この紹介資料は、「International Journal of Engineering and Management Research」に掲載された論文「Analysis and Optimisation of High Pressure Die Casting Parameters to Achieve Six Sigma Quality Product Using Numerical Simulation Approach」に基づいています。
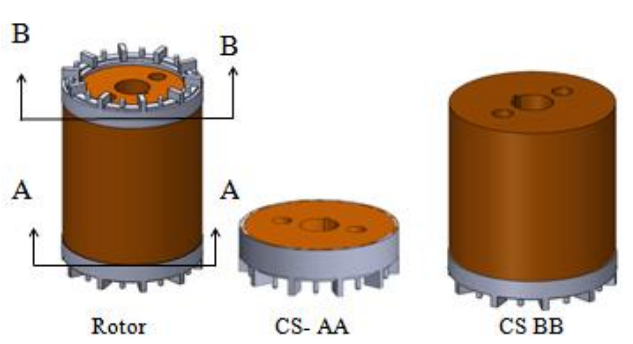
1. 概要:
- タイトル: 数値シミュレーションアプローチを用いたシックスシグマ品質製品達成のための高圧ダイカストパラメータの解析と最適化 (Analysis and Optimisation of High Pressure Die Casting Parameters to Achieve Six Sigma Quality Product Using Numerical Simulation Approach)
- 著者: Suraj R. Marathe¹ and Dr. Carmo E. Quadros² (¹研究員, 機械工学科, ASSAM DON BOSCO大学, インド; ²教授, 機械工学科, ASSAM DON BOSCO大学, インド)
- 発行年: 2021年 (2月)
- 発行学術誌/学会: International Journal of Engineering and Management Research
- キーワード: 高圧ダイカスト (HPDC), パラメータ, ProCAST, シミュレーション, シックスシグマ品質
2. 抄録:
高圧ダイカストにおける最適なパラメータ設定を予測するために、数値シミュレーションアプローチが提案されています。最適なパラメータの中でも、温度は他のパラメータよりも鋳造品質により大きな影響を与えることが示されました。本研究の成果は、ダイカストにおける不適切なプロセスパラメータ設定によって発生する鋳造欠陥の解決策を見つける上で有益でした。したがって、数値最適化技術と鋳造シミュレーションの組み合わせは、ダイカスト産業における鋳造製品の品質を向上させるためのツールとして役立ちます。本論文は、欠陥の原因となる射出圧力、溶湯温度、保持時間、プランジャー速度などの重要なパラメータを解析し、最適化することを目的としています。本研究論文では、有限要素解析技術を使用するProCASTシミュレーションソフトウェアを用いて、最適な圧力、温度、保持時間、プランジャー速度のパラメータを提供するための取り組みが行われました。溶湯温度、射出圧力、保持時間、プランジャー速度を変化させてパラメータを最適化する数値解析は、ホットスポットにおける凝固時間に関して、シミュレーションモデルにおける欠陥解析を研究するための重要なパラメータです。
3. 緒言:
ダイカストプロセスは、プロセスパラメータの関与により、しばしば品質や生産性の低下に悩まされます。MohantyとJena (2014) によれば、ゼロ欠陥部品を達成するためにはプロセスパラメータを制御する必要があります。ダイカストプロセスにおける不良率は11~13%であることが判明しました。この不良の原因は、ブローホール、不十分な射出圧力、不適切な充填時間、気孔(ポロシティ)、ホットスポットです。プロセスパラメータを制御するためには、プロセスパラメータが鋳造に与える影響とその欠陥への影響を知る必要があります。本研究では、図1に示すように、ダイカストローター部品と、溶湯がゲーティングシステムに入る箇所と底部断面の2つの断面について調査します。
4. 研究概要:
研究テーマの背景:
高圧ダイカスト(HPDC)プロセスは、プロセスパラメータのばらつきにより、品質問題や生産性の低さに影響を受けやすいです。これらのばらつきは、ブローホール、気孔、不適切な充填、ホットスポットなどの鋳造欠陥を引き起こし、著しい不良率(11-13%)をもたらす可能性があります。
従来の研究状況:
MohantyとJena(2014)などの従来の研究では、ゼロ欠陥部品を達成するためのプロセスパラメータ制御の必要性が強調され、業界の高い不良率が指摘されています。不良の主な原因として、不適切なパラメータ設定に直接関連する欠陥が特定されています。
研究目的:
本研究は、数値シミュレーションアプローチを用いて、重要なHPDCパラメータ、具体的には射出圧力、溶湯温度、保持時間、プランジャー速度を解析し、最適化することを目的としています。目標は、凝固時間を最小化し、それによって鋳造欠陥を削減し、製品品質をシックスシグマレベルに向上させる最適なパラメータ設定を決定することです。
中核研究:
本研究の中核は、有限要素解析(FEA)を用いるProCASTシミュレーションソフトウェアを使用して、ローター部品のHPDCプロセスをモデル化することです。体系的な数値最適化技術が適用され、定義された範囲内で4つの主要パラメータ(温度、圧力、速度、保持時間)が変化させられました(表2)。本研究では、これらの変化がローターおよび特定の断面(CS AAおよびCS BB、図1)のホットスポットにおける凝固時間に与える影響を分析します。目的は、欠陥解析と品質改善に不可欠と考えられる最小凝固時間を生み出すパラメータの組み合わせを特定することです。
5. 研究方法論
研究デザイン:
本研究では、数値シミュレーションと最適化の方法論を採用しています。ローター部品のHPDCプロセスは、有限要素法(FEM)に基づくProCASTソフトウェアを使用してシミュレーションされました。多段階最適化アプローチ(図5、図6)が用いられ、4つの主要パラメータ(温度、圧力、速度、保持時間)のそれぞれが、定義された範囲内の25レベルにわたって順次解析され(表2、図4)、凝固時間を最小化しました。
データ収集・分析方法:
- モデリング: ローター鋳造品、ゲーティングシステム、金型の3D幾何モデルがUnigraphics NX4.0を使用して作成され、*.x_tファイルに変換されました。
- メッシング: 有限要素メッシュはProCASTのMeshCASTモジュールを使用して生成されました(図7)。
- シミュレーション: ProCASTソフトウェアを使用してHPDCプロセスをシミュレーションしました。初期境界条件とプロセスパラメータ(表2)はプリプロセッサで定義されました。合計7800回のシミュレーション実験が計画されました(図4)。
- 分析: シミュレーション結果(例:凝固時間、固相率、引け巣、ホットスポット、充填時温度、ガスによる湯回り不良感度、射出圧力)は、Visual-Viewer(Cast)ポストプロセッサを使用して分析されました。主要な分析は、各最適化段階でローター部品と断面AA、BBの凝固時間を最小化することに焦点を当てました(図8-15)。最適パラメータはこれらの結果に基づいて決定されました(表3-10)。Crompton Greaves Ltd(CGL)からの産業データは、ヒートサイクル(図2、表1)と実験設定(図3)の文脈を提供しました。
研究テーマと範囲:
本研究は、アルミニウム合金ローター部品(外径100 mm、内径25 mm、高さ135 mm)の高圧ダイカスト(HPDC)に焦点を当てています。範囲には、4つの重要なプロセスパラメータの数値シミュレーションと最適化が含まれます:
- 溶湯温度 (T): 680 °C ~ 752 °C
- 射出圧力 (P): 300 bar ~ 348 bar
- プランジャー速度 (V): 116.6 m/s ~ 121.4 m/s
- 保持時間 (HT): 52 s ~ 76 s
目的は、鋳造欠陥を削減し、シックスシグマ品質を達成するための手段として凝固時間を最小化することです。
6. 主要な結果:
主要な結果:
- ProCASTを用いた数値シミュレーションアプローチにより、HPDCローター部品の凝固時間を最小化するための最適なプロセスパラメータ設定が成功裏に特定されました。
- 温度は、研究された他のパラメータ(圧力、速度、保持時間)と比較して、鋳造品質により大きな影響を与えることがわかりました。
- 多段階最適化プロセスにより、以下の最適なパラメータ範囲が得られました(表11):
- 温度 (T): 728 ≤ T ≤ 731 °C
- 圧力 (P): 330 ≤ P ≤ 332 bar
- 速度 (V): 119.6 ≤ V ≤ 120 m/s
- 保持時間 (HT): 67 ≤ HT ≤ 69 s (注記: 表11では65 ≤ HT ≤ 69と記載されていますが、各段階の結果を示す表3, 6, 8, 10では最適時間がそれぞれ67, 69, 69, 68秒となっています。最終結論では67秒が言及されています。当該要約表との一貫性を保つため、表11の範囲を使用します。)
- 特定された平均最適設定は、T = 730 °C、P = 331 bar、V = 119.8 m/s、HT = 67 sでした。
- これらの最適パラメータを用いて実施された確認実験により、ローター起因のモーター不良率が4.35%から0.89%に減少したと報告されています(CGLデータ)。
- 最適設定を用いて実施されたProCASTシミュレーションでは、充填時間、総引け巣、湯回り不良感度に関して重大な欠陥は見られませんでした(図16)。
- Figure 3: Experimentation setup: vertical die casting machine of the capacity of 100 Tons (Industrial caseCGL)
- Figure 4: The proposed experimentation set up for solving flow for optimisation of parameters
- Figure 5: Block diagram showing four stages of numerical simulation for the optimisation of solidification time
- Figure 6: Flow diagram showing the final stage of a numerical simulation approach
- Figure 7: Meshed and position of cross-sections of the rotor component
- Figure 8: Graphical representation of temperature analysis of the rotor and at cross-sections AA and BB
- Figure 14: Graphical representation of holding time at various sections
- Figure 15: (a, b, and c) Simulation output for solidification time at rotor component, Cross-Section AA and BB.
