この文書は、2007年9月にJournal of Computing and Information Science in Engineeringに掲載された研究論文「ダイカスト部品の自動分割方向および分割線決定のためのフィーチャ認識」を要約したものです。この論文は、従来、専門家の直感と時間のかかる手作業に頼っていたダイカストにおける分割方向と分割線の自動決定という重要な課題に取り組んでいます。
1. 概要:
- タイトル: ダイカスト部品の自動分割方向および分割線決定のためのフィーチャ認識 (Die-Casting Feature Recognition for Automated Parting Direction and Parting Line Determination)
- 著者: ジャティンダー・マダン (Jatinder Madan)、P.V.M. ラオ (P.V.M. Rao)、T.K. クンドラ (T.K. Kundra)
- 発表年: 2007年9月
- 掲載ジャーナル/学会: Journal of Computing and Information Science in Engineering
- キーワード: ダイカスト (die casting)、フィーチャ認識 (feature recognition)、抜き方向 (withdrawal direction)、分割方向 (parting direction)、分割線 (parting line)、設計製造 (design for manufacture)
2. 研究背景:
- 研究テーマの社会的/学術的背景: ダイカストは重要なニアネットシェイプ製造プロセスとして強調されています。他のニアネットシェイププロセスと同様に、ダイカストは主にコアとキャビティという2つの金型半体を利用します(図1参照)。論文では、特に製品設計段階で部品設計の複雑さが増すにつれて、金型設計と部品の全体的な製造可能性が著しく困難になると強調しています。主な問題点は、部品設計者がダイカストプロセスの複雑さ、特に分割方向と分割線の決定に関連する問題についての包括的な知識が不足していることが多いことです。現在の業界慣行は、設計の製造可能性を確保するために、部品設計者と製造専門家の間の反復サイクルによって特徴付けられます。
- 既存研究の限界: 論文は、研究者が分割方向と分割線の選択に関するガイドラインを提案している一方で、自動化の欠如により、部品の形状と形状に関連する広範なデータ処理が必要になると指摘しています。この手動実装は時間がかかり、ダイカスト専門家の多大な労力を必要とします。以前のフィーチャ認識研究は、主に機械加工と板金成形に集中しており、ダイカストとは異なるフィーチャ定義を持っています。既存のダイカストフィーチャ認識および分割方向決定方法は、いくつかの側面で制限されています。
- かなりの手動入力と計算努力が必要な場合が多い。
- 一部の方法は、特定のタイプの表面(例:平面、多面体部品)に限定されています。
- 局所的な可視性に基づくアプローチは、業界慣行を正確に反映していない可能性があります。
- 既存のフィーチャ認識技術は、複雑でネスト化され、相互作用するフィーチャに対処するのに苦労する可能性があります。
- 一部の方法は、事前定義されたフィーチャライブラリに依存しており、新しい設計への適応性を制限しています。
