本論文要約は、['Journal of Materials Engineering and Performance']誌に掲載された論文 ['Low Solution Temperature Heat Treatment of AlSi9Cu3(Fe) High-Pressure Die-Casting Actual Automotive Components'] に基づいて作成されました。
1. 概要:
- タイトル: 低温溶体化熱処理を施したAlSi9Cu3(Fe)高圧ダイカスト自動車部品 ['Low Solution Temperature Heat Treatment of AlSi9Cu3(Fe) High-Pressure Die-Casting Actual Automotive Components']
- 著者: Silvia Cecchel, Andrea Panvini, Giovanna Cornacchia
- 発行年: 2018年
- 発行学術雑誌/学会: Journal of Materials Engineering and Performance, ASM International
- キーワード: ブリスター, 熱処理, 高圧ダイカスト, 非鉄合金, 気孔率, 二次アルミニウム合金


2. 抄録または序論
通常、高圧ダイカスト (HPDC) 部品は、表面仕上げとして許容できないブリスターの発生や機械的特性の低下を招くため、高温での熱処理を行うことができません。この背景から、本論文の目的は、HPDC AlSi9Cu3 合金に対して、特殊な低温溶体化 T6 熱処理の有効性を分析することでした。ブリスターの発生を防ぐために、非常に低い溶体化温度 (< 450 °C、165 °C の時効処理後) を、工業的応用を可能にする一般的な時間 (1 ~ 16 時間) と組み合わせて適用しました。一般的な製造で遭遇する典型的な欠陥を評価するために、実際の鋳造品から採取したサンプルに対して処理を実施しました。特性は、外観検査、微細組織観察、画像解析、硬さ、引張試験、および破面解析によって分析しました。その結果、AlSi9Cu3 合金において、顕著なブリスターリングなしに強化効果を得るために、T6 熱処理において数時間、450 °C 未満の溶体化温度を使用することが可能であることが示されました。最適な特性の組み合わせは、430 °C で 4 時間の溶体化処理と、それに続く 165 °C で 8 時間の時効処理によって得られ、降伏強度が約 50 MPa 増加、延性が増加し、最高の品質指数値が得られました。
3. 研究背景:
研究テーマの背景:
輸送は地球規模の大気質に大きな影響を与えているため、自動車の排出量削減は主要な関心事です。この文脈において、達成可能な主要な解決策の 1 つは、輸送車両を軽量化するために、アルミニウム合金 (Ref 1, 2) のような低密度材料を使用することです。実際、現在、従来の鋼鉄や鋳鉄をアルミニウム合金に置き換える傾向があります (Ref 3-5)。この文脈において、既存の合金を常に最適化する必要があることに留意することは重要です。なぜなら、すべての用途の要件を満たす合金を見つけることはしばしば困難だからです。さらに、化学組成は、広範囲の組成範囲で多様な特性を示す特定の合金を選択する上で重要な要素の 1 つです (Ref 6, 7)。製造の観点から、高圧ダイカスト (HPDC) は、高い生産性 (Ref 8, 9) のため、軽合金を大量生産する最も広く使用されている方法です。アルミニウム合金にとって最も汎用性の高い技術として認められている利点にもかかわらず、HPDC には、金属ダイの充填速度と急速な凝固が相まって、鋳造品に高圧で空気が閉じ込められるという欠点があります (Ref 10)。この高レベルの気孔率が、ダイカスト部品に熱処理を実行できない理由です (Ref 11)。
既存研究の現状:
HPDC の欠点を克服するために、半凝固金属およびレオキャスティングプロセスのような有望な技術に関するさまざまな研究が、製造におけるより高い健全性を提供するために行われています (Ref 12, 13)。機械的および構造的な観点からは、重力鋳造技術は優れた性能を保証しますが、製造サイクルの遅さと、潜在的な軽量化を制限するより厚い部品厚さの要件のため、大量生産には適していません (Ref 14-19)。今日、HPDC 技術は、品質とコストの間の最良の妥協点を提供するため、依然として最も広く使用されています。HPDC 部品の最大の不都合は、高温での熱処理を実行することの複雑さです。これは、引張挙動を低下させる表面ブリスターリング (高圧空気の閉じ込めによって発生) の形成によるものです (Ref 20)。最近、真空を追加する従来の HPDC プロセスのアップグレードが開発されました。この新しい技術は、ガス気孔率を最小限に抑え (Ref 21)、鋳造品の最終品質を大幅に向上させます。非常に重要な側面は、ガス含有量が少ないおかげで、真空ダイカスト部品を熱処理できる可能性があることです (Ref 21)。一方、真空のサポートなしに HPDC 技術で二次合金の高い機械的特性を達成することは、確かに、より手頃なソリューションにつながるでしょう。
研究の必要性:
実際、二次 (スクラップから製造) AlSi9CuX 合金は、良好な機械的特性と高温での挙動により、リサイクルアルミニウムの含有量が多いにもかかわらず (Ref 22, 23)、シリンダーヘッドやエンジンなどの幅広い部品の製造のために輸送分野で最も多く使用されています。これらの再処理された二次アルミニウム合金が、自動車の軽量化の環境上の利点を改善し、最大化するために重要であることに注目する価値があります (Ref 24-28)。これらの合金の使用をより重い用途に拡大するためには、従来の HPDC 部品の高温熱処理の限界を克服することが大きな課題です。本研究をよりよく理解するために、このクラスの合金に関するいくつかの詳細情報を提供することが重要です。