熱電対をコアピンの表面付近に挿入して温度を測定しました。突き出し荷重は、エジェクタピン背面のロードセルで測定しました。
分析方法:
離型抵抗 F (MPa) は、突き出し荷重 PN (ロードセルで測定) をエジェクタピンの表面積で割ることによって計算しました。Fe/Al 反応層の形成に関連する焼付きパラメータ S は、exp(-Q/R/Ts) の時間積分を用いて計算しました。焼付きパラメータ S と離型抵抗 F の相関関係を分析しました。FEM (有限要素法) 解析を用いて、熱電対測定値と熱解析結果を相関させることにより、表面温度 Ts を推定しました。
研究対象と範囲:
本研究では、ダイカストで一般的に使用されている SKD61 金型鋼と ADC12 アルミニウム合金の界面に焦点を当てました。研究の範囲は、溶融金属温度、金型冷却、表面処理など、さまざまなダイカスト条件下での金型表面の離型抵抗を予測および評価することでした。
6. 主な研究成果:
主な研究成果:
- 離型抵抗式の導出: SKD61 と ADC12 の境界における Fe/Al 化合物層の形成を考慮して、金型表面の離型抵抗の式を導き出しました。Fe/Al 反応の活性化エネルギー Q は 313 kJ/mol と推定されました。
