1. 概要:
- タイトル: ダイカスト部品のコンピュータ支援製造性解析 (コンピュータ支援による製造容易性分析)
- 著者: J. Madan, P. V. M. Rao, T. K. Kundra
- 発表年: 2007年
- 掲載ジャーナル/学会: Computer-Aided Design & Applications (コンピュータ支援設計と応用)
- キーワード: 製造容易性設計 (DFM), 幾何学的推論, ダイカスト, プロセス知識, 特徴認識
2. 研究背景:
- 研究テーマの社会的/学術的背景:
- 現代の産業界は、製品開発期間の短縮、生産性と効率の向上に努めています。
- 設計部門と製造部門が異なる場所に配置されている大規模企業では、Design for Manufacture (DFM: 製造のための設計) の概念が生まれました。
- Van Vlietら [30] によれば、「DFM、すなわち製造のための設計とは、製品の設計段階において、製造の容易性を確保するために製品とプロセスの概念を最適化することを意味します」。
- 部品のコストの70%は設計段階で決定されると報告されており [1]、DFM原則を設計プロセスの初期段階に組み込むことの重要性が強調されています。
- DFMツールを導入することは、設計から製造へのスムーズな移行にとって非常に重要です。設計者は、最新の製造プロセスとツールに関する知識を持つか、DFMサポートシステムを利用する必要があります。
- DFMを実装することで、製品設計の製造容易性の向上、市場投入までの時間の短縮、コスト削減などのメリットが得られます。
- DFMの応用分野は、検証、定量化、最適化の3つの領域に分類できます [30]。
- DFMのアプローチは、ルールベースとプランベースに大別されます [11]。ルールベースのアプローチでは、プロセス能力を超える設計属性を特定するためにルールが使用されます。一方、プランベースのアプローチでは、時間とコストを最小限に抑えるために、まず実現可能なプロセスプランを作成します。
- DFMの指標には、定性的な側面(グッドプラクティスルールなど)と定量的な側面(コストと時間見積もりなど)が含まれます [27]。
- 既存研究の限界:
- 既存のDFM研究は、主に機械加工 [11, 32] や板金加工 [25, 31] の分野に集中しており、ダイカストへの関心は低いものでした。
- ダイカスト部品の包括的な自動製造性研究は、ほとんど存在しません。
- ダイカストでは、設計チームと製造チームの間、金型設計と製造の間、そして生産開始前のプロセスシミュレーションとテストの間で、より多くの反復が必要となるため、生産リードタイムが特に長くなり、DFMの実装が重要になります。
- 金型設計の分野では、生産リードタイムの短縮に関する研究がいくつか行われていますが [33, 34]、ダイカスト部品の自動DFM解析は依然として重要な課題です。
- 従来のDFMシステムには、以下のような限界があります。
- 対話的な部品情報入力への依存。
- CADモデルからの全体的な部品属性のみの考慮。
- 成形工具がアクセスできない特徴、肉厚のばらつき、プロセス制限の違反などのDFM問題が未解決。
- グッドプラクティスルールに基づいた設計改善のための包括的な提案の欠如。
- 製造特徴の認識と製造容易性のための幾何学的側面の評価能力の限定。
- 部分的な自動化と、設計履歴や中間面品質への依存。
- 形状修正システムにおける設計改善のための製造容易性アドバイスの欠如。
- 研究の必要性:
- 既存のアプローチの限界を克服し、ダイカスト製造特有の課題に対処するために、ダイカスト部品の自動DFM解析の必要性は明らかです。
- 設計者が設計を改善するためのフィードバックとして使用できる、部品CADモデルからの自動製造容易性アドバイスを生成するシステムが必要です。
- 設計変更が製造コストと時間に与える影響を設計者が理解できるように、自動化されたコストと時間見積もりを組み込むことが重要です。
- ダイカスト部品の製造容易性解析の設計検証と定量化の両段階に対処する包括的なシステムが、設計の効率と有効性を高めるために必要です。
3. 研究目的と研究課題:
- 研究目的:
- 本研究の主な目的は、ダイカスト部品に特化した自動製造容易性解析システムを開発することです。
- このシステムは、設計者が製造可能なダイカスト部品を作成するのを支援することを目的としています。
- 設計および製造プロセスにおけるコストと時間を節約することを目指しています。
- このシステムは、ダイカスト部品の品質と機能要件を損なうことなく、これらの目的を達成するように設計されています。
- 主な研究課題:
- CADモデルに基づいてダイカスト部品の製造容易性を自動的に解析するシステムをどのように開発できるか?
