本テクニカルブリーフは、[Tri Pujadi氏ら]が執筆し、[Proceedings of the International Conference on Industrial Engineering and Operations Management] ([2021年])で発表された学術論文「[Preventive Maintenance Modeling on Die Casting Machines with Information Systems]」に基づいています。ダイカスト製造の専門家であるCASTMANが、業界のプロフェッショナル向けにその要点を解説します。
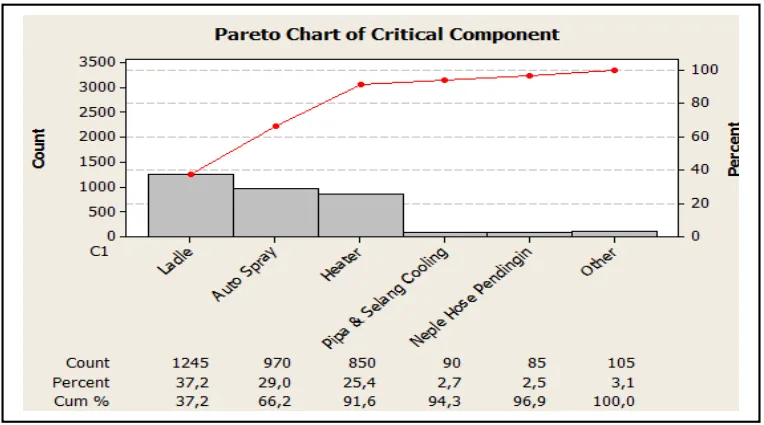
キーワード
- 主要キーワード: 予防保全 ダイカストマシン
- 副次キーワード: ダウンタイム削減, MTTF (平均故障時間), 信頼性向上, 設備保全, コスト削減, ダイカスト部品, 情報システム
エグゼクティブサマリー
(多忙な専門家向けに、研究の核心を30秒で理解できるようにまとめました。)
- 課題: 生産スケジュールが優先されるあまり、適切なメンテナンスが行われず、突発的な機械故障による生産停止が頻発している。
- 手法: 最もダウンタイムの長いダイカストマシン(DC-07)とその重要部品(レードル、オートスプレー、ヒーター)を特定。平均故障時間(MTTF)を算出し、最適な予防交換時期を割り出す定量的分析を実施。
- 重要な発見: 提案された予防保全計画の実施により、マシンの信頼性が最大129.25%向上し、総ダウンタイムが53.04%削減され、メンテナンスコストも最大38.90%削減可能であることが示された。
- 結論: 「故障したら直す」という事後保全から、データに基づいた予防保全へ移行することで、生産性と収益性を大幅に改善できる。
課題:なぜこの研究がダイカスト専門家にとって重要なのか
製造業、特にダイカスト業界において、生産目標の達成は最優先事項です。しかし、その裏で「生産スケジュールがタイトである」ことを理由に、本来行うべき設備のメンテナンスが後回しにされている現場は少なくありません。本研究の対象となった企業も同様の課題を抱えており、コンポーネントの交換は、機械が突然故障した時にのみ行われる「事後保全」が常態化していました(Introduction
より)。
このアプローチは、予期せぬ長時間のダウンタイムを引き起こし、生産計画を大きく狂わせます。特に、クランクケースやシリンダーコンプといった重要部品を生産するダイカストマシンが停止した場合、その影響は甚大です。この研究は、多くの製造現場が直面するこの根深い問題を解決するため、データに基づいた科学的なアプローチで予防保全の最適化を目指したものです。
アプローチ:研究手法の解明
研究チームは、この問題を解決するために、定量的アプローチを採用しました。その手順は以下の通りです(Methodology
より)。
- 重要マシンの特定: 2019年から2020年にかけての全ダイカストマシンのダウンタイムデータを分析し、最も生産に影響を与えている「クリティカルマシン」を特定。
- 重要コンポーネントの特定: 特定されたマシンの故障データをパレート分析し、故障頻度の高い「クリティカルコンポーネント」を割り出す。
- データ分析: 各重要コンポーネントの故障間隔(TTF)と修理時間(TTR)のデータを収集。統計的分布を適合させ、平均故障時間(MTTF)と平均修理時間(MTTR)を算出。
- 最適交換時期の決定: ダウンタイムを最小化する最適なコンポーネント交換時期(Age Replacement)を試行錯誤法により計算。
- 効果測定: 提案された予防保全を導入した場合の信頼性、可用性、ダウンタイム、総コストを算出し、導入前の状態と比較分析。
この体系的なアプローチにより、勘や経験に頼るのではなく、実際のデータに基づいて最も効果的なメンテナンス計画を立案することが可能になります。
発見:主要な研究結果とデータ
分析の結果、ダイカストプロセスにおける生産性向上のための具体的な数値が明らかになりました。
発見1:最重要マシンの特定
Table 1のデータによると、全16台のダイカストマシンの中で「DC-07」が総ダウンタイムの12.20%を占め、最もクリティカルなマシンであることが判明しました。発見2:最重要コンポーネントの特定
DC-07マシンの故障要因を分析したFigure 2のパレート図から、「レードル(Ladle)」「オートスプレー(Auto Spray)」「ヒーター(Heater)」の3つのコンポーネントが故障全体の91.6%を占めるクリティカルな部品であることが特定されました。発見3:最適な予防交換時期の算出
MTTFの計算に基づき、各コンポーネントの最適な予防交換間隔がTable 4で示されました。- レードル: 108時間
- オートスプレー: 506時間
- ヒーター: 320時間
発見4:予防保全による劇的な改善効果
この交換間隔を適用することで、信頼性、ダウンタイム、コストのすべてにおいて大幅な改善が見られました。- 信頼性の向上 (
Table 6