それらの機械的特性は、特に Mg および Cu 含有量の点で、使用される組成によって強く影響を受け、規格 EN 1706:1998 に準拠しています。具体的には、AlSi9Cu3 は、初晶デンドライト状 α-アルミニウムマトリックスと、共晶シリコンおよびさまざまな金属間化合物で構成されています。Al-Si 合金に銅を添加すると、熱処理性が向上し、CuAl2 相やその他の金属間化合物が形成され、鋳造部品の強度が向上します (Ref 29-31)。銅の添加は、合金の融点と共晶温度を大幅に低下させます。したがって、銅は合金の凝固範囲を拡大し (Ref 30, 32, 33)、気孔形成条件を容易にします (Ref 34)。固溶体熱処理なしの析出硬化効果は、主に鋳造後の冷却速度に依存し、肉厚や鋳造パラメータの影響を受けるため、鋳造品では異なる機械的特性が得られます (Ref 35)。一般に、同じグレードの合金で作られ、他の鋳造技術で製造された部品の場合、合金の均質化、共晶シリコンの球状化、およびマトリックス内の金属間化合物の溶解を改善するために、比較的高温での溶体化処理が採用されています (Ref 36)。β-Mg2Si や θ-Al2Cu のような粒子は、π-Al8Mg3FeSi6、Q-Al5Cu2Mg8Si6、Al15(Fe, Mn)3Si2 (Ref 36) のような他の粒子よりも容易に固溶化されます。異なる鋳造 Al-Si 合金の微細組織および機械的特性に対する熱処理中の異なるプロセスパラメータ (温度および時間) の影響は、広範囲に研究されてきました (Ref 37-42)。Cu を含まない合金と比較して、Cu を含む Al 合金は、鋳造微細組織の形態のために均質化時間が長くなることを実証する価値があります (Ref 17, 43)。そのような例のいくつかは、最近の Lumley らの研究です (Ref 10, 44-46)。彼らは、HPDC Al-Si-X 合金部品をブリスターの発生なしに熱処理できる実験室規模のプロセスパラメータ範囲を確立することに成功しました。このプロセスは、他の技術を使用して鋳造された部品に使用される温度よりも低い溶体化温度 (< 500 °C) と短い時間 (~ 15 分) を適用することで構成されています。Pabel ら (Ref 47) は、Al Si9Cu3(Fe)(Zn) 合金を研究して、異なる熱処理条件の影響を調査しました。特に、高圧ダイカストサンプルは、鋳造直後に水冷され、その後、室温または高温で保管されました。自然時効と人工時効の組み合わせもテストされました。その結果、両方の処理の最適化された組み合わせによって、改善された機械的特性を達成できることが示されています。これらの考察は、本論文の文脈に焦点を当てたものです。実際、本研究の目的は、従来の HPDC AlSi9Cu3 合金を熱処理する可能性を調査することであり、同時に実際の産業プロセスの通常の制約条件を考慮することです。