本紹介論文は、「[Machines]」によって発行された論文「Double-Sided Surface Structures with Undercuts on Cold-Rolled Steel Sheets for Interlocking in Hybrid Components」に基づいています。
![Figure 1. Scheme of the rolling process for surface structures (as proposed by Senge et al. [15]); view
in the normal direction (ND) and transverse direction (TD)](https://castman.co.kr/wp-content/uploads/image-1904-1024x219.webp)
1. 概要:
- タイトル: ハイブリッド部品のインターロックのための冷間圧延鋼板上のアンダーカット付き両面表面構造 (Double-Sided Surface Structures with Undercuts on Cold-Rolled Steel Sheets for Interlocking in Hybrid Components)
- 著者: Aron Ringel, Sindokht Shayan and David Bailly
- 発行年: 2024
- 発行学術誌/学会: Machines
- キーワード: interlocking; multi-material components; structured cold rolling; FE-modelling
2. 抄録:
輸送部門において温室効果ガス排出量を削減したり、電気自動車の航続距離を延長したりするためには、軽量化戦略が不可欠です。軽量組立戦略の分野では、マルチマテリアル設計が大きな可能性を提供します。自動車分野で一般的に使用されるアルミニウムや鋼などの材料の接合は、溶融溶接などの従来プロセスが不適切であるため、課題をもたらします。したがって、新しい技術が設計オプションを拡張できます。以前の研究では、鋼板上のアンダーカット付き冷間圧延表面構造とダイカストアルミニウム間の機械的インターロックが提示されました。この方法は、今回、両方のシート表面に接合部を持つより複雑な用途向けに、両面構造へと拡張されました。