本紹介資料は、「[Journal/academic society of publication]」に掲載された論文「Inhomogeneous Skin Formation and Its Effect on the Tensile Behavior of a High Pressure Die Cast Recycled Secondary AlSi10MnMg(Fe) Alloy」を基に作成されています。
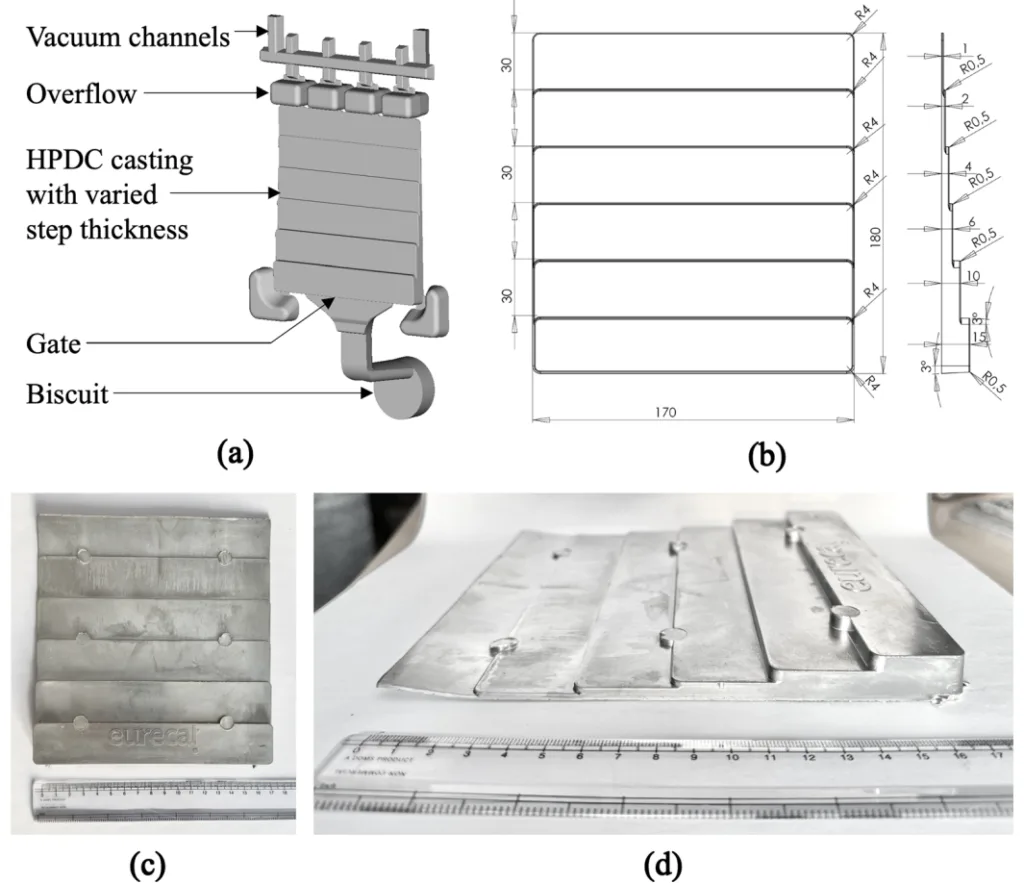
1. 概要:
- 論文タイトル: Inhomogeneous Skin Formation and Its Effect on the Tensile Behavior of a High Pressure Die Cast Recycled Secondary AlSi10MnMg(Fe) Alloy (不均一スキン層形成と高圧ダイカスト再生二次AlSi10MnMg(Fe)合金の引張挙動への影響)
- 著者: BISWAJIT DALAI, SIMON JONSSON, MANEL DA SILVA, LIANG YU, and JÖRGEN KAJBERG
- 発行年: 2024
- 掲載学術誌/学会: Metallurgical and Materials Transactions A
- キーワード: 論文中に記載なし
2. 抄録:
本研究では、高圧ダイカスト(HPDC)で製造された新規再生二次合金のミクロ組織変化、機械的特性、および破壊挙動を調査した。鋳造ままのミクロ組織は、(i)初晶α-Al、(ii)α-Al15(FeMn)3Si2金属間化合物、および(iii)Al-Si共晶から構成されていた。HPDC鋳造品の表面から深さ方向へのミクロ組織は、(i)表面の微細粒スキン層、(ii)中間位置でのAl-Si共晶の増加、および(iii)中心部の粗大なα-Alデンドライトから成っていた。これに応じて、硬度はスキン層から中間部にかけて増加し、その後鋳造品中心に向かって減少した。スキン層の形成は非常に不連続であり、これはダイキャビティ内の複雑な溶湯流動パターンに起因すると考えられた。スキン層はHPDC合金の強度をわずかに向上させることを示したが、材料の延性を大きなばらつきとともに制限した。このような延性挙動は、不均一なスキン層が隣接するマトリックスとの結合不良のために引き起こす破壊メカニズムに起因するものであった。この二次合金は、このような材料の破壊の駆動要因として知られている鋳造欠陥やα-Al15(FeMn)3Si2金属間化合物を含んでいたにもかかわらず、本研究では不均一なスキン層からの影響が支配的であることが判明した。
3. 緒言:
高圧ダイカスト(HPDC)は、高い生産性を有するプロセスであり、自動車産業においてシャシーやボディインホワイト(BIW)構造のような、幾何学的に精密で薄肉の部品を製造するために広く利用されている。従来のHPDC合金は、しばしばAl-Si-Mg系をベースとしている。これらの合金は通常、不純物としてFe(0.8-1.1 wt pct)を含んでおり、これは金型への焼き付き(die sticking)を防止するのに役立つが、有害な針状のβ-Al5FeSi化合物を形成し、機械的特性、特に延性を著しく損なう。これを軽減するために、Fe含有量を制限し(<0.25 wt pct)、Mnを添加(0.4-0.8 wt pct)した一次AlSi10MnMg合金(例: EN AC-43500)が開発された。Mnは「鉄補正剤(iron corrector)」として機能し、β-Feの代わりに害の少ないα-Fe金属間化合物の形成を促進し、またFe含有量の低減による焼き付き傾向を補償する。しかし、低いFeレベルを達成することは、希釈の必要性から生産コストを増加させる。持続可能性とコスト削減への関心が高まる中、スクラップのリサイクルにより本質的に高いFe含有量を持つ二次(再生)Al-Si合金の使用への関心が高まっている。本研究は、HPDCで処理された再生二次AlSi10MnMg(Fe)合金のミクロ組織、機械的挙動、および破壊メカニズムを理解することに焦点を当て、しばしば見過ごされる表面スキン層の形成とその潜在的な不均一性に特に注意を払う。
4. 研究の概要:
研究テーマの背景:
