This paper introduction was written based on the 'High Pressure Die Casting of Aluminium and Magnesium Alloys - Grain Structure and Segregation Characteristics' published by 'Norwegian University of Science and Technology (NTNU)'.
1. 概要:
- タイトル: High Pressure Die Casting of Aluminium and Magnesium Alloys - Grain Structure and Segregation Characteristics
- 著者: Hans Ivar Laukli
- 出版年: 2004年
- 出版ジャーナル/学会: Norwegian University of Science and Technology (NTNU) への学位論文
- キーワード: (論文中にキーワードの明示的な記載はありませんが、内容から推測されるキーワードは以下です) High Pressure Die Casting (HPDC), Aluminium Alloys, Magnesium Alloys, Grain Structure, Segregation, Solidification, Microstructure
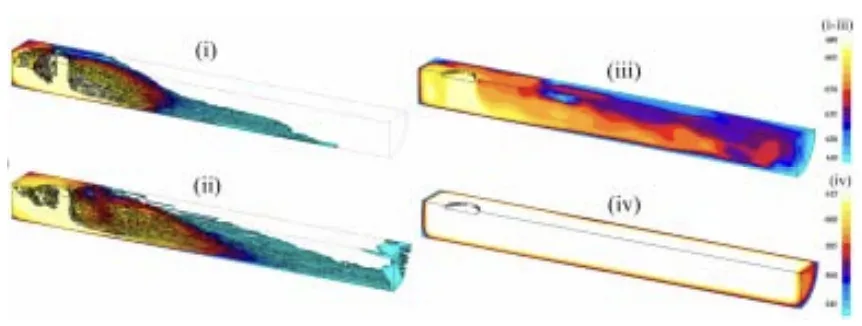
2. 抄録または序論
コールドチャンバー高圧ダイカスト(HPDC)は、複雑なニアネットシェイプのアルミニウムおよびマグネシウム合金鋳物の製造における重要な商業プロセスです。本論文で提示された研究は、このタイプの鋳造における微細構造形成の調査を目的としています。プロセスと合金に関連する凝固特性は、結晶粒と欠陥の形成を制御します。これは、鋳物の機械的特性に大きな影響を与えます。
調査は主にAM60マグネシウム合金とA356アルミニウム合金を使用して実施されました。コールドチャンバーHPDC法と重力ダイカスト法の2つの異なる鋳造方法が使用され、異なる流れと凝固条件を可能にしました。鋳物中の微細構造は、光学顕微鏡、画像解析、走査型電子顕微鏡、電子後方散乱回折測定、および電子プローブマイクロアナリシスを使用して調査されました。
HPDC実験では、ショットスリーブの凝固条件は、主に注湯時の溶融金属の過熱度を変化させることによって調査されました。これは、鋳物中の微細構造に大きな影響を与えました。外部凝固結晶(ESC)の割合は、AM60とA356ダイカストの両方で、ゲート付近で一貫して最大であることがわかりました。これは、固有のショットスリーブ凝固条件とプランジャーの動きによって設定された流れに起因すると考えられます。過熱度を上げると、鋳物中のESCの割合が減少しました。さらに、高い過熱度は、AM60とA356鋳物の両方で、樹枝状/伸長した幹の形態を持つESCを与え、低い過熱度は、より粗く、より球状のESCを生成しました。ESCは通常、ダイカストのゲートから遠く離れた断面の中央領域に向かって偏析しました。
