この技術要約は、M.C. Carter、S. Palit、M. LittlerがNADCA(2010年)で発表した学術論文「Characterizing Flow Losses Occurring in Air Vents and Ejector Pins in High Pressure Die Castings」に基づいています。HPDC(ハイプレッシャーダイカスト)の専門家のために、CASTMANの専門家がGemini、ChatGPT、GrokなどのLLM AIの助けを借りて分析・要約しました。
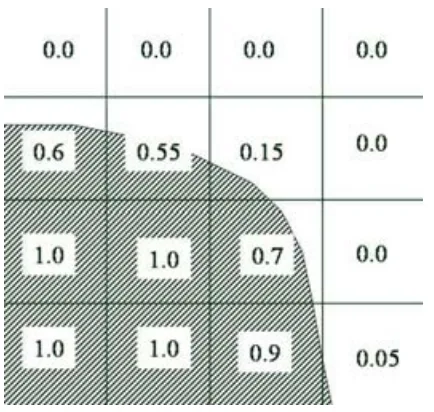
キーワード
- 主要キーワード: HPDCベンティングシミュレーション
- 副次キーワード: 流れ損失係数、FLOW-3Dシミュレーション、ガス気孔低減、エジェクタピンベンティング、ダイカスト欠陥、断熱気泡モデル、計算流体力学(CFD)
エグゼクティブサマリー
- 課題: HPDCにおいて、ベントやエジェクタピン、その他の漏れ経路を通る流れ損失を単純な計算で定量化することは困難であり、ガスの巻き込みとそれに起因する気孔(ポロシティ)を正確に予測・制御することは大きな課題です。
- 手法: 研究者たちは、市販の金型を用いた物理的な「空打ち」射出実験と、計算流体力学(CFD)ソフトウェアであるFLOW-3D®を用いたシミュレーションを組み合わせました。実際のキャビティ内の圧力変化を測定し、このデータを用いてシミュレーションの流れ損失係数を校正(キャリブレーション)しました。
- 主な成果: 本研究は、CFDモデル、特にFLOW-3D®の断熱気泡モデルとバルブモデルを校正することで、ベント、エジェクタピン、金型の残留リークからの累積的な流れ損失を正確に再現できることを実証しました。
- 結論: これにより、技術者は生産前にベンティング戦略をシミュレーション、分析、最適化するための強力で検証済みの手法を手に入れることができます。結果として、ガス気孔を大幅に削減し、より高品質な部品の生産が可能になります。
課題:この研究がHPDC専門家にとって重要な理由
長年にわたり、技術者たちはHPDC製品の表面欠陥や内部気孔の問題に直面してきました。降伏強度や延性といった機械的特性を損なうこれらの欠陥は、主に巻き込まれた空気や潤滑剤の分解によって発生するガスが原因です。真空システムは解決策の一つですが、高価であり、工程を複雑にします。
論文の序論で述べられているように、ベンティングは巻き込まれた空気を除去するための「最も簡単で安価な方法」であり続けています。しかし、効果的なベンティングシステムの設計は決して単純ではありません。総排気量は、専用のベント、ショットスリーブ、エジェクタピン、パーティングラインを通過する流れの複雑な総和だからです。これらの流れ損失を確実に特性評価する方法がなければ、技術者は経験と試行錯誤に頼ることが多くなり、高価な金型修正や不安定な部品品質につながります。本研究は、これらの重要な流れ損失をモデル化するための実用的で正確な方法を模索することにより、この根本的な問題に正面から取り組んでいます。
アプローチ:研究手法の解説
この課題を解決するため、研究者たちは物理的な実験と高度なシミュレーションを組み合わせた巧みな方法論を考案しました。彼らはLittler DieCast社でモーターエンドヘッド用の市販金型を使用し、溶湯なしでの射出実験(「空打ち」)を実施しました。
実験の核心は以下の通りです:
- 変数分離: すべてのベントを開放、真空バルブを閉鎖、パーティングラインを密封、エジェクタピンを密封、すべてのベントを閉鎖、といった様々な構成で金型を稼働させました。
- データ収集: 金型キャビティ内に圧力変換器を設置し、各構成について時間経過に伴う圧力上昇を精密に測定しました(図3)。
- CFDシミュレーション: 商用CFDソフトウェアであるFLOW-3D®を使用して、これらの「空打ち」シナリオを再現しました。鍵となったのは、ソフトウェアの断熱気泡モデル(adiabatic bubble model)を用いてキャビティ内の空気を表現し、バルブモデル(valve model)を用いて様々なオリフィスを通る流れ損失をモデル化したことです。
- 校正(キャリブレーション): 最終的な目標は、シミュレーションの圧力曲線が実際の実験データと完全に一致するまで、シミュレーション内の「累積損失係数」を調整することでした。このプロセスはシミュレーションを効果的に校正し、実際の金型のベンティング性能を忠実に再現するデジタルツインとします。
ブレークスルー:主要な研究結果とデータ
本研究は、HPDCにおけるベンティングについて我々の考え方に直接影響を与える、いくつかの重要な洞察をもたらしました。
- 発見1:ベンティング源の定量化: 図3の実験的な圧力曲線は、各ベンティング経路の相対的な重要性を明確に示しました。真空バルブを閉じたときに最大の圧力上昇が見られ、これが主要なベンティング源であることが特定されました。また、密封されていないエジェクタピンが引き起こす、より小さいながらも重要な圧力低下(2 Psi未満)も定量化されました。対照的に、パーティングラインは十分に密封されており、キャビティ圧力への影響はごくわずかでした。
- 発見2:残留リークの重要な役割: 「すべて閉鎖」の実験と純粋な理論シミュレーションを比較したことから、大きな発見がありました。シミュレーションでは最終圧力が169 psiと予測されましたが(図5)、実際の実験では約25 psiにしか達しませんでした(図3)。この144 psiもの大きな差は、ショットスリーブなどの経路を通る「残留リーク」が非常に大きいことを示しており、これらはしばしば見過ごされますが、空気の排出において明らかに大きな役割を果たしています。
- 発見3:シミュレーション精度の検証: 本研究は、校正されたFLOW-3D®モデルが実験結果を正確に再現できることを成功裏に実証しました。「真空バルブ閉鎖」と「すべて開放」の両ケースにおける計算上の圧力曲線は、図6に示すように、測定された実験データと優れた一致を示し、これが信頼性の高いエンジニアリングツールであることを検証しました。
- 発見4:特定の損失係数の決定: 校正プロセスを通じて、研究者たちは正確な累積損失係数を算出しました。「真空バルブ閉鎖」シナリオ(エジェクタピンと残留リークを通るベンティング)の係数は3.73e-6 m²/√(kg/m³)でした。「すべて開放」シナリオ(すべてのベンティング経路を合わせた場合)の係数は6.4e-6 m²/√(kg/m³)でした。これらの値は、将来のシミュレーション作業にとって強力なデータポイントとなります。
HPDC製品への実用的な示唆
- プロセスエンジニア向け: 本論文の手法は、推測に頼るアプローチから脱却する方法を提供します。「結果と考察」セクションで詳述されているように、各金型要素のベンティングへの寄与度を定量化することで、過度な試行錯誤に頼ることなく、完全な空気排出を確保するためのショットプロファイルと増圧をより精密に最適化できます。