自動車産業は、軽量なAl-Si合金部品の製造にHPDCを利用している。Fe含有量の管理は重要であり、高Feは有害なβ-Fe相を形成し、低Feはコストと金型焼き付きの可能性を高める。一次合金は、低FeとMn添加(α-Fe形成)を用いて、特性と鋳造性のバランスを取っている。二次(再生)合金はコストと環境面での利点を提供するが、Fe含有量が高いため、β-Feを避けるためには慎重な制御(例: Mn:Fe比)が必要となる。金属間化合物、欠陥、表面スキンなどのミクロ組織的特徴は、HPDC部品の最終特性に大きな影響を与える。
先行研究の状況:
一次AlSi10MnMg HPDC合金に関する研究では、典型的なミクロ組織(α-Al、α-Fe、Al-Si共晶)、表面(微細)から中心(粗大)への変化、および様々なα-Fe形態が特徴付けられている。破壊はしばしば、大きなポロシティ、表面欠陥、または応力集中源として作用するα-Fe粒子に関連付けられている。二次AlSi10MnMg(Fe)合金の研究は、β-Fe形成を抑制するためにMn:Fe比(通常0.58-1.3)を最適化することに焦点を当ててきた。そのミクロ組織は一次合金と類似しており、破壊もまた、大きなα-Fe化合物やラミネーションのような鋳造欠陥で開始すると報告されている。しかし、不均一な表面スキン層の形成とその影響は、破面で時折暗黙的に観察されるものの、体系的には調査されておらず、知識のギャップとなっている。
研究の目的:
本研究の目的は、真空アシストHPDCプロセスによって製造された新規再生二次AlSi10MnMg(Fe)合金のミクロ組織変化、機械的特性、および破壊挙動を調査することであった。特に、表面スキン層の形成、その潜在的な不均一性、および合金の引張応答、特に近年の構造用途に関連する薄肉(2mm)鋳造品に対するその影響に焦点を当てた。
研究の核心:
本研究の核心は以下を含む:
- OM、SEM、EDSを用いた二次AlSi10MnMg(Fe)合金の鋳造ままミクロ組織の特性評価。相の同定(α-Al、α-Fe、共晶)、形態、および2mm厚さ全体にわたる分布に焦点を当てる。
- 表面スキン層の形成と均一性を異なる場所で調査する。
- HPDC部品に存在する鋳造欠陥を特定する。
- 鋳造品の厚さ方向の硬度プロファイルを測定する。
- 元のスキンを持つ試験片とスキンを除去した試験片で単軸引張試験を実施し、スキンが強度と延性に及ぼす影響を評価する。
- 高速度カメラ撮影、SEM破面観察、および側面OM分析を用いた詳細な破壊解析を実施し、亀裂の発生と伝播メカニズムを理解し、特に観察されたミクロ組織とスキン層の不均一性に関連付ける。
5. 研究方法論
研究デザイン:
本研究は実験的アプローチを採用した。再生二次AlSi10MnMg(Fe)合金を真空アシストHPDCプロセスを用いて段付き形状部品に鋳造した。2mm厚さの部分から採取したサンプルを、ミクロ組織特性評価、硬度試験、および単軸引張試験(表面スキン有無の比較)に供した。破面および隣接する側面を分析し、機械的挙動をミクロ組織的特徴、特にスキン層の不均一性と関連付けた。
データ収集・分析方法:
- 材料: Raffmetal社供給の二次AlSi10MnMg(Fe)合金 (組成はTable I参照、特にSi: 9.547, Fe: 0.297, Mn: 0.65, Mg: 0.218 wt pct, Mn:Fe ≈ 2.1)。
- HPDCプロセス: Buhler社製コールドチャンバーマシン(型締力5250 kN)を用いて段付き部品を鋳造(Fig 1b)。主要パラメータ: 溶湯温度700-720 °C、プランジャー速度4 m/s (充填段階)、計算上の湯口速度42 m/s、VDS真空システム(85-100 mbar)、最終圧力900-950 bar。
- ミクロ組織特性評価: 2mm厚ステップからサンプルを切り出し、マウント、研磨(P120~P4000 SiC紙)、ポリッシング(1µmダイヤモンド、0.05µm OPS)。光学顕微鏡(OM)はNikon Eclipse MA200を使用。走査電子顕微鏡(SEM)およびエネルギー分散型X線分光法(EDS)は、FEI Magellan 400 XHR SEMを用いて相組成分析を実施。
- 機械的試験:
- 硬度: ビッカース微小硬度(Struers Duramin-40、荷重0.05 kgf、保持時間10秒)を研磨断面で測定。