- 研究の必要性: 本研究は、設計プロセス効率を向上させ、設計-製造統合を可能にするための重要なツールとして、自動化された製造可能性分析の必要性を強調しています。さらに、プロセス計画における自動化の強化は、製造におけるより高い効率と生産性を達成するために不可欠です。ダイカストフィーチャ、分割方向、分割線、サイドコア、キャビティ数の自動決定は、プロセス計画にとって重要な入力であり、生産時間、部品コスト、および全体的な収益性に直接影響を与えます。論文は、特に自動化されたダイカストフィーチャ認識や分割方向と分割線の自動選択など、プロセス計画の自動化にはほとんど注意が払われていないと具体的に指摘しています。したがって、分割方向と分割線を決定するための自動化されたアプローチは、ダイカスト設計-製造統合および自動化されたDFM(Design for Manufacture、製造のための設計)分析にとって非常に重要です。提案されたシステムは、STEPファイルから直接製品データを利用し、自動分割方向および分割線決定のためにダイカストフィーチャを識別することにより、これらのニーズに対処することを目的としています。
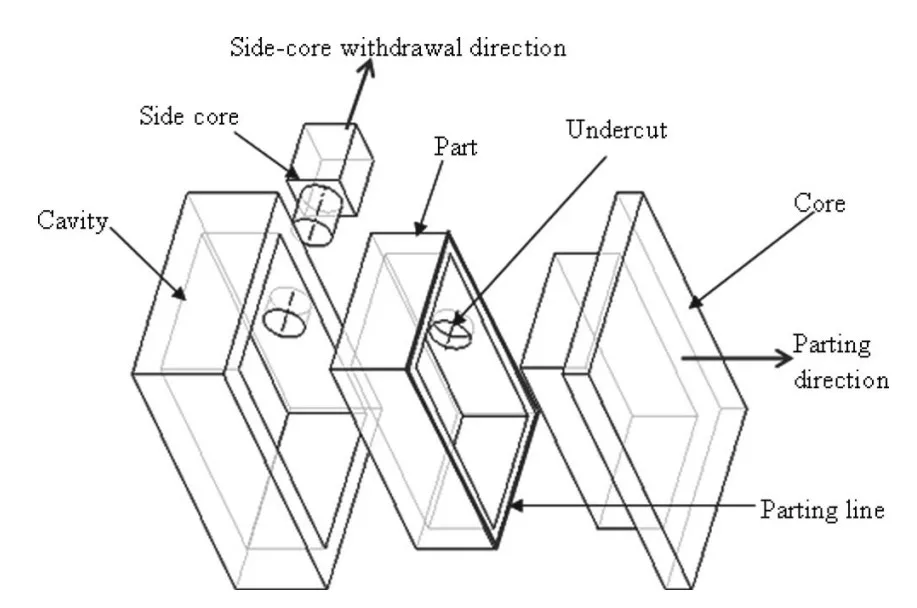
3. 研究目的と研究課題:
- 研究目的: 主な研究目的は、以下のような包括的な自動化システムを開発することです。
- ダイカストフィーチャ認識: STEPファイルで表現された部品CADモデルからダイカストフィーチャ(突起部と凹部)を自動的に識別および分類します。
- 自動分割方向決定: 認識されたフィーチャとプロセス制約に基づいて、ダイカスト部品の最適な分割方向を自動的に決定します。
- 自動分割線決定: 選択された分割方向に基づいて、プロセス制約と優先順位を考慮して分割線を自動的に決定します。
- 主要な研究課題: 本研究は、以下の主要な質問に答えることを目指しています。
- 事前定義されたフィーチャライブラリに依存せずに、STEPファイルデータから複雑でネスト化され、相互作用するフィーチャを含むダイカストフィーチャをどのように自動的に認識できるでしょうか?
- 産業慣行に合わせてダイカストフィーチャの抜き方向を決定するために、自動化システムでグローバルな可視性を効果的に活用するにはどうすればよいでしょうか?
- 選択された分割方向に基づいて分割線を決定するために、プロセス制約と優先順位を自動化システムに統合するにはどうすればよいでしょうか?
- 包括性、精度、および複雑な産業用ダイカスト部品への適用可能性の点で、既存のアプローチの限界を克服する自動化システムを開発できるでしょうか?
- 研究仮説: 中核となる研究仮説は、STEPファイル入力、幾何学的推論、グローバルな可視性分析、およびプロセス制約の考慮事項を活用する新しく開発された自動化システムが、ダイカスト部品の分割方向と分割線の決定を効果的かつ包括的に自動化できるということです。このシステムは、既存の自動化されたアプローチの限界を克服し、ダイカスト業界の専門家の決定と一致する結果を提供すると仮説立てられています。
4. 研究方法:
- 研究デザイン: 本研究では、開発と検証の研究デザインを採用しています。ダイカストフィーチャ認識と分割方向/分割線決定のための新しい自動化システムの開発に焦点を当てています。その後、システムの性能と結果を専門家の知識と業界慣行と比較して検証します。
