この論文概要は、"Materials MDPI" に掲載された論文 "[Development of Low-Pressure Die-Cast Al–Zn–Mg–Cu Alloy Propellers—Part I: Hot Tearing Simulations for Alloy Optimization]" に基づいて作成されました。
1. 概要: 高強度アルミニウム合金プロペラ、熱間割れ問題解決のための合金最適化研究
- タイトル: Development of Low-Pressure Die-Cast Al–Zn–Mg–Cu Alloy Propellers—Part I: Hot Tearing Simulations for Alloy Optimization
- 著者: Min-Seok Kim, Jiwon Kim
- 発行年: 2024年
- 発行ジャーナル/学会: Materials MDPI
- キーワード: Al–Zn–Mg–Cu合金, 低圧ダイカスト, シミュレーション, プロペラ, 熱間割れ
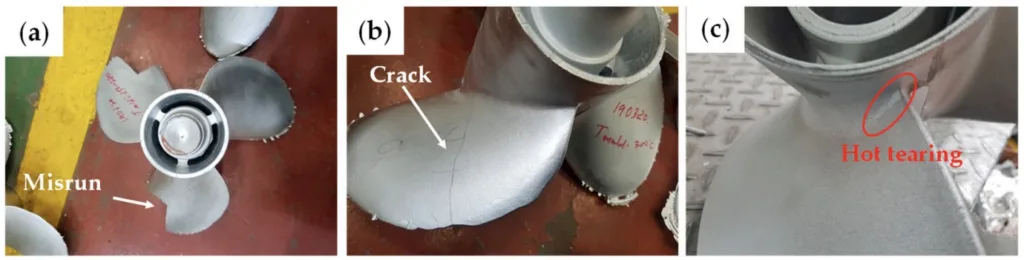
2. 研究背景: レジャーボート産業における高性能プロペラの需要、7xxx系合金の熱間割れ問題
- 研究テーマの社会的/学術的背景: レジャーボート産業の急速な成長により、高性能プロペラ材料の需要が増加しています。従来のAl-Si合金は鋳造性は優れていますが、機械的特性に限界があります。一方、7xxx系アルミニウム合金(Al-Zn-Mg-Cuベース)は機械的特性に優れていますが、鋳造時に熱間割れが発生しやすいという問題があります。
- 既存研究の限界: 既存研究は主にAl-Si合金に集中しており、7xxx系合金の鋳造特性、特に熱間割れ感受性に関する詳細な研究は不足していました。市販の高強度合金を鋳造プロセスに直接適用することには限界がありました。
- 研究の必要性: Al-Si合金の機械的特性の限界を克服し、ステンレス鋼プロペラに代わる高強度アルミニウム合金の開発が必要です。7xxx系合金の低圧ダイカスト(LPDC)プロセス最適化を通じて、プロペラの性能と耐久性を向上させる研究が求められています。
3. 研究目的と研究課題: 7xxx系合金の熱間割れ感受性評価と最適合金組成の探索
- 研究目的: 本研究は、7xxx系アルミニウム合金の低圧ダイカスト(LPDC)プロセス適用時の熱間割れ感受性を評価し、これを最小限に抑える最適な合金組成を開発することを目的としています。
- 主な研究課題:
- Al-Zn-Mg-Cu合金において、各成分の変化が熱間割れ感受性(HTS)に及ぼす影響は何か?
- 有限要素シミュレーションは、これらの合金の熱間割れ感受性を効果的に予測できるか?
- LPDCプロペラ製造に適した、熱間割れ感受性の低い最適なAl-Zn-Mg-Cu合金組成は何か?