- 引張試験: 2mm厚ステップ中央部から平板試験片(Fig 3a)を加工。2セット試験:「スキンあり」(表面をP1200紙で研磨)および「スキンなし」(各表面から約150 µmをP1200までの研磨で除去後、ゲージ部をP1200で研磨)。Instron 1272試験機を用い、2 mm/min(ひずみ速度0.001 s⁻¹)で試験、伸び計(ゲージ長25 mm)使用。Phantom V2512高速度カメラ(96,000フレーム/秒)で亀裂発生を記録。
- 破壊解析: SEM(Magellan、3 kV、0.8 nA、ETD検出器)を破面観察に使用。OM(Nikon)を破壊箇所に隣接する研磨側面の観察に使用(Fig 4)。
- 凝固時間/冷却速度推定: OM画像から二次デンドライトアーム間隔(SDAS, d)を測定(Fig 9)。HanとZhang [41]に基づく経験式(Eq. [1]-[3])を用い、測定されたSDASと近似的なTL(600 °C)、TS(590 °C)を使用して局所凝固時間(ts)と冷却速度(q)を推定。
研究テーマと範囲:
本研究は、HPDCプロセスで2mm厚の鋳造品に加工された特定の再生二次AlSi10MnMg(Fe)合金に焦点を当てた。範囲は以下を含む:
- 鋳造ままミクロ組織の詳細分析: 相構成要素、形態、厚さ方向分布。
- 表面スキン層形成、その特性、特に不均一性の調査。
- 一般的な鋳造欠陥の特定。
- ミクロ組織と硬度分布の相関。
- 表面スキン層が引張特性(YS、UTS、伸び)に及ぼす影響の評価。
- 不均一スキン層の役割対他の要因(欠陥、金属間化合物など)を強調した破壊メカニズムの解明。
6. 主要な結果:
主要な結果:
- ミクロ組織: 鋳造ままミクロ組織は、初晶α-Al (デンドライト状(α-Al)Iおよび球状(α-Al)II)、α-Al15(FeMn)3Si2金属間化合物 (多角形状(α-Fe)I、微細多角形状(α-Fe)II、およびチャイニーズスクリプト状)、およびAl-Si共晶から構成される(Fig 5)。Mn:Fe比約2.1は、有害なβ-Al5FeSiの形成を効果的に抑制した。EDS分析によりα-Fe相の組成を確認した(Table II)。
- ミクロ組織勾配: 2mm厚さ全体にわたって明確なミクロ組織勾配が存在した: 微細粒α-Alスキン層(Region 1、厚さ約30-150 µm)、Al-Si共晶が増加した中間領域(Region 2)、および粗大なα-Alデンドライト((α-Al)I)が支配的な中心部(Region 3)(Fig 6)。
- 不均一スキン層: スキン層の形成は非常に不均一であることが判明した。スキン層の突然の途絶、スキン層が表面から内部へ移動するように見える現象、一部の表面でのスキン層の完全な欠如が観察された(Fig 7)。
- 鋳造欠陥: コールドフレーク、コールドショット、収縮ポロシティ、および不均一スキン層に関連するラミネーションなど、様々な欠陥が特定された(Fig 8)。
- SDASと冷却速度: 平均SDASはスキン層(Region 1)の3.6 µmから中心部(Region 3)の14.6 µmに増加した(Fig 9)。推定冷却速度はスキン層で約33 °C/s、中心部で約0.5 °C/sであったが、これらは桁レベルの推定値である(Table III)。
- 硬度プロファイル: 硬度はスキン層(約86 HV)から中間領域(共晶が多いため)にかけて増加し、その後中心部(粗大なα-Alのため)に向かって減少した(Fig 10)。圧痕下の相混合と相関して、硬度の顕著な局所的変動が観察された。
- 引張特性: スキン層ありの試験片は、スキン層なしの試験片と比較して、平均YSはわずかに高かった(117.6 MPa vs 111.3 MPa)が、平均UTS(221.8 MPa vs 237 MPa)および平均全伸び(TE)(4.2% vs 6.2%)は著しく低かった(Fig 11, 12)。決定的に、スキン層ありの試験片はUTSとTEの両方ではるかに大きなばらつき(散布度)を示した。
- 破壊挙動: 高速度カメラ撮影により、スキン層ありの試験片では亀裂発生が試験片端部で起こったが、スキン層なしの試験片では平坦な表面で起こったことが示された(Fig 13)。SEM破面観察により、不均一スキン層の存在に対応する角/端部での脆性破壊開始の特徴が明らかになった(Fig 14)。側面OM分析により、低伸びで破断した試験片BおよびCの亀裂発生部位に隣接して、不規則または内部に移動したスキン層が存在することが確認された(Fig 15, 16)。不均一スキン層と下地マトリックス間の結合不良界面に沿った層間剥離(デラミネーション)が、これらの場合の主要な破壊開始メカニズムとして特定された(Fig 14c, 15c3, 16b)。亀裂伝播は主にAl-Si共晶領域を通り、Si粒子およびα-Fe金属間化合物を破壊しながら進行した(Fig 18)。
