本ページは、2022年にDefect and Diffusion Forumに掲載された研究論文「成形およびダイカスト金属部品のインターロックのための構造化された冷間圧延における表面形状の最適化(Optimization of the Surface Geometry in Structured Cold Rolling for Interlocking of Formed and Die-Cast Metal Components)」を要約したものです。
1. 概要:
- タイトル: 成形およびダイカスト金属部品のインターロックのための構造化された冷間圧延における表面形状の最適化
- 著者: アーロン・リンゲル(Aron Ringel)およびヨハネス・ローマー(Johannes Lohmar)
- 発行年: 2022年
- 発行ジャーナル/学会: Defect and Diffusion Forum
- キーワード: インターロック(interlocking)、マルチマテリアル部品(multi-material components)、構造化された冷間圧延(structured cold rolling)、FEモデリング(FE-modelling)
2. 研究背景:
- 研究テーマの社会的/学術的背景:
近年の軽量設計は、特に自動車産業においてますます重要になっています。マルチマテリアル部品は、性能と安全性を維持しながら重量を削減するための重要な戦略です。鋼鉄とアルミニウムのような材料を組み合わせることは利点がありますが、潜在的な化学反応により接合が困難であり、これは典型的な溶融溶接が機械的性質の低い金属間化合物形成のために適していない原因となっています。液体金属を固体金属に接合するハイブリッド(または複合)鋳造は、実行可能な解決策として浮上しています。板金の場合、多パス圧延によってアンダーカットのある表面構造を作成することが、インターロックジョイントを形成するのに効果的であることが証明されています。しかし、これらのアンダーカットでジョイント強度を最大化する最適な表面構造は、依然として未解決の問題です。 - 既存研究の限界:
多パス圧延で生成されたアンダーカットのある表面構造がインターロックジョイントに使用されていますが、「ジョイントを支持するこれらのアンダーカットに対する最適な表面構造は依然として不明です。」既存の研究ではまた、「内部ノッチは亀裂の開始に弱く、その後部品の破損につながる可能性がある」と指摘しています。 - 研究の必要性:
これらの限界に対処するために、本研究は「アンダーカットと内部ノッチの形成メカニズムを理解し、内部ノッチの形成を避けながらアンダーカットを最大化する最適点を導き出す」ことが必要です。この理解は、「表面構造形状と達成可能な部品強度との関係についての健全な理解を確立する」上で非常に重要です。
3. 研究目的および研究課題:
- 研究目的:
主な研究目的は、「チャネル深さ、アンダーカット、および内部ノッチに関する表面構造を分析し、最終的にジョイント強度を最大化する」ことです。追加の目標は、「アンダーカットと内部ノッチの形成メカニズムを理解し、内部ノッチの形成を避けながらアンダーカットを最大化する最適点を導き出す」ことです。 - 主な研究課題:
本研究は、構造化された冷間圧延における表面形状の最適化という課題を解決しようとしています。特に、以下を決定することを目的としています。- 内部ノッチの形成を防ぎながらアンダーカット幅を最大化する表面形状は何か?
- 内部ノッチなしでアンダーカット幅が広い表面構造を生成する最適なプロセス条件は何か?
