論文概要:
この論文概要は、"[Clinching of Heated Aluminum Die Casting]" を "WGP 2021, LNPE (Lecture Notes in Production Engineering)" にて発表された論文に基づいて作成されています。
1. 概要:
- タイトル: 加熱アルミニウムダイカストのクリンチング (Clinching of Heated Aluminum Die Casting)
- 著者: S. Yarcu, S. Huebner, D. Yilkiran, K. Brunotte, B.-A. Behrens, T. Schuchardt, S. Mueller, K. Dilger
- 発表年: 2022年
- 掲載ジャーナル/学会誌: WGP 2021, LNPE (Lecture Notes in Production Engineering) に掲載, Springer Nature Switzerland AG
- キーワード: ジョイントクリンチング, ダイカスト, 加熱クリンチング, テンパードクリンチング
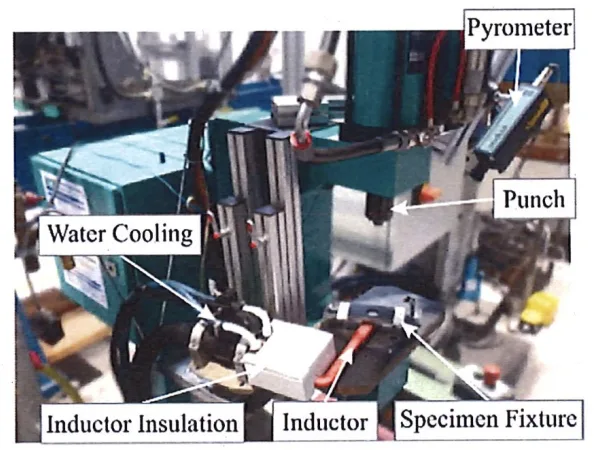
2. 研究背景:
現代の自動車車体製造分野では、マルチマテリアルボディ (MMB) の利用がますます増加しています。このアプローチは、軽量構造、コスト最適化、および剛性などの厳しい性能要件という、相反する要求に対応するものです。しかし、異種材料間の電気化学的ポテンシャル、機械的特性、および熱膨張係数の固有の差異は、接合技術と腐食対策において重大な課題をもたらします。車体構造で一般的に使用される従来の抵抗スポット溶接などの接合方法では、アルミニウムと鋼の接合には、それらの異なる熱特性のためにしばしば不適切です。クリンチングは、このような用途に適した代替手段として浮上しています。
しかし、アルミニウムダイカスト合金は、その固有の脆さのために、自然硬化状態ではクリンチング能力が限られています。先行研究では、これらの合金を初期状態で直接クリンチングすると、ジョイント表面に亀裂が入りやすいことが示されています。既存の研究では、アルミニウムダイカストの代替接合方法として、セルフピアスリベットや摩擦攪拌接合などが検討されてきました。Jäckelら [5] は、セルフピアスリベットについて調査し、最適化された工具形状によって亀裂を抑制しましたが、インターロックの減少を招きました。Neuserら [6] は、さまざまな工具構成を用いたセルフピアスリベットをさらに調査し、フラットダイを使用することで、ジョイント強度を損なうことなく亀裂を低減できることを示しました。Hovanskiら [7] は、摩擦攪拌接合を検討し、ダイカストジョイントの曲げや材料の脆さに起因する早期破損に対する感受性を強調しました。
これらの制約は、特にMMB用途における堅牢で亀裂のないジョイント形成のために、アルミニウムダイカスト合金のクリンチング性を向上させる革新的なアプローチの必要性を強調しています。
3. 研究目的と研究課題:
- 研究目的:
本研究の主な目的は、シートメタルと接合する際のアルミニウムダイカスト合金のクリンチング性能を向上させることです。これは、プロセス安全で信頼性の高いクリンチングを目指し、制御された加熱戦略による局所的なアニール (焼きなまし) を組み込むことによって達成されます。本研究では、3つの異なる加熱方法がクリンチングジョイントの特性に及ぼす影響を具体的に調査します。 - 主な研究課題:
本研究では、以下の主要な研究課題に取り組むことを目的としています。- 加熱板、抵抗加熱、誘導加熱という異なる加熱方法が、アルミニウムダイカスト合金のクリンチングジョイントの生成と品質にどのように影響するか?
- これらの加熱方法が、プロセス時間、接合点の幾何学的属性、およびクリンチングジョイントの結合強度などの重要なプロセスパラメータに及ぼす比較効果は何か?