- 支配的要因: 本研究は、不均一なスキン層形成が、結合不良と層間剥離を引き起こし、試験されたHPDC二次合金試験片(スキン層あり)の破壊挙動を支配し、延性(大きなばらつきを引き起こす)を制限する主要な要因であり、それらの特定のケースにおいては鋳造欠陥やα-Fe粒子の影響を上回ると結論付けた。スキン層の除去は、改善され、より一貫した延性をもたらした。
図のリスト:
- Fig. 1—(a) HPDC構成の各部を示す図、(b) HPDCプロセスで使用された金型の寸法を示す模式図、(c) 実際の鋳造部品の上面図、(d) 異なる肉厚のステップを示す実際の鋳造部品の側面図。
- Fig. 2—2mm肉厚の鋳造まま部品の模式図。緑と赤のボックスはそれぞれ、顕微鏡分析と硬度測定に使用された位置を示す。ピンクの矢印は、スキン層が形成されると想定される2つの鋳造表面を示す(カラー図オンライン)。
- Fig. 3—(a) 単軸引張試験に使用された試験片の寸法を示す模式図、(b) 2mm肉厚の鋳造まま部品から機械加工された実際の引張試験片。
- Fig. 4—SEMおよびOM分析が実施された破断面および側面を示す引張試験済み試験片の模式図。
- Fig. 5—2mm肉厚の鋳造ままAlSi10MnMg(Fe)合金で形成された異なる特徴を示すOM画像。
- Fig. 6—AlSi10MnMg(Fe)合金の2mm厚鋳造まま部品の厚さ方向のミクロ組織変化を示すOM画像。
- Fig. 7—AlSi10MnMg(Fe)合金の2mm厚鋳造ままステップにおけるスキン層の不均一形成を示すOM画像:(a) 赤矢印で示される表面スキン層の突然の消失、(b) 紫矢印で示される表面から離れて深さ方向に移動するスキン層の形成、(c) 鋳造表面の一方におけるスキン層の欠如(カラー図オンライン)。
- Fig. 8—AlSi10MnMg(Fe)合金の2mm厚鋳造ままステップ部品で生成された異なる鋳造欠陥を示すOM画像:(a) 赤矢印で示される顕著な平坦なエッジを持つコールドフレーク、(b) コールドショット、(c) 収縮ポロシティ、(d) 紫矢印で示される不均一スキン層形成によるラミネーション(カラー図オンライン)。
- Fig. 9—AlSi10MnMg(Fe)合金の2mm厚鋳造ままステップ部品におけるSDAS測定箇所を示すOM画像:(a) Region 1: スキン層、(b) Region 3: 中心部。
- Fig. 10—(a) AlSi10MnMg(Fe)合金の2mm厚鋳造ままステップ部品における微小硬度試験で作成された圧痕のOM画像。異なるミクロ組織領域に対する相対位置を示す。(b) 対応する深さ方向の硬度分布。(b)の赤と紫の矢印は、対応する硬度値の比較的大きなばらつきを示す(カラー図オンライン)。
- Fig. 11—2mm肉厚を持つ6つのAlSi10MnMg(Fe)合金試験片の引張試験から得られた公称応力-公称ひずみ曲線:サンプルA、B、Cはスキン層を保持した鋳造まま状態で試験。サンプルD、E、Fはスキン層除去後に試験。
- Fig. 12—二次合金試験片(スキン層あり/なし)の引張試験から得られた0.2%耐力(YS)、最大引張強さ(UTS)、および全伸び(TE)の平均値。エラーバーは各ケースで計算された標準偏差を示す。
- Fig. 13—高速度カメラで撮影された引張試験中の画像:(a) A、(b) B、(c) C、(d) D、(e) E、(f) F。(a~c)および(d~f)はそれぞれスキン層あり/なしの引張試験片を示す。上段の画像の黄色い矢印は各ケースの亀裂発生を示し、下段の画像はその後の時間ステップでの亀裂伝播を示す(カラー図オンライン)。
- Fig. 14—引張試験済み試験片における赤破線矩形で示される亀裂発生箇所のSEM画像:(a) A、(b) B、(c) C、(e) F。(c)の青矢印は層間剥離の縁を示す。(d)は(c)の黄色矩形で囲まれた領域の拡大画像で、緑破線ボックスは微細粒の存在を示す(カラー図オンライン)。