このようにして考慮された主な要件は、均一なバッチ条件を確保することであり、これは鋳造工場でのより長い処理時間を意味します。特殊な T6 熱処理が開発され、AlSi9Cu3 合金において顕著なブリスターリングなしに強化効果があるかどうかが検証されました。特に、非常に低い溶体化温度 (< 450 °C、165 °C 時効後) を、工業的応用を可能にする一般的な時間 (1 ~ 16 時間) と組み合わせて適用しました。このような低温は、長時間維持しても空気気孔の膨張に影響を与えないと考えられています。さらに、低温熱処理は、HPDC 部品の加熱によって生じる他の一般的な問題である膨張や歪みを防ぎ、処理時間を延長すると、より大きな均質化と結果的により良好な時効反応が得られます。一般的な生産で遭遇する典型的な欠陥を評価するために、実際の鋳造品から採取したサンプルに対して処理を実施しました。特性は、外観検査、微細組織観察、硬さ、引張試験、および破面解析によって分析しました。
4. 研究目的および研究課題:
研究目的:
本研究の主な目的は、低温溶体化 T6 熱処理が、従来の HPDC AlSi9Cu3 合金部品の機械的特性を向上させる上で有効であるかどうかを評価することであり、特に表面ブリスターリングの軽減に焦点を当てています。
主要な研究課題:
本研究は、非常に低い溶体化温度 (< 450 °C) を、工業的に適用可能な処理時間 (1 ~ 16 時間) および後続の 165 °C 時効ステップと組み合わせることで、顕著なブリスターリングなしに AlSi9Cu3 合金で有意な強化を達成できるかどうかを中心に展開します。本研究では、機械的特性を最大化するために、これらの制約条件内で最適な溶体化温度と時間の組み合わせを調査します。
研究仮説:
中心となる仮説は、T6 熱処理において 450 °C 未満の溶体化温度を長時間使用して、AlSi9Cu3 合金において有害なブリスターリングを引き起こすことなく強化を達成することが可能であるということです。さらに、これらの低温で溶体化処理時間を延長すると、均質化が促進され、時効反応が改善され、機械的特性が向上するという仮説を立てました。
5. 研究方法:
研究デザイン:
本研究では、T6 熱処理サイクル内で溶体化処理パラメータを体系的に変化させる実験計画法を採用しました。予備的な低温溶体化処理 (< 450 °C) を、さまざまな時間 (1、2、4、8、16 時間) で実施し、硬度応答と微細組織の変化を評価しました。これらの予備的な知見に基づいて、選択された溶体化温度 (430、450、および 490 °C) と時間 (4、8、および 490 °C の場合は 0.25 時間) を、165 °C でさまざまな時間 (1、2、4、8、16 時間) の一定の人工時効処理と組み合わせた T6 熱処理のセットを設計しました。
データ収集方法:
分析用のサンプルは、二次 AlSi9Cu3 合金 (EN AC 46000) 製の実際の HPDC 自動車部品から採取しました。データ収集には、以下の方法を使用しました。
- 外観検査: 溶体化処理後のブリスターリングを検出するために、目視検査によって表面品質を評価しました。
- 微細組織観察: 光学顕微鏡を使用して、溶体化処理前後の微細組織の変化を調べ、シリコンの破砕と球状化に焦点を当てました。
- 硬さ試験: ビッカース硬さ HV60 試験を、ASTM E 18-03 手順 (Ref 48) に従って実施し、熱処理が合金の硬さに及ぼす影響を定量化しました。
- 引張試験: 円筒形ダイカスト引張試験片を、UNI EN ISO 6892-1:2009 規格に従って試験し、降伏強さ (σy)、引張強さ (σm)、および伸び (A%) を評価しました。
- 破面解析: 走査型電子顕微鏡 (SEM) を使用して、引張サンプルの破面と直交断面を調べ、破壊メカニズムと微細組織の特徴を分析しました。
- エネルギー分散型分光法 (EDS): EDS を使用した半定量化学分析を実施し、金属間化合物を特性評価しました。
- 画像解析: LAS 4.0 ソフトウェアを使用して、直交断面で金属間化合物画像解析を実施し、金属間化合物の体積、サイズ、真円度、および気孔率を定量化しました。
分析方法:
収集されたデータを分析して、異なる溶体化処理パラメータが AlSi9Cu3 合金の機械的特性と微細組織に及ぼす影響を判断しました。硬さ-時間曲線をプロットして、溶体化処理の速度論を評価しました。引張試験の結果を比較して、機械的特性の改善を評価し、品質指数 (QI) (Ref 52) を計算して、全体的な冶金学的品質を比較しました。微細組織画像と破面解析を分析して、特性の変化と微細組織の進化 (シリコンの球状化、金属間化合物相の形態変化)、気孔率の特性との相関関係を分析しました。画像解析は、金属間化合物と気孔率の特徴に関する定量的なデータを提供し、定性的な観察を裏付けました。
研究対象と範囲:
本研究は、自動車部品に一般的に使用されている二次 AlSi9Cu3 合金 (EN AC 46000) に焦点を当てました。実際の生産条件との関連性を確保するために、工業的に生産された HPDC 自動車鋳造品からサンプルを採取しました。研究の範囲は、低温溶体化 T6 熱処理と、ブリスターリングおよび機械的特性、特に降伏強さ、引張強さ、伸び、および硬さに及ぼす影響の調査に限定されました。
6. 主な研究結果:
主要な研究結果:
本研究では、450 °C 未満の溶体化温度を持つ低温溶体化 T6 熱処理を、顕著なブリスターリングを引き起こすことなく、HPDC 二次 AlSi9Cu3 合金部品に効果的に適用できることを実証しました。特定された最適な熱処理条件は、430 °C で 4 時間の溶体化処理と、それに続く 165 °C で 8 時間の時効処理でした。この処理により、降伏強度が約 50 MPa 増加、延性が 2 倍に増加、および最高の品質指数値が得られ、これは鋳造状態よりも 50% 向上したことを示しています。硬さ測定の結果、430 °C と 450 °C の両方で溶体化時間が長くなるにつれて硬さが徐々に低下し、これは漸進的な金属間化合物溶解とシリコン破砕を示唆しています。引張試験の結果、鋳造状態と比較して、すべての熱処理されたサンプルで機械的抵抗が向上し、降伏強さと引張強さは溶体化温度とともに増加しました。