- 調査対象の加熱方法の中で、どの方法と関連するプロセスパラメータが、アルミニウムダイカスト部品の堅牢かつ効率的なクリンチングを達成するために最も有望な性能を示すか?
- 研究仮説:
正式な仮説としては明示されていませんが、本研究は、クリンチング前に加熱工程を組み込むことで、アルミニウムダイカスト合金の脆性を緩和し、室温クリンチングと比較して、インターロックと結合強度が向上した亀裂のないジョイントの形成が可能になるという理解に基づいています。さらに、異なる加熱方法は、これらの改善を達成する上でさまざまな程度の有効性を示し、ジョイント品質とプロセス効率の両方に影響を与えることが予想されます。
4. 研究方法
- 研究デザイン:
本研究では、3つの異なる加熱方法をクリンチングプロセスと組み合わせて評価および比較するために、実験計画法を採用しました。この研究では、アルミニウムダイカスト合金とアルミニウムシートの接合に焦点を当て、加熱方法を系統的に変化させながら、一貫したクリンチングパラメータを維持しました。 - データ収集方法:
クリンチングジョイントを包括的に評価するために、以下のデータ収集方法を利用しました。- 表面分析: クリンチングジョイント周辺の表面亀裂の有無と程度を評価するために、目視検査と写真記録を実施しました。
- 幾何学的寸法測定: クリンチングジョイントの断面の金属組織顕微鏡写真を分析して、ネック厚さ (tn)、インターロック (f)、および底面厚さ (tb1, tb2) などの主要な幾何学的パラメータを定量化しました。
- 結合強度試験: DIN EN ISO 14273 および DIN EN ISO 14272 [10] にそれぞれ準拠して実施されたヘッド引張試験およびせん断試験を実施して、クリンチングジョイントの機械的強度を測定しました。
- 分析方法:
収集されたデータは、定性的および定量的な方法を使用して分析されました。- 定性分析: 表面分析データを定性的に評価して、各加熱方法および条件における亀裂の有無を判断しました。
- 定量分析: 幾何学的測定値を統計的に分析して、室温クリンチングジョイントと比較した特性寸法のパーセント変化を決定しました。結合強度データを異なる加熱方法および条件間で比較して、ジョイント性能への影響を評価しました。
- 研究対象と範囲:
本研究では、以下の材料と実験パラメータに焦点を当てました。- 材料:
- パンチ側シート: アルミニウムシート EN AW5182、厚さ 1.5 mm。
- ダイ側シート: アルミニウムダイカスト合金 AlSi10MnMg、厚さ 3 mm、自然硬化状態 F で試験。
- クリンチング装置: TOX CEJ 75.200 クリンチングプレス、クローズドクリンチングダイシステム付き。
- 加熱方法:
- 誘導加熱: Eldec MFG 18 ジェネレーター (18 kW) に接続されたリングインダクター。
- 抵抗加熱: 50 kW 変圧器に接続された銅電極 (CuBe2)。
- 加熱板: HOTSET RR508/1 温度制御ユニット (22 kW) に接続された 4 つの加熱カートリッジを備えた加熱板。
- 目標温度: 加熱クリンチング実験では 250 °C。