- 研究仮説:
- Al-Zn-Mg-Cu合金において、ZnとCuの含有量が増加すると、一般的に熱間割れ感受性(HTS)が増加するだろう。
- Mg含有量を十分に添加すると、ZnとCuの増加によるHTSの増加を緩和できるだろう。
- シミュレーションおよび実験的検証を通じて、LPDCプロペラ製造に適した、熱間割れ感受性の低い最適な4元系Al-Zn-Mg-Cu合金を見つけることができるだろう。
4. 研究方法: 拘束ロッド鋳造(CRC)および有限要素シミュレーションの活用
- 研究デザイン: さまざまなAl-Zn-Mg-Cu合金組成の熱間割れ感受性(HTS)を評価するために、実験的な拘束ロッド鋳造(CRC)法と有限要素シミュレーションを併用しました。
- データ収集方法:
- 合金化学組成分析: ICP-OES (誘導結合プラズマ発光分光分析法) 分析
- 熱間割れ評価: CRC鋳造後の目視検査により、熱間割れの程度を4段階(short hairline, full hairline, crack, half-broken rod)に分類
- シミュレーションデータ: ProCAST 2021ソフトウェアを使用して、熱間割れ指標(HTI)および有効塑性ひずみデータを収集
- 分析方法:
- 実験的HTS指数(HTSexp.)の計算: 割れの重症度、ロッド長、割れ位置に基づいてHTS指数を計算
- シミュレーションHTS指数(HTSsimul.)の計算: Gurson構成モデルに基づくProCASTソフトウェアを活用し、HTI値を基にHTSsimul.値を算出
- 合金組成の変化に伴うHTSsimul.の変化を分析
- 研究対象と範囲: 市販の7xxx系アルミニウム合金(AA7075、AA7068、AA7055)および様々な組成のAl-Zn-Mg-Cu 4元系合金を研究対象として設定しました。研究範囲は、拘束ロッド鋳造(CRC)によるHTS評価、および最適合金を活用したプロペラLPDCシミュレーションと実験鋳造を含みます。
5. 主な研究結果: Zn, Cu含有量増加でHTS増加、Mg 2wt.%添加でHTS緩和
- 主な研究結果:
- CRC実験の結果、AA7075、AA7068、AA7055合金のHTSexp.値はそれぞれ328、376、384となり、AA7075からAA7055へとHTSが増加する傾向を示しました。
- シミュレーション結果は、予測されたHTS(rod)simul.値と実験的に評価されたHTS(rod)exp.値との間に高い線形関係を示し、シミュレーションモデルの有効性を検証しました。
- Al-Zn-Mg-Cu 4元系合金において、ZnおよびCu含有量が増加するほどHTSsimul.値が増加する傾向が見られましたが、Mg含有量が2 wt.%以上の場合、HTSの増加幅が緩和されることを確認しました。
- HTSsimul.値が比較的低い最適な4元系合金2種(Al-6Zn-2Mg-0.5Cu、Al-6Zn-2Mg-1.5Cu)を選定しました。
- LPDCシミュレーションおよびプロペラの実験鋳造の結果、Al-6Zn-2Mg-0.5Cu合金は熱間割れが発生しませんでしたが、Al-6Zn-2Mg-1.5Cu合金はハブ-ブレード接合部で熱間割れが発生することを確認し、シミュレーション予測と一致する結果を得ました。
- 統計的/定性的分析結果:
- 市販合金の実験的HTSexp.値は、AA7075 < AA7068 < AA7055 の順に増加しました。
- HTS(rod)simul.値とHTS(rod)exp.値の間に高い線形相関(R² = 0.98)を確認しました。
- 4元系合金のHTSsimul.値は、ZnおよびCu含有量の増加に伴い増加する傾向を示しましたが、Mg 2 wt.% 添加により増加幅が鈍化しました。
- データ解釈:
- ZnおよびCu含有量の増加に伴うHTSの増加は、凝固温度範囲(STR)の増加に起因します。
- Mg 2 wt.% 添加は、十分な共晶液相の形成を誘導し、HTSを効果的に低減すると考えられます。これは、凝固収縮および熱収縮を効果的に補償するためです。
- シミュレーション結果は、CRCおよびLPDCプロセスの両方で熱間割れの発生傾向と位置を正確に予測しました。
- 図リスト:
- 図 1. LPDC 7xxx系アルミニウム合金プロペラの鋳造欠陥の例: (a) ミスラン, (b) クラック, (c) 熱間割れ.
- 図 2. 拘束ロッド鋳造用金型の外観.
- 図 3. 3Dメッシュシミュレーションモデル: (a) CRC, (b) LPDC.
- 図 4. シミュレーションで使用されたアルミニウム合金の熱物性: (a) 熱伝導率, (b) 密度, (c) エンタルピー, (d) 粘度, (e) 熱膨張, (f) ヤング率, (g) 耐力, (h) ポアソン比, (i) 塑性率.
- 図 5. 拘束ロッド鋳造の結果: (a) AA7075, (b) AA7068, (c) AA7055.