AM60ダイカストの製造において、ショットスリーブ壁に薄い断熱コーティング層を適用すると、鋳物中のすべてのESCがほぼ除去されました。A356合金(およびショットスリーブコーティングなし)を使用した場合、(Tiを固溶させない状態で)ESCの割合が大幅に減少しましたが、AlTi5B1結晶粒微細化剤の添加は、ESCの割合の増加と鋳物中の結晶粒径の大幅な微細化を誘導しました。AlTi5B1結晶粒微細化剤をA356合金に添加すると、球状ESCの形成が促進されました。
制御された実験室レベルの重力ダイカスト実験では、典型的なHPDC微細構造が、半凝固金属を鋼製ダイに注湯することによって作成されました。ESCは、最大充填(ESCの割合〜35〜40%)に達するまで、流れの間に中央領域に偏析/移動することがわかりました。偏析の程度は、ESCの割合によって決定され、ダイ温度はESCの位置に影響を与えます。ESCの偏析は、揚力の結果として流れの間に発生すると説明されました。
縞状欠陥の形成も研究されました。縞の位置は、ダイ温度とESCの割合によって影響を受けました。縞の性質とその発生に基づいて、欠陥縞の形成に関する新しい理論が提案されました。流れの間、ダイ壁からの固体の分布は、3つの領域で構成されています。1)壁面の固体分率勾配。2)運搬する低固体分率領域(3)ESCのネットワーク。変形速度が樹枝状晶間の流速を超える臨界固体分率が存在します。誘導応力がネットワーク強度を超えると、変形は滑りによって発生し、その後に液体の流れが続きます。液体の流れは、凝固収縮、内部ESCネットワーク上の静水圧、および液体を引き込むギャップの形成によって引き起こされます。
3. 研究背景:
研究トピックの背景:
輸送産業、特に自動車産業は、堅牢な部品の開発において軽量材料を求めることを義務付けられています。したがって、アルミニウムおよびマグネシウム合金の世界的な生産量が増加しており、アルミニウムの消費量は、既存の一次金属の生産能力を同時に上回っています。したがって、リサイクルおよび燃料消費規制の要件を満たす統合機能を備えた軽量製品を提供できる、経済的に持続可能なプロセスを開発または発明する必要があります。高圧ダイカスト(HPDC)は、これらの要求に非常に適した方法です。
HPDCは、複雑で薄肉のニアネットシェイプ鋳物の製造のための、全自動、大容量、高生産性のプロセスであり、部品重量は数グラムから15kg以上まで及びます。従来はハウジングなどの製造に利用されてきましたが、これは変化しました。現在、実現可能な製品は、マグネシウム合金の自動車用フロントエンド構造およびインストルメントパネル、アルミニウム合金のBピラーです。しかし、HPDCが拡張された自動車用途で競争力を持ち、新しい市場セグメントにとって魅力的であるためには、耐衝撃性と疲労特性を改善し、プロセスと金属挙動の科学的な理解が必要です。
既存研究の状況:
HPDCプロセスにおける金属挙動に関する研究は、多くの研究者によって行われてきました。数値モデリングと実験的研究は一般的に類似した構成的な金属挙動を明らかにしています。ショットスリーブ充填シミュレーションと主要な流れの特性は、図6 [32, 33]に示されており、主な流れの特性は次のとおりです。1)金属はプランジャー付近のショットスリーブ底部に衝突します。2)ショットスリーブの端まで流れ、次に後方に流れます。3)サージ波が注湯口に向かって後退します。4)さらに、金属はプランジャーに継続的に洗い流され、部分的にそこに蓄積します(図6aの上部にある速度スケールバーに注意してください)。サージ波は、金属の流れがフルード数[35]、Fr = v /(gh)1/2によって特徴付けられる油圧ジャンプ[34]に似ています。金属が充填中にどこに配置されるかを考慮することが重要です。図6b [33]に示すように、緑色の粒子は初期に溶融金属に浸漬され、主にダイ付近に配置されます。より「古い」赤色と黄色の粒子はプランジャー付近に残ります。