両面構造の製造を調査するために、数値シミュレーションと検証実験が実施されました。さらに、上部構造と下部構造の相互の位置合わせが、結果として得られる構造形状と圧延荷重に及ぼす影響が分析されました。シフト(shifted)配置では、より有利な幾何学的パラメータ(例:24%大きいアンダーカット)と、約24.1%低い成形荷重(20%の高さ減少時)が観察されました。しかし、対応する実験では、構造化ローラーの著しく高い摩耗が発生しました。
3. 緒言:
軽量構造は、部品特性(剛性や衝突安全性など)を維持しつつ、温室効果ガス排出量の削減や電気自動車の航続距離延長の要求に応えるため、輸送部門において不可欠です[1, 2]。特に、低密度のアルミニウムと高強度鋼を組み合わせたマルチマテリアル設計は、魅力的な解決策です[3]。しかし、これらの異種材料を接合する際、溶接のような一般的な技術は脆い金属間化合物(IMP)を生成する可能性があります[4]。そのため、リベット接合やクリンチングのような機械的接合、ハイブリッド成形や鋳造プロセスを含む成形による接合プロセスが代替案として提供されます[5, 6, 7, 8]。特にハイブリッド鋳造は、複雑な部品形状と大量生産を可能にし、冶金的結合[9]または機械的インターロック[7]を達成する可能性があります。機械的インターロックは通常、表面構造化とその後の組立ステップを含みます。広い鋼板表面を構造化する有望な方法の一つは、多パス冷間圧延プロセスを用いてアンダーカット付きのチャネル構造を作成し、その後、例えばダイカストアルミニウムで充填することです[15, 16]。このプロセスは、以前に片面構造について研究され、最大45 MPaの接合強度を達成しました[16]。初期の構造圧延パスとそれに続く平坦化パスによりアンダーカット(Figure 1)が形成されます。本研究は、ルーフクロスビーム断面(Figure 2)に基づくデモンストレーター部品など、より複雑な部品に必要な両面構造へと概念を拡張し、鋼板インサートの両面に構造を製造するプロセスを調査します。
4. 研究概要:
研究テーマの背景:
特に鋼とアルミニウムを組み合わせた軽量マルチマテリアル部品の開発は、自動車産業にとって極めて重要です。溶融溶接で一般的な脆い金属間化合物の形成を回避する効果的な接合方法が必要です。ハイブリッド鋳造(例:高圧ダイカスト - HPDC)前の表面構造化による機械的インターロックは、実行可能な代替手段です。
