本稿は、「SAE International」が発行した論文「The Application of Magnesium Die Casting to Vehicle Closures」を基に作成されています。
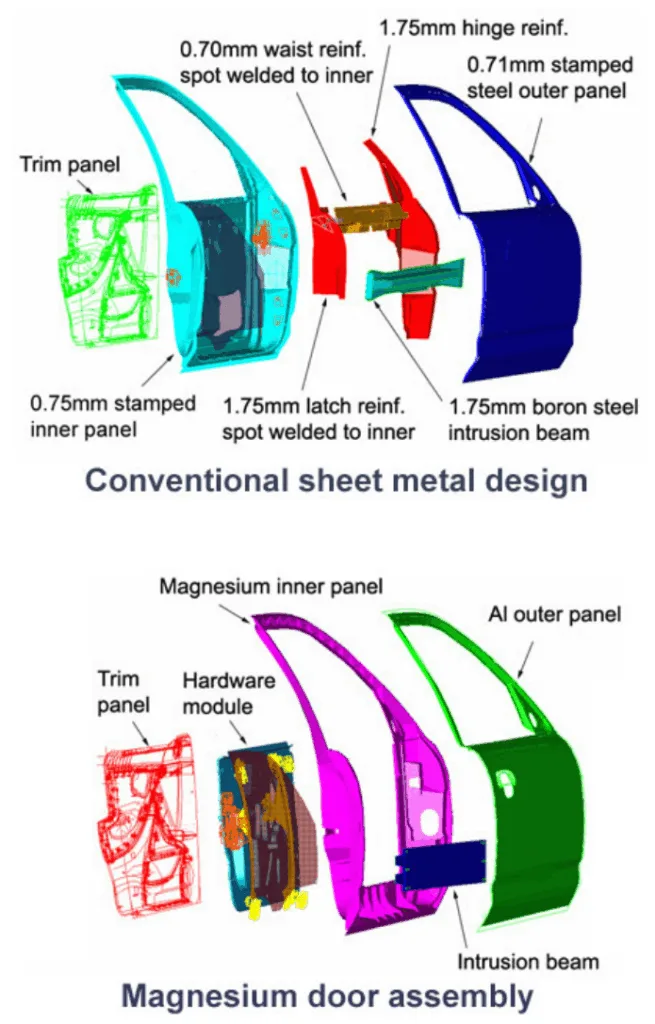
1. 概要:
- タイトル: The Application of Magnesium Die Casting to Vehicle Closures (マグネシウムダイカストの車両クロージャーへの応用)
- 著者: Patrick J. Blanchard, Gregory T. Bretz, Saravanan Subramanian and James E. deVries (Ford Motor Company); Andrew Syvret, Andrew MacDonald and Peter Jolley (Aston Martin)
- 発行年: 2005
- 発行学術誌/学会: SAE International
- キーワード: 論文に明記されていません。
2. 抄録:
過去10年間で、マグネシウムダイカスト技術の進歩により、大型軽量薄肉ダイカスト部品の製造が可能となり、低投資の車体構造技術への新たなアプローチが提供されています。その結果、多くのOEMが、投資削減の機会と最大50%の潜在的な重量削減効果から、マグネシウム製ドアクロージャーシステムに関心を示しています。しかし、このような用途では、製品エンジニアは、展伸材製品と比較して弾性係数と延性が低い材料を使用し、衝突が重要な用途で剛性と強度を設計するという課題に直面しています。サイドドアシステムのコンセプトデザインは文献で発表されており、構造性能目標が達成可能であることを示しています。しかし、現在までの量産設計では、構造荷重を処理するために、ダイカストに取り付けられた多数の補助的な板金補強材が特徴となっています。このアプローチは依然として性能上の利点を提供できますが、追加の工具費と組立費は、全体重量と事業性の両方に悪影響を及ぼします。対照的に、本稿で提示されるマグネシウムドアのコンセプトは、板金スタンピング部品の大部分を単一のマグネシウムダイカストで置き換えるように設計されたサイドドアシステムの開発について説明しています。設計、解析、試作、試験段階の概要が、2004年モデル車両用の量産ドアシステムの開発に加えて報告されています。製造および試験結果のレビューは、マグネシウムが低投資の軽量車両クロージャーの製造に効果的に使用できることを示しています。
3. 序論:
車両質量が燃費に与える影響はよく理解されており、企業平均燃費を向上させるための重要な要因と考えられています。実際、1980年代初頭には車両の空車重量が平均20%減少したため、大幅な改善が報告されました[1]。しかし、車両モデルに新しい機能や利便性を追加する傾向が続いているため、重量目標は現在、ますます大きな圧力にさらされています。その結果、OEMはコストを管理しながら消費者のニーズを満たすために、幅広い材料とプロセスを検討してきました。場合によっては、鋼をアルミニウムに単純に置き換えることも行われています[2]。しかし、アルミニウム合金の成形限界は、その用途をしばしば制限します。これを克服するために、スタンピング、押出、鋳造を組み合わせたハイブリッドドアシステムが開発されました。しかし、最終的な重量上の利点は、組立の複雑さと変動費の増加によって容易に相殺される可能性があります。