- 鋳造条件の影響: 数値解析の結果、溶融 ADC12 温度の低下と内部水路による金型冷却が離型抵抗を効果的に低減することが示されました。
- 表面処理の効果: 内部水冷却なしで溶融 ADC12 温度が高い条件下でも、「AMICOAT®-D」表面処理により、離型抵抗の大幅な低減が観察されました。
- S と F の相関: 焼付きパラメータ S (Fe/Al 反応層の厚さに関連) と離型抵抗 F の間に明確な正の相関関係が確立され、式 F = C1⋅SC2 で表されました。
提示されたデータの分析:
- 図 3: (a) 突き出し荷重 P と (b) 離型抵抗 F の違いを示しています。コアピンの表面積で補正された離型抵抗 F は、焼付きの重症度をサイズに依存しない尺度で提供します。図 3(b) は、焼付きの温度感受性の高い領域を示しており、約 432℃ 付近で 14℃ 温度が上昇すると離型抵抗が 5 MPa から 10 MPa に倍増します。
- 図 5: (a) 表面温度 Ts と (b) 焼付きパラメータ S=∫(exp(-Q/R/Ts))dt の過渡変化を示しています。Fe/Al 反応に関連する積分された熱履歴を表す焼付きパラメータ S は、離型抵抗と相関していることが示されています。
- 図 6: 焼付きパラメータ S と離型抵抗 F の関係を示しています。塩浴軟窒化 (PS) や PVD (AMICOAT®-D) などの表面処理は、無処理と比較して離型抵抗を大幅に低減します。
- 図 9: さまざまな条件下での鋳造離型抵抗 F の分布を示しています。図 9(a) (700℃ 溶融金属、冷却なし) は、最も高い離型抵抗を示しています。溶融金属温度を 650℃ に下げる (図 9(b))、水冷を適用する (図 9(c))、および AMICOAT®-D 表面処理を使用する (図 9(d)) ことはすべて、離型抵抗を効果的に低減します。
図のリスト:
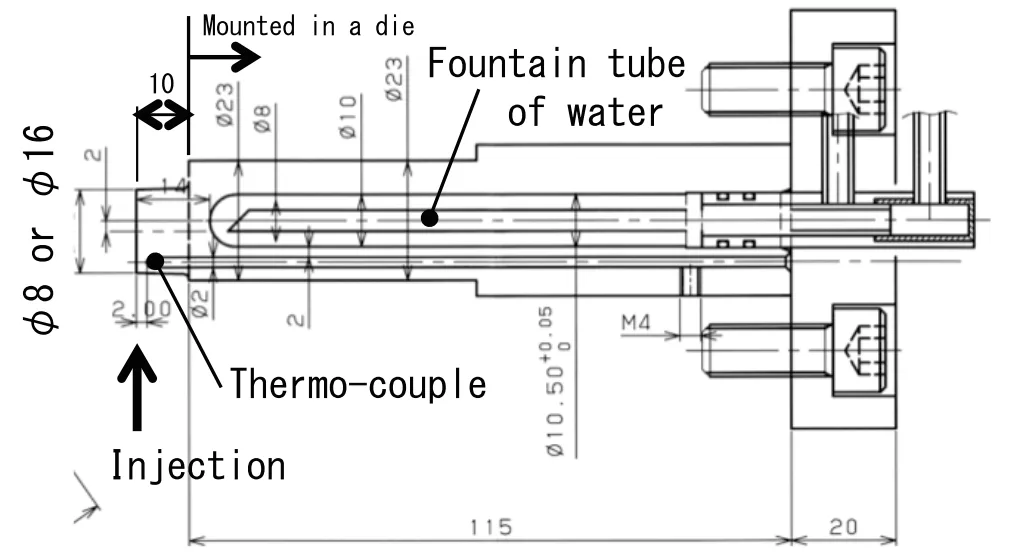
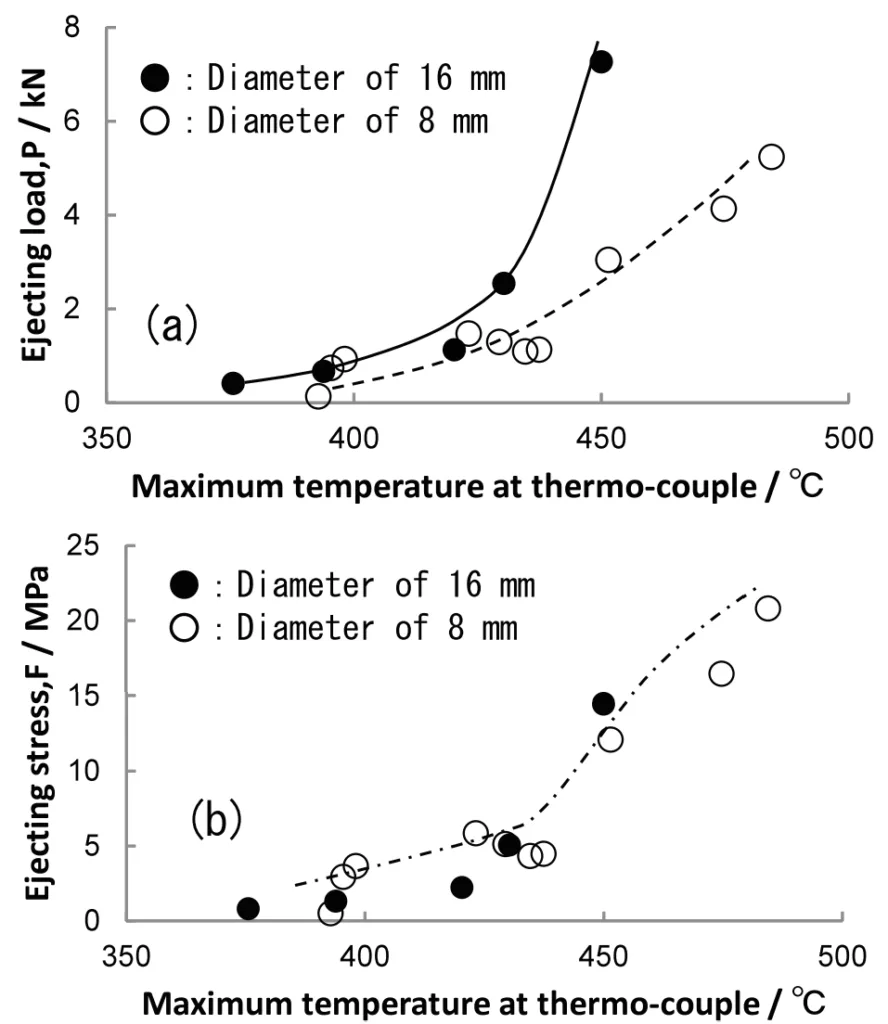

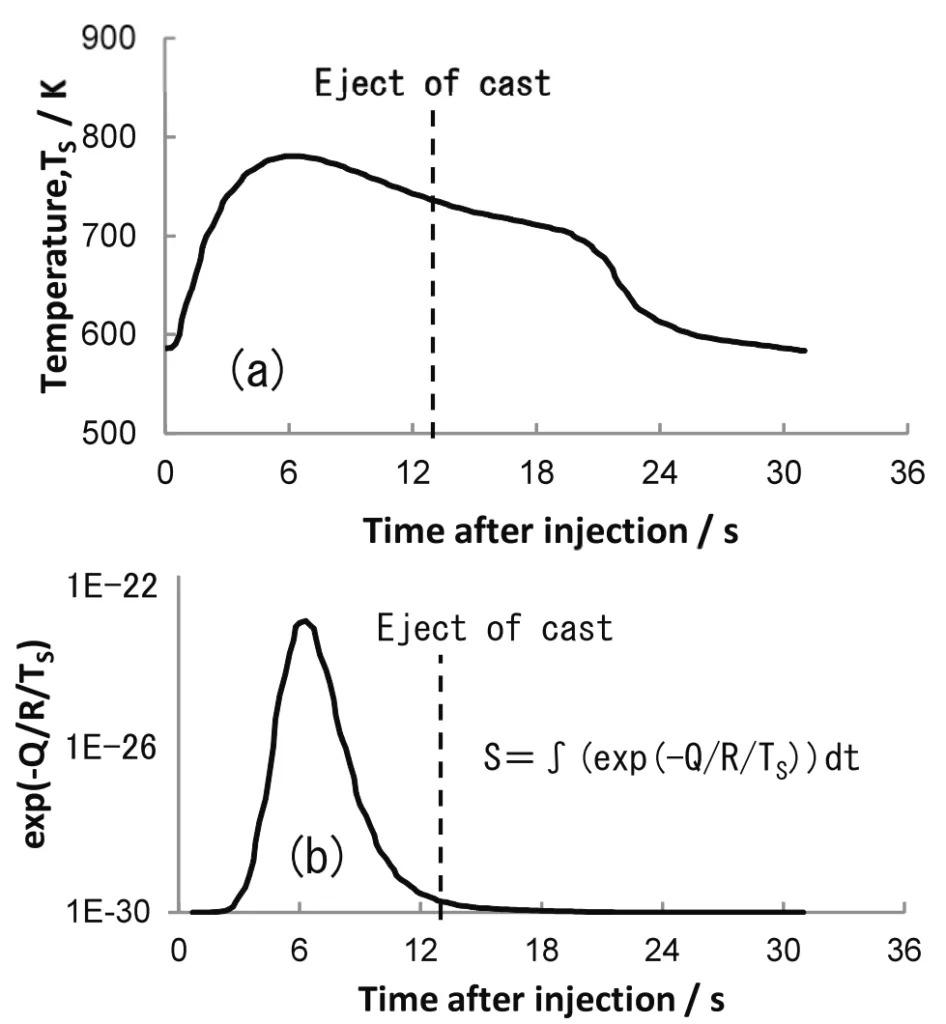