- 図 6. CRC 7xxx系合金の熱間割れ指数シミュレーション結果.
- 図 7. CRC 7xxx系合金のシミュレーションと実験結果の比較: (a) HTS(rod)exp. vs. HTS(rod)simul., (b) HTSexp. vs. HTSsimul..
- 図 8. Al-Zn-Mg-Cu合金におけるZn, Mg, Cu含有量の変化に伴うHTSsimul.値: (a) Al-7Zn-xMg-yCu, (b) Al-xZn-2.0Mg-yCu.
- 図 9. LPDC Al-Zn-Mg-Cu合金のシミュレーションと実験結果: (a) Al-6Zn-2Mg-0.5Cu, (b) Al-6Zn-2Mg-1.5Cu (wt.%).
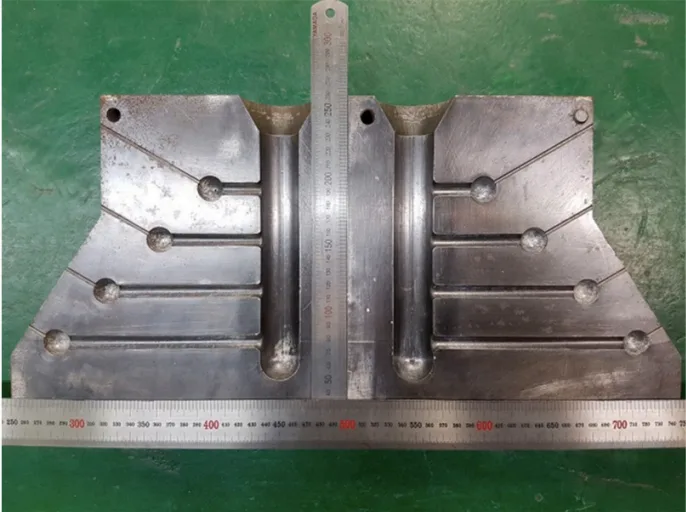
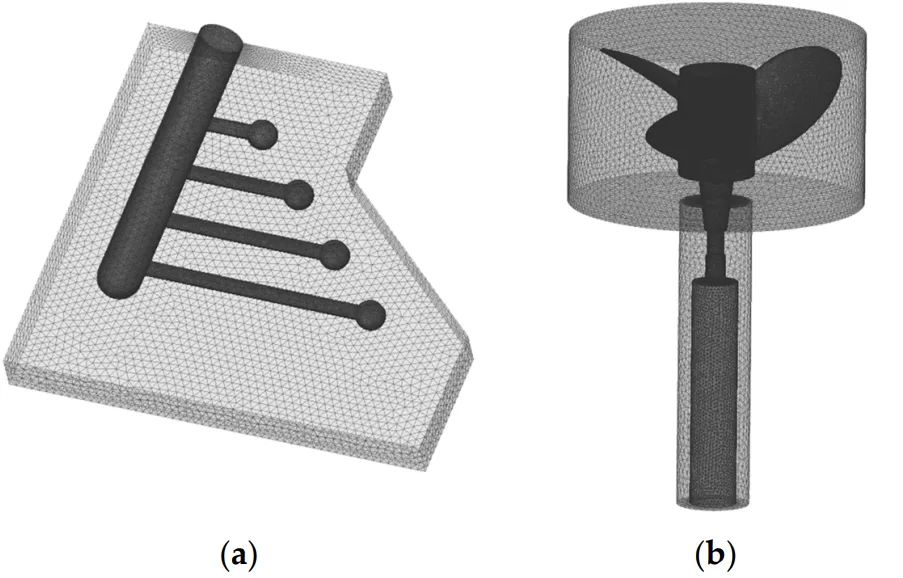
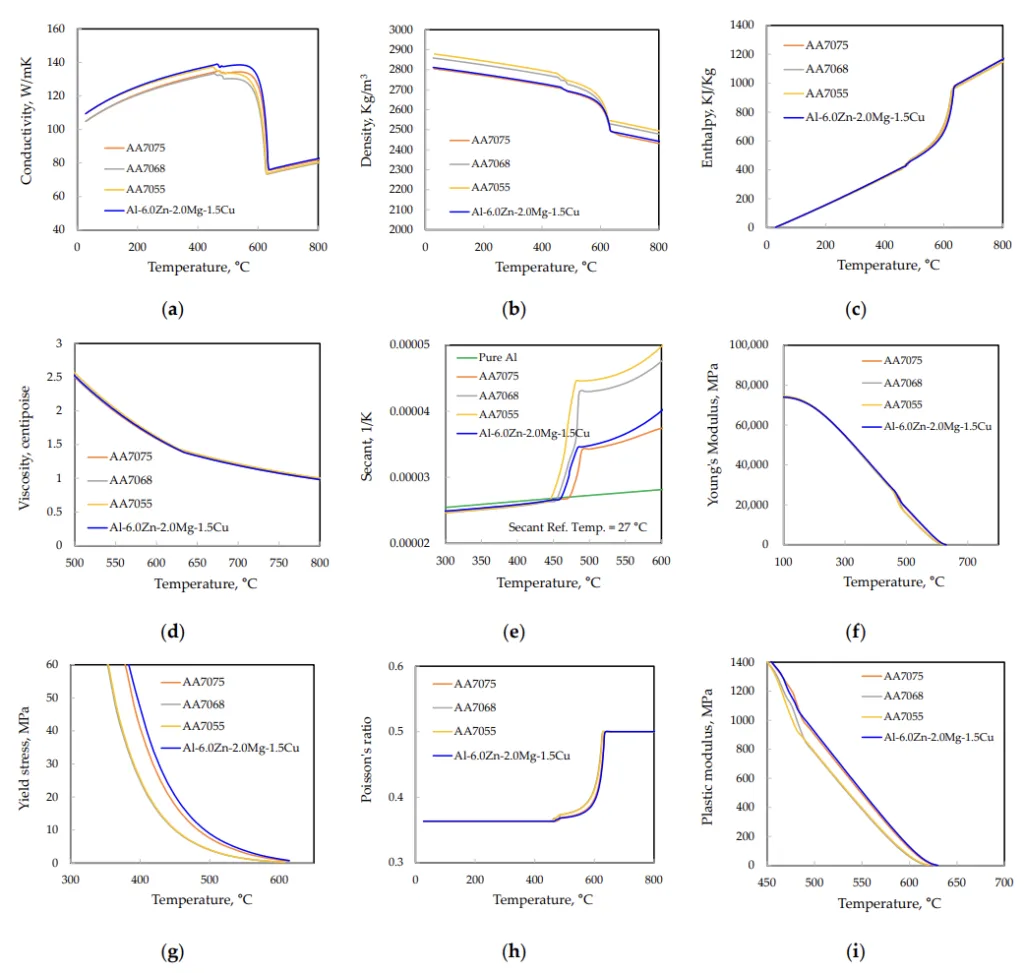
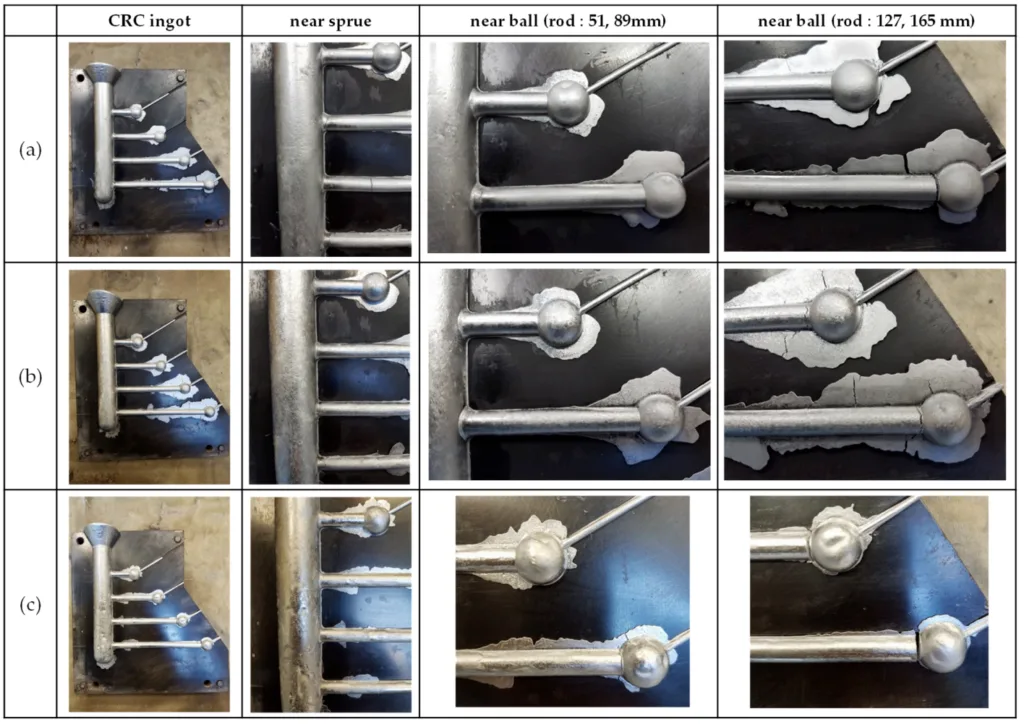
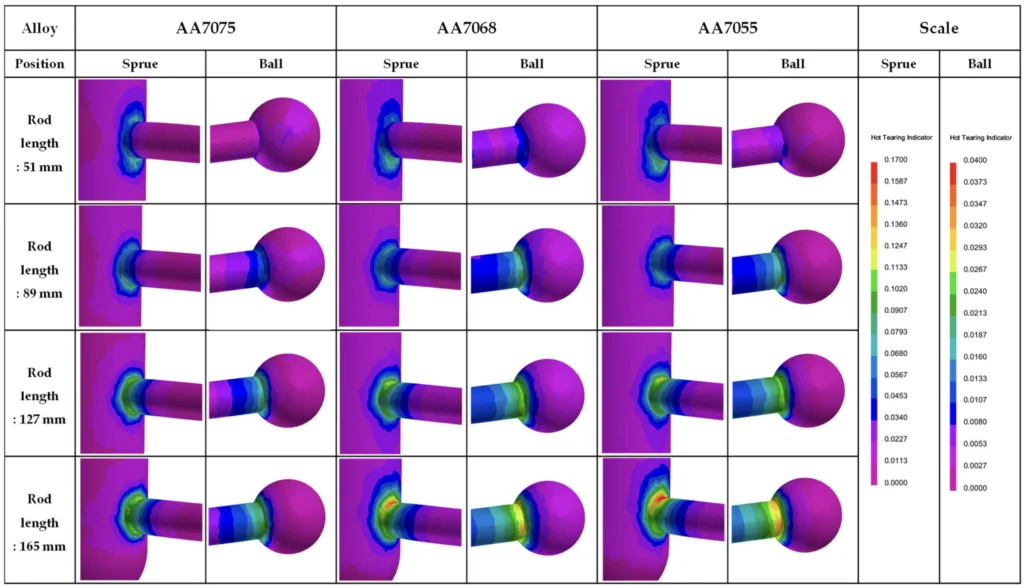
6. 結論と考察: 7xxx系合金プロペラの製造可能性を確認、追加の工程最適化が必要