一方、マグネシウムは多くの自動車用途で成功裏に使用されてきました。低密度や高い強度対重量比などの特性により、マグネシウムは部品の質量削減に魅力的な材料となっています。その結果、過去10年間でいくつかの構造用鋳物が報告されており、より大きく、より複雑なダイカストが実証されるにつれて、用途の範囲が拡大しています[3,4]。いくつかのプログラムの焦点となっている特定の用途の1つは、ダイカスト車両クロージャーパネルの開発です[5,6,7]。これらの提案の多くはコンセプトとして残っていますが、リフトゲートとサイドドアの量産バージョンが登場しています[6]。これらの中で最も注目すべきは、メルセデスがCLおよびSLモデルに実装したものです。しかし、マグネシウム鋳物の荷重を制限し、構造要件を満たすためにドアアセンブリに補助的な補強材を固定するという一般的な傾向は依然として残っています。これは再び、全体的な重量と組立コストに悪影響を与える可能性があります。
本稿は、主要な補強材をダイカストに統合することにより、補助的なスタンピングを排除するように設計された新しいマグネシウムドアインナーパネルの開発に焦点を当てています。したがって、マグネシウムパネルはドア構造の不可欠な部分となり、車両の静的および動的衝突性能に貢献します。初期コンセプトの設計、解析、試験の概要が提示され、続いてMY2004アストンマーティンDB9に実装された量産意図のドアシステムの開発が続きます。両方の設計の最終的な重量評価に加えて、従来の鋼製スタンピングと比較した技術コストを特定するための経済分析が提供されます。
4. 研究の概要:
研究テーマの背景:
自動車産業は、燃費向上と性能向上のために車両質量を削減するという継続的な圧力に直面しています。マグネシウムダイカスト技術は、特に車両クロージャー向けに、大型で軽量な薄肉部品を製造するための有望な手段を提供し、投資削減と大幅な重量削減の可能性を秘めています。しかし、衝突が重要な用途向けにマグネシウムを設計するには、従来の鋼と比較して弾性係数と延性が低いという課題に対処する必要があります。
従来の研究状況:
従来の研究には、達成可能な構造性能を示すマグネシウムサイドドアシステムのコンセプトデザインが含まれています。しかし、既存の量産設計では、構造荷重を管理するためにダイカストに取り付けられた多数の補助的な板金補強材が組み込まれていることがよくあります。このアプローチはいくつかの利点を提供しますが、コスト、複雑さ、重量が増加し、全体的な利点が減少します。マグネシウムクロージャーの注目すべき例としては、メルセデスCLおよびSLモデルのクロージャーがあり、これらも補強材を使用する傾向があります。
研究の目的:
本研究の主な目的は、主要な補強材をダイカスト自体に統合することにより、補助的なスタンピングの必要性を排除する新しいマグネシウムドアインナーパネルを開発することでした。本研究は、マグネシウムパネルがドア構造の不可欠な部分として機能し、静的および動的衝突性能に貢献できることを実証することを目的としていました。具体的な目的は次のとおりです。
- 初期コンセプトの設計、解析、試作、試験の概要。