先行研究の状況:
先行研究では、ダイカストアルミニウムとの機械的インターロックのために、鋼板上にアンダーカット付きの片面表面構造を作成する多パス冷間圧延プロセス(構造圧延後の平坦化圧延)が確立されました[15]。研究では、プロセスパラメータ、結果として得られる形状(アンダーカット Wf-uc、内部ノッチ Wf-no)、接合強度(最大45 MPa)[16]、プロセスのFEモデリング[17]、およびその後の曲げの影響[20]が調査されました。両面構造を必要とするデモンストレーター部品が概念化され、鋳造パラメータに焦点を当てた複合強度が分析されました[21]。しかし、成形プロセス分析は片面構造に限定されていました。
研究目的:
主な目的は、確立された冷間圧延および平坦化技術を使用して両面表面構造を製造する際の材料流動と構造形成を理解することでした。具体的には、両側からの同時圧痕がチャネルとアンダーカットの形成にどのように影響するかを調査し、2つの異なる配置、すなわち「ミラー(mirrored)」配置と「シフト(shifted)」配置(Figure 3)を比較することを目的としました。目標は、この理解を用いて、アンダーカット幅と結果として得られる接合強度に関してプロセスを最適化することでした。
中核研究:
本研究では、DC04鋼板上に両面構造を作成するために、冷間圧延および平坦化法を拡張しました。2つの構成が調査されました:ミラー配置(リブ対リブ、チャネル対チャネル)とシフト配置(リブ対チャネル)。有限要素(FE)シミュレーション(Abaqusを使用)が開発され、物理的な圧延実験によって検証されました。研究では、配置が結果として得られる構造形状(チャネル深さ ∆hs、アンダーカット幅 Wf-uc、内部ノッチ長さ Wf-no)および構造圧延と平坦化圧延の両パス中の必要な圧延荷重に及ぼす影響を分析しました。
5. 研究方法論
研究設計:
本研究では、両面表面構造に対する2つの異なる配置(ミラーおよびシフト)を調査する比較研究設計を採用しました。方法論は、数値シミュレーション(2D FEモデリング)と実験的検証(構造冷間圧延実験)を組み合わせました。
データ収集および分析方法:
- FEシミュレーション: 以前の片面モデル[17]に基づき、Abaqus 2017で2D FEモデルが開発され、平面ひずみ条件を仮定しました。モデルは、剛体ローラー(パンチ)を使用した構造圧延とその後の平坦化をシミュレーションし、任意ラグランジュ・オイラー(ALE)メッシングとパス間のフィールド変数(応力、ひずみ)のマッピング[23]を組み込みました。摩擦係数 µ = 0.07が使用されました[22]。メッシュサイズと摩擦感度に関する収束研究が実施されました。幾何学的特徴(∆hf, Wf-uc, Wf-no)はPythonスクリプトを使用して評価されました。2Dシミュレーションからの圧延荷重は、実験との比較のために式(6)を使用して変換されました。
- 実験的検証: 圧延は、Dreistern P3.160ロール成形機を使用してDC04鋼板(ho = 2.0 mm)で行われました。プロファイルローラー(半径92.5 mm)が初期構造を作成し、フラットローラー(半径93.0 mm)が5.8 m/minで平坦化圧延を実行しました。側面ガイドレールが使用されました。圧延荷重はロードセルを使用して測定されました。断面はウォータージェット切断、研磨、および3%ナイタールエッチングによって準備されました。形状はキーエンスVHX-7000デジタルマイクロスコープを使用して測定されました。高さ減少率(ɛh,1, ɛh,2)および平均幾何学的特徴(Wf-uc, Wf-no)は、式(1, 3, 4, 5)を使用して計算されました。
研究トピックと範囲:
研究は、構造化冷間圧延および平坦化による冷間圧延DC04鋼板上の両面アンダーカット構造の製造プロセスに焦点を当てました。範囲には以下が含まれます:
- 両面構造作成の実現可能性調査。
- 上部および下部構造の「ミラー」対「シフト」配置の比較。
- FEシミュレーション(PEEQ)および実験断面を使用した材料流動分析。
- プロセスパラメータ(高さ減少率)の関数としての結果形状(チャネル深さ、アンダーカット幅、内部ノッチ長さ)の定量化。
- 両方の配置およびプロセスステップに対する圧延荷重の測定とシミュレーション。
- 実験データによるシミュレーション結果の検証。
6. 主要な結果:
主要な結果:
- 材料流動: FEシミュレーション(Figure 6)とエッチングされた実験断面(Figure 7)は、2つの配置で異なる材料流動パターンを示しました。ミラー配置はチャネルからリブへの横方向および垂直方向の流動を示唆し、シフト配置はチャネルとリブの交差点でのせん断の証拠を示しました。