研究の必要性:
HPDC製品の機械的特性は、鍛造製品と比較して、一貫性がないという評判があります。これは、通常、プロセスパラメータの変動に起因すると考えられていますが、そのような文書化はしばしば不十分です。プロジェクトの開始時に、Norsk Hydroは最先端の設備を備えたHPDCマシンを設置しました。したがって、HPDCプロセスと異なるパラメータが異なる製品や合金に及ぼす影響について、より体系的な調査が可能になりました。プロジェクト委員会では、ショットスリーブ条件に関する博士課程の研究を開始し、ダイに供給された金属によって引き起こされる鋳物中の微細構造への影響を分析することが決定されました。
4. 研究目的と研究課題:
研究目的:
本論文で提示された研究は、このタイプの鋳造における微細構造形成の調査を目的としています。プロセスと合金に関連する凝固特性は、結晶粒と欠陥の形成を制御します。これは、鋳物の機械的特性に大きな影響を与えます。
主要研究:
- ショットスリーブの凝固条件が微細構造に及ぼす影響
- 溶融金属の過熱度が微細構造に及ぼす影響
- 結晶粒微細化剤の添加が微細構造に及ぼす影響
- ESCの偏析と移動のメカニズム
- 縞状欠陥の形成メカニズム
研究仮説:
- ショットスリーブ内の凝固条件は、鋳物中のESCの分布と形態に大きな影響を与える。
- 溶融金属の過熱度を変化させることで、ESCの割合と形態を制御できる。
- 結晶粒微細化剤の添加は、ESCの形成と結晶粒径に影響を与える。
- ESCの偏析と移動は、揚力と流動条件によって制御される。
- 縞状欠陥の形成は、固体分率勾配と流動条件によって説明できる。
5. 研究方法
研究デザイン:
実験的研究
データ収集方法:
- HPDC実験
- 重力ダイカスト実験
- 光学顕微鏡観察
- 画像解析
- 走査型電子顕微鏡観察
- 電子後方散乱回折測定
- 電子プローブマイクロアナリシス
分析方法:
- 定性的な微細構造観察
- 定量的な画像解析によるESCの割合と分布の評価
- EPMAによる組成分析
- EBSDによる結晶方位解析
研究対象と範囲:
- 材料: AM60マグネシウム合金、A356アルミニウム合金
- 鋳造方法: コールドチャンバーHPDC、重力ダイカスト
- 実験パラメータ: 溶融金属の過熱度、ダイ温度、結晶粒微細化剤の添加、ショットスリーブコーティング
6. 主な研究成果:
主要研究成果:
- ESCの割合は、ゲート付近で最大であり、ゲートから離れるにつれて減少する。
- 過熱度が高いほど、ESCの割合は減少し、より樹枝状の形態になる。
- 過熱度が低いほど、ESCの割合は増加し、より球状の形態になる。
- ショットスリーブに断熱コーティングを施すと、ESCの形成が抑制される。
- AlTi5B1結晶粒微細化剤の添加は、球状ESCの形成を促進し、結晶粒径を微細化する。
- ESCは、流れの間に中央領域に偏析/移動する。
- 縞状欠陥は、固体分率勾配と流動条件によって形成される。
提示されたデータの分析:
図の名前リスト:
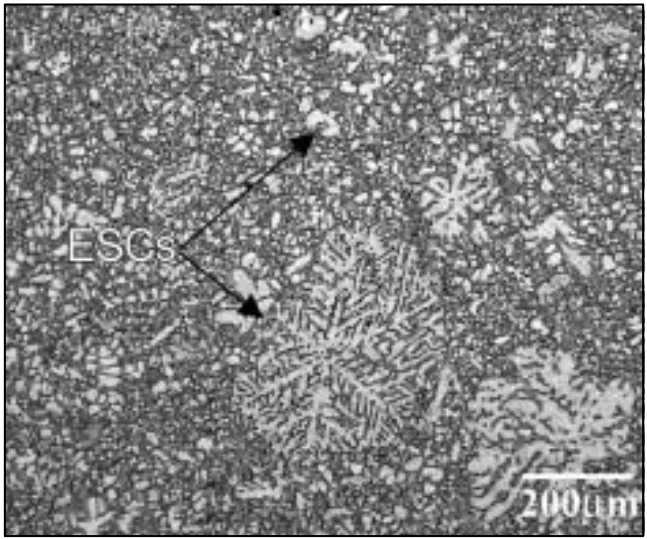
