このページは、「ダイカスト部品のサイドコア設計のための複雑なアンダーカット形状の自動識別」と題された研究論文を要約したものです。
1. 概要:
- タイトル: ダイカスト部品のサイドコア設計のための複雑なアンダーカット形状の自動識別 (Automated identification of complex undercut features for side-core design for die-casting parts)
- 著者: ランジット・シン (Ranjit Singh)、ジャティンダー・マダン (Jatinder Madan)、ラジェシュ・クマール (Rajesh Kumar)
- 発表年: 2014年
- 掲載ジャーナル/学会: Proc IMechE Part B: Journal of Engineering Manufacture
- キーワード: ダイカスト、複雑なアンダーカット形状、形状認識、サイドコア設計、抜き方向 (Die casting, complex undercut features, feature recognition, side-core design, release direction)
2. 研究背景:
- 研究テーマの社会的/学術的背景:
- ダイカストは、溶融金属を金型(ダイ)に圧入する重要な製造プロセスであり、金型はコアとキャビティのハーフで構成されています。
- ダイ設計は、ダイカスト部品のリードタイムと製造コストに大きな影響を与える、複雑で時間のかかるプロセスです。
- アンダーカット形状の識別は、ダイ設計における重要なステップであり、パーティングラインの決定とコアおよびキャビティの設計に直接影響を与えます。
- サイドコアは、アンダーカット形状を成形するために使用される特殊なツーリングコンポーネントであり、これらの形状が識別された後に設計されます。
- 従来、アンダーカット形状の識別は、ダイ設計の専門家が手動で行っていました。
- 既存研究の限界:
- 形状認識とアンダーカット形状検出に関する以前の貴重な研究にもかかわらず、文献レビューの結果、複雑なアンダーカット形状の処理におけるギャップが明らかになりました。
- 特に、以前の研究では、以下の点が十分に検討されていませんでした。
- 複雑なアンダーカット形状の認識。
- 複雑なアンダーカット形状の分類。
- 複雑なアンダーカット形状を単純な形状への分割。
- 研究の必要性:
- 手動によるアンダーカット形状の識別は、ダイカストプロセスにおける設計-製造統合のボトルネックとギャップを表しています。
- 本研究は、複雑なアンダーカット形状を自動的に識別するシステムを開発することにより、このギャップを埋める必要性に動機付けられています。
- さらに、後続のサイドコア設計を容易にするために、複雑なアンダーカット形状をより単純なコンポーネントに分割する方法論が必要です。
3. 研究目的と研究課題:
- 研究目的:
- 本研究の主な目的は、ダイカスト部品における複雑なアンダーカット形状の識別、分類、分割、および抜き方向の決定のための自動化システムを開発することです。
- 提案されたシステムは、これらの目的を達成するために、可視性とアクセス性の概念を活用しています。
- 主要な研究課題:
- B-repモデルからダイカスト部品の複雑なアンダーカット形状を自動的に識別するにはどうすればよいですか?
- 識別された複雑なアンダーカット形状を効果的に分類するにはどうすればよいですか?
- 複雑なアンダーカット形状を、より単純で管理しやすいアンダーカット形状に分割するにはどうすればよいですか?
- 各単純なアンダーカット形状の抜き方向を決定し、効率的なサイドコア設計のためにグループ化するにはどうすればよいですか?