- 構造圧延: 両面構造の実験的なチャネル深さ形成は、以前の片面研究[17]と比較してシミュレーションとの良好な一致を示しました(Figure 8)。総チャネル深さ(∆hs = ∆hs,up + ∆hs,low)1.0 mmは、ミラー配置で約27%の高さ減少率(ɛh,1)、シフト配置で26%で達成されました(Table 1)。実験的に、ミラー配置はシフト配置と比較して著しく高い圧延荷重(20% ɛh,1で約24.1%高い)を必要としました(Figure 10a)。これは、異なる材料流動メカニズムによる可能性があります。
- 平坦化: シミュレーションされたアンダーカット幅(Wf-uc)と実験的なアンダーカット幅の間で良好な一致が見られました(Figure 9a)。シフト配置は一貫してより大きなアンダーカットを生成しました(実験的最大値〜84 µm対ミラー配置の〜68 µm)。内部ノッチ(Wf-no)の発達は、シミュレーションでは両方の配置で同様に予測されましたが、実験ではシフト配置でより大きな内部ノッチが示されました(Figure 9b)。実験的な平坦化荷重は一定(〜48 kN)であり、シミュレーションよりも高かったですが、これはおそらく幅広の実験ローラーが未変形材料に接触したためです。実験的に配置間で荷重に有意な差は観察されませんでした(Figure 10b)。
- ローラー摩耗: 特に板材圧延時のシフト配置において、実験ローラーに著しい摩耗、特にローラーリブエッジのせん断が観察されました(予荷重および弾性ロールギャップ変化に起因)。
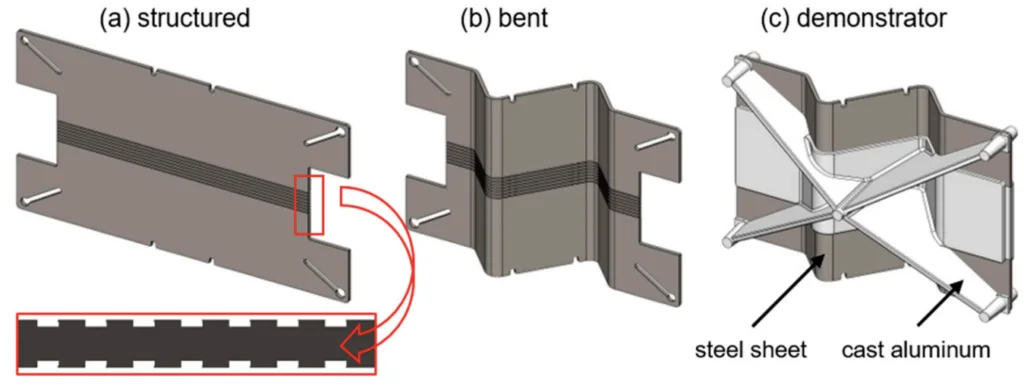
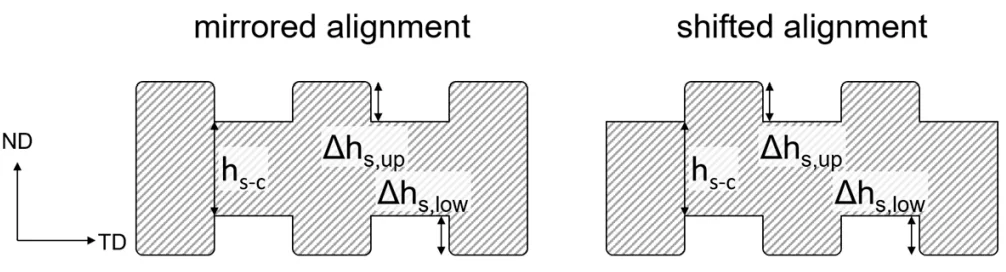
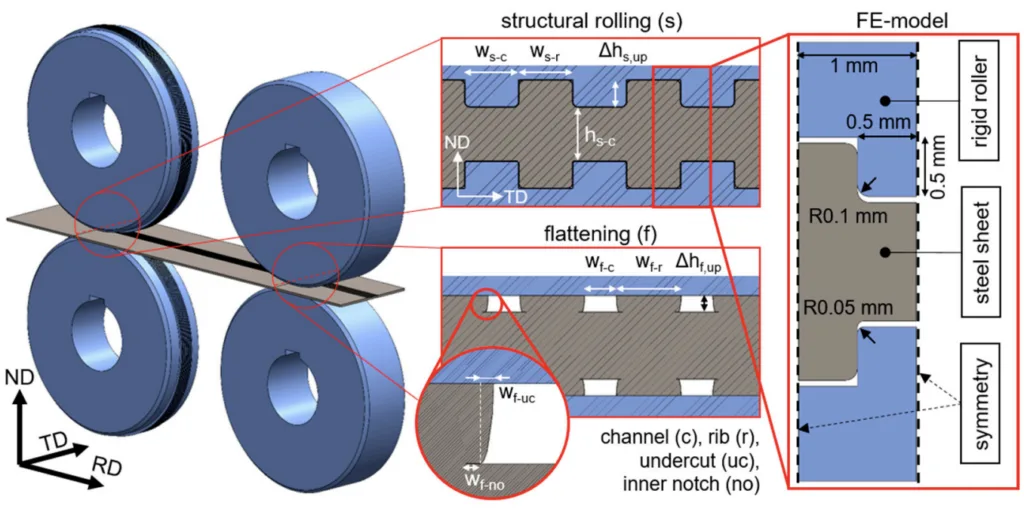
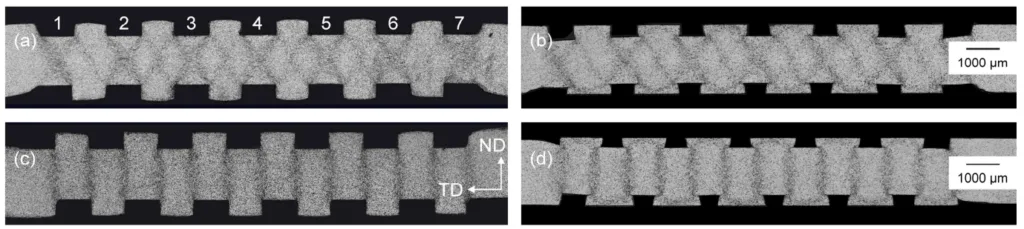
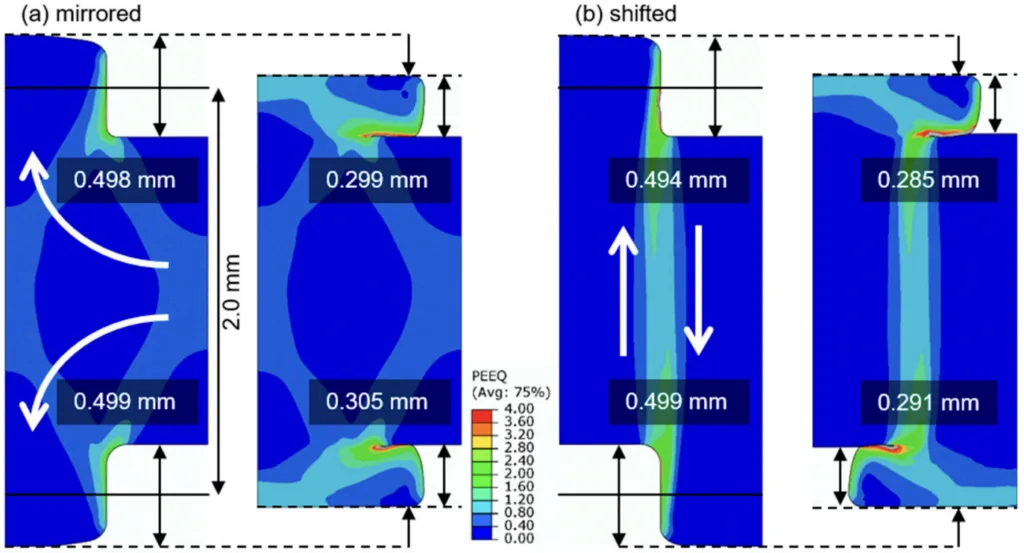
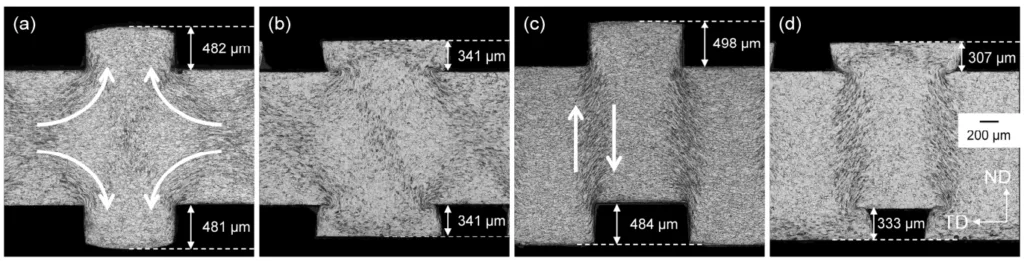
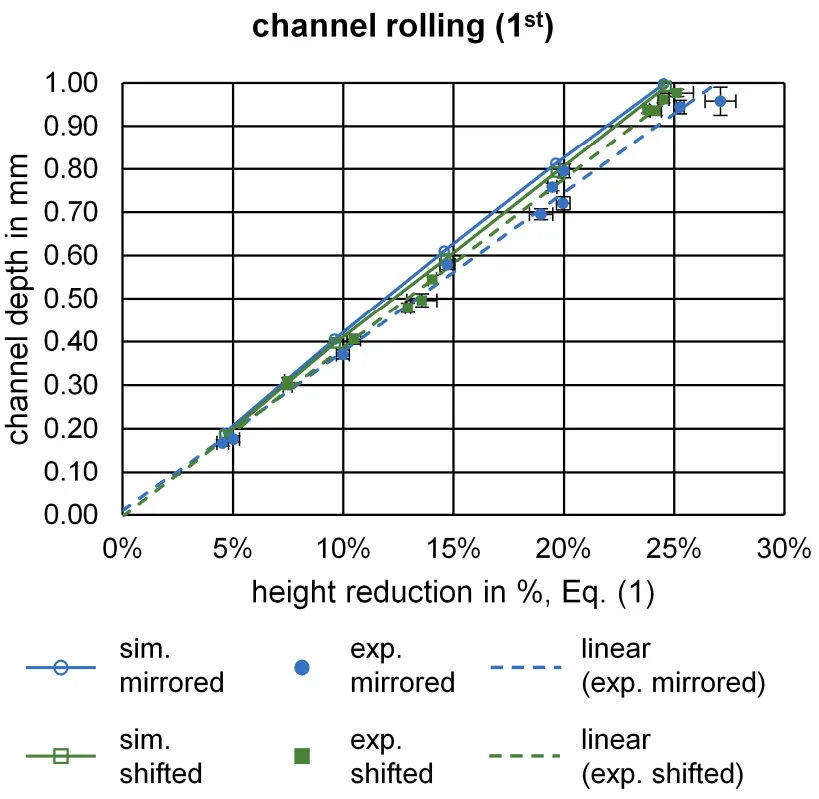
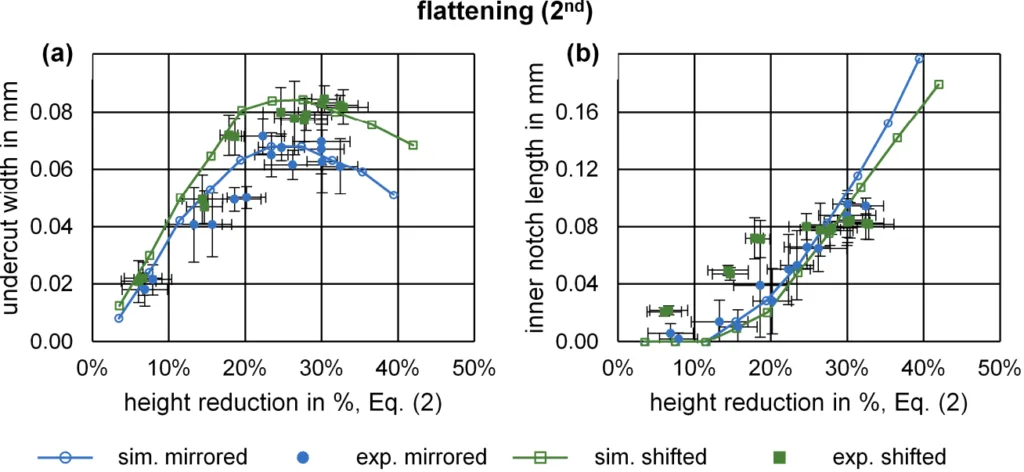
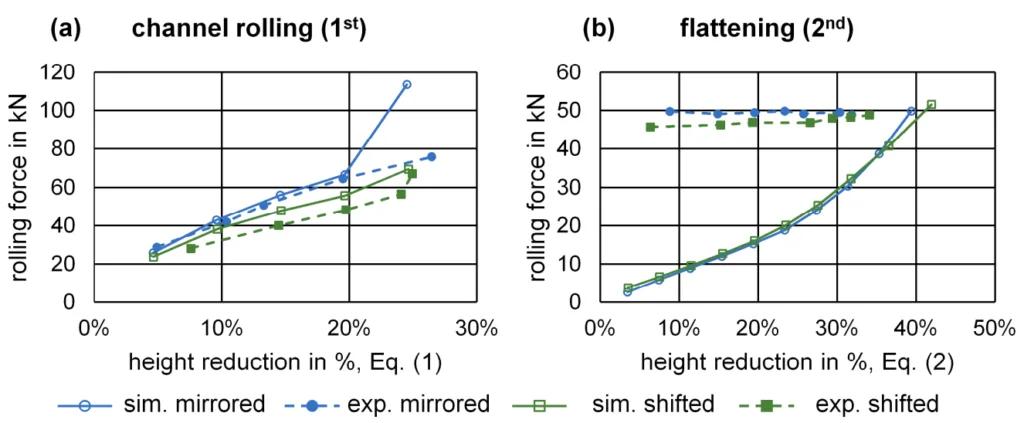
図の名称リスト:
- Figure 1. Scheme of the rolling process for surface structures (as proposed by Senge et al. [15]); view in the normal direction (ND) and transverse direction (TD).
- Figure 2. Examples of surface structures on steel sheets after (a) rolling and cutting, (b) bending, and (c) casting of the demonstrator part.
- Figure 3. Investigated alignments of the double-sided surface structure.
- Figure 4. 3D scheme of the rolling process and 2D simplification in the FE simulation.
- Figure 5. Cross-section preparations of (a) structural rolling, mirrored, (b) flattening, mirrored, (c) structural rolling, shifted, (d) flattening, shifted.
- Figure 6. Exemplary material flow in FE simulations by equivalent plastic strain (PEEQ) after structural rolling and flattening.
- Figure 7. Close-up cross-section measurement examples of (a) structural rolling, mirrored, (b) flattening, mirrored, (c) structural rolling, shifted, (d) flattening, shifted.
- Figure 8. Channel depth after structural rolling for simulations vs. experiments of both alignments.