- Fig. 15—スキン層ありの破断試験片の側面を示すOM画像:(a) A、(b) B、(c) C。(a~c)の赤矢印はFig. 14(a~c)に対応する亀裂発生箇所を示す。(a1~a3)は(a)の黄色ボックスで囲まれた領域の拡大画像。(b1, b2)は(b)の青ボックスで囲まれた領域の拡大画像。(c1~c3)は(c)のピンクボックスで囲まれた領域の拡大画像(カラー図オンライン)。
- Fig. 16—スキン層ありのサンプルCの他の破断片側面(Fig. 15(c)に既に示されたものと相補的)のOM画像:(a) 表面スキン層とコールドフレークの描写、(b) (a)の黄色矩形で示される亀裂発生箇所の拡大画像。赤と白の破線はそれぞれ不均一スキン層と初期鋳造表面を示す(カラー図オンライン)。
- Fig. 17—(a) スキン層なしの破断試験片Fの側面を示すOM画像。(a1)と(a2)はそれぞれ(a)の黄色と青のボックスで囲まれた領域の拡大画像(カラー図オンライン)。
- Fig. 18—引張試験済み試験片の破断面を示すSEM画像:(a) 黄色と青の矢印がそれぞれ初晶α-AlとAl-Si共晶を示す破断面マトリックス、(b) Al-Si共晶、(c) Al固溶体内の破断したSi粒子、(d) 破断したチャイニーズスクリプト状α-Fe化合物、(e) 破断した(α-Fe)II化合物と破断していない(α-Fe)II化合物、(f) 破断していない(α-Fe)I化合物、(g) 白矢印がα-Alデンドライトアームを示す収縮ポロシティ。(b~e)の赤矢印は亀裂を示す(カラー図オンライン)。
- Fig. 19—チャイニーズスクリプト状α-Fe化合物の見え方:(a) 鋳造まま部品のOM画像、(b) 引張試験済み部品のSEM画像。
- Fig. 20—左から右へ時間経過に伴うダイ充填パターンのシミュレーション静止画像。
- Fig. 21—本研究で使用されたHPDC再生二次合金が示す0.2%耐力と全伸び、およびTrimet[37]のデータシートから得られた一次trimal®-05合金の特性範囲(ここに提示された図はオリジナルであり、引用元からのデータのみを使用)。
7. 結論:
HPDCプロセスで製造された再生二次AlSi10MnMg(Fe)合金(2mm肉厚)の調査に基づき、以下の結論が導かれた:
- 合金組成(Mn:Fe ≈ 2.1)は、有害なβ-Fe形成を効果的に抑制し、害の少ない多角形状およびチャイニーズスクリプト状α-Fe化合物の形成を促進した。チャイニーズスクリプト構造は3Dでは複雑に絡み合ったアームとして現れる。
- ミクロ組織は厚さ方向に勾配を示す: 微細粒スキン層、次に増加したAl-Si共晶、そして中心部に粗大なα-Alデンドライト。平均SDASはスキン層の3.6 µmから中心部の14.6 µmに増加し、これはそれぞれ約10 °C/sおよび約1 °C/sの推定冷却速度に対応する。硬度もこの勾配に従い、スキン層から中間層にかけて増加し、その後中心部に向かって減少する。
- スキン層の形成は連続的または均一ではなく、これはダイキャビティ内の複雑な溶湯流動と変化する熱伝達に起因する。「波と湖(waves and lakes)」欠陥に類似した不均一スキン構造が観察された。
- スキン層は耐力を向上させるいくつかの兆候を示すが、その不連続性と制限された厚さのために、この効果は限定的である可能性がある。しかし、不均一スキン層は延性を著しく制限し、突然の破断を引き起こす。
- 不均一スキン層は、隣接するマトリックスとの弱い結合のために、層間剥離(デラミネーション)誘起の亀裂を促進する。このメカニズムは突然の破壊につながる可能性があり、スキン層を持つ研究対象サンプルにおいては、鋳造欠陥やα-Fe化合物のような他の要因よりも引張延性に対してより有害であるように見える。
- 再生二次合金は、特に不均一スキン層形成の有害な影響を軽減できれば(例: 表面除去やプロセス最適化により)、市販の一次合金と同等の強度および延性レベルを達成する可能性を示している。
8. 参考文献:
- [1] J.G. Kaufman and E.L. Rooy: Aluminum Alloy Castings: Properties, Processes and Applications, ASM International, Detroit, 2004, pp. 7-20.