- 主な結果の要約: 本研究では、CRC実験と有限要素シミュレーションを用いて、市販および最適化されたAl-Zn-Mg-Cu合金の熱間割れ感受性(HTS)を効果的に評価しました。ZnとCuの含有量が増加するとHTSが増加する一方、十分なMg(2 wt.%)の添加はこれを緩和することがわかりました。HTSが低い最適な合金2種(Al-6Zn-2Mg-0.5Cu、Al-6Zn-2Mg-1.5Cu)を選定し、LPDCプロペラの製造可能性を検証しました。
- 研究の学術的意義: 本研究は、7xxx系アルミニウム合金における熱間割れメカニズムの理解を深め、シミュレーションベースの合金最適化手法の有効性を実証しました。合金組成、凝固温度範囲、共晶液相分率間の複雑な相互作用がHTSに及ぼす影響を明らかにしました。
- 研究の実用的意義: 本研究は、LPDCプロセス、特にプロペラ製造に適したAl-Zn-Mg-Cu合金の設計指針を提供します。Al-6Zn-2Mg-0.5Cu合金は、従来の合金に代わる高性能プロペラ製造への応用が期待でき、熱間割れ欠陥の低減と生産コストの削減に貢献する可能性があります。
- 研究の限界: 本研究は合金組成の最適化に焦点を当てています。特にCu含有量の高いAl-6Zn-2Mg-1.5Cu合金の場合、熱間割れを完全に除去するためには、さらなる工程最適化が必要です。本研究はPart Iであり、熱間割れシミュレーションに重点が置かれており、Part IIでは追加の実験的検証と工程最適化を探求する予定です。
7. 今後のフォローアップ研究:LPDC工程変数の最適化および熱処理研究が必要
- 今後の研究方向: 今後の研究では、MgおよびCu含有量の高いAl-Zn-Mg-Cu合金のLPDC工程最適化を通じて、熱間割れをより効果的に抑制する方法を研究する必要があります。
- 追加の探求領域: Part IIの研究では、シミュレーションモデルを使用して、LPDC工程変数が熱間割れ発生に及ぼす影響を分析し、工程最適化戦略を詳細に議論する予定です。また、鋳造された合金の機械的特性を最大化するための熱処理工程の最適化研究も必要です。
8. 参考文献:
- Kluczyk, M.; Grządziela, A.; Batur, T. Design and operational diagnostics of marine propellers made of polymer materials. Pol. Marit. Res. 2022, 29, 49–59.