- 品質管理担当者向け: 理論的な「すべて閉鎖」圧力(図3 vs 図5)と実際の圧力との大きなギャップは、残留リークが重要かつ測定可能な要因であることを浮き彫りにします。これは、単純な空打ち圧力テストが、金型の摩耗やシールの完全性を評価するための強力な品質管理チェックとして導入できる可能性を示唆しており、溶湯を鋳込む前に潜在的な気孔問題を予測することができます。
- 金型設計者向け: 本研究は、FLOW-3D®のようなツールを用いることで、設計者が鋼材を加工する前にベンティングやオーバーフロー設計の有効性をデジタルでテストし、確認できることを実証しています。本研究で示されたように、校正された損失係数を割り当てることで、提案された設計が十分なベンティングを提供するかどうかをシミュレーションでき、高価な金型手直しを防ぎ、新しい金型に関する学習曲線を劇的に短縮できます。
論文詳細
Characterizing Flow Losses Occurring in Air Vents and Ejector Pins in High Pressure Die Castings
1. 概要:
- 論文名 (Title): Characterizing Flow Losses Occurring in Air Vents and Ejector Pins in High Pressure Die Castings
- 著者 (Author): M.C. Carter, S. Palit, M. Littler
- 発行年 (Year of publication): 2010
- 発行元 (Journal/academic society of publication): NADCA (North American Die Casting Association)
- キーワード (Keywords): HPDC, ベンティング, 流れ損失, 気孔, 計算流体力学, FLOW-3D, エジェクタピン, 断熱気泡モデル
2. 抄録 (Abstract):
It will be demonstrated how the commercial computational fluid dynamics (CFD) software, FLOW-3D®, can be used to model the flow losses occurring in ejector pins and air vents in high pressure die castings. The results from an ejection experiment done without melt at a commercial tool shop will be discussed. These results will then be used to compute flow loss coefficients for the air vents, ejector pins and residual leaks with the help of the adiabatic bubble model in FLOW-3D®. We will explore an effective tool for calibrating the losses that occur during a pressurized fill in high pressure die castings.
3. はじめに (Introduction):