- 研究仮説:
- 可視性とアクセス性の概念を利用するシステムを開発することにより、ダイカスト部品における複雑なアンダーカット形状の識別、分類、分割、および抜き方向の決定を自動化できると仮定します。
- 本研究で提案されたルールベースのアルゴリズムは、アンダーカット形状を効果的に分類および分割し、自動化されたサイドコア設計を可能にすると考えられます。
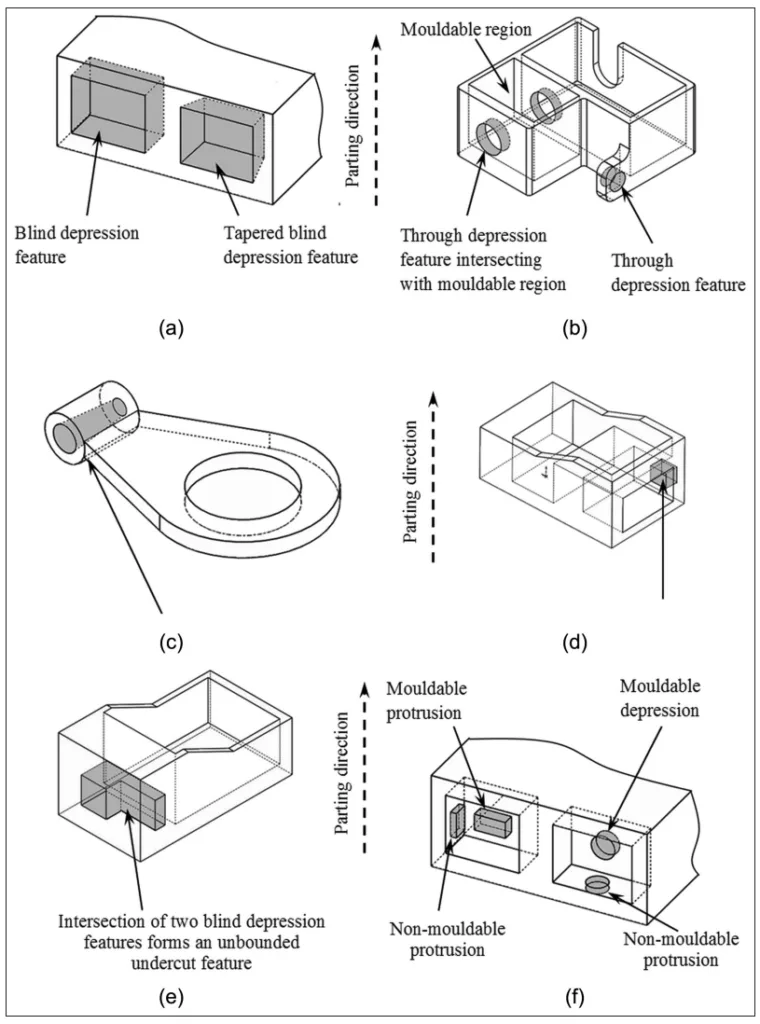
4. 研究方法:
- 研究デザイン:
- 本研究では、アンダーカット形状処理のための自動化システムを作成することに焦点を当てたシステム開発アプローチを採用しています。
- アンダーカット形状を分類および分割するために、ルールベースのアルゴリズムが設計および実装されました。
- 提案されたシステムの有効性は、例示的なダイカスト部品を使用したケーススタディを通じて評価されます。
- システムから得られた結果は、正確性と実用的な適用可能性を保証するために検証されます。
- データ収集方法:
- 主な入力データは、ダイカスト部品のB-rep(境界表現)ファイルで構成されています。
- これらのB-repモデルは、複雑なアンダーカット形状を含む、ダイカスト部品の幾何学的情報を表しています。
- 例示的なダイカスト部品は、提案されたシステムをテストおよび検証するためのケーススタディとして使用されます。
- 分析方法:
- コアとなる分析方法は、可視性とアクセス性の概念を利用するルールベースのアルゴリズムに基づいています。
- 可視性: 局所的な可視性が考慮され、表面上の点における法線は、局所的に見える方向を示します。可視性マップ(V-map)が使用され、これは半球です。
- アクセス性: 非凸面(Non-Convex Surface, NCS)のアクセス性は、同じ非凸領域(Non-Convex Region, NCR)内の他の表面からの障害物をチェックすることにより決定されます。
- エッジ、表面、およびそれらの関係を識別するために、部品の幾何学的および位相幾何学的データが分析されます。
- 抜き方向と表面法線の内積(Dot product, DP)は、表面を上向き、下向き、および中立の表面に分類するために使用されます。
- 研究対象と範囲:
- 本研究は、B-repモデルで表現できる複雑なアンダーカット形状を持つダイカスト部品に焦点を当てています。
- 範囲は、「複雑なアンダーカット形状は平面のみを持つ」という仮定で述べられているように、平面を持つ複雑なアンダーカット形状に限定されています。
- システムは、「ダイカスト部品は成形可能です」という仮定に基づいて、成形可能なダイカスト部品向けに設計されています。
5. 主な研究結果:
- 主な研究結果:
- 本研究では、以下のことが可能な自動化システムを開発することに成功しました。
- 複雑なアンダーカット形状の自動識別。
- これらの形状をさまざまなタイプ(例:ブラインドデプレッション、スルーデプレッション、非有界アンダーカット形状など)に分類。
- 複雑なアンダーカット形状を単純なアンダーカット形状に分割。
- 各単純なアンダーカット形状の抜き方向の決定。
- システムは実装され、例示的なダイカスト部品でテストされ、その機能と有効性が実証されました。
- 結果は検証され、ダイカスト設計のコンテキストにおけるシステムの精度と実用的な適用可能性を示しています。
- 本研究では、以下のことが可能な自動化システムを開発することに成功しました。
- 統計的/定性的分析結果:
- 本論文では、従来の意味での統計分析は提示されていませんが、ケーススタディの実装に基づいた定性的な結果を提供しています。
- システムの性能は、アンダーカット形状分析に手動でかかる時間と自動化システムを使用する時間を比較して評価されます。
- 「ダイカスト金型設計の専門家は、複雑なアンダーカット形状を単純な形状に識別、分類、分離し、抜き方向を決定するのに平均30〜40分を費やします。しかし、開発されたシステムの助けを借りれば、同じ活動に1〜2分しかかかりません。」これは、自動化システムを使用すると時間が大幅に短縮されることを示しています。