): レードルで92.44%、オートスプレーで129.25%、ヒーターで80.07%の信頼性向上を達成。 - ダウンタイムの削減 (
Table 7
): 対象コンポーネントの総ダウンタイムは4,258時間から2,258時間削減され、53.04%の改善。 - コストの削減 (
Table 8
): レードルで24.73%、オートスプレーで31.11%、ヒーターで38.90%の月間コスト削減を実現。
- 信頼性の向上 (
ダイカスト製品製造への実践的な示唆
この研究結果は、理論上の数値にとどまらず、実際のダイカスト製造現場に直接的なメリットをもたらします。
プロセスエンジニアへ: 本研究の「
Calculation
」セクションで示された分析手法は、自社の設備データに応用可能です。最も生産を阻害しているマシンと部品を特定し、データに基づいたメンテナンス計画を立案することで、突発的な生産停止を未然に防ぎ、生産効率を安定させることができます。品質管理担当者へ: 設備の信頼性向上は、製品品質の安定に直結します。Table 6で示されているように、適切な予防保全は設備の信頼性を飛躍的に高めます。これにより、設備不調に起因する鋳造欠陥のリスクを低減させることが期待できます。
保全・金型設計担当者へ: この研究は、コンポーネントの「寿命」をデータで予測することの重要性を示しています。この考え方は、金型のメンテナンス計画にも応用可能です。ショット数や使用時間に基づいた予防的なメンテナンス(例:冷却管の洗浄、可動部の交換)を計画することで、金型の突発的な破損を防ぎ、寿命を最大化することにつながります。
論文詳細
Preventive Maintenance Modeling on Die Casting Machines with Information Systems
1. 概要:
- Title: Preventive Maintenance Modeling on Die Casting Machines with Information Systems
- Author: Tri Pujadi, Bahtiar H. Simamora, Vikas Kumar, Yulia Magdalena, Witarsjah, Yunita Kartika Sari, Satya Windy
- Year of publication: 2021
- Journal/academic society of publication: Proceedings of the International Conference on Industrial Engineering and Operations Management
- Keywords: Risk, procurement, supply chain, failure mode effect analysis, mitigate risk, scrm
2. Abstract:
From the results of observations at the company, the main problem found is that maintenance activities have not been carried out properly due to the tight production schedule. It is the reason for replacing components, only when the machine is damaged suddenly. The purpose of the study is to determine the type of machine that requires periodic maintenance, and critical components, along with how much reliability if applied through an information system. The case study method carried out is a quantitative method by processing data according to preventive maintenance. The analysis is carried out by determining the engine and critical components and then calculating the meantime to failure (MTTF) and mean time to repair (MTTR) to get the value of age replacement, availability, reliability, and downtime. The results achieved are increased availability and reliability and decreased total downtime by implementing proposed preventive maintenance for ladle, auto spray and heater components.