- Cass, A.; Nielson, J.R. Smart energy systems approach to zero emissions long-range sailing vessels. Smart Energy 2022, 7, 100086.
- Oloruntobi, O.; Mokhtar, K.; Gohari, A.; Asif, S. Sustainable transition towards greener and cleaner seaborne shipping industry: Challenges and opportunities. Clean. Eng. Technol. 2023, 13, 100628.
- Baley, C.; Davies, P.; Troalen, W.; Chamley, A.; Dinham-Price, I.; Marchandise, A.; Keryvin, V. Sustainable polymer composite marine structure: Developments and challenges. Prog. Mater. Sci. 2024, 145, 101307.
- Dashtimanesh, A.; Ghaemi, M.H.; Wang, Y. Digitalization of high speed craft design and operation challenges and opportunities. Procedia Comput. Sci. 2022, 200, 566–576.
- Begovic, E.; Bertorello, C.; De Luca, F. KISS (Keep It Sustainable and Smart): A research and development program for a zero-emission small crafts. J. Mar. Sci. Eng. 2022, 10, 16.
- Choudhary, G.; Singh, G. Comparative analysis of corrosion behaviour of stainless steel grades 304 and 316L for different applications. I-Manag. J. Mater. Sci. 2020, 7, 8–22.
- Mendagaliev, R.; Klimova-Korsmik, O.; Promakhov, V.; Schulz, N.; Zhukov, A.; Klimenko, V.; Olisov, A. Heat treatment of corrosion resistant steel for water propellers fabricated by direct laser deposition. Materials 2020, 13, 2738.
- Konieczny, J.; Labisz, K. Materials used in the combat aviation construction. Transp. Probl. 2021, 16, 5–18.
- Bhuiyan, M.S.; Sian, I.H.; Kharshiduzzaman, M. Unveiling the microstructure of LES manufactured parts for sustainable productive business. J. Alloys Compd. 2023, 4, 100038.
- Zhou, B.; Liu, B.; Zhang, S. The advancement of 7xxx series aluminum alloys for aircraft structures: A review. Metals 2021, 11, 718.
- Wang, Z.; Jiang, H.; Li, H.; Li, S. Effect of solution-treating temperature on the intergranular corrosion of a peak-aged Al-Zn-Mg-Cu alloy. J. Mater. Res. Technol. 2020, 9, 6497–6511.
- Cheng, Q.; Ye, L.; Huang, Q.; Dong, Y.; Liu, S. Effect of two-stage overaging on microstructure and corrosion properties of an Al-Zn-Mg-Cu alloy. J. Mater. Res. Technol. 2022, 20, 3185–3194.
- Wang, A.; Silva, K.; Jones, M.; Robinson, P.; Larribe, G.; Gao, W. Anticorrosive coating systems for marine propellers. Prog. Org. Coat. 2023, 183, 107768.
- Xue, W.; Wang, C.; Tian, H.; Lai, Y. Corrosion behaviors and galvanic studies of microarc oxidation films on Al-Zn-Mg-Cu alloy. Surf. Coat. Technol. 2007, 201, 8695–8701.
- Jolly, M.; Katgerman, L. Modelling of defects in aluminium cast products. Prog. Mater. Sci. 2022, 123, 100824.
