この論文概要は、Journal of Manufacturing Processes に掲載された論文 「A complete computer aided engineering (CAE) modelling and optimization of high pressure die casting (HPDC) process」 に基づいています。
1. 概要:
- タイトル: 包括的なコンピュータ支援エンジニアリング(CAE)モデリングと高圧ダイカスト(HPDC)プロセスの最適化 (A complete computer aided engineering (CAE) modelling and optimization of high pressure die casting (HPDC) process)
- 著者: K. Dou, E. Lordan, Y.J. Zhang, A. Jacot, Z.Y. Fan
- 発表年: 2020年
- 掲載ジャーナル/学会: Journal of Manufacturing Processes, Elsevier Ltd. / The Society of Manufacturing Engineers
- キーワード: CAEシミュレーション, 有限要素法, HPDC, プロセス最適化, CFD, 機械的特性 (CAE simulation, finite element method, HPDC, Process optimization, CFD, Mechanical property)
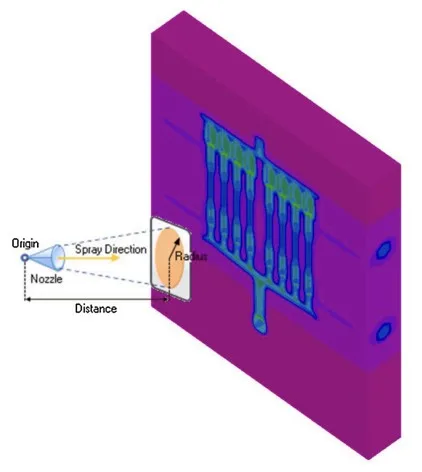
2. 研究背景:
- 研究トピックの社会的/学術的背景: コンピュータ支援エンジニアリング(CAE)は、その高い効率性と信頼性から製造業においてトレンドとなっています。鋳造業界では、CAEに基づく数値モデリングが、多くの面で従来の試行錯誤による研究開発手順に取って代わりました。高度な並列計算技術と多数の計算モデルにより、さまざまな鋳造条件下での流体流れ、熱伝達、凝固、および欠陥形成挙動を詳細に検討できます。この考えに基づき、コンポーネント設計と鋳造パラメータの最適化を実施して、その後の微細構造および機械的特性評価用の製品を製造できます。このようにして、プロセス条件、鋳造品質、および鋳造機械的特性間の直接的なリンクを、重力ダイカスト、高圧ダイカスト(HPDC)、連続鋳造などのプロセスにとって実用的、経済的、エネルギー効率の高い方法で確立できます。
- 既存研究の限界: HPDCプロセスの数値シミュレーションは珍しいものではありませんが、研究者や製造業者は、実際の作業では直接観察できないことをより良く理解しようと常に努めています。 既存の研究は、HPDCプロセスに影響を与える個々の現象に焦点を当てていることが多く、ゲーティングシステム設計、インゲート出口での液体ジェットの最適化、溶融金属の流れ特性、再酸化プロセス、ショットスリーブ充填の影響などが研究されてきました。しかし、上流のサブプロセスからの影響を考慮したHPDCサイクル全体の完全なシミュレーションは、これまでほとんど見られていませんでした。つまり、ダイ加熱、熱ダイサイクル、ショットスリーブ予備充填、低速ショット/高速ショット射出、ダイ充填/凝固、および増圧を含むHPDCサイクル全体を1つの数理モデルにチェーン化することです。