- データ解釈:
- システムは、ダイカスト部品設計における複雑で時間のかかるアンダーカット形状分析のタスクを効果的に自動化します。
- 複雑なアンダーカット形状を自動的に識別、分類、および分割することにより、システムは後続のサイドコア設計に貴重な情報を提供します。
- 単純なアンダーカット形状の抜き方向の決定は、サイドコアの自動化された設計をさらに容易にし、設計-製造統合ギャップを埋めることに貢献します。
- 図のリスト:
- 図 1. ダイカスト金型用語の図解
- 図 2. ダイカスト部品の表面の分類。
- 図 3. 非凸領域の概略図
- 図 4. 部分的にアクセス可能な表面の成形性。
- 図 5. アンダーカット形状の識別のための情報フロー図。
- 図 6. ダイカストアンダーカット形状の分類ツリー。
- 図 7. アンダーカット形状の例
- 図 8. 非有界アンダーカット形状の分割
- 図 9. 複雑な交差アンダーカット形状の分割
- 図 10. アンダーカット形状と交差成形可能領域の分割
- 図 11. 単純なアンダーカット形状の抜き方向決定のための情報フロー図。
- 図 12. 抜き方向の決定。
- 図 13. 例示部品 No. 1 の結果
- 図 14. 例示部品 No. 2 の結果
6. 結論と考察:
- 主な結果の要約:
- 本研究では、特にサイドコア設計のために、ダイカスト部品における複雑なアンダーカット形状の自動認識システムを開発し、実装することに成功しました。
- システムは、複雑なアンダーカット形状を識別、分類、およびより単純なコンポーネントに分割するプロセスを自動化します。
- また、サイドコア設計に不可欠なこれらの単純な形状の抜き方向を決定します。
- システムの有効性は、例示的なダイカスト部品に関するケーススタディを通じて実証および検証されました。
- 研究の学術的意義:
- 本研究は、複雑なアンダーカット形状の認識と処理に関して、以前の研究で特定された重要なギャップに対処しています。
- 複雑なアンダーカット形状を識別、分類、および分割するための新しい方法論を導入し、形状認識とダイ設計自動化の知識体系に貢献しています。
- 提案されたシステムは、自動化されたダイ設計および製造統合におけるさらなる研究のための貴重なフレームワークを提供します。
- 実用的な意義:
- 開発されたシステムは、ダイカスト業界にとって大きな実用的な意義を持っています。
- ダイ設計プロセスの自動化を促進し、リードタイムと設計コストの削減につながります。
- システムは、コアおよびキャビティ設計やサイドコア設計などのダウンストリームアクティビティに不可欠な情報を生成します。
- アンダーカット形状分析を自動化することにより、システムはダイカストにおける設計-製造統合の実現に貢献します。
- 分析時間の著しい短縮(手動で30〜40分からシステム使用時に1〜2分へ)は、その実用的な効率性を強調しています。
- 研究の限界:
- 現在のシステムは、平面を持つダイカスト部品と複雑なアンダーカット形状に限定されています。「提案されたシステムは、平面を持つダイカスト部品と複雑なアンダーカット形状を識別できます。」
- システムの適用可能性は、特定の幾何学的形状のアンダーカット形状で実証されていますが、アルゴリズムは一般的で適応可能であると指摘されています。
7. 今後のフォローアップ研究:
- フォローアップ研究の方向性:
- 今後の研究では、システムの機能を非平面を持つダイカスト部品を処理するように拡張することに焦点を当てる必要があります。「今後の研究では、非平面を持つ部品を含めることができます。」
- アンダーカット形状処理システムを自動化されたサイドコア設計と統合することは、価値のある次のステップとなるでしょう。「複雑なアンダーカット形状の識別とその単純なアンダーカット形状への分割により、本論文で提示された研究は、自動化されたサイドコア設計に拡張できます。」
