この要約は、射出成形およびダイカスト部品の自動化された製造容易性解析に焦点を当てた研究論文の概要を提供します。
1. 概要:
- タイトル: 射出成形およびダイカスト部品のための自動化された製造容易性解析 (AUTOMATED MANUFACTURABILTY ANALYSIS FOR INJECTION-MOLDED AND DIE-CAST PARTS)
- 著者: ダニエル A. マクアダムス (Daniel A. McAdams)、ラフル A. ビドカー (Rahul A. Bidkar)
- 発表年: 2003年
- 掲載ジャーナル/学会: 2003年 ASME 国際設計工学技術会議およびコンピュータ情報工学会議 (Proceedings of the 2003 ASME International Design Engineering Technical Conferences and the Computers and Information in Engineering Conference)
- キーワード: 設計製造 (Design for Manufacturing)、フィーチャ認識 (Feature Recognition)、自動化された製造容易性解析 (Automated Manufacturability Analysis)、射出成形 (Injection-Molding)、ダイカスト (Die-Casting)
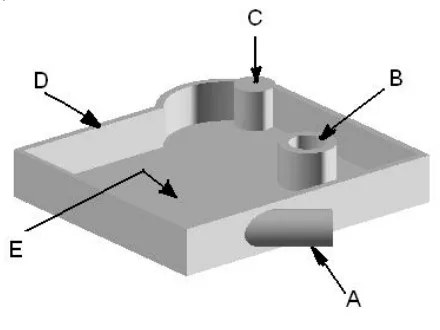
2. 研究背景:
- 研究トピックの社会的/学術的背景: 本論文では、製品の成功には設計と下流工程の円滑な統合が不可欠であることを強調しています。設計段階で部品の製造容易性を評価するコンピュータベースのツールは、設計と製造を結び付けるために不可欠です。自動化された製造容易性研究は、設計製造 (DFM)、計算幾何学、コンピュータ支援設計 (CAD)、およびフィーチャ認識に基づいて構築されています。
- 既存研究の限界: 既存の自動化された製造容易性解析研究は、主に機械加工プロセス(フライス加工、穴あけ加工など)に焦点を当てています。射出成形、ダイカスト、鍛造、スタンピングなどの非機械加工プロセスは、一般的かつ重要な製造プロセスであるにもかかわらず、注目されていません。現在のフィーチャ認識技術も主に機械加工アプリケーション向けであり、非材料除去プロセスへの適用性は限られています。CADシステムのソリッドモデルは高度ですが、低レベルのデータ(点、エッジ、面)を格納しており、DFM解析に必要なフィーチャ情報(ボス、穴、アンダーカット)が明示的に含まれていません。
- 研究の必要性: 射出成形およびダイカストのための自動化された製造容易性解析手法の開発は、設計製造への基本的な貢献となります。本研究は、これらのプロセスに特化したフィーチャ認識技術に焦点を当て、射出成形およびダイカスト部品の製造容易性を評価する方法を提示することにより、既存のツールのギャップに対処します。
3. 研究目的と研究課題:
- 研究目的: 射出成形およびダイカスト部品の自動化された製造容易性評価のための数学的フレームワークとアルゴリズムを開発すること。これには、新規なフィーチャ認識手法の作成と、これらの特定のプロセスにおける製造容易性解析のためのフィーチャ認識における主要な課題への対処が含まれます。
- 主な研究課題:
- コンピュータベースのツールを使用して、射出成形およびダイカスト部品の製造容易性を自動的に評価するにはどうすればよいか?
- 射出成形およびダイカストにおける製造容易性解析に適したフィーチャ認識手法を開発するにはどうすればよいか?
- 射出成形およびダイカスト部品のコンテキストで、パーティング面、アンダーカット、穴、およびボスの認識という課題にどのように対処するか?
- ソリッドモデルの3Dバイナリ表現は、これらのプロセスにおけるフィーチャ認識と製造容易性解析に効果的に使用できるか?