- 研究の必要性: HPDCプロセスに影響を与える個々の現象は、数値モデリングと実験を通じて広範囲に研究されてきましたが、上流のサブプロセスからの影響を考慮したHPDCプロセス全体の完全なシミュレーションは、これまでほとんど見られていませんでした。HPDCサイクル全体を1つの数理モデルに統合し、ダイ加熱、熱ダイサイクル、ショットスリーブ予備充填、低速ショット/高速ショット射出、ダイ充填/凝固、増圧などを包括的に扱うモデルが求められています。このようなモデルを確立することで、一連のモデリング研究が可能になり、溶融金属の流れ、凝固、HPDCでの欠陥形成に対するプロセスパラメータの影響を研究し、欠陥形成を抑制するための新しい技術を入手し、さらに検証して産業慣行に採用することを目指しています。
3. 研究目的と研究課題:
- 研究目的: 本研究の目的は、高圧ダイカスト(HPDC)プロセス全体のコンピュータ支援エンジニアリング(CAE)モデルを開発し、最適化することです。このモデルは、ダイ加熱、熱ダイサイクル、ショットスリーブ予備充填、低速ショット/高速ショット射出、ダイ充填/凝固、増圧など、HPDCプロセス全体をシミュレーションすることを目的としています。鋳造シミュレーションパッケージProCASTを用いて、Al-Si合金を対象に、HPDCプロセス全体をシミュレーションします。
- 主な研究課題:
- 完全な数値モデルに基づいてHPDCプロセスを最適化するための方法論を確立すること。
- 最適な熱ダイサイクル数を決定し、比較的健全な鋳造品質を保証するためにダイ温度の動的定常状態を得ること。
- 射出中の欠陥形成を低減するためにピストンショットプロファイルを調整すること。
- コンピュータシミュレーションの有効性を評価するために、最適化されたピストンショットプロファイルを使用して引張試験片を鋳造し、機械的特性(耐力、引張強さ、伸び)を試験すること。
- 研究仮説: (論文中に明示的な記述はありませんが、以下のように推測されます)
- 開発されたCAEモデルは、HPDCプロセスにおける熱伝達、流体流れ、凝固を正確に予測できる。
- 最適化された熱ダイサイクルとピストンショットプロファイルを用いることで、鋳造品の機械的特性が向上する。
- CAEシミュレーションによって最適化されたプロセスパラメータを用いることで、HPDCプロセスの効率と製品品質が向上する。
4. 研究方法:
- 研究デザイン: 本研究では、数値シミュレーションと実験的検証を組み合わせた研究デザインを採用しています。まず、ProCASTソフトウェアを用いてHPDCプロセス全体のCAEモデルを構築しました。次に、熱電対測定と赤外線イメージングを用いてダイ表面温度分布を測定し、溶融金属とダイ壁/ショットスリーブ間の界面熱伝達係数(iHTC)を調整しました。調整されたiHTCを組み込んだCAEモデルを用いて、HPDCプロセスの最適化シミュレーションを実施しました。最適化されたプロセスパラメータを用いて実際に引張試験片を鋳造し、機械的特性を評価することで、シミュレーション結果の検証を行いました。
- データ収集方法:
- 熱電対測定と赤外線イメージング: ダイ表面の温度分布を測定し、iHTCを調整するために使用されました。
- 機械的特性試験: 最適化されたピストンショットプロファイルを用いて鋳造された引張試験片の機械的特性(耐力、引張強さ、伸び)を評価するために実施されました。
- 分析方法:
- 有限要素法(FEM)シミュレーション: ProCASTソフトウェアのVisual-Mesh、Visual-Cast、Visual-Viewerモジュールを使用して、HPDCプロセス全体のFEMシミュレーションを実施しました。溶融金属の流れ、熱伝達、凝固は、エンタルピー法に基づく3D有限要素法を用いて計算されました。乱流モデルには標準k-εモデル、自由表面の追跡にはVolume of Fluid(VOF)法が用いられました。