3. Introduction:
Various efforts were made by manufacturing companies to improve performance, by conducting timely production processes, controlling raw material supplies, and distributing products to distributors on time, thus improving service to customers. The production process was based on good scheduling, material control to prevent the occurrence of material running out, product distribution according to the needs of distributors and customers. These efforts could be achieved, if supported using information technology to record sales orders from distributors, stock inventory of materials, the creation of purchase orders to suppliers, and in the creation of financial statements within the company.
In manufacturing companies, the smoothness of the production process affects the achievement of their targets. To achieve good performance, machines must have a maintenance system so that they can have optimal operation when used (Basri et all., 2017). However, in practice, many manufacturing industries still focus more on the production process and pay less attention to preventive measures to reduce machine damage during the production process.
The object studied here is a company engaged in the automotive industry, which produces various motorcycles ranging from cub type, scooter to sport type. In the maintenance and repair management system, the activities are scheduled every month in the first week and are adjusted to the production schedule (Angius et all., 2016). The tight production schedule causes maintenance activities to get less priority. Replacement of components is often only done when there is a sudden machine breakdown during the production process. 16 Die Casting machines have an essential role in producing Crank Case R, Crank Case L, and Cylinder Comp components in the Die Casting department. The maintenance management system that is not implemented regularly cause many die casting machines to experience disturbances when operated. It is why it is essential to implement a preventive maintenance system in the company's production process.
4. 研究の概要:
研究トピックの背景:
生産スケジュールが過密なため、適切なメンテナンス活動が行われておらず、機械が突然故障したときにのみ部品を交換する事後保全が中心となっている。これにより、予期せぬダウンタイムが発生し、生産性が低下している。
先行研究の状況:
多くの製造業では、生産プロセスに重点が置かれ、機械の損傷を減らすための予防措置にはあまり注意が払われていない。OEM(Original Equipment Manufacturer)の推奨に基づくメンテナンスは存在するが、各機械が稼働する固有の環境や状態を反映していないため、必ずしも最適ではない。
研究の目的:
本研究の目的は、定期的なメンテナンスを必要とするマシンの種類と、その中でも特に重要なクリティカルコンポーネントを特定することである。さらに、平均故障時間(MTTF)などのデータを用いて最適な交換時期を算出し、予防保全を導入した場合の信頼性、可用性、ダウンタイム、コストへの影響を定量的に評価し、そのプロセスを支援する情報システムの有用性を示すことにある。
研究の核心:
研究の核心は、実際の故障データに基づき、最も生産に影響を与えるダイカストマシン(DC-07)とその重要部品(レードル、オートスプレー、ヒーター)を特定し、Age Replacement(年齢取替)モデルを用いて最適な予防交換間隔を算出することにある。これにより、事後保全からデータ駆動型の予防保全への移行がもたらす信頼性、ダウンタイム、コスト面での具体的な改善効果を明らかにしている。
5. 研究方法
研究デザイン:
本研究では、記述的分析(descriptive analytic)手法を採用。実際の生産現場におけるダイカストマシンの故障データを収集し、定量的に分析することで、予防保全の効果を検証するケーススタディとして設計されている。
データ収集と分析方法:
2019年1月から2020年12月までのエンジン損傷およびダイカスト部品に関するデータ、修理・運用コストデータを収集。収集したデータを用いて、最もダウンタイムの長いマシンを特定し、パレート分析でクリティカルコンポーネントを絞り込む。その後、各コンポーネントの故障間隔(TTF)と修理時間(TTR)のデータから、平均故障時間(MTTF)と平均修理時間(MTTR)を計算。これらの値を用いて、最適な交換時期、信頼性、可用性、ダウンタイム、総コストを算出し、予防保全導入前後の効果を比較分析した。
研究の対象と範囲:
研究対象は、自動車産業に従事する企業のダイカスト部門にある16台のダイカストマシン。特に、分析の結果特定された最もクリティカルなマシン「DC-07」とその重要部品である「レードル」「オートスプレー」「ヒーター」に焦点を当てている。
6. 主要な結果:
主要な結果:
- クリティカルマシンの特定: ダイカストマシン「DC-07」が、総ダウンタイムの12.20%を占め、最もクリティカルなマシンとして特定された(Table 1)。