- データ収集方法: システムは、部品CADモデルのSTEPファイル(特にAP 203/214)を主要な入力データソースとして利用します。STEPファイルは中立的な標準であるため、さまざまなCADプラットフォームでより幅広い適用可能性が保証されます。システムは、面-エッジおよびエッジ-頂点関係を含む幾何学的データをこれらのSTEPファイルから直接抽出します。
- 分析方法: 方法論の中核は、幾何学的推論とルールベースのシステムに基づいています。
- フィーチャ認識: 幾何学的推論は、突起部または凹部領域として定義されるダイカストフィーチャを識別するために適用されます。システムは、これらのフィーチャを抜き方向(単一、二重、または複数)に基づいて分類します。ネスト化され、相互作用するフィーチャを認識するためのルールを組み込み、抜き方向計画にグローバルな可視性を使用します。
- 分割方向と分割線決定: 分割線決定は、プロセス制約と優先順位を考慮して、選択された候補分割方向に基づいています。分割方向と分割線の評価基準は、重要なダイカスト固有の要素を考慮しています。
- 検証: システムの結果は、ダイカスト業界の専門家からの意見と比較して検証されます。システムは産業部品でテストされ、専門家の解釈との出力の一貫性が評価されます。
- 研究対象と範囲: 本研究はダイカスト部品に焦点を当てており、特に突起部と凹部フィーチャの認識と分析を対象としています。範囲には以下が含まれます。
- フィーチャタイプ: 内部および外部アンダーカットに分類される突起部と凹部フィーチャ。
- 抜き方向: フィーチャは、単一、二重、または複数の抜き方向を持つことに基づいて分類されます。
- 部品形状: システムは、ネスト化され、相互作用するフィーチャを含む複雑な部品形状を処理するように設計されています。
- プロセス考慮事項: 方法論は、分割方向と分割線決定にダイカストプロセス制約を組み込んでいます。
- ソフトウェア実装: 研究には、STEPファイル入力から分割方向および分割線出力までのプロセス全体を自動化するソフトウェアシステムの開発が含まれます。
5. 主な研究結果:
- 主な研究結果: 本研究の主な成果は、ダイカストフィーチャ認識と自動分割方向および分割線決定のための機能的な自動化システムの開発です。システムは、以下のことを成功裏に実行します。
- ダイカストフィーチャの識別: STEPファイル入力から突起部と凹部を含むダイカストフィーチャを正確に認識します。
- 抜き方向によるフィーチャの分類: フィーチャを単一、二重、または複数の抜き方向に基づくカテゴリに効果的に分類します。
- 幾何学的推論とグローバルな可視性の活用: システムは、フィーチャ認識に幾何学的推論を使用し、業界慣行に合わせて抜き方向計画にグローバルな可視性を活用します。
- プロセス制約を考慮した分割線の決定: プロセス制約と優先順位を組み込んで、選択された分割方向に基づいて分割線を決定します。
- 既存システムの限界の克服: システムは、以前の自動化されたアプローチに見られる限界を克服し、より包括的なものとして提示されています。
- 統計的/定性的分析結果: 論文は、システムの結果をダイカスト業界の専門家の意見との比較を通じて検証することを強調しています。提供されたテキストに基づくこの要約では、特定の統計分析は詳細に説明されていませんが、専門家による定性的な検証は結果の重要な側面です。論文では、システムを3つの産業部品に適用した例を示しています。