- プロセス最適化方法: 以下の手順でHPDCプロセスの最適化を行いました。
- 熱ダイサイクル最適化: ダイ温度が動的定常状態に達する最適な熱ダイサイクル数を決定しました。
- ピストンショットプロファイル最適化: 射出中の欠陥形成を低減するためにピストンショットプロファイルを調整しました。特に、ピストンの低速ショット加速位置と速度に着目し、パラメータを変化させたシミュレーションを実施しました。
- 研究対象と範囲:
- 材料: アルミニウム合金A356
- プロセス: 冷間チャンバーHPDCプロセス
- シミュレーション範囲: ダイ加熱、熱ダイサイクル、ショットスリーブ予備充填、低速/高速ショット射出、ダイ充填/凝固、増圧を含むHPDCサイクル全体
- 実験範囲: 最適化されたピストンショットプロファイルを用いた引張試験片の鋳造と機械的特性評価
5. 主な研究成果:
- 主な研究成果:
- 最適な熱ダイサイクル数: シミュレーションにより、6〜7サイクル後、ダイ表面温度分布が準定常状態に達することが明らかになりました。したがって、7サイクル後のダイ表面温度分布を、その後のダイ充填モデリングに使用しました。
- 最適化されたピストンショットプロファイル: ピストンの低速ショット加速位置を変化させたシミュレーションにより、初期位置から10mmの加速位置が、鋳造品中の空気巻き込みが最も少なく、均一になることが示されました。
- 機械的特性の向上: 最適化されたピストンショットプロファイル(10mm加速位置、低速ショット速度0.4〜0.6m/s)を使用して鋳造された引張試験片は、機械的特性が向上しました。特に、引張強さ(UTS)と伸び(El)の値が最も高く、標準偏差が最も低くなりました。
- 統計/定性分析結果:
- 機械的特性データ (表3): ピストン速度プロファイル0.4〜0.6 m/sで製造された引張試験片は、平均UTSと伸び値が最も高く、これらの特性の標準偏差が最も低く、機械的性能の向上と安定化が示されました。
- 空気巻き込みシミュレーション (図17): 空気巻き込み分布の定性分析により、10mmのピストン低速ショット加速位置が、他の位置と比較して、より少なく、より均一に分布した空気巻き込みをもたらすことが示されました。
- 酸化物形成シミュレーション (図19): 酸化物指標シミュレーションは、0.4〜0.6 m/sの低速ショット速度が、他の速度と比較して、比較的均一な酸化物分布と低い酸化物傾向をもたらすことを示唆しました。
- データ解釈: これらの結果は、CAEシミュレーションがHPDCプロセスを効果的にモデル化し、最適化できることを示しています。熱ダイサイクルを最適化することで熱的安定性が確保され、CAEの洞察に基づいてピストンショットプロファイルを調整することで、欠陥形成を最小限に抑え、機械的特性を向上させることができます。引張試験による実験的検証はCAE予測を裏付け、最適化されたプロセスパラメータと鋳造性能の向上との間に明確な関連性があることを示しています。
- 図表リスト:
- Fig. 1. Modelling workflow of the entire HPDC process. (HPDCプロセス全体のモデリングワークフロー)
- Fig. 2. Typical HPDC procedures during one entire cycle. (1サイクルにおける典型的なHPDC手順)
- Fig. 3. Configuration and hybrid FEM mesh used in calculation (in ½ symmetry). (計算に使用される構成とハイブリッドFEMメッシュ(1/2対称))