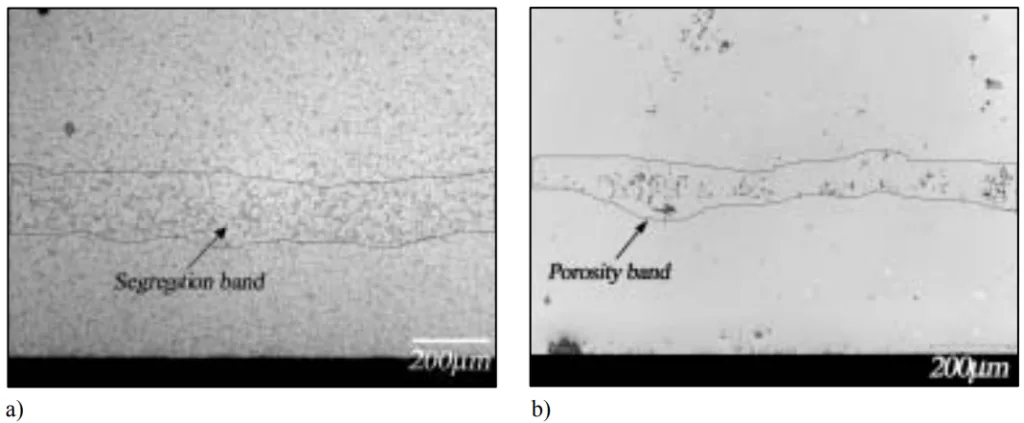
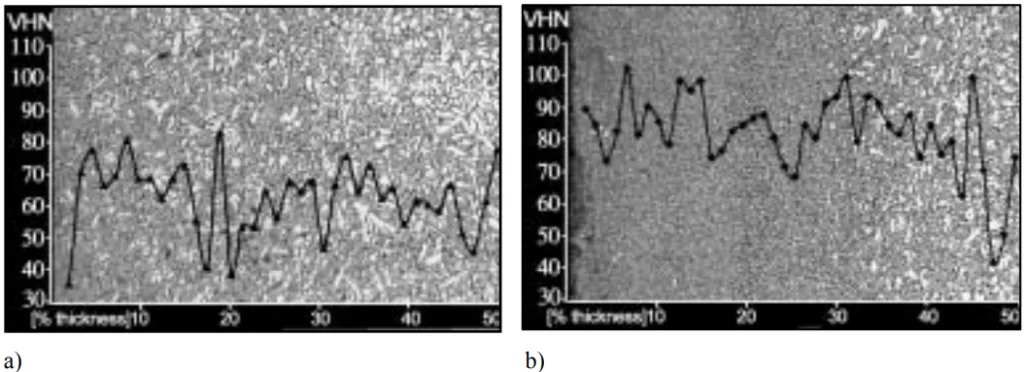
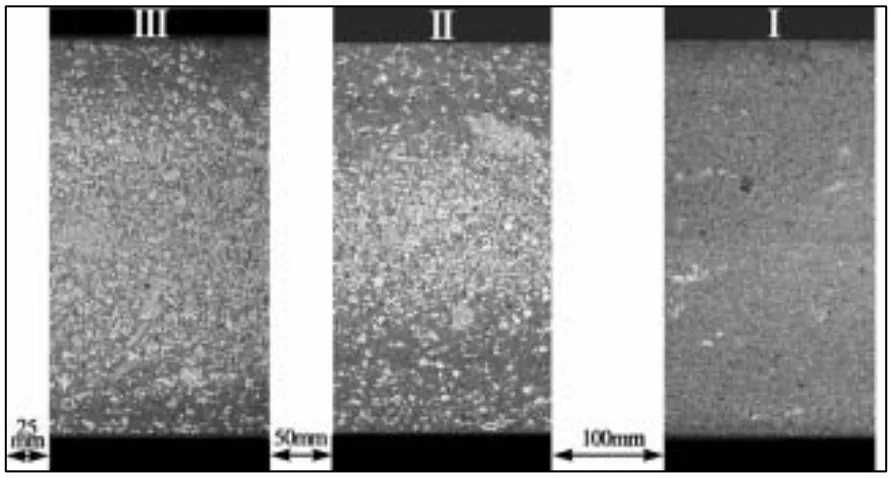
- Figure 1: Illustration of cold chamber high pressure die casting. Reproduced from [6, 7].
- Figure 2: Nucleation is feasible in the thermally undercooled region adjacent to the die wall when the melt undercooling, ΔTt, exceeds the required nucleation undercooling ΔTn.
- Figure 3: Illustration of the principles for constitutional undercooling [13] in constrained growth. Solute rejection at the crystal interface and simultaneous release of latent heat of fusion generates a constitutionally undercooled zone.
- Figure 4: The low-solute parts of the Al-Si, (black lines), and Mg-Al, (blue lines), binary phase diagrams. Liquidus-lines assumed linear. Thermosolutal transition temperatures indicated with Ttrans.
- Figure 5: Measurements of the shear strength of the material as a function of fraction solid, (fs), for the two extremes in crystal morphology; large dendritic crystals and small globular crystals [30].
- Figure 6: a) Simulation of the filling of an A380 aluminium alloy [32]. The scale bar indicates metal velocity; b) Simulation of particle position during filling. Reproduced with data from [33].
- Figure 7: Simulation of the melt temperature evolution in the shot sleeve, (longitudinal cross section), for an A356 aluminium alloy, (details in APPENDIX B). Total fs when injection starts is ~10%. The heat transfer coefficient was determined from experimental measurements.