Surface defects reduce thermal and mechanical properties such as yield strength, ductility and modulus of elasticity of parts produced in high pressure die casting. The surface defects occur due to air entrapment and/or solidification shrinkage. Entrapped gases during fill and the gases evolved during decomposition of lubricants, cause porosity. Vacuum die casting can eliminate these gases. Vacuum valves are expensive and there is a possibility of destroying the valve and/or pump if the valve is not closed before the metal leaves the shot sleeve. Moreover, an additional runner system needs to be adequately designed so that effective cooling and solidification occurs preventing the metal from entering the vacuum valve. If no vacuum is used then adequate venting along with proper gating and runner design can eliminate gas porosity. Venting helps eliminate entrapped air by allowing the gas to have an outlet during the fill. Venting is the easiest and least expensive method to use. The amount of venting through the sleeve, ejector pins, parting line, and vacuum valves are considered while designing vents.
4. 研究概要:
研究テーマの背景:
高圧ダイカスト中の空気巻き込みは気孔を発生させ、最終製品の機械的特性を低下させる。ベンティングはこの空気を除去するための最も一般的で費用対効果の高い方法だが、金型内の様々なオリフィスを通過する流れ損失を明確に理解しなければ、効果的なベンティングシステムを設計することは困難である。
先行研究の状況:
流れ損失をモデル化する先行研究では、Darcy-friction factorやMoody's diagramのような手法が用いられてきたが、これらは複雑で、ダイカスト環境におけるダイナミクスを完全には捉えきれていない可能性がある。
研究の目的:
本研究は、市販のCFDソフトウェア(FLOW-3D®)を用いて、HPDC金型におけるエアベント、エジェクタピン、および残留リークからの累積的な流れ損失をモデル化し、校正するための実用的で効果的な方法を実証することを目的とした。
中核的研究内容:
研究の中核は、様々なベンティング条件下で市販の金型を用いて物理的な「空打ち」射出実験を行うことであった。キャビティ内部の圧力を測定し、それをCFDシミュレーションの校正のための基準(ベンチマーク)として使用した。シミュレーションされた圧力曲線を実験データと一致させることにより、研究者たちはベンティングシステム全体の正確な累積損失係数を決定することができた。