- Figure 9. (a) Undercut width and (b) inner notch length after flattening for simulations vs. experiments of both alignments.
- Figure 10. Max. rolling forces for (a) channel rolling and (b) flattening for simulations vs. experiments of both alignments.
7. 結論:
本研究は、鋼板上にアンダーカット特徴を作成するための両面構造圧延プロセスを成功裏にシミュレーションし、実験的に検証しました。特に平坦化中のアンダーカット幅に関して、シミュレーションと実験の間で良好な一致が得られました。実験では、シート端部で中間チャネルと比較して理想的でないチャネル形成が明らかになりました。ミラー配置は、シフト配置と比較して構造圧延中により高い圧延荷重を示しました。逆に、シフト配置はより大きなアンダーカット(潜在的に接合強度に有利)をもたらしましたが、実験的にはより大きな内部ノッチ傾向を示し、板材を使用した実験設定で著しいローラー摩耗を引き起こしました。配置の選択にはトレードオフが伴います:シフト配置はより大きなアンダーカットと低い構造圧延荷重を提供しますが、摩耗と内部ノッチ形成を増加させる可能性があります。今後の研究では、運動学とガイドレールが構造均一性に及ぼす影響を分析し、HPDCアルミニウムと組み合わせたシフト配置構造の複合強度をテストします。
8. 参考文献:
- [1] Kim, H.C.; Wallington, T.J. Life-cycle energy and greenhouse gas emission benefits of lightweighting in automobiles: Review and harmonization. Environ. Sci. Technol. 2013, 47, 6089–6097. [CrossRef] [PubMed]
- [2] Cecchel, S. Materials and Technologies for Lightweighting of Structural Parts for Automotive Applications: A Review. SAE Int. J. Mater. Manf. 2021, 14, 81–97. [CrossRef]
- [3] Mori, K.; Abe, Y. A review on mechanical joining of aluminium and high strength steel sheets by plastic deformation. Int. J. Lightweight Mater. Manuf. 2018, 1, 1–11. [CrossRef]
- [4] Meschut, G.; Janzen, V.; Olfermann, T. Innovative and Highly Productive Joining Technologies for Multi-Material Lightweight Car Body Structures. J. Mater. Eng. Perform. 2014, 23, 1515–1523. [CrossRef]
- [5] Mori, K.; Bay, N.; Fratini, L.; Micari, F.; Tekkaya, A.E. Joining by plastic deformation. CIRP Ann. Manuf. Technol. 2013, 62, 673–694. [CrossRef]
- [6] Salamati, M.; Soltanpour, M.; Fazli, A.; Zajkani, A. Processing and tooling considerations in joining by forming technologies; part A—Mechanical joining. Int. J. Adv. Manuf. Technol. 2019, 101, 261–315. [CrossRef]
- [7] Feistauer, E.E.; dos Santos, J.F.; Amancio-Filho, S.T. A review on direct assembly of through-the-thickness reinforced metal-polymer composite hybrid structures. Polym. Eng. Sci. 2019, 59, 661–674. [CrossRef]
- [8] Noguchi, T.; Asano, K.; Hiratsuka, S.; Miyahara, H. Trends of composite casting technology and joining technology for castings in Japan. Int. J. Cast Met. Res. 2008, 21, 219–225. [CrossRef]
- [9] Fang, X.; Gundlach, J.; Schipperges, J.-J.; Jiang, X. On the Steel–Aluminum Hybrid Casting by Sand Casting. J. Mater. Eng. Perform. 2018, 27, 6415–6425. [CrossRef]
- [10] Ma, Y.; Zhang, G.; Cao, S.; Huo, Z.; Han, J.; Ma, S.; Huang, Z. A Review of Advances in Fabrication Methods and Assistive Technologies of Micro-Structured Surfaces. Processes 2023, 11, 1337. [CrossRef]
- [11] Müller, S.; Brand, M.; Dröder, K.; Meiners, D. Increasing the Structural Integrity of Hybrid Plastics-Metal Parts by an Innovative Mechanical Interlocking Effect. Mater. Sci. Forum 2015, 825–826, 417–424. [CrossRef]
- [12] Buxton, A.L.; Ferhati, A.; Glen, R.J.; Dance, B.G.I.; Mullen, D.; Karayiiannis, T. EB Surface Engineering for High Performance Heat Exchangers. In Proceedings of the First International Electron Beam Welding Conference, Chicago, Illinois, USA, 17–18 November 2009.