- [2] T.O. Mbuya, B.O. Odera, and S.P. Ng’ang’a: Int. J. Cast Met. Res., 2003, vol. 16, pp. 451-65. https://doi.org/10.1080/13640461.2003.11819622.
- [3] L. Wang, M. Makhlouf, and D. Apelian: Int. Mater. Rev., 1995, vol. 40, pp. 221-38. https://doi.org/10.1179/imr.1995.40.6.221.
- [4] L. Zhang, J. Gao, L.N.W. Damoah, and D.G. Robertson: Miner. Process. Extr. Metall. Rev., 2012, vol. 33, pp. 99–157. https://doi.org/10.1080/08827508.2010.542211.
- [5] G. Gustafsson, T. Thorvaldsson, and G.L. Dunlop: Metall. Trans. A, 1986, vol. 17, pp. 45-52. https://doi.org/10.1007/BF02644441.
- [6] P. Crepeau: Trans. Am. Foundryman’s Soc., 1995, vol. 103, pp. 361-66.
- [7] D. Apelian: Aluminum Cast Alloys: Enabling Tools for Improved Performance, North American Die Casting Association, Wheeling, 2009, pp. 5-18.
- [8] J.A. Taylor: Procedia Mater. Sci., 2012, vol. 1, pp. 19-33. https://doi.org/10.1016/j.mspro.2012.06.004.
- [9] S.A.V.S. p. A. Società Alluminio Veneto: Aluminium Alloys Ingots for Remelting: Alloy Data Sheet, S.A.V.S. p. A. Società Alluminio Veneto, 2020. https://www.sav-al.com/file?oid=613fle4c10834b044515e1f3. Accessed 26 July 2024.
- [10] Rheinhfelden Alloys: Primary Aluminium Alloys for Pressure Die Casting, Rheinhfelden Alloys, 2015. https://rheinfelden-alloys.eu/wp-content/uploads/2016/01/05-HB-DG_Ci_Sf_Cm_Td_Ma_RHEINFELDEN-ALLOYS_2015_EN.pdf. Accessed 26 July 2024.
- [11] L.A. Narayanan, F.H. Samuel, and J.E. Gruzleski: Metall. Mater. Trans. A, 1994, vol. 25A, pp. 1761-73. https://doi.org/10.1007/BF02668540.
- [12] M. da Silva, J. Pujante, J. Hrabia-Wiśnios, B. Augustyn, D. Kapinos, M. Węgrzyn, and S. Boczkal: Metals, 2024, vol. 14, p. 626. https://doi.org/10.3390/met14060626.
- [13] E. Cinkilic, M. Moodispaw, J. Zhang, J. Miao, and A.A. Luo: Metall. Mater. Trans. A, 2022, vol. 53A, pp. 2861-73. https://doi.org/10.1007/s11661-022-06711-4.
- [14] D. Bösch, S. Pogatscher, M. Hummel, W. Fragner, P.J. Uggowitzer, M. Göken, and H.W. Höppel: Metall. Mater. Trans. A, 2015, vol. 46A, pp. 1035–45. https://doi.org/10.1007/s11661-014-2700-8.
- [15] R. Lumley: JOM, 2019, vol. 71, pp. 382-90. https://doi.org/10.1007/s11837-018-3121-8.
- [16] F. Liu, H. Zhao, R. Yang, and F. Sun: Materials, 2019, vol. 12, p. 2065. https://doi.org/10.3390/ma12132065.