- クリティカルコンポーネントの特定: DC-07マシンにおいて、「レードル」「オートスプレー」「ヒーター」の3部品が故障の主要因であることがパレート分析により示された(Figure 2)。
- 最適交換間隔の決定: 各クリティカルコンポーネントの最適な予防交換間隔は、レードルが108時間、オートスプレーが506時間、ヒーターが320時間と算出された(Table 4)。
- 信頼性の大幅な向上: 予防保全の導入により、レードルの信頼性は92.44%、オートスプレーは129.25%、ヒーターは80.07%向上した(Table 6)。
- ダウンタイムとコストの削減: 提案された予防保全により、対象部品の総ダウンタイムは53.04%削減され(Table 7)、メンテナンスに関連する総コストも24.73%から38.90%削減された(Table 8)。
Figure Name List:
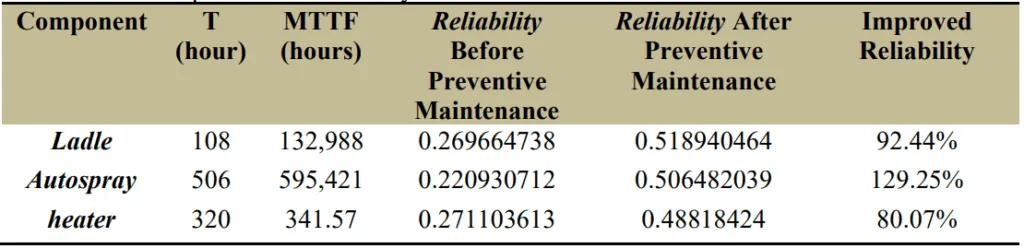


- Figure 1 Methodology Research
- Figure 2. The critical components of damage
- Figure 4 Use Case Diagram
7. Conclusion:
Based on the calculation of preventive maintenance, it was found that the die casting machine-07 is a binding machine with selected critical components ladle, auto spray and heater. In addition, it is known that preventive maintenance actions, especially replacement of damage prevention, are carried out after the ladle component reaches a service life of 108 hours, the auto spray component is 506 hours, and the heater component is 320 hours. Moreover, by performing preventive maintenance, the reliability curve of the ladle component shows an increase of 92.44%, auto spray 129.25%, and heater component 80.07%. The application of information system applications can support engine maintenance activities in terms of data collection and calculation of engine and component performance. The company should pay more attention to the DC-07 engine and its components to keep the engine performance always in normal condition.
8. References:
- Ab-samat, H., L. N. Jeikumar, E. I. Basri, N. A. Harun, “Effective Preventive Maintenance Scheduling: A Case Study," Proc. 2012 Int. Conf. Ind. Eng. Oper. Manag. Istanbul, Turkey, pp. 1249–1257, 2012.
- Angius, A., M. Colledani, L. Silipo, A. Yemane, “Impact of Preventive Maintenance on the Service Level of Multi-stage Manufacturing Systems with Degrading Machines,” IFAC-PapersOnLine, vol. 49, no. 12, pp. 568–573, 2016, doi: 10.1016/j.ifacol.2016.07.696. 2016
- Basri, E.I., I. H. A. Razak, H. Ab-Samat, S. Kamaruddin, “Preventive maintenance (PM) planning: A review,” J. Qual. Maint. Eng., vol. 23, no. 2, pp. 114-143, doi: 10.1108/JQME-04-2016-0014. 2017
- Duarte, J.A.C., J. C. T. A. Craveiro, T. P. Trigo, "Optimization of the preventive maintenance plan of a series components system,” Int. J. Press. Vessel. Pip., vol. 83, no. 4, pp. 244-248, doi: 10.1016/j.ijpvp.2006.02.016. 2006
- Hardt, F., M. Kotyrba, E. Volna, R. Jarusek, “Innovative approach to preventive maintenance of production equipment based on a modified tpm methodology for industry 4.0," Appl. Sci., vol. 11, no. 15, 2021, doi: 10.3390/app11156953. 2021
- Purnama, C., “Analyze Machine Maintenance Cost With Corrective Method and Preventive Method To Increase Production Result," Int. J. Bus. Rev. (The Jobs Rev., vol. 2, no. 1, pp. 1–8, 2019, doi: 10.17509/tjr.v2i1.15307. 2019
- Qian, F., K. Dong, “The Open Cybernetics & Systemics Optimizing Preventive Maintenance of Used Equipment for Lease Abstract :," no. Cm, doi: 10.2174/1874110X0171101008 2017
- Zahedi, Z., A. Salim, “Integrating Preventive Maintenance Scheduling As Probability Machine Failure And Batch Production Scheduling," ComTech Comput. Math. Eng. Appl., vol. 7, no. 2, p. 105, doi: 10.21512/comtech.v7i2.2247. 2016
専門家Q&A:あなたの疑問に答えます
Q1: この研究で特定された、信頼性向上に最も重要な単一の要因は何ですか?