- 研究仮説: 本論文では研究仮説は明示的に述べられていませんが、以下のことが示唆されています。
- 部品を要素キューブに分解し、それらの個々の製造容易性を評価する数学的フレームワークは、射出成形およびダイカスト部品の全体的な製造容易性を効果的に評価できる。
- ソリッドモデルの3Dバイナリ表現は、DFM解析における従来のB-repモデルの限界を克服し、射出成形およびダイカストにおいて重要な製造容易性情報を抽出するために使用できる。
4. 研究方法論
- 研究デザイン: 本研究では、製造容易性評価アルゴリズム (MEA) を作成し、C++ および Unigraphics ソリッドモデリングソフトウェアを使用して実装するという、開発および実装アプローチを採用しています。アルゴリズムは、新規なフィーチャ認識手法に基づいています。
- データ収集方法: この手法では、ソリッドモデルの3Dバイナリ表現を取得する手順を使用します。これには以下が含まれます。
- 要素キューブへの分解: 部品は、1(ソリッドキューブ)と 0(ボイドキューブ)の3Dバイナリ配列に分解されます。
- スライス: ソリッドモデルは、3Dメッシュを作成するために直交方向にスライスされます。
- ブール代数: キューブがソリッドモデルの体積の 50% 以上を占める場合、ソリッドキューブとみなされ、それ以外の場合はボイドキューブとみなされます。ソリッド/ボイドキューブはブール代数を使用して決定されます。
- 分析方法: 方法論の中核は、製造容易性評価アルゴリズム (MEA) です。MEA の主な側面は次のとおりです。
- ソリッドキューブのタイプ分類: ソリッドキューブは、タイプ I(部品の完全に内部)とタイプ II(境界上)に分類されます。タイプ II キューブは製造容易性にとって重要です。
- アクセス可能性分析: MEA は、製造容易性を判断するためにボイドキューブのアクセス可能性を調査します。アクセスできないボイドキューブは、製造上の問題を示します。
- アンダーカット認識: アンダーカットは、金型閉鎖方向に対して垂直な、アクセスできないタイプ II ソリッドキューブによって形成された表面として識別されます。
- パーティング面決定: パーティング面は、バイナリ表現の列をトラバースし、各列の最上部のソリッドキューブを識別することによって見つけられます。
- ボスと穴の認識: ボスと穴は、隣接するレイヤーのタイプ I ソリッドキューブ(ボスの場合)またはボイドキューブ(穴の場合)を「クラビング」、「接続」、「チェック」し、境界上のタイプ II キューブの形状と空間配置を分析することによって認識されます。
- 研究対象と範囲: 本研究は、射出成形およびダイカスト部品に適用可能な一般的なアルゴリズムの開発に焦点を当てています。クランクケースカバーの例と、ボスと穴のある単純な部品を使用して、アルゴリズムの能力を実証しています。バイナリ表現に使用されたキューブサイズは、約 70 mm x 40 mm x 20 mm の部品に対して 1 mm x 1 mm x 1 mm でした。
5. 主な研究結果:
- 主な研究結果:
- 新規なフィーチャ認識手法: 部品を要素キューブに分解し、バイナリ表現を使用する新しいフィーチャ認識手法が開発されました。
- 自動化された製造容易性評価アルゴリズム (MEA): 射出成形およびダイカスト部品の製造容易性を評価するためのアルゴリズムが作成および実装されました。
- パーティング面決定: MEA は、部品のパーティング面を正常に決定します。
- アンダーカット認識: MEA は、部品のアンダーカットを識別できます。
- ボスと穴の認識: MEA は、ボスと穴を認識し、円筒形と他の形状を区別できます。
- 製造容易性のためのアクセス可能性分析: MEA は、ボイドキューブのアクセス可能性分析を使用して、部品全体の製造容易性を判断します。
- 統計的/定性的分析結果: 本論文では、主に方法論の開発を提示し、例を通してその応用を実証しています。統計分析は提示されていません。定性的な結果は、例示部品におけるフィーチャの認識の成功を通して実証されています。
- データ解釈:
- バイナリ表現は、製造容易性解析のために部品の形状を効果的に捉えます。
- タイプ II ソリッドキューブは、製造容易性の問題とフィーチャ境界を識別するために不可欠です。
- ボイドキューブのアクセス可能性分析は、成形性を評価するための直接的な方法を提供します。
- MEA アルゴリズムは、射出成形およびダイカスト部品の主要なフィーチャと製造容易性に関する課題にうまく対処しています。
- 図のリスト:
- 図 1. ダイカストに重要なフィーチャを示す部品のソリッドモデル表現。
- 図 2. グローバル製造容易性解析アルゴリズムの主要なステップを示すフローチャート。
- 図 3. 部品が平らであるか箱型であるかを判断するための詳細なアルゴリズム。グローバル製造容易性解析アルゴリズムのステップ AA。