- ダイカスト部品設計における製造容易性の問題を特定するために、どのような幾何学的推論技術とプロセス知識を効果的に活用できるか?
- 設計改善を促進するために、製造容易性アドバイスを設計者に明確かつ実行可能な方法でどのように提示できるか?
- 設計変更の影響を定量化するために、自動化されたコストと時間見積もりを製造容易性解析システムにどのように統合できるか?
- ダイカスト部品の製造容易性解析の設計検証(違反の特定)と定量化(コストと時間見積もり)の両側面を、システムはどのように対処できるか?
- 研究仮説: (論文の目的と結果から暗黙的に述べられ、推測される)
- 幾何学的推論とダイカストプロセス知識を用いるコンピュータ支援システムは、ダイカスト部品の製造容易性解析を効果的に自動化できると仮説を立てています。
- 設計者に自動化された製造容易性アドバイスとコスト/時間見積もりを提供することで、ダイカスト部品設計の改善、設計反復の削減、製造効率の向上が期待できると仮説を立てています。
- 提案されたシステムは、以前に未解決だった製造容易性の問題に対処し、設計検証と定量化を統合することで、ダイカストに対する既存のDFMアプローチよりも包括的で効果的であると仮説を立てています。
4. 研究方法:
- 研究デザイン:
- 本研究では、ダイカスト部品の製造容易性解析のためのコンピュータ支援ツールを作成するために、システム開発アプローチを採用しています。
- システムは自動化されるように設計されており、解析プロセスにおけるユーザーの介入を最小限に抑えます。
- 設計は、幾何学的推論、プロセス知識、およびコスト/時間見積もりモジュールをまとまりのあるシステムに統合することに重点を置いています。
- データ収集方法:
- システムは、ダイカスト部品のCADモデルを、中立的で標準化されたフォーマットであるSTEPファイル形式(ISO 10303)で入力として使用します。
- ダイカストのプロセス知識と設計ルールをコンパイルし、知識ベースに組み込みます。この知識ベースには、材料固有のプロセス制限と能力が含まれています。
- コストと時間見積もりをサポートするために、材料とエネルギーデータ、製造リソースとツーリングデータが収集されます。
- 分析方法:
- 幾何学的推論: 幾何学的推論を適用して、STEPファイルデータから製造特徴と部品属性を抽出します。これには、STEPファイルを解析して面-エッジおよびエッジ-頂点関係を取得し、ルールを適用してダイカスト特徴を認識することが含まれます。
- 特徴認識: ダイカスト固有の特徴(非製造容易性特徴、サイドコアを必要とする特徴、部品属性など)を識別するための特徴認識モジュールが開発されました。このモジュールは、幾何学的推論を使用し、以前に開発された方法 [20] を基に構築されています。
- プロセス知識の適用: 抽出された特徴と属性は、ダイカストプロセス制約と設計ガイドラインの知識ベースに対して評価されます。これには、部品形状の制限、全体的な部品属性の制限、およびグッドプラクティスルールの遵守の確認が含まれます。
- 肉厚解析: 独自のソフトウェアGeomCaliper® [10] を使用して、肉厚のばらつきを解析し、肉厚違反を特定します。ローリング球アルゴリズムを採用しています。
- コストと時間見積もり: 自動化されたコストと時間見積もりモジュールが統合されており、特徴マッピング知識、製造リソース、ツーリングデータ、および知識を利用しています。コストと時間見積もりの方法論は、以前の研究 [21] で詳しく説明されています。
- 製造容易性アドバイスの生成: 解析に基づいて、システムは製造容易性アドバイスを生成し、特定された問題に対処し、製造容易性を向上させるための設計変更を提案します。
- 研究対象と範囲:
- 研究は、ダイカスト部品とダイカスト製造プロセスに焦点を当てています。