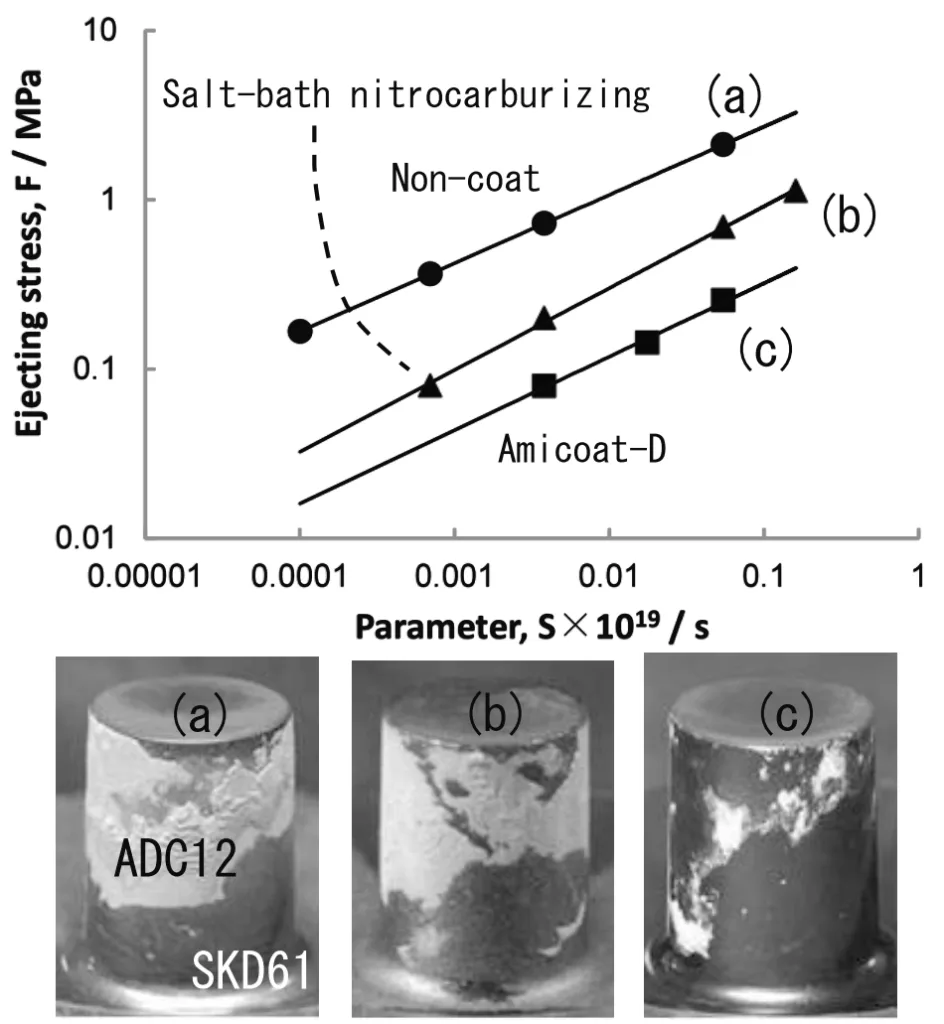
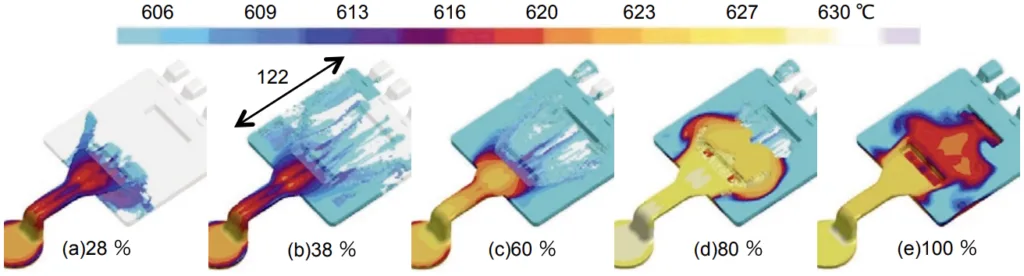
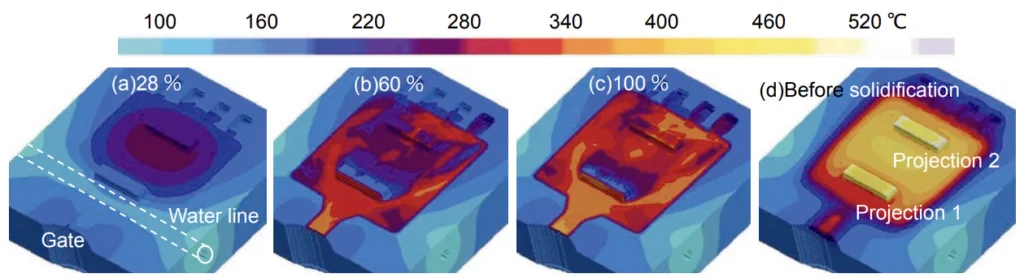
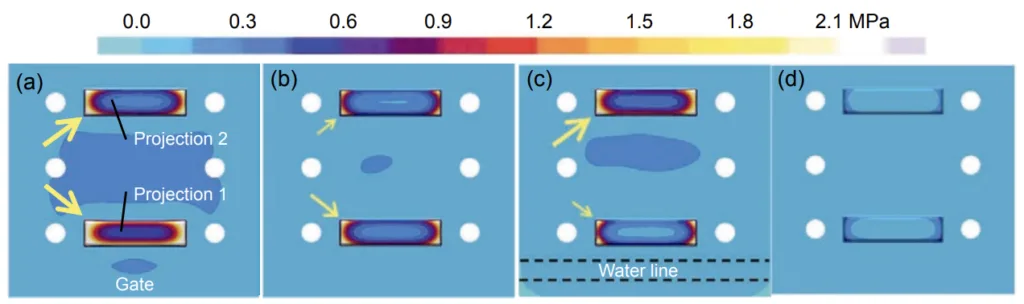
- Fig. 1. Distribution of Fe and Al at soldering part. Fe/Al compound layer is observed.
- Fig. 2. Core-pin like specimen of soldering experiment on die-casting. Dimension is given in millimeters. Specimen is mounted in a die located close to the injection gate. A thermo-couple is inserted at 1 mm below the surface of the specimen.