- Fig. 4. A356 alloy thermophysical properties. (A356合金の熱物性)
- Fig. 5. Time-dependent iHTCs used in this work. (本研究で使用された時間依存性iHTC)
- Fig. 6. Temperature distribution on the die surface after heating from atmosphere. (大気からの加熱後のダイ表面の温度分布)
- Fig. 7. Temperature distribution at die surface during the 6th HPDC cycle. (6回目のHPDCサイクル中のダイ表面の温度分布)
- Fig. 8. Schematic illustration of spray/blow after part ejection. (部品突き出し後のスプレー/ブローの模式図)
- Fig. 9. Comparison of predicted die surface temperature distribution with infrared images obtained during HPDC. (HPDC中に取得された赤外線画像と予測されたダイ表面温度分布の比較)
- Fig. 10. Calculated temperature curves at sampling positions of die surface at multiple thermal cycles. (複数の熱サイクルにおけるダイ表面のサンプリング位置で計算された温度曲線)
- Fig. 11. Flowrate curve used during shot sleeve filling. (ショットスリーブ充填中に使用される流量曲線)
- Fig. 12. Flow and temperature evolution of melt during filling of shot sleeve prior to piston injection, images from two viewing angles. (ピストン射出前のショットスリーブ充填中の溶融金属の流れと温度変化、2つの視点からの画像)
- Fig. 13. Distribution of externally solidified crystals along the shot sleeve. (ショットスリーブに沿った外部凝固結晶の分布)
- Fig. 14. Filling sequence of the melt and distribution of air in the die cavity. (ダイキャビティ内の溶融金属の充填シーケンスと空気の分布)
- Fig. 15. Section cut-off for position where solidification time is below 0.7 s. (凝固時間が0.7秒未満の位置の断面カットオフ)
- Fig. 16. Piston shot curves with different slow shot acceleration positions. (異なる低速ショット加速位置でのピストンショット曲線)
- Fig. 17. Modelling results of air entrainment in casting with different slow shot acceleration position. (異なる低速ショット加速位置での鋳造における空気巻き込みのモデリング結果)