5. 研究方法
研究設計:
本研究は、CFDシミュレーション結果を物理的な実験データと比較する比較研究設計を採用した。モーターエンドヘッド金型を用いて溶湯なしで射出実験を行った。実験構成には、すべて開放、真空バルブ閉鎖、パーティングライン閉鎖、エジェクタピンとパーティングライン閉鎖、すべて閉鎖が含まれた。
データ収集と分析方法:
金型に圧力変換器を設置し、各実験実行について時間経過に伴う圧力を記録した。これらの圧力曲線は、FLOW-3D®からのシミュレーション出力と比較された。ソフトウェアのバルブモデルは、計算結果が実験データと良好な一致を示すまで累積損失係数を調整することによって校正された。
研究テーマと範囲:
本研究は、高圧ダイカスト金型における空気の流れ損失の特性評価に焦点を当てた。その範囲には、真空バルブ、26本のエジェクタピン、パーティングライン、およびその他の残留リークを通過する損失が含まれた。研究では、FLOW-3D®の断熱気泡モデルとバルブモデルを用いてシミュレーションを行った。
6. 主な結果:
主な結果:
- 実験データから、真空バルブが主要なベンティング経路であり、次いでエジェクタピンであることが示された。パーティングラインの漏れはごくわずかであった。
- 理論的な「すべて閉鎖」時の圧力(169 psi)と測定された実験圧力(約25 psi)との間の大きな不一致から、重大な残留リークの存在が確認された。
- 断熱気泡モデルを用いたFLOW-3D®シミュレーションは、一度校正されると、実験的な圧力曲線と優れた一致を示した。
- 具体的な累積損失係数が計算された:「真空バルブ閉鎖」ケースでは3.73e-6 m²/√(kg/m³)、 「すべて開放」ケースでは6.4e-6 m²/√(kg/m³)。
図の名称リスト (Figure Name List):
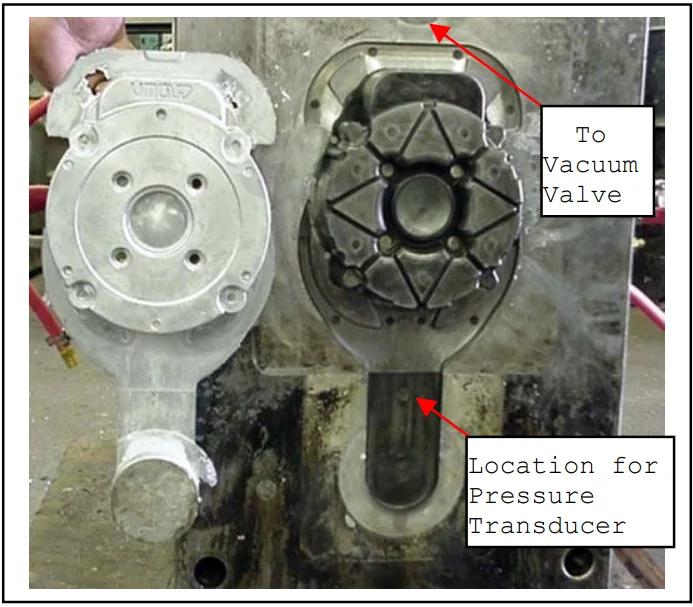
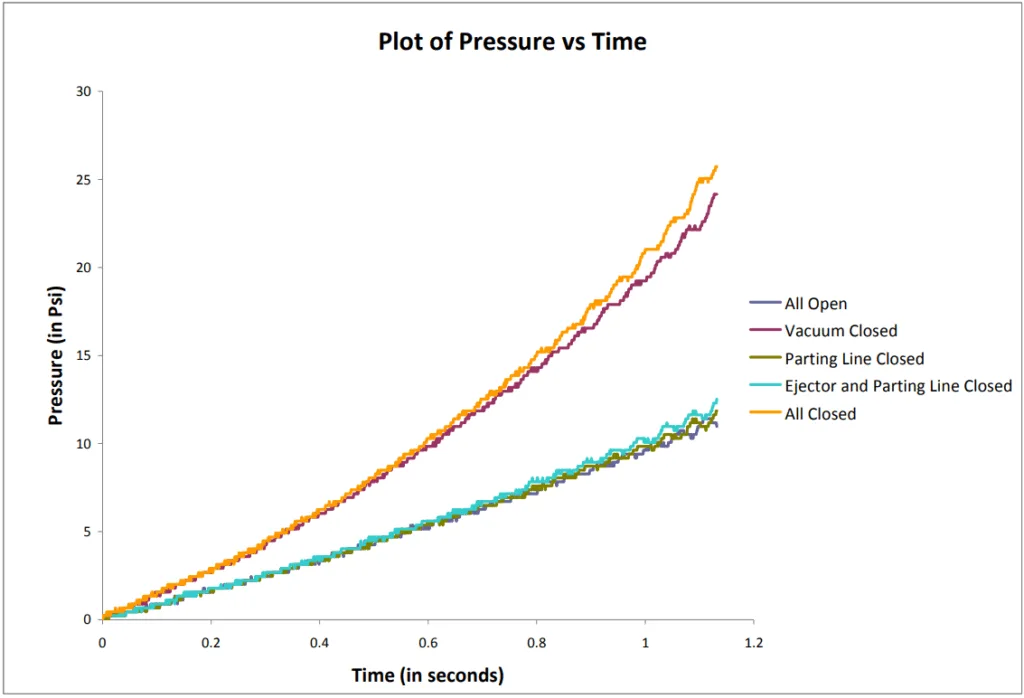
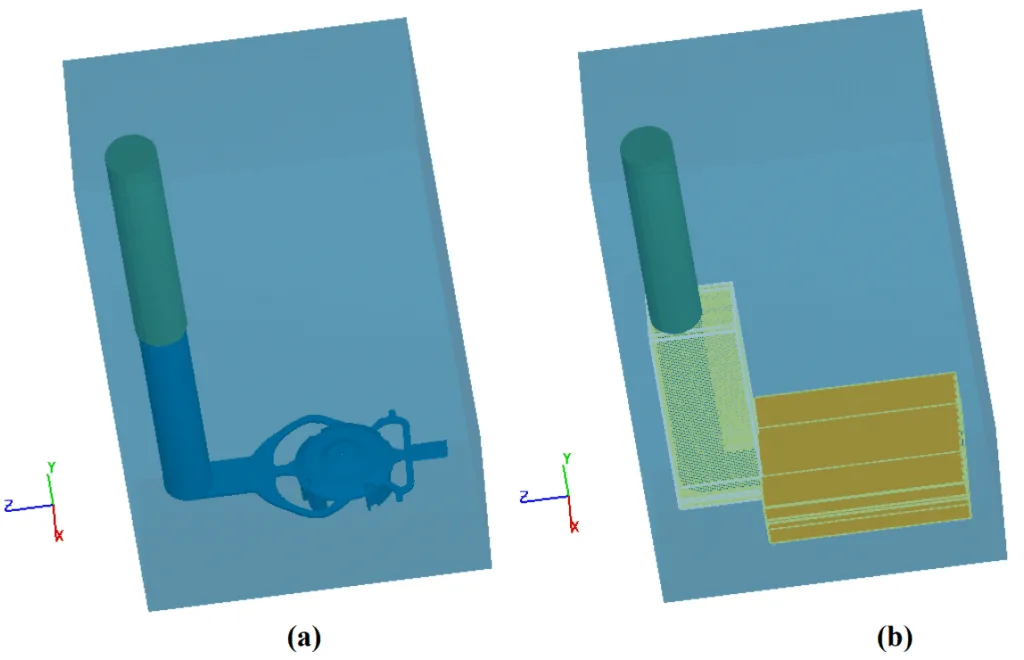
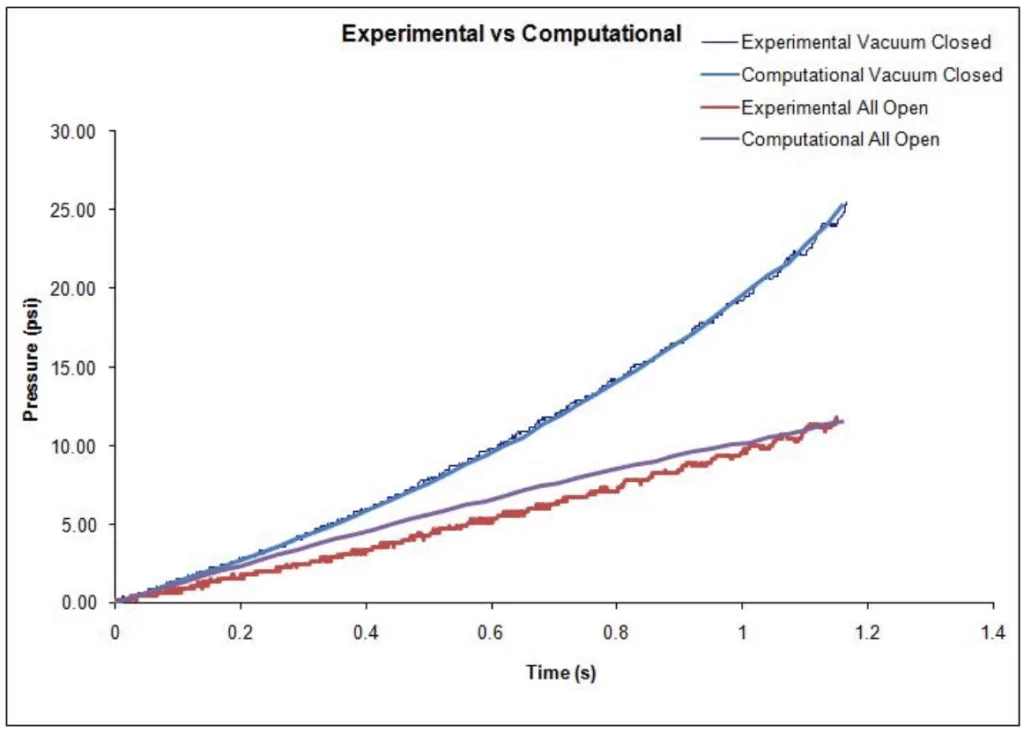
- Figure 1: Typical values of the VOF function near a moving metal front.
- Figure 2: The cast part (end head of motor) and the die.
- Figure 3: Experimental results of pressure (in Psi) plotted against time (in sec) for the dry runs.
- Figure 4: A snapshot of the geometry (a) without mesh and (b) with computational mesh.
- Figure 5: Pressure curves from the "All Closed" for 1-compressible and 2-adiabatic simulations.
- Figure 6: Comparison of experimental and computational results.
7. 結論 (Conclusion):