- 自動車用ダイカスト部品(図12): フィーチャ認識と抜き方向の結果を表1に示します。フィーチャ連結の結果を表2に示します。分割方向評価の結果を表3に示します。最適な分割方向は「A」と決定されました。
- ソケットハウジング(図13(a)): ネスト化されたフィーチャと外部凹面エッジを使用するフィーチャを含む13個のフィーチャが識別されました。最適な分割方向は「Y」です(表4)。
- カウンタウェイト(図13(b)): フィーチャ認識の結果を示します。最適な分割方向は「Y」です(表4)。
- データ解釈: 結果は、開発されたシステムがダイカストフィーチャ認識、分割方向、および分割線決定の複雑なタスクを効果的に自動化することを示しています。さまざまなフィーチャタイプを識別し、グローバルな可視性を考慮し、プロセス制約を組み込むシステムの能力は、経験豊富なダイカスト専門家の決定と一致する結果をもたらします。これは、システムが以前の自動化された方法の限界を首尾よく克服し、ダイカスト設計と製造のための実用的なツールを提供することを示唆しています。
- 図のリスト:
- 図1 ダイカストプロセス
- 図2 用語
- (a) V-マップ
- (b) 凸エッジ
- (c) 凹エッジ
- (d) グローバルな可視性(アクセス可能性)
- (e) ローカルな可視性
- 図3 単一抜き方向を持つ孤立した凹部フィーチャ
- 図4 固有の抜き方向を持つネストされた凹部
- (a) ネストされた円筒穴
- (b) ネストされた角柱状および円筒状の凹部
- 図5 スルーホールと凹部
- (a) スルー円筒穴
- (b) スルー角柱状凹部
- 図6 孤立した突起部の抜き方向
- (a) 円筒状突起部
- (b) 円錐状突起部
- (c) 球状突起部
- 図7 簡略化されたトレイモデル
- 図8 一般的な凹部と突起部
- (a) 一般的な凹部
- (b) 一般的な突起部
- 図9 外側のアンダーカット
- 図10 相互作用するアンダーカット
- (a) 相互作用する凹面エッジと円筒状突起部
- (b) 相互作用する凹面エッジと円筒状凹部
- 図11 分割線識別
- (a) PLRとPLS
- (b) 選択された分割線
- 図12 自動車用ダイカスト部品 [50]
- 図13 フィーチャ認識結果
- (a) ソケットハウジング
- (b) カウンタウェイト
- 図14 分割線識別結果
- (a) ソケットハウジング
- (b) カウンタウェイト
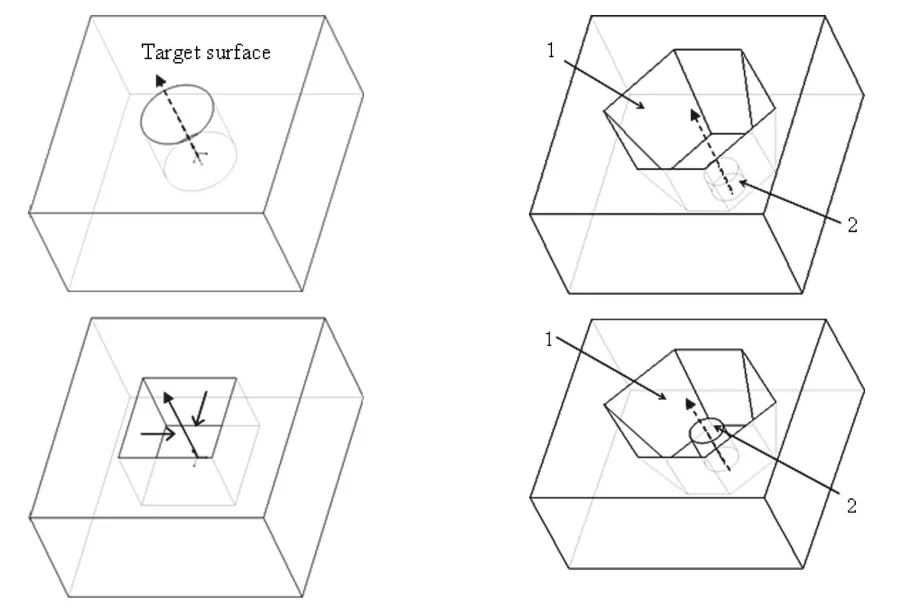
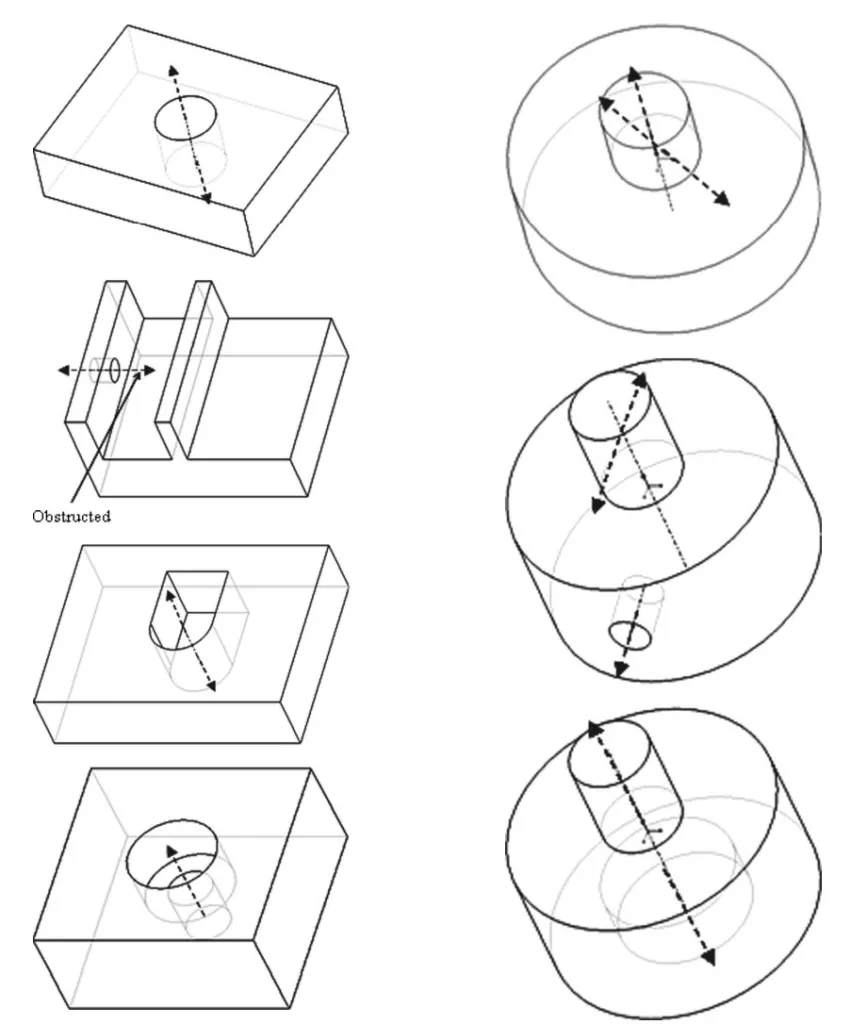
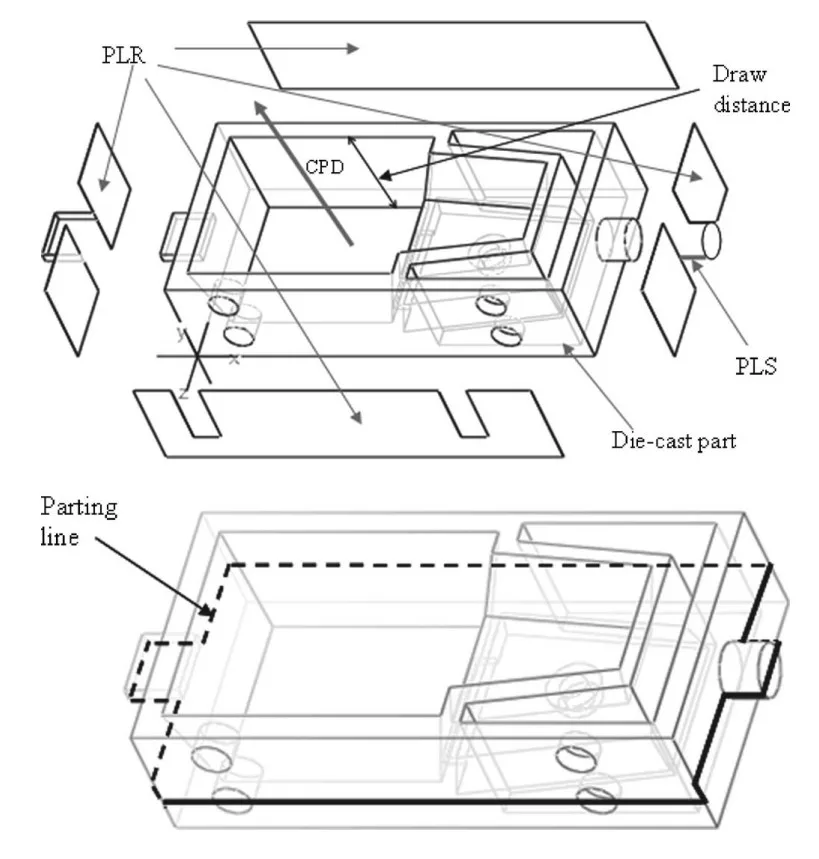
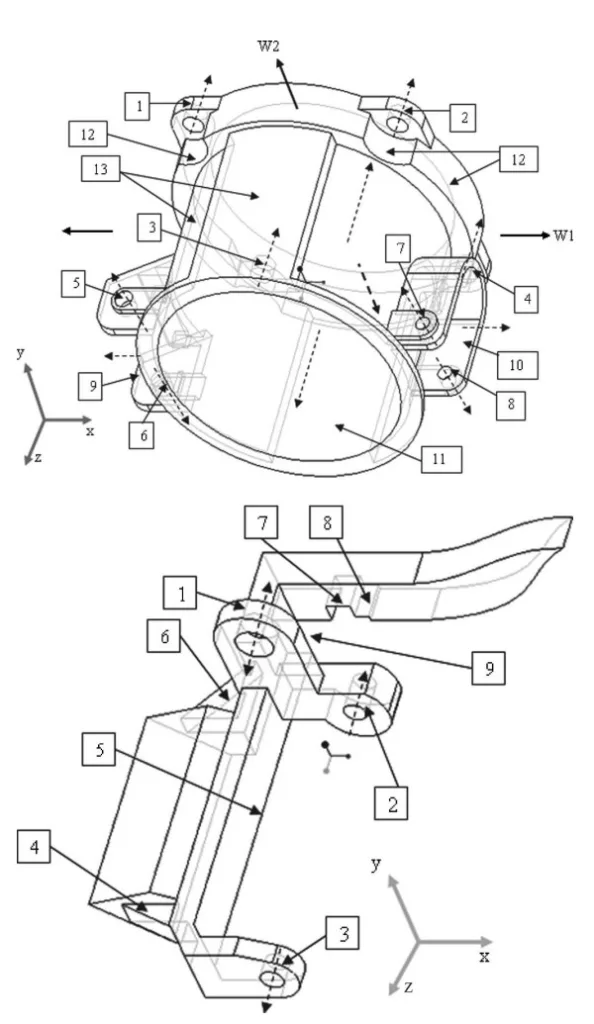
6. 結論と考察:
- 主な結果の要約: 本研究では、ダイカストフィーチャ認識、分割方向、および分割線のための自動化システムを首尾よく開発し、検証しました。このシステムは、より包括的で実用的なアプローチを提供することにより、以前の研究の限界を効果的に克服します。ダイカストフィーチャを正確に識別し、最適な分割方向と分割線を決定し、その結果はダイカスト業界の専門家の判断と一致しています。