- Figure 8: a) Cross sectional micrograph from the biscuit. Interfaces between solid surface layers and melt solidified later indicated with arrows; b) Magnification of the microstructure near the plunger. AM60B alloy.
- Figure 9: Cross sectional micrograph from an A380 aluminium alloy die casting [44] which shows large cold flakes embedded in the microstructure.
- Figure 10: Optical micrograph from an industrially produced HPDC AM60 instrument panel. Etched microstructure: The large white particles are ESCs, whilst the gray structure is the fine grained matrix.
- Figure 11: Shot profile from an AM60 magnesium alloy die casting. The diagram shows plunger stroke, velocity and pressure as a function of time. I): slow shot phase (1-7s); II) die filling phase (0.01-0.3s); III): pressurization phase (5-20s).
- Figure 12: Surge wave, with velocity vw, ahead of plunger tip, with velocity vp.
- Figure 13: Simulation of slow shot plunger movement and simultaneous metal flow and fraction solid distribution, indicated by the color scale bar [52]. The hottest melt, (blue colour), enters runner first.
- Figure 14: At approximately 70% plunger movement photographs of: a) The fragmented flow front; b) A location where the metal has frozen through the thickness during die filling, (marked with arrow). Principal die filling direction is vertical, parallel with acceleration of gravity.
- Figure 15: a) Segregation band in an A356 die casting; b) A porosity band in an AM60 die casting. Bands delineated with black lines and marked with arrows.
- Figure 16: Illustration of: a) The fraction solid profile; b) The corresponding strength profile; c) The resulting microstructure where the central region facilitates deformation by slip along the segregated shear plane [30].
- Figure 17: a) Segregation bands in an A356 aluminium alloy die casting. Few ESCs are present; b) Typical HPDC microstructure: The ESCs are located in the central region of the cross section. Flow direction to the right and parallel to the page.
- Figure 18: Measurements of microhardness (VHN), (10g indentation load), from the surface to the centre in half of the cross sections of thin walled, (2.5mm), AM60 magnesium alloy die castings: a) Large fraction of ESCs ~evenly distributed, with an average VHN 63; b) The ESCs are only located in the central region. Average VHN: 79.
- Figure 19: Cross sectional micrographs from tensile tested specimens taken from AM60 magnesium alloy die castings: a) Near the gate, typical elongation: 3-10%; b) Farther from the gate, typical elongation: 15-25%.
- Figure 20: Schematic illustration of the plunger movement and corresponding qualitative description of fraction solid distribution. Metal with increasing fs, (ESCs), corresponding to locations I-III, enters the runner with further plunger movement.
- Figure 21: The solidification and metal flow in the shot sleeve results in microstructures with different thermal histories in the casting. The microstructures correspondingly possess different fractions of ESCs. The locations marked III, II and I, correspond to position A, B and C, respectively, in the box shaped die castings in article #1-4. Thickness of the casting: 2.5mm.
- Figure 22: Schematic illustration of the packing of ESCs in the central region. At a specific fraction solid, further packing is restricted and the central region with ESCs becomes larger by an amount r(2r+r).
7. 結論:
主な調査結果の要約:
本研究では、アルミニウム合金およびマグネシウム合金の高圧ダイカストにおける結晶粒構造と偏析特性について詳細な調査を実施しました。主な調査結果は以下の通りです。
- ショットスリーブ内の凝固条件は、鋳物中のESCの分布と形態に大きな影響を与えます。ESCの割合は、ゲート付近で最大であり、ゲートから離れるにつれて減少します。
- 溶融金属の過熱度を変化させることで、ESCの割合と形態を制御できます。過熱度が高いほどESCの割合は減少し、より樹枝状の形態になり、過熱度が低いほどESCの割合は増加し、より球状の形態になります。
- ショットスリーブに断熱コーティングを施すことで、ESCの形成を抑制できます。
- AlTi5B1結晶粒微細化剤の添加は、球状ESCの形成を促進し、結晶粒径を微細化します。
- ESCは、流れの間に中央領域に偏析/移動します。
- 縞状欠陥は、固体分率勾配と流動条件によって形成されます。
研究の学術的意義:
本研究は、高圧ダイカストにおける微細構造形成メカニズムの理解を深める上で重要な貢献をしました。特に、ショットスリーブ内の凝固条件、溶融金属の過熱度、結晶粒微細化剤の添加がESCの形成と分布に及ぼす影響を明らかにしました。また、縞状欠陥の形成メカニズムに関する新しい理論を提案しました。
実際的な意味合い:
本研究の成果は、高圧ダイカストプロセスの最適化と鋳物の品質向上に役立つ可能性があります。ショットスリーブの凝固条件を制御することで、ESCの形成を抑制し、鋳物の機械的特性を改善できる可能性があります。また、結晶粒微細化剤の適切な使用は、結晶粒径の微細化とESCの形態制御に有効であることが示唆されました。
研究の限界と今後の研究分野:
本研究は、AM60マグネシウム合金とA356アルミニウム合金に焦点を当てていますが、他の合金における同様の現象を調査する必要があります。また、ESCの偏析と移動、縞状欠陥の形成メカニズムについては、さらなる詳細な研究が必要です。特に、流動条件、熱伝達、凝固挙動を考慮した数値シミュレーションによる検証が重要です。
8. 参考文献:
- [1] E.J. Vinarcik, High Integrity Die Casting Processes, John Wiley & Sons, Inc., 2003.