- 範囲は、幾何学的製造容易性解析に限定されており、製造容易性に影響を与える部品設計の幾何学的側面に対処しています。
- システムは、さまざまなダイカスト材料(亜鉛、アルミニウム、マグネシウム、銅)とそれらの特定のプロセス制約を考慮しています。
- 公差と表面仕上げの評価は、機械可読形式でデータが利用できないため、対話的に対処されており、これらの領域における部分的な範囲を示しています。
5. 主な研究成果:
- 主な研究成果:
- ダイカスト部品の自動製造容易性解析のためのコンピュータ支援システムが、MATLAB 7 on Windows 2000を使用して開発および実装されました。
- システムは、非製造容易性設計の特徴を効果的に識別し、製造容易性アドバイスの形で設計者にフィードバックを提供します。
- 設計者は、提案された変更を組み込むことで部品を再設計し、製造容易性を向上させることができます。
- システムは、元の部品と再設計された部品の両方の時間とコストの見積もりを表示することで、製造容易性の向上を定量化します。
- システムは、2つの典型的なダイカスト部品(サンプル部品1とサンプル部品2)を使用して実証および検証されました。
- 統計的/定性的分析結果:
- サンプル部品1:
- 初期設計コスト: 30.0ドル
- 初期設計製造時間: 137秒
- 再設計部品コスト (製造容易性アドバイス実装後): 18.9ドル
- 再設計部品製造時間: 85秒
- 改善: コスト削減 37%, 時間削減 38%.
- サンプル部品2:
- 初期設計コスト: 128.0ドル
- 初期設計製造時間: 138秒
- 再設計部品コスト (製造容易性アドバイス実装後): 61.0ドル
- 再設計部品製造時間: 80秒
- 改善: コスト削減 52%, 時間削減 42%.
- 結果は、システムの助言を適用し、部品を再設計した後、製造コストと製造時間の両方が大幅に削減されたことから明らかなように、製造容易性の著しい改善を示しています。
- サンプル部品1:
- データ解釈:
- システムによって生成された製造容易性アドバイスは、製造容易性の問題に対処する設計変更を効果的に導きました。
- 提案された設計変更を実装すると、製造時間とコストの削減によって証明されるように、部品の製造が容易になり、経済的になります。
- コストと時間の改善を定量化するシステムの能力は、設計者に設計変更の影響と製造容易性解析システムの有効性を評価するための具体的な指標を提供します。
- 製造時間とコストの削減は、設計反復の可能性の削減も示唆しており、製品開発サイクルの迅速化に貢献しています。
- 図表リスト:
- 図 1: ダイカストプロセス用語。
- 図 2: 部品形状の制限。
- 図 3: ダイカストにおけるグッドプラクティスルール (出典: [2, 3, 22])。
- 図 4: リブ形状に関する設計ルール。
- 図 5: 自動製造容易性解析システムのアーキテクチャ。
- 図 6 (a) サンプル部品 1
- 図 6(b) 再設計されたサンプル部品 1
- 図 7 (a) サンプル部品 2
- 図 7(b) 再設計されたサンプル部品 2
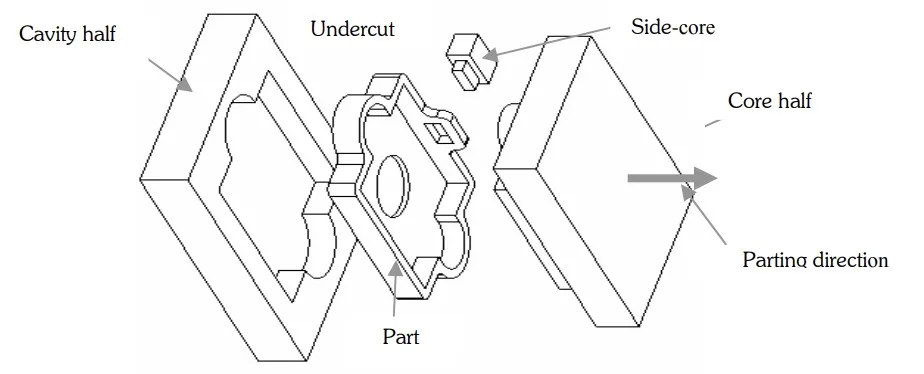
6. 結論と考察:
- 主な結果の要約:
- ダイカスト部品のコンピュータ支援製造容易性解析システムが発表されました。
- 開発されたシステムは、以前のシステムよりも包括的であり、ルールベースとプランベースの両方の設計評価方法の特徴を効果的に組み合わせていると説明されています。
- システムは、プロセスに関する詳細な知識がなくても、製造生産性を向上させるための迅速なフィードバックを設計者に提供します。
- 製造容易性に関するフィードバックの提案が生成され、設計者が検討し、実装する可能性のあるものとして提示されます。
- 研究の学術的意義:
- 本研究は、機械加工や板金加工と比較して注目度が低かったダイカストに焦点を当てることで、自動DFMの分野における重要なギャップに対処しています。
- このシステムは、幾何学的推論、ダイカストプロセス知識、およびコスト/時間見積もりを単一の自動化フレームワーク内に統合することにより、DFMの知識体系に貢献しています。
- 本研究は、幾何学的推論とプロセス知識を使用して、ダイカストのような複雑な製造プロセスの製造容易性解析を自動化することの実現可能性と有効性を実証しています。
- 実用的な意義:
- 開発されたシステムは、ダイカスト部品の設計者が、設計の初期段階で製造容易性の問題に積極的に対処するための貴重なツールを提供します。
- システムを使用することで、設計者は設計の製造容易性を向上させ、製造コストと生産時間の削減につながります。
- このシステムは、製造可能な設計を最終決定するために必要な設計反復回数を削減し、製品開発サイクルと市場投入までの時間を短縮するのに役立ちます。
- このシステムを使用する設計者の生産性と効率の向上は、より経済的で競争力のある製造オペレーションに貢献できます。
- 研究の限界:
- 現在のシステムでは、部品の機能要件を明示的に考慮していません。設計者は、機能的なニーズの文脈で製造容易性アドバイスを評価し、提案を実装するかどうかを決定する責任があります。
- 再設計された部品の生成の自動化は実装されていません。設計者は、システムの助言に基づいて部品を手動で再設計する必要があります。
- 相互作用する特徴や自由曲面を持つ部品を処理するシステムの能力は、今後の改善の領域として特定されています。
- 公差と表面仕上げの評価は、対話的な入力を通じて部分的にのみ対処されており、これらの側面における完全な自動化には限界があることを示しています。
7. 今後のフォローアップ研究:
- フォローアップ研究の方向性:
- 再設計の自動化: 今後の研究では、システムから提供される製造容易性アドバイスに基づいて、再設計された部品を生成するプロセスを自動化することに焦点を当てる必要があります。これには、形状修正アルゴリズムやジェネレーティブデザイン技術の統合が含まれる可能性があります。
- 相互作用する特徴の処理: システムが相互作用する特徴から生じる製造容易性の問題を解析および対処する能力を強化するために、研究が必要です。これには、より高度な特徴認識および解析手法の開発が含まれる可能性があります。
- 自由曲面: システムを自由曲面を持つ部品を処理するように拡張することは、より幅広い適用範囲にとって重要です。これには、非平面形状の幾何学的推論と特徴認識の進歩が必要になります。
- 機能要件の統合: 今後の研究では、機能要件を製造容易性解析プロセスに統合することを目指すべきです。これには、設計変更が部品の性能に与える影響を評価するために、機能シミュレーションおよび解析ツールを組み込むことが含まれる可能性があります。
- さらなる探求が必要な分野:
- より広範囲なダイカストプロセスのバリエーション、材料、および設計ガイドラインを捉えた、より包括的な知識ベースの開発には、さらなる探求が必要です。
- 特徴認識、製造容易性予測、およびアドバイス生成を改善するために、高度なAIおよび機械学習技術の使用を調査することは有益である可能性があります。
- 製造容易性アドバイスとシステムフィードバックの明確さと使いやすさを向上させるためのユーザーインターフェースの強化も、さらなる探求の分野です。
8. 参考文献:
- [1] Barton, J. A; Love, D. M; Taylor, G. D.: Design determines 70% of cost: A review of implications for design evaluation, J. Engineering Manufacture, 12 (1), 2001, 41-58.