- MY2004アストンマーティンDB9用の量産ドアシステムの開発の詳細。
- 両方の設計の重量評価の提供。
- 従来の鋼製スタンピングと比較した技術コストを特定するための経済分析の実施。
研究の核心:
本研究は、主に2つの段階で実施されました。
- コンセプト実証(フォード・コンターベース): この段階では、MY2000フォード・コンターをベースにしたマグネシウムドア構造の開発と評価を行いました。これには、CAEを用いた設計、重力砂型鋳造による試作品の製作、静的耐久性試験、および生産用の高圧ダイカストを想定した事業性の検討が含まれました。
- 生産実装(アストンマーティンDB9): コンセプト評価後、MY2004アストンマーティンDB9用の生産意図ドア設計が開発されました。この段階では、衝突性能と腐食保護に焦点が当てられました。生産用ダイカスト金型が製造され、製造検証や周期的腐食試験を含む包括的な試験のために部品が生産されました。
5. 研究方法論
研究設計:
本研究は、2段階の開発アプローチに従いました。
- 第1段階:コンセプト実証(フォード・コンター):
- MY2000フォード・コンターのフルフレームサイドドアアセンブリに基づく設計。
- 重力砂型鋳造を用いた試作品の製作。
- 静的耐久性に関するCAEと試作品試験の組み合わせによる技術評価。
- 高圧ダイカストの事業性開発。
- 第2段階:実装(アストンマーティンDB9):
- MY2004アストンマーティンDB9用の生産意図ドア設計の開発。
- 衝突性能と腐食保護に焦点。
- 生産用ダイカスト金型を用いた部品の製造。
- 保護システムを評価するための周期的腐食試験。
データ収集および分析方法:
- コンピュータ支援エンジニアリング(CAE): 有限要素モデルを使用して、主要な荷重条件(ねじり剛性、横剛性、たるみ、ドロップオフなど)および非線形衝突解析(例:FMVSS-214側面衝突)に対するシステム応答をシミュレートしました。
- 試作品試験:
- フォード・コンター試作品の静的耐久性試験:ねじり剛性、フレーム横剛性、ドアドロップオフ、ドアたるみ、ドアスラム(84,000サイクル)。
- 実験的検証(アストンマーティンDB9):
- 特定の場所から採取したサブサイズの引張試験片(ASTM E8)を使用して、ダイカストドアインナーパネルから局所的なひずみデータを取得しました。
- 実車側面衝突試験(静的FMVSS-214)。
- 腐食試験: アルミニウムクーポンに接合された鋳造マグネシウムサンプルに対する周期的腐食試験(フォード試験方法BI123-01、100サイクル)を実施し、さまざまな表面前処理とコーティングを評価しました。
- 寸法分析: プロセス開発中に生産されたダイカストを測定し、公差への準拠を評価しました。
- 経済性評価: さまざまな生産量シナリオ(低自動化/投資および高自動化/投資)について、マグネシウムドアアセンブリの総費用と従来の鋼製スタンピングを比較しました。
研究トピックと範囲:
- 主要トピック: 車両クロージャー、特にサイドドアへのマグネシウムダイカスト技術の応用。
- 主要調査分野:
- 剛性、強度、耐衝突性のためのマグネシウムダイカストドアインナーパネルの設計。
- 部品点数と組立の複雑さを軽減するためのダイカストへの補強材の統合。
- 従来の鋼製ドアと比較して達成可能な重量削減。