- Fig. 3. Difference between (a) ejecting load P and (b) ejecting stress F. F is given by considering the surface area of core-pin then size effect is compensated.
- Fig. 4. Estimated temperature distribution through FE-analysis. Marked influence of (a) time and (b) depth from a surface on temperature can be seen.
- Fig. 5. Transition change of (a) surface temperature Ts and (b) soldering parameter S=f(exp(-Q/R/Ts))dt.
- Fig. 6. Relationship between soldering parameter S and ejecting stress F.
- Fig. 7. Flow behavior and temperature of molten ADC12 in a cavity. Filling rate given by volume fraction represent from (a) 28 percent up to (e) 100 percent.
- Fig. 8. Transition of die temperature. Filling rate of molten ADC12 represent (a) 28 percent up to (c) 100 percent. At 6 seconds after filling corresponds to (d) just before finish of solidification.
- Fig. 9. Distribution of cast ejecting stress F. (a), (b), (c) and (d) represent molten ADC12 of 700 °C, molten ADC12 of 650 °C, water cooling line in a die with molten ADC12 of 700 °C and surface treatment “AMICOAT®-D" with molten ADC12 of 700°C under the condition of no internal water cooling respectively.
7. 結論:
主な知見のまとめ:
本研究では、離型抵抗をダイカストにおける焼付き評価のための定量的な指標として策定し、検証することに成功しました。主な知見は次のとおりです。
- Fe/Al 反応層の形成に基づいた離型抵抗式を導出し、推定活性化エネルギー Q は 313 kJ/mol でした。
- 溶融金属温度の低下、金型冷却、AMICOAT®-D 表面処理が離型抵抗を効果的に低減することを実証しました。
- 焼付きパラメータ S と離型抵抗 F の相関関係を確立し、湯流れ解析による焼付きポテンシャルの予測を可能にしました。
研究の学術的意義:
本研究では、ダイカストにおける焼付きリスクを評価するための、客観的で温度感受性の高い新しい指標である離型抵抗 F を導入しました。臨界温度に依存する従来の主観的な方法とは異なり、離型抵抗は Fe/Al 反応層形成の冶金現象に直接関連する定量的な尺度を提供します。
実用的な意義:
離型抵抗 F は、ダイカストにおけるプロセス設計と最適化のための実用的な指標として活用できます。湯流れ解析を通じて離型抵抗分布を予測することにより、エンジニアは、鋳造条件の調整、冷却システムの最適化、適切な表面処理の選択など、さまざまな焼付き対策の有効性を定量的に評価できます。プロセス設計のガイドラインは、離型抵抗 F が鋳造品の強度または引張強度を超えないようにすることです。
研究の限界と今後の研究分野:
本研究は、焼付き評価のための貴重なフレームワークを提供しますが、今後の研究では、金型表面粗さ、突き出し速度、異なる合金系などの他の要因が離型抵抗と焼付き挙動に及ぼす影響を調査する可能性があります。より広範囲のダイカストプロセスと形状にわたるさらなる検証も、離型抵抗指標の一般的な適用性を強化するでしょう。
8. 参考文献:
- 1) 青山俊三,下条浩:鋳造工学会 131回全国講演大会講演概要集(1997), 94.
- 2) 柴田浩二,諸住正太郎,幸田成康:日本金属学会誌, 30(1966), 382.
- 3) 伊吹基宏,尾崎公造:電気製鋼,76(2005), 241.
- 4) 西直美:鋳造工学,70(1998), 648.
- 5) 三中西信治,小川裕二,鈴木孝尚:鋳造工学会 130回全国講演大会講演概要集(1997), 54.
- 6) 特開2011-79053.
- 7) 西田公至:生産研究,28(1976), 464.
- 8) http://www.zerocut-watanabe.co.jp/pg321.html
9. 著作権:
- この資料は、「Masamichi KAWANO, Satoshi UNO and Naoki YOKOI」の論文:「Prediction and Evaluation of Ejecting Stress Distribution at Die Surface of Die-Casting through Numerical Analyses」に基づいています。
- 論文ソース: [DOI URL は利用可能であれば追加されます。それ以外の場合は、論文ソース情報を使用してください]
この資料は上記の論文を紹介するために作成されたものであり、商業目的での無断使用は禁止されています。
Copyright © 2025 CASTMAN. All rights reserved.