- 研究の学術的意義: この研究は、コンピュータ支援設計および製造の分野、特にダイカストの領域において重要な学術的貢献をしています。開発されたシステムは、重要な設計およびプロセス計画タスクの自動化を推進します。適応性と範囲を強化する、事前定義されたライブラリに依存しない一般的なフィーチャ認識のための新しい方法論を紹介します。グローバルな可視性の使用と、分割方向と分割線決定へのプロセス制約の組み込みは、以前のアプローチからの大幅な改善を表しています。
- 実用的な意味合い: この研究の実用的な意味合いは、ダイカスト業界の部品設計者とプロセスプランナーの両方にとって重要です。自動化されたシステムは、いくつかの主要な利点を提供します。
- 時間の節約: 時間のかかる手動プロセスを自動化し、分割方向と分割線の決定に必要な時間を大幅に短縮します。
- 効率の向上: 設計プロセスとプロセス計画活動の効率を向上させます。
- コスト削減: 金型設計とプロセス計画を最適化することにより、生産時間と部品コストの削減に貢献します。
- 設計-製造統合: 設計段階と製造段階間のより良い統合を促進します。
- 自動化されたDFM分析: 自動化されたDFM(Design for Manufacture、製造のための設計)分析を可能にし、製造可能性の問題を早期に特定して解決できるようにします。
- より広い適用可能性: STEPファイルを入力として使用することで、さまざまなCADプラットフォームでより広い適用可能性が保証されます。
- 研究の限界: 論文は、現在の研究の特定の限界を認めています。
- 金型タイプの仮定: システムは、部品がサイドコアを使用して潜在的に2ピース金型を使用して成形可能であると仮定しています。スプリットコアが必要なシナリオは明示的に扱っていません。
- 自由曲面: 現在のシステムは、自由曲面を持つ部品を直接処理しません。ただし、著者は、自由曲面に関する可視性と金型アクセス可能性の研究を統合することで、システムの適用範囲を拡大できる可能性があることを示唆しています。
- 内部スプリットコア: システムは、ダイカストでの動作が事実上不可能と見なされるため、内部スプリットコアを考慮していません。
7. 今後のフォローアップ研究:
- 今後の研究方向: 著者は、開発されたシステムの機能をさらに強化および拡張するために、いくつかの今後の研究方向を提案しています。
- スプリットコアの処理: スプリットコアが必要になる可能性のあるダイカストシナリオに対応するようにシステムを拡張します(ダイカストでは一般的ではなく、複雑ですが)。
- 自由曲面の統合: 自由曲面を処理するための技術を統合し、潜在的にそのような表面の可視性と金型アクセス可能性に関する既存の研究を活用します。
- プロセス計画システムとの統合: より包括的な自動化されたダイカストプロセス計画環境を作成するために、より広範なコンピュータ支援プロセス計画(CAPP)システムとのインターフェースと統合を開発します。
- DFMシステムとの統合: ダイカスト部品の製造可能性評価をさらに自動化するために、DFM(Design for Manufacture、製造のための設計)システムとシステムを統合します。
- さらなる探求が必要な領域: 次の領域でのさらなる探求が推奨されます。
- 複雑な部品形状: さらに広範囲の複雑な産業部品形状に対するシステムの性能をテストおよび改善します。
- プロセス制約の改善: システムの意思決定プロセスに、より詳細で微妙なダイカストプロセス制約をさらに調査し、組み込みます。
- 評価基準の強化: 進化する業界のベストプラクティスとダイカストの技術進歩をより適切に反映するために、分割方向と分割線選択に使用される評価基準を継続的に改善します。