- 材料:
5. 主な研究結果:
- 主な研究結果:
実験的調査により、アルミニウムダイカストクリンチングへの異なる加熱方法の適用に関して、以下の主要な結果が得られました。- 誘導加熱: 誘導加熱を使用し、加熱時間 10 秒、ジェネレーター出力 9 kW (出力 50%) で、亀裂のないクリンチングポイントが一貫して達成されました。
- 抵抗加熱: 最初の抵抗加熱試験では、ダイの急速加熱 (7 秒) により亀裂が発生しました。プロセスを変更して、クリンチングダイのより遅く、制御された加熱を 45 秒かけて 400 °C まで行うことで、亀裂の発生が大幅に減少しました。
- 加熱板: 加熱板を使用すると、90 秒の長い保持時間を使用した場合に、亀裂が最小限に抑えられたクリンチングジョイントが得られました。ただし、この方法で完全に亀裂のないジョイントを達成するには、これらの長い保持時間が必要でした。
- 幾何学的分析: 室温クリンチングと比較して、加熱クリンチングはジョイントの形状を明らかに改善しました。誘導加熱はインターロック (f) を 15% 増加させましたが、加熱板法ではインターロックが 21% 増加しました。ネック厚さ (tn) は、すべての加熱方法で比較的一定のままでした。部分的な底面厚さの測定値は、加熱クリンチングの場合、パンチ側 (tb1) で減少し、ダイ側 (tb2) で増加することを示しました。
- 結合強度: 加熱板クリンチングは、ヘッド引張試験で最高のジョイント強度を示しました。誘導加熱法と抵抗加熱法は、室温クリンチングと比較して同程度のジョイント強度向上を示しましたが、加熱板法よりも低くなりました。
- 統計的/定性的な分析結果:
- 表面分析 (図 8): 目視検査により、室温クリンチングジョイントと急速抵抗加熱で製造されたジョイントに亀裂が存在することが確認されました。誘導加熱法と加熱板法は、亀裂を効果的に低減または排除しました。
- 幾何学的数値 (表 1): 表 1 は、室温クリンチングと比較した各加熱方法の幾何学的パラメータ (tn, f, tb1, tb2) のパーセント変化を定量化し、加熱クリンチングによるインターロックの増加を強調しています。
- ヘッド引張強度 (図 9): 図 9 は、各加熱方法のヘッド引張強度をグラフで示しており、加熱板クリンチングの優れた性能と、誘導加熱および抵抗加熱で達成された同程度の改善を示しています。
- データ解釈:
結果は、加熱クリンチングが、加熱方法に関係なく、アルミニウムダイカスト合金のクリンチング性を向上させることを示しています。加熱クリンチングジョイントで観察されたインターロックの増加は、結合強度の向上に直接的に貢献しています。加熱板法は、最高のジョイント強度をもたらしますが、プロセス時間が長くなるという欠点があります。誘導加熱は、プロセス速度とジョイント品質のバランスが取れた有望な妥協案として浮上しており、加熱板と比較して大幅に加熱時間を短縮しながら、亀裂のないジョイントを達成しています。より遅く、制御された抵抗加熱法も亀裂低減の可能性を示していますが、正確なプロセス制御が必要です。 - 図のリスト:
- 図 1. Audi TT Coupé を例としたアルミニウムを多用した複合構造 [3]。
- 図 2. TOX 社のクリンチングプレス (左) と使用したクリンチング工具システム (右)。
- 図 3. クリンチングポイントの幾何学的寸法と関連する特性値 [9]
- 図 4. インダクターの概略磁力線と工具システムの配置
- 図 5. 誘導加熱の実験セットアップ。
- 図 6. a) 抵抗加熱セットアップの CAD 設計 b) 抵抗加熱試験の実験セットアップ。
- 図 7 a) 加熱板セットアップの詳細図 b) 実験セットアップの概要。
- 図 8. 室温および加熱クリンチング後の3つの調査対象加熱方法の表面分析の結果。
- 図 9. 室温および加熱クリンチングにおけるクリンチングジョイントのヘッド引張強度 (異なる加熱方法)。
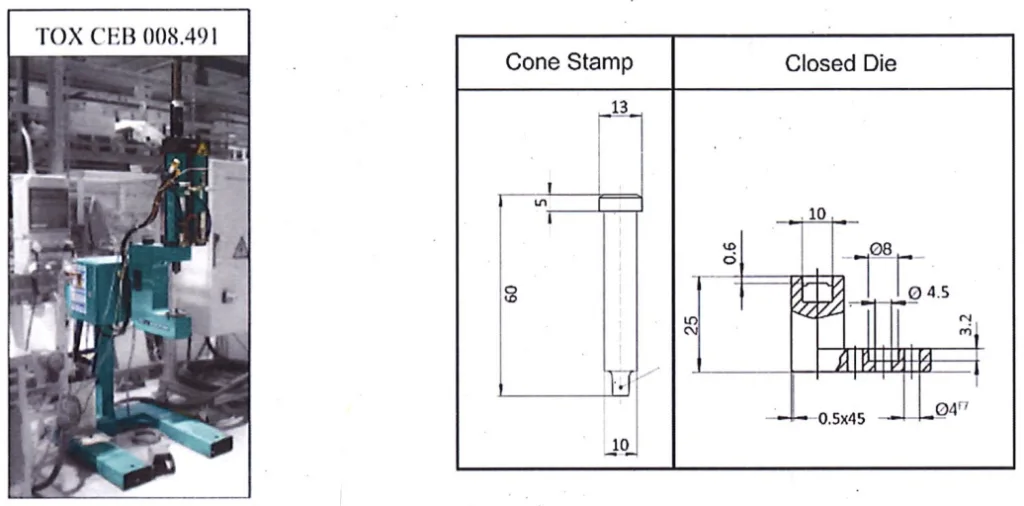
![Fig. 3. Geometric dimensions and relevant characteristic values of a clinching point [9]](https://castman.co.kr/wp-content/uploads/image-342-1024x330.webp)
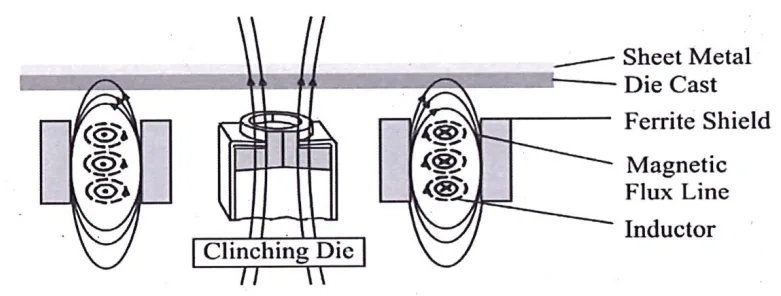
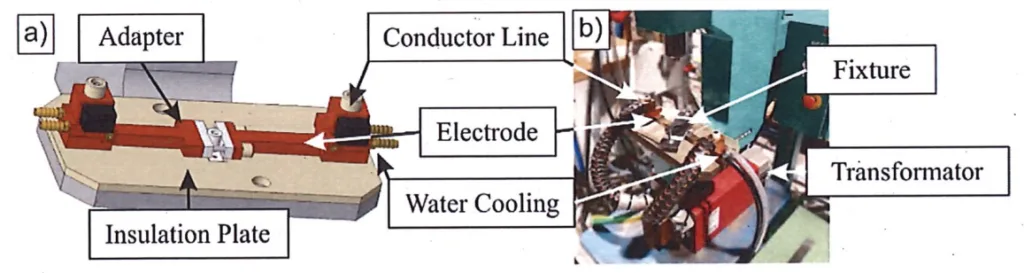
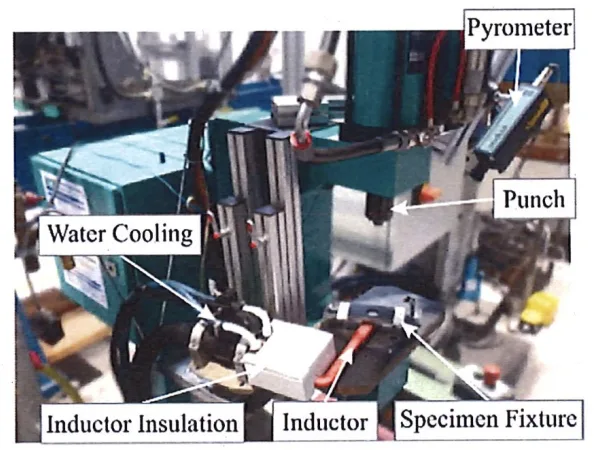
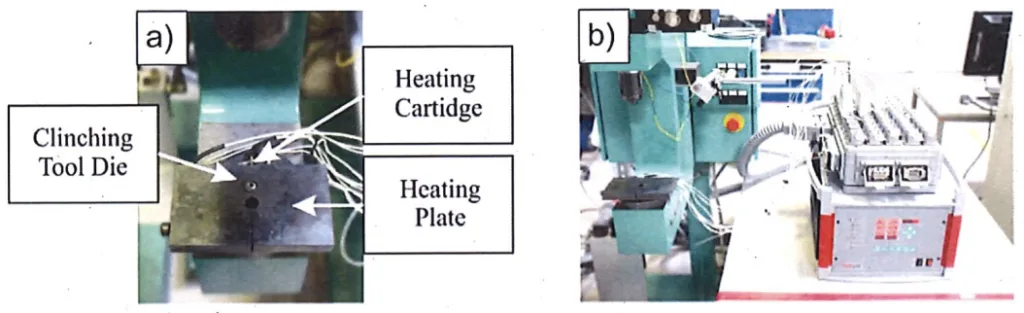
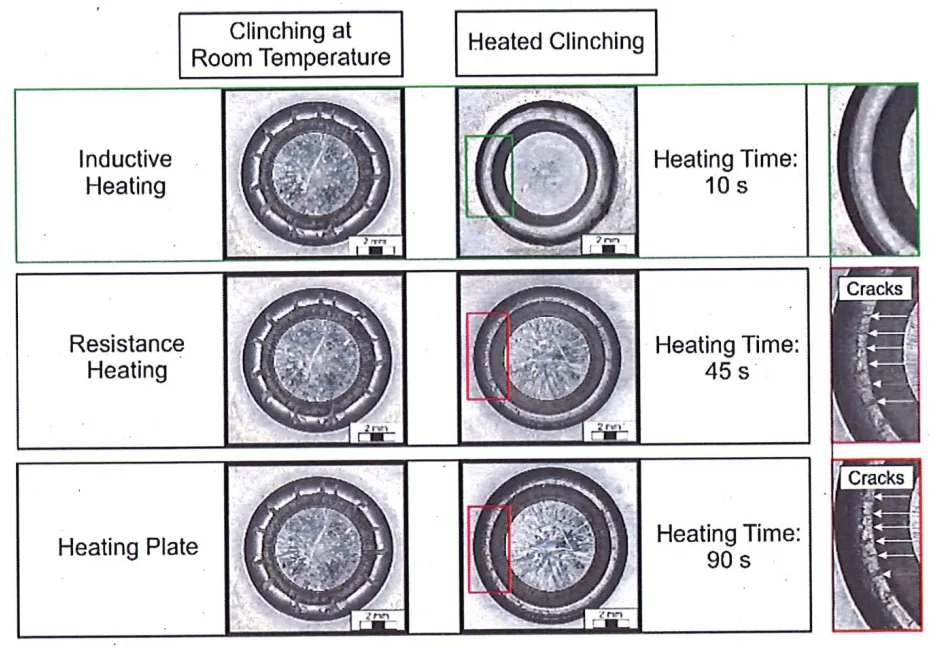
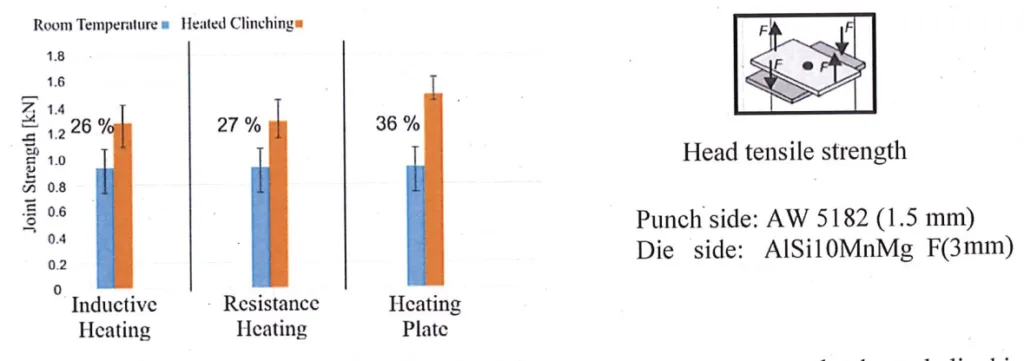
6. 結論と考察:
- 主な結果の要約:
本研究は、加熱工程をクリンチングプロセスに組み込むことで、脆性アルミニウムダイカスト合金の亀裂発生を効果的に抑制できることを決定的に示しています。調査対象の3つの加熱方法 (誘導加熱、抵抗加熱、加熱板) はすべて、亀裂を低減することに成功しました。誘導加熱は、短い加熱サイクルで亀裂のないジョイントを達成できる能力で際立っており、加熱板クリンチングは最高のジョイント強度を提供しますが、プロセス時間が大幅に長くなります。最適化されたより遅い加熱パラメータを備えた抵抗加熱も、亀裂低減の有望性を示しています。 - 研究の学術的意義:
本研究は、軽量自動車設計の文脈におけるマルチマテリアル構造の接合技術の理解に大きく貢献しています。特にアルミニウムダイカスト合金のような困難な材料の接合に対する加熱クリンチングの応用に関する貴重な洞察を提供します。異なる加熱方法の比較分析は、望ましいジョイント品質とプロセス効率に基づいて適切な加熱戦略を選択するための堅牢なフレームワークを提供します。 - 実用的な意義:
本研究の知見は、特に自動車製造における産業用途に大きな実用的な意義を持ちます。誘導加熱は、その迅速な加熱能力と亀裂のないジョイントを製造する能力により、連続生産で加熱クリンチングを実装するための実行可能で効率的な方法を提供します。本研究は、アルミニウムダイカスト部品の接合技術としてのクリンチングの適用範囲を拡大し、軽量マルチマテリアル設計の利用増加を促進します。 - 研究の限界:
本研究は、特定の材料 (EN AW5182 および AlSi10MnMg) とクリンチングパラメータに限定されています。より広範囲のアルミニウムダイカスト合金およびシートメタルに対して、加熱パラメータとクリンチングプロセスを最適化するために、さらなる研究が必要です。抵抗加熱法は、その堅牢性とプロセス効率を向上させるために、さらなる改良が必要です。
7. 今後のフォローアップ研究:
- フォローアップ研究の方向性:
今後の研究は、アルミニウムダイカストの加熱クリンチングの応用をさらに進めるために、以下の分野に焦点を当てる必要があります。- 誘導加熱の最適化: より高いジェネレーター出力と最適化されたインダクター設計を組み合わせて使用し、誘導加熱の加熱時間をさらに短縮しながら、クリンチング工具の熱管理を確保することの調査。
- 抵抗加熱の改良: 高度なフィードバック制御システムと電極設計を通じて、亀裂制御と加熱サイクルを高速化するための抵抗加熱プロセスのさらなる最適化。
- 構造性能評価: 加熱クリンチングジョイントの亀裂低減効果と長期性能をさらに検証するために、疲労および耐久性評価を含む包括的な構造試験の実施。
- さらなる探求が必要な分野:
さらなる探求には、以下が含まれる必要があります。- 材料パラメータの最適化: より広範囲のアルミニウムダイカスト合金とシートメタルの組み合わせに対する最適な加熱パラメータとクリンチングパラメータの体系的な調査。
- 長期的なジョイント性能: さまざまな環境および負荷条件下での加熱クリンチングジョイントの長期耐久性、耐食性、および疲労性能の評価。
- 費用対効果分析: 装置コスト、エネルギー消費量、およびプロセススループットなどの要因を考慮した、産業実装のための異なる加熱方法の徹底的な費用対効果分析の実施。
8. 参考文献:
- [1] Hirsch, J.: Aluminium in innovative light-weight car design. Mater. Trans. 52(5), 818–824 (2011)
- [2] Taub, A.L., Krajewski, P.E., Luo, A.A., et al.: The evolution of technology for materials processing over the last 50 years: the automotive example. JOM 59(2), 48–57 (2007)
- [3] Mueller, S.: Flexibel einsetzbare Fügetechnologien zur Realisierung unterschiedlicher Karosseriekonzepte, Tagungsband des 7. Fügetechnischen Gemeinschaftskolloquiums Dresden (2017)