- 図 4. 部品に示されている射出成形およびダイカストのフィーチャ認識ニーズに適用した場合の既存のフィーチャ認識技術の適用性の概要。
- 図 5. 成形される単純な部品。
- 図 6. 小さな構成要素に分解された候補部品。
- 図 7. 中空ボスのある単純な部品。
- 図 8. 円筒ボスのあるブロック。
- 図 9. 部品のスライスバージョン。
- 図 10. タイプ I またはタイプ II としてソリッドキューブを分類。
- 図 11. アンダーカットを見つけるためのアクセス可能性分析の説明。
- 図 12. アンダーカットの認識の説明。
- 図 13. 単純な部品のパーティング面を決定。
- 図 14. ボスと穴のある単純な部品。
- 図 15. 部品のソリッドキューブのタイプ分類。
- 図 16. 図 15 に示す部品のレイヤーのバイナリ表現。
- 図 17. 隣接するレイヤーの接続の説明。
- 図 18. 「製造要件」の説明。
- 図 19. バイナリデータにおける「製造要件」の説明図。
- 図 20. 認識された穴とボス。
- 図 21. 穴のある単純な部品。
- 図 22. 認識された穴。
- 図 23. MEA と ASV アプローチのグラフィカルな比較。
- 図 24. 特定されたパーティング面と例の認識されたフィーチャ。
Figure 23. A Graphical comparison between MEA and ASV approach
Figure 24. The identified parting surface and recognized features for the example.
6. 結論と考察:
- 主な結果の要約: 本研究では、射出成形およびダイカスト部品の自動化された製造容易性解析のための製造容易性評価アルゴリズム (MEA) を開発し、実装することに成功しました。MEA は、ソリッドモデルの新規なバイナリ表現を利用し、パーティング面決定、アンダーカット、穴、ボス認識など、これらの製造プロセスに特有のフィーチャ認識の課題に効果的に対処します。
- 研究の学術的意義: 本研究は、射出成形やダイカストなどの非材料除去プロセスへの応用を拡大することにより、自動化された製造容易性解析の分野に大きく貢献しています。成形および鋳造の物理学に触発された新しいフィーチャ認識フレームワークを導入し、主に機械加工に焦点を当てた既存の技術と比較して独自のアプローチを提供します。製造容易性評価のための要素キューブとバイナリ表現の使用という概念は、斬新な貢献です。
- 実用的な意義: MEA は、設計エンジニアが設計の初期段階で射出成形およびダイカスト部品の製造容易性を評価するための貴重なツールを提供します。これにより、以下につながる可能性があります。
- 設計反復の削減と製品開発サイクルの迅速化。
- 製造容易性の問題を事前に特定して対処することにより、製造コストを削減。
- 射出成形およびダイカストプロセスに適した部品設計の改善。
- 研究の限界:
- 現在のフィーチャ認識アプローチは、金型閉鎖方向に平行なボスと穴に限定されています。角度のあるフィーチャはアンダーカットとして分類されます。
- 現在の実装では、最初に金型閉鎖方向を指定する必要があります。
- 本論文では、壁、リブ、その他の複雑なフィーチャを認識するためのルールを形式化する必要があることを認めています。
- MEA の一般化可能性とロバスト性は、より広範囲の複雑な射出成形およびダイカスト部品でテストする必要があります。
7. 今後のフォローアップ研究:
- 今後のフォローアップ研究の方向性:
- 3Dバイナリデータで壁、リブなどの複雑なフィーチャ、およびその他のフィーチャを認識するためのルールを形式化および確立します。
- 3Dバイナリ配列をスキャンし、フィーチャを認識することにより、金型閉鎖の優先方向を自動的に決定するアルゴリズムを開発します。
- 金型閉鎖方向に対して角度のあるフィーチャを含めるようにフィーチャ認識機能を拡張し、平行フィーチャだけにとどまらないようにします。
- MEA の妥当性とロバスト性を確立するために、より広範囲の複雑な射出成形およびダイカスト部品で MEA をテストおよび検証します。
- 製造容易性解析の結果に基づいて部品の再設計提案を提供する「自動合成」機能を開発し、より完全な「コンピュータ支援設計」システムに向けて進みます。
- さらなる探求が必要な分野:
- さまざまなフィーチャサイズと製造能力に合わせて、精度と計算コストのバランスを取るためのバイナリ表現のメッシュサイズを最適化します。
- 設計ワークフロー内でシームレスな製造容易性解析を実現するために、MEA を商用 CAD システムと統合することを検討します。
- MEA の鍛造やスタンピングなどの他の非機械加工プロセスへの応用を探求します。
8. 参考文献:
- Dastidar, P. G., A knowledge-based manufacturing advisory system for the economical design of metal stampings, PhD dissertation, University of Massachusetts Amherst, 1991.
- Dixon, J. R. and Poli, C., Engineering Design and Design for Manufacturing, Field Stone Publishers, 1995. Gadh, R., Feature mapping and feature recognition in geometric design generation, In Jami Shah, Martti Mäntylä and Dana S. Nau, editors, Advances in Feature based Manufacturing, chapter 6, pp. 107-128, Elsevier publishers, 1994.
- Gadh, R. and Prinz, F. B., Recognition of geometric forms using the differential depth filter, Computer Aided Design, Butterworth-Heinemann publishers, 24 (11), pp. 583-598, 1992.
- Gupta, S. K., Regli, W. C., Nau, D. S., and Zhang, G., A methodology for systematic generation and evaluation of alternative operation plans, In Jami Shah, Martti Mäntylä and Dana S. Nau, editors, Advances in Feature based Manufacturing, chapter 8, pp. 161-184, Elsevier publishers, 1994.
- Gupta, S. K. and Nau, D. S., A systematic approach for analyzing the manufacturability of machined parts, Computer Aided Design, 1995.
- Gupta, S. K., Regli, W. C., Das, D., and Nau, D. S., Automated Manufacturability Analysis: A Survey, Research in Engineering Design, Vol. 9, No. 3, pp. 168- 190, 1997.
- Henderson, M. R., Extraction of feature information from three-dimensional CAD data, PhD dissertation, Purdue University, 1984.
- Henderson, M. R., Srinath, G., Stage, R., Walker, K. and Regli, W., Boundary Representation-based Feature Identification, In Jami Shah, Martti Mäntylä and Dana S. Nau, editors, Advances in Feature based Manufacturing, chapter 2, pp. 15-38, Elsevier publishers, 1994.
- Joshi, S. and Chang, T. C., Graph based heuristics for recognition of machined features from a 3D solid model, Computer Aided Design, 20 (2), pp. 58-66, 1988.
- J. W. Van Vliet C. A. Van Luttervelt and H. J. J. Kals, State Of the Art report on Design for Manufacturing. In Design Engineering Technical Conference, ASME, 1999. INCLUDE PAPER NUMBER
- Kramer, T. R., Nau, D. S., Gupta, S. K., Regli, W. and Zhang, G., Development of Machining Alternatives, Based on MRSEVs, Proc. of the ASME Computers in Engineering Conference, 1993.