- [2] L.J.D. Sully, Metals Handbook, 15, 286-295.
- [3] M. M. Avedesian, H. Baker, Magnesium and Magnesium Alloys, ASM International, 1999.
- [4] A. Kaye, A. Street, Die Casting Metallurgy, Butterworth scientific, 1982.
- [5] N. Fantetti, O. Holta, J.B. R¯nhaug, D. Albright, NADCA Trans., 1997, 19, T97-054.
- [6] Melting and handling magnesium for die casting, Hydro Magnesium Data Sheet, 2002.
- [7] Introduction to Die Casting, NADCA, 1997.
- [8] A.D. Figueredo, Science and Technology of Semi-Solid Metal Processing, NADCA, 2001.
- [9] Die Casting - Process Optimization, B¸hler Druckguss, 2001.
- [10] L. B‰ckerud, C. Chai, J. Tamminen, Solidification Characteristics of Aluminium Alloys, AFS/Skanaluminium, 2, 1990.
- [11] W.G. Walkington, Die Casting Defects - Causes and Solutions, NADCA, 1997.
- [12] M.C. Flemings, Solidification Processing, McGraw-Hill, 1974.
- [13] W. Kurz, D.J. Fisher, Fundamentals of Solidification, Trans Tech Publications, 1998.
- [14] P.A. T¯ndel, PhD thesis, Norwegian Institute of Technology (Trondheim), 1994.
- [15] D.A. Porter, K.E. Easterling, Phase Transformations in Metals and Alloys, Chapman & Hall, 1997.
- [16] J. Campbell, Castings, Butterworth-Heinemann, 1997.
- [17] A. Ohno, Solidification - The Separation Theory and its Practical Applications, Springer Verlag, 1987.
- [18] B. Chalmers, J. Aust. Inst. of Metals, 1963, 8, 255-263.
- [19] R.T. Southin, Trans. AIME, 1966, 239, 220-225.
- [20] W.C. Winegard, B. Chalmers, Trans. ASM, 1954, 46, 1214-1224.
- [21] I. Maxwell, A. Hellawell, Acta Met., 1975, 23, 229-237.
- [22] K.A. Jackson, J.D. Hunt, D.R. Uhlmann, T.P. Seward, Trans. AIME, 1966, 236, 149-158.
- [23] E.F. Emley, Principles of Magnesium Technology, Pergamon Press Ltd., 1966.
- [24] A.W. Woods, J. Fluid Mech., 1992, 239, 429-448.
- [25] G. Hansen, A. Hellawell, S.Z. Lu, R.S. Steube, Met. Mat. Trans. A, 1996, 27A, 569-581.
- [26] Die Cast Magnesium Alloys, Hydro Magnesium Data Sheet, 2001.
- [27] J.R. Davis, Aluminum and Aluminum Alloys, ASM International, 1993.
- [28] A. Hellawell, 4th Int. Conf. on Semi-Solid Proc. Alloys Comp., 1996, 60-65.
- [29] Q. Han, A. Hellawell, Met. Mat. Trans. B, 1997, 28B, 169-173.
- [30] A.K. Dahle, D.H. StJohn, Acta Mat., 1998, 47, 31-41.
- [31] A.K. Dahle, L. Arnberg, J. of Met., 1996, 48, 34-37.
- [32] L. Wang, T. Nguyen, G. Savage, C.J. Davidson, Int. J. C.Met.R., 2003, 16, 409-417.