- 大型薄肉マグネシウムダイカストの製造可能性と課題。
- 異種金属アセンブリにおけるマグネシウムに適した腐食保護システムの評価と選択。
- さまざまな生産量におけるマグネシウムダイカストドアの経済的実行可能性。
- 範囲: 本研究は、初期コンセプト(フォード・コンターに基づく)から、少量生産の高級車(アストンマーティンDB9)に実装された生産意図設計までの開発プロセスを網羅しました。
6. 主要な結果:
主要な結果:
フォード・コンター コンセプト段階:
- 重量削減: マグネシウムドアアセンブリ(9.62kg)は、従来のプレス鋼設計(15.56kg)と比較して5.94kg(38%)の重量削減を達成しました(Table 1)。マグネシウムインナーパネルとハードウェアモジュールは5.83kgで、すべての補強材を含む8.09kgの鋼製インナーパネルよりも28%軽量でした。
- 剛性上の利点: マグネシウムインナーパネルの高い剛性により、アウターパネルに低密度のアルミニウム/プラスチックラミネートを使用することが可能になり、重量削減に大きく貢献しました(鋼製アウターパネルと比較して3.67kg)。
- 性能試験 (Table 2):
- CAE予測では、5つの主要な試験仕様すべてに適合することが示されました。
- 実験試験では、ねじり剛性で不合格(実際5.7mmに対し、要件<4mm)、ドアのたるみが予測よりも大きい(実際13.3mmに対し、CAE 5.4mm)ことが明らかになりましたが、依然として仕様内(<38mm)でした。これらの不一致は、試作品のヒンジピンクリアランスと試作品ヒンジの塑性変形に起因すると考えられました。
- ドアスラム耐久試験は成功し、84,000サイクル(寿命の3倍)後も損傷はありませんでした。
- 経済性分析 (Figure 4 & 5):
- 少量生産(例:年間10,000台)では、マグネシウムドアアセンブリは、主に部品統合と工具投資の削減により、鋼製対応品よりも13%安価でした。
- 鋼製スタンピングがより費用対効果が高くなる損益分岐点は、年間約30,000台でした。
- 材料価格(基準$2.90/kg)と機械稼働率がコストに影響を与える主要な要因として特定されました。
アストンマーティンDB9 実装段階:
- 設計: 非モジュラー構造のフレームレスドアシステムが開発されました。アウターベルト補強材を含む主要な補強材がダイカストインナーパネルに統合されました。
- 重量削減:
- 試作品のアストンマーティンDB9ドアインナーパネルの重量は3.711kg(Table 3)で、ドアインホワイトアセンブリ全体の重量9.749kgに貢献しました。
- ダイ充填のためのさらなる解析により、局部的な肉厚増加が行われ、最終的なマグネシウムインナーパネルの重量は4.32kgとなりました。
- 最終的なDB9ドアアセンブリは、同等のプレス鋼アセンブリと比較して43%の重量削減が見込まれました。
- 静的耐久性 (Figure 8): 肉厚はCAEおよびダイカスト充填シミュレーションに基づいて最適化されました。例えば、上部ヒンジ取り付け部(セクション5)の肉厚を20%増加させると、ドアドロップ変形に対する剛性が36.4%向上しました。
- 衝突性能 (AM50合金):