提示されたデータの分析:
- 硬さ-時間曲線 (図 2 および 4): 硬さが溶体化時間の増加とともに減少することを示し、シリコンの球状化と金属間化合物の溶解を示しています。時効後に硬さが増加し、時効硬化応答を確認しました。
- 光学顕微鏡 (図 3): 熱処理後のシリコン相の破砕と球状化、および合金の均質化を含む微細組織の変化を明らかにしました。
- 引張試験曲線 (図 5): T6 処理後に引張特性が改善されたことを示し、溶体化温度によって変動がありました。
- SEM 分析 (図 6 および 7): 破面と直交断面を示し、金属間化合物相と気孔率を明らかにしました。ロゼット状の Fe-Mn 粒子が破面で観察されました (表 4)。
- EDS 分析 (表 3 および 4): 金属間化合物相の組成データを提供しました。
- 画像解析 (表 5): 金属間化合物の特徴を定量化し、溶体化温度の上昇に伴い金属間化合物の寸法と真円度が減少し、熱処理後に気孔寸法が増加することを示しました。
図のリスト:
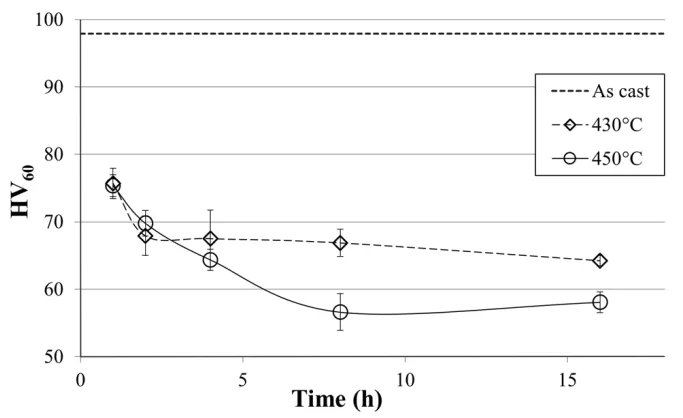
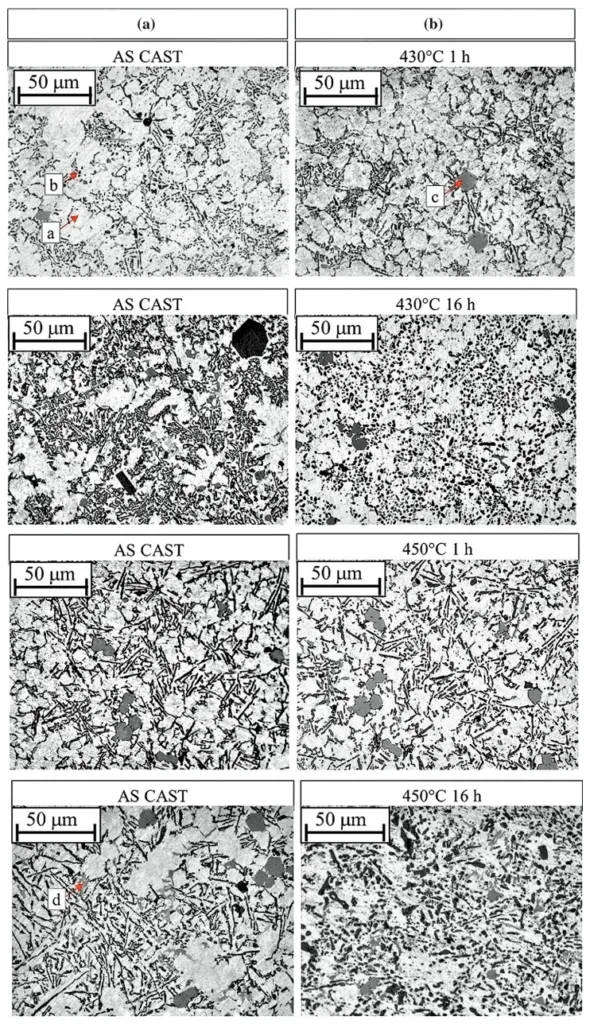
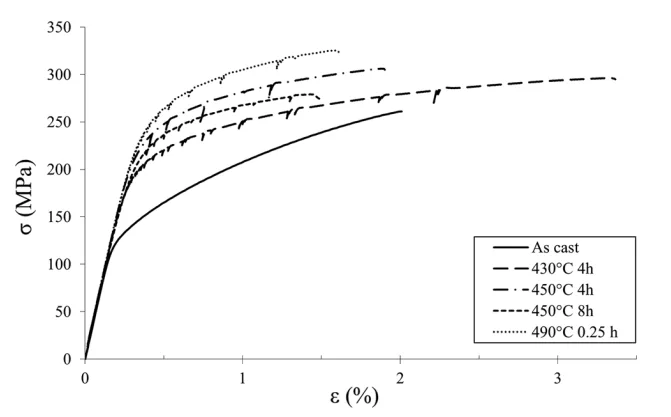
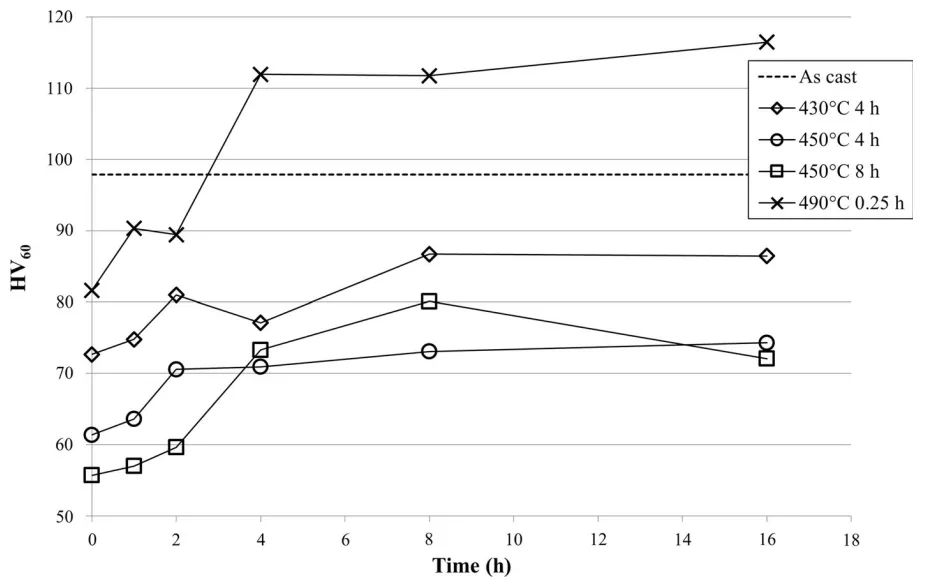
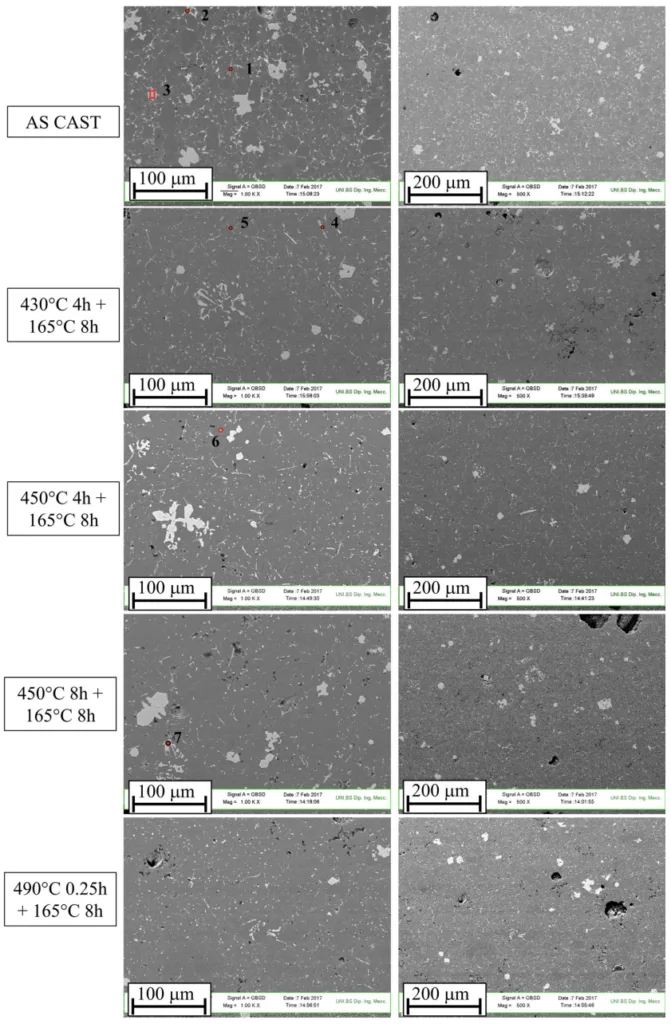
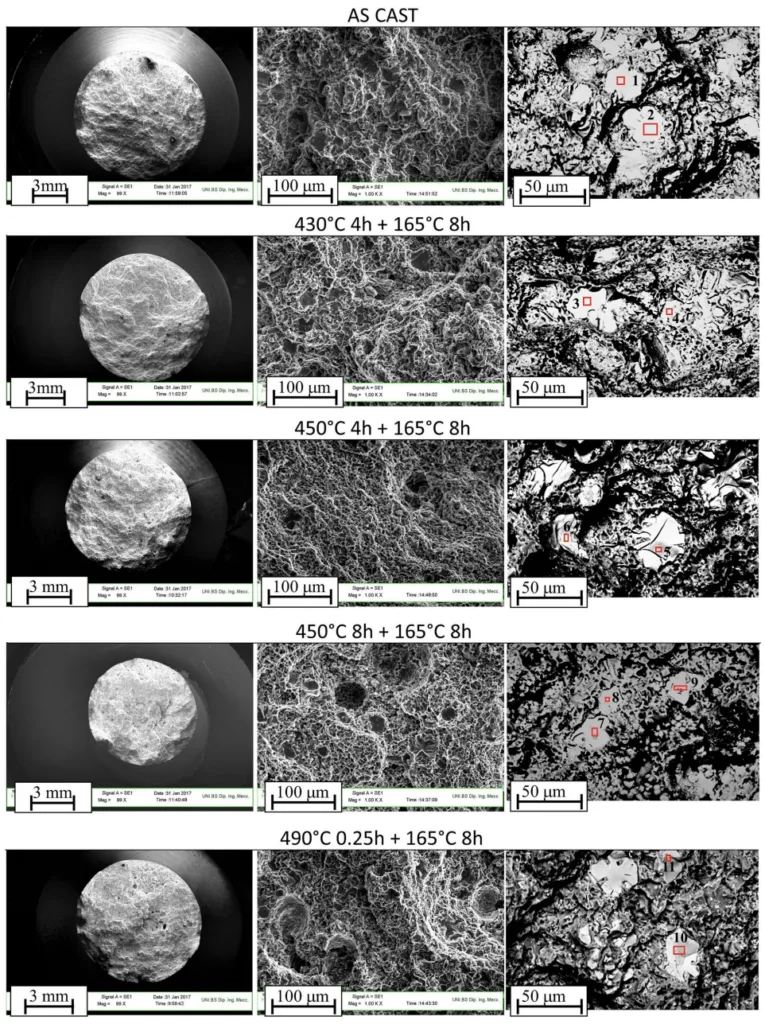
- 図 1 実験的溶体化処理パラメータ (左) および実験的 T6 熱処理条件選択 (右)
- 図 2 異なる時間-温度条件で溶体化処理された合金 EN AC 46000 の硬さ-時間曲線
- 図 3 鋳造状態 (A) および 430 および 450 °C (B) で溶体化処理された EN AC 46000 サンプルの同一断面の光学顕微鏡 500 倍。詳細: α-Al-デンドライト (a)、Al-Si-Al2Cu-共晶 (b)、初晶 Al15 (Mn, Fe,Cr)3Si2 (c) および Al₂Cu (d)
- 図 4 165 °C で時効処理された合金 EN AC 46000 の硬さ-時間曲線 (異なる溶体化処理手順後)
- 図 5 異なる溶体化処理手順後、165 °C で 8 時間時効処理された合金 EN 46000 の引張試験曲線の比較
- 図 6 引張サンプルの直交断面の SEM
- 図 7 引張サンプルの破面の SEM