- 研究仮説:
本研究は、「ジョイント強度はアンダーカット形状によって決定的に決定される」という仮説の下に進められます。また、「材料変位によって形成されたアンダーカットは、平坦圧延パスにおける高さ減少とともに増加」するが、「一定量の材料変位後、チャネル側面エッジがチャネル底部の上に折り畳まれ、内部ノッチを形成し始める」という観察に基づいています。
4. 研究方法論:
- 研究デザイン:
本研究では、「実験と数値研究を組み合わせた」方法を使用しています。このアプローチは、表面構造を分析するために「実験と数値研究を配置」することを統合します。 - データ収集方法:
実験データは、「Dreistern GmbH & Co. KG社のロール成形機P3.160」を使用して収集されました。さまざまな表面構造を持つ鋼鉄サンプルは、「ウォータージェットで断面準備のために切断」されました。内部ノッチは「3%ナイタールエッチングを使用して可視化」されました。結果の構造は、「Keyence VHX-1000Dデジタル顕微鏡」を使用して測定されました。 - 分析方法:
数値解析は、Abaqusソフトウェアを使用して「2D明示的FEモデル」シミュレーションを通じて実行されました。「アンダーカット幅および内部ノッチ長に関する結果評価は、Pythonスクリプトを介して自動化」されました。実験結果は、表面構造を測定し、これらをプロセス変数と相関させて分析しました。 - 研究対象および範囲:
本研究は、「DC04タイプの2.0mm厚鋼板」に焦点を当てました。表面は「最大0.5mm深さのチャネルで構造化され、その後さまざまな高さ減少で平坦化」されました。実験には、幅160mm、長さ245mmの鋼板が使用されました。シミュレーションは、「チャネルとリブの半分の高さと幅をカバーする」2D平面ひずみモデルに単純化されました。
5. 主な研究結果:
- 主な研究結果:
この研究では、表面形状の最適化に関するシミュレーションと実験の両方の結果が得られました。- シミュレーション結果: 「2D 明示的 FE モデルからの結果は、内側のノッチなしでアンダーカット幅の大きいこれらの表面構造のプロセス最適値が、14% の高さ減少で存在することを示唆しています。」
- 実験結果: 「しかし、実験では、内側のノッチは、与えられた実験設定で約 20 µm 幅のアンダーカットで、約 8% の高さ減少で形成され始めました。対照的に、最大約 50 µm のアンダーカットは、26% の高さ減少で形成されますが、約 60 µm の長さの内側のノッチも引き起こします。」
- 実験では「ノッチフリーのアンダーカットは約 25 µm 幅のみ」です。
- 統計的/定性的分析結果:
- 図 3: 「ɛh,1 = 12.08% および ɛh,2 = 28.18% の 2D 平面ひずみシミュレーションの例」は、プロセス中の材料の流れと応力分布を示しており、チャンネルの形成と潜在的な内側のノッチを示しています。特定のひずみ値に対して、「0.498 mm」のチャンネル深さ、「0.142 mm」のアンダーカット幅、「0.358 mm」の内側のノッチ長を示しています。
- 図 4: 「アンダーカットと内側のノッチを備えたチャンネルの断面、(ɛh,₁ = 18% および ɛh,2 = 33%)」は、実験サンプルの顕微鏡画像を示しており、「アンダーカット幅」と「内側のノッチ長」を可視化しています。スケールバーは「50.00 μm」を示しています。
- 図 5: 「シミュレーションと実験の幾何学的パラメータ」は、「チャンネル圧延(1st)」と「平坦化(2nd)」のシミュレーション結果と実験結果をグラフで比較しています。「チャンネル深さ [mm]」、「アンダーカット幅 [mm]」、および「内側のノッチ長 [mm]」を、「高さ減少 [%]、式 (1)」および「高さ減少 [%]、式 (2)」に対してそれぞれプロットしています。シミュレーションでは、アンダーカットが約 7% の高さ減少で始まり、14% の高さ減少で最大約 60 µm に達することが予測されています。実験では、最大アンダーカット幅が約 50 µm で、約 26% の高さ減少で発生し、内側のノッチは約 8% の高さ減少で現れます。
- データ解釈:
シミュレーション結果は、内側のノッチなしでアンダーカット幅を最大化するための最適な高さ減少が 14% であることを示しています。しかし、実験結果は、内側のノッチがより早く現れ、最大アンダーカット幅がより高い高さ減少 (26%) で達成されるが、内側のノッチを伴うことを示しています。「チャンネル圧延パスの場合、平面ひずみシミュレーションは、実験結果と比較してチャンネル深さを過大評価しています。」この食い違いは、実験で観察された「チャンネル圧延中の長手方向の材料の流れが、サンプルの変形していない側によって完全に抑制されていない」ことに起因しており、これは 2D 平面ひずみシミュレーションでは制約されています。「平面ひずみ制限のため、シミュレーションラインの傾きは、高さ減少のパーセントあたり約 0.04 mm です。長手方向の材料の流れのため、実験的な傾きはわずか 65% です。」 - 図のリスト:
- 図 1: プロセススキーム (Senge et al. [12] による提案)
- 図 2: 2D シミュレーションのアセンブリ
- 図 3: ɛh,1 = 12.08% および ɛh,2 = 28.18% の 2D 平面ひずみシミュレーションの例
- 図 4: アンダーカットと内側のノッチを備えたチャンネルの断面、(ɛh,₁ = 18% および ɛh,2 = 33%)
- 図 5: シミュレーションと実験の幾何学的パラメータ
- 図 6: DC04 のフローカーブ
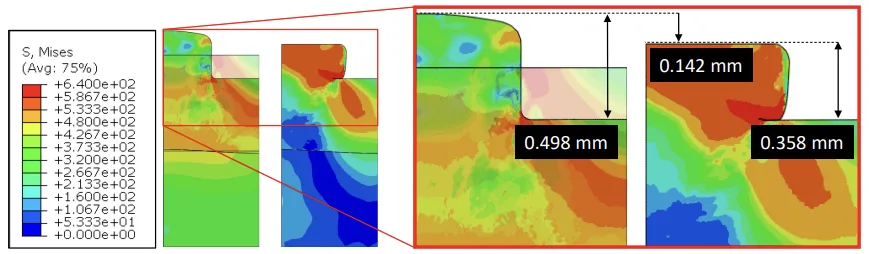
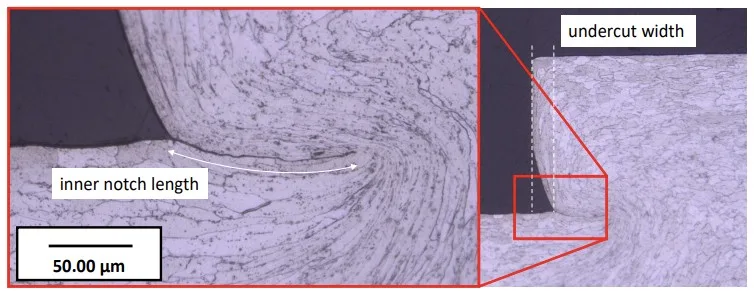
6. 結論と考察:
- 主な結果の要約:
「本研究では、ノッチフリーのアンダーカットのための DC04 シートの表面構造形状を最大化するために、シミュレーションと実験を実施しました。」シミュレーションは、ノッチフリーのアンダーカットのために「2 mm DC04 および選択されたローラー形状に対して、約 14% の高さ減少で最適な点」を示唆しています。実験では、26% の高さ減少で「最大 50 µm 幅までのアンダーカット」を達成しましたが、これらは「約 60 µm の内側のノッチ付き」でした。実験設定では「ノッチフリーのアンダーカットは約 25 µm 幅のみ」であり、内側のノッチが回避された低い高さ減少で発生しました。「この挙動は、現在のところシミュレーションでは再現されていません。」 - 研究の学術的意義:
この研究は、構造化冷間圧延における「アンダーカットと内側のノッチの形成メカニズム」の理解に貢献しています。材料の流れの複雑さと、これらのプロセスで 2D シミュレーションを使用して表面形状を正確に予測することの課題を強調しています。 - 実用的な意義:
この知見は、特に自動車産業における「マルチマテリアル部品のインターロックジョイント」のためのシートメタルの表面形状を最適化するための貴重な洞察を提供します。この研究は、内側のノッチなしで最大のアンダーカット幅を達成するには、冷間圧延プロセスにおける高さ減少の慎重な制御が必要であることを示唆しています。 - 研究の限界:
「精度を向上させ、有効性を維持する 1 つの方法は、2D 平面ひずみモデルに運動学的境界条件を追加することです。」「2D 平面ひずみモデルには、特に実験で観察された長手方向の流れなど、材料の流れを完全に捉える上で限界があります。」「シミュレーションは、内側のノッチ形成に関する実験結果を完全に再現していません。」
7. 今後のフォローアップ研究:
- フォローアップ研究の方向性:
著者は、知見の精度と適用性を向上させるために、今後の研究のいくつかの方向性を示唆しています。- 「精度を向上させ、有効性を維持する 1 つの方法は、2D 平面ひずみモデルに運動学的境界条件を追加することです。」
- 「あるいは、側面の変形していないシートを含む計算コストの高い 3D モデルは、運動学的および応力状態を正確に記述し、摩擦効果の調査を可能にするでしょう。」
- 「高精度のためには、使用されるフローカーブ外挿も重要な役割を果たすようです。」
- 「さらに、チャンネル圧延パスにおけるローラー形状の影響を調査する必要があります。構造化ローラーのリブエッジでより大きなフィレット半径を使用すると、平坦化パスにおける内側のノッチの形成を遅らせる可能性があるためです。」
- 「さらに、アンダーカット幅は、チャンネル圧延パスでより広いリブで増加する可能性があります。」
- さらなる探求が必要な分野:
さらなる探求が必要な分野は次のとおりです。- 「ローラー形状の影響」
- 「摩擦効果」
- 「より良い精度のための 3D モデリング」
- 「今後の研究では、シミュレーションの精度を実用的な観点から評価するために、圧延/ダイカスト複合部品を使用して、この構造形状がジョイント強度に与える影響をテストする必要があります。」
8. 参考文献:
- [1] H.E. Friedrich, Leichtbau in der Fahrzeugtechnik, Springer Fachmedien, Wiesbaden, 2017.