- さらなる探求が必要な分野:
- より広範囲の幾何学的形状と形状の複雑さに対してアルゴリズムを適用するには、さらなる探求が必要であり、わずかな修正が必要になる可能性があります。「他の形状の場合、アルゴリズムのわずかな修正が目的に適うでしょう。」
- より包括的な自動化されたダイカスト設計ワークフローを実現するために、このシステムを他のダイ設計および製造プロセスと統合することを調査します。
8. 参考文献:
- Kalpakjian S and Schmid SR. Manufacturing engineering and technology. 4th ed. New Delhi: Pearson Education, 2011.
- Singh R and Madan J. Systematic approach for automated determination of parting line for die-cast parts. Robot Cim: Int Manuf 2013; 29: 346-366.
- Kumar V, Madan J and Gupta P. A system for design of multicavity die casting dies from part product model. Int J Adv Manuf Tech 2013; 67: 2083-2107.
- Gan GH, Woo TC and Tang K. Spherical maps: their construction, properties and approximation. J Mech Des: T ASME 1994; 116: 357-363.
- Elber G and Cohen E. Arbitrarily precise computation of Gauss maps and visibility sets for freeform surface. In: Proceedings of the third ACM symposium on solid modeling and applications (SMA ‘95), Salt Lake City, UT, 17–19 May 1995, pp.271–279. New York: ACM.
- Fuh JYH, Wu SH and Lee KS. Development of a semi-automated die casting die design system. Proc IMechE, Part B: J Engineering Manufacture 2002; 216: 1575-1588.
- Dhaliwal S, Gupta SK, Huang J, et al. Algorithms for computing global accessibility cones. J Comput Inf Sci Eng 2003; 3(3): 200-209.
- Surti A and Reddy NV. Non-discretized approach to visibility analysis for automatic mold feature recognition using step part model. J Adv Manuf Syst 2012; 12(1): 1-16.
- Liu M and Ramani K. Computing an exact spherical visibility map for meshed polyhedral. In: Proceedings of the 2007 ACM symposium on solid and physical modelling, Beijing, China, 4–6 June 2007, pp.367–372. New York: ACM.