A1: 最も重要な要因は、ダウンタイムが最も長いクリティカルなマシン(本研究ではDC-07)と、その故障の大部分を占めるクリティカルなコンポーネント(レードル、オートスプレー、ヒーター)にメンテナンス資源を集中させることです。これは論文の「Conclusion
」セクションで結論付けられており、Table 1とFigure 2のデータによって裏付けられています。
Q2: この研究のアプローチは、従来の問題対処法とどう違いますか?
A2: 論文の「Introduction
」セクションで述べられているように、従来の方法は「機械が突然故障したときにのみ部品を交換する」という事後保全が中心でした。対照的に、本研究は実際の故障データに基づいて最適な交換時期を事前に計算し、故障が発生する前に部品を交換する「データ駆動型の予防保全」を導入しています。
Q3: この発見は、すべてのダイカストマシンに適用可能ですか、それとも特定のマシンに限られますか?
A3: 本研究は、「Result And Discusion
」セクションで詳述されている通り、DC-07ダイカストマシンに特化して行われました。この研究で示された具体的な交換時間(例:レードル108時間)はDC-07に固有のものですが、その分析手法(クリティカルなマシンと部品を特定し、MTTFを計算する)は、他のダイカストマシンや設備にも広く応用可能です。
Q4: この結論に至るために、研究者たちはどのような具体的な測定・分析手法を用いましたか?
A4: 研究者たちは、「Methodology
」セクションで説明されているように、定量的分析手法を用いました。具体的には、実際の故障間隔と修理時間のデータから平均故障時間(MTTF)と平均修理時間(MTTR)を算出し、それを用いてダウンタイムを最小化する最適な交換時期(Age Replacement)を決定しました。
Q5: 論文が推奨する、クリティカルコンポーネントの具体的な交換間隔は何ですか?
A5: Table 4に示されている通り、研究が算出した最適な予防交換間隔は以下の通りです。
- レードル (Ladle): 108時間
- オートスプレー (Autospray): 506時間
- ヒーター (heater): 320時間
Q6: この論文からダイカスト工場が得られる、直接的で実践的な教訓は何ですか?
A6: 最も重要な教訓は、勘や経験に頼ったメンテナンスから脱却し、実際の設備データに基づいた予防保全計画に移行することで、ダウンタイムとコストを劇的に削減し、信頼性を大幅に向上させることが可能であるという点です。これは論文「Preventive Maintenance Modeling on Die Casting Machines with Information Systems
」の全体的な結果によって強く支持されています。
結論と次のステップ
本研究は、ダイカスト製造における生産性と信頼性を向上させるための、価値あるロードマップを提供しています。その発見は、品質改善、欠陥削減、そして生産最適化に向けた、明確でデータに裏付けられた道筋を示しています。
CASTMANでは、お客様が抱える最も困難なダイカストの課題を解決するため、最新の業界研究を積極的に活用しています。もし本稿で議論された課題が貴社の事業目標と共鳴するものであれば、ぜひ弊社の技術チームにご相談ください。これらの先進的な原則を貴社のコンポーネント製造にどのように活かせるか、共に検討させていただきます。
著作権
- 本資料は、「Tri Pujadi氏ら」による論文です。「Preventive Maintenance Modeling on Die Casting Machines with Information Systems」に基づいています。
- 論文の出典: Proceedings of the International Conference on Industrial Engineering and Operations Management, Monterrey, Mexico, November 3-5, 2021
本資料は情報提供のみを目的としています。無断での商業利用は禁じられています。
Copyright © 2025 CASTMAN. All rights reserved.