- [13] Ucsnik, S.; Gradinger, R.; Becirovic, A.; Waldhör, A. Enhanced Performance of Steel-Aluminium Cast Nodes through Cold Metal Transfer. Mater. Sci. Forum 2013, 765, 736–740. [CrossRef]
- [14] Abe, H.; Chung, J.C.; Mori, T.; Hosoi, A.; Jespersen, K.M.; Kawada, H. The effect of nanospike structures on direct bonding strength properties between aluminum and carbon fiber reinforced thermoplastics. Compos. Part B Eng. 2019, 172, 26–32. [CrossRef]
- [15] Senge, S.; Brachmann, J.; Hirt, G.; Bührig-Polaczek, A. Interlocking Multi-Material Components made of Structured Steel Sheets and High-Pressure Die Cast Aluminium. In Proceedings of the 20th International ESAFORM Conference on Material Forming, Dublin, Ireland, 26–28 April 2017; p. 190007.
- [16] Senge, S.; Brachmann, J.; Hirt, G.; Bührig-Polaczek, A. Evaluation of interlocking bond strength between structured 1.0338 steel sheets and high pressure die cast AlMg5Si2. In Proceedings of the 21st International ESAFORM Conference on Material Forming, Palermo, Italy, 23–25 April 2018; p. 40019.
- [17] Ringel, A.; Lohmar, J. Optimization of the Surface Geometry in Structured Cold Rolling for Interlocking of Formed and Die-Cast Metal Components. Defect Diffus. Forum 2022, 414, 89–94. [CrossRef]
- [18] Jakumeit, J.; Behnken, H.; Laqua, R.; Eiken, J.; Brachmann, J. Multi-scale simulation of hybrid light metal structures produced by high pressure die casting. IOP Conf. Ser. Mater. Sci. Eng. 2020, 861, 12035. [CrossRef]
- [19] Joop, D. Präzisionsbestimmende Faktoren bei der Herstellung blechverstärkter Hybridstrukturen im Druckguss: Grenzflächenanalyse und Verzugsoptimierung. Doctoral Thesis, Gießerei-Institut, RWTH Aachen University, Aachen, Germany, 2018.
- [20] Ringel, A.; Hirt, G. Bending behavior of structured steel sheets with undercuts for interlocking with Al die-cast metal. Int. J. Mater. Form. 2024, 17, 2. [CrossRef]
- [21] Bruckmeier, L.; Ringel, A.; Vroomen, U.; Bailly, D.; Bührig-Polaczek, A. Influence of High-Pressure Die Casting Process Parameters on the Compound Strength of Hybrid Components with Undercut Sheet Metal. Metals 2023, 13, 1717. [CrossRef]
- [22] Tieu, A.; Liu, Y. Friction variation in the cold-rolling process. Tribol. Int. 2004, 37, 177–183. [CrossRef]
- [23] Clausmeyer, T.; Schowtjak, A.; Wang, S.; Gitschel, R.; Hering, O.; Pavliuchenko, P.; Lohmar, J.; Ostwald, R.; Hirt, G.; Tekkaya, A.E. Prediction of Ductile Damage in the Process Chain of Caliber Rolling and Forward Rod Extrusion. Procedia Manuf. 2020, 47, 649–655. [CrossRef]
9. 著作権:
- 本資料は、「Aron Ringel, Sindokht Shayan and David Bailly」による論文です。「Double-Sided Surface Structures with Undercuts on Cold-Rolled Steel Sheets for Interlocking in Hybrid Components」に基づいています。
- 論文出典: https://doi.org/10.3390/machines12080562
本資料は上記論文に基づいて要約したものであり、商業目的での無断使用を禁じます。
Copyright © 2025 CASTMAN. All rights reserved.