- CAEシミュレーション(FMVSS-214)では、ドアアセンブリがこの試験の要件を大幅に上回ることが示されました(Figure 10)。
- ダイカストサンプルを用いた引張試験では、平均破断ひずみが要件を上回りました。ラッチ、ビーム取り付け部、ウエストレール部では15%以上、ヒンジ部では最大28%でした。ロッカー部は平均8%でした(Figure 11)。
- 実車静的FMVSS-214側面衝突試験では、6インチのラム変位で97%、12インチで87%、18インチで60%と、各段階で要件を上回る性能を示しました(Figure 12)。延性挙動が観察されました。
- 寸法管理 (Figure 13): 全体公差は一般的に+/- 0.5mmに維持されました。量産前インナーパネルでは、測定された22点中21点が仕様を満たしました。1つの位置は0.039mm仕様外でしたが、これはさらなるダイカストプロセス調整によって対応されました。
- 腐食保護:
- トップコートを施した陽極酸化ベース層が最も効果的な保護を提供しました。
- エポキシポリエステル粉体塗装と組み合わせたクロムベースの化成処理は、ほぼ同等の性能を示し、コストを考慮して使用が選択され、クロムフリーシステムへの計画的な移行が予定されていました。
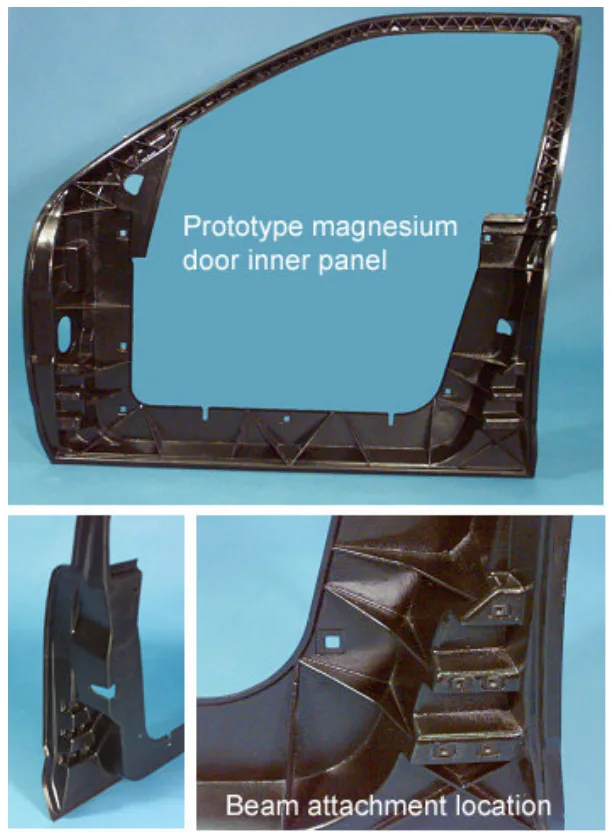
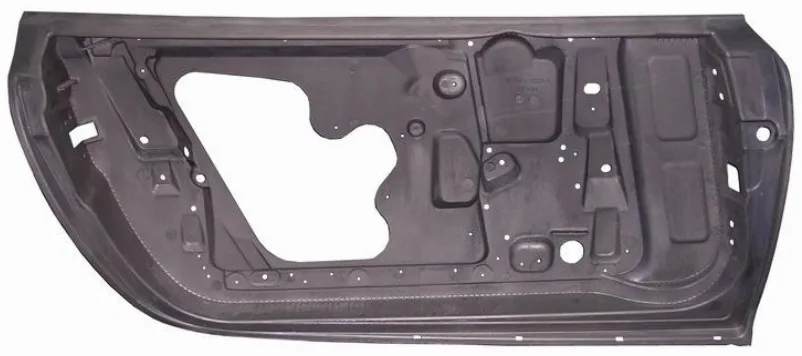
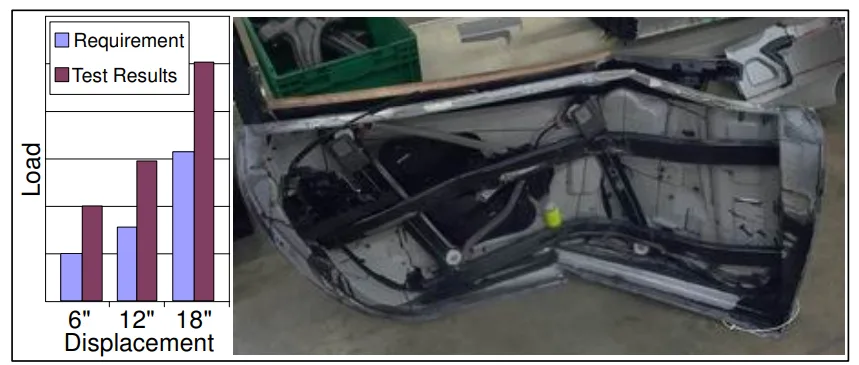
図の名称リスト:
- Figure 1. Lightweight magnesium door architecture.
- Figure 2. Casting section thickness variations magnesium door inner panel.
- Figure 3. Magnesium door inner panel prototype based upon the MY2000 Ford Contour
- Figure 4. Economic comparison of conventional and magnesium door assemblies for the MY2000 Ford Contour.
- Figure 5. Sensitivity analysis of piece cost to model input data.
- Figure 6. Aston Martin DB9 magnesium door assembly.
- Figure 7. Aston Martin DB9 magnesium door inner panel.
- Figure 8. The effect of wall thickness on door drop off.
- Figure 9. FMVSS 214 test setup.
- Figure 10. Strain map of a preliminary magnesium door inner panel design following static FMVSS-214 testing.
- Figure 11. Mean tensile failure strains of castings by location (see Figure 10).