- [4] Behrens, B.-A., et al.: FEA-based optimisation of a clinching process with an open multiple-part die aimed at damage minimisation in CR240BH-AlSi10MnMg joints. Mater. Sci. Eng. Chem. 21, 04009 (2015)
- [5] Neuser, M., et al.: Joining suitability of cast aluminium for self-piercing riveting. IOP Conf. Ser. Mater. Sci. Eng. 1157, 012005 (2021)
- [6] Jäckel, M., et al.: Mechanical joining of materials with limited ductility: analysis of process-induced defects. In: Proceedings of the 20th International ESAFORM Conference on Material Forming, AIP Conference Proceedings, vol. 1896, pp. 110009-1–110009–6 (2017)
- [7] Hovanski, Y., Upadyay, P., Kleinbaum, S., Carlson, B., Boettcher, E., Ruokolainen, R.: Enabling dissimilar material joining using friction stir scribe technology. JOM 69(6), 1060–1064 (2017)
- [8] Varis, J.: Ensuring the integrity in clinching process. J. Mater. Process. Technol. 174, 277–285 (2006)
- [9] Xiaocong, H.: Clinching for sheet materials. Sci. Technol. Adv. Mater. 18, 381-405 (2017)
- [10] Varis, J.: The suitability of clinching as a joining method for high-strength structural steel. J. Mater. Process. Technol. 132, 242–249 (2003)
9. 著作権:
- この資料は、"[S. Yarcu et al.]" の論文: "[Clinching of Heated Aluminum Die Casting]" に基づいています。
- 論文ソース: https://doi.org/10.1007/978-3-030-78424-9_10
この資料は上記の論文に基づいて要約されたものであり、商業目的での無断使用は禁止されています。
Copyright © 2025 CASTMAN. All rights reserved.