8. 参考文献:
- [1] Gupta, S. K., Das, D., Regli, W. C., and Nau, D. S., 1997, "Automated Manufacturability Analysis: A Survey," Res. Eng. Des., 9(3), pp. 168-190.
- [2] Chen, L. L., Chou, S. Y., and Woo, T. C., 1993, "Parting Directions for Mould and Die Design," Comput.-Aided Des., 25, pp. 762-768.
- [3] Gan, G. H., Woo, T. C., and Tang, K., 1994, "Spherical Maps: Their Construction, Properties and Approximation," ASME J. Mech. Des., 116, pp. 357-363.
- [4] Elber, G., and Cohen, E., 1995, "Arbitrarily Precise Computation of Gauss Maps and Visibility Sets for Freeform Surface," Transactions of ACM Solid Modeling '95, Salt Lake City, UT.
- [5] Corney, J., Hayes, C., Sundararajan, V., and Wright, P., 2005, "The CAD/CAM Interface: A 25 Years Retrospective," ASME J. Comput. Inf. Sci. Eng., 5, pp. 188-191.
- [6] Gao, S., and Shah, J. J., 1998, "Automatic Recognition of Machining Features Based on Minimal Condition Subgraph," Comput.-Aided Des., 30(9), pp. 727-739.
- [7] Nnaji, B. O., Kang, T.-S., Yeh, S., and Chen, J.-P., 1991, "Feature Reasoning for Sheet Metal Components," Int. J. Prod. Res., 29(9), pp. 1867-1896.
- [8] Gavankar, P., and Henderson, M. R., 1990, "Graph Based Extraction of Protrusions and Depression From Boundary Representation," Comput.-Aided Des., 22(7), pp. 442-450.
- [9] Floriani, L. D., 1989, "Feature Extraction From Boundary Models of Three-Dimensional Objects," IEEE Trans. Pattern Anal. Mach. Intell., 2(8), pp. 785-798.