- [17] X.Y. Jiao, Y.X. Liu, J. Wang, W.N. Liu, A.X. Wan, S. Wiesner, and S.M. Xiong: J. Mater. Sci. Technol., 2023, vol. 140, pp. 201-09. https://doi.org/10.1016/j.jmst.2022.09.014.
- [18] R. Liu, J. Zheng, L. Godlewski, J. Zindel, M. Li, W. Li, and S. Huang: Mater. Sci. Eng. A, 2020, vol. 783, p. 139280. https://doi.org/10.1016/j.msea.2020.139280.
- [19] X.Y. Jiao, Y.F. Zhang, J. Wang, H. Nishat, Y.X. Liu, W.N. Liu, H.X. Chen, and S.M. Xiong: J. Mater. Process. Technol., 2021, vol. 298, p. 117299. https://doi.org/10.1016/j.jmatprotec.2021.117299.
- [20] X.Y. Jiao, C.F. Liu, Z.P. Guo, G.D. Tong, S.L. Ma, Y. Bi, Y.F. Zhang, and S.M. Xiong: J. Mater. Sci. Technol., 2020, vol. 51, pp. 54-62. https://doi.org/10.1016/j.jmst.2020.02.040.
- [21] G. Ubertalli, F. D’Aiuto, S. Plano, and D. De Caro: Procedia Struct. Integr., 2016, vol. 2, pp. 3617-24. https://doi.org/10.1016/j.prostr.2016.06.451.
- [22] E. Fracchia, F.S. Gobber, and M. Rosso: Metals, 2020, vol. 10, p. 618. https://doi.org/10.3390/met10050618.
- [23] X.Y. Jiao, P.Y. Wang, Y.X. Liu, J. Wang, W.N. Liu, A.X. Wan, L.J. Shi, C.G. Wang, and S.M. Xiong: J. Mater. Res. Technol., 2023, vol. 25, pp. 1129-40. https://doi.org/10.1016/j.jmrt.2023.05.281.
- [24] A. Niklas, A. Baquedano, S. Orden, E. Noguès, M. Da Silva, and A.I. Fernández-Calvo: Key Eng. Mater., 2016, vol. 710, pp. 244-49. https://doi.org/10.4028/www.scientific.net/KEM.710.244.
- [25] J.M. Sanchez, M. Arribas, H. Galarraga, M. Garcia de Cortazar, M. Ellero, and F. Girot: Heliyon, 2023, vol. 9, p. e13005. https://doi.org/10.1016/j.heliyon.2023.e13005.
- [26] E. Cinkilic, C.D. Ridgeway, X. Yan, and A.A. Luo: Metall. Mater. Trans. A, 2019, vol. 50A, pp. 5945-56. https://doi.org/10.1007/s11661-019-05469-6.
- [27] J. Piątkowski, M. Hejne, and R. Wieszała: Arch. Mater. Sci. Eng., 2023, vol. 123, pp. 5-12. https://doi.org/10.5604/01.3001.0053.9750.
- [28] L.B. Otani, J. Soyama, G. Zepon, A. Costa e Silva, C.S. Kiminami, W.J. Botta, and C. Bolfarini: J. Phase Equilib. Diffus., 2017, vol. 38, pp. 298-304. https://doi.org/10.1007/s11669-017-0542-y.
- [29] A. Bakedano, R. González-Martínez, A. Niklas, M. Da Silva, M. Garat, and A.I. Fernández-Calvo: 71st World Foundry Congress on Advanced Sustainable Foundry, 2014.
- [30] A. Niklas, A.I. Fernández-Calvo, A. Bakedano, S. Orden, M. Da Silva, E. Nogués, and E. Roset: Metall. Ital., 2016, vol. 108, pp. 9-12.
- [31] A. Niklas, A. Bakedano, S. Orden, M. da Silva, E. Nogués, and A.I. Fernández-Calvo: Mater. Today Proc., 2015, vol. 2, pp. 4931-38. https://doi.org/10.1016/j.matpr.2015.10.059.
- [32] H. Zheng, Y. Jiang, F. Liu, and H. Zhao: J. Alloys Compd., 2024, vol. 976, p. 173167. https://doi.org/10.1016/j.jallcom.2023.173167.
- [33] Z. Yuan, Z. Guo, and S.M. Xiong: J. Mater. Sci. Technol., 2019, vol. 35, pp. 1906–16. https://doi.org/10.1016/j.jmst.2019.05.011.
- [34] H.M. Yang, Z. Guo, and S.M. Xiong: J. Mater. Process. Technol., 2020, vol. 275, p. 116377. https://doi.org/10.1016/j.jmatprotec.2019.116377.