- [2] B. Klein, T. Gänsicke, Leichtbau-Konstruktion, Springer Fachmedien, Wiesbaden, 2019.
- [3] W. Cai, G. Daehn, A. Vivek, J. Li, H. Khan, R.S. Mishra, M. Komarasamy, A State-of-the-Art Review on Solid-State Metal Joining, J. Manuf. Sci. Eng. 141 (3) (2019).
- [4] M. Rübner, M. Günzl, C. Körner, R.F. Singer, Aluminium-aluminium compound fabrication by high pressure die casting, Mater. Sci. Eng. A 528 (22-23), (2011) 7024–7029.
- [5] A. Bührig-Polaczek, T. Röth, E. Baumeister, N. Nowack, T. Süßmann, Hybride Leichtbaustrukturen in Stahlblech-Leichtmetall Verbundguss, FH Aachen (2006).
- [6] S. Senge, J. Brachmann, G. Hirt, A. Bührig-Polaczek, Evaluation of interlocking bond strength between structured 1.0338 steel sheets and high pressure die cast AlMg5Si2, in ESAFORM, (2018) p. 40019.
- [7] X. Fang, Evaluation of Coating Systems for Steel Aluminum Hybrid Casting; Mater. Sci. Eng. A 7 (2) (2017).
- [8] S. Ucsnik, R. Gradinger, A. Becirovic, A. Waldhör, Enhanced Performance of Steel-Aluminium Cast Nodes through Cold Metal, Transfer. Mater. Sci. Forum 765, (2013) 736–740.
- [9] N. Pasligh, Hybride formschlüssige Strukturverbindungen in Leichtbaustrukturen aus Stahlblech und Aluminiumdruckguss, Dissertation, Gießerei-Institut, Aachen (2011).
- [10]D. Joop, S. Heupel, C. Schnatterer, D. Zander, A. Bührig-Polaczek, Evaluation of Corrosion Mechanisms of Hybrid Light Metal Structures by High Pressure Die Casting, Mater. Sci. Forum 825-826, (2015) 441-448.
- [11]J. Jakumeit, H. Behnken, R. Laqua, J. Eiken, J. Brachmann, Multi-scale simulation of hybrid light metal structures produced by high pressure die casting; IOP Conf. Ser.: Mater. Sci. Eng. 861, (2020) p. 12035.
- [12] S. Senge, J. Brachmann, G. Hirt, A. Bührig-Polaczek, Interlocking Multi-Material Components made of Structured Steel Sheets and High-Pressure Die Cast Aluminium, in ESAFORM, (2017) p. 190007.
- [13]S. Senge, Walztechnische Herstellung von Oberflächenstrukturen für formschlüssige Verbindungen, Dissertation, Verlagshaus Mainz GmbH, Aachen (2020).
- [14] Y. Iino, Local Fatigue Damage Accumulation around Notch Attending Crack Initiation, Metall. Mater. Trans. A (26A), (1995) p. 1419.
- [15] A. Tieu, Y. Liu, Friction variation in the cold-rolling process, Tribol. Int. 37 (2), (2004) p. 177.
- [16] T. Clausmeyer, A. Schowtjak, S. Wang, R. Gitschel, O. Hering, P. Pavliuchenko, J. Lohmar, R. Ostwald, G. Hirt, A.E. Tekkaya, Prediction of Ductile Damage in the Process Chain of Caliber Rolling and Forward Rod Extrusion, Procedia Manuf. 47 (1), (2020) p. 649–655.
9. 著作権:
- この資料は、アーロン・リンゲル (Aron Ringel) および ヨハネス・ローマー (Johannes Lohmar) の論文:「表面形状最適化構造化冷間圧延による成形・ダイカスト金属部品のインターロック (Optimization of the Surface Geometry in Structured Cold Rolling for Interlocking of Formed and Die-Cast Metal Components)」に基づいています。
- 論文ソース: doi:10.4028/p-z54p05
この資料は上記の論文に基づいて要約されたものであり、商業目的での無断使用は禁止されています。
著作権 © 2025 CASTMAN. 無断複写・転載を禁じます。