- Kyprianou, L., Shape classification in Computer Aided Design, PhD dissertation, Cambridge, UK, 1980.
- Lei, S. and Qamhiyah, A., Wavelet-based surface analysis for form feature extraction, Proc. of Design for Manufacturing Conf. ASME, 2000. INCLUDE PAPER NUMBER
- Mill, F.G., Naish, J.C. and Salmon, J.C., Design for machining with a simultaneous-engineering workstation, Computer Aided Design, pp. 521-527, 1994.
- Mortenson, M., Geometric modeling, Wiley, 1985.
- Poli, C., Escudero, J. and Fernandez, R., How Part Design Affects Injection Molding Tool Costs, Machine Design, 1988.
- Poli, C., Fredette, L. and Sunderland, J. E., Trimming the cost of die-castings, Machine Design, 1990.
- Poli, C., Design for Manufacturing: A Structured Approach, Butterworth Heinemann, Boston, 2001.
- Prabhakar, S., An experiment on the use of neural nets in form feature recognition, Master’s thesis, Arizona State University, 1990.
- Priest, J. W. and Sanchez, J. M., An empirical methodology for measuring producibility early in product development., International Journal of Computer Integrated Manufacturing, 4(2),pp. 114-- 120, 1991.
- Regli, W. and Nau, D. S., Building a general approach to feature recognition of material removal shape element volumes (MRSEVs), Second Symposium on Solid Modeling Foundations and CAD/CAM Applications, 1993.
- Regli, W., Gupta, S. K. and Nau, D. S., Feature recognition for manufacturability analysis, ASME Computers in Engineering Conference, pp. 93-104,1994.
- Regli, W., Geometric Algorithms for the Recognition of Features from Solid Models, Ph.D. dissertation, University of Maryland, 1995.
- Requicha, A. A. G. and Han, J., Feature recognition from CAD models, IEEE Computer Graphics, 1998.
- Sakurai, H. and Gossard, D. C., Shape Feature Recognition from 3D solid models, ASME Computers in Engineering, 1988.
- Shah, J., Mäntylä, M. and Nau, D. S., editors, Advances in Feature based Manufacturing, chapter 1, pp. 1-11, Elsevier publishers, 1994.
- Shah, J. and Mäntylä, M., Parametric and Feature-Based CAD/CAM: Concepts, techniques and applications, Wiley–Interscience Publication, 1995.
- Trucks, H. E., Designing for Economical Production, Society of Manufacturing Engineers, MI, 1987. UniGraphics Solutions Inc., V18.0 UniGraphics Help, 2001.
- Vandenbrande, J., Automatic recognition of machinable features in solid models, PhD dissertation, University of Southern California, 1990.
- Vandenbrande, J. H. and Requicha, A. A. G., Spatial reasoning for the automatic recognition of machinable features in solid models, IEEE Pattern Analysis and Machine Intelligence, vol. 15, no. 12, pp. 1269-1285, 1993.
- Woo, T., Feature recognition by volume decomposition, Proc. of Conference CAD/CAM technology in Mechanical Engineering, Cambridge, MA, 1982.
- Yong Se Kim, Volumetric feature recognition using convex decomposition, In Jami Shah, Martti Mäntylä and Dana S. Nau, editors, Advances in Feature based Manufacturing, chapter 3, pp. 39-63, Elsevier publishers, 1994. Zeid, I., CAD/CAM Theory and Practice, McGraw-Hill, 1991.
9. 著作権:
*この資料は、ダニエル A. マクアダムスとラフル A. ビドカーの論文に基づいています:「射出成形およびダイカスト部品のための自動化された製造容易性解析」(AUTOMATED MANUFACTURABILTY ANALYSIS FOR INJECTION-MOLDED AND DIE-CAST PARTS)。
*論文ソース:?
この資料は上記の論文に基づいて要約されたものであり、商業目的での無断使用は禁止されています。
Copyright © 2025 CASTMAN. All rights reserved.