- Fig. 18. Piston shot curves with different slow shot velocities. (異なる低速ショット速度でのピストンショット曲線)
- Fig. 19. Comparison of modelling results with different piston slow shot velocity magnitude. (異なるピストン低速ショット速度におけるモデリング結果の比較)
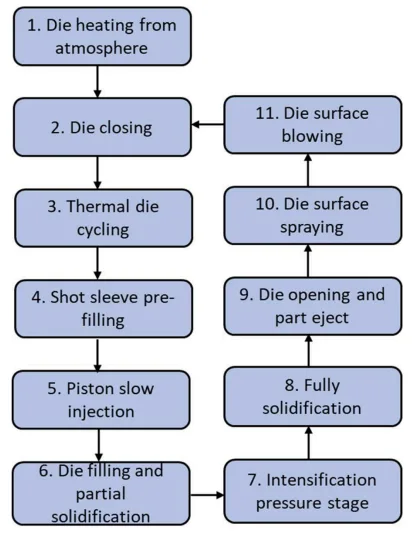
6. Conclusion and Discussion:
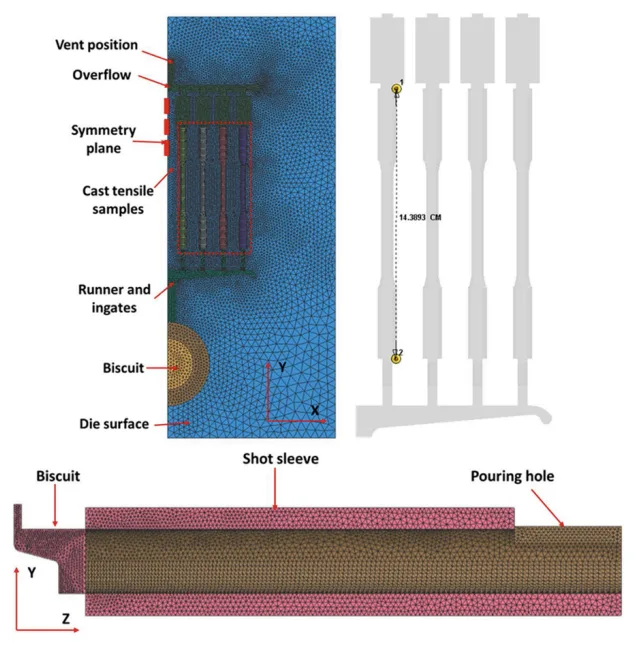
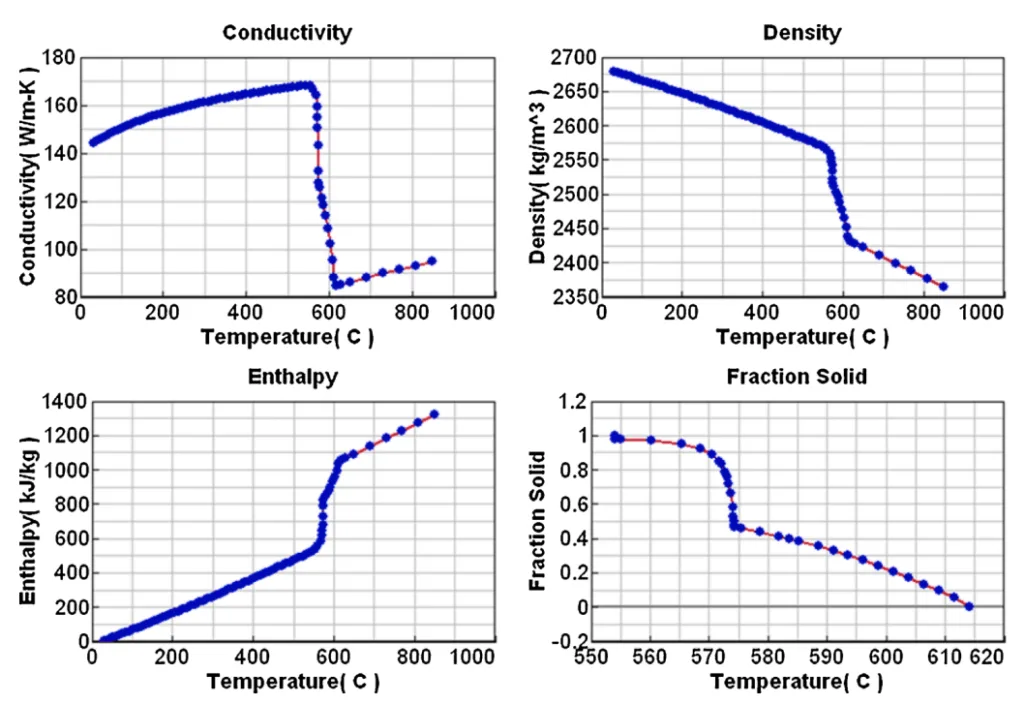
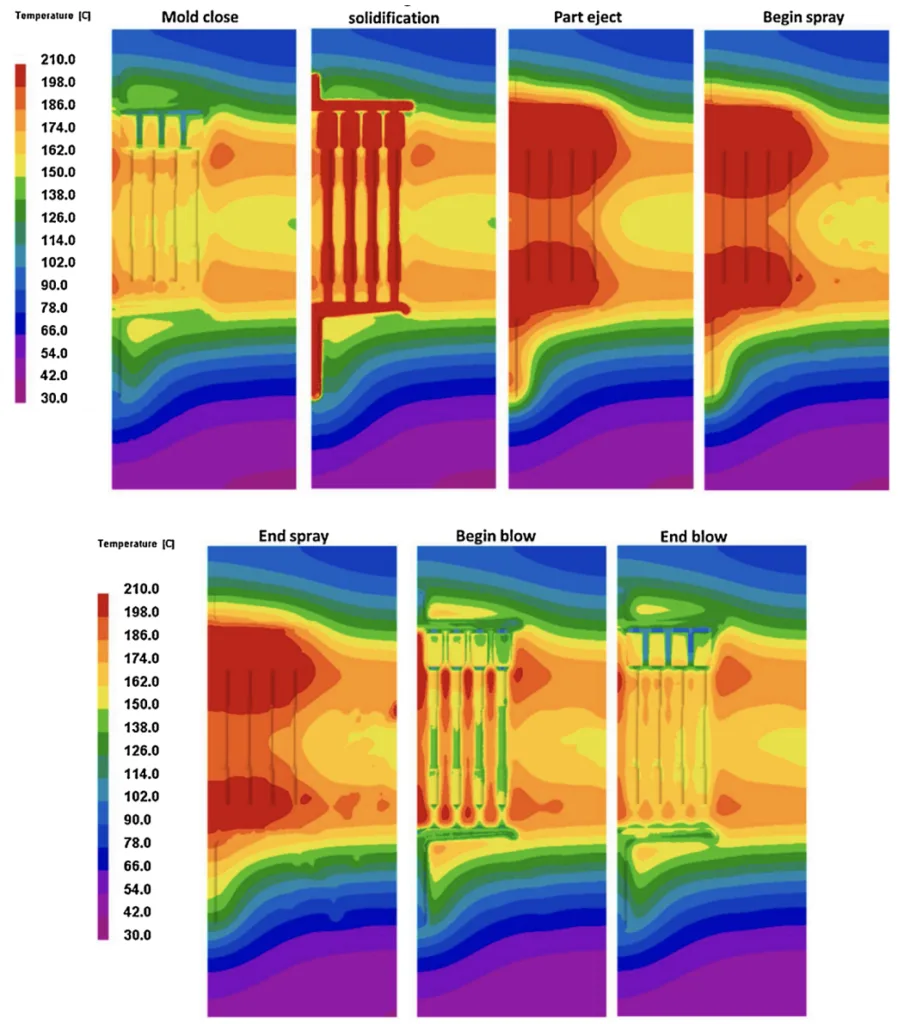
6. 結論と考察:
- 主な結果の要約: ProCASTプラットフォームで冷間チャンバー高圧ダイカストの完全なシミュレーションアプローチが確立されました。FEMに基づいて、ダイ加熱、熱ダイサイクル、ショットスリーブ予備充填、射出、凝固を含む完全なHPDCプロセスがモデル化されました。熱ダイサイクルとピストンショットプロファイルの最適化は、シミュレーションを通じて達成されました。実験的検証により、CAE最適化パラメータを用いて製造された鋳造品は、機械的特性が向上していることが確認されました。最適なピストン低速ショット加速位置は初期位置から10mmであり、最適な低速ショット速度範囲は、研究条件下では0.4〜0.6m/sでした。
- 研究の学術的意義: 本研究は、HPDCプロセス全体のシミュレーションのための包括的な方法論を提供し、孤立した側面に焦点を当てた以前の研究の限界に対処しました。実験データ(iHTC)をCAEモデルに統合することで、その精度と予測能力が向上します。この研究は、HPDCプロセス内の複雑な相互作用を理解し、プロセスパラメータを最適化するための包括的なCAEアプローチの価値を実証しています。
- 実際的な意義: 開発されたCAE手法は、HPDCエンジニアに、時間とコストのかかる経験的な試行錯誤を必要とせずに、HPDCセル内の鋳造パラメータと運転条件を最適化するための体系的かつ費用対効果の高いルートを提供します。この仮想エンジニアリングアプローチを使用することで、製造業者は欠陥を減らし、鋳造品質を向上させ、機械的特性を高め、HPDCプロセスでの材料とエネルギー消費を削減できる可能性があります。最適なピストンショットプロファイルパラメータに関する知見は、プロセス設定に関する実用的なガイドラインを提供します。
- 研究の限界: ProCASTにおける空気巻き込みの予測は定性的であると指摘されています。有用なガイドを提供しますが、空気巻き込みレベルの正確な定量的予測を提供しない場合があります。空気巻き込みモデルのさらなる改良と検証が有益となる可能性があります。本研究は、A356合金と特定のHPDC設定に焦点を当てており、最適化されたパラメータの他の合金および鋳造システムへの一般化には、さらなる調査が必要です。
7. 今後のフォローアップ研究:
- フォローアップ研究の方向性:
- 開発されたCAEモデルを使用して、溶融金属の流れ、凝固、およびHPDCでの欠陥形成に対するさまざまなプロセスパラメータ(ピストンショットプロファイルと熱ダイサイクル以外)の影響をさらに調査します。
- HPDCプロセスにおける欠陥形成を抑制するための新しい技術を調査および検証し、物理的な実装前にCAEシミュレーションを使用してこれらの技術を設計および最適化する可能性を探ります。