- [33] L. Wang, T. Nguyen, M. Murray, NADCA Trans., 2001, 21, T01-014.
- [34] H.T. Haaland, PhD thesis, Norwegian University of Science and Technology (Trondheim), 2000.
- [35] F.M. White, Fluidmechanics, McGraw-Hill, 1999.
- [36] S. Sannes, 2003. Personal communication.
- [37] H. Iwahori, M. Nakamura, K. Tozawa, Y. Yamamoto, NADCA Trans., 1985, 13, 1-9.
- [38] P. Paliani, L. Zalewski, J. Barreto, N. Tsumagari, J. Brevick, C. Mobley, NADCA Trans., 1995, 18, 149-155.
- [39] S. Sannes, Fill Tests - Simulations and Microstructures in U-profile Castings, Hydro Aluminium, Porsgrunn, 2003, 03P_BN2.doc.
- [40] P. Schmidt, PhD thesis, Royal Institute of Technology (Stockholm), 1994.
- [41] W. Sequeira, PhD thesis, The University of Queensland (Brisbane), 2000.
- [42] S. Sannes, H. Gjestland, H. Westengen, H.I. Laukli, Proc. Int. Conf. Mg. Alloys & Appl., 2003, 6, 725-731.
- [43] R. Chatfield, P.W. Rohan, ADCA Die Casting Conf., 2000, paper15; 11-15.
- [44] N. Tsumagari, T. Liang, J. Brevick, C. Mobley, NADCA Trans., 2001, 21, 251-256.
- [45] M. Gershenzon, P.W. Rohan, M.T. Murray, NADCA Trans., 1999, 20, 305-315.
- [46] T. Abbott, M. Easton, Mat. Forum, 2001, 25, 181-201.
- [47] D. StJohn, A.K. Dahle, T. Abbott, M.D. Nave, M. Qian, Proc. Magnesium Techn., 2003, 95-100.
- [48] S. Sannes, H. Gjestland, 2004. Personal communication.
- [49] P. Koch, Die Casting Eng., 1974, 18, 44-46.
- [50] L.W. Garber, Die Casting Eng., 1982, 26, 14-22.
- [51] J. Brevick, M. Duran, Y. Karni, NADCA Trans., 1991, 15, 399-404.
- [52] OSU Center for Die Casting, Effects of ESP on wave celerity and die cast products - 2D athermal model, 2002, http://www.mse.eng.ohio-state.edu/~mobley/diecasting/.
- [53] E.A. Herman, Heat Flow in the Die Casting Industry, NADCA, 1997.
- [54] A. Bowles, PhD thesis, The University of Queensland (Brisbane), 2002.
- [55] Z.W. Chen, Mat. Sci. Eng. A, 2003, 348, 145-153.
- [56] T.B. Hill, BNF Guide to Better Magnesium Die Casting, BNF Metals Technology Centre, 1976.
- [57] S. Sannes, H. Westengen, Proc. Int. Conf. Mg. Alloys & Appl., 1998, 4, 223-228.
- [58] P.D.D. Rodrigo, V. Ahuja, Proc. Int. Conf. Mag. Sci. Techn., 2000, 97-104.
- [59] C. Pitsaris, T. Abbott, C.J. Davidson, Light Met. Techn., 2003, 223-226.
- [60] H. Cao, M. Wessen, 11th Mg Autom.End User Sem., 2003, 1-22.
- [61] G.K. Batchelor, Theoretical and Applied Mechanics, Elsevier Science publishers, 1989, 27-40.
- [62] G.E. Dieter, Mechanical Metallurgy, McGraw-Hill, 1988.
- [63] C. Pitsaris, T. Abbott, C.H.J. Davies, G. Savage, Proc. Int. Conf. Mg. Alloys & Appl., 2003, 6, 694-699.
- [64] C. D¯rum, O.S. Hopperstad, O.-G. Lademo, M. Langseth, Int. J. Sol. Struct., 2004, submitted.
- [65] C. D¯rum, 2004. Personal communication.
- [66] H. Gjestland, 2004. Personal communication.
9. 著作権:
- この資料は、"[Author of the paper]"の論文です: "[Paper Title]" に基づいています。
- 論文ソース: [DOI URL]
この資料は上記の論文に基づいて要約されたものであり、商業目的での無断使用は禁止されています。
Copyright © 2025 CASTMAN. All rights reserved.