Many authors have tried to model the flow losses at vents using the Darcy-friction factor and Moody’s diagram and Fanno flows where compressibility effects are taken into account. We have shown that these losses can be modeled through the use of simple adiabatic bubble and valve models in FLOW-3D®. In future this model needs to be used in conjunction with an actual metal fill in order to study the porosity in the part due to improper venting. The valve model also needs to be used in a broader framework which looks at compressible flow losses occurring at vents under certain conditions as well as the effect of different geometries, and gas densities on the cumulative loss coefficient.
8. 参考文献 (References):
- [1] White, F.M., Fluid Mechanics, 4th ed., p 256, John Fellows Publishing Co., New York, NY (1940)
- [2] Flow of Fluids Through Valves, Fittings, and Pipe, Crane Technical Paper No. 410, Joliet, IL: Crane Co., 1988.
- [3] C.W. Hirt and B.D. Nichols, “Volume-of-Fluid (VOF) Method for the Dynamics of. Free Boundaries,” J. Comp. Phys., 39, 1981, pp. 201-225.
- [4] FLOW-3D® v 9.4 Manual
- [5] Mold Filling Simulation of High Pressure Die Casting for Predicting Gas Porosity, Modeling of Casting, Welding, and Advanced Solidification Processes X, TMS (The Mineral, Metals, & Materials Society), 2003, pp. 335
- [6] Modeling of Air Venting in Pressure Die Casting Process, Nouri-Borujerdi, A., Goldak, J.A., AD, Journal of Manufacturing and Science and Engineering, ASME, 2004
専門家Q&A:トップ質問への回答
Q1:HPDCにおいて、流れ損失を正確にモデル化することがなぜそれほど重要なのですか?