- [10] Lockett, H. L., and Guenov, M. D., 2005, "Graph-Based Feature Recognition for Injection Moulding Based on a Mid-Surface Approach," Comput.-Aided Des., 37, pp. 251-262.
- [11] McAdams, D. A., and Bidkar, R. A., 2003, "Automated Manufacturability Analysis for Injection Moulding and Die Cast Parts," Proceedings of DETC 2003/DFM-48154, Chicago, IL.
- [12] Fu, M. W., Fuh, J. Y. H., and Nee, A. Y. C., 1999, "Undercut Feature Recognition in an Injection Mold Design System," Comput.-Aided Des., 31, pp. 777-790.
- [13] Ye, X. G., Fuh, J. Y. H., and Lee, K. S., 2001, "A Hybrid Method for Recognition of Undercut Features From Molded Parts," Comput.-Aided Des., 33, pp. 1023-1034.
- [14] Ye, X. G., Fuh, J. Y. H., and Lee, K. S., 2004, "Automatic Undercut Feature Recognition for Side Core Design of Injection Molds," J. Mech. Des., 126, pp. 519-526.
- [15] Chung, K., Lee, K., and Kim, T., 2002, "Recognition of Pass Features for Automatic Parting Surface Generation in Injection Moulds," Proc. Inst. Mech. Eng., Part B, 216, pp. 783-796.
- [16] Lim, T., Corney, J., and Clark, D. E. R., 2001, "Laminae-Based Feature Recognition," IEEE Trans. Pattern Anal. Mach. Intell., 23(9), pp. 1043-1048.
- [17] Bralla, J. G., 1999, Design for Manufacturability Handbook, McGraw Hill, New York.
- [18] ASM, 1970, Metals Handbook, Forging and Casting, Vol. 5, American Society of Metals, Metals Park, OH.
- [19] Pye, R. G. W., 1978, Injection Mould Design: A Design Manual for the Thermoplastic Industry, The Plastic and Rubber Institute, London.
- [20] Ravi, B., and Srinivasan, M. N., 1990, "Decision Criteria for Computer Aided Parting Surface Design," Comput.-Aided Des., 22, pp. 11-18.
- [21] Madan, J., Rao, P. V. M., and Kundra, T. K., 2006, "Optimal Parting Direction Selection for Die-Casting," paper communicated to International Journal of Manufacturing Technology and Management.
- [22] Chen, Y., H., 1997, "Determining Parting Direction Based on Minimum Bounding Box and Fuzzy Logic," Int. J. Mach. Tools Manuf., 37(9), pp. 1189-1199.
- [23] Chen, Y. H., Wang, Y. Z., and Leung, T. M., 2000, "An Investigation of Parting Direction Based on Dexel Model and Fuzzy Decision Making," Int. J. Prod. Res., 38(6), pp. 1357-1375.
- [24] Chen, L. L., and Chou, S. Y., 1995, "Partial Visibility for Selecting a Parting Direction in Mould and Die Design," J. Manuf. Syst., 14(5), pp. 319-330.
- [25] Mochizuki, T., and Yuhara, N., 1992, "Methods of Extracting Potential Undercut and Determining Optimal Withdrawal Direction for Mold Designing," Int. J. Jpn. Soc. Precis. Eng., 26, pp. 68-73.
- [26] Yin, Z. P., Ding, H., and Xiong, Y. L., 2000, "Moldability Analysis for Near-Net-Shaped Manufactured Parts Using Freedom Cones," Int. J. Adv. Manuf. Technol., 16, pp. 169–175.
- [27] Yin, Z. P., Ding, H., and Xiong, Y. L., 2001, "Virtual Prototyping of Mold Design: Mouldablity Analysis for Near Net Shape Manufactured Parts by Feature Recognition and Geometric Reasoning," Comput.-Aided Des., 33, pp. 137-154.
- [28] Kurth, G. R., and Gadh, R., 1997, "Virtual Prototyping of Die-Design: Determination of Die-Open Directions for Near-Net-Shape Manufactured Parts With Extruded or Rotational Features," Comput.-Integr. Manuf. Syst., 10(1), pp. 69-81.
- [29] Fu, M. W., Fuh, J. Y. H., and Nee, A. Y. C., 1999, "Generation of Optimal Parting Direction Based on Undercut Features in Injection Molded Parts," IIE Trans., 31, pp. 947-955.
- [30] Khardekar, R., Burton, G., and McMains, S., 2006, "Finding Feasible Mold Parting Directions Using Graphics Hardware," Comput.-Aided Des., 38(4), pp. 327-341.
- [31] Lu, H. Y., and Lee, W. B., 2000, "Detection of Interference Elements and Release Directions in Die-Cast and Injection Molded Components," Proc. Inst. Mech. Eng., Part B, 214, pp. 431-441.