- 特に欠陥予測(気孔率、空気巻き込み、酸化物など)について、CAEモデルのより詳細な定量的検証を実施し、シミュレーション結果と実験的測定値を比較します。
- さらなる探求が必要な分野:
- 溶融金属の流れ特性、凝固挙動、およびHPDCにおける欠陥形成メカニズム間の複雑な相互作用に関するより深い調査。
- 包括的なCAEモデルの適用範囲を、より広範囲のアルミニウム合金および他のダイカスト合金(マグネシウム合金など)に拡大します。
- 特にHPDCシミュレーションにおける空気巻き込みと酸化物生成の、より洗練された定量的精度が高い欠陥形成予測モデルの開発。
- HPDCにおける動的プロセス制御と最適化のためのリアルタイムプロセス監視データとCAEモデルの統合。
8. 参考文献:
- [1] Zhou Y, Guo Z, Xiong SM. Effect of runner design on the externally solidified crystals in vacuum die-cast Mg-3.0Nd-0.3Zn-0.6Zr alloy. J. Mater. Process. Technol. 2019;267:366-75. https://doi.org/10.1016/j.jmatprotec.2018.12.032.
- [2] Gunasegaram DR, Givord M, O'Donnell RG, Finnin BR. Improvements engineered in UTS and elongation of aluminum alloy high pressure die castings through the alteration of runner geometry and plunger velocity. Mater. Sci. Eng. A. 2013;559: 276-86. https://doi.org/10.1016/j.msea.2012.08.09
- [3] Tsoukalas VD. The effect of die casting machine parameters on porosity of aluminium die castings. Int. J. Cast Met. Res. 2003;15:581-8. https://doi.org/ 10.1080/13640461.2003.11819544.
- [4] wu Wu M, bo Li X, peng Guo Z, mei Xiong S. Effects of process parameters on morphology and distribution of externally solidified crystals in microstructure of magnesium alloy die castings. China Foundry. 2018;15:139-44. https://doi.org/ 10.1007/s41230-018-7242-z.
- [5] Kwon HJ, Kwon HK. Computer aided engineering (CAE) simulation for the design optimization of gate system on high pressure die casting (HPDC) process. Robot. Comput. Integr. Manuf. 2019;55:147-53. https://doi.org/10.1016/j. rcim.2018.01.003.