- [2] Boothroyd, G.; Dewhurst; P.; Knight, W.: Product Design for Manufacture and Assembly, Marcel Dekker Inc., New York, 1994.
- [3] Bralla, J.G.: Design for Manufacturability Handbook, McGraw Hill, New York, 1999.
- [4] Chen, Y.-M.; Miller, R. A; Sevellar, K.: Knowledge-based manufacturability assessment: an object-oriented approach, Journal of Intelligent Manufacturing, 6, 1995, 321-337
- [5] Chen, Y.-M.: Development of a computer-aided concurrent net shape product and process development environment, Robotics and Computer Integrated Manufacturing, 13 (4), 1997, 337-360.
- [6] Chen, Y. -M.; Wen, C. C.; Ho, C. T.: Extraction of geometric characteristics for manufacturability assessment, Robotics and Computer Integrated Manufacturing, 19, 2003, 371-385.
- [7] Deng, Y. M.; Britton, G. A; Lam, Y. C: Towards automatic shape modification in injection-moulded-plastic-part design, 2005. (Available online: DOI 10.1007/s00170-004-2388-9)
- [8] Dixon, J. R.; Poli, C.: Engineering Design and Design for Manufacture, Field Stone Publishers, Massachusetts, USA, 1995.
- [9] Driscoll, M. O.: Design for manufacture, Journal of Materials Processing Technology, 22, 2002, 318-321.
- [10] GeomCaliper® Software, Geometric Software Solutions Limited, USA.
- [11] Gupta, S. K.;, Das, D.; Regli, W. C; Nau, D. S.: Automated manufacturability analysis: A survey, Research in Engineering Design, 9(3), 1997, 168-190.
- [12] Grosse, I. R.; Sahu, K.: Preliminary design of injection moulded parts based on manufacturing and functional simulations. In Advances in Feature Based Manufacturing. (Shah, J. J.; Mantyla M.; Nau, D. S.: Elsevier Science Limited, 1994.)
- [13] Hanada, H.; Leifer, L. J.: Intelligent design system for injection moulded parts based on the process function analysis method, Proc. NSF Engineering Design Research Conf., Amherts, MA, 1989, 599-612.
- [14] Herrmann, J. A; Cooper, J.; Gupta, S. K; Hayes, C. C.; Ishii, K.; Kazmer, D.; Sandborn, P. A.; Wood, W. A.: New Directions In Design For Manufacturing, Proceedings of ASME, DETC 2004-57770, September 28-October 2, 2004, Salt Lake City, Utah USA.
- [15] Hui, K. C.: Geometric aspects of the mouldability of parts, Computer aided design, 29 (3), 1997, 197-208.
- [16] Ishii, K.; Miller, R. A.; Design Representation for Manufacturability Evaluation in CAD: Beyond Feature-based Design, ASME/ CIE '92 AI stream, 1992.