A1: 流れ損失を正確にモデル化することは、制御されていない空気の巻き込みがガス気孔の主な原因であるため、非常に重要です。論文の序論で述べられているように、気孔は降伏強度や延性といった基本的な機械的特性を低下させ、部品の不良やスクラップの増加につながります。
Q2:ベントは正しく設計されているように見えますが、それでもガス気孔が発生します。原因は何でしょうか?
A2: 本研究は、ショットスリーブなどを通る「残留リーク」が、非常に重要でありながら見過ごされがちなベンティング要因であることを強調しています。研究では、完全に密閉された金型において、理論と現実の間に140 psi以上の圧力差があることが判明し、これらのリークが相当なものであることを証明しています。あなたの問題は、主要なベントではなく、これらの定量化されていないリーク経路にあるのかもしれません(図3と図5の比較)。
Q3:エジェクタピンと専用ベントから、それぞれどのくらいのベンティング効果が得られるかを定量化できますか?
A3: はい、可能です。本論文の方法論は明確なテンプレートを提供します。一度に一つのベンティングシステムを閉鎖する逐次的な「空打ち」を実施する(例:実行1:すべて開放、実行2:専用ベント閉鎖)ことで、図3で行われたように圧力変換器を用いて圧力曲線の変化を測定できます。これにより、各コンポーネントのベンティング効果を分離し、定量化することができます。
Q4:「断熱気泡モデル」とは何で、なぜ有用なのですか?
A4: 断熱気泡モデルはFLOW-3D®の機能の一つで、圧縮性ガスの複雑な物理現象を、非常に効率的で正確な計算に単純化します。図5が示すように、その結果はより複雑な圧縮性ガスシミュレーションと「優れた一致」を示しました。これにより、充填シミュレーション中の金型キャビティ内の圧力上昇を正確に計算するための、強力かつ実用的なツールとなります。
Q5:新しい金型の鋼材を加工する前に、シミュレーションを使ってベンティング設計を最適化するにはどうすればよいですか?
A5: 本研究は、CFDモデルを校正することで、金型全体のベンティングシステムを表す単一の「累積損失係数」を決定できることを示しています。論文の結論で述べられているように、これによりFLOW-3D®のようなツールを使用して、金型を製造する前に様々なベントサイズ、オーバーフロー設計、配置をデジタルでテスト・比較し、適切な空気排出を確保することができます。これにより、時間とコストを大幅に節約できます。
Q6:この研究で参考にできる主要な数値結果は何でしたか?
A6: この研究では、2つの主要な校正値が算出されました。エジェクタピンと残留リークのみを介したベンティング(「真空バルブ閉鎖」)の累積損失係数は3.73e-6 m²/√(kg/m³)でした。システム全体でベンティングした場合(「すべて開放」)の係数は6.4e-6 m²/√(kg/m³)でした。これらは図6に示されるように、シミュレーションを実世界のデータと一致させることで導出されました。
結論と次のステップ
本研究は、HPDCのベント設計において直感を超えるための貴重なロードマップを提供します。対象を絞った物理実験と校正済みのCFDシミュレーションを組み合わせることで、金型内の空気の流れ経路の複雑なネットワークを定量化し、最適化することが可能です。この知見は、部品品質の向上、気孔関連の欠陥削減、そして初日から生産を最適化するための、明確でデータに基づいた道筋を示しています。
CASTMANでは、お客様の最も困難なダイカストの問題を解決するために、最新の業界研究を応用することに専念しています。本稿で議論された課題が貴社の事業目標と共鳴するものであれば、ぜひ当社の技術チームにご連絡いただき、これらの先進的な原理を貴社の部品にどのように適用できるかご相談ください。
著作権
- 本資料は、「M.C. Carter, S. Palit, and M. Littler」による論文に基づいています。論文名:「Characterizing Flow Losses Occurring in Air Vents and Ejector Pins in High Pressure Die Castings」。
- 論文の出典:NADCA CastExpo'10 Conference Proceedings.
本資料は情報提供のみを目的としています。無断での商業利用は禁じられています。Copyright © 2025 CASTMAN. All rights reserved.