- [6] Pereira GG, Cleary PW, Serizawa Y. Prediction of fluid flow through and jet formation from a high pressure nozzle using Smoothed Particle Hydrodynamics. Chem. Eng. Sci. 2018;178:12-26. https://doi.org/10.1016/j.ces.2017.1
- [7] Cleary PW, Ha J, Prakash M, Nguyen T. Short shots and industrial case studies: Understanding fluid flow and solidification in high pressure die casting. Appl. Math. Model. 2010. https://doi.org/10.1016/j.apm.2009.10.015.
- [8] Brůna M, Bolibruchová D, Pastirčák R. Reoxidation Processes Prediction in Gating System by Numerical Simulation for Aluminium Alloys. Arch. Foundry Eng. 2017; 17:23-6. https://doi.org/10.1515/afe-2017-0084.
- [9] Korti AIN, Abboudi S. Effects of shot sleeve filling on evolution of the free surface and solidification in the high-pressure die casting machine. Int. J. Met. 2017;11: 223-39. https://doi.org/10.1007/s40962-016-0051-5.
- [10] Dou K, Lordan E, Zhang YJ, Jacot A, Fan ZY. Numerical simulation of fluid flow, solidification and defects in high pressure die casting (HPDC) process, IOP Conf. Ser. Mater. Sci. Eng. 2019;529:012058. https://doi.org/10.1088/1757-899X/529/ 1/012058.
- [11] Gleeson J, Gourlay CM, Schaffer PL, Laukli HI. Gate microstructure in an AlSi9MgMn High-Pressure Die Casting. Proc. 12th Int. Conf. Alum. Alloy 2010: 751-6.
- [12] Cao H, Wessén M. Characteristics of microstructure and banded defects in die cast AM50 magnesium components. Int. J. Cast Met. Res. 2005;18:377-84. https://doi. org/10.1179/136404605225023216.
- [13] Hong Hai N. Effect of Pressure on Solidification Process and Mechanical Properties During Semi-Solid Casting by Computational Fluid Dynamics (CFD). Adv. Mater. 2019;7. https://doi.org/10.11648/j.am.20180702.15. 44.
- [14] Yuan Z, Guo Z, Xiong SM. Skin layer of A380 aluminium alloy die castings and its blistering during solution treatment. J. Mater. Sci. Technol. 2019;35:1906–16. https://doi.org/10.1016/j.jmst.2019.05.011.
- [15] Otarawanna S, Gourlay CM, Laukli HI, Dahle AK. Agglomeration and bending of equiaxed crystals during solidification of hypoeutectic Al and Mg alloys. Acta Mater. 2010;58:261-71. https://doi.org/10.1016/j.actamat.2009.09.002.
- [16] Wang BS, Xiong SM. Effects of shot speed and biscuit thickness on externaly solidified crystals of high-pressure diet cast AM60B magnesium alloy. Trans. Nonferrous Met. Soc. China (English Ed. 2011;21:767-72. https://doi.org/ 10.1016/S1003-6326(11)60778-4.
- [17] Jiao XY, Wang J, Liu C, Guo Z, Wang J, Wang Z, Gao J, Xiong SM. Influence of slow-shot speed on PSPs and porosity of AlSi 17 Cu 2.5 alloy during high pressure die casting. J. Mater. Process. Technol. 2019;268:63-9. https://doi.org/10.1016/j. jmatprotec.2019.01.008.
- [18] Yuan L, Xiong S, Liu B, Masayuki M, Yoshihide M, Shingo I. Numerical simulation and optimization of liquid metal flow in the shot sleeve of cold chamber die casting process. MCWASP Conf. Model. Cast. Welding, Adv. Solidif. Process. Opio, Fr. Miner. Met. Mater. Soc. 2006:111-8.
- [19] Wang QL, Xiong SM. Effect of multi-step slow shot speed on microstructure of vacuum die cast AZ91D magnesium alloy. Trans. Nonferrous Met. Soc. China (English Ed. 2015;25:375-80. https://doi.org/10.1016/S1003-6326(15)63613-5.
9. 著作権:
- この資料は、"K. Dou, E. Lordan, Y.J. Zhang, A. Jacot, Z.Y. Fan" の論文 "A complete computer aided engineering (CAE) modelling and optimization of high pressure die casting (HPDC) process" に基づいて作成されました。
- 論文ソース: https://doi.org/10.1016/j.jmapro.2020.10.062
この資料は上記の論文に基づいて要約されたものであり、商業目的での無断使用は禁止されています。
Copyright © 2025 CASTMAN. All rights reserved.