- 図 8 軸に直交する断面の SEM 調査における金属間化合物マッピングの結果
7. 結論:
主な知見の要約:
本研究は、低温溶体化 T6 熱処理を HPDC 二次 AlSi9Cu3 合金に適用することが可能であることを決定的に実証しています。450 °C 未満の溶体化温度を、工業的に関連する時間と組み合わせることで、顕著なブリスターリングを引き起こすことなく、合金を効果的に強化しました。最適と特定された T6 処理は、430 °C/4 時間の溶体化と 165 °C/8 時間の時効を含み、降伏強さ (約 50 MPa 増加)、延性 (2 倍増加)、および全体的な品質指数 (約 50% 増加) において大幅な改善をもたらしました。
研究の学術的意義:
本研究は、HPDC アルミニウム合金、特に二次合金の熱処理応答に関する科学的理解に貢献します。従来使用されていたよりも低い溶体化温度で効果的な強化を達成できることを実証し、熱処理可能な HPDC 部品の加工範囲を拡大します。本研究は、低温溶体化処理パラメータ、微細組織の進化 (シリコンの球状化、金属間化合物相の変態)、および結果として得られる機械的特性との関係に関する貴重な洞察を提供します。
実用的な意義:
本研究の知見は、HPDC 二次 AlSi9Cu3 合金部品を熱処理するための、実用的で実行可能かつより手頃なアプローチを提供します。真空補助 HPDC または高温溶体化処理の必要性をなくすことで、この低温 T6 処理は、従来の鋳造環境に容易に実装でき、機械的性能を向上させ、HPDC アルミニウム部品、特に自動車分野での応用範囲を拡大できます。
研究の限界と今後の研究分野:
本研究は重要な洞察を提供していますが、さまざまな HPDC 部品形状および合金組成に対して低温 T6 処理を最適化するためには、さらなる研究が必要です。最適化されたパラメータで処理された部品の疲労およびクリープ挙動を含む長期性能評価が推奨されます。低温溶体化処理中の金属間化合物相変態と気孔率の進化の正確なメカニズムに関するさらなる調査も有益でしょう。
8. 参考文献:
- [参考文献リストは、元の要約の 8 番の参考文献リストと同じ]
9. 著作権:
- 本資料は、"[Silvia Cecchel, Andrea Panvini, and Giovanna Cornacchia]" の論文: "[Low Solution Temperature Heat Treatment of AlSi9Cu3(Fe) High-Pressure Die-Casting Actual Automotive Components]" に基づいています。
- 論文ソース: https://doi.org/10.1007/s11665-018-3478-4
本資料は上記の論文に基づいて要約されたものであり、商業目的での無断使用は禁止されています。
Copyright © 2025 CASTMAN. All rights reserved.