- Li, Y.; Li, H.; Katgerman, L.; Du, Q.; Zhang, J. Recent advances in hot tearing during casting of aluminium alloys. Prog. Mater. Sci. 2021, 117, 100741.
- Pulisheru, K.S.; Birru, A.K. Effect of pouring temperature on hot tearing susceptibility of Al-Cu cast alloy: Casting simulation. Mater. Today Proc. 2021, 47, 7086–7090.
- Ali, R.; Zafar, M.; Manzoor, T.; Kim, W.Y.; Rashid, M.U.; Abbas, S.G.; Zai, B.A.; Ali, M. Elimination of solidification shrinkage defects in the casting of aluminum alloy. J. Mech. Sci. Tehnol. 2022, 36, 2345–2353.
- Rahangmetan, K.A.; Sariman, F.; Parenden, D. The effect of riser use in the quality of casting Al 7075 for ship propeller. Int. J. Mech. Eng. Technol. 2019, 10, 10–17.
- Dong, G.; Li, S.; Ma, S.; Zhang, D.; Bi, J.; Wang, J.; Starostenkov, M.D.; Xu, Z. Process optimization of A356 aluminum alloy wheel hub fabricated by low-pressure die casting with simulation and experimental coupling methods. J. Mater. Res. Tehnol. 2023, 24, 3118–3132.
- Song, J.; Pan, F.; Jiang, B.; Atrens, A.; Zhang, M.X.; Lu, Y. A review on hot tearing of magnesium alloys. J. Magnes. Alloy 2016, 4, 151–172.
- Wang, Z.; Song, J.; Huang, Y.; Srinivasan, A.; Liu, Z.; Kainer, K.U.; Hort, N. An Investigation on Hot Tearing of Mg-4.5Zn-(0.5Zr) Alloys with Y Additions. Metall. Mater. Trans. A 2015, 46, 2108–2118.
- Wang, J.; Fu, P.; Peng, L.; Wang, Y.; Ding, W. A simplified hot-tearing criterion for shape castings based on temperature-field simulation. Metall. Mater. Trans. A 2019, 50, 5271–5280.
- Li, L.; Zhang, R.; Yuan, Q.; Huang, S.; Jiang, H. An integrated approach to study the hot tearing behavior by coupling the microscale phase field model and macroscale casting simulations. J. Mater. Proc. Technol. 2022, 310, 117782.
- Xu, Y.; Zhang, Z.; Gao, Z.; Bai, Y.; Zhao, P.; Mao, W. Effect of main elements (Zn, Mg and Cu) on the microstructure, castability and mechanical properties of 7xxx series aluminum alloys with Zr and Sc. Mater. Charact. 2021, 182, 111559.
- Guo, J.; Samonds, M.T. Alloy thermal physical property prediction coupled computational thermodynamics with back diffusion consideration. J. Phase Equlib. Diff. 2007, 28, 58–63.
- Li, Y.; Zhang, Z.R.; Zhao, Z.Y.; Li, H.X.; Katgerman, L.; Zhang, J.S.; Zhuang, L.Z. Effect of main elements (Zn, Mg, and Cu) on hot tearing susceptibility during direct-chill casting of 7xxx aluminum alloys. Metall. Mater. Trans. A 2019, 50, 3603–3616.
- Kim, J.H.; Jo, J.S.; Sim, W.J.; Im, H.J. The influence of alloy composition on the hot tear susceptibility of the Al-Zn-Mg-Cu alloy system. Korean J. Met. Mater. 2012, 50, 669–675.
- Clyne, T.W.; Wolf, M.; Kurz, W. The effect of melt composition on solidification cracking of steel, with particular reference to continuous casting. Metall. Trans. B 1982, 13, 259–266.
9. 著作権:
本資料は、Min-Seok Kim、Jiwon Kimの論文 "Development of Low-Pressure Die-Cast Al–Zn–Mg–Cu Alloy Propellers—Part I: Hot Tearing Simulations for Alloy Optimization" に基づいて要約されています。
論文ソース:[DOI URL] https://doi.org/10.3390/ma17133133
本資料は上記の論文に基づいて要約されており、商業目的での無断使用は禁止されています。
Copyright © 2025 CASTMAN. All rights reserved.