- [35] S. Otarawanna, C.M. Gourlay, H.I. Laukli, and A.K. Dahle: Mater. Chem. Phys., 2011, vol. 130, pp. 251-58. https://doi.org/10.1016/j.matchemphys.2011.06.035.
- [36] Y. Yang, S. Huang, J. Zheng, L. Yang, X. Cheng, R. Chen, and H. Wei-Jian: Trans. Nonferr. Met. Soc. China, 2024, vol. 34, pp. 378-91. https://doi.org/10.1016/S1003-6326(23)66405-2.
- [37] Trimet-05: Trimal®-05-Die Cast Alloy for Crash-Relevant Applications, Trimet-05, 2008. https://www.trimet.eu/en/products/foundry-alloys/trimal-05. Accessed 26 July 2024.
- [38] C.M. Dinnis, J.A. Taylor, and A.K. Dahle: Scripta Mater., 2005, vol. 53, pp. 955-58. https://doi.org/10.1016/j.scriptamat.2005.06.028.
- [39] J.I. Goldstein, D.E. Newbury, J.R. Michael, N.W.M. Ritchie, J.H.J. Scott, and D.C. Joy: Scanning Electron Microscopy and X-Ray Microanalysis, 4th ed. Springer, New York, 2018. https://doi.org/10.1007/978-1-4939-6676-9.
- [40] B. Dybowski, A. Kiełbus, and Ł Poloczek: Eng. Fail. Anal., 2023, vol. 150, p. 107223. https://doi.org/10.1016/j.engfailanal.2023.107223.
- [41] Q. Han and J. Zhang: Metall. Mater. Trans. B, 2020, vol. 51B, pp. 1795-1804. https://doi.org/10.1007/s11663-020-01858-0.
- [42] H. Yang, S. Ji, and Z. Fan: Mater. Des., 2015, vol. 85, pp. 823-32. https://doi.org/10.1016/j.matdes.2015.07.074.
- [43] X. Dong, X. Zhu, and S. Ji: J. Mater. Process. Technol., 2019, vol. 266, pp. 105-13. https://doi.org/10.1016/j.jmatprotec.2018.10.030.
- [44] X.Y. Jiao, C.F. Liu, Z.P. Guo, H. Nishat, G.D. Tong, S.L. Ma, Y. Bi, Y.F. Zhang, S. Wiesner, and S.M. Xiong: J. Alloys Compd., 2021, vol. 862, p. 158580. https://doi.org/10.1016/j.jallcom.2020.158580.
- [45] S. Otarawanna, C.M. Gourlay, H.I. Laukli, and A.K. Dahle: Metall. Mater. Trans. A, 2009, vol. 40A, pp. 1645-59. https://doi.org/10.1007/s11661-009-9841-1.
- [46] S. Ji, Y. Wang, D. Watson, and Z. Fan: Metall. Mater. Trans. A, 2013, vol. 44A, pp. 3185-97. https://doi.org/10.1007/s11661-013-1663-5.
- [47] S. Ji, W. Yang, F. Gao, D. Watson, and Z. Fan: Mater. Sci. Eng. A, 2013, vol. 564, pp. 130-39. https://doi.org/10.1016/j.msea.2012.11.095.
- [48] H. Becker, T. Bergh, P.E. Vullum, A. Leineweber, and Y. Li: Materialia, 2019, vol. 5, p. 100198. https://doi.org/10.1016/j.mtla.2018.100198.
- [49] Α.Κ.Μ.Α. Ahamed and H. Kato: Mater. Trans., 2008, vol. 49, pp. 1621-28. https://doi.org/10.2320/matertrans.F-MRA2008814.
- [50] H. Kato, T. Suzuki, Y. Annou, and K. Kageyama: Mater. Trans., 2004, vol. 45, pp. 2403-09. https://doi.org/10.2320/matertrans.45.2403.
- [51] Z.W. Chen: Mater. Sci. Eng. A, 2003, vol. 348, pp. 145-53. https://doi.org/10.1016/S0921-5093(02)00747-5.
- [52] S. Midson: Die Casting Defects, North American Die Casting Association. https://pdfcoffee.com/nadca-overview-of-defets-in-die-casting-pdf-free.html. Accessed 4 Sep 2024.
9. 著作権:
- 本資料は「BISWAJIT DALAI, SIMON JONSSON, MANEL DA SILVA, LIANG YU, and JÖRGEN KAJBERG」による論文です。「Inhomogeneous Skin Formation and Its Effect on the Tensile Behavior of a High Pressure Die Cast Recycled Secondary AlSi10MnMg(Fe) Alloy」に基づいています。
- 論文の出典: https://doi.org/10.1007/s11661-024-07631-1
本資料は上記の論文に基づいて要約されており、商業目的での無断使用は禁じられています。
Copyright © 2025 CASTMAN. All rights reserved.