- [17] Kuo, T. C.; Huang, S. M.; Zhang, H. C.: Design for manufacture and design for, X': Concepts, applications and perspectives, Computers & Industrial Engineering, 41, 2001, 241-260.
- [18] Lockett, H. L.; Guenov, M. D.: An Intelligent Manufacturing Advisor for Casting and Injection-Moulding Based On A Mid-Surface Approach, Proceedings of ASME, DETC2002/CIE-34497, Montreal, Canada, September 29-October 2, 2002.
- [19] Lenau, T.; Nielsen, L.H.; Alting, L.: Design for Pressure Die Casting--a DFM Example, International Journal of Advanced Manufacturing Technology, Vol. 6 (2), 1991, 141-154.
- [20] Madan, J.; P. V. M. Rao; Kundra, T. K.: An automated cost estimation system for die-cast parts, Transactions of ASME Journal of Computing and Information Science in Engineering, 2006. (Article submitted)
- [21] Madan, J.; P. V. M Rao.; Kundra, T. K.: System for early cost estimation of die-cast parts, International Journal of Production Research, 2006. (Available online)
- [22] Product Design for Die Casting, North American Die Casting Association (NADCA), Rosemont, USA, 1998.
- [23] Poli, C.; Dastidar, P.; Fernandez, R.: Design Knowledge Acquisition for DFM Methodologies, Research in Engineering Design, 4, 1992, 131-145.
- [24] Pratt, M. J.; Wilson, P. R.: Requirements for support of form features in a solid modeling system', CAM-I, R-85-ASPP-01, 1985.
- [25] Ramana, K. V.; Rao, P. V. M.: Automated manufacturability evaluation system for sheet metal components in mass production, International Journal of Production Research, 43 (18), 2005, 3889–3913.
- [26] Shah, J.; Rogers, M.: Functional Requirements and Conceptual Design of Feature Based Modeling System, Journal of Computer Aided Engineering, 5(1), 1988, 9-15.
- [27] Shah, J. J.; Wright, P. K.: Developing theoretical foundations of DfM, DETC2000/ DFM 14015, September 10-14, Baltimore, MD, 2000.
- [28] Stauffer, L.; Rule, R.: A template for design for manufacture guidelines, Proceedings of ASME, DETC2003/DFM-48135, Chicago, Illinois, USA, September 2-6, 2003.
- [29] Venkatchalam, A. R.; Mellichamp, J. A.; Miller, D. M.: A knowledge-based approach to design for manufacturability, Journal of Intelligent Manufacturing, 4, 1993, 355-366.
- [30] Van Vliet, J. W.; Van Luttervelt, C. A.; Kals, H. J. J.: State of the art report on design for manufacturing, Proceedings of ASME DETC, Las Vegas, Navada, September 12-15, 1999.
- [31] Zhao, Z.; Shah, J. J.: Domain independent shell for DfM and its application to sheet metal forming and injection molding, Computer-Aided Design, 37, 2005, 881–898.
- [32] Srikumaran, S.; Sivaloganathan, S.: Proving manufacturability at the design stage using commercial modeling software, Computer-Aided Design and Applications, 2 (1-4), 2005, 507-516.
- [33] Song, I. -H.; Park, J. –M; Chung, S. -C: web based interference verification system for injection mold design, Computer-Aided Design and Applications, 3 (1-4), 2005, 129-138.
- [34] Ni, Q.; Lu, W. F.; Yarlagadda, P. K. D. V.: A PDM-based framework for Design to Manufacturing in mold making industry, 3 (1-4), 211-220.
9. 著作権:
- この資料は、J. Madan、P. V. M. Rao、および T. K. Kundra の論文「Computer Aided Manufacturability Analysis of Die-cast Parts」に基づいています。
- 論文ソース: [https://doi.org/](DOI URL はテキストに記載されていません。)
この資料は上記の論文に基づいて要約されたものであり、商業目的での無断使用は禁止されています。
Copyright © 2025 CASTMAN. All rights reserved.