- [32] Huang, J., Gupta, S. K., and Stoppel, K., 2003, "Generating Sacrificial Multi-Piece Molds Using Accessibility Driven Spatial Partitioning," Comput.-Aided Des., 35(13), pp. 1147-1160.
- [33] Banerjee, A. G., and Gupta, S. K., 2006, "A Step Towards Automated Design of Side Actions in Injection Molding of Complex Parts," Geometric Modeling and Processing Conference, Pittsburgh, PA.
- [34] Tan, S. T., Yuen, M. F., Sze, W. S., and Kwong, K. W., 1990, "Parting Lines and Parting Surfaces of Injection Molded Parts," Proc. Inst. Mech. Eng., Part B, 204, pp. 211-219.
- [35] Wong, T., Tan, S. T., and Sze, W. S., 1998, "Parting Line Formation by Slicing a 3D CAD Model," Eng. Comput., 14, pp. 330-343.
- [36] Weinstein, M., and Manoochehri, S., 1997, "Optimum Parting Line Design of Molded and Cast Parts for Manufacturability," J. Manuf. Syst., 16, pp. 1-12.
- [37] Nee, A. Y. C., Fu, M. W., Fuh, J. Y. H., Lee, K. S., and Zhang, Y. F., 1998, "Automatic Determination of 3-D Parting Lines and Surfaces in Plastic Injection Mold Design," CIRP Ann., 47(1), pp. 95-98.
- [38] Fu, M. W., Nee, A. Y. C., and Fuh, J. Y. H., 2002, "The Application of Surface Visibility and Moldability to Parting Line Generation," Comput.-Aided Des., 34, pp. 469-480.
- [39] Nainy-Nejad, M., and Creese, R. C., 1999, "Computer Generation and Optimization of Parting Directions, Parting Lines and Core Cavities," One Hundred Third Annual Meeting of the American Foundrymen's Society, Rosemont, IL, September.
- [40] Penny, F. D., 1953, A Handbook of Die Casting, Ministry of Supply, York House, London.
- [41] Boothroyd, G., Dewhurst, P., and Knight, W., 1994, Product Design for Manufacture and Assembly, Marcel Dekker Inc, New York.
- [42] Elber, G., Chen, X., and Cohen, E., 2005, "Mold Accessibility via Gauss Map Analysis," ASME J. Comput. Inf. Sci. Eng., 5, pp. 79-85.
- [43] Pratt, M. J., and Wilson, P. R., 1985, "Requirements for Support of Form Features in a Solid Modelling System," Computer Aided Manufacturing International (CAMI), Paper No. R-85-ASPP-01.
- [44] Shah, J., and Rogers, M., 1988, "Functional Requirements and Conceptual Design of Feature Based Modeling System," Journal of Computer Aided Engineering, 5(1), pp. 9-15.
- [45] Shah, J. J., Anderson, D., Kim, Y. S., and Joshi, S., 2001 "A Discourse on Geometric Feature Recognition From CAD Models," ASME J. Comput. Inf. Sci. Eng., 1, pp. 41-51.
- [46] Dhaliwal, S., Gupta, S. K., and Huang, J., 2000, "Computing Exact Global Accessibility Cones for Polyhedral Objects," ASME Design for Manufacturability Conference, Baltimore, MD, September.
- [47] Dhaliwal, S., Gupta, S. K., Huang, J., and Priyadarshi, A., 2003, "Algorithm for Computing Global Accessibility Cones," ASME J. Comput. Inf. Sci. Eng., 3, 200-209.
- [48] Priyadarshi, A., and Gupta, S. K., 2004, "Geometric Algorithms for Automated Design of Multi-piece Permanent Molds," Comput.-Aided Des., 36(3), pp. 241-260.
- [49] Pahl, G., and Beitz, W., 1996, Engineering Design, Springer Verlag, London.
- [50] NADCA, 2007, Website of North American Die Casting Association, Rosemont, Illinois, http://www.diecasting.org/information/dc_shape. htm (accessed on Jan. 2, 2007).
- [51] Madan, J., Rao, P. V. M., and Kundra, T. K., 2006, "System for Early Cost Estimation of Die-Cast Parts," Int. J. Prod. Res., accepted for publication.
- [52] Zhao, Z., and Shah, J. J., 2005, "Domain Independent Shell for Dfm and Its Application to Sheet Metal Forming and Injection Molding," Comput.-Aided Des., 37, pp. 881-898.
9. 著作権:
- この資料は、ジャティンダー・マダン、P.V.M. ラオ、T.K. クンドラの論文:「ダイカスト部品の自動分割方向および分割線決定のためのフィーチャ認識」に基づいています。
- 論文ソース: DOI: 10.1115/1.2768369
この資料は上記の論文に基づいて要約されたものであり、商業目的での無断使用は禁止されています。
Copyright © 2025 CASTMAN. All rights reserved.
Die-casting feature recognition for automated parting direction and parting line determinationDownload