- Chen YH. Determination of parting direction based on minimum bonding box and fuzzy logic. Int J Mach Tool Manu 1997; 37(9): 1189-1199.
- Hui KC and Tan ST. Mould design with sweep operations a heuristic search approach. Comput Aided Design 1992; 24(2): 81-92.
- Wong T, Tan ST and Sze WS. Parting line formation by slicing a 3D CAD model. Eng Comput 1998; 14: 330-343.
- Fu MW, Fuh JYH and Nee AYC. Generation of optimal parting direction based on undercut features in injection moulded parts. IIE Trans 1999; 31: 947-955.
- Lu HY and Lee WB. Detection of interference elements and release directions in die-cast and injection-moulded components. Proc IMechE, Part B: J Engineering Manufacture 2000; 214(6): 431-441.
- Yin Z, Ding H and Xiong Y. Virtual prototyping of mould design: geometric mouldability analysis for near net shape manufactured parts by feature recognition and geometric reasoning. Comput Aided Design 2001; 33: 137-157.
- Ye XG, Fuh JYH and Lee KS. A hybrid method for recognition of undercut features from moulded parts. Comput Aided Design 2001; 33: 1023-1034.
- Ye XG, Fuh JYH and Lee KS. Automatic undercut feature recognition for side core design of injection molds. J Mech Design 2004; 126(3): 519-526.
- Khardekar R, Burton G and McMains S. Finding feasible mold parting directions using graphics hardware. Comput Aided Design 2006; 38: 327-341.
- Banerjee AG and Gupta SK. Geometrical algorithms for automated design of side actions in injection moulding of complex parts. Comput Aided Design 2007; 39: 882-897.
- Kumar N, Ranjan R and Tiwari MK. Recognition of undercut features and parting surface of moulded parts using polyhedron face adjacency graph. Int J Adv Manuf Tech 2007; 34(1-2): 47-55.
- Madan J, Rao PVM and Kundra TK. Die-casting feature recognition for automated parting direction and parting line determination. J Comput Inf Sci Eng 2007; 7(3): 236-248.
- Fu MW. The application of surface demoldability and moldability to side-core designing die and mold CAD. Comput Aided Design 2008; 40: 567-575.
- Madan J, Singh A and Kumar S. Recognition of intersecting features and identification of separable regions for design-manufacturing integration. In: Proceedings of the international conference on digital factory (ICDF), Trichy, India, 11-13 August 2008, pp.60-67.
- Huang TS. Algorithms for recognizing undercut feature. J Technol 2008; 23(1): 61-69.
- Bidkar RA and McAdams DA. Methods for automated manufacturability analysis of injection-molded and die-cast parts. Res Eng Des 2010; 21: 1-24.
- Bassi R, Reddy NV and Bedi S. Automatic recognition of intersecting features for side-core design in two piece permanent molds. Int J Adv Manuf Tech 2010; 50: 421-439.
- Ran JQ and Fu MW. Design of internal pins in injection mold CAD via the automatic recognition of undercut features. Comput Aided Design 2010; 42(7): 582-597.
- Sunil VB and Pande SS. Automatic recognition of features from freeform surface CAD models. Comput Aided Design 2008; 40: 502-517.
- Tan ST, Yuen MF, Sze WS, et al. Parting lines and parting surfaces of injection moulded parts. Proc IMechE, Part B: J Engineering Manufacture 1990; 204: 211-221.
9. 著作権:
- この資料は、ランジット・シン、ジャティンダー・マダン、ラジェシュ・クマールの論文:「ダイカスト部品のサイドコア設計のための複雑なアンダーカット形状の自動識別」に基づいています。
- 論文ソース: DOI: 10.1177/0954405413514744
この資料は上記の論文に基づいて要約されたものであり、商業目的での無断使用は禁止されています。
Copyright © 2025 CASTMAN. All rights reserved.