- Figure 12. FMVSS-214 side impact results for the DB9 magnesium door assembly.
- Figure 13. Dimensional data for a pre-production DB9 magnesium die cast door inner panel.
7. 結論:
この2段階の開発プログラムの結果は、マグネシウムダイカストがサイドドアアセンブリ内で完全に構造部材として効果的に使用できることを示しています。主要な機能を統合した単一のマグネシウム鋳物で複数の金属スタンピング部品を置き換えることにより、大きな利点が得られました。これらには、部品点数の削減によるサブアセンブリプロセスの簡素化、工具投資の削減が含まれます。さらに、このアプローチは、性能と重量の両方について設計を最適化する機会を提供します。アストンマーティンDB9のドアインホワイトアセンブリの予測重量削減率は43%でした。
経済性評価では、中低生産量の派生プログラムの場合、このマグネシウムダイカスト技術はコストペナルティなしで利点を提供できることが示されました。しかし、大量生産車両の場合、従来のプレス鋼アセンブリが依然として最も費用対効果の高い製造ルートです。2つの製造技術の正確な損益分岐点を決定するには、特定の対象用途の詳細な分析が必要となります。
8. 参考文献:
- [1] http://www.nhtsa.dot.gov/cars/rules/cafe/NewPassengerCarFleet.htm.
- [2] Seksaria, D.C. and R.K. Patel. "An Ultra-Light Thin Sliding Door Design - A Multi Product Multi Material Solution." SAE Technical Paper Series, 2002-01-0391.
- [3] Balzer, J., et al. "Structural Magnesium Front End Support Assembly." SAE Technical Paper Series, 2003-01-0186.
- [4] Friedrich, H. and S. Schumann, "Research for a "new age in magnesium" in the automotive industry." Journal of Materials Processing Technology, 2001. 117(3): p. 276-281.
- [5] Jonason, P., et al. "MAGDOOR- Magnesium in Structural Application." SAE Technical Paper Series,1999-01-3198.
- [6] Schreckenberger, H., M. Papke, and S. Eisenberg. "The Magnesium Hatchback of the 3-Liter Car: Processing and Corrosion Protection." SAE Technical Paper Series, 2000-01-1123.
- [7] "Design of a magnesium/aluminum door frame", Automotive Engineering, 1993, Vol 101, 5,pp 57-60.
- [8] Federal Motor Vehicle Safety Standard 214, Side Impact Protection.
- [9] Ames, W. and W. Altenhof. "Observations of the Relative Performance of Magnesium and Aluminum Steering Wheel Skeletons with Identical Geometry." SAE Technical Paper Series, 2000-01-0784.
- [10] Aune, T. and L. Riopelle. "An Evaluation of the Mechanical Properties Critical to the Design of Interior Magnesium Components." SAE Technical Paper Series, 960415.
- [11] Alain, R. et al. "Robustness of Large Thin Wall Magnesium Die Castings for Crash Applications." SAE Technical Paper Series, 2004-01-0131.
- [12] Ford Laboratory Test Method BI 123-01. "Painted Sheet Metal Corrosion Test (Laboratory Simulated Arizona Proving Ground Test)", 2001.
- [13] Bretz, G.T., et al. "Adhesive Bonding and Corrosion Protection of a Die Cast Magnesium Automotive Door." The Minerals, Metals and Materials Society. 2004: Magnesium Technology 2004.
- [14] Blanchard, P.J., et al. "Evaluation of Corrosion Protection Methods for Magnesium Alloys in Automotive Applications." The Minerals, Metals and Materials Society, Magnesium Technology 2005.
9. 著作権:
- 本資料は、「Patrick J. Blanchard, Gregory T. Bretz, Saravanan Subramanian, James E. deVries, Andrew Syvret, Andrew MacDonald and Peter Jolley」氏による論文です。「The Application of Magnesium Die Casting to Vehicle Closures」に基づいています。
- 論文の出典: [https://doi.org/10.4271/2005-01-0338]
本資料は上記論文に基づいて要約したものであり、商業目的での無断使用を禁じます。
Copyright © 2025 CASTMAN. All rights reserved.