図のリスト:
- Figure 1: 数値解析のためのダイカストローター部品とAA、BB断面
- Figure 2: 秒単位のタイムラインで表されるダイカスト熱プロセスサイクル(産業事例-CGL)
- Figure 3: 実験設定:100トン容量の縦型ダイカストマシン(産業事例-CGL)
- Figure 4: パラメータ最適化のための流れ解析を行う提案実験設定
- Figure 5: 凝固時間最適化のための数値シミュレーションの4段階を示すブロック図
- Figure 6: 数値シミュレーションアプローチの最終段階を示すフロー図
- Figure 7: ローター部品のメッシュ分割と断面位置
- Figure 8: ローターおよびAA、BB断面における温度解析のグラフ表示
- Figure 9: (a, b, c) ローター部品、断面AAおよびBBにおける凝固時間のシミュレーション出力
- Figure 10: 各種断面における圧力解析のグラフ表示
- Figure 11: (a, b, c). ローター部品、断面AAおよびBBにおける凝固時間のシミュレーション出力
- Figure 12: 各種断面におけるプランジャー速度解析のグラフ表示
- Figure 13: (a, b, c) ローター部品、断面AAおよびBBにおける凝固時間のシミュレーション出力
- Figure 14: 各種断面における保持時間解析のグラフ表示
- Figure 15: (a, b, c) ローター部品、断面AAおよびBBにおける凝固時間のシミュレーション出力
- Figure 16: (a, b, c,) 充填時間、総引け巣、湯回り不良感度に関するProCASTシミュレーション結果
7. 結論:
数値シミュレーションアルゴリズムは、凝固時間を最小化することにより、HPDCプロセスパラメータを効果的に最適化しました。凝固時間が短いほど、一般的にブローホールや気孔などの内部欠陥が減少します。本研究では、ダイカストパラメータの影響を研究するために7800回のシミュレーション実験を実施しました。特定された最適パラメータ(注入温度730 °C、圧力331 bar、プランジャー速度119.8 m/s、保持時間67 s)は、確認実験によって検証され、ローター欠陥によるモーター不良率の大幅な削減(4.35%から0.89%へ、CGLデータ)が示されました。これらの最適設定でのProCASTシミュレーションは、最小限の欠陥(充填時間、引け巣、湯回り不良)を確認しました。温度は鋳造品質に最も大きな影響を与えました。数値最適化技術と鋳造シミュレーションの組み合わせは、ダイカスト産業における鋳造製品の品質を向上させるための貴重なツールとして機能し、シックスシグマ品質に向けた最適パラメータ設定のための意思決定ツールを提供します。
8. 参考文献:
- [1] Domkin, K., Hattel, J., & Thorborg, J. (2009). Modelling of high temperature and diffusion controlled die soldering in high aluminium pressure die casting. Journal of Material Processing Technology, 209(8), 4051-4061.
- [2] Fiorese, E., Richiedei, D., & Bonollo, F. (2016). Improving the quality of die castings through optimal plunger motion planning: analytical computation and experimental validation. International Journal of Advanced Manufacturing Technology, 88, 1475–1484.
- [3] Fu, J. & Wang, K. (2014) Modelling and simulation of the die casting process for A356 semi-solid alloy. Procedia Engineering, 81, 1565–1570.
- [4] Jorstad, J. & Apelian, D. (2009). Pressure assisted processes for high integrity aluminium castings - part 1. International Journal of Metal Casting, 250-254.
- [5] Kumar, S., Gupta, A., & Chandna, P. (2012). Optimisation of process parameters of pressure die casting using taguchi methodology. World Academy of Science, Engineering and Technology, 6, 590-594.
- [6] Lattanzi, L., Fabrizi, A., Fortini, A., Merlin, M., & Timelli, G. (2017). Effects of microstructure and casting defects on the fatigue behaviour of the high-pressure die-cast AlSi9Cu3 (Fe) alloy. Procedia Structural Integrity, 7, 505-512.
- [7] Mohanty, C. & Jena, B. (2014). Optimisation of aluminium die casting process using artificial neural network. International Journal of Emerging Technology and Advanced Engineering, 4(7), 146-149.
- [8] Syrcos, G. (2002). Die casting process optimisation using taguchi methods. Journal of Material Processing Technology, 135, 68-74.
- [9] Wang, L., Turnley, P., & Savage, G. (2011) Gas content in high pressure die castings. Journal of Materials Processing Technology, 211, 1510–1515.
- [10] Zhang, M., Xing, S., Xiao, L., Bao, P., Liu, W., & Xin, Q. (2008). Design of process parameters for direct squeeze casting. Journal of University of Science and Technology, 15(3), 339-343.
- [11] Zhang, X., Xiong, S., & Xu, Q. (2006). Numerical methods to improve the computational efficiency of solidification simulation for the investment casting process. Journal of Materials Processing Technology, 173, 70-74.
9. 著作権:
- 本資料は、「Suraj R. Marathe and Dr. Carmo E. Quadros」による論文です。「Analysis and Optimisation of High Pressure Die Casting Parameters to Achieve Six Sigma Quality Product Using Numerical Simulation Approach」に基づいています。
- 論文の出典: https://doi.org/10.31033/ijemr.11.1.15
本資料は上記の論文に基づいて要約されており、商業目的での無断使用は禁じられています。
Copyright © 2025 CASTMAN. All rights reserved.